
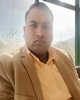
- Open Access
- Authors : Aravind Chauhan , Syed Agha , Ishan Rattan
- Paper ID : IJERTV10IS090089
- Volume & Issue : Volume 10, Issue 09 (September 2021)
- Published (First Online): 27-09-2021
- ISSN (Online) : 2278-0181
- Publisher Name : IJERT
- License:
This work is licensed under a Creative Commons Attribution 4.0 International License
Strengthening of Reinforced Concrete Beam using FRP Sheet
Mr. Aravind Chauhan, 1 Syed Agha, 2 Ishan Rattan, 3
1- A.P. School of Civil Engineering Bahra University Waknaghat, H.P.
2- Student Master of Technology in Civil Engineering 3- Student Master of Technology in Civil Engineering
Abstract:- The rehabilitation of existing reinforced concrete (RC) bridges and building becomes necessary due to ageing, corrosion of steel reinforcement, defects in construction/design, demand in the increased service loads, and damage in case of seismic events and improvement in the design guidelines. Fiber-reinforced polymers (FRP) have emerged as promising material for rehabilitation of existing reinforced concrete structures. The rehabilitation of structures can be in the form of strengthening, repairing or retrofitting for any type of deficiencies. RC rectangular-section is the most common shape of beams and girders in buildings and bridges.
INTRODUCTION:
I owe my deep gratitude to the individuals who have prominently contributed in completion of this report.
Foremost, I would like to express my heartfelt gratitude to my esteemed guide, Mr. Aravind Chauhan (HOD, School of Civil Engineering, Bahra University Shimla Hills, waknaghat H.P) for providing me a platform to work on challenging regions of Structural Engineering & Construction Management Engineering. His profound intuitions and consistent devotion towards microscopic details have been enormous inspirations contributed power plus to my research work.
This acknowledgement would not be ever completed without expressing my heartfelt gratitude & abundant regards to my Parents and Brothers. Definitely their consistent love, patience, encouragement, guidance & support are the source of my motivation and inspiration throughout my work which was the principal reinforcement to my achievement.
Eventually, I would like to dedicate my work and this thesis to my beloved family.
FRP AND RETTROFITTING
INTRODUCTION:
Retrofitting of existing infrastructure is bound to increase all over the world. This is because of deterioration of structural strength of existing infrastructure (due to age and environmental attacks),up-grading of various design codes(due to better understanding of various design concepts in due course of time) and higher load carrying capacity demand (due to present day increased service needs) etc. Fiber Reinforced Polymer (FRP) is a relatively new class of composite material manufactured from fibers and resins and has proven efficient and economical for the development and repair of new and deteriorating structures in civil engineering.
NEED OF RETROFITTING IN RC STRUCTURES:
The strengths of various types of concrete have increased from the low levels of 15-20 MPa to values in the range of 40-70 MPa. Such uses include increasing the load capacity of existing structures (such as existing parking garages) that were designed to tolerate far lower service loads. Other uses include seismic retrofitting, and repair of damaged concrete structures. Repair and rehabilitation work for concrete structures can broadly be classified into two categories:
-
repair in which damage due to deterioration and cracking is corrected to restore the original structural shape, and
-
Repair which is necessary to strengthen the structural capacity of members whose load carrying capacity is either inadequate or whose strength has been severely impaired due to sustained damage.
Degradation of steel reinforcements due to corrosion, cracking of concrete due to weathering, rapidly changing traffic needs (both in terms of intensity and load levels) and recent earthquake damages have necessitated the use of strengthening of basic structural components such as slabs, panels, walls, beams and columns.
WHAT ARE FRPs?
Fiber-reinforced polymer commonly known as FRPs represents a class of materials that falls into a category referred to as composite materials. Composite materials consist of two or more materials that retain their respective chemical and physical characteristics when combined together. FRPs are commonly used in the aerospace, automotive, marine, and construction industries. Fibers can be formed from a wide range of amorphous and crystalline materials but in the construction industry the three fibers which are generally used in structural systems are
-
The glass fiber (the E-glass fiber, the S-glass fiber and the Z-glass fiber),
-
The aramid fiber (the aromatic polyamides, Kevlar 49 fiber) and
-
The carbon fiber (the ultra-high-modulus fiber, the high-modulus fiber and the high-strength fiber).
The primary function of fiber reinforcement is to carry load along the length of the fiber and to provide strength and stiffness in one direction. Therefore FRP composites properties are directional, i.e. the best mechanical properties are in the direction of the fiber placement.
SUITABILITY OF FRP FOR USES IN STRUCTURAL ENGINEERING:
Externally bonded fiber-reinforced polymers (FRPs) in the form of continuous carbon (C), glass (G) or aramid (A) fibers bonded together in a matrix made of epoxy, vinyl ester or polyester, have been employed extensively throughout the world in numerous rehabilitation applications of reinforced concrete or masonry structures. The high strength-to-weight ratio, immunity to corrosion and easy handling and installation has made FRP jackets the material of choice in an increasingly large number of projects where increased strength or inelastic deformation capacity must be achieved for seismic retrofitting, despite the relatively high material costs.
When an FRP specimen is tested in axial tension, the applied force per unit cross-sectional area (stress) is proportional to the ratio of change in a specimen's length to its original length (strain). When the applied load is removed, FRP returns to its original shape or length. In other words, FRP responds linear-elastically to axial stress.
Among FRPs high strength properties, the most relevant features include
-
-
Excellent durability and corrosion resistance.
-
High strength-to-weight ratio.
-
A member composed of FRP can support larger live loads since its dead weight does not contribute significantly to the loads that it must bear.
-
Ease of installation.
-
Versatility.
-
Anti-seismic behavior.
-
Electromagnetic neutrality.
-
Excellent fatigue behavior and fire resistance.
One of the most common uses for FRP involves the repair, rehabilitation and retrofitting of damaged or deteriorating structures as shown in Fig.1.1 (a), (b).
