
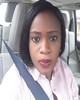
- Open Access
- Authors : Mamudu Angela , Emetere Moses , Elehinafe Francis, Akande Odunayo , Ishola Felix, Lawal Dorcas
- Paper ID : IJERTV9IS050843
- Volume & Issue : Volume 09, Issue 05 (May 2020)
- Published (First Online): 04-06-2020
- ISSN (Online) : 2278-0181
- Publisher Name : IJERT
- License:
This work is licensed under a Creative Commons Attribution 4.0 International License
The Production of the Matrix Component of the Fluid Catalytic Cracking Unit from Watermelon Peel
Mamudu Angela*1, Emetere Moses 2, Ishola Felix3, Lawal Dorcas1, Elehinafe Francis1, and Akande Odunayo4
1Department of Chemical Engineering, Covenant University, Ota, Nigeria
2Department of Physics, Covenant University, Ota, Nigeria
3Department of Mechanical Engineering, Covenant University, Ota, Nigeria
4Department of Agriculture, Federal University of Agriculture, Abeokuta, Nigeria.
Abstract:- Fluid Catalytic Cracking is considered one of the most predominant and sophisticated contributions to the technological advancement of the petroleum industry. One of the major reasons why this is so has been the introduction of the FCC catalysts, which comprises of the crystalline zeolites, binders, matrix and fillers. The ever-increasing costs of Fluid Catalytic cracking catalysts have led researchers to develop alternative materials which can be gotten locally and have similar if not superior properties than the commercial FCC Catalyst. Over the years, there have been many significant improvements in the FCC catalysts and most of them have been focused on the zeolite. However, research over the last five decades has shown that the benefits derived from improved FCC catalyst technology- such as increased gasoline yields, improvements in catalyst attriton resistance, enhanced bottoms cracking, can be associated with advancement of the catalyst matrix technology . In this study, the matrix component of the FCC Catalyst was synthesized using watermelon peel as starting materials. The matrix was synthesized using chemical modification while varying reagent concentration and reaction time. The resultant products were evaluated using FTIR, and SEM analysis. The results prove that acid- modified activated carbon has a huge potential as matrix for the FCCU catalyst though research is still on-going.
Keywords: Fluid Catalytic Cracking Unit; Zeolite Y; Matrix; Palm Kernel shells; Watermelon peel.
1. INTRODUCTION
The fluid catalytic cracking unit (FFCU) which falls under the conversion group of the Petroleum refinery operations remains an indispensable unit operation in refineries. Due to the growing demand for high octane value gasoline, the FCCU is regarded as the heart of any petroleum refinery (Fahim et al., 2010, Mamudu et al., 2019). It converts about 40% of the heavy residues gotten from both vacuum and atmospheric distillation into lighter and more useful products with high octane value.
Although the FCCU has existed for about eight decades, it has become irreplaceable due to frequent upgrades of the catalytic process that continues to further improve product selectivity. An FCCU catalyst constitutes of four major components : the crystalline zeolites, the matrix, binder and filler. Over the years, researchers have come to discover that the ultimate performance of an FCCU catalyst largely depends on the nature and composition of the zeolite and matrix components and how all of these are integrated to
create a functional cracking system (Humphries & Wilcox 1989). Technology reviews on improved performance of FCC catalysts have been centered on advancements of zeolites in the past. In recent years, more attention is being shifted towards matrix technology innovations ( Rajagopalan, 1992).
An effective cracking system provides the ability of active alumina and a crystalline zeolite to assist in the efficient upgrading of bottom distillates into higher-quality gasoline and light cycle oil. Zeolites are hydrated alumina silicate materials made from interlinked tetrahedral of alumina (AlO) and silica (SiO). 130 out of 840 catalysts used in industrial applications are based on zeolites and the FCCU in petroleum refineries utilizes over 61% of these zeolite- based catalysts (Oil & Gas Journal, 2003, Elehinafe et al, 2019).
