
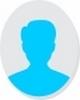
- Open Access
- Authors : Zhao-Xing Yin
- Paper ID : IJERTV10IS010211
- Volume & Issue : Volume 10, Issue 01 (January 2021)
- Published (First Online): 01-02-2021
- ISSN (Online) : 2278-0181
- Publisher Name : IJERT
- License:
This work is licensed under a Creative Commons Attribution 4.0 International License
The Influence of Zrb2 Target Power on the Structure and Performance of Zrb2-Cu Thin Film
Zhao-Xing Yin
Tianjin University of Technology and Education Tianjin 300222, China
AbstractObjective to improve the toughness and wear resistance of ZrB2 coating by doping proper amount of soft phase copper, and to reveal the effect of copper content on the structure and performance of ZrB2 coating by changing the target power of ZrB2.Methods ZrB2-Cu thin films were prepared by pulsed DC magnetron sputtering technology. X-ray diffractometer, scanning electron microscope, nano indentation tester, scratch tester and high temperature friction machine were used to study the influence of ZrB2 target power on the microstructure, mechanical properties and friction properties of ZrB2-Cu thin films. Results With the increase of ZrB2 target power, the grain size of ZrB2-Cu film decreased gradually, and the surface roughness decreased. The film is dominated by ZrB2 phase growing along the (101) crystal plane. With the increase of ZrB2 target power, the crystallinity of Cu is inhibited. When the ZrB2 target power was 2.4kW, the hardness and critical load of the film reached the maximum, which were 4.4GPA and 23.4N, respectively. When the target power of ZrB2 is 1.6kW, the film has a smaller average friction coefficient of 0.49 and a wear rate of 11.32×10-14 m3/N·m. The wear marks are narrow and shallow, and there are fewer debris and microcrack defects. Conclusion When the target power of ZrB2 is 1.6W, ZrB2-Cu film has the best comprehensive performance.
Key wordsPulsed DC magnetron sputteringZrB2 – Cu thin filmTougheningMechanical properties
. INTRODUCTION
With the rapid development of the extreme working environment and processing technology of modern aerospace and weapons, more and more requirements are put forward for lightweight and high temperature resistant materials. Boride ultra-high temperature ceramic materials have a wide range of application prospects because of their excellent properties such as ultra-high temperature resistance, low density and high strength. Among them, ZrB2 high temperature ceramics are highly concerned by researchers [1]. Due to both ionic bond and covalent bond, ZrB2 crystal has the dual properties of ceramics and metals. It has excellent
physical properties such as high melting point (3245 ),
high hardness (23GPa), electrical and thermal conductivity, good corrosion resistance and oxidation resistance. These excellent properties make it widely used in machining tools, cutting tool coating materials, wear-resistant, corrosion-resistant coating and ultra-high temperature coating, as well as various molding mold protective coating and
turbine blade coating in aviation industry [2]. ZrB2 thin films have been developed since 1970s. The main preparation methods include magnetron sputtering[3], chemical vapor deposition[4], thermal spraying[5], laser cladding[6], etc. Gong Jie [7] and others deposited ZrB2 / AlN nano multilayers by RF magnetron sputtering technology. The effects of working pressure and substrate bias on the structure and properties of the coating were studied. The results show that with the increase of substrate bias and the decrease of working pressure, the hardness and crack resistance of the film are improved. Shappirio, J. R [8] and others prepared ZrB2 thin films by RF two-stage sputtering, and studied their oxidation characteristics and compatibility with aluminum. It was
found that the oxide film formed slowly at 600 and
quickly at 675 , and the film had excellent stability for aluminum at 600 .