These include structures such as siding/cladding, roofing, flooring and partitions.
-
(b)
Figure.1.1 (A). Application of Externally Bonded FRP Composites.
Figure 1.1 (B). Retrofitting Of Column-Beam Joint.
The first application of FRP strengthening was made to reinforce the concrete beams. The beams are load bearing structural elements that are designed to carry both vertical gravity loads and horizontal loads due to seismic or wind. The structurally deficient beams fail during such events. There are mainly two types of failure of beams i.e., flexural and shear.
Hence, the strengthening of such beams is needed in flexure or shear or both zones and the use of external FRP strengthening to beams may be classified as:
-
Flexural strengthening
-
Shear strengthening
Flexural strengthening
Beams are strengthened in flexure through the use of FRP composites bonded to their tension zone using epoxy. The direction of fibers is parallel to that of high tensile stresses. Both prefabricated FRP strips, as well as sheets are applied.
Shear strengthening
The shear failure of an RC beam is distinctly different from the flexural failure. The flexural failure of a beam is ductile in nature, whereas shear failure is brittle and catastrophic. When the RC beam is deficient in shear, or when its shear capacity is less than the flexural capacity after flexural strengthening, shear strengthening must be considered. Both FRP composite plates and sheets can be used in shear zone to enhance the capacity of beam, but the latter are more popular because of their flexible nature and ease of handling and applications. There are various FRP bonding schemes which can be applied to increase the shear resistance of RC beams. These include:-
-
Bonding FRP to the sides of the beam only,
-
Bonding FRP U-jackets covering both the sides and the tension face, and
-
Wrapping FRP around the whole cross section of the beam.
FRPs are strong only in the directions of fibers. The fiber directions in FRP composites may be unidirectional, bi-directional or multi-directional. The use of fibers in two directions can be beneficial with respect to shear resistance even if strengthening for reversed loading is not required, except for unlikely case in which one of the fiber directions is exactly parallel to the shear cracks.
Modes of failure of FRP strengthened beams are:
-
Fiber failure in the FRP
It occurs when the tensile stress in the fibers exceeds the tensile strength. It is characterized by a rapid progressive fiber failure in the composite, particularly for sheets, but the failure is brittle in most of the cases. The orientation of the fibers with respect to the principal strain in concrete affects the ductility of the composite.
-
Bond failure
Bond failure is governed by the properties of the weaker materials in contact, i.e. concrete and adhesive. When the shear strength of one of these exceeds the force then transfer cannot be ensured anymore and a slip is produced. The deboning can take place in the concrete, between the concrete and the adhesive, in the adhesive, between the adhesive and the fibers. The use of side- bonded FRP sheets enhance the shear capacity of the flange beam, but strength of FRP sheets in fullest extent may not be utilized due to the bond failure between the FRP and the concrete. U-jacketing is currently the most popular shear strengthening solution due to its high practicality, but it is limited by end peeling of the U-jacket legs. These drawbacks have opened up a new area of research on development of anchorage system.
TYPES OF FRPs
There are three types of fibers dominate. These are carbon, glass, and aramid fibers and the composite is often named by the reinforcing fiber
-
Carbon Fiber Reinforced Polymer (CFRP)
Carbon fiber reinforced polymer, is a material consisting of extremely thin fibers about 0.0050.010 mm in diameter and composed mostly of carbon atoms. The carbon atoms are bonded together in microscopic crystals that are more or less aligned parallel to the long axis of the fiber.
The crystal alignment makes the fiber very strong for its size. Several thousand carbon fibers are twisted together to form a yarn, which may be used by itself or woven into a fabric (Fig.1.2).
Fig.1.2 Carbon Fiber Sheet Fig.1.3 Glass Fiber Sheet
-
Glass Fiber Reinforced Polymer (GFRP)
GFRP is a lightweight, strong material with very many uses, including boats, automobiles, water tanks, roofing, pipes and cladding. The plastic matrix may be epoxy, a thermosetting plastic (most often polyester or vinyl ester) or thermoplastic. Glass fibers are basically made by mixing silica sand, limestone, folic acid and other minor ingredients. The mix is heated until it melts at about 1260°C. The molten glass is then allowed to flow through fine holes in a platinum plate. The glass strands are cooled, gathered and wound. The fibers are drawn to increase the directional strength. The fibers are then woven into various forms for use in composites (Fig.1.3).
-
Aramid Fiber Reinforced Polymers (AFRP)
Aramid is the short form for aromatic polyamide. Aramid fibers are most commonly known Kevlar, Nomex and Technora. Aramids are generally prepared by the reaction between an amine group and a carboxylic acid halide group, commonly this
occurs when an aromatic polyamide is spun from a liquid concentration of sulfuric acid into a crystallized fiber. Fibers are then spun into larger threads in order to weave into large ropes or woven fabrics (Fig. 1.4).
Fig.1.4 Aramid Fiber Sheet
-
Properties of CFRP
-
-
-
Carbon fiber reinforced polymer (CFRP) is alkali resistant.
-
Carbon fiber reinforced polymers (CFRP) are resistant to corrosion; hence they are used for corrosion control and rehabilitation of reinforced concrete structures.
-
Carbon fiber reinforced polymer composite has low thermal conductivity.
-
CFRP composites have high strength to weight ratio and hence it eliminates requirements of heavy construction equipment and supporting structures.
-
CFRP composites are available in rolls of very long length. Therefore, they need very few joints, avoiding laps and splices, and its transportation is also very easy.
-
CFRP composites have a short curing time. Therefore, the application takes a shorter time. This reduces the project duration and down time of the structure to a great extent.
-
Application of CFRP composites does not require bulky and dusty materials in a large quantity; therefore, the site remains tidier.
-
CFRP composites possess high ultimate strain; therefore, they offer ductility to the structure and they are suitable for earthquake resistant applications.
-
CFRP composites have high fatigue resistance. So they do not degrade, which easily alleviates the requirement of frequent maintenance.