The pore distribution, acidic properties, high selectivity and thermal stability of Zeolite catalysts make them stand out amongst other non-zeolite catalysts in the FCCU due to the significant increase in gasoline yield and octane number boost. The zeolite component makes up 10-50 wt % of the catalyst and provides activity, stability, and selectivity. The matrix comprises 50-90% of the catalyst and provides desirable physical properties, as well as some catalytic activity (Leiby,1992).
Matrices have various physical and chemical properties that make them stand out as components of a fluid catalytic cracking catalyst. The matrix usually in a fluid catalytic cracking unit is considered as catalyst support which is usually silica-alumina. One of the functions of matrices is to act as a diffusion medium that allows the diffusion of hydrocarbons in and out of the catalyst particles. (Haas, 1996). It also helps to avoid over-cracking by moderating the zeolites activity and protecting the zeolite from structural damage by facilitating heat transfer during cracking and regeneration. Another major function of the matrix is to provide the microspheres with physical strength and the attrition resistance necessary to withstand the stress of rapid circulation. It usually acts as a cracking component for gas molecules that are too large to enter the zeolites pores. The most common matrices being used are amorphous silica, alumina and silica-alumina (Ballmoos and Hayward, 2008).
Researchers have begun to place more attention on the effect of matrices on the activity of FCC catalysts and poisoning mechanisms such as vanadium and nickel (Chen, 2005).There are various types of synthetic zeolites but a major catalyst that has continued to gain worldwide recognition is the type- Y zeolites from the faujasite family. This is so because modification and re-modification have been made on its structural framework over the past decades which have helped to upgrade its inherent physico-chemical properties- acidity, thermal stability and the evident increase in gasoline yield (Liu,2016).
In 2003, a new catalyst called Flex-Tee was commercialized by Engelhard Corporation , tHe production of this new catalyst was centered around the Distributed matric structyre DSM technology. The basic concept in DSM technology was the introduction of a unique pore structure that enhances the diffusion of the feed stock molecules and the provision of highly selective pre-cracking sites (Sakashita, 2011). With respect to the matrix of an FCC catalyst, similar properties of the conventional matrix has been found in activated carbon like its resistance to attrition and large pore size which will encourage diffusion of hydrocarbon molecules (Ballmoos &Hayward, 2008).
Hence, the possibility of synthesizing pure activated carbon (matrix) from watermelon peels is studied in this work. The formulated matrix is targeted for industrial use in FCCU applications.
-
AIM AND OBJECTIVES
The aim of this study is to investigate the possibility of synthesizing matrix component of the fluid cagtalytic cracking catalyst from watermelon peels. This will be achieved via the following objectives;
-
Chemical treatment of watermelon peel using different activating agents while varying concentration to produce activated carbon (used as a matrix in place of silica and alumina)
-
Characterization of the activated carbon.
-
2.0 MATERIALS AND METHODS
-
Synthesis of FCCU Matrix
The procedure employed in the synthesis of FCC matrix was that used by Abdulkareem in the production of activated carbon. (Abdulkareem et al, 2014)
-
Physical Treatment
The watermelon peel were gotten from the cafeteria of Covenant University. The peels were washed with distilled water to remove dirt and seeds before they were sundried for a period of 7 days to constant weight. The dried peels were then crushed to powder form using a mechanical grinder.
-
Chemical Modification
-
12g portions of the ground watermelon peel samples were stirred and left to be soaked separately in a known weight of
1.0 M and 1.5 M, each for phosphoric acid and Zinc chloride. The impregnation ratio and time were 0.3:1 and 24 hours respectively. The activated product was then washed with warm distilled water until the distillate reached a pH of 7 to remove phosphoric acid and Zinc chloride content. The activated product was dried in an oven at a temperature of 105C for 1 hour.
