
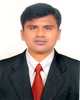
- Open Access
- Authors : Harish H , U N Kempaiah
- Paper ID : IJERTV10IS010239
- Volume & Issue : Volume 10, Issue 01 (January 2021)
- Published (First Online): 03-02-2021
- ISSN (Online) : 2278-0181
- Publisher Name : IJERT
- License:
This work is licensed under a Creative Commons Attribution 4.0 International License
Studies on Process Feasibility of using Acetylene and Diesel as A Fuel in CI Engines
Harish H
Research scholar Department of Mechanical Engineering,
UVCE, K R Circle, Bengaluru-560001, India.
U N Kempaiah
Professor
Department of Mechanical Engineering , UVCE,K R Circle, Bengaluru-560001, India.
Abstract:- Necessity for replacement of fuel is growing at a rapid rate since transportation and industry fields are growing widely. Researchers throughout the world are searching for a better alternative than fossil fuels. Acetylene gains advantage over other fuels for its characteristics like high flammability, good calorific value, low cost and Exceptional combustion characteristics. Additionally Acetylene as a fewer carbon content related to supplementary fuels, plays a vital role in environment deprivation. In this paper an effort has made to check the Performance Combustion and Emission characteristics of CI engine using acetylene as a fuel at various flow rates (1lit/min,2lit/min,3lit/min). The brake thermal efficiency at full load for neat diesel was found to be 34% and for blends it was (33%) for 1lpm of Acetylene (34.51%) for 2lpm of Acetylene(35%) for 3lpm of acetylene. fuel consumption decreased by 7.08% for 3lit/min of acetylene when related with baseline diesel. CO emission was maximum for diesel. The peak pressure is reaching 58.34 bar at full load for Baseline diesel. However the pressure showed increasing trend for Acetylene induction. The pressure inside the cylinder after acetylene induction was found to be 62, 66 and 70 bar at full load for 1lpm , 2lpm and 3lpm respectively. Under dual fuel mode at full load the HRR was found to be 58.34 (J/0CA), 62.67(J/0CA) and 66.12(J/0CA) 1lpm , 2lpm and 3lpm respectively. HRR for Base line diesel under full load was 56.12(J/0CA).Results showed a decrease trend in CO emissions for blended acetylene at different flow rates. At full Load NOx emission was maximum for diesel(1242PPM) .The NOx emissions for blends were (1218), (1239) and (1363) ppm for1Lpm ,2Lpm 3Lpm respectively. The maximum HC emission was shown for diesel at full load and when compared to acetylene at various flow rates showed a decreased trend. Since optimum engine performance has been observed, it can be concluded that Acetylene can be successfully used in C.I engines as an alternative and Optimal results were obtained for 3lpm of acetylene injection.
-
INTRODUCTION
It is been observed that there is a steep increase in the vehicles and automobile sector. Countrys Economy is affected due to substantial usage of fossil fuels. The Nations Progress depends on how much energy resource is available and how well a country is able to utilize it. The environment pollution from vehicles has big Challenge of Acid Rain and climatic change. Henceforth governments in the world have been concentrating on Utilization of renewable energy resources has to look into Environment degradation. Research is been carried out to check the feasibility of alternative fuels in IC engines. This has led to many alternatives like CNG, LPG, Methanol, Ethanol, Acetylene, Bio diesel and biomass
resources. The primary requirement of Alternative fuel is its availability Cost and Good calorific value. Our study is to check the feasibility Acetylene and it can give better performance on par with Diesel engine. Research has been carried out using acetylene as a primary fuel and alcohol as a secondary fuel. It was noted that introduction of alcohol reduced the cylinder temperature of the engine (1). Acetylene has a great potential to substitute Fossil fuels. Acetylene with good calorific value and excellent Combustion Characteristics is definitely a future fuel to look into. Experiments were conducted on SI engine using Acetylene as a fuel and results were tabulated. (2) Nagarajan and Lakshmanan Worked on the efficiency and the quality of emission in diesel engine, to Inject Acetylene at various flow rates. Fixed amount of 3L/m of acetylene is delivered in dual fuel mode. The