
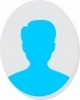
- Open Access
- Authors : Motaleb Hosain , Zahid Hasan , Fahim Faisal , Nafiza Anjum
- Paper ID : IJERTV9IS030410
- Volume & Issue : Volume 09, Issue 03 (March 2020)
- Published (First Online): 31-03-2020
- ISSN (Online) : 2278-0181
- Publisher Name : IJERT
- License:
This work is licensed under a Creative Commons Attribution 4.0 International License
Static and Vibration Analysis of Functionally Graded Metal-Ceramic Beam for Different Boundary Conditions
Motaleb Hosain
Dept. of Mechanical Engineering Shahjalal University of Science and Technology
Sylhet, Bangladesh
Zahid Hasan
Dept. of Mechanical Engineering Shahjalal University of Science and Technology
Sylhet, Bangladesh
Fahim Faisal
Dept. of Mechanical Engineering Shahjalal University of Science and Technology
Sylhet, Bangladesh
Nafiza Anjum
Dept. of Mechanical Engineering Shahjalal University of Science and Technology
Sylhet, Bangladesh
AbstractStatic analysis of functionally graded metal- ceramic beam is shown in this paper for different boundary conditions. For the ceramic part Zirconium Carbide was chosen for its high toughness and melting point. Structural steel is used in the metal part. Properties of the beam varies in the thickness direction according to power law. This paper also shows the principal natural frequency under different boundary conditions of the functionally graded beam. The static loadings are applied at the metal surface of the beam and the analysis are carried out through finite element method using higher order shear deformation theory for different power law exponent of the FGM.
KeywordsFunctionally graded matrial; power law; static analysis; metal ceramic beam;
-
INTRODUCTION
Functionally graded materials (FGM) are anisotropic materials normally consist of mixture of ceramic and metal. FGM is composed of various layers including pure ceramic at one end and pure metal at the other end. The layers in between the pure ceramic and metal are mixture of both ceramic and metal. The volume fraction of the fundamental materials is varying gradually through the thickness direction from one layer to another. By this way the composite can have the both specification of the both materials. As the layers have gradually varying properties along the thickness, the FGM can exhibit the ability to reduce the residual stress, thermal stress and stress concentration at the interface of the layer found in conventional composites. Ceramics usually have better thermal load capacity than the metal, but due to lack of their ductility they cannot withstand higher mechanical load. On the other hand, metals have better ability to withstand high mechanical load but as their co efficient of thermal expansion is higher than the ceramic, they cant withstand high thermal load. As mentioned above, FGM can exhibit the specification of both metals, they can withstand a very high thermal load and a mechanical load which is practically impossible compared to single materials. So, they are designed for high temperature applications such as, nuclear reactor, space shuttle, blade of a gas turbine armor protection for military vehicles, fusion energy devices, bio medical implants such as bone implants, dental implants etc.
Fig. 1. A typical FGM
The material properties at the various layers of an FGM can be found by means of a power series [1]. An example of a typical FGM is shown in fig. 1.
-
imek [2] solved the functionally graded simply supported beam subjected to a uniformly distributed load. The beam has been investigated by using Ritz method within the framework of higher order shear deformation theory and Timoshenko beam theory analytically. Aydogdu and Taskin [3] investigated the free vibration of an FGM using the Euler boundary bean theory, parabolic shear deformation theory and exponential shear deformation theory. H.J. Xiang and J. Yang [4] determined the free and forced vibrations of the FGM using the Timoshenko beam theory. Chakraborty and Gopalakrishnan [5] analyzed the wave propagation behavior of FG beam under high frequency impulse mechanical and thermal loading, by using a spectrally formulated finite element method. S. Alexraj,
-
Vasiraja and P. Nagaraj [6] studied about the cantilever and simply supported FGM beam under mechanical and thermal load by means of finite element method. They [6] assumed two boundary conditions, cantilever and simply supported and also they used Al as the metal in the FGM and ZrO2 as the ceramic. Yang J., Chen Y., Xiang Y. and Jia X.L. [7] studied about the free and forced vibration of cracked FGM subjected to an axial load and moving load. Benatta M.A., Mechab I., Tounsi A. and Adda Bedia E.A. [8] proposed an analytical solution of functionally graded short beams including warping effect.
