
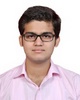
- Open Access
- Authors : Ayush Verma
- Paper ID : IJERTV10IS050289
- Volume & Issue : Volume 10, Issue 05 (May 2021)
- Published (First Online): 27-05-2021
- ISSN (Online) : 2278-0181
- Publisher Name : IJERT
- License:
This work is licensed under a Creative Commons Attribution 4.0 International License
Utilization of Recycled Plastic Waste in Road Construction
Ayush Verma1
1P.G. Student, Mewar University, Chittorgarh, Rajasthan, India
Abstract – The use of recycled plastic waste in construction of a pavement helps in economic savings and conservation of natural resources as well as solves problem of disposal of large amount of waste materials produced every year. Considering significant benefits of recycled plastic waste, the highway agencies around the world are encouraged to use it in construction of pavements. However, use of plastic waste is not popular in India due to the lack of specific guidelines and design procedure. Furthermore, measurement and interpretation of rheological performance of RAP blended binders require advance laboratory instruments. A flexible pavement experiences different weather, extreme solar radiation, temperature, oxidation, and traffic loading and unloading conditions, which results in a stiffer and aged binder over time.
The waste plastic and its disposal is a major threat to the environment, which results in pollution and global warming. The utilization of plastic waste in bituminous mixes enhances its properties and its strength 1. In addition, it will also be a solution to plastic disposal & various defects in pavement viz., potholes, corrugation, ruts, etc. the waste plastic used are poly-ethylene, polystyrene, polypropylene. The waste plastic is shredded & coated over aggregate & mixed with hot bitumen and resulted mix is used for pavement construction. This will not only strengthen the pavement and increases its durability. The titanium-dioxide is used as a smoke absorbent material, which will absorb the smoke from the vehicles. This innovative technology will be boon for Indian hot-humid climate. It's economical and eco-friendly. In this paper, we have discussed about the soil properties to be considered in design of pavement, pavement design, process of construction flexible and plastic- smoke absorbent pavement.
The plastic wastes could be used in road construction and the field tests withstood the stress and proved that plastic wastes used after proper processing as an additive would enhance the life of the roads and solve environmental problems. Plastic use in road construction is not new. It is already in use as PVC or HDPE pipe mat crossings built by cabling together PVC (polyvinyl chloride) or HDPE (high-density poly-ethylene) pipes to form plastic mats. Waste plastic is ground and made into powder; 3 to 4 % plastic is mixed with the bitumen. The durability of the roads laid out with shredded plastic waste is much more compared with roads with asphalt with the ordinary mix. The use of the innovative technology not only strengthened the road construction but also increased the road life as well as will help to improve the environment and creating a source of income.
Key Words: Flexible pavement, High Density poly-ethylene, polyvinyl chloride
-
INTRODUCTION
The flexible pavements are preferred in India. These are economical about both initial construction cost and maintenance costs. Bituminous binders commonly used in surface courses are unmodified binders bitumen (depending on the climatic conditions hot or cold) and modified binders
by polymers (PMBs). Polymer-modified bitumen can improve fatigue life, temperature susceptibility and resistance to permanent deformation (Panda and Mazumdar, 2002; Jew and Woodhams, 1986).
The term Rheology is the study of flow of fluids and deformation of solids under the presence of stress and strain. Rheology has becomes a very useful tools in characterization of the bitumen performance on the pavement. Viscoelastic properties of bitumen binder can be described by rheological properties, they are phase angle () & complex shear modulus (G*) .complex shear modulus (G*) is the measurement of total resistance of a material to deformation under the repeated action of shear stress, whereas phase angle () is angle made by a complex modulus with horizontal axis.
Generally, the rheological behavior of bitumen is very complex phenomenon which varies from purely viscous to elastic depending on the time of loading and temperature. A viscoelastic material, bitumen play a very prominent role in determining the various aspects of road performance, for example, bituminous pavement need to be stiff at high temperature to prevent rutting and also needs to be flexible enough at low temperature to prevent cracking of pavement. These functional properties are required to enable pavement to accommodate the increasing traffic loading in varying climatic environment conditions. But unfortunately, due to the increased performance related to the requirement on the bituminous pavements, conventional bitumen does not always perform as it expected.
The scope of this study is to improve Viscosity, Marshall Stability, Penetration value and softening point of the Bitumen, to utilize waste materials as a pavement ingredient, to improve the binding property and water resistance of the bitumen and Reduction in construction coast of road pavement.