outcomes of using diesel as primary fuel under various loads were tabulated. The air articulated acetylene ended with slight lower efficiency.CO and HC emission reduced considerable when related with baseline diesel. NOx formations significantly increased as acetylene was inducted to the cylinder (3). Shaik Khader Basha, P.Srinivasa Rao et al The Tests were conducted with known quantity of acetylene flow rates from 0.1Lit/min to 5Lit/min with an increment of 0.5Lit/min in every step.The primary objective was to find the moderate acetylene flow rate and to reduce emissions. On tabulating the results the efficiency of acetylene was nearer to Diesel with reduction in emissions Due to its promising characters acetylene is definitely the best alternative with safe operation and slight increase in Smoke and NOx. According to Roshan Raman and Naveen kumar when they conducted Experiments on Acetylene at various flow rates of LPM (2, 4, 6 and 8) and compared it with base diesel they found that optimal results were found for a maximum load of 4 lpm. It was resolved that Acetylene can be effectively utilized at 4lpm. (5) Research has also been conducted by varying the compression ratio (18, 19, 20, 21
and 22) and flow rate of acetyleneof 60, 120, 180 and 240 litres per hour. Optimal results were found at 120 litre per hour and the optimum Compression ratio was found to be 21. Hydrocarbon smoke emissions and Carbon monoxide were found to be lower with bit increase in Nox Emission when related with pure diesel.(6) Deepak kumar T and Manjunatha worked on exploration of B20 fish Biodiesel in diesel engines blended with waste Plastic oil. t was noted that the BTE of blends was 9.5% increased than that of diesel. Due to higher oxygen content in blending mixture led to better combustion of Fuel with increased cylinder pressure. HC and CO
decreased to certain extent in blends when related with diesel. Conclusion were drawn that plastic oil blended with fish Biodiesel can be one of the promising alternate fuel (7). Renewable energy can be used to major prospective thereby reducing the usage of fossil fuels. Without any Adjustments in CI engine C2H2 gas was used by parallel production and Variable gas flow technique. It was noted that the C2H2 gas was more cost effective and optimal flow rate was found without compromising on efficiency (8). Research Trend shows that there is enormous scope for emission reduction and cylinder technologies. Developed countries are working upon the technology of using the major energy share with gaseous fuels like acetylene in engines as it is richly available and easily produced (12). Experiments were done on petrol and diesel engines in duel fuel mode by using acetylene and alcohol. Results reflected that there is a considerable improvement in BTH, and clean burning was noted. Engine life increased when compared with traditional engines (13). Intensive research was done on acetylene in homogeneous charged compression ignition (HCCI) operating mode. The results stated that NOx and Smoke Opacity reduced considerable wheras efficiency was almost same as that of diesel. Most of the researchers have recommended PMI and EGR technique to reduce NOx Emissions when gaseous fuel are used in CI engines(15).
-
METHODOLOGY
Trials were done on a single cylinder, four stroke, water cooled Diesel engine [KIRLOSKAR MAKE] to study the Efficiency and Emission characteristics of Acetylene as a fuel. Figure 1 shows the various parts of the test engine. Eddy Current dynamometer was used to control Torque and in turn loading on engine. Digital computer synchronized with data acquistion system comprising of sensor was used to note Torque load, Speed, fuel intake and BMEP etc. AVL di-gas analyzer was used to measure the Exhaust Gas Emissions.
Initially the diesel engine was warmed by running it for 20 minutes with diesel. Trials were conducted with increase in Torque (Loading). The trials were carried out at fixed speed of 1800 rpm by increasing the loads ranging from 0%, 20%, 40%, 60%, 80% and 100%. Acetylene was injected upto 36% by volume using timed manifold injection (TMI) technique. At 0% loading condition, the flow rate of diesel was found to be 0.78kg/hr. Diesel flow was reduced upon the induction of acetylene in the range of (1lt/min, 2lit/min, 3lit/min) until the engine attained rated speed of 1800rpm.
