
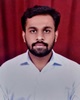
- Open Access
- Authors : Bharath J
- Paper ID : IJERTV11IS120170
- Volume & Issue : Volume 11, Issue 12 (December 2022)
- Published (First Online): 10-01-2023
- ISSN (Online) : 2278-0181
- Publisher Name : IJERT
- License:
This work is licensed under a Creative Commons Attribution 4.0 International License
Simulation of Effect of Weld on the Acoustic Performance of the Muffler
Bharath J
MTech student, Dept of Mechanical Engineering
B.M.S College of Engineering, Bengaluru, India
Abstract The acoustic characteristics of a simple expansion chamber muffler is examined in this study. Basically, two mufflers have been studied: a solid muffler with no welded areas and a muffler with welding between the baffle plates and tubes, in addition to longer inlet and outlet pipes. For the finite element approach (FEM) analysis, the acoustic module of MSC Actran, MSC Nastran and Patran software is employed. The muffler is designed using the 3D modelling application Solid works. The modal extraction is performed for the both type of mufflers for the frequency range of 10Hz to 2000Hz to obtain different modes and to determine its dynamic characteristics. The results showed that the normal modes frequencies are slightly higher for welded muffler than solid muffler. The transmission loss (TL) of the muffler generated by the FEM simulation model is measured using a unit value of excitation of 1Pa with a frequency response of 10Hz to 2000Hz and muffler with and without the welded section is tested. The value of the transmission loss for the solid muffler is found to be higher than the welded muffler. The tailpipe noise simulation is also carried out for the both muffler types by creating a microphone at the distance of 30m with an angleof 45 degrees from sound source. The noise may vary with increase in the distance from the tailpipe. After evaluating all the results, it was found that increase in the stiffness or elastic modulus of the muffler with welded joints leads to increase in the normal modes frequencies, thereby decreasing its sound attenuating ability, but thetailpipe noise was almost similar to both types.
Keywords Muffler; Modal Extraction; Transmission Loss; Tailpipe Noise; Frequency Response
-
INTRODUCTION
Any acoustic item typically makes noise, which can be uncomfortable. In its most basic form, noise is the motion of air or gas molecules which creates differential pressure inside human ear canals. Such pressure fluctuations have been turned in with what humans term "Noise" through our auditory receptors. Pressure waves are produced in an internal combustion engine when the outlet valve frequently releases, enabling higher gas into the exhaust manifold. The noise we perceive is caused by pressure pulses. As both the motor speed rises, consequently do the pressure variations, resulting in an increased frequency noise.
The exhaust system somehow doesn't produce all of the noise produced by a vehicle. Suction sound, structural vibrations, and generated noise from the motor housing and transmission are further factors to vehicle noise level [1]. The muffler would be a component that reduces the volume of sound released through a combustion engines exhaust.
Most engines with internal combustion have mufflers mounted in their exhausts, despite the fact that the muffler is not meant to perform any main exhaust purpose. The muffler is developed as an acoustic sound dampening equipment to decrease the intensity of the engine's noise level through Acoustic shushing.
-
Classification of the Muffler
There isnt any technical distinction between a muffler and a silencer, and both names are used alternately. Even though the concepts are not unfamiliar tomany individuals, mufflers make regular living considerably more pleasant. The need for mufflers is mostly focused toward machine components or regions wherethere is a great quantity of generated noise, such as high combustion tubes, turbomachinery, and rotary pumps [4]. Despite the various requirements for mufflers, only two primary types are employed. They are both passive and active silencers. Absorptive mufflers are made up of sound- absorbing materials and are used to envelop the released energy in a gas flow. Reactive silencers use a sophisticated approach to enhance sound absorption while meeting predefined parameters such as drop in pressure, flow rates, and so on [4]. Many complex silencers in the market now integrate both technologies to enhance sound absorption and generate realistic parameters.
-
Absorptive mufflers: Acoustic materials are those that reduce vibration and noise. There are four distinct kinds of materials which are frequently utilized to reduce vehicle vibration and noise. These act as obstructions and absorption coefficients in loud areas, as well as insulation and attenuation in bright areas. Certain substances reduceair sounds, while others reduce structure-borne sound. In this section, each of the materials described has an impressible factor on the sound transmission loss (TL).
Fig. 1. Absorptive Muffler. (3)
Such sort of muffler is used in conjunction with absorbent materials to convert acoustic energy into heat. Absorptive mufflers are typically linear pipes with many layers of
absorptive materials, such as fiberglass, to reduce the gener- ated sound output. The consistent dampening property of sound – absorbing materials is an unique characteristic of this kind of muffler.
