
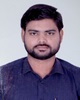
- Open Access
- Authors : Imran Khan , S. Parekar
- Paper ID : IJERTV10IS040240
- Volume & Issue : Volume 10, Issue 04 (April 2021)
- Published (First Online): 30-04-2021
- ISSN (Online) : 2278-0181
- Publisher Name : IJERT
- License:
This work is licensed under a Creative Commons Attribution 4.0 International License
Bituminous Cold Mix Design for Flexible Pavement
1 Imran Khan, 2 Prof. S. Parekar
1 Mtech Student
2 Assistance Prof.
Transportation Engineering Civil Engineering Department
G H Raisoni University Saikhera MP, India
Abstract This paper based on reducing lot of emission of Co2 with explaining the need for sustainable technology innovation as need of road construction. Further, the paper proceeds to explain need of energy conservative, sustainable technology in flexible road construction works, thereby employing the Construction of Green Roads Construction Move on to energy conservative development.. Although India fall NON-ANNEX B party without binding targets of Carbon emission by Kyoto Protocol(1992) as per international treaty of United Nation Framework Convention on climate change(UNFCCC), but we can reduce the carbon foot print with the help of ANNEX-I (Industrialized or developed) Countries and can extract new advance technology from these countries by emission trading scheme of UNFCCC to reduce carbon dioxide, because global warming in worldwide increasing geographically. Cold mix construction is based on not only reducing pollution but also labour friendly construction because labour will not deal with high temperature of mix during construction works, cold mix technology is a energy saving technology which save lot of fuel for preparation of hot mix in case of hot mix design, cold mix found a revolutionary road construction materials specially for rural area, hilly area and where plant setup are problematic for hot mix design, labourers of North-East in general (hilly area where plant set up of hot mix and transportation of material become problematic) and Rural area in particular. Today under scheme of Pradhan mantri gram sadak yojna (PMGSY) lot of rural road and hilly roads are running and constructed as well by Cold mix Technology
Keywords Pollution in Road Construction, Cold Mix Concept, Road Construction Labourers, Northeast India, Rural India,Co2 Emission, Sustainable Roads construction.
-
INTRODUCTION
Construction of Flexible pavements contributed Majority in Indian road network including airfield and rural roads,In Cold mix technology the mix is produce at ambient temperature with water emulsion mixture in aggregates mix, these mix gain strength when water evaporate and percolate into ground during curing process. Although in Hot mix technology which is a very conventional method for road construction, has structurally satisfied the performance requirements over many years. Hot mix involve : heating of binder and aggregate, mixing, tack coating, laying of mix followed by the compaction process everything done at Elevated temperature in a range of 120ºC to 165ºC temperature. Though performance wise this has been the most suitable for pavement structures, but their high use have several drawbacks like environmental degradation, high energy consumption, increase in carbon footprint, low output for mix production,
low laying work in rains and cold weather, limited construction period in a year, oxidant hardening of binder, health and safety hazard to labour. Besides this, in some North and North Eastern parts of India like Jammu and Kashmir, Assam, Manipur, Meghalaya, Arunachal Pradesh and others, rural road projects involving several lakhs and crore of rupees are beyond time. Due to topographical and weather constraints, it is difficult to work with hot mix technology in such hilly regions, heavy rainfall and forest zones. So, it is desirable to find out a suitable alternative for hot mix technology these alternative fall in cold mix technology
-
MATERIAL USED
-
Aggregates
Black Basalt aggregates of 20 mm, 10mm used as coarse aggregates, crushed sand as fine aggregates and Lime as filler used Following are the sources of materials
Table no. -01
-
Testing on aggregates- Before conducting cold mix design material suitability checked then mix design conducted, Following Testing conducted on aggregates-
-
Impact value,
-
Water absorption and Specific gravity
-
Durability by soundness.
-
Sand equivalent value, only for fine aggregate.
