
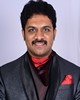
- Open Access
- Authors : Hariprasad Thimmegowda , Yadu Krishnan S
- Paper ID : IJERTV10IS010228
- Volume & Issue : Volume 10, Issue 01 (January 2021)
- Published (First Online): 02-02-2021
- ISSN (Online) : 2278-0181
- Publisher Name : IJERT
- License:
This work is licensed under a Creative Commons Attribution 4.0 International License
Computational and Experimental Study on Flow Quality of Open-Loop Low-Speed Wind Tunnel
Hariprasad Thimmegowda Department of Aerospace Engineering Alliance University, Bangalore, India
Yadu Krishnan S Department of Aerospace Engineering Alliance University, Bangalore, India
Abstract- Several kinds of wind tunnels are developed in the past few decades. It is an essential tool for aerodynamic studies in research and academia. However, irrespective of the tunnel, it becomes crucial to maintain the flow quality in the test section holding the measurements accurate. This study emphasizes on the flow quality of low speed subsonic open-loop wind tunnel. Experimental findings were validated with computational results. Flow quality parameters were examined by verifying the uniformity and velocity profile of the test section. At various fan speed, test section wind velocity was measured and compared with numerical results. Both results agree with each other. Uniformity assessment was evaluated along the centerline of the test section and noted that wind velocity remains constant in both experimental and computational investigation. Velocity profile was measured from the upper to lower wall, which confirms the boundary layer near the walls. The profile, in computational and experimental results, were similar. These validated results can be employed as a reference to the design and construction of a low- speed subsonic wind tunnel.
Keywords: Subsonic wind tunnel, flow quality, flow uniformity, velocity profile, numerical techniques, experimental analysis.
-
INTRODUCTION
In the current era, the computational techniques in aerodynamics have revolutionized the way we approach the flow problems. However, the numerical solutions are not accurate and have to be validated with experiments and theoretical solutions. The wind tunnel, for example, is one of the best experimental tools for aerodynamic applications. The key components of a wind tunnel are honeycomb, contraction duct, test section and diffuser. Honeycomb section has various meshes varying in size to remove eddies in the flow and create a streamlined flow. Contraction cone helps to increase the flow velocity at the test section, decreasing the power requirement. Low subsonic wind tunnels have contraction ratio between 6 to 9 (Mehta and Bradshaw, 1979). The shape and size of the test section depend on the flow requirements, as the measurements are being made in the test section. The flow quality of the test section plays a vital role in the measurements made during the experiment. Diffusers are used to reduce the backpressure and expand the volume of the air by which the air pressure increases, and the flow velocity decreases (Cermak, 1981). The most important aspect of wind tunnels is their capability to replicate the flow complexity of the fluid flow. The aim of any wind tunnel is to attain a parallel steady controlled flow with uniform velocity throughout the test section. It is assumed that the flow is incompressible for such low subsonic speeds.
Calautit et al. (2014), investigated the design and simulation of flow parameters in a closed-loop wind tunnel using ANSYS
Fluent. The Full-Scale Wind Tunnel model with an empty test section and with a block model in the test section was considered for the study. They established the flow quality of the empty test section and validated experimental results with the numerical results. Hence, concluded that numerical results replicate wind tunnel measurements of velocity, turbulence intensity, and pressure coefficient with an error below 10%.
Singh et al. (2014), has designed and constructed a low-cost sub-sonic open circuit wind tunnel model (SWOT). The design parameters considered were boundary layer separation, controlled airflow quality, turbulence intensity, streamline flow, cost-effectiveness, design ease at Mach Number of 0.15. The airflow obtained is of smooth quality with no boundary layer thickening process at the test chamber.
Nguyen Quoc Y (2014) has tested the quality of wind flow created by an open jet type wind tunnel with nozzle area of 1 m x 1 m and the maximum wind speed of 14 m/s. He measured velocity distribution and turbulence at the nozzle by a thermal- couple anemometer. The measurements showed that the turbulence intensity was below two percent while the uniformity of wind speed across the nozzle over ninety-five percent.
Abbaspour and Shojaee (2008) have suggested a new multipurpose wind tunnel with adjustable test section design which could be used either as the environmental, subsonic or climatic wind tunnels. For this purpose, a novel design approach was adopted by adjusting the nozzle of the test section. It could be used as any of the three wind tunnels. The computational fluid dynamics model analyzed the flow properties and flow separation of contractions in computer software. This method is also suitable for existing low-speed wind tunnels with special applications. They presented the numerical results in the paper.
Aboelezz (2019) describes the design and optimization of a low-speed wind tunnel using CFD techniques. Pressure drop calculations are presented and compared between analytical, computational and experimental for different parts of the wind tunnel. They optimized contraction cone using the response surface technique. Results suggest that the pressure drop, and turbulence level were modified as compared to the old wind tunnel.
The aim of the present work included maximum achievable speed, flow uniformity, and verify the flow quality for Alliance University Wind Tunnel. In this study, flow velocity is measured in the test section of the wind tunnel to determine the flow quality and are being compared with numerical results. The full-scale subsonic wind tunnel, considered for this study, is numerically analyzed to validate the experimental results.