-
Objective of Purposed work
-
Study the quantitative changes in Viscosity, softening point, Penetration value, Marshal Stability and DSR test which is used to describe the viscous and elastic behavior of the modified bitumen at different temperature.
-
To find the optimum percentage of plastic waste needed in bitumen for best result of modified bitumen.
-
-
Scope of Purposed work
With increasing population and industrialization, demand of various development projects, construction of various industrial structures, building and roads have become important. For efficient and optimal design understanding of the behavior of road surface is of prime importance. The scope of present study is:
-
To improve Viscosity, Marshall Stability, Penetration value and Softening point of the Bitumen.
-
Eco-friendly environment.
-
To utilize waste materials as a pavement ingredient (as bitumen modifier).
-
To improve the binding property and water resistance of the bitumen.
-
Reduction in construction coast of road pavement.
-
-
Research framework and Significance
Plastic waste from different sources are increasing in a large amount which is causing hazard to life due to its non- biodegradable nature so we have to reduce it by utilizing it in engineering field by adopting proper techniques. Property of modified bitumen by plastic waste is far better from the pure bitumen in following aspects: –
-
The Marshal stability, viscosity, ductility, strength, softening point, penetration value etc. properties of modified bitumen will be improved.
-
Vast economical saving.
-
Reduced maintenance responsibility.
-
Environmentally friendly.
-
Improved water resistance of the pavement surface.
-
-
-
LITERATURE REVIEW
Literature review gives the idea about the physical and rheological properties such as complex modulus (G*) and phase angle (), Viscosity, Softening Point, Penetration value etc. of bitumen. It also covers the specific areas that either influence or area involved in the modeling of the rheological characteristics of bitumen. The review section deals with measurement of bitumen properties from the conventional physical test and rheological test. The most commonly test used on bitumen are penetration, softening viscosity test and Marshall Stability.
Punith and Veeraragvan (2011), studied the procedure for modification of 80/100-paving grade bitumen using recycled plastic derived from low-density polyethylene carry bags collected from domestic waste. Wet process was adopted to test different empirical test. They found that viscosity increases and penetration decreases with increasing amount of plastic. He observed that maximum bitumen content is 6% by weight of bitumen. Dynamic shear rheometer test results revealed that PE-modified binders (when subjected to the same stress) experienced lower strains than the neat asphalt; in addition, tan values of PE-modified binders considerably decreased as the PE content was increased. It was found that 6% PE content in modified asphalt by weight is adequate in terms of enhanced binder properties studied.
D Sybilski says Polymer-bitumens constitute non-Newtonian pseudoplastic systems showing two Newtonian regions. To analyze the relationship of polymer-bitumen binder properties and the behavior of a road pavement under traffic load, the absolute viscosity of the binder may be applied, i.e. viscosity under zero-shear stress conditions. This paper presents a new equation to compute absolute viscosity from measurements
conducted with a rotational viscometer. The equation is a simplified form of a four-parameter CROSS equation.
Vasudevan et. al. (2013), found that waste plastics collected from different sources could be used in modifying bitumen. Their softening point is above 100 degree Celsius and they do not emit poisonous gas when mixing with bitumen. When plastic is spread over heated aggregate then it get coated on the aggregate and this is found to be a better raw material for constructing pavement. They then mixed bitumen with this raw material in standard condition then was tested. This shows Marshall Stability higher than the actual aggregate mix bitumen. The sample shows high Marshall Stability value in the range of 18-20KN.
Zhu Xiao-qing et. al. (2009), used the mechano-chemically de-vulcanized ground tire rubber (m-GTR) prepared by solid- state mechano-chemical reactor is used in the modification of bitumen with styrene-butadiene-styrene block (SBS) copolymer powder. The conventional property _such as penetration index, softening point, 5°C ductility, and aging test$$and rheological properties of bitumen modified by 8, 10, and 12 wt. %m-GTR/SBS were investigated in this paper. Rheological data demonstrated that all of the testing results of 10 wt. %m-GTR/SBS modified bitumen were better than those of SBS modified bitumen under the condition of high temperature.
Devi et. al. (2013), investigates the method of coating aggregate using plastic. They first collected plastic from different sources like dumping zone, household then shredded it into smaller particles. Bitumen of grade 60/70 was used during investigation and mixes were made. Normal bitumen was coated with plastic and then by Marshall Method OBC was calculated for normal and plastic coated bitumen.
