
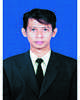
- Open Access
- Authors : Yayang Permadi , Harus Laksana Guntur
- Paper ID : IJERTV11IS070227
- Volume & Issue : Volume 11, Issue 07 (July 2022)
- Published (First Online): 02-08-2022
- ISSN (Online) : 2278-0181
- Publisher Name : IJERT
- License:
This work is licensed under a Creative Commons Attribution 4.0 International License
Application of Modal Analysis to Modify Chassis Structure using Strain Energy Density
Yayang Permadi
Mechanical Engineering
Sepuluh Nopember Institute of Technology Surabaya 60111, Indonesia
Harus Laksana Guntur
Mechanical Engineering
Sepuluh Nopember Institute of Technology Surabaya 60111, Indonesia
Abstract The performance assessment of a vehicle structure relates to its strength and rigidity to achieve a level sufficient to support its own load and weight. In vehicle dynamic system modeling, the model can be simplified such as mass, spring and damper. Finite element analysis produces algebraic equations simultaneously as a solution to a structural problem that refers to determination of displacement at each node. Modal analysis generalizes displacement assuming there is no force on the damper in the eigenvalue problem so that dynamic characteristics in the structure can be obtained as natural frequencies and mode shapes. Information about the amount of mass in a structure is known by the participation factor in each mode. Structural modification is done by utilizing elastic materials to store strain energy. The strain energy distributed in the structure per unit volume is known as the strain energy density. An unknown mass was added to strengthen the chassis structure. To determine the natural frequency of the vehicle chassis structure, modal modeling has been done on Ansys Mechanical. Finally, the study evaluates the strain on the chassis and modifies it to obtain new results with a stronger chassis.
Keywords Chassis structure, Three-wheeled electric vehicle, Modal analysis, Strain energy density and Modified structure.
-
INTRODUCTION
The vehicle chassis structure is a resonant system with an unlimited number of natural frequencies. Modal analysis represents the behavior in the resonance region and all parameters can be determined experimentally3. so that the performance of the vehicle chassis structure can be achieved by minimizing unwanted vibrations1. Data from modal analysis can be used as an analysis of a system4. Such as structural modification5, prediction of structure response6 or detection of structural damage7. Structural modifications make changes to the mass, stiffness or damping of the system. This physical change will certainly change the dynamic behavior of the system. By using the system modal model, simulation and prediction can be performed. Physical changes can be made by adding mass to a part of the system, hence the existing modal model and mass together should predict the new modal model after structural modification.
Structural modification technique as an analytical application is used to determine the effect of changes in the physical parameters of a structural system on its dynamic properties in the form of natural frequency and mode shape. Structural modification theory uses a mass and stiffness matrix so that changes in physical parameters are projected into changes in the mass and stiffness properties of the system. For a simple mass-spring system, the actual physical parameters are the mass and stiffness values of the physical elements. For continuous systems such as cantilevers, this parameter can be either the thickness or the length of the beam section so that its
changes can affect the mass and stiffness properties. For real structures such as automobile chassis, the physical parameters can be changes in mass and local stiffness caused by changes in cross-sectional area or by additional welded components between two locations. So that structural modification does not have to depend on knowing the mass and stiffness matrices2.
The elastic behavior of a material is a form of the material's effort to store strain energy or potential energy. The external force will be equal to the stored strain energy. In expressing strain energy there are several assumptions such as a material must be elastic, stress is at a proportional limit and loads are applied gradually. If the strain energy is distributed evenly within the material, then the strain energy per unit volume is known as the strain energy density. Most structures are designed with the expectation that the material will remain within the elastic range assuming the stresses in the material reach the elastic limit. As long as the load is below the elastic limit, all strain energy is restored and there is no permanent deformation. Thus the material acts as an elastic spring that stores and releases energy when a load is applied and removed.
In this study, the mode shape generated by modal analysis is considered to be participatory so that the strain energy density of the chassis structure can be used as a modification idea to add mass or connection with the result of increasing the strength of the structure.
-
METHOD
-
Design
Three-wheeled electric vehicle design was generated by Solidwork and imported into Ansys Mechanical, the material properties and boundary conditions are specified in Table I and Fig 1.
Fig. 1. Magnetic field distribution of in-wheel motor
There are 3 components of plate, pipe and profile with two types of materials. Plates and pipes use 6061 T6 aluminum material, while profiles use 6063 T5 aluminum material.