Figure1: Diesel engine test rig
Figure 2: Schematic Diagram of Experimental set up
1 = Control Panel
2 = Computer system
3 = Diesel flow line 4 = Air flow line
5 = Calorimeter
6 = Exhaust gas analyzer 7 = Smoke meter
8 = Rota meter 9= Inlet water temperature
10= Calorimeter inlet water temperature
11= Inlet water temperature
12 = Calorimeter outlet water temperature
13 = Dynamometer 14 = CI Engine
15 = Speed measurement
16 = Burette for fuel measurement 17=Exhaust gas Outlet 18= Outlet water Temperature
Table 1: Specification of engine
Manufacturer
Kirloskar oil Engines Ltd
No of Cylinder
1
Model
TV-2
Type of Engine
Vertical, 4-Stroke cycle, Single
Fuel
Diesel
Cooling
Water
HP
16HP
Bore
87.5mm
Stroke
110mm
Starting
Hand Cranking
Cubic Capacity
1322cc
Nominal Compression Ratio
17.5:1
Inlet valve opens BTDC
4.5 Deg
Exhaust valve opens BTDC
35.5 Deg
Inlet valve closes ATDC
35.5 Deg
Exhaust valve closes ATDC
4.5 Deg
Cubic Capacity
1322cc
Nominal Compression Ratio
17.5:1
Inlet valve opens BTDC
4.5 Deg
Exhaust valve opens BTDC
35.5 Deg
Inlet valve closes ATDC
35.5 Deg
Exhaust valve closes ATDC
4.5 Deg
mixing and complete combustion of fuel. This displays that there is 1% increase in BTE when related with diesel.
3.1.2 Brake specific fuel consumption.
Load vs BSFC
0.43
Table 2: Properties of alternative fuels.
2 0.316 0.264 0.259 0.235
BSFC
BSFC
1 0
0
Properties
Gasoline
Diesel
Hydrogen
Acetylene
Molecular weight
105
200
1
26.04
Density kg/m3
780
830
0.08
1.092
Specific gravity
0.78
0.83
0.0696
0.920
Boiling point
0
32-220
180-
340
-252.8
-84.4
Lower Calorific Value value kJ/kg
43,890
42,700
1,20,000
48,225
Flash point 0c
-43
74
–
32
Auto ignition temperature
0c
300-450
250
572
305
Properties
Gasoline
Diesel
Hydrogen
Acetylene
Molecular weight
105
200
1
26.04
Density kg/m3
780
830
0.08
1.092
Specific gravity
0.78
0.83
0.0696
0.920
Boiling point
0
32-220
180-
340
-252.8
-84.4
Lower Calorific Value value kJ/kg
43,890
42,700
1,20,000
48,225
Flash point 0c
-43
74
–
32
Auto ignition temperature
0c
300-450
250
572
305
0 20 40 60 80 100
Load
Baseline Diesel Diesel+1L/m Diesel+2L/m Diesel+3L/m
-
RESULTS AND DISCUSSION
-
Performance characteristics
Brake Thermal Efficiency(%)
Brake Thermal Efficiency(%)
-
Brake Thermal efficiency
Load vs BTE
40
30
20 30.74 33.48 35.01
26.19
10 19.12
0
00 20 40 60 80 100
Load (%)
Baseline Diesel Diesel+ 1L/m A Diesel+2L/m A diesel +3L/m A
Figure 3: Load vs Brake Thermal efficiency
Pressure In Bar
Pressure In Bar
The variation of BTE with load for various flow rates of (Diesel and Acetylene) is as shown in fig 3.The efficiency at full load for neat diesel was found to be 34% and for blends it was (33%) for 1L/m (34.51%) for 2L/m (35%) for 3L/m flow of acetylene. The maximum BTE is accounted for 3L/m acetylene injection (35%) .At partial loads with 1L/m of acetylene been injected the BTE decreases slightly this may be due to the flame from the ignition center not propagating to entire regions of combustion chamber. With the introduction of acetylene at 3L/m the BTE increases ( 35%) due to high flame speed and extensive flammability limits of acetylene. Moreover Acetylene fully participates in Combustion leading to proper
Figure 4: Load vs. BSFC
It was noted that SFC showed decreased trend with increase in torque. SFC is found to be maximum for diesel (0.2532 Kg/kw-hr) and minimum for 3L/m Acetylene injection (0.235 Kg/kw-hr). So there is 7.18% decrease in SFC of3L/m Acetylene injection.. At lower load with slight fuel, heat released is utilized by large air present which results in low BMEP and high BSFC. At high Load all the air is involved in combustion which results in increase BMEP and low BSFC.
