
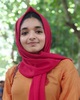
- Open Access
- Authors : Suhana Navas , Ruksana S , Riya Junaid , Aleeaha M Ali, Anees Beegom H
- Paper ID : IJERTV11IS070257
- Volume & Issue : Volume 11, Issue 07 (July 2022)
- Published (First Online): 04-08-2022
- ISSN (Online) : 2278-0181
- Publisher Name : IJERT
- License:
This work is licensed under a Creative Commons Attribution 4.0 International License
Sustainable Building Replacing Normal Construction Materials with Sustainable Materials
Suhana Navas, Ruksana S, Riya Junaid, Aleesha M Ali
Civil Engineering Students
Mes Institute of Technology And Management Kollam, Kerala
Prof. Anees Beegom H
Dept. of Civil Engineering
Mes Institute of Technology And Management Kollam, Kerala
Abstract The construction industry of the world is rapidly developing with the abrupt increase of the urban population. To meet the needs of the evolving industry and the surging population, the need of raw materials for the construction industry is rising day by day. Energy consumption in the building sector is very high. Carbondioxide emission are connected with offsite manufacturing of building materials and components ( cradle to site) . the materials such as cement ,hollow concrete block, bricks, reinforcement bars etc. emit unconsiderable amount of carbondioxide during the manufacturing process.. Embodied energy can be consumed directly in construction of building and other relative processes or indirectly for extracting raw materials manufacturing the building materials and relative products and transporting. In the present study we are entirely replacing the traditional material with sustainable material. Construction industry consumes more than fifty percentage of the raw materials obtained from the earths crust. In the nearby future these resources will get emptied. So it's time to find the suitable sustainable alternative for the building components. Geopolymer concrete is the new development in the field of building construction in which cement is totally replaced by pozzolanic material like fly ash and activated by alkaline solution. This gives the effect of concentration of sodium hydroxide, temperature and duration of overheating on compressive strength of fly ash based geopolymer concrete. The Wool Glass Shell Brick (WGSB) is filled with waste materials from plants and other industries. Bamboo reinforced concrete construction follows the same design, mix proposition and construction techniques as used for steel reinforced. Steel reinforcement is replaced with bamboo reinforcement. Natural materials, bamboo has been widely used for many purposes. Mainly as a strength bearing material. Then wool glass shell brick, geopolymer concrete slab reinforced with bamboo, and geopolymer concrete block are manufactured. The manufactured materials are subjected to their respective tests and prototype is also constructed. From the study of materials, it is observed that percentage economy can be achieved using this sustainable material .The test results showed that the compressive strength, tensile strength and of the manufactured materials are much better than the conventional construction materials.
-
INTRODUCTION
Today construction industry uses more raw materials by weight than any other industrial sector. Greenhouse gas emissions by India are the third largest in the world and the main source is cement. To minimize the consumption of non renewable raw material by construction industry, finding an adequate substitute that is sustainable and has no disadvantage to the environment is indispensable. Recently, the drive to find more
sustainable alternatives in the construction industries is high. Geopolymer concrete is the new development in the field of building construction in which cement is totally replaced by pozzolanic material like fly ash and activated by alkaline solution. This gives the effect of concentration of sodium hydroxide, temperature and duration of overheating on compressive strength of fly ash based geopolymer concrete. Wool glass shell brick (WGS) is one of our new innovation, which is prepared by using the materials such as clay, wool, glass powder, egg shell, iron oxide, and magnesium oxide. The brick is of low cost than the normal available brick. The materials used in this are recycled from different industries and organic matters, it is very economical and eco-friendly. Strength of the WGS brick is 3 times more than that of the normal brick, and the size and shape of the WGS brick is the same as that of the usual brick. Bamboo is frequently referred to as a highly renewable and high strength alternative material to timber and, occasionally, as strong as steel reinforcement for concrete. Bamboo reinforced concrete slab construction follows the same design, mix proposition and construction techniques as used for steel reinforced. steel reinforcement is replaced with bamboo reinforcement. Compressive strength of the bamboo reinforced concrete is higher than that of steel reinforcement. Bamboo is readily available in many tropical and subtropical locations, whereas steel reinforcement is relatively more expensive..
-
EASE OF USE
-
Significance
The construction industry ,by its very nature , is a big user of natural resources . but with growing concerns over climate change and the finite nature of these resources , there is increasing pressure on construction firms to reduce their environment impact.
