
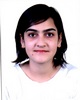
- Open Access
- Authors : Pooja Chokshi , Mihir Hirenbhai Parekh
- Paper ID : IJERTV9IS110131
- Volume & Issue : Volume 09, Issue 11 (November 2020)
- Published (First Online): 11-12-2020
- ISSN (Online) : 2278-0181
- Publisher Name : IJERT
- License:
This work is licensed under a Creative Commons Attribution 4.0 International License
Comparative Studies on Performance of Fiber and Steel Laminated Rubber Isolators
Pooja Harsh Chokshi
Vadodara, India
Mihir Hirenbhai Parekh
Surat, India
Abstract The mechanical characterization of multi-layer rubber isolation bearings was carried out in ANSYS where the reinforcing material is carbon fiber reinforced plastic instead of conventional steel shims. An alternative to the conventional isolator is fiber laminated rubber isolation bearing which proves to be low cost and effective in application. It is of crucial importance to develop such a low-cost and lightweight isolator for its wide range of application as seismic protection method. Thus a square shaped rubber isolator is modeled in ANSYS Mechanical APDL and analysis is carried out. Performance in terms of displacement and stress were evaluated. Also the rubber pads used were of High Damping Rubber which provides extra damping and then a comparison were made between fiber laminated rubber isolator (FRI) and steel laminated rubber isolator (SRI).
Key words: Seismic Isolation, Fiber Laminated Rubber Isolator (FRI), Steel Laminated Rubber Isolator (SRI), High Damping Rubber, ANSYS Mechanical APDL, UBC-97, Yeoh Nonlinear Material Model
Rubber Bearings have Steel Laminated Rubber types and Steel Laminated Rubber types with lead nucleus. Rubber based systems are most widely used. Typically this system consists of alternate thin layers of rubber and steel shims bonded together to provide vertical rigidity and horizontal flexibility. Vertical rigidity assures that Base Isolator will support the weight of structure and horizontal flexibility alters horizontal motions into gentle movement. On top and bottom, the bearing is fitted with steel plates which are used to hook up the bearing to the structure and foundation. Horizontal stiffness of the bearing is controlled by the low shear modulus of elastomer while steel plates provides high vertical stiffness as well as prevent bulging of rubber (3). High vertical stiffness of the bearing has no consequence on the horizontal stiffness. The damping in the bearing is improved by adding fillers such as carbon-black, graphene-sheets, silica, etc.
-
INTRODUCTION
Due to increase in demand of earthquake resisting building, the concept of Lateral-force-resisting element and Seismic Isolation Techniques are most widely used concept in every structure. The three principal types of lateral force resisting elements are shear walls, braced frames, and moment- resisting frames (1). Seismic Isolation is considerably more effective to recruit for structures which have short natural period.
Seismic Isolation System is a simple structural design methodology to lessen the earthquake damage potential. Moreover, Seismic Isolation is a methodology to earthquake resistant design that is based on the convention of reducing the seismic demand rather than increasing the earthquake resistant capacity of the structure. Suitable application of this technology leads to improved performance of structures that will remain elastic during large magnitude earthquakes.
Classification of Seismic Isolation System on the basis of their operation principles are: Active Control System, Passive Control System, Semi-Active Control System and Hybrid System (2). Seismic Base Isolator is a passive control technique which operates without utilization of any external energy source system and can control displacement.
-
Seismic Base Isolator
The basic concept of seismic base isolator is to de-couple the building from its foundation resting on shaking ground. The two basic types of base isolation system are:
-
Rubber Bearings
-
Sliding System
Fig. 1 Laminated Rubber Bearing (3)
Fig. 2 Lead Plug Rubber Bearing (3)
-
-
Hyperelastic Model
Rubber is considered as Hyperelastic materials that are widely used in many applications of industries. The peculiar characteristic of hyperelastic material is its capacity to undergo large strain under small load without permanent deformation in unloading condition. Thus, the stress-strain relationship is high non-linear. Various (4)models used for nonlinear material modeling are:
-
Neo-Hookean Model
-
Mooney-Rivlin Model
-
Yeoh Model
-
Odgen Model
-
Arruda-Boyce Model
-
These models are based on strain energy function which itself is a function of strain invariants (I1,I2, and I3).
The Yeoh model is used wider in application because they are able to perform with simple deformation as uniaxial tension. Also it compute coefficient on basis of single stress-strain data.
-
-
FINITE ELEMENT MODEL
A. Geometric Properties
In order to study the behavior of isolator, isolator was design according to code UBC-97 (5). Following geometric properties are considered:
Table I Geometric Properties of Isolator
-
Meshing
All the layer are created as area and meshed using Quad Free Mesh.
-
Boundary Condition and Load
Nodes are used to impose all boundary conditions and loads acting on model. Bottom nodes are fixed and loads are applied at top node. On top node 101.56tonne load is applied.
-
Analysis
A non-linear static analysis is performed to obtain the stress components and displacement components.
-
-
RESULTS
-
Deformed Shape Results
Parameters
Value
Width
440
Length
440
Thickness of Rubber Layer
12
Thickness of Steel Shim
2
No. of Rubber Layers
12
No. of Steel Shims
11
Thickness of End Steel Plates
25
No. of End Steel Plates
2
Parameters
Value
Width
440
Length
440
Thickness of Rubber Layer
12
Thickness of Steel Shim
2
No. of Rubber Layers
12
No. of Steel Shims
11
Thickness of End Steel Plates
25
No. of End Steel Plates
2
Deformed shaped of conventional isolator i.e. Steel laminated rubber isolator (N40S) and Fiber laminated rubber isolators (N40CFRP) is shown in Fig.3 and Fig.4 respectively.