Although ZrB2 coating has high hardness, it has a disadvantage of low toughness, which makes the coating easy to crack or even peel off from the substrate under the impact of external force, which greatly hinders its wide application. Therefore, it is very important to study the toughening methods of ZrB2 films. The toughening effect of hard coating is realized by the principle that interfacial strength, dislocations and defects of two phases hinder the generation and propagation of cracks. So far, hard coatings have been toughened by many methods, including second phase toughening, phase transformation toughening, compressive stress toughening, optimizing coating structure toughening [9]. In recent years, the research of two-phase composite structure in second phase toughening is more extensive. The second phase toughening is toughened by multi-phase nano composite. Its structure includes at least two phases: one phase is crystal, the other phase is amorphous; or both phases are crystal. In general, ceramic is used as crystal and soft metal as amorphous layer in ceramic gold nanocomposite coating to form a two-phase cellular structure. Due to the high toughness of soft metal, it can absorb the energy of plastic deformation to prevent the crack generation; when the crack is generated, it can bypass the mechanism or cut through mechanism to expand in the film; at the same time, the interface between the two phases can also hinder the crack growth. At present, soft metals commonly used in
research include Cu, Ni, Ag, CO [10], such as Zr-Cu-N[11]
Ti-Ni-N[12] Ti-Ag-N[13], etc. Li Zhuguo [14] et al. Studied the effect of Cu content on the structure and properties of Ti-Cu-N thin films by changing the sputtering current of Cu
Target by double target magnetron sputtering method. The results showed that when the Cu content was 2%, the crack length between grain boundaries was shortened due to the uniform distribution of Cu grains between tin columnar grains, which made the thin films have superhard properties, and the hardness increased to twice that of pure tin thin films. However, with the increase of Cu content, the hardness of the films decreases obviously. Similar results have been reported in Cu doped TiB2 films [15]. This shows that the content of doped metal phase has a great influence on the performance of the coating.
At present, a few scholars at home and abroad have studied the ZrB2-Cu composite. They used hot pressing sintering method to explore the influence of ZrB2 content and temperature on the compactness and conductivity of the composite [16,17]. The influence of doped metal on the structure and properties of ZrB2-Cu film and the existing form have not been discussed. Therefore, it is very important to study the effect of copper on ZrB2-Cu films. To solve this problem, ZrB2-Cu thin films were deposited by pulsed DC magnetron sputtering. Because the sputtering yield of Cu is obviously higher than that of Zr, and the previous experiments show that even at the lowest starting power (0.3kW), the sputtering yield of Cu from Cu target is still too much, resulting in a significant decrease in the hardness of the film. Therefore, the effect of the relative content of Cu on the structure and properties of ZrB2 thin films was studied indirectly by changing the target power of ZrB2 and keeping the minimum starting power of Cu unchanged.
. EXPERIMENTAL
-
Coating preparation
ZrB2-Cu thin films were deposited on mirror polished cemented carbide (25 mm × 25 mm × 3 mm), 304 stainless steel (40 mm × 30 mm × 1 mm) and single crystal Si (100) substrates by pulsed DC magnetron sputtering (pdcms). The ZrB2 target (99.5%, Zr/B stoichiometry= 1:2) and Cu target (99.99%) were connected to the magnetron sputtering source. Before charging, the substrates were cleaned by ultrasonic cleaning in degreaser, ultrapure water and absolute ethanol for 15 minutes, dried with high purity N2, clamped on the sample plate, hung on the central rotating frame in the vacuum chamber, andthe distance between the target and the substrate was about 80 mm. Vacuum to 3.5×10-3Pa with
rotary pump and turbo molecular pump, heat to 400 in
the vacuum chamber, inject argon to keep the working pressure at 1.2Pa, turn on – 800V bias, and glow discharge for 15min to remove impurities in the furnace and on the sample surface. Keep the bias voltage of – 800V, change the pressure to 0.6Pa, turn on the pulsed DC Cu Target for 8 min. In order to avoid re-sputtering, the bias voltage was adjusted to – 150V, the pulsed DC ZrB2 target was turned on, and the ZrB2-Cu thin film was deposited. The rotating speed of the rotating frame was set to 40rpm, and the deposition time was 240min. ZrB2-Cu thin films with different relative copper contents were prepared by changing the sputtering power of ZrB2
target. The deposition parameters of ZrB2-Cu thin films are shown in Table 1.
-
Structure characterization and mechanical properties test
-
X-ray diffraction (XRD) was used to analyze the phase composition of the films. The monochromatic K ray ( = 0.154nm) from Cu target was used to radiate. The power was 40 kV × 40 ma. The scanning range of diffraction angle (2) was 20 ° to 80 ° and the step width was 0.02. The counting time of each step was 0.2 s. The surface and cross-section morphology of ZrB2-Cu films were observed by s-4800 field emission scanning electron microscope (SEM).