-
Data collection
To create our sustainable building we have researched for the suitable , sustainable and economical raw materials and their respective sources . we have studied various journals and reports related to sustainable construction
-
Collection of raw materials
Our sustainable building is made up of geopolymer concrete , wool glass shell brick, bamboo reinforced slab and columns . The materials required for geopolymer concrete are fly ash , ground granulated blast furnace slag, sodium hydroxide
,sodium silicate, fine aggregate, coarse aggregate and for wool glass shell brick are glass powder , wool , iron oxide
,magnesium oxide ,calcium oxide, silica sand and alumina clay.
-
Sustainable Construction material substitutes
GEOPOLYMER CONCRETE: Concrete is the most widely used material in existence and is only behind water as the planet's most consumed resource. Here cement concrete is replaced by geopolymer concrete Geopolymer binding material is made to act as the substitute for the cement. The constituents of geopolymer concrete are fly ash, GGBS, fine aggregate, coarse aggregate, sodium silicate solution, sodium hydroxide and water.
Compound
Weight (Kg/m3)
Fly ash
408.31
GGBS
450.36
Fine aggregate
703.20
Coarse aggregate
1243.08
Sodium silicate solution
145.8
Sodium hydroxide
30.33
Water
As needed
Geopolymer depend on thermally activated natural materials like meta kaolinite or industrial by product like fly ash or slag to provide a source of silicon and aluminium. These silicon and aluminium is dissolved in an alkaline activating solution and subsequently polymerises into molecular chains and become the binder. The reaction of Fly Ash with an aqueous solution containing Sodium Hydroxide and Sodium Silicate in their mass ratio, results in a material with three dimensional polymeric chain and ring structure consisting of Si-O-Al-O bonds. Water is not involved in the chemical reaction of Geopolymer concrete and instead water is expelled during curing and subsequent drying. This is in contrast to the hydration reactions that occur when Portland cement is mixed with water, which produce the primary hydration products calcium silicat hydrate and calcium hydroxide. This difference has a significant impact on the mechanical and chemical properties of the resulting geopolymer concrete, and also renders it more resistant to heat, water ingress, alkali aggregate reactivity, and other types of chemical attack.
Table 1 :components of geopolymer concrete BAMBOO REINFORCED SLAB
Bamboo reinforced slabs is made of geopolymer concrete and bamboo reinforcement . its construction follows same design , mix proportions and construction techniques as used for steel reinforced. Just steel reinforcement is replaced with bamboo reinforcement. Bamboo is biodegradable and renewable in nature .it is energy efficient as it is for natural origin and environmentally sustainable in nature .selection of bamboo for reinforced can be done based on these factors ; Color and age
: employ bamboo having an evident brown color . this shows the age of bamboo to be at least 3 years . Diameter : use the
one with long large culms Harvesting : try to avoid those bamboos that are cut either during spring or summer seasons . Species : among 1500 species of bamboo, the best one must checked , tested to satisfy the requirement as a reinforcing material The properties of bamboo for reinforced concrete are:
-
It hold very good tension and compressive strength. Flexural strength of the beam having bamboo reinforcement shows greater strength. . As construction materials bamboo has a very strong fibre. Bamboo has a higher tensile strength than many alloys of steel.
WOOL-GLASS-SHELL BRICK
Wool glass shell bricks are made by adding wool fibres, glass powder, egg shell to the clay material which is riched in alumina and silica. The regular clay material was replaced by 20% with these waste materials . To test the feasibility of incorporating this waste into brick material, we study examined the reuse of glass wool as a fluxing agent in the production of clay bricks. This is a more sustainable and healthy alternative to conventional building materials such as baked earth bricks and concrete blocks.
Components of wool glass shell brick are :
WOOL The wool fibres improve the strength of compressed bricks, reduce the formation of fissures and deformities as a result of contraction , reduce drying time and increase the bricks resistance to flexion .
GLASS POWDER Waste glass is a major component of the solid waste stream in many countries. In this experiment We replace a portion by waste glass powder. It has the capacity to makes the resulting brick more stronger, durable and more water resistant. The process is environmentally friendly since it reduces the amount of glass that ends up in landfills around the world.
Sources of waste glass : · Glass food and beverages container.