-
Reactive Muffler: Another muffler is employed using a variety of intricate routes to reduce the quantity of acoustic energy transmuted. It is accomplished by changes in impedance at the connections, which causes rise to reflected pulses. The engines performance is reduced by limiting the quantity of energy transmuted, so the energy returned to the source is extremely high [5]. These kind of muffler is commonly used for gasoline engines and mufflers in harsh situations. The mufflers effectiveness is optimal in lower frequency, whereas absorptive types are employed at high frequencies
A dissipative muffler uses sound-absorbing materials to eliminate the energy of the acoustic motion in the wave as it passes through the muffler. Higherabsorption coefficients may result to even more energy absorption and lower emitted noise intensity. Probably one of the best uses for this type of muffler is in sportscars when performance characteristics is desired and high back pressure is not created to mask the sound. As a result, the mufflers performance improves. This kind is frequently employed in applications involving broadband and narrowband sounds [4].
Fig. 2. Reactive Muffler. (3)
The following is a distinction between both types of silencers: absorptive mufflers break sound energy, whereas reactive mufflers absorb energy and generate disturbance to limit the outgoing sound power. Reactive silencers, that are commonly used in automobiles, reflect sound waves back to the source and prevent sound from travelling through the pipe. The silencers governing concept is a Helmholtz resonator or expansion chamber, which requires line theory of acoustic transmission. Muffler performance is described by three criteria: noise reduction, insertion loss, and transmission loss [4].
-
-
Engine Exhaust Muffler Regulation
In practice, an exhaust muffler was intended to meet a portion or all of the minimum guidelines.
-
A significant insertion loss: An exhaust muffler is meant to keep sup pressed tailpipe sound at least 5 decibels below than gasoline engine body noise and or common sources of noise, such as transmission noise in earth moving machinery [2]. Although it is widely known that the
majority of the noise is restricted to the firing frequency and its first couple vibrations,a spectrum analysis or speed order analysis of unmuffled exhaust noise is often necessary for awareness of the frequencyrange of interest [3].
-
Backpressure: It refers to the additional static pressure put on the engine by the muffler due to the limitation in the flow of flue gas. This needs to be maintained to a limit. Although, for single-cylinder two- stroke-cycle engines, the immediate pressure applied by huge (usually nonlinear) vibrations is more important than average back pressure, which would affect the brake power, volumetric efficiency, and thus the particular fuel usage rate in a four-stroke-cycle engine [3].
-
Size of the muffler: A huge muffler would present issues with space, stability (due to its heaviness), and, of course, pricing [3].
-
Durability: A consistent wall temperature is necessary to prevent thermal cracking. The muffler must be constructed of a corrosion-resistant substance [3].
-
Oftentimes, ignition capability is necessary (specifically for agricultural application) [3].
-
Overall purity of the tailpipe noise at idling and when accelerating from the curb is also important (specifically for passenger cars) [3].
-
Breakout sound from silencer chambers should be kept to a minimum such that perhaps the gross transmission loss is close to the axial transmission loss [3]
-
The effectiveness of the muffler really should not change over time [3].
-
Fluid sound inside this muffler component as well as at engine exhaust outlet must be kept to a minimum, especially for mufflers with a high transmission loss. In addition, the fluid sound frequently limits the insertion loss of Ventilation systems mufflers [3].
-
-
-
LITERATURE REVIEW
Takashi Yasuda et al presented in this study, based on the normal construction, a muffler with just a connecting hole on the tail pipe to increase its acoustic performance. The suggested mufflers acoustic capabilities were investigated both experimentally and theoretically in the frequency and temporal domains. This was discovered that linking hole enabled the suggested muffler to exhibit Helmholtz Resonator noise reduction performance. As a result, the suggested muffler may reduce noise at both low and intermediate frequencies. Using the acoustic electronic analogy, the frequency equation of this structure was determined. It is useful for assessing attenuation performance during the pre-design or tuning stages [10].
Anant W. Wankhade et al proposed a simple-to-build, effective silencing is a device that can produce excellent results in noise reduction. One of the ways for assessing the noise level at the tail pipe is acoustical evaluation. This optimization uses Finite Element Analysis to improve the acoustic analysis of a muffler. PRO E Wildfire 5.0 is used to model the muffler, and COMSOL MULTIPHYSICS is utilized for
acoustic analysis. The impact of protrusion of inlet and outlet pipe within the chamber, as well as the location of the additional inlet tube (i.e. split inlet) to the chamber, were then tuned to achieve the lowest sound intensity (SPL) or the highest transmission loss (TL).The impact of SPL on the exhaust surfaces is not taken into account. The mufflers substance is likewise unconsidered. This improved elliptical muffler type is manufactured and then validated via experimental research [11].