-
Combine Flakiness & Elongation
-
Coating test was conducted of water emulsion mixture with aggregates including filler to determine coating ability of aggregates visually.Table no 02 show the result of aggregates testing and their specifications.
Table no. -02 Aggregates Testing Results
Property
Test
Test Result
Specification as per IRC SP 100:2014
Method of Test
Cleanliness(Dust)
Grain Sieve Analysis
0.00%
Max 5% Passing
0.075 mm Sieve
IS 2386 P-1
Particle Shape
Combine Flakiness and Elongation Test
25.63%
Max 35%
IS 2386 P-1
Strength
Aggregate impact value
12.36%
Max 27%
IS 2386 P-4
Durability
Soundness by Naso4 or Mgso4
3.63 % By Naso4 and 4.78% by Mgso4
Max 12% By Naso4 and max 18% By Mgso4
IS 2386 P-5
Water Absorption
Water Absorption
1.05%
Max 2%
IS 2386 P-5
Stripping value
Coating and stripping
100%
Minimum reatained Coating 95%
IS 6241
water sensitivity
Retained Tensile Strength
64.00%
Min 80%
AASHTO T 283
Fine Clay particles
Sand Equivalent value
82.63%
Min 50%
IS 2720 P-37
C.Testing on Bitumen Emulsion- An emulsion is a dispersion of small droplets of one liquid in another liquid. Emulsions can be formed by any two immiscible liquids, but in most emulsions one of the phases is water. Bitumen emulsion is a liquid product in which a substantial amount of bitumen is suspended in a finely divided form in water in presence of emulsifiers. The bitumen droplets range from 0.1 to 20 micron in diameter. Standard bitumen emulsions is a brown liquid and contain 40% to 75% bitumen, 0.1% to 2.5% emulsifier, 25% to 60% water plus some minor components.in this research work bitumen emulsion of slow setting-1 grade (SS-1) taken as binder for cold mix design,these emulsion tested on laboratory before making cold mix specimen for design mix, in table no.03 shown the parameters and testing results of SS-1 grade bituminous emulsion.
Table no.03 -Emulsion Testing Results
Sr. No.
Test Parameter
Method of Test
Result
Specification as per
IS 8887 :2018
SS-1
SS-1
(i)
Viscosity by saybolt furol Viscometer,Seconds
1)At 250C
ANNEX A of IS 3117 :2004
40.3
20-100
2)At 500C
–
–
(ii)
Coagulation of emulsion at low Temperature
ANNEX C of IS 8887 :2018
Nill
Nill
(iii)
Coating ability and water resistance
1) Coating, dry aggregates
ANNEX F of IS 8887 :2018
Good
–
2) Coating , After spraying
Good
–
3) Coating , wet aggregates
Good
–
4) Coating , After spraying
Good
–
(iv)
Miscibility with water
ANNEX H of
IS 8887 :2018
Immiscible
Immiscible
(v)
Test on residue
1) Residue by evaporation %
ANNEX J of
IS 8887 :2018
–
–
2) Penetration 250C/100g/5sec(1/100mm)
IS 1203
–
–
3) Ductility 270C in cm
IS 1208
–
–
4) Solubility I tricholoethylne,% by mass
IS 1216
98.83
Min 98
-
-
METHOD OF COLD MIX
-
The bituminous binders used in cold mixes are emulsified and hence in liquid form. So, it can be applied at relatively low temperatures compared to that of hot mix. Till now there is no universally accepted cold mix design method and therefore no thumb rule that can be followed. Marshall method has been popularly used to design cold mixes.and Manual of Indian road congress IRC SP 100- 2014 recommended Marshall Method, Manual of Ministry of Road Transport and Highways (MORTH, 2013) 5th Rev.,(Government of India) specification for Road and Bridge Works (Fourth Revision) introduced the procedures for bituminous cold mix as per MS14. The design guidelines were based on those of Asphalt Institute Manual Series 14 To determine the Optimum Residual Asphalt Content (ORAC), Determination of optimum pre-wetting water content(OPWC) is important factor which coat all aggregates with bitumen emulsion visually and then evaporate from mix at ambient temperature, after finding OPWC, optimum residual asphalt content(ORAC) find keeping OPWC constant by soak stability test which give optimum Total Liquid content (OTLC) The design