In this paper, the static analysis of a ten layered ZrC- Structural steel FGM has done, and also investigated the natural frequency behavior of an FGM under no load for different boundary conditions were investigated. The analysis has been done by finite element method. It is assumed that the material property of the beam vary through its thickness direction according to the power law [1]. The boundary conditions are
assumed as cantilever, simply supported and both ends fixed. In this study, various displacements, stresses and strains of the FGM beam for different material compositions are examined.
-
-
THEORY AND FORMUALTION
A functionally graded beam having length of L, width b, thickness h with three different boundary conditions is shown in figure 2. The beam is subjected to a uniformly distributed load q0. In this paper, not only the behavior of FGM under bending loads but also the behavior of the FGM under compressive load is also presented. In the FGM the effective properties like
Fig. 3. Variation of Youngs modulus along the thickness direction
(a) (b) (c)
Fig. 2. (a) both ends fixed (b) cantilever (b) simply supported beam subjected to a uniformly distributed load.
(a) (b) (c)
Fig. 2. (a) both ends fixed (b) cantilever (b) simply supported beam subjected to a uniformly distributed load.
Where
xx and
xy are the normal and the shear strain
Youngs modulus E, Poissons ratio v, coefficient of thermal expansion and modulus of rigidity G vary continuously through the thickness direction according to the power law [1]. According to the power law form,
(1)
(2)
(3)
(4)
(1)
(2)
(3)
(4)
Efgm (Em Ec )Vc Ec
respectively. We are assuming that, the FGM obeys Hookes law, the stresses in the beam become
(9)
(10)
(9)
(10)
xx E fgm xx
xy Gfgm xy
Where xx and xy are axial normal and the shear stresses. The strain energy of the beam is given by
v fgm
(vm
-
vc
)Vc
-
vc
1 L
xx xx xy xy
xx xx xy xy
U ( y )dAdx 2
(11)
fgm
(m
c
)Vc
0 A
c
Gfgm
Efgm
2(1 v fgm )
Where A is the cross-sectional area of the beam. The equivalent stress is given by
z 1 N
xx yy xx yy cos2
sin 2
Vc h 2
2 2 xy
Here, N is a non-negativ variable parameter which describes the material property variation through the thickness
xx
2
yy
xx yy cos2
2 xy
sin 2
(12)
(13)
(12)
(13)
direction. Constituents c and m stands for ceramic and metal respectively. It is clear from equation (1-3) is that
Where is an arbitrary angle between equivalent stress and the normal stress. Now, substituting equation (7),(8),(9),(10) into
E fgm Ec
v fgm vc
fgm
c
at z h / 2
equation (11) gives
E E
v v
at
z h / 2
A (u
)2 2(B
-
kE )
fgm
m fgm m
fgm m
xx
0, x
xx xx
Variation of Youngs modulus along the thickness direction
(u0, x )(, x ) 2kExx (u0, x )
of an FGM is shown in figure 3.
Based on the higher order shear deformation theory, the axial displacement, ux, and the transverse displacement of any point
(w0, xx ) (Dxx k
2kFxx )(, x ) 2k(kH
2kFxx )(, x ) 2k(kH
U
U
xx
xx
1 L
2
2
H xx
of the beam, uz, are given as [9]
2 dx
(14)
u (x, z) u (x) z(x) kz3 (w
(x) (x))
2 0 F )(w )( ) k 2
x 0 0,x
xx 0, xx , x
Where u
and w
uz (x, z) w0 (x)
(5)
(6)
(5)
(6)
are the axial and the transverse displacement
H
H
xx
(w0, xx
)2 ( A
xx
xx
0 0 6kD
-
9k 2 F
)( w
)2
of any point on the neutral axis, is the rotation of the cross section, k=4/3p, and ( )x denotes a derivatives with respect to
(7)
(8)
(7)
(8)
x. Relationship between strain and displacement is given by
Where
xy
xy 0, x
E
(1, z, z 2 , z 3 z 4 ,
xx
ux,x
u0,x
-
-
-
z,x
kz3 (, x w )
( Axx , Bxx , Dxx , Exx , Fxx , Hxx )
fgm
0,xx
0,xx
0,x
0,x
z 6 )dA
xy
ux, y
-
zy,x
(1 3kz2 )( w ) A
( Axy
, Dxy
, Fxy )
Gfgm A
(1, z 2 , z 4 )dA
with the increment of power law exponent, the deformation decreases.
Solving Equation (12) by variational method and formulating
Table 1 Maximum Deformation Under 100kN Load.