Potente, Daniel in this article discusses broad concepts of muffler design and illustrates the primary benefits of various muffler types. While building a muffler for any purpose, different functional criteria, including both acoustic and nonacoustic engineering concerns, should be considered, as outlined in this paper. From the transmission loss vs. frequency graph for a straight pipe absorptive silencer, Double transmission loss can be achieved by utilizing an absorptive substance [12].
A. Selamet et al The acoustic absorption of a single-pass, perforated concentric silencer packed with continuous strand fiber is first theoretically and empirically explored. The investigation is then expanded to a specific form of hybrid silencer composed of two single-pass perforated filling chambers coupled with a Helmholtz resonator [13].
Rahul et al focused on the transmission loss (TL) and natural frequency (NF) of the muffler were studied. They created a single expansion chamber and a double expansion chamber muffler for this. They used CATIAV-5 to model the solid modal of an exhaust muffler, and ANSYS to perform modal analysis to examine the vibration and natural frequency of the muffler. To avoid resonance, distinguish the operating frequency from the natural frequency. They discovered that a double expansion chamber outperforms a single expansion chamber [14].
Mr. Jigar H et al tries to explain numerous types of mufflers and the architecture of an engines exhaust system. The goal of this research is to select a muffler design that minimizes engine noise and back pressure significantly. There are several parameters that must be taken into account when designing. These variables have an impact on muffler effectiveness. They eventually discovered that a combined muffler is more efficient than reactive and absorptive mufflers [15].
The following facts are revealed by the literature on exhaust muffler analysis. Experimental modal analysis by Brian J. Schwarz et al detailed the various Frequency response measurement testing. Getting modal parameters in various methods. Wang jie et al. conducted the modal analysis of a car exhaust muffler throughout the design process to discover the natural frequencies and mode shapes. To avoid resonance in the exhaust muffler, identify the operating frequency from the natural frequency [16].
Tyler de la Roy did work in this area [18]. This research focuses on the use of absorption material in mufflers to decrease tailpipe noise. In his experiment. ,Mehdizadeh et al. employed polyester lining. The 3D Finite Element Method might be used to solve the exhaust noise problem. This approach calculates the Transmission Loss (TL) of a muffler
[19]. Hazel et al employed a finite element technique to forecast the 4-pole parameter for various muffler combinations in order to get transmission loss characteristics. Rockwool is employed as an absorbing medium in their operations [20]. Zheng et al. extended this technology to a linked hybrid muffler. The Galerkian or Variational approach is used to perform the FEM [21].Farhat et al. solved the Helmholtz issue using the Galerkian technique, i.e., the Helmholtz equation [22]. Denia et al. focused on muffler size, expanded inlet/outlet responsibilities, absorbent resistivity, and used a two-dimensional axisymmetric technique to match acoustic pressure and velocity over the muffler. Its findings show that quarter wave resonances boost acoustic performance at low and mid frequencies, whereas absorption materials attenuate sound at high frequencies. It also shows that increasing the radius and chamber length leads to larger transmission loss.
According to Jorge P Arenas and Malcohn J Crockers work, many porous or fibrous absorption materials can be employed to reduce exhaust system noise. According to them, the absorption qualities of the materials vary based on frequency, composition, thickness, surface polish, and mounting technique. They believe that metal foam or ceramic foams will be the most effective sound absorption materials in the near future. SiC is one such ceramic type that can withstand high temperatures [23].
Oishi et al. developed a patented ceramic acoustic absorber using SiC fiber as a lightweight sound absorption material. It provides a high level of sound absorption [24]. It can withstand temperatures ranging from 1800 to 2300 Celsius. It may also function as a perforated body due to its void ratio of 80- 92 percentage. It has a typical diameter of 50-450 m on the front surface and 500-3400 m near the back.
The air flow resistivity of the material ranges from 4 to 60 [CGS Rayls/cm]. In research, Bilawchak and Fyfe used numerical methods to calculate the TL in various silencrs. They came to the conclusion that FEM and the three-point technique worked well in a packed muffler. They employed perforated plates as acoustic medium, as well as air and absorption materials. To confirm its findings, many test scenarios were reviewed and compared to experimental outcomes [25].