-
In the study, dense (SDBC) cold mixes was prepared. Selection of materials and aggregate gradations was as per specifications specified later. For compaction of cold mixes,Marshall compaction Methods was followed as per MORTH (2013) & IRC SP 100 (2014) specification procedures are summarized Below by flow chart –
As per MS 14 (1997) method Determination of Aggregate gradation (As per specification for optimum blending)
IRAC and IEC (As per formula) OPWC (Coating Test)
OTLC (Dry Stability Test)
ORAC (Dry Stability and Soaked) (Stability Test for each RAC)
a)Determination of Aggregate Gradation:
This simply follows standard specifications for aggregate gradation selection as per IS 2386 P-1, Percentage passing of aggregates of each size sieve result are shown in table no.04
Table no-04 Gradation of aggregates and graph for SDBC mix
%Blending
IS SIEVE
(mm)
Coarse
Fine
% for blending
Total % of Passing
MID LIMIT
LIMIT AS PER IRC SP:100 -2014
TABLE -7.4
%Passing
20mm
10mm
Stone Dust
Filler (Lime)
20mm
10mm
Stone Dust
Filler (Lime)
45.00%
18.00%
35.00%
2.00%
100.00%
Lower Limit
Upper limit
13.20
100.00
100.00
100.00
100.00
45.00
18.00
35.00
2.00
100.00
100.00
100
100
9.50
86.98
100.00
100.00
100.00
39.14
18.00
35.00
2.00
94.14
95.00
90
100
4.75
0.32
36.45
89.63
100.00
0.14
6.56
31.37
2.00
40.08
43.00
35
51
2.36
0.00
0.00
91.63
100.00
0.00
0.00
32.07
2.00
34.07
31.50
24
39
1.18
0.00
0.00
62.31
100.00
0.00
0.00
21.81
2.00
23.81
22.50
15
30
0.300
0.00
0.00
33.63
100.00
0.00
0.00
11.77
2.00
13.77
14.00
9
19
0.075
0.00
0.00
6.97
100.00
0.00
0.00
2.44
2.00
4.44
5.00
2
8
Gradation of aggregates Blending graph
a)Determination of Initial Residual Asphalt Content (IRAC) and the Initial Emulsion Content (IEC):
Initial Residual Asphalt Content (IRAC) is calculated utilizing an empirical formula by IRCSP:100-
IRAC = (0.05A+0.1 B + 0.5 C) × (0.7) ……………………. (i)
Where A is the percentage of aggregate retained on sieve 2.36 mm, B is the percentage of aggregate passing sieve 2.36 mm and retained on 0.075 mm and C is the percentage of aggregate passing 0.075 mm.
-
Coating Test and Determination of optimum pre-wetting water content (OPWC):
Using the IEC value coating test is carried out by mixing dry aggregates and filler with varied amount of water. After the pre-wetting of aggregates the asphalt emulsion is added and then mixed for about 2 to 3 minutes until the uniform coating is obtained. The optimum pre-wetting water content (OPWC) that gives the best asphalt coating on the mineral aggregates (in which the mixture was neither too sloppy nor too stiff) is determined. The degree of coating should not be less than 50
% by visual observation.
-
Dry Stability Test and Determination of Optimum Total Liquid Content at Compaction (OTLC):
Utilizing the IEC, the mix is compacted at the predetermined compaction level (50 Marshall blows on each side of the sample). The loose mixtures are compacted at OPWC and then at PWC (pre-wetting water content) with 1 % increasing steps from OPWC. The samples are kept for one day in their moulds after compaction and thereafter extruded and kept for one day in an oven at 40ºC. Then they are removed from the oven and stored at room temperature for one day. After that the samples are tested for Marshall Stability at room temperature and the results obtained are referred as dry stability. This test gives the OTLC at which the dry stability of the sample is maximum. Where OTLC is the summation of liquid content of IEC and pre-wetting water content at maximum dry stability.