-
The hardness and elastic modulus of the coating were measured by the nano indentation instrument (ttx-nhtcsm instruments) under the dynamic continuous linear loading and unloading mode. In order to eliminate the influence of the substrate on the measurement results, the indentation depth was not more than 1 / 10 of the film thickness [18]. Each sample was indented 10 times and the average value was selected.
-
The film / substrate bonding strength was tested by Anton Paar rst-3 scratch tester. The tip angle of diamond scratch needle was 120 ° and the tip radius was 200 M. During the test, the normal load gradually increases from zero to 100 N, the stroke rate is 1.0 mm / s, and the scratch length is 5 mm. The optical microscope attached to the scratch tester was used to observe the scratch morphology. The critical load of the film was defined as the load at the position where the film began to peel off from the substrate. The average value was obtained by measuring the same sample five times.
Parameter
Value
Base pressure/Pa
3.5×10-3
Working pressure/Pa
0.6
Deposition temperature/
400
Pulsed DC sputtering power(ZrB2 target)/kW
1.21.62.02.4
Pulsed DC sputtering power(Cu target)/kW
0.3
Ar flow ratio /mL/min
150
Distance between target and substrate/mm
80
Parameter
Value
Base pressure/Pa
3.5×10-3
Working pressure/Pa
0.6
Deposition temperature/
400
Pulsed DC sputtering power(ZrB2 target)/kW
1.21.62.02.4
Pulsed DC sputtering power(Cu target)/kW
0.3
Ar flow ratio /mL/min
150
Distance between target and substrate/mm
80
Tab.1 Deposition parameters of ZrB2-Cu thin films prepared by pulsed magnetron sputtering
-
The friction coefficient of the film was tested by Anton Paar tht at room temperature of about 20 and relative humidity of 25% ~ 30%. The diameter of alumina
-
ball with 6 mm was selected as the grinding pair, the normal load was 2n weight, the sliding linear velocity was 0.1 M / s, the rotation radius was 8 mm, and each sample was rotated for 200 cycles. During the test, the computer records the friction coefficient in real time, and the average friction coefficient is expressed by the arithmetic mean value of the friction process entering the stable stage [19]. The cross-sectional area of wear scar was measured by surface profiler, and the wear rate was calculated according to the
formula k = V / (SL), where V is the wear volume, s is the slip distance, and l is the normal load. Ultra depth of field microscope (KEYENCE, vhx-1000c) was used to observe the wear morphology of the films.
RESULTS AND DISUSSION
-
Deposition rate
Figure 1 shows the deposition rates of ZrB2-Cu films at different ZrB2 target powers. It is obvious that the deposition rate increases linearly from10.4 nm/min to16.3 nm/min with the increase of ZrB2 target power from 1.2 kW to 2.4 kW. When the target power is between 1.2 kW and 1.6 kW, the deposition rate increases slowly; when the target power is between 1.6 kW and 2.0 kW, the deposition rate increases fastest; when the target power is between 2.4 kW, the deposition rate increases slowly. When the substrate temperature, bias voltage and working pressure are the same with the incident angle of the particles, the bombardment intensity of the film is mainly determined by the energy of the incident particles, and the energy of the incident particles is closely related to the target power [20]. With the increase of target power, the incident particle flux density and sputtering yield increase, which makes the splashed Zr, B and Cu ions combine more fully, and the thickness of deposition on the substrate surface increases. According to the related theory of thin film growth [21], when the power of ZrB2 target is high, because the energy of incident particles exceeds a certain threshold, the implantation effect occurs. At the same time, the collision between ions heats the gas on the target surface
and dilutes the ion density, which reduces the sputtering yield and limits the increase of deposition rate.