Murphy et. al. (2001), examined the possibility to incorporate waste polymer into bitumen as a modifier. The aim was to find recycled polymer modified binders that would be like proven modified binders or that would augment the properties of 100 penetration grade bitumen. A wide range of recycled polymers were tested, including polyethylenes, polypropylenes, polyether polyurethane, ground rubber, and truck tire rubber. Tests included viscosity, penetration, softening point, aging, and rheology. Stiffness tests on samples of bituminous mixes made using a selection of binders also formed part of the research program. Although stability problems were evident with some recycled modified bitumen, some cases were found to be successful.
Gawande (2012), explained the method of modifying bitumen with plastic. The modified bitumen was used in flexible pavement and he found that the plastic could be used upto 6- 10 % by weight of bitumen. He also found that the Marshall Stability value was high enough from unmodified sample.
Poweth et. al. (2013), discussed the suitability of plastic waste materials for pavement construction. The waste is mixed in different proportions to the soil sample and their influences on geotechnical properties were studied. The results of the tests indicated that plastic alone is not suitable for pavement
subgrade. When quarry dust was added along with soil plastic mix, it maintains the CBR value within the required range.
Khan and Gundaliya (2012), confirmed that waste plastic when spread on hot aggregate then it get coated around the aggregates to form a layer. Due to this coating the porosity, water absorption reduces and binding property get enhanced. The bitumen modified by 6 % plastic waste showed best result. The Marshall Stability was also increasing with plastic content and it has maximum value at 6%. At 6% Marshall Value was 35 % higher than unmodified mix.
.
-
Waste Collection Source
The materials which can be used are waste plastic bottles, bags, wrappers, collected from the nearby dumping places of houses and apartments and from the large dump yards. But the collected waste has to be recycled before it can be used with the bitumen. The collected waste should be free from other type of waste such as dust, soil, vegetable etc. and if it not then it should be separated properly. Then it should be cleaned and dried.
Figure 2.1 Sources of waste plastic
-
Recycling Process
-
Selection or analysis: The recyclers have to select and analyze the waste, which are suitable for recycling/reprocessing.
-
Collection or segregation: The materials which can be used are waste plastic bottles, bags, wrappers, collected from the nearby houses and apartments and from the dump yards.
-
Transporting or processing: After selection and segregation of the used plastic waste; it shall be washed, shredded, agglomerated, extruded and granulated. Waste plastic was segregated, and shredded using shredding machine (particle size 2-3 mm).
-
Figure 2.2 Material after recycling and shredding
-
-
METHODOLOGY
Bitumen is a Visco-elastic material which performs like an elastic solid at low service temperature and high rate of loading and while at high service temperature and slow rate of loading it acts like a viscous fluid. The purpose of this chapter is to describe the detail and description study of all physical and rheological test procedures.
-
Conventional Physical Properties Test
-
Penetration Test: Penetration test is the most commonly adopted test on bitumen to determine the grade of material in terms of its hardness because of its simplicity. The penetration grade of bitumen binders are generally denoted as 80/100, 60/70, or 30/40 grade bitumen.
-
Softening Point Test: Softening point is defined as the temperature at which the bitumen attains a degree of softening under précised circumstance of test. Commonly lower softening point of the materials designates the higher temperature and preferred in cold climates and vice versa.
-
Viscosity Test: Viscosity of a liquid is the property that retards its flow due to internal friction so it is a measure of resistance between the layers of liquid. The flow of a liquid under a force depends on its viscosity; higher the viscosity, slower is the rate of flow.
-
Dynamic Shear Rheometer Test: DSR was used to find the viscoelastic properties of bitumen such as fatigue cracking and rutting resistance at low, intermediate and high service temperatures. It measures both viscous and the elastic properties of the bitumen binders.
-
-
Methods of production of Mix
The plastic wastes that can be used for the work was collected from different places. Normal mix specimens were prepared with bitumen contents of 2.0%, 4.0%, 6.0%, 8.0%, and 10.0%. Tests were conducted on the modified bitumen to find out the changes in its properties ike viscosity, penetration value, softening point, DSR test and Marshall Stability and Marshall Flow values by empirical methods. Plastic modified mix specimens with plastic contents of 2 percent, 4 percent, 6 percent, 8 percent and 10 percent by weight of bitumen were prepared through Wet process by adding plastic to heated bitumen at a temperature of 180°C and a homogeneous mixture was formed by stirring it with a stirrer at high speed (3000 rpm) for 20-25 minutes.
-
Wet process
It is the blending of shredded plastic material and bitumen prior to the production of modified bituminous mixes. The chemical processes that produces binders, are considered to be swelling of the plastic particles from absorbing some of the more volatile compounds from the bitumen, followed by degradation of the plastic from De- vulcanizing and polymerization.