-
Window repair shops · Glass decorative items · Old tube lights
, electric bulbs · Glass polishing and glass window and door manufacturing shop
EGG SHELL POWDER
Egg shell functioned as a bio-filter and sintering aid added into earthenware clay compounds to make fire clay bricks via extrusion process. The main composition of egg shell is calcium carbonate (CaCO3) while the main composition of earthenware is aluminosilicate (Al2O3.2SiO2.2H2O) and other oxide compounds.
-
-
Manufacturing of Geopolymer Concrete slab and Wool Glass shell Brick
CASTING PROCEDURE
Mixing of the components of geopolymer concrete mixture is done conventionally by hand and trowel. In this mix, the materials used are ground granulated blast furnace slag, fly ash, sodium hydroxide solution, sodium silicate solution, Sand, Coarse aggregate of below 12mm size and a sufficient amount of water. The dry ingredients are mixed and water is added slowly until the mix is workable. This mixture may need to be modified depending on the aggregate used to provide a concrete of the right workability.
MIXING OF MATERIALS FOR GEOPOLYMER CONCRETE
:
The materials used for the conventional mix are GGBS, fly ash, fine aggregate, Coarse aggregate of below 12mm size and sufficient water. The coarse aggregate and fine aggregate are mixed thoroughly and kept aside. The GGBS and fly ash are weighed and mixed measured sodium silicate is added to it.15N NaOH is added to catalyze the reaction and to achieve its binding property. Fine aggregate and coarse aggregate is added and mixed together with trowel until a 31 uniform colour is obtained, to this mixture coarse aggregate is added stage by stage and a uniform mixture is achieved. Then water is added carefully making sure no water is lost during mixing. While adding water care should be taken to add it in stages so as to prevent bleeding which may affect the strength of concrete. Another important constituent in geopolymer concrete is its reinforcement. The reinforcement material used here is Bamboo reinforcement. The bamboo is made to size as required. Raw unrated bamboo is used here s reinforcement.
MATERIALS
MIX PROPORTION (%)
Fly ash
40
GGBS
45
NaOH
12
Na2SiO4
3
Table 2 : Mix proportion of Geopolymer concrete
BAMBOO REINFORCED GEOPOLYMER CONCRETE SLAB
Plywood mould of size 30*30*6.5 cm for test specimen slab and 64*64*.5 cm for the slab to be placed at the prototype. The mould was lined with plastic sheets to prevent expansion of the mould and loss of water. GGBS, Fly ash and the chemicals Sodium Silicate and Sodium hydroxide constitute mixture 1. The mixture 2 consist of fine aggregate and coarse aggregate. These are mixed together thoroughly. Mixture 1 and Mixture 2 are mixed and water is added until it reaches its required consistency. A uniform paste1 is obtained. The bamboo is tied in a mesh form. A part of the paste1 is poured into the mould up to its half. The Bamboo mesh is placed above a part of the paste 1 and the rest of the slab is filled with the paste1. 24 hours setting time is given for the proper setting of the slab. The setted slab is put into the curing tank for 7 days.
Fig 1 : bamboo reinforced geopolymer concrete slab GEOPOLYMER BINDING MATERIAL
GGBS, Fly ash and the chemicals Sodium Silicate and Sodium hydroxide constitute mixture 1. It is then mixed with fine aggregate and water and a uniform paste 2 is obtained. This paste is used as the binding material for the prototype to replace cement grout.
WOOL GLASS SHELL BRICK
The clay-rich in silica and alumina is mixed with wool, glass powder and egg shell powder. Adequate amount of water is added to the mix. The mix is first mixed manually and then it is subjected to machine mixing. The mix comes out of the machine and is subjected to cutting immediately in the brick dimension 20*10*10 cm. Brick making is done in a brick making plant.The brick is sundried for a week. After drying the brick is placed in the kiln and baked.
Materials
MIX PROPORTION (%)
Clay
75
Glass powder
10
Egg shell powder
5
wool
10
Table 3: Mix proportion of wool glass shell brick
Fig2 : wool glass shell brick
. TEST ON THE MANUFACTURED SUSTAINABLE CONSTRUCTION MATERIALS
-
TEST ON WOOL GLASS SHELL BRICK
CRUSHING STRENGTH TEST: Compressive strength test on bricks are carried out to determine the load carrying capacity of bricks under compression with the help of compression testing machine.