Fig.1 Deposition rate of ZrB2-Cu thin films deposited at different ZrB2 target powers
-
Surface topography
Figure 2 shows the surface morphology of ZrB2-Cu films at different sputtering power of ZrB2 target. It can be seen from Fig. 2 (a) that there are spherical particles with uneven size on the surface of the film at low power, and the surface is rough. With the increase of ZrB2 target power, the surface roughness of the film decreases, and the average size of surface particles decreases, which reaches the minimum when the target power is 2.0kW, indicating that the increase of target power can refine the surface particles of the film. The reason may be that, on the one hand, under the condition of constant temperature, bias voltage and working pressure, the gradually increasing target power improves the bombardment effect of incident ions on the film, thus improving the particle size and flatness of the film surface; on the other hand, as a soft metal, Cu has a certain effect on the grain growth. Wei Chunbei et al. [22] found that when the content of Cu is high, it is easy to aggregate Therefore, the surface roughness of ZrB2 films is related to the relatively high content of Cu in the films when the target power is small.
a 1.2kW
b 1.6kW
c 2.0kW
d 2.4kW
Fig.2 Surface morphology of ZrB2-Cu thin films deposited at different ZrB2 target powers
-
Phase analysis
Figure 3 shows the XRD diffraction patterns of ZrB2-Cu films at different sputtering power of ZrB2 target. It can be seen from the figure that the diffraction peaks of dense hexagonal structure ZrB2 and face centered cubic structure Cu appear in all films, which indicates that both ZrB2 and Cu exist in crystal state. When the targt power of ZrB2 is 1.2kW, ZrB2 shows obvious (001), (100) and (101) diffraction peaks, and grows preferentially along the (101) crystal plane. With the increase of ZrB2 target power from 1.2kW to 2.4kW, the intensity of the three diffraction peaks of ZrB2 increases gradually, and the FWHM of the diffraction peak increases. This is mainly because the increase of ZrB2 target power improves the energy and activity of Zr and B ions, and promotes the crystallization of the deposited particles The
sputtering power reported by Jin et al. [23] is helpful to improve the atomic mobility of the growth surface, and the crystallinity is higher at higher target power. When the target power is small, Cu (111) and weak (200) diffraction peaks appear in the films. Similar phenomena also appear in the studies of Guo Jun [24] and Wei Keke [25]. When the target power increases from 1.2kW to 2.0kW, the diffraction peak intensity of Cu decreases and widens, indicating that the increase of ZrB2 target power will inhibit the crystallinity of Cu and refine the grain size to a certain extent. Zou cunlei [26] believes that Zr and B, as refiners, have significant refining effect on Cu grains.
Fig.3 XRD patterns of ZrB2-Cu thin films at different ZrB2 target powers
-
Mechanical property
The hardness h and elastic modulus E of ZrB2-Cu thin film under different sputtering power of ZrB2 target are shown in Fig. 4. It can be seen that when the target power of ZrB2 is 1.2kW, the film has the minimum hardness of 1.4GPa and elastic modulus of 117GPa. With the increase of target power, the hardness and elastic modulus of the films increase nonlinearly, reaching the maximum at 2.4kW, which are 4.4GPa and 185GPa, respectively. The reason may be that the target power increases the bombardment intensity of the film, and more B elements are splashed out to form strong covalent B-B bond, which increases the hardness of the film The hardness of the film increases with the decrease of grain size [27]. Combined with XRD analysis results, the increase of target power can achieve the effect of grain refinement. At the same time, doping a small amount of Cu can hinder the growth of grains and refine the grains. According to Griffith microcrack theory, fine Cu grains are dispersed between ZrB2 columnar crystals, which shortens the crack length between columnar crystals and improves the quality of the film The fracture strength and hardness of the film were studied [28], so the hardness of the film reached the maximum at 2.4kW. Some scholars found that the hardness corresponding to (001) crystal plane was the maximum for diboride with close packed hexagonal structure. In this experiment, when the target power of ZrB2 was 2.4kW, the diffraction peak intensity of ZrB2 (001) was the maximum, and the hardness was the highest.