-
Dry process
Penetration value (dmm)
Penetration value (dmm)
It is the process of mixing the appropriate quantity of dry shredded waste plastic with hot aggregate prior to production of bituminous mixes at hot mix plant by varying percentage of plastic by weight of mix. In this process first dry aggregate is heated to a temperature of 150-160 °C then required amount of plastic is spread on the aggregate. Due to high temp. Plastic get melted and it coats the aggregate then bitumen is added to this modified aggregate. Due to coating of plastic on aggregate the voids get covered which increase the resisting from acid and water entrance which ultimately results in better performance of pavement.
-
-
Material Used
It presents the methodology of experimental program to accomplish the overall framework of the present study and deals with experiments carried out on the materials and detailed test procedures for plastic modified bitumen.
-
Bitumen
Physical properties of unmodified bitumen which was used are illustrated in the following table.
-
Recycled Plastic Waste
-
temperature (°C)
temperature (°C)
In this investigation, plastic waste in 2%, 4%, 6%, 8% and 10% (by weight of bitumen) was used as a modifier. The Waste Plastic and its Sources of plastic waste are presented in this table:
Penetration Value
Penetration Value
70
60
50
40
30
20
10
0
Penetration Value
70
60
50
40
30
20
10
0
Penetration Value
0% 2% 4% 6% 8% 10%
PlasticPlasticPlasticPlasticPlasticPlastic
plastic mix %
0% 2% 4% 6% 8% 10%
PlasticPlasticPlasticPlasticPlasticPlastic
plastic mix %
Fig.3.1 Penetration value with plastic mixed Bitumen
Property
Range
Penetration 0.1 mm @25°c
60-70
Softening point (°c )
49-60
Minimum Marshall strength (kg)
900
Viscosity @ 150°c (poise)
3-6
Softening Point
Softening Point
100
80
60
40
20
0
plastic mix %
Property
Range
Penetration 0.1 mm @25°c
60-70
Softening point (°c )
49-60
Minimum Marshall strength (kg)
900
Viscosity @ 150°c (poise)
3-6
Softening Point
Softening Point
100
80
60
40
20
0
plastic mix %
3.4.2 Softening Point: In this test, various percentage of plastic was added to the original bitumen. The test showed the variation of softening point with the various percentages of plastic modified bitumen. It was observed that softening point increases with the increasing amount of plastic content (%).
Waste Plastic
Origin
Low Density Polyethylene (LDPE)
Carry bags, Sacks, milk pouches.
High Density Polyethylene (HDPE)
Carry bags, bottle caps, house hold articles etc.
Polyethylene Teryphthalate (PET)
Drinking water bottles etc.
Polypropylene (PP)
Bottle caps and closures, wrappers of detergent, biscuit, wafer packets etc.
Polystyrene (PS)
Food trays, egg boxes, disposal cups, protective packaging etc.
Polyvinyl Chloride (PVC)
Mineral water bottles, credit cards, toys, pipes, folders and pens, medical disposal etc.
Waste Plastic
Origin
Low Density Polyethylene (LDPE)
Carry bags, Sacks, milk pouches.
High Density Polyethylene (HDPE)
Carry bags, bottle caps, house hold articles etc.
Polyethylene Teryphthalate (PET)
Drinking water bottles etc.
Polypropylene (PP)
Bottle caps and closures, wrappers of detergent, biscuit, wafer packets etc.
Polystyrene (PS)
Food trays, egg boxes, disposal cups, protective packaging etc.
Polyvinyl Chloride (PVC)
Mineral water bottles, credit cards, toys, pipes, folders and pens, medical disposal etc.
3.4 Physical Test on Plastic Waste Modified Bitumen
3.4.1 Penetration Test: In this test, various percentage of plastic (%) was added to the original bitumen. The test showed the variation of penetration value with the various percentage of plastic modified bitumen and it presented that consistency increases with addition of plastic.
100
90
80
70
60
50
40
30
20
10
0
Fig.3.2 Softening point with different plastic content
Penetration Value Softening Point
0% 2%
4% 6%
8% 10%
Plastic Plastic Plastic Plastic Plastic Plastic
Fig.3.3 Penetration value (d mm) and softening point (°C) of modified Bitumen
-
Viscosity Test: Viscometer test was conducted by using Visco-88 Viscometer. The apparatus was used to measure viscosity characteristics of conventional and plastic modified bitumen.
