
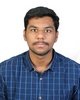
- Open Access
- Authors : Ch. Hemanth Kumar , Abrar Ahmed , M. Sai Abhiram , P. Chetan Kumar, Bdy Sunil
- Paper ID : IJERTV10IS060173
- Volume & Issue : Volume 10, Issue 06 (June 2021)
- Published (First Online): 26-06-2021
- ISSN (Online) : 2278-0181
- Publisher Name : IJERT
- License:
This work is licensed under a Creative Commons Attribution 4.0 International License
Design, Analysis & Manufacturing of Disc Brake
CH. Hemanth Kumar1, Abrar Ahmed2, M. Abhiram3, P. Chetan Kumar4, BDY Sunil5.
1,2,3,4 UG Student Department of Mechanical Engineering, Institute Aeronautical Engineering, Hyderabad. Telangana, INDIA.
5Associate Professor & Head, Department of Mechanical Engineering, Institute Aeronautical Engineering, Hyderabad.
Telangana, INDIA
Abstract:- In todays Industrial era the technology and machines has overtaken man power in the development and manufacturing of materials and products. Most of the materials either used by end consumers or further used for assembling are fabricated into desired shapes with required mechanical properties by one or combination of two or more of the following methods; Casting, Welding, Forming and machining. Out of these machining is one of the most important processes employed.Machining of the objects with complex shapes includes contours and deep cuts. It is difficult on conventional machines to perform such operations. CNC (Computer Numerically Controlled) machines efficiently overcome these problems.
In this paper we have reviewed brake disc fabrication solutions through various machining processes using CNC machine tools. The
engineering method of implementing them in large-scale manufacturing was described. During typical braking, disc brakes are exposed to high temperatures, resulting in significant thermal stress. This leads to two adverse phenomenon: Brake fading and significant amount of plastic deformation in the brake rotor, resulting in a brake rotor with a short fatigue life. The purpose of this study is to look at the temperature distribution of grey cast iron disc such that the design can optimize the temperature distribution so as to minimize the above two mentioned adverse effects. The main goal of this paper is to review design, modelling, analysis and manufacturing with optimized parameters using advanced PLM software such as NX9 and CNC machine tools.
Key Words:CNC, Disc Brakes, Optimization, Brake fade, Thermal Stresses, Manufacturing, Designing, part programming, Machining, Turning, Milling, Drilling, FEA
INTRODUCTION:
Computer Numerical Control (CNC) refers to automated control of machining tools (such as lathes, mills, grinders) via a computer. CNC machine manufactures a piece of material to meet requirements which is otherwise achieved by following a coded instruction and without a direct intervention of an operator of the machining operation.Most of the CNC systems today use a microcomputer- based controller unit. This is due to the trend towards cutting down the size of computers and subsequently utilization of a committed and stored programs to play out a few or the entirety of the essential numerical functions is being carried out by CNC systems. For a CNC, the program is entered once and then stored in the micro-computer memory. As a result, the tape reader is only used for initial loading versatility and standard capability. By simply reprogramming the CNC controller, new device options may be added. This reprogramming ability, both in terms of part programming and system control options has made CNC to be often referred as soft wired numerical control.
Disc brake is a type of brake which slows down wheel rotation by the friction as a result of brake pads rubbing on a brake disc using calipers. The brake disc is typically constructed of cast iron, though composites such as strengthen carbon-carbon or ceramic matrix composites may be used in some situations. This is linked to the axle and or to the wheel. Brake pads, which are fixed on a mechanism known as a brake caliper, which in turn provide friction, is pressed against both sides of the disc mechanically, hydraulically, pneumatically, or electromagnetically to stop the wheel. Friction slows or stops the disc and its associated wheel. Brakes turn motion into heat, and if they get too hot, they lose their effectiveness, which is known as brake fade.
Grey cast iron is a typical material for brake discs because of its operational stability, low cost of raw materials, and simplicity of fabrication. Special applications need the use of other materials. Carbon composite materials, for example, are employed in the manufacture of brake discs for racing vehicles and planes. Ventilated brake discs are becoming more frequent in high- performance braking systems. The design of internal bridging, often known as "blades," has a significant impact on air circulation.
CNC MACHINE TOOLS:
Working Theory:
-
Computer Numerical Control (CNC) actuate automatic control of the machine tools through precisely programmed instructions which are loaded on micro-computers memory, as contrary to manually operated conventional machines via levers and hand-wheels or otherwise mechanically automated via cams or through hydraulics alone.
-
In CNC system, computers are an essential component of the control system. In modern CNC, CAD and Computer aided manufacturing techniques and software are employed in the development of design and manufacturing of the component.
-
Coming to movement and positioning of tools, motors push the tool's direction through a system of steps-down gears, allowing for extremely precise movement. Direct-drive stepper motors and servo motors are more typically employed in modern systems.