-
To determine the compressive strength of wool glass shell brick, The brick specimen are immersed in water for 24 hours. After that the specimen is placed in compression testing machine with 6 mm plywood on top and bottom of it to get uniform load on the specimen. Size of the specimen is 19*9 m
. After placing the brick in compression testing machine , 36 apply load on it until the brick breaks. At 180 KN , the brick get broken and noted. Then the crushing strength is the ratio of crushing load to the area of brick loaded. Average of five specimen is taken as the crushing strength OBSERVATION
Fig 3: Compressive strength testing on brick
-
Applied load = 180 KN
-
Compressive strength of brick = 10.52 N/mm2
-
RESULT Compressive strength of brick = 10.52 N/mm2
-
WATER ABSORPTION TEST :Water absorption test on bricks are conducted to determine durability property of bricks such as degree of burning ,quality and behaviour of bricks in weathering .A brick with water absorption of less than 7% provides better resistance to damage by freezing. To determine the water absorption capacity of wool glass shell brick, The dry specimen is put in an oven maintained at a temperature of 105 to 115o C, till it attains substantially constant mass. After cooling specimen at room temperature weight of specimen recorded as W1. The dry specimen is then immersed completely in the water at a temperature of 27 ± 2 o C for 24 hours. Take out specimens from water and wipe all water from its surface with a wet cloth. Complete weighing of the specimen, 3 minutes after the specimen has been removed from the water. Let this weight be W2. Water absorption after 24 hours immersion in cold water is given by (W2 W1) x 100 / W1
-
OBSERVATION: Weight of dry brick ,W1 =3.1 kg Weight of water absorbed brick ,W2 = 3.34 % of water loss = (3.34-3.1)*100/3.1 =7.74%
-
RESULT Water absorption of wool glass shell brick = 7.74
%
-
HARDNESS TEST A good brick should resist the scratches against sharp things . so , far this test a sharp tool or finger nail is used to make scratch on brick. We observed that there is no scratch impression on brick then it is said to be hard brick.
-
SHAPE AND SIZE TEST: The shape of bricks should be purely rectangular with sharp edges . standard brick size consists length * breadth * height as 19cm *9cm* 9cm .To perform this we select 20 bricks randomly from brick group and stack them along its length , breadth, height and compare. 38
IV. SOUNDNESS TEST Soundness test of bricks shows the nature of brick against sudden impact . in this test , we choose
2 bricks randomly and struck with another . then sound produced should be clear bell ringing sound and brick should not break so
-
STRUCTURE OF BRICKS: To know the structure of bricks , pick one brick randomly from the group and break it. We observed that the inner portion of brick clearly . It is free from lumps and homogeneous VI.
-
COLOR TEST :Wool glass shell brick possess bright and uniform color throughout its body VII.
-
EFFLORESCENCE TEST A good quality brick should not contain any soluble salts in it. If soluble salts are there , the it will cause efflorescence on brick surfaces. To know the presence of soluble salts in a brick , we placed it in a water bath for 24 hours and dry it in shade . After dried, observed the brick surface thoroughly . there is no any white or grey color deposits
, then it is used for construction
-
TEST ON GEOPOLYMER CONCRETE
Fig 4: compressive strength testing on geopolymer concrete
-
COMPRESSIVE STRENGTH TEST Compressive testing is conducted to be observed the effect of retarder addition on the compressive strength of the geopolymer concrete. AIM: To determine the compressive strength of geopolymer concrete 39 PROCEDURE The concrete specimen are immersed in water for 24 hours. After that specimen is placed in compressive strength testing machine with 6mm plywood on top and bottom of it to get uniform load on the specimen .the size of the specimen is 15*10 cm .The specimen is then placed in the machine in such a manner that the load shall be applied gradually The maximum load at failure was taken . Here specimen fails at the rate of 1100 KN . Then compressive strength can be calculated by using the equation : Compressive strength = load at failure / area of specimen
-
OBSERVATION: Area of specimen = 15*10 cm Load at failure of specimen = 1100KN Compressive strength = 1100/15*10 = 73 Mpa
-
RESULT Compressive strength of geopolymer concrete = 73 Mpa
-
TEST ON BAMBOO REINFORCEMENT SLAB
-
COMPRESSIVE STRENGTH TEST :To determine the compressive strength test on bamboo reinforced slab, After 7 days of curing , the specimen is placed in compression testing machine with 6 mm plywood on top and bottom of it to get uniform load on the specimen. The compressive strength test is carried out on a specimen of size 30* 30 cm. After placing the slab in compression testing machine , apply load on it until the slab breaks. At 1800 KN the slab get broken and noted. Then the crushing strength is the ratio of crushing load to the area of slab. Fig 4.13 compressive strength testing on bamboo reinforced slab 41
-
OBSERVATION Area of the specimen = 30*30 cm Load at the failure of specimen = 1800KN Compressive strength = 1800/30*30 = 20 Mpa.