0.4
Viscosity (pas.sec)
Viscosity (pas.sec)
0.3
Comparision of Viscosity
UNMODIFIED BITUMEN
0.2 2% PLASTIC
MIX BITUMEN
0.1
0
135° C 145° C 155° C 165° C 175° C
4% PLASTIC MIX BITUMEN
Fig. 3.6 Graph of (G*/sin) and temperature for Unmodified bitumen
Comparision of Viscosity
Comparision of Viscosity
1.6
1.4
1.2
1
0.8
0.6
0.4
0.2
0
6% PLASTIC
MIX BITUMEN
8% PLASTIC
MIX BITUMEN
10% PLASTIC
MIX BITUMEN
1.6
1.4
1.2
1
0.8
0.6
0.4
0.2
0
6% PLASTIC
MIX BITUMEN
8% PLASTIC
MIX BITUMEN
10% PLASTIC
MIX BITUMEN
135° 145° 155° 165° 175° C C C C C
135° 145° 155° 165° 175° C C C C C
Viscosity (pas.sec)
Viscosity (pas.sec)
Fig.3.4 Comparison of different viscosity by graph
-
Dynamic shear Rheometer test: The dynamic shear rheometer (DSR) is used to describe the viscous and elastic behavior of binders at different temperatures. This characterization is used in the superpave PG asphalt binder specification. Objectives of DSR test is to find:
-
Complex shear modulus (G*/sin)
-
Complex modulus (G*)
-
Phase angle ()
Fig. 3.5 Result of DSR for Unmodified bitumen
Fig.3.7 Graph of (G*/sin) and temperature for 2% plastic mix bitumen
Fig.3.8 Graph of (G*/sin) and temperature for 4% plastic mix bitumen
Complex Modulus (G*) of Unmodified Bitumen
Complex Modulus (G*) of Unmodified Bitumen
60
50
40
30
20
60
50
40
30
20
Complex Modulus (G*) of Unmodified Bitumen
Complex Modulus (G*) of Unmodified Bitumen
10
0
10
0
0.00
0.00
50.00 100.00
TEMPERATURE (°C)
50.00 100.00
TEMPERATURE (°C)
COMPLEX MODULUS (kPa)
COMPLEX MODULUS (kPa)
Fig. 3.9 Graph of (G*/sin) and temperature for 6% plastic mix bitumen
Fig.3.10 Graph of (G*/sin) and temperature for 8% plastic mix bitumen
Fig.3.11 Graph of (G*/sin) and temperature for 10% plastic mix bitumen
Fig. 3.12 Graph of Complex Modulus (G*) and temperature of Unmodified Bitumen
0.00
0.00
50.00
TEMPERATURE (°C)
100.00
0.00
0.00
50.00
TEMPERATURE (°C)
100.00
Complex Modulus (G*) of 2% Plastic Mix Bitumen
350.00
300.00
250.00
Complex Modulus (G*) of 2% Plastic Mix Bitumen
350.00
300.00
250.00
200.00
150.00
100.00
200.00
150.00
100.00
Complex Modulus (G*) of 2% Plastic Mix Bitumen
Complex Modulus (G*) of 2% Plastic Mix Bitumen
50.00
50.00
Complex Modulus (G*) of 4% Plastic Mix Bitumen
350.00
300.00
250.00
Complex Modulus (G*) of 4% Plastic Mix Bitumen
350.00
300.00
250.00
200.00
150.00
200.00
150.00
Complex Modulus (G*) of 4% Plastic Mix Bitumen
Complex Modulus (G*) of 4% Plastic Mix Bitumen
COMPLEX MODULUS (kPa)
COMPLEX MODULUS (kPa)
COMPLEX MODULUS (kPa)
COMPLEX MODULUS (kPa)
Fig. 3.13 graph of Complex Modulus (G*) and temperature of 2% plastic mix bitumen
0.00
0.00
50.00
TEMPERATURE (°C)
100.00
0.00
0.00
50.00
TEMPERATURE (°C)
100.00
100.00
50.00
100.00
50.00
Fig. 3.14 Graph of Complex Modulus (G*) and temperature of 4% plastic mix bitumen
Complex Modulus (G*) of 6% Plastic Mix Bitumen
Complex Modulus (G*) of 6% Plastic Mix Bitumen
350.00
300.00
250.00
200.00
150.00
100.00
50.00
0.00
0.00
350.00
300.00
250.00
200.00
150.00
100.00
50.00
0.00
0.00
Complex Modulus (G*) of 6% Plastic Mix Bitumen
Complex Modulus (G*) of 6% Plastic Mix Bitumen
50.00
TEMPERATURE (°C)
50.00
TEMPERATURE (°C)
100.00
100.00
Comparision of Complex Modulus of different % of Plastic Modified Bitumen
800
700
unmodified
600 Bitumen
Comparision of Complex Modulus of different % of Plastic Modified Bitumen
800
700
unmodified
600 Bitumen
500
500
2% Plastic Mix bitumen
2% Plastic Mix bitumen
400 4% Plastic Mix
300 Bitumen
6% Plastic Mix
200 Bitumen
400 4% Plastic Mix
300 Bitumen
6% Plastic Mix
200 Bitumen
100
100
COMPLEX MODULUS (kPa)
COMPLEX MODULUS (kPa)
COMPLEX MODULUS (kPa)
COMPLEX MODULUS (kPa)