-
CFRP composites are bad conductor of electricity and are non-magnetic.
SUITABILITY OF CFRP IN CIVIL ENGINEERING:
Civil structural applications of fiber reinforced polymer (FRP) composites include both new constructions as well as existing structures. CFRP is a more costly material than its counterparts in the construction industry, glass fiber-reinforced polymer (GFRP) and aramid fiber-reinforced polymer (AFRP), though CFRP is, in general, regarded as having superior properties. Applied to reinforced concrete structures for flexure, CFRP typically has a large impact on strength (doubling or more the strength of the section is not uncommon), but only a moderate increase in stiffness (perhaps a 10% increase). This is because the material used in this application is typically very strong (e.g., 3000 MPa ultimate tensile strength, more than 10 times mild steel) but not particularly stiff (150 to 250 GPa, a little less than steel, is typical).
Fig. 1.5 Properties of Different Fibers and Typical Reinforcing Steel.
CFRP is widely used to strengthen concrete structures that have lost reinforcing steel mass due to corrosion and concrete deterioration because CFRP possess good rigidity, high strength, low density, corrosion resistance, vibration resistance, high ultimate strain, high fatigue resistance, and low thermal conductivity. They are bad conductors of electricity and are non- magnetic.
ADVANTAGES:
FRP materials have higher ultimate strength and lower density as compared to steel. When these properties are taken together they lead to fiber composites having a strength/weight ratio higher than steel plate in some cases. The lower weight of FRP makes installation and handling significantly easier than steel. Here, no bolts are requred; in fact, the use of bolts would seriously weaken the material unless additional cover plates are bonded on.
-
Laps and joints are not required
-
The material can take up irregularities in the shape of the concrete surface
-
The material can follow a curved profile; steel plate would have to be pre-bent to the required radius.
-
The material can be readily installed behind existing services
-
Overlapping, required when strengthening in two directions, is not a problem because the material is thin.
DISADVANTAGES
The main disadvantage of externally strengthening structures with fiber composite materials is the risk of fire, vandalism or accidental damage, unless the strengthening is protected. A particular concern for bridges over roads is the risk of soffit reinforcement being hit by over-height vehicles. However, strengthening using plates is generally provided to carry additional live load and the ability of the un-strengthened structure to carry its own self-weight is unimpaired. A disadvantage in the eyes of many clients will be the lack of experience of the techniques and suitably qualified staff to carry out the work. Finally, a significant disadvantage is the lack of accepted design standards.
OBJECTIVE
The main objectives of the present work are:
-
To study the contribution of externally bonded Fiber Reinforced Polymer (FRP) sheets on the behavior of RC beams.
-
To know the contribution of FRP sheet composites as repair materials under sustain loading condition.
-
To know the suitability of the FRP composites as repair materials for RC Structures.
-
To investigate the behavior of RC beam for various configuration of loads.
REVIEW OF LITERATURE
BRIEF REVIEW:
The state of deterioration of the existing civil engineering concrete structures is one of the greatest concerns to the structural engineers worldwide. The renewal strategies applied to existing structures comprise of rehabilitation and complete replacement. The latter involves a huge expenditure and time; hence the rehabilitation is the only option available. Fiber reinforced polymers (FRP) are the promising materials in rehabilitation of the existing structures and strengthening of the new civil engineering structures. A brief review of the existing literature in the area of reinforced concrete (RC) beams strengthened with epoxy-bonded FRP.
CRITICAL OBSERVATION FROM THE LITERATURE:
It is clear that there lies a vast scope of research in the field of retrofitting of concrete structures especially beams using externally bonded FRP composites. In the above section it has been shown how the structural strength and stiffness can be improved by externally bonded material.
SCOPE
Based on the critical review of the existing literature and to fulfil the objective outlined earlier, the scope of the present work is defined as follows:
-
To study the behavior of different types of loading on RC beams.
-
To study the contribution of CFRP composites on ultimate load carrying capacity and failure pattern of reinforced concrete beams.
-
To know the behavior of reinforced concrete beams retrofitted with CFRP.
-
To know the practical feasibility of FRP in the construction industry.
EXPERIMENTAL PROGRAM
The objective of the experimental program is to study the effect of externally bonded (EB) fiber reinforced plastic (FRP) sheets on the load bearing capacity of reinforced concrete beam. Five number of reinforced concrete rectangular-beams are cast and tested up to failure by applying single-point loading system. Out of five numbers of beams, one beam was not strengthened by FRP and was considered as a control beam, whereas all other four beams were strengthened with externally bonded CFRP sheets.
CASTING OF THE SPECIMENS
For conducting experiment, the proportions in the concrete mix are tabulated in Table 3.1 as per IS: 456-2000. The water cement ratio is fixed at 0.5. The mixing is done by hand mixing. The beams are cured for 28 days. For each beam six concrete cube specimens were made at the time of casting and were kept for curing, to determine the compressive strength of concrete at the age of 7 days & 28 days. The uniaxial compressive tests on the specimens (150 × 150 × 150 mm concrete cube) were performed and the average concrete compressive strength at 28 days for each beam is shown in Table 3.2.
Table 3.1 Nominal Mix Proportions of Concrete
Description
Cement
Sand (Fine Aggregate)
Coarse Aggregate
Water
Mix Proportion (by weight)
1
1.48
3.19
0.5
Quantities of materials for one specimen beam (kg)
16.71
24.73
53.42
8.37
Table 3.2 Test Result of Cubes after 28 Days
Specimen Name
Specimen ID
Size of Cube Specimen (mm)
Average Cube Compressive Strength (MPa)
Control Beam
CB
150x150x150
25.93
Strengthened Beam 1
SB1
150x150x150
26.02
Strengthened Beam 2
SB2
150x150x150
26.90
Strengthened Beam 3
SB3
150x150x150
26.77
Strengthened Beam 4
SB4
150x150x150
25.20
MATERIALS PROPERTIES
CONCRETE:
It is composed of Portland cement and water combined with sand, gravel, crushed stone, or other inert material such as expanded slag or vermiculite.