2.2.3 Carbonization
In the course of the carbonization experiments, 15g of the activated samples were weighed into four different clean and pre-weighed crucibles, which were then introduced into the hot zone of a muffle furnace. The activated crushed peels were carbonized at a temperature of 300C. The samples were held at a temperature of 60 minutes in order to establish the optimum conditions for the process. The contents were then removed from the muffle furnace after the set period and cooled in an open-air for one hour. The produced activated carbon was then characterized using SEM and FTIR.
-
RESULTS AND DISCUSSION
-
Characterization of synthesized FCCU matrix
The activated carbon produced by chemical modification of watermelon peels using Zinc chloride and phosphoric acid were characterized using SEM and FTIR to determine if it is fit to be used as a matrix in the Fluid Catalytic Cracking Unit.
a
a
Fig 1: SEM image of (a) Synthesized AC at 10 µm (b)
Synthesized AC at 15 µm
Fig 4.2.1a and Fig 4.2.1b give the representative image of the morphology of the activated carbonmatrix. The large pores of the activated carbon are represented by the dark spaces in Fig 4.2.1b which is a property of a good matrix to ensure diffusion of molecules through the large pore openings.
Figure 2: Structural Analysis of Synthesized Activated Carbon
Figure 2 above shows the structural effect of the chemical modification and carbonization process with a grain wise size of 147.41nm. The image shows that it is naturally compacted and evenly distributed at the centre than the edges.
3.3. Fourier Transform Infrared Spectroscopy Analysis
The FTIR- spectra show a band at 3423.79cm-1 which is due to the O-H stretching of water. The band at 1640 cm-1 has been noticed by previous researchers where C=C stretching adsorption was found to frequently occur at this region. The band observed at 2935.76 cm-1 was found to correspond to methylene asymmetric, C – H stretching. The band given at 1592.29 cm-1 was an indication of the presence of pyridine, C = N stretching while the band at 1402.3 cm-1 was ascribed to azo compound, N= N stretching. Finally, the bands at 1015 and 1108 cm-1 was found to be due to aliphatic C- N stretching while the band at 683.79 cm-1 was due to P =S stretching. The FTIR shown in Figure 6 is quite similar to Figure 5 as the peaks in both spectra have a close range of values. This shows that the variation in the reagent used for chemical modification only slightly affects the absorption peaks.
11.91
11.5
11.0
10.5 2401.00
10.0
9.5
9.0
8.5
4383.00
3967.00
2099.00
1398.00
1315.00
1108.00
1015.00
8.0
7.5
7.0
6.5
6.0
5.5
1640.61
5.0
%T
4.5
4.0
3.5
3.0
2.5
2.0 3423.00
1.5
1.0
0.5
0.0
-0.5
-1.0
416.37
377.85
-1.5
-2.00
4400.0 4000 3600 3200 2800 2400 2000 1800 1600 1400 1200 1000 800 600 350.0
cm-1
Figure 5: FTIR spectra of activated carbon synthesized using 0.5M of ZnCl2
76.0
75
74
73
72
71
70
69
68
67
66
65
64
63
62
61
3775.41
2369.66
1725.57
1431.57
1371.87 1252.00
1322.66
770.61
608.00
532.73
%T
60
59
58
57
56
55
54
53
52
51
50 3431.00
49
48
47
2926.57
1631.68
1038.33
46.0
4400.0 4000 3600 3200 2800 2400 2000 1800 1600 1400 1200 1000 800 600 350.0
cm-1
Figure 6: FTIR spectra of activated carbon synthesized using 1.5M of Phosphoric acid
CONCLUSION
The synthesized activated carbon from watermelon peels were found to have the suitable characteristics of Matrix in the FCCU. Hence, it can be concluded that palm kernel shells and watermelon peels are good starting materials for the production of matrix respectively to be used as a component of the Fluid Catalytic Cracking catalyst.
ACKNOWLEDGEMENTS
I want to express my deep thanks to the management of Covenant University, Nigeria for providing an enabling environment for this research. I also want to express my profound gratitude to my co- authors for their wonderful contributions.
