
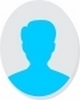
- Open Access
- Authors : Puneeth Kumar N , Dr. Srikantappa A S
- Paper ID : IJERTV11IS080126
- Volume & Issue : Volume 11, Issue 08 (August 2022)
- Published (First Online): 30-08-2022
- ISSN (Online) : 2278-0181
- Publisher Name : IJERT
- License:
This work is licensed under a Creative Commons Attribution 4.0 International License
Temperature and Tool Wear Analysis on Machining of Two Different Composition of C45 Steel
Puneeth Kumar N
Department of Mechanical Engineering (VTU-RC), CMR Institute of Technology
Bengaluru -560037, India
Dr. Srikantappa A S
Department of Mechanical Engineering, Principal and Professor Cauvery Institute of Technology
Mandya -571402, India
AbstractThe study of temperature and wear of tool were analyzed in this work for machining C45 increasing amounts of trace metals like phosphorus and sulphur in steel. Medium carbon steel is steel having carbon percentage of 0.42 to 0.50% and minute amount of sulphur, phosphorus, nickel, and molybdenum were present in it, C45 steel is divided as low, medium and high carbon steel. Shafts, connecting rods, nuts, bolts, and rollers are among the items made from this particular steel. In this study, temperature analysis and the observation of the wear surface of uncoated carbide tool inserts were done using two distinct samples of specific, changing Sulphur and Phosphorus%. The C45 bars were used for machining using uncoated tungsten carbide tool inserts at various cutting speeds (11.0 m/min and 15.58 m/min), varied rates of feed (0.125, 0.175
and 0.225 mm/min), and DOC (0.5, 1 and 1.5 mm). Outcomes revealed that materials with a larger proportion of phosphorous and sulphur trace elements had better machining capabilities, and as a result, traces within a certain amount produce results in better. The behavior and impact on the attributes of a tool sample were also observed.
KeywordsC45 steel, machining, tool wear, and tool tip temperature Introduction
-
INTRODUCTION
According to its carbon content, C45 is a medium carbon steel that has an approximate 0.400.50% carbon content. In the majority of industries, plain carbon steels are utilized extensively because they are simple to work with and affordable [1]. It strikes a nice balance between ductility, strength, and wear resistance. Axles, bolts, torsion bars, light gears, guide rods, shafts, axes, and drills for woodworking, among other things, are made of C45 steel bars. Numerous drill bit varieties, such as twist drills, are constructed of carbon steel, and while the shafts are hot-rolled, they were finished by turning [2]. The quality of the produced steel can be significantly impacted by trace impurities of numerous additional elements. The machinability of medium carbon steel is enhanced by the presence of traces of sulphur in steel [3], and to a lesser extent by phosphorus, which also enhances increases yield strength and corrosion resistance in metals. Sulphur contributes to the soft, chip-breaking discontinuity known as manganese sulphide, and an increase in sulphur improves the material's mechanical characteristics [4]. In order to prevent a built-up edge on the cutting tool, it also functions as a dry lubricant. Turning is a generalized machining operation with a number of benefits, including high material removal rates [5], the ability to produce parts with tight
tolerances, and some degree of surface quality [6]. The benefits of employing carbon-tipped tools include their low cost, capacity for dissipating heat, longevity, ease of replacement, and ability to produce cleaner cuts and finishes [6, 7] [edges stay sharper for longer]. The development uncoated inserts with sufficient hot toughness and strength to withstand greater temperatures produced under high-speed circumstances is a result of cutting tool technology advancements [8]. Review of Due to the enormous amount of heat that will be produced at the point of tool contact during machining, cutting tool temperature is crucial [5]. Tool performance is dependent on the heat as a factor. Number of scientists and researchers are carrying out work to develop new materials and characterize them so that the appropriate material can be selected for specific end use.
To further understand how these components contribute to increasing machinability by lowering the required cutting forces, the present work turns two separate samples of C45 utilizing uncoated tungsten carbide tools.
-
METHODOLOGY
-
Material
Selection of sample and cutting tool inserts Samples tested at NABL accredited metallurgical testing centers as per the test method ASTME 415: 2017/IS 8811-1998. Two samples were determined based on the testing; table 1 outlines the two samples. Table 1 also includes the composition according to the standard.