-
In metalworking machine tools closed loop controls are essential and necessary to satisfy the demands for precision, speed, and reproducibility.
-
The majority of CNC machines have control systems made by Siemens or Fanuc. G codes and M codes are more typically used for coding in the Fanuc systems. G codes which refers to preparatory codes are used for machining processes and equipment movement whereas M codes refers to miscellaneous functions codes are used to monitor spindle movements such as on/off, rotation in a clockwise or counter-clockwise direction and tool shift operations.
CNC Milling Machine:
-
Milling is the process of machining a flat, curved, or uneven surface by feeding it into a spinning cutter with many cutting edges. The milling machine is made up of two parts: a motorized spindle that mounts and rotates the milling machine cutter, and a reciprocating adjustable workbench that mounts and feeds the work piece.
-
A CNC milling machine is the most flexible milling machine operated by a computer. The spindle can move in all three directions, and the table can rotate 360 degrees, making it an enhanced version of the bed type milling machine.
-
All of these actions are hydraulically regulated and controlled by a computer. A sketch of the job is layered on the PC, which is then cut on the work piece by the cutters.
CNC Turning Lathe:
-
CNC turning is a fabrication process in which material pieces are rotated in a chuck while a tool is fed to the component to remove material in order to generate the required form. A turret (a rotating holder for tools), which is equipped with tooling, is programmed to travel to the raw material and remove material in order to get the desired outcome.
-
Because it includes material removal, this is also known as "subtraction machining". Although initially materials are circular, different forms like as squares or hexagons can be used. It is capable of producing cylindrical pieces with a variety of shapes and contours.
-
In turning centers tooling is mounted on a computer-controlled turret. There are a variety of CNC turning centers available, each with its own set of featues such as different spindle options, capabilities in terms of power and speed, tooling options, outer diameter limitations, etcetera which has an impact on the kind of parts that can be produced on it at a reasonable cost.
CNC Part Programming:
The CNC control unit receives instructions from the part program to carry out the machine operations.
Coordinate system of the machine:
The coordinate system makes it easy to provide the description of traverse path movements. The instruction to "advance the longitudinal slide in the orientation of the spindle head" is rather lengthy. Moreover, it would be different in each language.
Movement of the machine tool parts with respect to coordinate system is as follows:
-
axis: Table positioning.
-
axis: Saddle positioning.
-
axis: Spindle head movement.
-
Programming methods:
In a CNC machine, there are two ways to define the path of motion.
-
Absolute programming method.
-
Relative programming method (or) incremental programming method
In the absolute programming approach, a single coordinate generally referred to as an origin on the work piece or anywhere on the table is used as a reference or zero point, and all other coordinates are expressed in relation to that origin or zero point.
In the relative programming approach, the next point dimension in each step is referenced to the preceding step's last point. The tool still starts at the origin (work zero), but each set of coordinates moves the tool closer to the point it was in before.
Disc Brakes:
The brake disc is typically constructed of cast iron, though composites such as strengthen carbon-carbon or ceramic matrix composites may be used in some situations. This is linked to the axle and or to the wheel. Brake pads, which are fixed on a mechanism known as a brake caliper, which in turn provide friction, is pressed against both sides of the disc. Brake plate have more noteworthy halting force than drum slows down and are generally introduce on the front wheels to improve slowing down during unexpected stops. Brake plate comprises of metal circle, or a rotor, that is associated with the wheel. A gadget called a caliper lays on the edge of the rotor and holds to grinding cushions on eider sides of the rotor. Applying the brakes makes liquid push a cylinder inside the caliper, which squeezes the brake cushions against the rotor and eases back the wheel. Brake plate don't have return springs, similar to those in drum brakes, to withdraw the brakes.
Brake plates are viewed as better than drum brakes, since brake circles can deal with higher slowing down temperature and scatter heat all the more rapidly. Additionally, brake plates don't trap water as drum brakes can. At the point when drum brakes become wet, they endure a reduction in slowing down, called brake blur, which can happen when passing through profound puddles. Most vehicles and trucks use brake circles on the front wheels. Brake circles commonly required add pedal pressing factor, so most vehicles outfitted with these brakes have power-stopping mechanism to lessen a driver's pedal exertion. Most force stopping mechanisms utilize a vacuum to expand vacuum force and motor cylinders make a vacuum as they bring air into the motor.
Brake discs machining:
Brake disc demand is high on a global scale, reaching several million pieces each year, necessitating large-scale fabrication. A technical procedure for manufacturing brake discs in a contemporary plant that produces thousands of discs per day, with 120 type-sizes every month, for both new automobiles and service is shown.