-
Soaked Stability Test and Variation of Residual Asphalt Content (RAC):
By maintaining a constant OTLC value, the RAC is varied in a range of 7 to 10 % emulsion content (EC) value with
0.5 % increment in RAC. Specimens are mixed, compacted at each of these RAC values. Then the same curing process is followed up to the completion of the oven curing as explained above in case of dry stability test. The dry samples are then water conditioned (capillary soaking). In this procedure half the thickness of each compacted specimen is soaked in water at room temperature for 24 hour. The specimen is then inverted and the other half is soaked for next 24 hour. The samples are subsequently towel dried and tested for Marshall Stability at room temperature. The Marshall Stability test results obtained are referred as soaked stability. At this condition the samples do not achieve full curing stage as contained some amount of water.
-
Determination of Optimum Residual Asphalt Content (ORAC):
ORAC is determined by optimizing the parameters such as soaked stability, air void, flow value for soaked samples of 15 all residual asphalt content (RAC) variation. The main parameter considered is the maximum soaked stability while all other parameters should meet the CMA design requirement as per MORTH (2013 5th Rev.) specification at the proposed ORAC. In case either the soaked stability or the air void result is found to be inadequate, the compaction level should be increased to meet the required target.
-
Determination of Retained Stability:
Retained stability is the ratio of soaked stability to dry stability. Both soaked stability and dry stability are considered at ORAC only. Maintaining the OTLC value, the dry stability of the mixture is determined at ORAC only. The maximum stability loss is 50 %, hence, the minimum retained stability is 50 % at the proposed ORAC.
-
Method and Level of Compaction:
-
Medium compaction level: The compaction effort generated when applying 50 blows to each end of the sample using a Marshall hammer as per (IRC SP 100).
-
Heavy compaction level: The compaction effort generated when applying 75 blows to each end of the sample using a Marshall hammer.
-
-
RESULTS
-
Design Justifications and ORAC Determination:
Samples were compacted by Marshall method after mixing the coarse aggregate, fine aggregate and Lime as filler material according to the adopted aggregate gradation given in table 04 to produce dense graded graded cold mix respectively. For cold mix IRAC values was considered. One value was chosen according to the empirical formula and another value was taken arbitrarily. By using these two IRAC values two sets of mixes were produced for each gradation.
-
Dense graded cold mixes(SDBC)
As per the adopted design procedure samples of aggregates, filler and emulsion (SS-1) taken for analysis were produced by Marshall compaction. For suitability design of mix samples taken from different sources to determine conformity testing, their testing parameters, result and specifications shown in table 02 and 03 respectively, the optimum composition found based on initial residual asphalt content(IRAC) by arbitrary value and by empirical formula shown in table 05
Table 05 Optimum compositions of dense graded cold mixes
IRAC by Empirical formula
IRAC by arbitrary value
IRAC = 5.94 %
IRAC = 6.0 %
IEC = 3.50 %
IEC = 4.0 %
OPWC =4.00 %
OPWC =5.0 %
OTLC = 7.45 %
OTLC = 8.05 %
ORAC = 4.80 %
ORAC = 4.70 %
Soaked Stability = 5.70kN
Soaked Stability = 3.16kN
Dry Stability 8.90kN
Dry Stability = 3.69kN
-
Determination of OTLC values:
– by empirical formula
IRAC=(0.05A+0.1B+0.5C)×(0.7)
=(0.05×65.93+0.1×29.63+0.5×4.443)x0.7=5.94%
2.080
2.00 3.00
4.00
PWC %
5.00 6.00 7.00
2.080
2.00 3.00
4.00
PWC %
5.00 6.00 7.00
2.320
2.320
2.240
2.240
IRAC –
Constant- 5.94%
IRAC –
Constant- 5.94%
2.160
2.160
Dry Density(gm/cc)
Dry Density(gm/cc)
Graph of PWC and dry density of mix by IRAC formula
-by arbitrarily value
Determination of OTLC by arbitrarily value, in which varying amount of emulsion added having constant value of pre-wetted emulsion content, Generally, value obtained by arbitrarily value is greater than of value obtained by empirical formula as mentioned in table no. 05 in which result obtained of OPWC is 4.00% and by arbitrarily value OPWC is 5.0%.