Fig.4 Hardness and elastic modulus of ZrB2-Cu films deposited at different ZrB2 target powers
Figure 5 shows the critical loads of ZrB2-Cu films at different target powers. In order to reduce the influence of the hardness of the film and the substrate, the thickness of the film and the interface properties on the critical load, the critical load of the film was determined by comprehensively considering the failure mode of acoustic emission signal and scratch morphology [29]. It can be seen from the figure that the critical load of the film shows an obvious growth trend. When the target power of ZrB2 is 1.2kW, the critical load of the film is the smallest, only 13.8N. When the target power is further increased to 1.6kW, the critical load of the film is greatly improved, and the critical load of the film increases gently with the increase of the target power. This is mainly due to the high target power, which improves the activity and diffusion ability of the deposited ions, and makes the structure of the film substrate interface become compact.
Fig.5 Critical loads of ZrB2-Cu films deposited at different ZrB2 target powers
-
Tribological properties
Figure 6 shows the friction coefficient of ZrB2-Cu films prepared under different sputtering power of ZrB2 target. The friction coefficient is the average value of the stable stage in the selected wear process. It is obvious from the figure that the average friction coefficients of the films are between 0.46 and 0.51. When the target power of ZrB2 is 1.2kW, the film has the lowest friction coefficient, which is about 0.47. However, the surface of ZrB2-Cu film prepared at this power is relatively rough and loose, and the compactness is poor.
Fig.6 Friction coefficient of ZrB2-Cu films deposited at different ZrB2 target powers
Combined with the step tester test, it is found that the
maximum wear scar depth of the film is greater than the thickness of the film, indicating that the film is broken. The
friction coefficient at this time is considered to be the comprehensive average friction coefficient between the substrate and the film, not the thin film The friction coefficient of the membrane is not considered in the analysis. When the target power of ZrB2 is 1.6kW, the average friction coefficient of the film is about 0.49. At this time, the relative content of soft phase copper in the film is the most, which
inhibits the grain boundary sliding. At the same time, the soft phase metal fills the uneven surface in the friction process, which has a certain anti friction effect [30]. With the increase of target power, the average friction coefficient increases slightly. This may be due to the relative content of copper reduction is not enough to provide the necessary lubrication
[31].Fig.7 Surface wear scar morphology of ZrB2-Cu thin films prepared at different ZrB2 target powers
Ultra depth of field microscope was used to observe the wear scar morphology of ZrB2-Cu film after friction and wear experiment, as shown in Figure 7. When the target power of ZrB2 is 1.2kW, the wear scar of the film is the widest, and a large amount of wear debris accumulates on both sides, which is more serious. This may be due to the relatively high content of Cu in the soft phase of the film at a small target power of ZrB2. At this time, the hardness of the film is low, and the adhesion is small. Under the action of shear, the film has a large area of spalling, and the spalling wear debris can not be removed in time, and is pressed into the surface of the wear scar, thus causing new damage to the film Abrasive wear of [32]. When the target power of ZrB2 is 1.6kW, the wear scar of the film is narrow and shallow, and the wear debris and microcrack defects are less. Combined with the friction coefficient and wear rate, the wear resistance of the film is the best. With the increase of target power, the wear scar of the film becomes wider and wider, accompanied by local peeling off. The reason is that with the increase of power, the relative content of ZrB2 in the film increases, the brittleness of the film increases, and it is easier to shear on the surface, which leads to the increase of wear. Therefore, doping appropriate amount of soft phase Cu can improve the wear resistance of the films.
In order to more specifically characterize the wear condition of ZrB2-Cu film after friction test, the cross-sectional area of wear marks is measured by a step meter, and the wear volume of the film is calculated, so as to comprehensively reflect the wear resistance of the coating. The variation law is shown in Fig. 8. When the target power of ZrB2 is 1.2kW, combined with the step meter test, it is found that the maximum wear scar depth of the film exceeds the film thickness, indicating that the film is broken, so it is not considered. When the target power of ZrB2 is 1.6 kW, the wear rate of ZrB2-Cu coating is about 11.32×10-14 m3/N·m. with the increase of target power, the wear rate of the film increases greatly. This is because the increase of ZrB2 target power increases the content of ZrB2 in the film. Due to the
high brittleness of ZrB2, the film is easy to break under the action of friction load, resulting in many fine ZrB2 hard particles. In the process of friction, these small particles that are not discharged in time rub the film back and forth with the friction pair, thus aggravating the wear of the film.