-
Element Type
All units are in SI (mm)
A sandwich layer of elastomer-reinforcing material- elastomer was modeled in ANSYS Mechanical APDL
15.0. Both the materials were modeled as 4 node structural shell element with six degrees of freedom at each node; SHELL181.It is suitable for layered application for modeling composite shells or sandwich construction. MPC-184 element was given between the interfaces of layers so that load can be transmitted.
-
Material Properties
Steel was modeled as linear isotropic material with the following properties available in literature (4): E=51200MPa; µ=0.3
Elastomers (High Damping Natural Rubber with carbon content 40%) were modeled as hyperelastic material. Hyperelasticity refers to material which experience large elastic strain tha is recoverable. The fundamental behavior of hyperelastic material is obtained from strain energy potentials. Also it has a peculiar characteristic that stiffness changes with the stress level. Non-linear model adopted to model the elastomer is Yeoh 3rd order model. The material parameters used were:
C10=0.2885MPa; C20=-0.0394MPa; C30=0.0074MPa
Fiber material used was Carbon Fiber Laminated Material(CFRP). Fiber reinforcement was modeled as linear orthotropic material with following properties (4): Ex=4400MPa; Ey=4400MPa; Ez=10000MPa
µxy=0.3; µyz=0.25;µzx=0.25
Gxy=10000MPa; Gyz=5000MPa; Gzx=5000MPa
Fig. 3 Deformed Shape of N40S isolator
Fig. 4 Deformed Shape of N40CFRP isolator
-
Displacement Vector Contour
Displacement Vector Solution is shown in Fig.5 and Fig.6 for N40S isolator and N40CFRP isolator respectively. Maximum Displacement in N40S is 0.017737mm and for N40CFRP is 0.0011903mm.
Fig. 5 Displacement Vector for N40S isolator
Fig. 6 Displacement Vector for N40CFRP isolator
-
Stress Contour
Maximum Stress component is shown in Table II for N40S isolator and N40CFRP isolator respectively.
Table II: Maximum Stress Component
Stress Component (MPa) |
N40S |
N40CFRP |
SX |
0.026722 |
0.022645 |
SY |
0.00223 |
0.00184 |
SZ |
0.030259 |
0.02648 |
Stresses developed under vertical load are shown in Fig.7 and Fig.8 for N40S isolator and N40CFRP isolator respectively.
Fig. 7 Vertical Stress Component Contour for N40S isolator
Fig. 8 Vertical Stress Component Contour for N40CFRP isolator
-
DISCUSSION
From the results and contour plots obtained it can be analyzed that reinforcing material is an important material which can make a wide difference in performance of isolator and cost too.
Maximum Stress component is obtained in N40S isolator than the N40CFRP isolator. Vertical Stress developed in N40CFRP and N40S isolators are quite less than the other two component stress. Moreover, vertical stress developed while analysis indicates that maximum vertical stress develops in rubber layer.
Thus, when values compared, it can be analyzed that performance of isolator depends on material property and loading condition.
-
CONCLUSION
From above computation in ANSYS, it can be concluded that for structures such as residential buildings and schools, fiber laminated rubber isolator can be adopted where steel laminated rubber isolator are too expensive. Thus, fiber laminated rubber isolator is relatively low cost and provides effective performance. Also, the performance of isolator can be increased by selecting qualitative material property and proper design.
ACKNOWLEDGMENTS
I am particularly grateful for the assistance provided by Professor Nirav Patel of Navrachana University for always motivating me towards my project. Finally, I would thanks to my mother for always being my support and my co-author Mihir Parekh for helping me in my research work.
REFERENCES
-
Controlling Seismic Effect on the Structure by Optimum Placement of Shear Wall. Pooja, Shah and Nirav , Patel. February 2017, International Journal of Advance Engineering and Research Development. 2348-4470.
-
James M., Kelly and Farzad, Naeim. Design of Seismic Isolated Structures: From theory to practice. s.l. : Wiley & Sons Inc.
-
Base Isolation for Earthquake-Resistant Design. [book auth.] Dr. R.S Jangid. Introduction to Earthquake Engineering. s.l. : NPTEL, 2013,
8. IIT Bombay.
-
Modeling of Fiber-Reinforced Elastomeric Base Isolators. Animesh, Das, Anjan , Dutta and S.K., Deb. Portugal : 15 WCEE, 2012. PROCEEDINGS OF THE FIFTHTEENTH WORLD CONFERENCE ON EARTHQUAKE ENGINEERING.
-
Uniform Building Code. 1997. International Conference of Building Officials. Vol. 2. USA.
-
Gent, Alan N. Engineering with Rubber: How to Design Rubber Components. 3rd. s.l. : Hanser Publication.
-
Gilles, Delfosse. Full Earthquake Protection through Base Isolation System. Structural Dynamics Department, CNRS. France : s.n.
-
Effect Of Thickness Of High Damping Rubber On The Design Of Base Isolator For RCC Building. M. Parvez, Alam, Garima, Arora and Manish, Bhati. I, January 2014, International Journal of Advances in Engineering Research, Vol. 7. 2231-5152.
-
Seismic Response Control using Base Isolation Strategy. S. Keerthana, et al., et al. 4, June 2014, International Journal of Emerging Technology and Advanced Engineering, Vol. 4. ISO 9001:2008. 2250-2459.
-
Behavior of Rubber Base Isolator with Various Shape Factors. Tavio, et al., et al. 2017. International Conference on Construction and Building Engineering. 3rd Proceeding.
-
A Review on Graphene as Fillers in Rubber Nano-Composites. Pooja Sanjaybhai Shah, Mihir Parekh, Krishna Nair. 09, Vadodara : IJERT, September 21, 2019, Vol. 08. 2278-0181.