K B 0
K B 0
global stiffness matrices
Cantilever
Both ends fixed
Simply supported
K1 N N
K 2 N N
K3 N N A
f
N (mm) (mm) (mm)
K K
K K
4 N N
5 N N 6 N N
(15)
Direction
Directio nal (w0)
K
K
K
C
0 0
0.0796
7 N N
8 N N
9 N N
Where [K ],,[K ] are the stiffness matrices of the beam. f is
0.1 0.408
0.059327 0.0147 0.003533
0.0657
0.06145
Total Dire
al (
ction Total
w0)
al (w0)
Total
0.510 0.07
8861 0.0176
0.004062
0.0864
3
46
2
57
Total Dire
al (
ction Total
w0)
al (w0)
Total
0.510 0.07
8861 0.0176
0.004062
0.0864
3
46
2
57
1 9 87
9 61 1
the generalized load vector governed by the uniformly distributed loads that is applied on the beam.
0.5 0.376
34
1 0.356
99
3 0.328
1
0.058783 0.0129
61
0.05822 0.0119
39
0.057259 0.0105
98
0.003243
7
0.003067
4
0.002792
4
0.0571
65
0.0570
61
0.0533
6
0.05358
2
0.04117
2
0.04934
7
Fig. 4. Modeling of FGM in ANSYS
Fig. 4. Modeling of FGM in ANSYS
5 0.315
77
0.054277 0.0101
63
0.002679 0.0520
05
0.04797
10 0.301
71
100 0.252
71
0.050854 0.0097
539
0.039671 0.0085
072
0.002551
7
0.002030
8
0.0476
44
0.0427
38
0.0404
0.02533
2
-
-
METHODOLOGY
The finite element analysis of the beam is carried out in this paper to investigate the static behavior of an FGM under mechanical load and natural frequency under no load. There are few software like ANSYS, ABAQUS that can analyze finite element method. In this paper, ANSYS is used to carry out the calculation of finite element method.
The functionally graded beam is composed of zirconium carbide (ZrC; Ec=406GPa, vc=0.19, c=1.41×10-7K-1) and structural steel (Em=200GPa, vm=0.3, m=1.2×10-5K-1). The properties of the transitional layers between metal and ceramic changes through the thickness of the beam according to the power law. The bottom surface of the beam is pure ceramic and the upper surface of the beam is pure metal. The length, width and the thickness of the beam is kept as L=0.4m, b=0.1m, h=0.1m. Uniformly distributed load of 1000N, 1500N, 2000N, 2500N, 3000N, 5000N, 10000N, 20000N, 50000N and
100000N are applied on the beam respectively and the performance is studied. The mechanical load was applied on the metal surface. The FGM beam was modeled in ANSYS. The mesh size of 1mm is taken in this paper. Total number of nodes is 2342610 and the total number of elements is 500000. Figure 4 shows the modeling of an FGM in ANSYS.
-
RESULTS
The responses under static loading is shown in this section. Table 1. represents the response total deformation and directional deformation under 100kN force. The total deformation under other applied forces are shown in fig. 8-10. From the figures, deformation is maximum for the minimum value possible for power law exponent. That means the deformation is maximum for metal constituents. After that,
The stress and strain under 100kN force is tabulated in table 2 and table 3 respectively. And responses under other loads are shown in fig. 5-7 for different boundary conditions. Both the stress and strain are maximum for N=0.1 for all boundary conditions except shear stress for both ends fixed beam. For both ends fixed beam, shear stress is maximum for metal constituents only. There is a dissimilarity in this stress and strain section compared to the previous deformation section. For cantilever FG beam, both the equivalent and shear stress is maximum for N=0.1. After that point, stress is reducing gradually with the decrease in power law exponent. For both ends fixed beam, equivalent stress is maximum for N=0.1 but shear stress is maximum for metal constituent. After that point the power law exponent was taken as 0.5, for this exponent, both equivalent and shear stress decreased, but after that point, both the stresses increased and then decreasd with the increment of power law exponent. Same phenomenon happened for simply supported FG beam too.
The same response is also true for strains too. It can clearly be seen from table 3 and fig. 5-7.