-
-
Combustion Characteristics
Acetylene consists of 2 atoms of carbon and 2 atoms of Hydrogen. Moreover they are bonded by triple bond. When acetylene attains its Self ignition Temperature enormous amount of energy is released due to breakage of triple bond. Acetylene upon reacting with Oxygen can reach flame temperature of 30000 C to 35000 C (17) due to breakage of Triple bond. Combustion takes place rapidly as Acetylene comes in contact with air fuel mixture but initially there is a delay in combustion might be due to presence of Acetylene, Diesel fuel is incapable of mixing with air at lower loads. As the Load increases complete combustion of fuel is observed.
Crank angle Vs Pressure
70.276
80
60
40
20
0
300 320 340 360 380
Crank Angle
Diesel Diesel+1L\M A Diesel+2L\M A Diesel+3 L\M A
Figure 5: Crank angle vs Pressure
Crank angle Vs Pressure
70.276
80
60
40
20
0
300 320 340 360 380
Crank Angle
Diesel Diesel+1L\M A Diesel+2L\M A Diesel+3 L\M A
Figure 5: Crank angle vs Pressure
-
Cylinder pressure
The deviation of cylinder pressure with combustion process signifies how operative the engine cylinder is Figure 5 shows the trend of pressure and Crank angle. The Gaseous fuel is been introduced to cylinder the pressure increases this might be due to higher flame speed, more oxygen inside cylinder and higher energy release rate. The peak pressure is reaching 58.34 bar at full load for Baseline diesel. However the pressure showed increasing trend for Acetylene induction. The pressure inside the cylinder after acetylene induction was found to be 62, 66 and 70 bar at full load for 1lpm , 2lpm and 3lpm respectively.
-
Heat released Rate
Heat Release Rate
Heat Release Rate
Heat release rate is an important parameter to know how much is the heat released during Combustion of Acetylene and Diesel under dual fuel Mode. As it helps to analyze out of Total heat release how much quantity of heat was effectively utilized. It is been reported that for diesel operation the burning rate diagram has 4 different phases: Ignition delay, premixed combustion phase, Mixing controlled combustion phase and late combustion phase. The combustion Process in dual fuel mode is also quite similar with 4 different Phases: Pre oxidation reaction of gas, combustion of Pilot Fuel, Premixed Combustion and Diffusion combustion phase.
Crank angle Vs Heat Release Rate
66.12
70
60
50
40
30
20
10
0
310 320 330 340 350 360 370 380
Crank angle
Diesel Diesel+1L\M A Diesel+2L\M A Diesel+3 L\M A
Figure 6: Crank Angle vs Heat Release Rate
Figure 6 shows the variation of Crank angle and Heat release rate. Under dual fuel mode at full load the HRR was found to be 58.34 (J/0CA) ,62.67(J/0CA) and 66.12(J/0CA) 1lpm , 2lpm and 3lpm respectively.
HRR for Base line diesel was 56.12(J/0CA). When dual fuel mode is compared with base line diesel the trend is similar but a slight variation was observed in Pre mixed phase and Diffusion Combustion phase. This is due to less pre mixed combustion of diesel with inducted acetylene and also due to the presence of unburnt acetylene.
-
-
Emission Characteristics
CO (%)
CO (%)
-
Carbon Monoxide
LOAD vs CO
0.15
0.1
0.098
0.05 0.08 0.068
0.056
0 0.041 0.035
0 20 40 60 80 100
Load (%)
Diesel Diesel+1L\M A Diesel+2L\m A Diesel+3L\m A
Figure 7: Load vs CO
-
Nitrogen Oxides
-
NOx (ppm vol)
NOx (ppm vol)
Fig 7 depicts the deviation of CO emissions with load. The Emission of CO results from improper combustion of HC. The formation of CO can be avoided by enriching the oxygen in the fuel. Due to combustion there is a steep increase in pressure and temperature at higher loads resulting in complete combustion leading to low CO formation. Air fuel ratio is also the primary factor in accessing the formation of CO. Better Air fuel mixing tends to complete combustion which further leads to less CO formation. For baseline diesel at full load CO was found to be 0.045% were as after induction of acetylene the CO level reduced to0.040%,0.038% and 0.035% for 1lpm , 2lpm and 3lpm respectively. Co reduces by 22.33% for 3lpm acetylene induction compared to diesel.