Table1: C45 Medium carbon steel chemical composition
Composition
Carbon%
S%
P%
Standard
0.40 0.50
0.045 max
0.045max
Sample-1
0.45
1 0.006
0.013
Sample-2
0.45
0.017
0.025
Tool inserts selected – DCMT: D-Diamond shape, 15- Width and 04-Thichness
Figure 1: DCMT tool insert
-
Experimentation
Under dry cutting conditions, In order to process the round bars, two different cutting rates (11.0 m/min and 15.58 m/min) were used. Utilizing uncoated tungsten carbide tool inserts,
different feed rates (0.125, 0.175 and 0.225mm/min) and cut depths (0.5, 1 and 1.5mm) were achieved. These parameters' effects on surface quality, material removal rate, cutting forces, tool flank wear, and tool tip temperature were examined. The specimen had a 3 minute machining time, a 32 mm diameter, and a 150 mm length.
Process parameters like temperature and tool wear determined as follows:
-
The tool maker's microscope is used to measure tool wear, specifically flank wear.
-
Tool tip temperature using thermocouple.
-
-
RESULTS AND DISCUSSIONS
-
Tool wear
Figures 2 and 3 illustrate how tool wear changes as cutting depth increases when turning C45 steel with an uncoated tungsten carbide tool insert under various feed rate scenarios and a speed of 11.10 m/min. The temperature rises as the depth of the cut does, which causes an increase in tool wear. Figures 2 and 3 shows that for C45 steel with lower sulphur percentages, at lower depths of cut tool wear are less on the surface of the tool. When the feed rate is increased, tool wear rises up to a certain cut depth before progressively declining. Temperature and cut depth are the key determinants of tool wear. The graph shows that tool wear is influenced by feed rate as well.
Figure-2: Tool wear with DOC for cutting speed 11.10m/min having lower percentage of S and P.
Figure-3: Tool wear with DOC for cutting speed 11.10m/min having higher
percentage of S and P.
Figure-4: Tool wear with DOC for cutting speed 15.58m/min having lower percentage of S and P.
Figure-5: Tool wear with DOC for cutting speed 15.58m/min having higher percentage of S and P.
Figures 4 and 5 shows the results obtained for higher cutting speed conditions. At moderate feed rate, lower sulphur content will show decreasing tool wear characteristics. At moderate feed rate increase in sulphur and phosphorous percentage has decreased the tool wear.
-
Temperature
At cutting speed of 11.10m/min: During machining, the tool tip's temperature increased linearly as the depth of cut and feed rate increased. But the temperature of the tool was found be comparatively higher while machining sample 1 than sample 2 as evident in figure 6 & 7.
Figure-6: Temperature with DOC for cuting speed 11.10m/min having lower percentage of S and P.
Figure-7: Temperature with DOC for cutting speed 11.10m/min having higher percentage of S and P.
From figure 8 and 9 as the feed rate increases the cutting forces required gradually increases for both sample 1 and sample 2. But the Temperature of sample 2 as shown in figure 9 is comparatively low at feed rate of 0.175mm/min and 0.225mm/min. But at initial feed rate of 0.125mm/min and 0.5mm depth of cut Temperature are more for sample1.
Figure-8: Temperature with DOC for cutting speed 15.58m/min having lower percentage of S and P.
Figure-9: Temperature with DOC for cutting speed 15.58m/min having higher percentage of S and P.
-
Scanning Electron Microscopy
SEM image of the worn-out flank surface of an uncoated tungsten carbide tool insert used to convert C45 steel work material with sulphur 0.006% and phosphorous 0.013%
Figure 10 shows the tungsten carbide tool inserts worn-out flank surface, which was used to machine C45 Steel. The insert sample utilised for speed used for turning 11.10m/min and feed rate 0.225mm/min for depth of cut 0.5 mm showed wider and deeper craters on the surface of the tool. Figure 11 demonstrates that the tool sample used to calculate the speed of 15.58 m/min contains a greater concentration of sulphur and phosphorous trace elements and feed rate 0.175 mm/min resulted in reduced surface degradation because of the lubricating properties of the C45 material. The tool's degraded flank surface is shown in figure 11 depicts the formation of white layer. It is observed that ferrous material has been transported and bonded on to the surface of the tool insert.