D.Siano et al found that Acoustic performance is given at the component level as attenuation vs frequency (Transmission Loss), based on the components proper ties. Various numerical analyses are used to achieve this goal. First, a one- dimensional simulation code (GT PowerTM) is utilized to investigate the effect of high temperature gas flow on the mufflers acoustic attenuation performance in the plane wave zone. The VNOISETM code, which is especially built for acoustic applications, is also used to realize a more advanced 3D FEM/BEM method. Obviously, such analysis provides for more precise findings at high frequency, with less reliance on mesh size. Flow velocities and gas temperatures are also explored. The Transmission Loss factor acquired from these methods is then compared, as well as their potential and limits [26].
Material selection influences several elements of a components design. Many factors influence material selection. One interesting factor is that the more challenges a component faces during its in-service life, the greater the need to improve material performance and the broader the research required to understand the challenges confronting the component prior to carrying out material selection. High temperature and corrosion attack were identified as the primary defects limiting the service life of an automotive exhaust system, and stainless steel (Ferritic stainless steel and Austenitic stainless steel) was chosen as a suitable material to withstand these challenges, which is not too different from the material of conventional exhaust system [9].
-
METHODOLOGY
-
Problem Definition
Mufflers are positioned at the back, bottom of the car and are portion of an exhaust system. They help to reduce car emissions and noise. When an airflow opens, a tremendous rush of the burned hydrocarbons produced during the combustion of the engine is expelled into the exhaust. This gas discharge generates extremely intense acoustic signals.
Each part of the muffler is intended to help with noise cancellation. Also, the panels of a muffler have been specially engineered to collect part of the sound waves. Numerous things must be considered while developing a muffler for an automobile application. Examples include appropriate insertion loss, backflow, dimension, sturdiness, ideal sound, cost, weight, simple structure, and style. Since the welding procedure is carried out around different parts inside the muffler, the properties of MIG weld join across the sections will also affect the acoustic performance and modal behavior of the muffler.
Fig. 3. Muffler with welded regions. (figure caption)
This study explores the mufflers acoustic performance and modal behavior with and without welded joints. Initially, the simulation of acoustic performance and its mode shape nature is addressed without taking the welding portions into account. Subsequently, simulations will be performed using MSC Actran FFT software by considering the welded sections into account. The outcomes are then evaluated how the welding on the muffler impacts its acoustic performance such as transmission loss, tailpipe noise and mode shapes characteristics of muffler.
-
3D Modelling of the Muffler
This is actually a form of reactive muffler. As a result, sound wave cancellation takes place inside the muffler to reduce noise. The resonant chamber is built in such a way that the same amount of frequency created against the sound waves coming from the engine exhaust cancels out the influence of the other. Muffler is divided into three primary resonant chambers such as input chamber, middle chamber, and output chamber.
Fig. 4. Inside view of Muffler.
The exhaust gas from the engine output enters the muffler from the intake pipe and passes through the catalytic converter. The gas is reflected from the muffler wall. Some of it reflects in the opposite direction of the entrance flow gas, while other gas travelling in the reverberation chamber and passing through the baffle hole enters the middle chamber. Next, gases from the perforation and the input chamber combine and enter the exit chamber, where it is expelled to the atmosphere via the outlet pipe. The 3D model will have dimensions of 300mm x 200mm x 100mm, with one that has no welding sections and another with welded sections.
Fig. 5. 3D model with and without welded region.
The necessary weld size of 5mm will be used to construct the fillet weld between the centre baffle plate and the outer shield.Following that, the mufflers normal mode analysis will be performed, followed by transmission loss.
Fig. 6. Inside view of welded regions on muffler.
-
Mesh model of the muffler
After modeling of CAD model of muffler, meshing of all components of the muffler i.e., inlet-pipe, outlet-pipe, and baffle plates of the muffler were done simultaneously with fine mesh type. The meshed model of the fixture had 446109 elements and 89538 nodes. Fig. 7 depicts the meshed model of the muffler without welded region.
Fig. 7. Meshed model of the solid muffler.
Mesh refinement near welded regions, edges, holes were done to capture stresses more effectively. The meshed model of the fixture had 491244 elements and 103374 nodes. Fig. 8 depicts the meshed model of the muffler with welded region.
Fig. 8. Meshed model of the welded muffler.
-
Normal Modes Analysis of the muffler
Modal analysis is an approach for understanding a system in terms of own dynamic properties, that include frequency, damping, and mode forms. Natural vibration modes are intrinsic in a dynamic model and are totally controlled by its physical parameters and spatial patterns. Upon loading the Solid works model into MSC Actran.