REFERENCES
-
Abdulkareem A.S, Jimoh W.A and Giwa A. (2014), Production of Activated Carbon from Watermelon peel. International Journal of Scientific & Engineering Research, Volume 5, Issue 2, February 2014 66 ISSN 2229-5518
-
Ballmoos R.V, Hayward C.T (2008) Matrix versus Zeolite Contributions to the Acidity of Fluid Cracking Catalysts. Studies in Surface Science and Catalysis Volume 65, pg 171-183
-
Cejka J., Corma A., and Zone S. (2010), Zeolites and Catalysis, Synthesis, Reactions and Applications. WILEY-VCH Verlag GmbH & Co. KGaA,
Weinheim
-
Chen, Q., Shen, B.-X., Tan, C.-G., J. East China Univ. Sci. Tech., 31, (4), 438 (2005).
-
Faizul C.P and Abdullah C., (2017) Zeolite synthesis from oil Palm Ash using Hydrothermal Treatment. Advanced Materials Engineering and Technology AIP Conference Proceedings 1835, 020016 (2017); https://doi.org/10.1063/1.4981838 Published Online: 26 April 2017
-
Elehinafe, F.B., Okedere, O.B., Odunlami, O.A., Oladimeji, T.A., Mamudu, O.A. and Sonibare, J.A. (2019). Comparative Study of Non- Metallic Contents of Sawdust of Different Wood Species and Coal Species in Nigeria. Pet Coal (2019); 61(5) 1183-1189 ISSN 1337-7027
-
Haridoss S. (2017), A study on the role of catalysts used in catalytic cracking process in Petroleum Refining, International Journal of Chem. Tech Research vol.10 No.7 pp79-86.
-
Haas A., Nee, J.R., (1996) The role of zeolite and matrix activity in FCC catalysts on the molecular weight distribution of vacuum gas oil cracking products. Erdoel Erdgas Kohle 112(7),pg 312-314.
-
Humphries, A., & Wilcox, J.R. Zeolite components and matrix composition determine FCC catalyst performance. United States.
-
Leiby S., (1992) FCC catalyst technologies expand limits of process capability Oil and Gas Journal SRI International Menlo Park, Calif
-
Liu Z., Shi C., Wu D., He S., and Ren B., A Simple Method of Preparation of High Silica Zeolite Y and Its Performance in the Catalytic Cracking of Cumene, Journal of Nanotechnology, vol. 2016, Article ID 1486107, 6 pages, 2016. https://doi.org/10.1155/2016/1486107.
-
Mamudu, O.A., Igwe, G.J and Okonkwo, E (2019). Process Design Evaluation of an Optimal Modular Topping Refinery for Nigeria Crude Oil using Hysys Aspen Software. Cogent Engineering (2019), 6: 1659123.
-
Pa F.C, Kasmuin M.Z, Ismail.S and Baharun.N (2007), Hydrothermal synthesis of zeolites from Fly Ash Journal of Nuclear and Related Technology
vol.4, 2007, 87-91.
-
Rahman, M.M and Hasnida N. (2009) Preparation of zeolite Y using Local Raw Material Rice Husk as aSilica source. Journal of Scientific Research 1(2),285-291
-
Rajagopalan, K., Habib, E.T.,(1992) Understand FCC Matrix Technology Hydrocarbon Processing Journal.
-
Sakashita, K., and Asaoka S.,(2011) Role of nanoporous Al2O3 as matrix for catalytic cracking. Journal of the Japan Petroleum Institute, 54(3), 180- 188
-
Somerset, V.S., Petrik, L.F., White, R.A., Klink, M.J., Key D., Iwuoha, E.F.(2005) Alkaline Hydro-thermal Zeolites synthesized from high SiO and AlO co-disposal fly ash filtrates. Fuel 84(2005) 2324-2329
-
Vogt E.T and Weckhuysen B.M (2015),Fluid catalytic cracking: recent developments on the grand old lady of zeolite catalysis. Chem.soc. Rev, 2015,44,7342.