2.240
2.160
2.080
2.000
1.920
1.840
1.760
2.00
IRAC –
arbitrerily value
2.240
2.160
2.080
2.000
1.920
1.840
1.760
2.00
IRAC –
arbitrerily value
3.00
3.00
4.00
PWC %
4.00
PWC %
5.00
5.00
6.00
6.00
7.00
7.00
Dry Density(gm/cc)
Dry Density(gm/cc)
Graph of PWC and dry density of mix by arbitrarily value
-
Determination of ORAC values:
by empirical formula
8.00
7.00
6.00
5.00
4.00
3.00
2.00
1.00
2.00 3.00 4.00 5.00 6.00 7.00 8.00
% RAC
8.00
7.00
6.00
5.00
4.00
3.00
2.00
1.00
2.00 3.00 4.00 5.00 6.00 7.00 8.00
% RAC
Stability in( KN)
Stability in( KN)
ORAC determination by stability and RAC Graph(Empirical formula)
-
Determination of ORAC values:
by arbitrarily value
6.00
5.00
4.00
3.00
2.00
1.00
1.00 2.00 3.00 4.00 5.00 6.00 7.00 8.00
% RAC
6.00
5.00
4.00
3.00
2.00
1.00
1.00 2.00 3.00 4.00 5.00 6.00 7.00 8.00
% RAC
Stability in( KN)
Stability in( KN)
ORAC determination by stability and RAC Graph(Arbitrarily value)
-
Graphical Representation of mix parameters result of semi dense bituminous concrete (SDBC) as mentioned in table no.05
Table no, 05 Design Parameters of cold mix
18.00
18.00
17.00
17.00
16.00
16.00
15.00
3.50
4.50
5.50
6.50
15.00
3.50
4.50
5.50
6.50
RAC
RAC
Flow in mm
Flow in mm
% VMA
% VMA
% VMA and RAC Graph
6.0
5.0
4.0
3.0
2.0
1.0
0.0
3.50
4.50
5.50
6.50
6.0
5.0
4.0
3.0
2.0
1.0
0.0
3.50
4.50
5.50
6.50
RAC
RAC
Flow value (mm) and RAC Graph
12.00
10.00
8.00
6.00
4.00
2.00
12.00
10.00
8.00
6.00
4.00
2.00
3.50
4.50
5.50
6.50
3.50
4.50
5.50
6.50
RAC
RAC
% Air Voids
% Air Voids
Mix Density(gm/cc)
Mix Density(gm/cc)
air void and RAC Graph
2.320
2.240
2.160
2.080
2.000
1.920
3.00
4.00 5.00
RAC
6.00
7.00
2.320
2.240
2.160
2.080
2.000
1.920
3.00
4.00 5.00
RAC
6.00
7.00
Mix Density (g/cc) and RAC Graph
Design Parameter
Results
Specification as per Morth 5thReivision
Marshall Stability
8.9
2.2 KN
Flow value
3.2
Min. 2 mm
Retained Stability
64
Max 50%
Emulsion Content
9.53
8-10%
Air Voids
4.23
3-5%
VMA
18.63
Min 14%
Design Parameter
Results
Specification as per Morth 5thReivision
Marshall Stability
8.9
2.2 KN
Flow value
3.2
Min. 2 mm
Retained Stability
64
Max 50%
Emulsion Content
9.53
8-10%
Air Voids
4.23
3-5%
VMA
18.63
Min 14%
Design parameters of cold mixes at 50 blows of compaction Table no.-06
Effect of Compaction Level Table no-07 Dense graded cold mix (SDBC)
Design Parameter
50 blows Compacti on level
75
blows Compac tion level
Specification as per Morth 5thReivision
Marshall Stability
8.9
13.62
2.2 KN
Flow value
3.2
3.69
Min. 2 mm
Retained Stability
64
74
Max 50%
Emulsion Content
9.53
9.53
8-10%
Air Voids
4.23
4.01
3-5%
VMA
18.63
17.54
Min 14%
Effect of Additives – As majority of cement use as a filler in bituminous mix but in this design lime powder used as filler as a substitute of cement which is naturally found and give equivalent water sensitivity resistance and same properties of cold mix parameter test results.