Basic disc-shaping processes are carried out by semi-automatic machining groups, which are made up of numerically controlled turning lathes, CNC drill machines and CNC milling machines linked by transfer lines. SRAK PRESTEK's PCC job turning lathes are used to perform the turning operations. These are two-chamber machines having a moveable electro-spindle on a vertical center of rotation for dry machining.
The electro-AC spindle's motor has a power of 18 kW, a rotating speed range of 50-1900 RPM, and a max spindle torque of 750 Nm, while the maximum work piece diameter is 350 mm.
The electro-spindle, which is mounted on a cross slide, moves longitudinally within a range of 500 mm at a feed speed of 0- 4100 mm/min and transversely within a range of 1750 mm at a feed speed of 0-10100 mm/min.
A horizontal axis of rotation turret with six 30 mm diameter cylindrical tool sockets is included with the turning lathes. As an additional lathe axis, the turret is controlled by a Fanuc control system.
Drilling activities in the manufacturing of brake discs are carried out using HURCO's high-performance CNC drilling equipment. The machine tools are connected via transfer links to operate much like robots. Machine cutting variables were optimized for all operations, and part programs for lathes, mills and drillers were changed.
Specifications of Brake disc
Operations sequence and description
Modifications in manufacturing technological parameters:
A change was made to the ventilated brake disc machining technical procedure(Podmagorski, 2003). The major goal of the change was to boost productivity by altering machining variables using ceramic plates which were done as following:
-
Two for turning operation
-
Three for boring and drilling operation
-
One for milling operation
For carbide tools, the machining variables were feed rates= 0.1-0.5 mm/rev and cutting speeds = 100-500 m/min, respectively.
Because of the control systems' capabilities, several of those settings were raised to their optimum conditions. The changes and modifications applied resulted in a decrease of upto 20 percent in the machining processes. The use of ceramic plates boosted productivity by lowering the rate with which they had to be replaced, while still maintaining the brake disc quality criteria.
Design and Thermal Analysis: Material Selection:
The fundamental and crucial stage in constructing a suitable rotor of disc brake is material selection. Quality functional deployment factor is based on type of material chosen for the rotor. The element used must have a high tensile strengths and yield strength, as well as the appropriate coefficient of friction and the ability to withstand a wide temperature range. For this review comparison was carried out among three materials: cast iron, carbon composite and steel.
Design Considerations:
To develop a disc rotor, we must first evaluate all hard measurements and wheel geometry, as well as the mounting pattern of the wheel assembly. The manufacturing process and its dependability are the most important factors to consider while designing, as the manufacturing process is the most important factor that impacts the product's functioning and operating performance. The design of the disc brake takes into account the generation of heat at the moment of clamping the disc brake, allowing for maximum heat dissipation via radiation and convection through the disc.
Assumptions:
-
The vehicle's kinetic energy is lost through the brake discs, which means there is no heat loss between the tire and the road surface and uniform deceleration.
-
The study is based only on thermal loads. The brake rotor's life is not determined by the study.
-
The material employed for the analysis has a consistent thermal conductivity throughout.
Calculations:
Where:
-
K = 0.9 (% of KE absorbed by disc)
-
M = Mass of disc (kg)
-
V = Vehicle speed(km/h)
-
= weight distribution of axle on either side
Design and Modelling in NX 9.0:
Results:
CONCLUSIONS:
The purpose of this paper was accomplished. Changes o part programs for lathes, milling and drilling operations were made to optimize machine cutting characteristics.The changes and modifications applied resulted in a decrease of upto 20 percent in the machining processes. The alterations made to the brake disc manufacturing process considerably boosted production while maintaining execution precision.
In terms of temperature vs. time, the graphs are generated for various elements in meshing. The Moment of Inertia of the rotor is lowered, causing the vehicle's pick-up acceleration to rise and the quantity of gasoline consumed to decrease, potentially making it a major environmental aspect affect. This review supports both steady-state thermal and static structural analyses. This study report also includes brake disc meshing.
Finally, I conclude that, the advantages aimed are achieved practically during the manufacturing of the above component on CNC vertical center.
-
Baker, A. K. (1986). Vehicle braking.
REFERENCES:
-
The Machining Of Brake Discs, By WOLNY, R. & RYGALLO, A.
-
Structural and Thermal Analysis of Rotor Disc of Disc Brake Manjunath T V1, Dr Suresh P M2.
-
Design of Band and Disc Brakes form NPTEL
-
MitPatel,MansiRaval, and Jenish Patel Design of Disc Brake rotor, International journal Of Engineering Development and Research, Vol.04, Issue 4, pp. 919-926, 2016.
-
CNC Fundamentals and programming 2/e PB (Authors: P.M. AGRAWAL & V.J. PATEL).
-
CNC Programming Handbook 3rd edition (Authors: Peter Smid).
-
Brake Design and Safety (Authors: Rudolf Limpert).