Material Properties
6061 T6
6063 T5
Density (g/cm3)
2.7
2.7
Ultimate strength (Mpa)
310
185
Yield strength (Mpa)
275
145
Elastis modulus (Gpa)
69
69
Poissons ratio (N/A)
0.33
0.33
Bulk modulus (GPA)
69
69
Shear modulus (Gpa)
26
26
TABLE I. MECHANICAL PROPERTIES OF MATERIAL
The participation factor identifies the amount of mass moving in each direction in the mode shape. This information is used to eliminate the number of mode shapes.
Mode
Frekuensi (Hz)
Deformation (mm)
Ratio
X
Direction
Y
Direction
Z
Direction
1
54.602
32.385
0.84789
0.00006
0.00015
2
72.296
56.294
1.00000
0.00062
0.00037
3
75.351
32.213
0.00037
0.90680
1.00000
4
79.231
50.154
0.68916
0.00014
0.00002
5
97.263
48.5
0.61770
0.00024
0.00075
6
120.67
25.347
0.00005
1.00000
0.22612
7
128.94
39.506
0.00119
0.71659
0.83122
8
149.04
62.656
0.14830
0.00050
0.00095
9
159.83
66.179
0.00051
td>
0.05361
0.00332
10
163.4
38.964
0.00006
0.65466
0.49913
TABLE II. PARTICIPATION FACTOR
Boundary conditions of the modal simulation only use fix supports placed on the front and rear swing arm mountings and suspensions. There is no effect of gravity or force on modal analysis. Modal analysis settings use 10 modes maximum by generating mode shapes based on frequency results. The value of deformation in the structure can be obtained based on the mode shape. The result of the deformation of the mode shape can be used to evaluate the component because it displays a certain dynamic behavior.
-
Modal Analysis
Modal analysis is performed on all parts of the chassis structure with 10 selected modes. Structural deformation was observed based on the frequency value. Chassis strength is increased by identifying the most influential components.
Modification of the structure is done by identifying the most influential components. There are several procedures used to determine the modification target for each mode shape.
-
Modal analysis to get natural frequency and mode shape
-
Participation factor to identify significant mode
-
Strain energy density to provide design change ideas
The first step by using modal analysis to determine the natural frequency and mode shape of the chassis structure. The structure can be modeled using a linear dynamic system, the mathematical model consists of a mass matrix [M] and a stiffness matrix [K]. This matrix corresponds to the natural frequency r and the mode shape {}r (r = 1, 2, . . . , N) of the eigenvalue equation
([] 2[]){} = {0} (1)
If the modification of the structure is quantified by changes
in the mass and stiffness matrices which are denoted respectively as [M] and [K], hen the eigenvalue equation of the system is modified to
([] + [] 2[] + []){} = {0}, = 1, 2,. , (2)
Modification matrices characterize mass and stiffness
modifications in the spatial model. Modifications are not made to the matrix but to physical components or parameters such as beam elements in the structure8.
The value of deformation in the structure can be obtained based on the mode shape. The result of the deformation of the mode shape can be used to evaluate the component because it displays a certain dynamic behavior. The natural frequency modification target is determined by selecting the ratio of the participation factors close to 1 that may resonate6.
The modulus of elasticity is the formula for elastic strain energy. When a force is applied to an object, the object changes shape. And if force is no longer applied, the object regains its dimensions and all strain energy is released. The elastic behavior of a material is a form of work in the material to store strain energy.
= 1 (3)
2
If the strain energy is evenly distributed in the object, then
the strain energy per unit volume is known as the strain energy density. Its value is given by
= 1 (4)
2
The location of the strain energy in the structure becomes
the idea for the modification model.
-
-
RESULTS AND DISCUSSION
Structural modification technique as an analytical application is used to determine the effect of changes in the physical parameters of a structural system on its dynamic properties in the form of natural frequency and mode shape.
-
Original Structure
Based on the participation factor data, it can be concluded that there are five modes that affect the structure shown in Table III.
TABLE III. PARTICIPATION FACTOR RATIO
Mode
Direction
1
X
2
X
3
Y
Z
6
Y
7
Y
Z
The third step is to give the output energy per volume of the selected mode shape.
Fig. 2. Mode shape 1
Mode shape 1 provides three modification points. In this area, the contours with the maximum mass amount are experienced. The direction of movement is in accordance with Table III for X direction.
Fig. 3. Mode shape 2
In mode shape 2, mass will be added in the X direction.
Fig. 4. Mode shape 3
Modifications were made by changing the components in modes 3.
Fig. 5. Mode shape 6
In mode shape 6 there is a limitation that the long members come from aluminum profiles. So for that area, an additional plate covering the area of the cargo base is added.