-
-
CONCLUSION
-
From the limited study it is observed that initial stability of the mix is dependent on optimum total liquid content (OTLC) of the compacted mix. At same binder content higher the total liquid content, greater is the curing time to obtain full strength of the mix. Although achieving OTLC is difficult for field application, it may be applied for laboratory procedures to avoid delay in work process. This concept has supported the adopted design procedure of the present study.
-
Increment in the compaction level is found not to be much effective in decreasing the air voids in cold mixes rather it increased the stability loss value.
-
Lime can be used as filler material in cold mix design without affecting volumetric parameters of mix.
-
A very precise quality control require in the field as compare to laboratory design of cold mix, there is chance of temperature variation in field as compare to laboratory ambient temperature condition which effect OTLC.in which suitable correction applied to compensate actual OTLC required on the field.
-
-
REFERECES
-
Asphalt Institute Manual Series No.14 (MS-14) (1997), Asphalt cold mix manual (Third Edition).
-
MORTH (2013), Specifications for Road and Bridge Works (Fifth Revision), Ministry of Road Transport and Highways, New Delhi.
-
Cold Mix Technology in Construction and maintenance of Roads Using Bitumen Emulsion (IRC: SP: 100-2014).
-
IS 1202 (1978), Indian standard methods for testing tar and bituminous materials (First Revision), Bureau of Indian Standards, New Delhi.
-
IS 2386: Part – I (1963), Methods of Test for Aggregates for Concrete (P-I): Particle size and shape, Bureau of Indian Standards, New Delhi.
-
F IS 2386: Part – III (1963), Methods of Test for Aggregates for Concrete (P-III): Specific Gravity, Density, Voids, Absorption, Bulking, Bureau of Indian Standards, New Delhi.
-
IS 2386: Part – IV (1963), Methods of Test for Aggregates for Concrete (P-IV): Mechanical properties, Bureau of Indian Standards, New Delhi.
-
IS 8887 (2018), Bitumen emulsion for roads (cationic type) – Specification (Second Revision), Bureau of Indian Standards, New Delhi.
-
Oke Oluwaseyi Lanre (2010), A Study on The Development of Guidelines for The Production of Bitumen Emulsion Stabilize RAPs for Roads in The Tropics, Unpublished Ph.D. Thesis, University of Nottingham.
-
Pundhir N.K.S (2012), Construction Of Rural Roads With Cationic Bitumen Emulsion Based Cold Mix Technology, Central Road Research Institute, New Delhi.
-
Suliman M. and Awwad M. (2000), The use of oil shale aggregates as a pavement material, Internal Rep., Amman College for Engineering Technology and Al-Balqa Applied Univ., Jordan Engineers Assoc., Amman, Jordan.
-
Studies on Cold Bituminous mixes with NanoTac Additive Prof. Harish J Kulakarni1 , Mohan Kumar M N , Basavarajappa M H.
-
Designing Cold Mix Asphalt (CMA) and Cold-In-Place Recycling (CIR) Using SUPERPAVE Gyratory Compactor,by Murugaiyah Piratheepan,University of Nevada, Reno.
-
Emulsion cold mix asphalt in the UK: A decade of siteand laboratory experienceDennis DayIan Michael LancasterDougie McKay.