Fig.8 Wear rate of ZrB2-Cu films prepared at different ZrB2 target powers
CONCLUSION
In this paper, ZrB2-Cu thin films were deposited by pulsed DC magnetron sputtering. The effects of different copper content on the microstructure, mechanical properties and Tribological Properties of the films were studied indirectly by changing the target power of ZrB2. The main results are summarized as follows:
-
The results show that the grain size of the films decreases with the increase of ZrB2 target power, and the surface roughness decreases. The ZrB2-Cu films mainly grow along the (101) crystal plane. Meanwhile, the increase of ZrB2 target power will inhibit the crystallinity of Cu and refine the grain size to a certain extent.
-
With the increase of ZrB2 target power, the hardness and critical load of the films increase. When the target power of ZrB2 is 2.4kW, the maximum hardness is 4.4GPa, and the corresponding Cu content in the film is the least.
-
The results show that the average friction coefficient and wear rate of ZrB2-Cu thin films increase with the
-
increase of ZrB2 target power. Doping appropriate amount of soft phase Cu can improve the wear resistance of the thin films.
REFERENCE
-
Zhou Ting, Xie Zheng Fang. Research progress in preparation of ZrB2 ceramics [J]. Progress in chemical industry201332102434-2439.
-
Song Guihong, Du Hao, he Chunlin. Hard and superhard coatings structure, properties, preparation and characterization [M]. Beijing: Chemical Industry Press, 2000,200797-97.
-
Tengdelius Lina, Greczynski Grzegorz, Chubarow Mikhail, et al. Stoichiometric, epitaxial ZrB2 thin films with low oxygen-content deposited by magnetron sputtering from a compound target: Effects of
deposition temperature and sputtering power[J]. Journal of Crystal Growtp015,430:55-62.
-
Zhang Jun, Zhang Lei, Li Guodong, et al. Microstructure and preferential
grain growth of chemical vapor deposited ZrB2 coatings [J]. Journal of materials research, Beijing, China,2017,313168-174.
-
I.A.Podchernyaeva, O.N.Grigoriev, A.D.Panasyuk et al, High-Temperature ZrB2-Based Coatings on Metallic Alloys Produced by
High-Velocity Air-Fuel Thermal Spraying[J]. Powder Metallurgy and Metal Ceramics,2017,5511689-697.
-
Farotade.G.A, Adesina.O.S, Popoola.A.P.I et al. Laser Cladding and Characterization of NiSiCZrB2 Cermet Coatings on Ti6Al4V for
High-Temperature Applications[J]. Metallography, Microstructure, and Analysis,2019,83:349-358.
-
Gong Jie, Liu Mengyin, Wang Haiyuan, et al. Effects of working pressure and substrate bias on the structure and mechanical properties of
ZrB2/A1N nano multilayers [J]. Journal of Vacuum Science and technology, 2011314453-458.
-
J.R.SHAPPIRIOJ.J.FINNEGANR.A.LUX et al. Resistivity Oxidation Kinetics and Diffusion Barrier Properties of Thin Film ZrB2. [J].Thin Solid Films198411923-30.
-
Pei Chen Rui, sun De En, Sam Zhang, et al. Toughening and evaluation of hard ceramic coatings [J]. Surface engineering, China2016,262 1-9.
-
Wang huaiyong. Study on structure and toughness of metal doped TiB2 based coatings [D]. Anhui: Anhui University of technology,2013.
-
J.MusilP.Zeman H.Hruby et al. ZrN/Cu nanocomposite film-a novel
superhard material[J]. Surface and Coatings Technology1999120 179-183.
-
H.R.StockM.DiesselbergH.W. Zoch. Investigation of magnetron
sputtered titanium-nickel-nitride thin films for use as mould coatings[J].Surface and Coatings Technology2008203717-720.
-
Jeon G. HanHyun S. MyungHyuk M. Leeet al. Microstructure and mechanical properties of TiAgN and TiCrN superhard nanostructured coatings[J]. Surface and Coatings Technology2003
174783-743.