CEMENT:
Table 3.3: Physical Properties of Cement
S.No.
Characteristics
Values obtained
Standard values
1
Normal Consistency
35%
30%
2
Initial Setting time
48 min
Not be less than 30 minutes
3
Final Setting time
588 min
Not be greater than 600 minutes
4
Fineness
4.8%
<10%
5
Specific gravity
2.88
3.15
Compressive Strength:- Cement : Sand (1:3)
1
7 days
51.4 MPa
50MPa
2
28 days
55 MPa
53 MPa
FINE AGGREGATE
Fine aggregate / sand is an accumulation of grains of mineral matter derived from the disintegration of rocks.
Table 3.4: Physical Properties of Fine Aggregates
Sr. No.
Characteristics
Value
1
Specific gravity
2.63
2
Bulk density
1.4 g/cc
3
Fineness modulus
2.836
4
Grading Zone (Based on percentage passing 0.60mm)
Zone III
Table 3.5 Sieve Analysis of Fine Aggregate
Description of Sample
Specific Gravity
GRADING
Remarks
Sieve Designation in mm
% PASSING
Obtained
Required
Sand
2.63
10.0
4.75
2.36
1.18
0.600
0.300
0.150
100
99.9
97.7
90
74.4
48.3
5.8
100
90-100
85-100
75-100
60-79
12-40
0-10
Sand comes under Grading zone III as per IS: 383-1970
Specifications.
Total weight taken = 1000 gm
Fineness Modulus of fine aggregates = 2.836
COARSE AGGREGATE
Coarse aggregate are the crushed stone is used for making concrete. The sizes are from 0.25 to 2.5 in (0.64 to 6.35 cm), although lager sizes may be used for massive concrete aggregate.
Table 3.6 Physical Properties of Coarse Aggregates
S.No.
Characteristics
Value
1
Type
Crushed
2
Specific Gravity
2.62
3
Total Water Absorption
0.56%
4
Fineness Modulus
8.0535
Table 3.7 Sieve Analysis of Coarse Aggregate
Description of Sample
Specific Gravity
GRADING
Remarks
Sieve Designation in mm
% PASSING
Obtained
Required
Coarse Aggregate
2.62
40
20
10
4.75
100
92.75
1.3
0.1
100
95-100
25-55
0-10
Confirms to 20mm full graded Coarse aggregate as per IS: 383-1970
specifications.
Total weight taken = 3Kg
FM of Coarse aggregate = (305.35+500) /100 = 8.0535
WATER
Water fit for drinking is generally considered good for making the concrete. Water should be free from acids, alkalis, oils, vegetables or other organic impurities.
REINFORCING STEEL
High-Yield Strength Deformed (HYSD) bars confirming to IS 1786:1985. The reinforcements of FE-500- 16 mm and FE-500- 12 mm diameter will be used for the longitudinal reinforcement and the stirrups of FE-500- 8 mm diameter. The modulus of elasticity of steel bars was 2 × 105 MPa.
DETAILING OF REINFORCEMENT IN RC BEAMS
For all the five reinforced concrete beams the same arrangement of reinforcement will be made. The tension reinforcement consists of 2 numbers of 16 mm and 1 number of 12 mm HYSD bars shown in figure 3.1.
Fig. 3.1 Cross Section
FRP
Fiber Reinforced Polymer (FRP) composites comprise fibers of high tensile strength within a polymer matrix such as vinyl ester or epoxy. FRP composites have proved to be extremely useful for strengthening of RCC structures against both normal and seismic loads. Unidirectional CFRP sheets as shown in Fig. 3.2 having cross section (500 X 1.0) mm are used for wrapping the beams. Table 3.8 shows the properties of CFRP Sheet.
Fig 3.2 CFRP Sheet Used In the Experiment
Table 3.8 Properties of CFRP Sheets
S.No.
Physical properties
Value
1
Tensile Strength
4000 MPa
2
Tensile Modulus
230 GPa
3
Ultimate Elongation
1.7%
4
Density
1.74 g/cm3
5
Minimum weight per sq. yd.
0.54 Kg
Table 3.9 Properties of Diff. Fibers
Material
Density (g/cm3)
Tensile modulus (E)
(GPa)
Tensile Strength () (GPa)
Specific Modulus (E/)
Specific Strength
Relative cost
E-Glass
2.54
70
3.45
27
1.35
Low
S-Glass
2.50
86
4.50
34.5
1.8
Moderate
Carbon, High Strength
1.9
400
1.8
200
0.9
High
Carbon, High Modulus
1.7
240
2.6
140
1.5
High
Boron
2.6
400
3.5
155
1.3
High
Kelver 29
1.45
80
2.8
55.5
1.9
Moderate
Kelver 49
1.45
130
2.8
89.5
1.9
Moderate
EPOXY RESIN
The success of the strengthening technique primarily depends on the performance of the epoxy resin used for bonding of FRP to concrete surface. Numerous types of epoxy resins with a wide range of mechanical properties are commercially available in the market. These epoxy resins are generally available in two parts, a resin and a hardener.
It is made by mixing base saturant and hardener in ratio 100:42. Mixing of saturant and hardener is done thoroughly for five minutes until components are thoroughly dispersed. Properties of Epoxy are discussed in Table 3.10.
Table 3.10 Properties of Saturant
S.No.
Properties
Values
1
Mixing ratio, by weight (B:H)
100:42
2
Tensile strength
72.4 MPa
3
Tensile Modulus
3180 MPa
4
Flexural Strength
123.4 MPa
5
Flexural Modulus
3120 MPa
6
Elongation Percent
5.0%
FORM WORK
Fresh concrete being plastic in nature requires good form work to mould it to the required shape and size. So the form work should be rigid and strong to hold the weight of wet concrete without bulging anywhere. The joints of the form work are sealed to avoid leakage of cement slurry. Mobil oil was then applied to the inner faces of form work. The reinforcement cage was then lowered, placed in position inside the side work carefully with a cover of 20mm on sides and bottom by placing concrete cover blocks.