Figure 10: SEM image of worn out flank of uncoated carbide tool used to machine C45 Steel material having sulphur 0.006% & phosphorous 0.013%
Figure 11: SEM image of worn out flank of uncoated carbide tool used to machine C45 Steel material havingsulphur 0.017% & phosphorous 0.025%
-
-
CONCLUSIONS
Analyzing the results of the experiment, this resulted in the following findings.
-
Increase in doc increases the wear in the flank of uncoated carbide tipped tool, at greater feed rates and cutting speeds, tool wear will be minimal and flank wear will be reduced.
Temperature plays the major role in turning operation;
-
When cutting at a speed of 11.10 m/s: The temperatures of tool tip were increasing linearly when the feed rate and doc increase. But the temperature of the tool was found be comparatively higher while machining sample 1 than sample 2.
-
At cutting speed of 15.58m/min: It is observed that sample 2 has very good results in terms of tool tip temperature. The tool tip temperature was comparatively higher for sample 1 than sample 2 while machining at feed rate of 0.225mm/min.
REFERENCES
[1] M. Riaz The Mechanical Properties of S45c Medium Type Carbon Steel Specimens under Lathe Machining and Quenching Conditions [2] Changyou Li , Weibing Dai, Fei Duan, Yimin Zhang and David Fatigue Life Estimation of Medium-Carbon Steel with Different surface roughness Journal of applied sciences, Published: 29 March 2017 [3] Debanshu Bhattacharya Effect of Sulfur and Zirconium on the Machinability and Mechanical Properties of AISI 1045 SteelsJune 1981, Volume 12, Issue 6, pp 973985 [4] Richard Gundalch, Matthew Meyer, Leonard Winardi Influence of Mn and S on the properties of cast iron part3-Testing and AnalysisCopyright © 2015 American Foundry Society [5] Farag Abdallah, Sabreen A. Abdelwahab, Wael. A. Aly, Ibrahim Ahmed Influence of cutting factor on the cutting tool temperature and surfaceroughness of steel C45 during Turning processvolume 6, issue -01,
IRJET,2019
[6] Dr. Srikantappa. A.S, Shiva kumara. C. M, Adaveesha. B Tool Characteristics for better Performance in machining OHNS Steel using Tungsten Carbide tool inserts ICIMA 2018-P2-3003-IJMMM [7] Eugene E. Feldshtein and Szymon Wojciechowski Wear of carbide inserts during turning of C45 steel in dry cutting conditions and in presence of emulsion mistE3S Web of Conferences 19, 03009 (2017)DOI:10.1051/e3sconf/20171903009EEMS 2017
[8] G Sridhar Failure analysis of free-cutting grade steels: A case studyProceedings: Cofa-1997©Nml Jamshedpur; pp. 121-139
[9] Chetan Darshan, Paprinder Singh, Sanjeev Saini, Rajat Goswami Comparative Evaluation of Untextured and Textured WC Inserts Under Dry and near dry machining of c45 steel. IJGET – ISSN(P):2278- 9928;ISSN(E):2278-9936Vol. 6, Issue 5, Aug Sep 2017; 1-16 [10] Narinder Gupta, Naveen Singla and Kanwal jeet Singh Analysis of Machining Properties in Dry, Near Dry & Wet Machining on EN9 SteelInternational Journal of Engineering Research & Technology (IJERT) Vol.3 Issue8, August-2014ISSN: 2278-0181 [11] Pedro I. Ezeanyagu1 and Sam. N. Omenyi Effect of Cutting Parameters on Feed Cutting Force and Estimation of Feed Cutting Force in Dry Orthogonal Turning International Journal Of Multidisciplinary Sciences And Engineering, Vol. 6, No. 9, September 2015 [12] T.Senthil Kumar, G.Mahadevan, T.R.Vikraman Evaluation of Surface Finish on Machining of Mild Steel Using High Speed steel Tooling lathe with Normal Coolant (or) Nano material added coolant. IOSR Journal of Mechanical and Civil Engineering(IOSR-JMCE)e-ISSN: 2278- 1684,p-ISSN: 2320-334X, Volume 11, Issue 3 Ver. V (May- Jun. 2014), PP 01-09