Load Vs NOx
1600 1363
1400
1200 962
1000
800 688
502
600
400 204
200 82
0
0 20 40 60 80 100
Load
Diesel 1lpm 2lpm 3lpm
Figure 8: Load vs NOx
NOx Emission such as Nitrogen Monoxide and Nitrogen Dioxide are harmful to mankind.Fig8 depicts the deviations of NOx emission related to load. Higher temperature is more suitable for NOx formation, NOx emission increases with the temperature raise. It is noted from the figure that as the torque (load) increased the NOx
emissions increased this is because as diesel engines have higher compression ratio with in turn leads to peak temperature making way for the formation of NOx. NOx formation is intern dependent on temperature. The maximum NOx emissions at full load were showed for diesel(1242PPM) .The NOx emissions for blends were (1218), (1239) and (1363) ppm for1Lpm ,2Lpm 3Lpm respectively. The trend of NOx at baseline diesel with (1lpm and 2lpm) acetylene induction showed similar trend. However NOx increased by 4.6% for 3lpm of acetylene induction this might be due to higher flame speed excess air causing high Cylinder pressure and temperature.
HC (ppm)
HC (ppm)
Load vs HC
120
100
80 97
60
68
40 54
20 32 38
0 22
0 20 40 60 80 100
Load (%)
Diesel Diesel+1L\M A Diesel+2L\m A Diesel+3L\m A
Figure 9:Load vs HC
Load vs HC
120
100
80 97
60
68
40 54
20 32 38
0 22
0 20 40 60 80 100
Load (%)
Diesel Diesel+1L\M A Diesel+2L\m A Diesel+3L\m A
Figure 9:Load vs HC
3.3.2 Unburned Hydro Carbons
respectively. Under dual fuel mode at full load the HRR was found to be 58.34 (J/0CA) ,62.67(J/0CA) and 66.12(J/0CA) 1lpm , 2lpm and 3lpm respectively. HRR for Base line diesel under full load was 56.12(J/0CA).At full load maximum NOx emission were showed for diesel(1242PPM) .The NOx emissions for blends were (1218), (1239) and (1363) ppm for1Lpm ,2Lpm 3Lpm respectively. The CO emission was maximum for diesel. It clearly showed a decrease trend in CO emissions for blended acetylene at different flow rates. HC emissions at full load are observed for diesel (104 ppm). The HC emissions for blends were found to be 102, 98, 97 for 1L/m , 2L/m, 3L/m of Acetylene injection. Since optimum engine performance has been observed, it can be concluded that Acetylene can be successfully used in C.I engines as an alternative and optimal results were obtained for 3lpm of acetylene injection.
Hydro carbons are organic based compounds. Hydrocarbons are formed due to to incomplete combustion of fuel. Fig 9 depicts the deviations of HC emission related to load. At full load HC emission for diesel was (104 ppm). The HC emissions for blends were found to be 100,97,94(ppm) for 1L/m ,2L/m,3L/m of Acetylene injection which is 9.6% lower than that of diesel. This may be due to Higher burning velocity of acetylene and due to too much of air and less quantity of fuel in engine.