Table 2. Maximum Stress under 100kN Load
Cantilever (MPa)
Both ends fixed (MPa)
Simply supported (MPa)
N
Equiv alent ()
Shear (xy)
Equival ent ()
Shear (xy)
Equivale nt
()
Shear (xy)
0
231.9
9
63.876
65.976
20.48
513.89
125.31
0.1
376.5
8
79.442
74.893
18.747
1506.4
390.7
8
0.5
329.5
3
74.655
48.158
12.452
507.56
129.42
1
306.8
2
70.889
61.412
16.348
1462.9
380.2
2
3
287.2
9
9.648
55.89
14.95
1453.2
377.7
9
5
282.6
2
9.1192
54.315
14.407
1452
377.4
7
10
277.5
7
8.5166
52.87
4
13.823
497.22
126.89
100
201.8
8
5.9141
55.89
13.567
497.06
126.81
Table 3. Maxi
mum Strain under 100k
N Load
Cantilever
Both ends fixed
Simply supported
N
Equiv alent ()
Shear (xy)
Equival ent ()
Shear (xy)
Equival ent ()
Shear (xy)
0
0.001
16
0.00083
0.000
33
0.00026
6
0.0025
7
0.00162
9
0.1
0.001
476
0.0010
3
0.000
298
0.00024
4
0.0037
1
0.0022
91
0.5
0.001
382
0.0009
71
0.0001
79
0.00016
2
0.0012
5
0.00075
9
1
0.001
31
0.00092
2
0.000
255
0.00021
3
0.0036
03
0.0022
29
3
0.001
167
0.0001
25
0.000
229
0.00019
4
0.0035
79
0.0022
15
5
0.001
097
0.0001
19
0.000
219
0.00018
7
0.0035
76
0.0022
13
10
0.001
018
0.0001
11
0.000
208
0.00018
0.0012
25
0.00074
4
100
0.000
497
0.00003
47
0.000
142
0.00007
95
0.0012
24
0.00074
3
Table 3. Maxi
mum Strain under 100k
N Load
Cantilever
Both ends fixed
Simply supported
N
Equiv alent ()
Shear (xy)
Equival ent ()
Shear (xy)
Equival ent ()
Shear (xy)
0
0.001
16
0.00083
0.000
33
0.00026
6
0.0025
7
0.00162
9
0.1
0.001
476
0.0010
3
0.000
298
0.00024
4
0.0037
1
0.0022
91
0.5
0.001
382
0.0009
71
0.0001
79
0.00016
2
0.0012
5
0.00075
9
1
0.001
31
0.00092
2
0.000
255
0.00021
3
0.0036
03
0.0022
29
3
0.001
167
0.0001
25
0.000
229
0.00019
4
0.0035
79
0.0022
15
5
0.001
097
0.0001
19
0.000
219
0.00018
7
0.0035
76
0.0022
13
10
0.001
018
0.0001
11
0.000
208
0.00018
0.0012
25
0.00074
4
100
0.000
497
0.00003
47
0.000
142
0.00007
95
0.0012
24
0.00074
3
Fig. 11-13 show the variation of directional deformation (Y- Axis) along the length of the FG beam for different boundary conditions. It is very clear from the figures is that, the transverse displacement is maximum for metal rich FG beam and minimum for ceramic rich FG beam as we know that deformation is inversely proportional to the Youngs modulus. Metals have lower Youngs modulus compared to the ceramic. The functionally graded beam gradually becomes ceramic rich from the metal portions. As a result, the deformation is maximum for metal rich FG beam, but with the increment of power law exponent, the beam is intending to become more ceramic rich material. So, with the increment of
power law exponent, the deformation is decreasing.
The variation of transverse deformation curves are showing general trend regarding their boundary conditions when subjected to a uniformly distributed load. That confirmation depicts the validity of this work that is shown in this paper.
The variation of shear stress (xy plane) along the length of the FG beam for different boundary conditions are shown in fig. 14-16.
Fig. 6. Equivalent stress vs equivalent strain for both ends fixed beam.
Fig. 7. Equivalent Stress vs strain for simply supported beam
Fig. 6. Equivalent stress vs equivalent strain for both ends fixed beam.
Fig. 7. Equivalent Stress vs strain for simply supported beam
This phenomenon also obeys the stress relation with power law exponent that were mentioned earlier in this paper.
Fig. 5. Equivalent stress vs equivalent strain for the cantilever beam
Fig. 5. Equivalent stress vs equivalent strain for the cantilever beam
All the variations along the length of FG beams are taken from the upper side of the beam. Similarly, along the thickness direction, the results can be examined. In this paper, variation of responses along the length from the upper layer of the beam is presented only.
One question may arise, why are the responses showing pretty much same curve. Well the answer is : the responses under static loading represents similar curves because the applied loads were following pretty much same trend as the total deformation or stress vs strain curve.