Finally mesh the provided model. Ferrite stainless steel is used as a material for the analysis as shown in the
table. The material after the welding process will alter its material properties, in which the material will become more stiffer compared to this parent material.
TABLE I. MATERIAL PROPERTIES
Type of Muffler
Elastic Modulus (E), GPa
Density kg/m3
Poissons ratio
Solid Muffler
190
7800
0.3
Welded Muffler
215
7860
0.3
-
Boundary Conditions
Mufflers may be viewed of as models with both ends fixed at the inlet and outlet. Setting the mode extraction for the frequency range of 10Hz to 2000Hz with the 10 number of modes allows the relevant mode shape to be solved as long as each natural frequency is obtained.
Each nodes natural frequency and muffler displacement may be simply monitored and evaluated using MSC Actran or MSC Nastran and Patran, and the modal forms can be animated.
Fig. 9. Inlet and Outlet fixed.
-
Transmission Loss of the muffler
The TL is a comparative term that could be rapidly generated and measured between many acoustic qualities. The difference in sound level of power between both the incident wave driving the exhausts as well as the transmitted wave to an anechoic termination is denoted as TL.
Fig. 10. Illustration of transmission loss in a muffler.
MSC Actran software is used for the simulation of transmission loss of the muffler. After performing the modal extraction for the muffler, based on its frequency range i.e 10Hz to 2000Hz, Direct frequency response analysis will be performed for the same range withe the steps of 100Hz.The Direct Frequency Response analysis is a computing process that provides the physical coordinates ofthe response of a vibroacoustic or aero-acoustic system to a specific excitation.
-
Finite Fluid Components
Fluid components will be formed inside the muffler, and the fluid material will be called Air. Only the inner surface of the muffler, also known as the inside skin of the muffler, is pulled for forming the fluid components, i.e. wherever the fluid material would interact within the muffler, only those surfaces are taken. Because of the centre baffle plate within the muffler, two chambers will be formed, one for inlet chamber and one for outlet chamber.
TABLE II. FLUID PROPERTIES
Type of Fluid
Speed of the sound, m/s
Density kg/m3
Air
340
1.225
Fig. 11. Fluid Components for solid muffler.
Following the creation of the fluid components, the domain to which the fluid attributes will be assigned will be constructed.
Fig. 12. Fluid Components for welded muffler.
-
Modal Duct Components
Modal ducts are formed at the inlet and outlet pipes to allow air to flow within the muffler. During this method, a modal basis is applied at the inlet to excite the system by confining the plane mode.
First at the inlet, two propagating modes will be formed: mode 1 (plane mode excitation of intensity 1) and mode 2 (non- reflecting BC in the opposite direction). Because the excitation value at the inlet is 1Pa, unit value excitation will be employed in this simulation.
Fig. 13. Modal Duct Component at Inlet.
Next at the outlet, only one propogating mode will be formed. At the outlet, a modal basis is used to depict a non-reflecting BC (semi-infinite duct). In the transmission loss simulation it will be aasumed that the outlet pipe will be extending to some distance, and that sound will not be reflected.
Fig. 14. Modal Duct Component at Outlet.
-
Solid Component
The Isotropic material is assigned to the structural domain by the Solid component. The solid or parent material employed in this case will be ferrite stainless steel, and its parameters are listed below.
Property
Value
Unit
Name
Ferrite Stainless Steel
Elastic Modulus
190
GPa
Damping
0.1
%
Poissons Ratio
0.3
Solid Density
7800
kg/m3
TABLE III. PARENT MATERIAL PROPERTIES
Fig. 15. Stainless steel material for solid muffler.
Separate material attributes are allocated to the welded region. The elements on the welded areas were selected separately from the parent material, and the parameters such as elastic modulus and density were altered only for that welded region [27].
The properties of the welded region are listed in the below table
TABLE IV. WELD MATERIAL PROPERTIES
Property
Value
Unit
Name
MIG Welding
Elastic Modulus
215
GPa
Damping
0.1
%
Poissons Ratio
0.3
Solid Density
7860
kg/m3
This is how the welded region (shaded on the red colour) on the central baffle plate, end plates and on the surface of inlet an outlet pipe looks.
Fig. 16. Welded regions on solid muffler.