-
-
CONCLUSIONS
In this study experimental analysis was done to check the Performance Combustion and emission characteristics of CI engine using acetylene as a fuel at different flow rates(1lit/min,2lit/min,3lit/min). Trails were carried out under same condition and repeated 3 times to obtain steady values. The brake thermal efficiency at full load for neat diesel was found to be 34% and for blends it was (33%) for 1L/m of Acetylene (34.51%) for 2L/m of Acetylene(35%) for 3L/m of acetylene. Fuel consumption decreased by 7.08% for 3lit/min of acetylene when compared with baseline diesel. . The peak pressure is reaching 58.34 bar at full load for Baseline diesel. However the pressure showed increasing trend for Acetylene induction. The pressure inside the cylinder after acetylene induction was found to be 62, 66 and 70 bar at full load for 1lpm , 2lpm and 3lpm
REFERENCES
-
Sharma, P. K., Kuinkel, H., Shrestha, P., & Poudel, S. (2012). Use of acetylene as an alternative fuel in IC engine. Fuel, 2(H2), C8-C20..
-
Sharma, S., Sharma, D., Soni, S. L., Singh, D., & Jhalani, A. (2019). Performance, combustion and emission analysis of internal combustion engines fuelled with acetylenea review. International Journal of Ambient Energy, 1-19.
-
Lakshmanan, T., Avinash, A., & Nagarajan, G. (2017). RETRACTED: Experimental study on DI diesel engine with acetylene in dual fuel mode with DEE as an ignition enhancer.
-
Basha, S. K., Rao, P. S., Rajagopal, K., & Kumar, K. R. (2016). Evaluation of performance & emission characteristics of an acetylene aspirated diesel engine. In Proceedings of the World Congress on Engineering (Vol. 2).Raman, R., & Kumar, N. (2019). Experimental investigation to analyze the effect of induction length of diesel-acetylene dual fuel engine. Energy Sources, Part A: Recovery, Utilization, and Environmental Effects, 1-15.
-
Raman, R., & Kumar, N. (2020). Experimental studies to evaluate the combustion, performance and emission characteristics of acetylene fuelled CI engine. International Journal of Ambient Energy, 1-10.
-
Srivastava, A. K., Soni, S. L., Sharma, D., Sonar, D., & Jain, N.
L. (2017). Effect of compression ratio on performance, emission and combustion characteristics of dieselacetylene-fuelled single- cylinder stationary CI engine. Clean Technologies and Environmental Policy, 19(5), 1361-1372.
-
Ramesha, D. K. (2020, February). Performance, combustion and emission characteristics of B20 fish biodiesel blended with waste plastic oil on a diesel engine. In Journal of Physics Conference Series (Vol. 1473, No. 1, p. 012036)
-
Shaik, K. B., Masood, M., Ravi Kumar, K., & Srinivasa Rao, P. (2020). Experimental analysis of diesel engine with variable flow of acetylene gas in dual fuel mode. International Journal of Ambient Energy, 1-8.
-
Heywood, J. B. (2018). Internal combustion engine fundamentals. McGraw-Hill Education..
-
Ganesan V. Internal combustion engine. 3rd ed.
Singapore:McGraw Hill Book Company; 2007
-
Lakshmanan, T., & Nagarajan, G. (2011). Experimental investigation of port injection of acetylene in DI diesel engine in dual fuel mode. Fuel, 90(8), 2571-2577.
-
U.S. Geological survey, 2015 Mineral commodity summaries 2015 DOI: 10.3133/70140094
-
Kenneth Wark, Wulff Et Al Wulff, Cecil F. Warner, and Wayne,T.Davis,Internal Combustion SystemUsing Acetylene Fuel Jun. 20, 2000.
-
Harish, H., & Kempaiah, U. N. (2020, July). Experimental investigation on performance and emission of CI engine using B20 waste cooking oil with and without exhaust gas recirculation. In AIP Conference Proceedings (Vol. 2247, No. 1, p. 030002). AIP Publishing LLC.
-
Shaik, K. B., Masood, M., Ravi Kumar, K., & Srinivasa Rao, P. (2020). Experimental analysis of diesel engine with variable flow of acetylene gas in dual fuel mode. International Journal of Ambient Energy, 1-8.Potential of acetone butanol-ethanol (ABE) as a biofuel. Fuel http://dx.doi.org/10.1016/j.fuel.2019. 01.063.
-
Sharma, S., Sharma, D., Soni, S. L., Singh, D., & Jhalani, A. (2019). Performance, combustion and emission analysis of internal combustion engines fuelled with acetylenea review. International Journal of Ambient Energy, 1-19.