Fig. 8. Total deformation for cantilever beam
Fig. 9. Total deformation for both ends fixed beam
Fig. 12. Variation of directional deformation along the length of the FG both ends fixed beam
Fig. 10. Total deformation for simply supported beam
Fig. 13. Variation of directional deformation along the length of the FG simply supported beam
Fig. 11. Variation of directional deformation along the length of the FG cantilever beam
Fig. 14. Variation of shear stress along the length of the FG cantilever beam
Fig. 15. Variation of shear stress along the length of the FG both ends fixed beam
Fig. 16. Variation of shear stress along the length of the FG simply supported beam
Free vibration means the rate of vibration in a system when no load is applied on the system despite of its weight. Natural frequency depends on the material property of the structure. To be specific, the natural frequency depends on the density and Youngs modulus of any structure. Natural frequency is proportional to the square root of the modulus of elasticity and inversely proportional to the square root of the density [10]. Natural frequency also depends on different boundary condition as it affects the vibration modes. So, for specific application boundary condition should be specified properly before calculating the natural frequency.
As beams have infinite numbers of degree of freedom the natural frequency is also infinite. Because, each degrees of freedom have their own natural frequency. In this study, the principal mode of natural frequency is determined for three different boundary conditions.
Fig. 17. Natural frequency of the FG beam under different boundary conditions
Table 4. Natural frequency of ZrC/Steel based FGM
N
Cantilever
Hz
Fixed
Hz
Simply Supported
Hz
0
491.51
2431.2
862.14
0.1
538.95
2654.5
897.79
0.5
591.45
2901.7
934.79
1
614.95
3084.6
961.56
3
653.67
3344.9
1003.4
5
670.61
3440.1
1019.1
10
690.18
3535.7
1035.3
100
763.34
3825.6
1341
Table 4. shows the exact values of natural frequency for different power law exponent and for different boundary conditions. Fig. 17. shows a graphical representation of these values in terms of different boundary conditions and in terms of different values of power law exponent. It is clear from fig. 17 that natural frequency is maximum for both ends fixed beam. Also, whenever the FG beam intended to become ceramic rich, natural frequency increases.
-
CONCLUSION
Static and free vibration analysis of ZrC/Steel based FGM was carried out in this paper by finite element method. The results indicated that the response and stress propagation in the FG beam for different boundary conditions were much more different than those found in the isotropic beams. The free vibration analysis indicated that whenever the beam is intended to become ceramic rich, natural frequency increased. During the analysis, the material property at the different layers of the FG beam were strictly following the power law curve that has been shown in figure 3.
REFERENCES
[1] |
H. T. N. M. Wakashima K., Space applications of advanced structural materials, SP, 1990, pp. 303-397. |
[2] |
M. imek, "Static analysis of a functionally graded beam under a International Conference on Energy Efficient Technologies for uniformly distributed load by ritz method," International Journal of Sustainability (ICEETS), 2013. Engineering and Applied Sciences (IJEAS), vol. 1, no. 3, pp. 1-11, 2009. [7] Y. J., C. Y., X. Y. and J. X.L., "Free and forced vibration of cracked |
[3] |
M. Aydogdu and V. Taskin, " Free vibration analysis of functionally inhomogeneous beams under an axial force and a moving load," Journal graded beams with simply supported edges," Materials & Design, vol. of Sound Vibration, vol. 312, no. 1-2, pp. 166-181, 2008. 18, no. 5, pp. 1651-1656, 2007. [8] B. M.A., M. I., T. A. and Adda Bedia E.A., "Static analysis of |
[4] |
H. Xiang and J. Yang., ""Free and forced vibration of a laminated FGM functionally graded short beams including warping and shear Timoshenko beam of variable thickness under heat conduction," deformation effects," Computational Materials Science, vol. 44, no. 2, Composites: Part B , vol. 39, no. 1, pp. 292-303, 2008. pp. 765-773, 2008. |
[5] |
C. A. and G. S., "A spectrally formulated finite element for wave [9] R. J.N, Energy and Variational Methods in Applied Mechanics, New propagation analysis in functionally graded beams," International York: John Wiley, 1984. Journal of Solids and Structures, vol. 40, no. 10, pp. 2421-2448, 2003. [10] W. T. Thomson and M. D. Dahleh, Theory of Vibration with |
[6] |
S. Alexraj, N. Vasiraja and P. Nagaraj, "Static behaviour of functionally Applications, New Delhi: Dorling kindersley (India) Pvt. Ltd, 2007. graded material beam using finite element method," in IEEE 2013 |