Fig. 3.15 graph of Complex Modulus (G*) and temperature of 6% plastic mix bitumen
Complex Modulus (G*) of 8% Plastic Mix Bitumen
800.00
COMPLEX MODULUS (kPa)
COMPLEX MODULUS (kPa)
700.00
600.00
500.00
8% Plastic Mix Bitumen
8% Plastic Mix Bitumen
0
0.00
0
0.00
50.00
TEMPERATURE (°C)
50.00
TEMPERATURE (°C)
100.00
100.00
10% Plastic Mix Bitumen
10% Plastic Mix Bitumen
Fig.3.18 Complex Modulus (G*) and temperature of different % of plastic mix bitumen
400.00
300.00
200.00
100.00
0.00
0.00 50.00 100.00
TEMPERATURE (°C)
Complex Modulus (G*) of 8% Plastic Mix Bitumen
Phase angle (): Phase angle is defined as the time lag between applied stress and resulting strain. It can be used to describe the visco elastic behavior of asphalt binder.
The dynamic shear rheometer (DSR) imposes an amplitude of the resulting shear stresses and sinusoidal varying shear strain on the bitumen sample is determined in oscillatory deformation test.
Fig. 3.16 graph of Complex Modulus (G*) and temperature of 8% plastic mix bitumen
Complex Modulus (G*) of 10% Plastic Mix Bitumen
800.00
700.00
600.00
500.00
Complex
400.00 Modulus (G*) of
10% Plastic Mix
300.00 Bitumen
200.00
100.00
Complex Modulus (G*) of 10% Plastic Mix Bitumen
800.00
700.00
600.00
500.00
Complex
400.00 Modulus (G*) of
10% Plastic Mix
300.00 Bitumen
200.00
100.00
100
90
80
70
Angle()
Angle()
60
50
40
30
20
10
0
Phase angle comparision
unmodified Bitumen
2% Plastic Mix bitumen
4% Plastic Mix Bitumen
6% Plastic Mix Bitumen
8% Plastic Mix Bitumen
0.00
0.00
0.00
0.00
10% Plastic Mix Bitumen
50.00
TEMPERATURE (°C)
100.00
50.00
TEMPERATURE (°C)
100.00
Fig.3.17 graph of Complex Modulus (G*) and temperature of 10% plastic mix bitumen
0.00 50.00 100.00
COMPLEX MODULUS (kPa)
COMPLEX MODULUS (kPa)
Temperature (° C)
Fig.3.19 Phase angle comparison for different plastic modified Bitumen
3.4.5 Marshall Stability Test: In this test an attempt is made to compare the results of normal bitumen specimen and with Plastic modified bitumen specimen with varying % of plastic mixed. Three specimens were made for every different %age of bitumen and the specimen was tested in Marshall Testing Machine. Optimum Bitumen content (OBC) is calculated by
taking the average of % bitumen for which Marshall Stability, Density is maximum and 4% air void bitumen content.
Marshall Stability in (Kg)
Marshall Stability in (Kg)
3000
2500
2000
1500
1000
500
0
Marshall Stability (Kg)
Bitumen type
Fig.3.20 graph of Marshall Stability of different type of Bitumen (at 5.5% bitumen by weight)
Marshall flow in (mm)
Marshall flow in (mm)
7
6
5
4
5
4.5
4
3.5
3
2.5
2
1.5
1
0.5
0
void (%)
5
4.5
4
3.5
3
2.5
2
1.5
1
0.5
0
void (%)
Bitumen type
Bitumen type
Void, Vv (%)
Void, Vv (%)
Fig.3.23 Graph of voids of different type of Bitumen (at 5.5% bitumen by weight)
Void filled with bitumen (%)
Void filled with bitumen (%)
79
78
77
76
75
74
3 73
2
1 Marshall Flow (mm)
0
VFB (%)
Bitumen type
Fig. 3.21 Graph of Marshall Flow value of different type of Bitumen (at 5.5% bitumen by weight)
622
620
Density in (g/cc)
Density in (g/cc)
618
616
614
612
610
608
Bitumen type
Fig.3.24 Graph of void filled by bitumen of different type of Bitumen (at 5.5% bitumen by weight)
-
-
RESULT
The pupose of this paper is to describe the physical behavior of conventional Bitumen and modified Bitumen as well as analysis of test data. The framework of testing Bitumen was selected in order to examine the influence of plastic in the Bitumen properties subjected to different parameters. In this study both conventional and modified Bitumen were tested and a summary of all results obtained from the test is discussed below.