Fig5: Compressive strength testing on bamboo reinforced slab
-
RESULT
Compressive strength of bamboo reinforced slab = 20 Mpa. Use either SI (MKS) or CGS as primary units. (SI units are encouraged.) English units may be
used as secondary units (in parentheses). An exception would be the use of English units as identifiers in trade, such as 3.5- inch disk drive.
-
-
ECONOMICITY
Rate of Geopolymer concrete is same as that of normal concrete.
Rate of Wool glass shell brick is same as normal brick.
SUSTAINABLE MATERIALS
TRADITIONAL MATERIALS
1 ton GGBS : Rs 3500
1 ton fly ash : Rs. 1400
1 metric ton NaOH :Rs19000
:from waste
Lime: 1ton Rs.5500
Aluminium hydroxide:1ton Rs.1400
-
GEOPOLYMER CONCRETE
-
Bamboo : 1ton Rs.4000
-
Wool glass shell brick Clay rs.200 /ton
-
Wool glass egg shell
-
NORMAL CONCRETE
-
STEEL : 1 ton Rs.44000
-
NORMAL BRICK clay
Rate of bamboo reinforcement is very low as compared to normal reinforcement
-
-
CONCLUSION
Wool glass shell brick has found to be compressive strength of
10.52 N/mm^2 .It has 3 times more stronger than the ordinary brick. So it is useful for construction purpose .Compressive strength of geopolymer concrete has found to be 3 times more stronger than the normal concrete .ie, compressive strength of geopolymer concrete = 70 Mpa and normal concrete = 25 Mpa. Also compressive strength of bamboo reinforced slab is found to be 20 Mpa , it is more stronger than the steel reinforcement ( ie, 17 Mpa ) . All these sustainable materials attains suitable compressive strength .Therefore it is useful for construction purpose .Conventional building materials can be replaced suitably with innovative building components without compromising the strength and durability of the structure made by it and satisfying cost efficiency criteria. Use of innovative materials with sustainable application such as wool, glass etc. can have considerable benefits including finding the best optimization in energy consumption of the region, reducing environmental degradation. Cost efficiency in construction sector can be achieved by adopting economically cheaper and locally available building materials, thereby reducing the usage of high quantity of conventional building materials and components. Cost comparison studies through the experiments show that the sustainable building achieve a good percentage economy in both material cost and overall cost.
REFERENCES
[1] Suchampa Bagchi, Assistant Professor, Department of Civil Engineering. JSRREC R Rashmi Mano, Assistant Professor,Department of Civil Engineering. JSRREC N Thangam, Assistant Professor, Department of Civil Engineering. JSRREC in 2018 Bamboo as a Building Material. [2] Yuecheng Xin, Abbas Mohajerani, Halenur Kurmus and John V. Smith in 24 november 2020 possible recycle of waste glass in sustainable fried clay bricks. [3] LuÃs Gil Laboratório Nacional de Energia e Geologia, I. P., Estrada do Paço do Lumiar, 22, Edf. C, 1649-038 Lisboa, Portugal 20 November 2014 / Accepted: 4 February 2015 / Published: 10 February 2015 New Cork-Based Materials and Applications. [4] Ruy A. Sá Ribeiroa,b,* (ruy@desari.com.br), Marilene G. Sá Ribeirob (mlene@desari.com.br), Kaushik Sankara (sankar3@illinois.edu) , Waltraud M. Krivena (kriven@illinois.edu) aDepartment of Materials Science and Engineering, University of Illinois at UrbanaChampaign, Urbana, IL, 61801 USA Geopolymer-bamboo composite – sustainable construction material. [5] Anant L. Murmu, A. Patel Towards sustainable bricks production in 2018 about construction and building materials. [6] M.T ABDULALEEM, P.D ARUMAIRAJ international journal of engineering science and emerging technology in 2012 based on geopolymer B. Noble, and I.N. Sneddon, On certain integrals of Lipschitz-Hankel type involving products of Bessel functions, Phil. Trans. Roy. Soc. London, vol. A247, pp. 529-551, April 1955. (references)