-
Perforations
Mufflers are made of perforated metal tubing, which has good sound dispersion qualities. Most contemporary mufflers include a variety of components, but their sound silencing capabilities may be attributed to perforated tubes operating in conjunction with muffler packing material [28]. The sound energy from the engine flows through the systems pipes until it reaches the end of the muffler, where a piece of perforated tubing awaits. The holes in this tube guide sound into the mufflers sound-absorbing packing material or into the chamber, which is often comprised of fiberglass, steel wool or a similar substance in absorptive type and in reactive type it remains uncovered. The sound you hear as a car accelerates is what exits from there [29]. In this work a solid thin shell component used as perforation material. The properties of the perforation are listed in the below table.
TABLE V. PERFORATION MATERIAL PROPERTIES
Elastic Modulus
215
GPa
Damping
0.1
%
Poissons Ratio
0.3
Solid Density
7860
kg/m3
Perforation radius
0.0015
m
Plate thickness
0.001
m
Perforation Distance
0.006
m
Grid Geometry
TRIA
Fig. 17. Perforations regions on the tubes.
-
Tailpipe Noise of the Muffler
For a unit source input, the transmission loss is the ratio of sound pressure at intake to output. To obtain the true amount of noise at the mufflers end, we must insert a source at the entrance. The intake modal duct is provided an input in the following instance, and the noise level is measured at the outflow end. The radiation sphere will be added at the outlet modal duct component for the sole purpose of creating a sound reflecting surface; noise from the tailpipe will hit the surface and reflect. A tiny element will also be developed to operate as a sound receiver in order to receive the sound. This approach will apply to both types of mufflers i.e solid muffler
and welded muffler.
Fig. 18. Radiation Shell at the outlet.
The tailpipe noise would generally differ considerably on the distance from the receiver is located. The receiver isnt going to be kept immediately next to the tailpipe or on the outlet pipes centerline. The receiver is usually installed at a different angle and distance. Typically, the receiver will be positioned 10m to 50m distant from the tailpipe at an angle of 45 degrees. The transmission loss simulation will assume that the output pipe extends some distance and that sound is not reflected. However, in the tailpipe noise simulation, a reflected surface will be generated at the tailpipes end.
Property
Value
Unit
Name
Ferrite Stainless Steel
-
-
RESULTS AND DISCUSSION
-
Normal Modes Extraction for Solid Muffler
Upon meshing and adding boundary conditions, the complete deformation results are produced, and the frequency in Hz of the muffler at different mode shapes may be derived. These frequencies at various mode shapes are listed below.
Fig. 19. Frequency at Mode 1 (677.829 Hz).
Fig. 20. Frequency at Mode 2 (1066.39 Hz).
Fig. 21. Frequency at Mode 3 (1388.47 Hz).
Fig. 22. Frequency at Mode 4 (1448.97 Hz).
TABLE VI. MODAL EXTRACTION OF SOLID MUFFLER
Mode orders
1
2
3
4
Frequency in Hz
677.829
1066.39
1388.47
1448.97
-
Normal Modes Extraction for Welded Muffler
The overall displacement results are generated for the welded muffler after meshing and applying boundary conditions, and the frequency in Hz of the muffler at different mode shapes re determined. These frequencies are shown below for various mode forms.
Fig. 23. Frequency at Mode 1 (706.577 Hz).
Fig. 24. Frequency at Mode 2 (1088.8 Hz).
Fig. 25. Frequency at Mode 3 (1464.84 Hz).
Fig. 26. Frequency at Mode 4 (1565.11 Hz).
TABLE VII. MODAL EXTRACTION OF WELDED MUFFLER
Mode orders
1
2
3
4
Frequency in Hz
706.577
1088.8
1464.84
1565.11
-
Transmission Loss of the Muffler
Fig. 27. Transmission Loss for Solid Muffler
The above graph shows the transmission loss (TL) of a solid muffler with outlets and inlets within the muffler for frequencies ranging from 10 to 2000 Hz, as calculated using FEM acoustic modelling in MSC Actran software. The maximum value of TL = 56 dB was observed at the frequency range of 900 Hz and the minimum value of TL = 15 dB at 1200 Hz. The graph below depicts the transmission loss (TL) of a welded muffler with outlets and inlets within the muffler for frequencies ranging from 10 to 2000 Hz, as estimated in MSC Actran software using FEM acoustic modelling. The greatest value of TL = 38 dB was recorded at 900 Hz, while the minimum value of TL = 15 dB was measured at 240 Hz.
Fig. 28. Transmission Loss for welded Muffler
According to the above TL measurements including both types of mufflers, the solid muffler with no welded sections has superior sound attenuating characteristics than the welded muffler. Especially compared to a solid muffler, the stiffness of the connection in a welded muffler increases with the increase to the welded portion on the baffle plates and tubes. This clearly demonstrates that raising overall elastic modulus of the joints increases the stiffness of the joint, decreasing the TL or sound attenuating capabilities. Therefore, it is recommended that welding operation will not be suitable for joining the parts of the muffler.