606
604
602
Bitumen type
Density (g/cc)
-
Effect of plastic on penetration value and softening point
The penetration value decreases from 47.6 at 2% mix to 24.0 at 8% & 21.4 at 10% with original value being 65.6. The decrease in penetration value indicates that the strength of bitumen has increased which is due to better binding between the molecules of the bitumen. As the penetration is low, the PE-
Fig.3.22 Graph of Density of different type of Bitumen (at 5.5% bitumen by weight)
modified bitumen pavement will show high resistance toward deformation at heavy load and hence life of pavement will be better.
Similarly in softening point test, variation in softening point is from 69°C at 2% to 88°C at 10%. The softening point of unmodified bitumen was found to be 62°C. As the softening
point of modified bitumen is much higher this concludes that the modified bitumen is harder and will show better resistance in hot climate and in heavy loading. Due to higher softening point, bleeding phenomenon will also be quite low or negligible.
-
Effect of plastic on viscosity of Bitumen
Plastic modified Bitumen increases the viscosity of the Bitumen with increasing percentage of plastic mixed in Bitumen, viscosity is increasing sharply in the temperature range 135°C to 175°C.
As the viscosity is increasing with increasing percentage of plastic mixed in Bitumen, it is concluded that the layers wide have extra strength within the mix and hence flow will be lesser. Viscosity is also much higher at 175°C which says that at higher temperature. This has higher strength at high temperature. The viscosity obtained for 10% plastic mix bitumen is highest among all but the texture of this bitumen is changed from the actual texture of bitumen and it also has low elasticity so 10% plastic modified bitumen is less applicable for the pavement.
-
Effect of plastic on complex modulus (G*), phase angle
(S) & complex shear modulus (G*/sin)
Effect on complex modulus (G*) G* is the shear stress and its value represents the stiffness of the Bitumen binder. It is divided in two parts, the storage modulus G which describe the elastic properties and G the loss modulus which describe the viscous properties of the bitumen. Higher the value of G*, higher is the stiffness and hence harder is the Bituminous pavement. In the DSR test performed with different percentage of plastic mix Bitumen, G* value increases significantly. Its value is almost equal for 2%, 4% and 6%, but at 8% its value (760 kPa at 46°C) is much higher and then its value decreases a little at 10% (718 kPa at 46°C), which indicated optimity at 8%.
Phase angle values obtained are closer to 90°, which indicate that the Bitumen is more viscous in nature.
The G*/sin values is increasing from 2% to 10% plastic but is has maximum at 8% plastic mix (878 kPa at 46°C).
-
Effect of plastic on Marshall Stability, Flow value and Density of Bitumen
Effect on Marshall Stability- The Marshall stability of the mix is defined as a maximum load carried by a compacted specimen at a standard test temperature of 60°C. The Marshall stability value got increased to a large amount when we use Plastic modified bitumen. The stability value of unmodified bitumen was found to be 1503kg but after addition of 2% plastic in the bitumen it became 2053.8kg. Further it was 2113.16kg at 4% plastic, 2246.12kg at 6% plastic, 2592.7kg at 8% and 2224.75kg at 10% plastic mixed in the bitumen. The high stability value will resist the rutting effect which is generated due to high tire pressure and increased wheel loads of traffic moving on roads. As the Marshall Stability has increased significantly for the PE- modified bitumen this also indicates that the pavement can serve better for long time and at high traffic load it will have lesser deformation compare to unmodified bitumen. High Stability value indicates better binding of HMA.
-
-
CONCLUSIONS
Mixing various percentage of Plastic in Bitumen shows positive result on the empirical test done during this Dissertation. The fluctuation of test data with various degree of plastic mixed in Bitumen is changing up to optimum level then it either shows negative result or remains unchanged. In the current study of different laboratory test, the optimum plastic content was found to be 8% by weight of bitumen.