-
Li Zhuguo, Yu Hailiang, Wu Yixiong, et al. Deposition of super hard
nc-TiN/nc-Cu nanocomposite films by low energy ion beam magnetron sputtering [J]. Acta metal lurgica Sinica, 2006429993-997.
-
Ji Cheng Ding, Teng Fei Zhang, Je Moon Yun, et al. Effect of Cu addition on the microstructure and properties of TiB2 films deposited by a hybrid system combining high power impulse magnetron sputtering
and pulsed dc magnetron sputtering[J]. Surface and Coatings Technology2018344441-448.
-
Chenchen Wang, Huaijun Lin, Zhiguo Zhang, et al. Fabrication, interfacial characteristics and strengthening mechanisms of ZrB2
microparticles reinforced Cu composites prepared by hot-pressed sintering[J].Joural of Alloys and Comoounds2018748546-552.
-
Wei Shang, Hailong Wang, Shijing Zhao, et al. Processing and
Properties of ZrB2-Cu Composites Sintered by Hot-pressing Sintering[J].Key Engineering Materials2014602-603447-450.
-
Wang Tiegang, Li baisong, Zhang Jiaojiao, et al. Effect of deposition temperature on the structure and properties of AlCrSiN coatings prepared by high power pulsed magnetron sputtering [J]. Rare metal materials and engineering, 20184782578-2584.
-
Wang Tie Gang, Guo Yu Yao, Tang Kuan Yu, et al. Effect of N2 flux ratio on the structure and properties of composite magnetron sputtered Zr-B-N films [J]. Surface technology, 20184711210-217.
-
Liu Yanming. Effects of deposition parameters and N, C doping on the structure and properties of AlB2 type WB2 thin films [D]. Beijing: University of Chinese Academy of Sciences, Beijing, 2015.
-
Wu Ziqin, Wang Bing. Thin film growth [M]. Beijing: Science Press, 2001.
-
Wei Chunbei, Gong Chunzhi, Tian Xiubo, et al. Effect of Cu Zn doping on the microstructure and properties of tin composite films [J]. Journal
of inorganic materials, 20092461231-1235.
-
Yongzhong JinWei WuLi Liet al. Effect of sputtering power on surface topography of dc magnetron sputtered Ti thin films observed by AFM[J].Applied Surface Science200825584673-4679.
-
Guo Jun, Zhang Xiaojuan, Li Peng, et al. Study on properties of AlN/Cu nanocomposite coatings prepared by magnetron sputtering [J]. Journal
of Vacuum Science and technology, 2013,33101002-1006.
-
Wei Keke, Lin Jingjing, Zhang Lin, et al. Effect of Cu content on hardness of tin Cu nanocomposite thin films deposited by pulsed bias arc ion plating. [J]. Vacuum, 2013, 50352-56.
-
Zou cunlei. Preparation and properties of in situ Cu Ti (Zr) – B particle reinforced copper matrix composites [D]. Dalian: Dalian University of technology, 2018.
-
Lu Ke, Liu Xue Dong, Hu Zhuang Lin. hall Petch relationship of nanocrystalline materials [J]. Acta material is Sinica, 1994,85 385-391.
-
CHEN Y, DU H, CHEN M, et al. Structure and wear behavior of AlCrSiN-based coatings[J]. Applied surface science, 2016, 370: 176-183.
-
Du Jun, Wang Hongmei, Wang Xin. Analysis of influence factors on critical load value of scratch bonding strength [J]. Surface technology,
2015449134-139.
-
Song Guihong, Zhang Jingjing, Yang Xiaoping. Effect of Cu content on the structure and properties of tin Cu nanocomposite films [J]. Materials science and technology, 201523163-68.
-
Isaac Asempah, Junhua Xu, Lihua Yu, et al. The role of copper incorporation on the microstructure, mechanical and tribological properties of TiBN-Cu films by reactive magnetron sputtering[J].
Journal of Alloys and Compounds2019,801112-122.
-
Zhang Qinying, Chen Hao, Ren xingrun, et al. Effect of sputtering power of Al target on Microstructure and friction properties of CrAlN coating [J]. Nonferrous metal science and engineering, 201785 109-114.