-
Tail-pipe Noise of the Muffler
For a unit source input, the transmission loss is the ratio of sound pressure at entry to exit. To obtain the true amount of sound at the mufflers tip, we must insert a source at the entrance. The inlet modal duct is provided an input in the following scenario, and noise is measured at the output end [30].
Below that the two graph demonstrates no discernible variation in tailpipe noise measured from 30m at an angle of 45 degrees with respect to the source. The tailpipe noise will normally fluctuate depending upon the distance at which it has been assessed.
Fig. 29. Tailpipe noise for solid muffler.
Fig. 30. Tailpipe noise for welded muffler.
-
Evaluation of the Results
Once extensively evaluating the simulation results of a solid muffler and a welded muffler, it was discovered that the natural frequencies of the muffler increase after the welding processes are performed.
TABLE VII. COMPARISION OF RESULTS
Mode Orders
Solid Muffler Frequency in Hz
Welded Muffler Frequency in Hz
1
677.829
706.577
2
1066.39
1088.8
3
1388.47
1464.84
4
1448.97
1565.11
As nothing more than a consequence of the improvement in material characteristics, especially the elastic modulus and the materials density for welded sections on the muffler whilst also attempting to maintain the same characteristics for the parent material, it was discovered that there had been a
significant rise in the stiffness of the joint of the welded section, something that resulted in an improvement its own natural frequency or modal analysis, where it experience in providing the sound transmission loss or sound attenuating potentials.
-
-
CONCLUSION
The above research looked at the acoustic properties of a simple muffler. There were essentially two mufflers studied: a solid muffler with no welded areas and a muffler with welding between both the baffle plates and tubing, as well as longer input and outlet pipes. The acoustic module of MSC Actran, MSC Nastran, and Patran software is used for finite element approach (FEM) analysis.
Solid works, a computer aided application, was employed to create the muffler. Mode shapes extraction was carried out on both types of mufflers in the frequency spectrum of 10Hz to 2000Hz throughout attempt to obtain multiple modes and assess their dynamic characteristics. Research results revealed that the normal modes frequencies for welded sections on the mufflers are slightly higher than those for solid mufflers.
The transmission loss (TL) of the muffler obtained by the FEM simulation model is investigated using a unit value of excitation of 1Pa as well as a frequency response of 10Hz to 2000Hz, and also the muffler is evaluated both with and without the welded section. Overall transmission loss of the solid muffler is determined to be higher compared to that of the welded muffler.
Tailpipe noise simulation is also accomplished including both muffler designs by placing a microphone at a distance of 30m at an angle of 45 degrees from the noise waves. The level of noise may fluctuate as that of the distances from the exhaust increases. Tailpipe noise simulation is also performed for both muffler types by constructing a microphone at a distance of 30m at a 45-degree angle from the sound source. The noise level may change as the distance from the exhaust increases.
Upon comparing every one of the outcomes, it was discovered that enhancing the stiffness or elastic modulus of the muffler using welded connections generates an elevation in the normal modes frequencies, diminishing its sound attenuating performance, but even though the tailpipe noise was pretty much identical to the both types of mufflers.
ACKNOWLEDGMENT
I want to use this occasion to offer my heartfelt thanks to my guide. I feel thankful for their profound participation in my work and helpful advice. They have always been an inspiration source for me. Because to their unwavering requirement for excellence and their focus on completing task, I was able to complete such a task. I am really grateful to my entire family for their drive and support, as well as everyone who has in some way assisted me in accomplishingthis goal.