-
EXPERIMENTAL SETUP
The open-loop low subsonic wind tunnel facility available at Alliance University is as shown in the fig. 1. The plan length of the wind tunnel is 10 m. This wind tunnel comprises settling chamber, contraction cone, test section, diffuser, and driver section. Settling chamber is at the entrance of the wind tunnel, includes screens and honeycomb-shaped mesh, that straighten out the air to reduce turbulence. It draws the air from the surroundings with the help of a fan placed at the end of the diffuser. Contraction cone, with the ratio of 9:1, increases and streamlines the wind velocity into the test section. With a constant area, the test section has a cross-section of 0.6 m by 0.6 m and a length of 2 m, assumed to have a uniform and steady flow. Diffuser is placed at the end of the test section for the smooth transition of air from low pressure to atmospheric pressure by volume expansion. It facilitates to reduce the wind velocity before it exits the diffuser. The driver section is located at the exit of the diffuser, where the fan is housed. The maximum rotations per minute of the fan are restricted to 1500 as per the design specifications supplied by the manufacturer. It measures static and total pressure using a pitot- static tube connected to a multi-tube manometer.
a)
stationary. The reference pressure of the fluid was taken as atmospheric pressure and the fluid temperature as 25oC. There was no heat transfer through the wall of the domain and the no- slip condition was applied at the tunnel wall. The turbulence model was chosen was K-epsilon (Calautit et al., 2014). Inlet and outlet boundary conditions of the wind tunnel model were defined as velocity inlet and pressure outlet.
Fig. 2. Full cale model of wind tunnel in CATIA
Fig.3. Meshing of Full-scale geometry
-
Bell Mouth
-
Honeycomb
b)
-
Transition Zone
-
Diffuser
4. WIND TUNNEL EXPERIMENT AND TESTING.
The vacant test area of the wind tunnel performed three different checks. Measurement of pressure and velocities for the given fan speed, flow uniformity and velocity profile of the test section.
Initial experiment was performed to calibrate the speed of the test section for the prescribed fan speed. An orifice hole was
-
-
Settling Chamber, and screen sections
-
Contraction cone
-
Test Section
-
Fan Duct
-
Motor and Stand
drilled, one at the entrance of the contraction cone and the other at the entrance of the test section surfaces. These holes were
Fig. 1. a) wind tunnel facility housed at Alliance University b) schematic of
wind tunnel facility
3. NUMERICAL ANALYSIS.
Full-scale wind-tunnel geometry was created using CATIA V5 and 3D model was named as a fluid domain as shown in Fig. 2. Unstructured tetrahedral meshing was generated in the computation domain using ANSYS CFX software. The solution independence from the grid was examined by creating several meshes. Using grid adaption, the meshes were refined enough to get a grid-independent solution (Fig. 3). The number of elements and nodes generated for the refined mesh were 1211774 and 367395. There was no interference in the flow of fluid, so the air at 25oC as a continuous fluid has been selected. There was no buoyancy force acting on the domain and it was
connected to differential inclined manometer to read the differential head. The test section wind velocities were determined by altering the fan speed, through speed controller, from 100 rpm to 1000 rpm with an interval of 100 rpm.
Second experiment was conducted to measure the pressure using a pitot-static tube and evaluating velocities. Wind speed measurements were performed along the centerline of the test section, at intervals of 0.1 m (horizontal) with constant vertical distance (0.3 m), from the top, to determine the uniformity of the flow in the test section. Uniformity was examined at various fan speeds.
Test section velocity measurements were performed between the upper and lower walls of the test section. Pitot-static probe traversed from the upper to lower walls with more intervals near
the wall. With this, the velocity profile of the test section was plotted for three fan speeds.
The above measurements made are key in identifying the flow quality of the test section. The measurements were documented when the temperature of the wind tunnel was maintained at an ambient temperature of 298 K.
-
RESULTS AND DISCUSSIONS
The results presented here are test section wind velocity, pressure variation, measure of streamwise flow uniformity over the test section, and the velocity profile of the test section.
A. Test section wind velocity
a)
a)
b)
b)
Fig.4. (a): Test section velocity vs fan speed (b): validation of test section velocity
c)
Fig. 5. Contours of velocity magnitude at fan speed of a) 500 rpm b) 700 rpm
c) 1000 rpm
Fig. 4(a) displays the test section wind velocity against fan speed. Test section velocity increases with fan speed. The comparison of experimental and computational results is presented in fig. 4(b) for the test section wind velocity. At lower fan speeds the velocity was identical in both computational and experimental results, whilst there was slight variation at higher fan speed because of turbulence. Fig. 5 shows the computational results for selected fan speed.
a)
b)
Fig. 6. (a): pressure vs fan speed (b): velocity vs fan speed
The total pressure in the test section was constant at various fan speeds as shown in fig. 6(a). The velocity at the inlet and outlet of the test section is depicted in fig. 6(b). Because of the skin friction, the boundary layer develops over the surfaces of the inlet section and hence, the flow speed will be lowest at the surface. The wind velocity increases speed as it moves through the contraction cone and becomes the highest as it reaches the test section. The flow velocity continues to be constant through the test section and subsequently decreases in the diffuser. This variation in the experimental result is validated with the computational results as shown in figure 7.