The DSR test result concludes that the complex modulus (G*) of various plastic mix bitumen is much higher than the unmodified bitumen and is maximum for 8% plastic mix bitumen. Phase angle () is relatively lesser for plastic modified bitumen compare to unmodified bitumen.
High value of Complex shear modulus (G*/sin) results in better resistance towards the rutting and fatigue effect of the pavement. As the Viscosity of the modified bitumen is much higher than the unmodified bitumen, the different layers of bitumen will have high strength and thus increased the strength of pavement resulting in greater life and serviceability of the pavement.
REFRENCES
-
Awanti, S.S. Amaranth, M.S., and Veeraragavan, A.,(2008), Laboratory Evaluation of SBS Modified.Bituminous Paving Mix,journal of materials in civil engineering, pp. 327-330.
-
Bindu, C.S., (2010), Use of waste plastic in construction of bituminous road,Int. J. Engg. & Technology, 2(6), pp. 379-387.
-
Gawande, P.A.,(2013.), economics and viability of plastic road : a review,J. Curr. Chem. Pharm. Sc.: 3(4), 2013, pp. 231-242.
-
Garg, S.K.,(1999), Environmental Engineering, Vol.II Khanna Publishers.
-
Imtiyaz, Mohd., (2002), Adhesion Characteristics Study on Waste Plastics Modified Bitumen.
-
IRC SP: 53-2010, Guidelines on use of polymer and rubber modified bitumen in road construction.
-
IRC SP: 98-2013, Guidelines for the use of waste plastic in hot bituminous mixes (Dry process) in wearing courses.
-
Jain, P.K., Plastic waste.modified bituminous surfacing for rural road (CRRI),CSIRCentral Road Research Institute, New Delhi.
-
Kaur, Verinder.,Sangita., and Gupta, Reena.,(2011), a novel approach to improve road quality by utilizing plastic waste in road construction,Journal of Environmental Research And Development Vol. 5 No. 4. pp. 1036-1042.
-
Khan, Imtiyaz. and Dr. Gundaliya, P.J.,(2012), Utilization of Waste Polyethylene Material in Bituminous Concrete Mix for Improved
-
Performance of Flexible Pavements, International Journal of Scientific Research, Vol.-1
-
M. Devi, Rema., Stephen, Leni., And M. I. Mini.,(2013), Reduction of optimum bitumen content in bituminous mixes using plastic coated aggregates,International Journal of Innovative Research in Science, Engineering and Technology Vol. 2 .
-
Milkowski, W. (1985), Catalytic modification of road asphalt by polyethylene.
-
N. R. R. D. A., (2007),Ministry of Rural Development, GOI, Guidelines for use of Plastic Waste in Rural . Road Construction.
-
Panda, M., and Muzumdar, M., (2002), Utilization of reclaimed polyethylene in bituminous paving mixes journal of materials in civil engineering, pp. 527-530.
-
Poweth, M.J., Goerge, Solly., and Paul, Jessy.,(2013), study on use of plastic waste in road construction,International Journal of Innovative Research in Science, Engineering and Technology Vol. 2, Issue 3, March,pp. 633-638.
-
Swami, Vidula., Abhijeet, J., and Karan, P.,(2012), Use of waste plastic in the construction of bituminous road, International Journal ofEngineering Science and Technology, vol. 4, Issue 5, pp. 1-5.
-
Dr. Vasudevan,V., Dr. Paulraj, Samuvel., and Rajasekaran, S., (2013),
-
Reuse of Waste Plastics Coated Aggregates-Bitumen Mix Composite For Road Application Green Method,American Journal of Engineering Research (AJER) e-ISSN : 2320-0847 p-ISSN : 2320- 0936 Volume-02, Issue-11, pp.01-13.
-
Varma, S.S., (2008), Roads from Plastic Waste, The Indian Concrete Journal. pp.43-44.
-
N. Bhattacharya Sati Chapter 1 Rheology Fundamentals and Measurement, Royal Melbourne Institute of Technology, Australia (1997)
-
J. Stastna, et al. Viscosity.functions in polymer modified asphalts J.
Colloid Interface Sci., 59 (2002), pp. 200-209
-
Amit.Gawande, G.S Zamre, V.C Renge G.R Bharsakalea and SaurabhTayde, utilization of waste plastic in asphalt of roads, scientific reviews and chemical communication
-
D. Sybilsk New simplified equation for the computation of absolute viscosity of polymer-bitumens Mater. Struc., 30 (1997)