REFERENCES
[1] D. S. Auto. What is car exhaust system and how it works? (2019), [Online]. Available: https://dsauto.com.my/en/2019/03/13/car-exhaust- system-introduction/. J. Clerk Maxwell, A Treatise on Electricity and Magnetism, 3rd ed., vol. 2. Oxford: Clarendon, 1892, pp.68-73. [2] e. a. Kim S., Investigation of flow and acoustic performances of suction mufflers in hermetic reciprocat, International Journal of Refrigeration, pp. 7484. [3] M. L. Munjal, Acoustics of Ducts and Muffler. Wiley, 2014. [4] M. Kermani, Muffler design by noise transmission loss maximization, Ph.D. dissertation, Eastern Mediterranean University, 2015. [5] Z. T. A. F YSeybert, A review of current techniques for measuring muffler transmission loss, . Society of Automotive Engineers. [6] P. Gumpel and C. Hoffmann, Corrosion resistance of stainless steels to wet condensates in automotive exhaust systems, Proceedings of the 6th European Stainless Steel Conference, 2008. [7] R. H. D. Green and M. Swain, Transformation toughening of ceramics, Boca Raton, 1989. [8] N. Arlt, Korrosions-und hitzebest¨andige stahle in abgassystemen,CTI Exhaust Materials Forum, Frankfurt, Germany,2007
[9] G. A. Ikpe Aniekan E Orhorhoro Ejiroghene Kelly, Engineering material selection for automotive exhaust systems using ces software. [10] N. N. N. K. Yasuda T. Wu C., Studies on an automobile mufflr with the acoustic characteristics of low-pass filter and helmholtz resonator,Applied Acoustics, vol. 74, pp. 4957, 2015
[11] B. A. P. YWankhade A. W., Optimization and experimental validation of elliptical reactive muffler with central inlet central outlet, International Journal of Engineering Research Technology, vol. 4, 2015. [12] D. Potente, General design principles for an automotive muffler, Applied Acoustics, vol. 74, pp. 911, 2005. [13] H. N. Selamet A. Lee I.J., Acoustic attenuation of hybrid silencers, Journal of Sound and Vibration, vol. 74, no. 262, pp. 509527, 2003. [14] A. D. S. u. N. S. S. d. Rahul D. Nazirkar S.R.meshram, Design optimization of exhaust muffler design validation, Ph.D. dissertation, Lonavala-410401, India. [15] P. S. A. S. Mr. Jigar H. Chaudhri Prof. Bharat S. Patel, Muffler design for automotive exhaust noise attenuation – a review [16] M. H. R. Brian J Schwarz, Experimental modal analysis, Vibrant Technology, Inc. [17] Conrad, Factors influencing acoustic performance of sound absorptive materials, Australian Journal of Basic and Applied Sciences, vol. 74, pp. 461467, 1983. [18] T. W. L. Roy, Muffler characterization with implementation of the finite element method and experimental techniques, Ph.D. dissertation, Michigan Technological University, 2011. [19] P. M. Mehdizadeh O. Z., A three-dimensional finite element approach for predicting the transmission loss in mufflers and silencers with no mean flow, Applied Acoustics, vol. 66, pp. 902918, 2005. [20] A. Haluk Erol, Acoustic attenuation in fully-filled perforated dissipative mufflers with extended inlet/outlet, International Congress on Sound and Vibration, Vienna, Austria, vol. 66, pp. 26, 2006 [21] L. X. Zheng S Kang ZX, Acoustic matching simulation of muffler with hybrid approach, SAE International, vol. 66, no. 01, pp. 1516, 2011. [22] T. R. Farhat C Wiedemann-Goiran P, A discontinuous galerkian method with plane waves and lagrange multipliers for the solution of short wave exterior helmholtz problems on unstructured meshes, Wave Motion, vol. 39, no. 01, pp. 307317, 2004. [23] J. P. Arenas and M. J. Crocker, Recent trends in porous sound- absorbing materials, Journal of Sound and Vibration,, vol. 329, no. 01, pp. 1217, 2010. [24] T. S. H. Tsutomu Oishi Yoshiya Nishizuka, Light weight ceramic acoustic absorber and method of manufacturing the same, Journal of Sound and Vibration,, 2016. [25] F. K. Bilawchuk S, Comparison and implementation of the various numerical methods used for calculating transmission loss in silencer systems, Applied Acoustics, vol. 64, pp. 903916, 2003. [26] F. A. D. Siano and F. Bozza, A corelation study of computational techniques of a three pass perforated tube muffler including bem and 1d methods, Ph.D. dissertation, Naples, Italy, Naples, Italy. [27] A Elsayed, Investigation of baffle configuration effect on the performance of exhaust mufflers, Case Studies in Thermal Engineering., vol. 10, pp. 9197 [28] J. W Lee, Optimal topology of reactive muffler achieving target transmission loss values: Design and experiment, Applied Acoustics, vol. 88, pp. 104113, 2015. [29] T Yasuda, Acoustic attenuation performance of perforated dissipative mufflers with empty inlet/outlet extensions, Journal of Sound and Vibration, vol. 302, pp. 10001017 [30] T Yasuda, Predictions and experimental studies of the tail pipe noise of an automotive muffler using a one dimensional cfd model, Case Studies in Thermal Engineering., vol. 71, pp. 701707