Fig.3.3 Form Work
MIXING OF CONCRETE
Mixing of concrete is done thoroughly by hand mixing.
COMPACON
All specimens were compacted by tamping rod, and sufficient care was taken to avoid displacement of the reinforcement cage inside the form work. Finally, the surface of concrete was leveled and smoothened by metal trowel. After seven hours, the specimen detail and date of concreting was written on top surface to identify it properly.
CURING OF CONCRETE
Curing is done to prevent the loss of water which is essential for the process of hydration and hence for hardening. Usually, curing starts as soon as the concrete is sufficiently hard. Here, curing is done by spraying water on the jute bags or by spending wet hessians cloth over the surface for a period of 28 days.
STRENGTHENING OF BEAMS WITH FRP SHEETS
All the loose particles of concrete surface at the bottom sides of the beam were chiseled out by using a chisel. Then the required region of concrete surface was made rough using a coarse sand paper txture and cleaned with an air blower to remove all dirt and debris particles.
Fig. 3.4 Application of Epoxy and Hardener on Beam
Once the surface was prepared to the required standard, the epoxy resin was mixed in accordance with manufacturers instructions. The mixing is carried out in a plastic container and was continued until the mixture was in uniform. After their uniform mixing, the fabrics are cut according to the size then the epoxy resin is applied to the concrete surface. Then the CFRP sheet is placed on top of epoxy resin coating and the resin is squeezed through the roving of the fabric with the roller.
Air bubbles entrapped at the epoxy/concrete or epoxy/fabric interface are eliminated. The composite laminate was attached starting at one end and applying enough pressure to press out any excess epoxy from the sides of the laminate. During hardening of the epoxy, a constant uniform pressure is applied on the composite fabric surface in order to extrude the excess epoxy resin and to ensure good contact between the epoxy, the concrete and the fabric. This operation is carried out at room temperature. Concrete beams strengthened with carbon fiber fabric are cured for minimum of 72 hours at room temperature before testing.
Fig. 3.5 Roller Used For Removal of Air Bubbles
EXPERIMENTAL SETUP
The testing procedure for the all the specimen will be same. First the beams will be cured for a period of 28 days then its surface will be cleaned with the help of sand paper for clear visibility of cracks. The single-point loading arrangement will be used for testing of beams. Single-point loading is conveniently provided by the arrangement shown in Figure 3.6.
Fig 3.6 Single Point Loading Experimental Setup
Fig. 3.7 Shear Force and Bending Moment Diagram for Single Point Loading
Figure 3.8 Experimental Setup for Testing Beams
DESCRIPTION OF SPECIMENS
The experimental program consists of 5 number of simply supported RC rectangular-beams of same longitudinal reinforcement of two numbers of 16mm and three number of 12mm was provided, out of which one beam will be taken as controlled beam and other four beams will be strengthened using carbon fiber reinforced polymer (CFRP) sheets. Experimental data on load, deflection and failure modes of each of the beams are obtained. The change in load carrying capacity and failure mode of the beams are investigated as the configuration of FRP is altered.
BEAM – 1
CONTROL BEAM (CB)
The control beam (CB) not strengthened with CFRP sheet. It is check for its ultimate load bearing capacity under single point loading setup.
BEAM 2
STRENGTHENED BEAM 1 (SB1)
The beam SB1 is a pre-cracked beam. It is strengthened with one layer of CFRP sheet having U-wrap on bottom and web portions and then checks it to its ultimate load capacity under single point loading setup.
BEAM 3
STRENGTHENED BEAM 2 (SB2)
The beam SB2 is a pre-cracked beam. It is strengthened with one layer of CFRP sheet having fully-wrap on bottom, top and web portions and then checks it to its ultimate load capacity under single point loading setup.
BEAM 4
STRENGTHENED BEAM 3 (SB3)
The beam SB3 is a pre-cracked beam. It is strengthened with one layer of CFRP sheet under sustain loading having U-wrap on bottom and web portions and then checks it to its ultimate load capacity under single point loading setup.
BEAM 5
STRENGTHENED BEAM 4 (SB4)
The beam SB4 is a pre-cracked beam. It is strengthened with one layer of CFRP sheet having CFRP sheet on bottom portions and then checks it to its ultimate load capacity under single point loading setup.
SUMMARY
Five beams were tested in this experimental investigation. One control beams was tested, four beams were strengthened with CFRP sheet. The detail descriptions of above mentioned beams are presented in Table 3.11.
Table 3.11 Beam Test Parameters and Material Properties
Beam ID
fc (MPa)
Tension Reinforcement
Material Type
Sheet Thickness (mm)
Strengthening system with FRP sheets
CB
25.93
2 16mm,
1 12mm
————-
———-
Control Beam (No sheets)
SB1
26.02
2 16mm,
CFRP
1
One layer bonded to the bottom and sides of beam (U-shape)
1 12mm
SB2
26.90
2 16mm,
1 12mm
CFRP
1
One layer bonded to the bottom, top and sides of beam (fully wrap)
SB3
26.77
2 16mm,
1 12mm
CFRP
1
One layer bonded to the bottom and sides of beam (U-shape)
SB4
25.20
2 16mm,
1 12mm
CFRP
1
One layer bonded to the bottom sides of beam
TEST RESULTS AND DISCUSSIONS
INTRODUCTION
The results obtained from the testing of five number RC rectangular-beams for the experimental program are interpreted. Their behaviours throughout the test are described with respect to initial crack load and ultimate load carrying capacity, deflection, crack pattern and modes of failure.
FAILURE MODES AND CRACK PATTERNS
The following failure modes are be investigated for a CFRP strengthened section:
-
-
-
Crushing of concrete in compression before yielding of the reinforced steel;
-
Yielding of the steel in tension followed by concrete crushing;
-
Debonding of the FRP from the concrete substrate (FRP debonding).