Fig. 6. Mode shape 7
TABLE IV. NATURAL FREQUENCY AND STRAIN ENERGY DENSITY OF ORIGINAL STRUCTURE
Mode
Frekuensi (Hz)
Strain Energy Density (J/m3)
1
54.602
81.946
2
72.296
128.21
3
75.351
61.117
6
120.67
100.59
7
128.94
713.04
In the Table IV, the value of the strain energy density in each mode on the natural frequency of the vehicle structure is shown.
-
Structure Modification
The cases that occur in mode shape 1, 3 and 7 are the same, namely in the driver's seat and the steering wheel. But the mode shape 2 and 6 have a different case. In mode shape 2 is located on the cross members in the middle of the chassis structure while in mode shape 6 is located along the connection of long members and trust members.
The results of the overall structure modification are shown in Fig 8. With the new structure, re-testing is carried out to determine the possibility of the structure resonating in each mode shape.
Fig. 7. Modification based on mode shape
TABLE V. PARTICIPATION FACTOR STRUCTURE MODIFICATION
Mode
Frekuensi (Hz)
Deformation (mm)
Ratio
X
Direction
Y
Direction
Z
Direction
1
43.104
48.669
-0.006
0.000
0.000
2
52.893
77.296
0.000
0.032
-0.004
3
53.869
62.479
-0.004
0.001
0.000
4
57.384
77.055
0.000
0.046
-0.004
5
67.772
29.227
0.047
0.000
0.000
6
84.272
50.388
0.012
0.000
0.000
7
86.845
29.533
0.000
-0.054
0.031
8
122.53
26.899
0.000
-0.038
-0.012
9
129.08
33.627
0.000
-0.021
-0.019
10
130.95
59.533
0.038
0.000
0.000
Fig. 8. Structural modification
In the participation ratio, there is no significant change in mass in the direction of the XZ axis with a value of less than
-
So it can be stated that the modification of the chassis structure has achieved its goal and has sufficient strength.
-
-
-
CONCLUSIONS
The chassis structure has been tested according to its participation factor and has been analyzed with 10 mode shape.
Modification of the chassis structure using modal strain energy where this strategy utilizes the results of the modal analysis to continue analysis. In the original chassis, the frequency range is 54,602 Hz to 163.4 Hz in mode 1 and mode 10. While in the modified structure, the frequency value is in the range of 43.104 Hz to 130.95 Hz in mode 1 and mode 10. This value is affected by mass so that it has an impact on stiffness in the chassis structure. And not found that the form of the mode that significantly affects the resonance of the structure on the participation factor.
ACKNOWLEDGMENT
This work has been done in Labs. Vibration Engineering and Automotive Systems and I would like to thank all my friends for contributing fruitful discussion.
REFERENCES
[1] Chen, Xiaolin, and Yijun Liu. Finite element modeling and simulation with ANSYS Workbench. CRC press, 2018. [2] Fu, Zhi-Fang, and Jimin He. Modal analysis. Elsevier, 2001. [3] Ahirrao, Nilesh, and Santosh Bhosle. "To Evaluate Chassis Frequency Harmonics of Vehicles by Modal Analysis and Measurement." In Recent Trends in Mechanical Engineering, pp. 685-693. Springer, Singapore, 2020. [4] Balaguru, S., Elango Natarajan, S. Ramesh, and B. Muthuvijayan. "Structural and modal analysis of scooter frame for design improvement." Materials Today: Proceedings 16 (2019): 1106-1116. [5] Çakar, Orhan. "A method for shifting natural frequencies of a dynamic system to desired values with concentrated mass modifications." Journal of Vibroengineering 20, no. 1 (2018): 1-12. [6] Bonisoli, Elvio, Domenico Lisitano, Luca Dimauro, and Lorenzo Peroni. "A Proposal of Dynamic Behaviour Design Based on Mode Shape Tracing: Numerical Application to a Motorbike Frame." In Dynamic Substructures, Volume 4, pp. 149-158. Springer, Cham, 2020. [7] Christensen, Jesper, and Christophe Bastien. Nonlinear optimization of vehicle safety structures: Modeling of structures subjected to large deformations. Butterworth-Heinemann, 2015. [8] He, Jimin. "Structural modification." Philosophical Transactions of the Royal Society of London. Series A: Mathematical, Physical and Engineering Sciences 359, no. 1778 (2001): 187-204. [9] Hasan, Mohammad, and Taqi Abo Al-kibash. "Simulation and Analysis of a Vehicle Chassis by ANSYS Program." (2019).