a)
b)
c)
Fig. 7. Velocity contour at inlet, test section and outlet of wind tunnel at fan speed of a) 500 rpm b) 700 rpm c)1000 rpm
Fig. 8(a) shows the uniformity of the flow in the test section. The flow was uniform along the length of the test section measured at three different fan speeds. The flow angularity variation across the test section measured at the centerline for different fan speeds reveals zero degrees. This experimental result holds excellent with computational results as shown in fig. 2. The results in fig. 8(b) shows the vertical wind speed profiles. There was a boundary layer formation near the wall because of no-slip condition. Because of this, the velocities near the wall increased and reached a constant value outside the boundary layer hence the velocity profile is established. This result is validated with the computational analysis are shown in fig. 5 and fig. 6.
a)
b)
Fig. 8. (a): Uniform velocity distribution (b): Test section velocity profile
-
CONCLUSION
-
Our study determined the flow quality of the wind tunnel test section by varying the flow parameters. This paper performed both quantitative and statistical investigations. Numerical model was validated for an empty test section. It was observed that experimental evaluation of the empty test section was in strong alignment with the findings of the computation. The experimental velocity in the test section was observed to be 34.931m/s, while the computational velocity was 35.985m/s at a fan speed of 1000 rpm. Results differed by a meager percentage of 3.017. Test section validation with K-epsilon can replicate mean velocity measurements of wind tunnel with less error. Inlet pressure at the entry of wind tunnel was taken as 101325 Pa and the outlet pressure at the diffuser was found out to be 101300.312 Pa. The results differed by an amount of 24.688 Pa. The small pressure difference between the inlet and the outlet of the wind tunnel results in a large velocity change, as showed.
The uniformity of the flow at the test section centerline is constant along the length of the tunnel with zero-degree flow angularity, which agrees with computational results.
Another flow quality parameter is the velocity profile which is found to be in good agreement with the physics of the flow and the computational results. Outside the boundary layer the velocity is constant for different fan speeds. We conclude that the flow quality of the wind tunnel test section is found to be good. This numerical analysis shows that the k- model closely predicted the test section flow speed, uniformity and velocity profile. Hence, this model can be concluded as the most suitable turbulent model of the study.
REFERENCES
-
Abbaspour, M. and Shojaee, M.N., 2009. Innovative approach to design a new national low speed wind tunnel. International Journal of Environmental Science & Technology, 6(1), pp.23-34.
-
Aboelezz, A., 2019. Low Speed Wind Tunnel Design and Optimization Using Computational Techniques and Experimental Validation. Incas Bulletin, 11(2), pp.3-13.
-
Anderson, J., 2010. Fundamentals of Aerodynamics (In Si Units). 5th ed. Tata McGraw Hill Education Private Limited.
-
Calautit, J., Chaudhry, H., Hughes, B. and Sim, L., 2014. A validated design methodology for a closed-loop subsonic wind tunnel. Journal of Wind Engineering and Industrial Aerodynamics, 125, pp.180-194.
-
Cemak, J., 1981. Wind tunnel design for physical modelling of atmospheric boundary layers. J. Eng. Mech. 107(3), 523642.
-
Ciobaca, V., Melber-Wilkending, S. and Pott-Pollenske, M., 2009. A CFD process chain for simulating open windtunnel test sections. www. machtwissen. de AG.
-
Mehta, R., Bradshaw, P., 1979. Technical notes: design rules for small low speed wind tunnels. Aeronaut. J.R. Aeronaut. Soc., 443449.
-
Nguyen, Q., 2014. Designing, constructing, and testing a lowspeed openjet wind tunnel. Int. J. Eng. Res. Appl, 4(1), pp.243-246.
-
Pettersson, K., 2006. Scaling techniques using CFD and wind tunnel measurements for use in aircraft design (Doctoral dissertation, KTH).
-
Russ, D., 1987. CFD Modeling of Entrance and Exit Geometries of a Wind Speed Accelerator, Master's thesis, University of Louisville, Louisville, KY.
-
Singh, T., Vipul, S., Shaktiman, S., Kumar, S. and Jubin, A., 2014. Design, Analytical Analysis, Instrumentation and Flow Simulation of Sub-Sonic Open Circuit Wind Tunnel Model. International Journal of Modern Engineering Research (IJMER), 4(1), pp.43-52.
-
S, Y., Thimmegowda, H., R, S., Shaik, S. and Goodwill, V., 2019. A Numerical Investigation To Determine And Compare Drag Characteristics Of A Blunt Body With Various Configurations Of Aerospikes At Mach 6. In: 21st Annual CFD Symposium. [online] Bangalore: NAL, p.59.
-
Yang, C.C., 2008. Low Speed Virtual Wind Tunnel Simulation for Educational Studies in Introducing Computational Fluid Dynamics and Flow Visualization (Doctoral dissertation, University of Kansas).