The CFRP strengthened beam and the control beams are tested to find out their ultimate load carrying capacity. It is found that all the failed in flexure. Beam-CB failed in flexural and shear. Beam-SB1 failed due to fracture of CFRP sheet and then flexural failure of the beam took place. Beam-SB2 failed due to debonding of the CFRP sheet and then shear failure and then flexural failure of the beam took place. Beam-SB3 failed due to fracture of CFRP at the center followed by debonding and finally flexural failure of the beam.Beam-SB4 failed in the debonding of CFRP sheet and then flexural failure took place.
Table 4.1 Ultimate Load and Nature of Failure
Sr.
No.
Type Of Beam
Beam Designation
Ultimate Load (KN)
Nature Of Failure
=(strengthened beam/control beam)
1
Control Beam
CB
130
Flexural Failure + Shear Failure
–
2
Strengthened Beam
SB1
170
Fracture of CFRP + Flexural- Shear Failure + Crushing of Concrete
1.31
3
Strengthened Beam
SB2
180
Debonding of CFRP + Shear- Flexural Failure
1.38
4
Strengthened Beam
SB3
156
Debonding of CFRP + Shear- Flexural Failure + Crushing Of Concrete
1.2
5
Strengthened Beam
SB4
165
Debonding + Flexural Failure
1.30
Control Beam
Fig. 4.1 Crack Pattern of CB
Fig. 4.2 Crack Pattern of SB-1 Fig. 4.3 Crack Pattern of SB-1
STRENGTHENED BEAM-2
Fig. 4.4 Crack Patten of SB-2 Fig. 4.5 Crack Pattern of SB-2
STRENGTHENED BEAM-3
Fig. 4.6 Crack Pattern of SB-2
Fig. 4.7 Crack Pattern of SB-3 Fig. 4.8 Crack Pattern of SB-3
STRENGTHENED BEAM-4
Fig. 4.9 Crack Pattern of SB-4 Fig. 4.10 Crack Pattern of SB-4
LOAD DEFLECTION HISTORY
Load deflection history of all the beams was recorded. The mid-span deflection of the control and strengthened beams were measured at different load steps and the deflections under the point loads were also recorded. The load-deflection histories are illustrated in figures-4.11 to 4.20. These figures below show that the deflection curve was initially straight showing the linear relationship between the load and deflection and became non-linear with further increase in load.
140
120
LOAD (KN)
LOAD (KN)
100
80
60
40
20
0
CONTROL BEAM
DEFLECTI
0 0.5 1 1.5 2 2.5 3 3.5
DEFLECTION (MM)
FIGURE 4-11. LOAD VS. DEFLECTION CURVE FOR CB
Beam CB was the control beam. In beam CB strengthening was not done. Single point loading was done on the beam and at the each increment of the load; deflection at the middle of the beam was taken. Using this load deflection data, load vs deflection curve is plotted. At the load of 70 KN initial cracks started coming on the beam. Further with increase in loading propagation of the cracks took place. The beam CB failed completely in flexural.
SB1
180
160
140
120
100
80
60
40
20
0
DEFLECTION AT L/2
SB1
180
160
140
120
100
80
60
40
20
0
DEFLECTION AT L/2
0 0.5 1 1.5 2 2.5 3 3.5 4 4.5
DEFLECTION (MM)
0 0.5 1 1.5 2 2.5 3 3.5 4 4.5
DEFLECTION (MM)
LOAD (KN)
LOAD (KN)
FIGURE 4-12. LOAD VS. DEFLECTION CURVE FOR SB-1
LOAD (KN)
LOAD (KN)
Beam SB-1 was the strengthened beam. In beam SB-1 strengthening is done by application of CFRP sheet having U-wrap i.e. on three sides of the beam. Single point loading was done on the beam and at the each increment of the load; deflection at the middle of the beam was taken. Using this load deflection data, load vs deflection curve is plotted. The beam SB-1 failed completely in flexural.
SB2
SB2
200
180
160
140
120
100
80
60
40
20
0
DEFLECTION AT
200
180
160
140
120
100
80
60
40
20
0
DEFLECTION AT
0 0.5 1 1.5 2 2.5 3 3.5 4
DEFLECTION (MM)
0 0.5 1 1.5 2 2.5 3 3.5 4
DEFLECTION (MM)
FIGURE 4-13. LOAD VS. DEFLECTION CURVE FOR SB-2
Beam SB-2 was the strengthened beam. In beam SB-2 strengthening is done by application of CFRP sheet having fully wrap on beam. Single point loading was done on the beam and at the each increment of the load; deflection at the middle of the beam was taken. Using this load deflection data, load vs deflection curve is plotted. The beam SB-2 failed completely in flexural.
SB3
SB3
180
160
140
120
100
80
DEFLECTION AT L/2
180
160
140
120
100
80
DEFLECTION AT L/2
0
0.5
1
1.5
2
2.5
3
3.5
0
0.5
1
1.5
2
2.5
3
3.5
DEFLECTION (MM)
DEFLECTION (MM)
60
40
20
0
60
40
20
0
LOAD (KN)
LOAD (KN)
FIGURE 4-14. LOAD VS. DEFLECTION CURVE FOR SB-3
LOAD(KN)
LOAD(KN)
Beam SB-3 was the strengthened beam. In beam SB-3 strengthening is done by application of CFRP sheet having U-wrap i.e. on three sides of the beam. Single point loading was done on the beam and at the each increment of the load; deflection at the middle of the beam was taken. Using this load deflection data, load vs deflection curve is plotted. The beam SB-3 failed completely in flexural.
SB4
160
140
120
100
80
60
40
20
0
DEFECTION AT L/2
SB4
160
140
120
100
80
60
40
20
0
DEFECTION AT L/2
0 0.5 1 1.5 2 2.5 3 3.5 4
DEFLECTION (MM)
0 0.5 1 1.5 2 2.5 3 3.5 4
DEFLECTION (MM)
FIGURE 4-15. LOAD VS. DEFLECTION CURVE FOR SB-4
Beam SB-4 was the strengthened beam. In beam SB-4 strengthening is done by application of CFRP sheet only on bottom face of the beam. Single point loading was done on the beam and at the each increment of the load; deflection at the middle of the beam was taken. Using this load deflection data, load vs deflection curve is plotted. The beam SB-4 failed completely in flexural.
4.5
DEFLECTION (MM)
DEFLECTION (MM)
4
3.5
3
2.5
2
1.5
1
0.5
0
CB vs SB1
DEFLECTION FOR CB
10 20 30 40 50 60 70 80 90 100 110 120 130 140 150 160 170
LOAD (KN)
FIGURE 4-16. LOAD VS. DEFLECTION CURVE FOR CB VS SB-1
DEFLECTION (MM)
DEFLECTION (MM)
From the load and deflection data of beams CB and beam SB-1, load vs deflection curve is plotted for both the beams. From this load vs deflection curve, it is clear that beam SB-1 had higher ultimate load carrying capacity as compare to beam CB. It indicate that CFRP sheet provide extra strength to the beam SB-1 and increase its load carrying capacity by S30.77%.
CB vs SB2
CB vs SB2
4
3.5
3
2.5
2
1.5
1
0.5
0
DEFLECTION FOR CB
4
3.5
3
2.5
2
1.5
1
0.5
0
DEFLECTION FOR CB
10 20 30 40 50 60 70 80 90 100110120130140150160170180
LOAD (KN)
10 20 30 40 50 60 70 80 90 100110120130140150160170180
LOAD (KN)
FIGURE 4-17. LOAD VS. DEFLECTION CURVE FOR CB VS SB-2
From the load and deflection data of beams CB and beam SB-2, load vs deflection curve is plotted for both the beams. From this load vs deflection curve, it is clear that beam SB-2 had higher ultimate load carrying capacity as compare to beam CB. It indicate that CFRP sheet provide extra strength to the beam SB-2 and increase its load carrying capacity by 38.46%.
CB vs SB3
3.5
3
2.5
2
1.5
1
0.5
0
DEFLECTION FOR CB
CB vs SB3
3.5
3
2.5
2
1.5
1
0.5
0
DEFLECTION FOR CB
10 20 30 40 50 60 70 80 90 100 110 120 130 140 150 156
LOAD (KN)
10 20 30 40 50 60 70 80 90 100 110 120 130 140 150 156
LOAD (KN)
DEFLECTION (MM)
DEFLECTION (MM)
FIGURE 4-18. LOAD VS. DEFLECTION CURVE FOR CB VS SB-3
DEFLECTION (MM)
DEFLECTION (MM)
From the load and deflection data of beams CB and beam SB-3, load vs deflection curve is plotted for both the beams. From this load vs deflection curve, it is clear that beam SB-3 had higher ultimate load carrying capacity as compare to beam CB. It indicate that CFRP sheet provide extra strength to the beam SB-3 and increase its load carrying capacity by 20%.
CB vs SB4
4.5
4
3.5
3
2.5
2
1.5
1
0.5
0
DEFLECTION FOR CB DEFLECTION FOR SB4
CB vs SB4
4.5
4
3.5
3
2.5
2
1.5
1
0.5
0
DEFLECTION FOR CB DEFLECTION FOR SB4
10 20 30 40 50 60 70 80 90 100 110 120 130 140 150 160 165
LOAD (KN)
10 20 30 40 50 60 70 80 90 100 110 120 130 140 150 160 165
LOAD (KN)
FIGURE 4-19. LOAD VS. DEFLECTION CURVE FOR CB VS SB-4
From the load and deflection data of beams CB and beam SB-3, load vs deflection curve is plotted for both thebeams. From this load vs deflection curve, it is clear that beam SB-3 had higher ultimate load carrying capacity as compare to beam CB. It indicate that CFRP sheet provide extra strength to the beam SB-3 and increase its load carrying capacity by 26.92%.
SB3 vs SB1
SB3 vs SB1
4.5
4
3.5
3
2.5
2
1.5
1
0.5
0
DEFLECTION FOR SB3
4.5
4
3.5
3
2.5
2
1.5
1
0.5
0
DEFLECTION FOR SB3
10 20 30 40 50 60 70 80 90 100 110 120 130 140 150 156 160 170
LOAD (KN)
10 20 30 40 50 60 70 80 90 100 110 120 130 140 150 156 160 170
LOAD (KN)
DEFLECTION (MM)
DEFLECTION (MM)
FIGURE 4-20. LOAD VS. DEFLECTION CURVE FOR SB-3 VS SB-1
From the load and deflection data of beams SB-3 and beam SB-1, load vs deflection curve is plotted for both the beams. From this load vs deflection curve, it is clear that beam SB-1 had higher ultimate load carrying capacity as compare to beam SB-3. Both the beams were strengthened with same CFRP configuration i.e. U-wrapping. Beam SB-3 was strengthened under sustain load and beam SB-1 strengthened normally.
ULTIMATE LOAD CARRYING CAPACITY
The load carrying capacity of the control beams and the strengthen beam are plotted below. It is observed that beam SB2 is having the max load carrying capacity.
ULTIMATE LOAD
200
180
160
140
120
100
80
60
40
20
0 CB SB1 SB2 SB3 SB4 LOAD (KN) 130 170 180 156 165
ULTIMATE LOAD
200
180
160
140
120
100
80
60
40
20
0 CB SB1 SB2 SB3 SB4 LOAD (KN) 130 170 180 156 165
PERCENTAGE
45
40
35
LOAD (KN)
LOAD (KN)
PECENTAGE
PECENTAGE
30
25
20
15
10
5
0 SB1 SB2 SB3 SB4
PERCENTAGE 30.77 38.46 20 26.92
Capacity of Beams
Figure. 4.21. Ultimate Load Carrying Figure. 4.22 Percentage Increase in the Capacity Load Carrying Capacity W.R.T Control
Beam
From the above figure we can observe the amount of increase in the ultimate strength for each strengthened beam with respect to the Control Beam.
DEFLECTION AT A
LOAD OF 130 KN
3.3
3.2
3.1
3
2.9
2.8
2.7
2.6
2.5
DEFLECTION AT A
LOAD OF 130 KN
3.3
3.2
3.1
3
2.9
2.8
2.7
2.6
2.5
DEFLECTION (MM)
DEFLECTION (MM)
DEFLECTION (MM)
DEFLECTION (MM)
DEFLECTION AT ULTIMATE LOAD
5
4
3
2
1
2.4
2.4
CB
SB1
SB2
SB3
SB4
3.19
4.01
3.73
3.22
3.83
CB
SB1
SB2
SB3
SB4
3.19
4.01
3.73
3.22
3.83
0
CB SB1 SB2 SB3 SB4
CB SB1 SB2 SB3 SB4
DEFLECTION
AT A LOAD OF 3.19 2.99 2.75 2.72 3.05
130 KN
DEFLECTION
AT A LOAD OF 3.19 2.99 2.75 2.72 3.05
130 KN
DEFLECTION AT ULTIMATE LOAD
Figure. 4.23 Decreases in the Deflection Figure. 4.24 Deflection at Ultimate Load
W.R.T Control Beam
CONCLUSIONS
The present experimental study is done on the behavior of reinforced concrete beams strengthened by CFRP sheets. Five reinforced concrete (RC) beams having same reinforcement detailing are casted and tested. From the test results, the following conclusions are drawn:
-
The ultimate load carrying capacity of all the strengthen beams were enhanced as compared to the Control Beam CB.
-
Initial flexural cracks appear for higher loads in case of strengthened beams.
-
The load carrying capacity of the strengthened Beam 2 was found to be maximum of all the beams. It increased up to 38.46 % more than the control beam CB, 7.69% more than strengthened beam SB-1, 18.46 % more than strengthened beam SB-3 and
12.17 % more than the strengthened beam SB-4.
-
Beam SB-3 which was retrofitted under sustained load in the web and sides only showed minimum deflection values on same loads as compared to other strengthened beams and the control beam.
-
The beam strengthened with a U-wrap configuration is more effective than the side-wrap configuration.
-
Strengthened beam SB-3 which was strengthened under sustained load shows less ultimate load carrying capacity as compared to strengthened beam SB-1 which is strengthened normally.
It shows that actuals load carrying capacity on site will be little bit lower as compare to laboratory results.
RECOMMENDATIONS FOR FUTURE WORK
Based on the finding and conclusions of the current study the following recommendations are made for future research in FRP strengthening:
-
-
Study of the bond mechanism between CFRP, AFRP and BFRP and concrete substrate.
-
FRP strengthening of RC T-beams with different types of fibers such as carbon, aramid & basalt.
-
Strengthening of RC L-beams with FRP composite.
-
Strengthening of RC L-section beams with web opening.
-
Effects of web openings of different shape and size on the behaviour of T & L-beams.
-
Effects of shear span to depth ratio on shear strengthening of beams.
BIBLIOGRAPHY
-
Aiello MA, and Ombres L, Cracking and deformability analysis of reinforced concrete beams strengthened with externally bonded carbon fiber reinforced polymer sheet, ASCE Journal of Materials in Civil Engineering, vol. 16, No. 5, pp.292-399,2004.
-
Alex L., Assih J., and Delmas Y. (2001), Shear Strengthening of RC Beams with externally bonded CFRP sheets, Journal of Structural Engineering, Vol. 127, No. 4, Paper No. 20516.
-
Arduini M, and Nanni A, Behaviour of pre-cracked R. C. beams strengthened with carbon FRP sheets, ASCE Journal of Composites for Construction, vol. 1, No. 2, pp. 63-70, 1997.
-
Cao S. Y., Chen J. F., Teng J. G., Hao Z., and Chen J. (2005), Debonding in RC Beams Shear Strengthened with completely FRP wraps, Journal of Composites for Construction, Vol. 9, No. 5, pp. 417-428.
-
Ceroni F. (2010), Experimental performances of RC beams strengthened with FRP materials, Construction and Building materials, 24, 1547-1559.
-
Deifalla A., and Ghobarah A. (2010), Strengthening RC T beams subjected combined torsion and shear using FRP fabrics: Experimental Study, Journal of Composites for Construction, ASCE, pp. 301-311.
-
Joseph R. Yost, Shawn P. Gross, and David W. Dinehart, Shear strength of normal strength concrete beams reinforced with deformed GFRP bars, Journals of composites for construction/November 2001.
-
Lakshamikandhan K.N, Sivakumar P, Ravichandean R, Damage Assessment and Strengthening of Reinforced Concrete Beams, International journal of material and mechanical engineering (IJMME) volume 2 Issue2, May 2013.
-
Pannirselvam N., Nagaradjane V., and Chandramouli K. (2009), Strength behaviour of fiber reinforced polymer strengthened beam, ARPN Journal of Engineering and Applied Sciences, Vol. 4, NO. 9, ISSN 1819-6608.
-
Sebastian WM, Sinificance of mid-span de-bonding failure in FRP-plated concrete beams, ASCE Journal of Structural Engineering, vol. 127, No. 7, pp.792-798, 2001.
-
Sheikh S. A., DeRose D., and Mardukhi J. (2002), Retrofitting of concrete structures for shear and flexure with fiber-reinforced polymers, ACI Structural Journal, Vol. 99, No. 4, pp. 451-459.
-
Y.C. Wang and J.I. Restrepo, Response of RC T-beams strengthened for flexure with staggered CFRP plates, Journals of composites for construction/AUGUST 2001.