
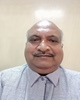
- Open Access
- Authors : Vijayakumar Halakatti
- Paper ID : IJERTV10IS120111
- Volume & Issue : Volume 10, Issue 12 (December 2021)
- Published (First Online): 22-12-2021
- ISSN (Online) : 2278-0181
- Publisher Name : IJERT
- License:
This work is licensed under a Creative Commons Attribution 4.0 International License
Self-Compacting Concrete – A Critical Study of Nan Su Method At Wide Range of Packing Factors
Vijayakumar Halakatti Associate Professor and Head, Department of Civil Engineering
JSSATENoida-201301 Uttar Pradesh,India
Abstract The Nan Su method for mix design of self- compacting concrete(SCC) suggests to use the optimal packing factor ranging from 1.12 to 1.18.The packing factor beyond this range is difficult to predict. However, a study on performance of SCC can be extended by using packing factor beyond this range. So, this paper addresses in identifying the merits and demerits of this method at wide range of packing factors from
-
to 1.24 before it is to be introduced to the construction industry, since the experimental evidence is much stronger than that which was previously obtained by analyzing a large amount of test results from the literature. Thus six mixes were designed for compressive strength of 50MPa first with fly ash as filler material and Glenium B233 as super plasticizer. The mixes are compared with EFNARC guidelines for mix proportions and workability requirement of fresh mix and strength requirement of harden mixes. Certain modifications were made in the mix proportion of M-5 designed for higher packing factor of 1.24 by increasing the water content and reducing the same volume of coarse aggregates to produce a workable mix. This is identified as M-5m. To improve the 28 days strength of hardened mixes, it is proposed to replace 40% of fly ash of all the mixes by GGBS. Then the mixes designed for lower packing factors up to 1.12 yields the 28 days design strength of 50MPa.The mixes with or without replacement of fly ash by GGBS designed for lower P F can be adopted to yield the strength at later ages of 120 days more than the design strength.
Keywords Self compacting concrete; Nan-Su method; packing factor range: aggregate-cement ratio; compressive strength; correction factor
-
INTRODUCTION
The self-compacting concrete is essential in members with congested and heavy reinforcement. Many mix design methods were introduced since from past three decades. However none of these methods procedures are accepted as a standard one as it is very sensitive to variations in moisture content, sand fineness and aggregate gradation. Of all the methods of design, Nan-Su method draws the attention of every concrete maker as it is simple to adopt.
Further, in Nan Su method, for particular design strength, the cement content to be used is same for any packing factor. There are two parameters such as packing factor and s/a ratio that decide the composition of the mix and hence the properties of fresh and harden mix. Of these two parameters, packing factor is an important factor as far as these properties are concerned. The packing factor of aggregates as defined is the ratio mass of tightly packed state in SCC to loosely packed state. The s/a ratio is the ratio of
mass of fine aggregate to total mass of aggregates. As packing factor is increased, the content of fine and coarse aggregates will be increased and decrease the content of binder in SCC. Consequently its flow-ability, self-compacting ability and compressive strength will be reduced. On the other hand, a low P.F will increase the content of binders and thus the cost. The drying shrinkage of concrete will increase. However, the range of P.F as predicted by Nan Su is 1.12 to
-
These ranges of P.F values are insufficient to clearly distinguish advantages and disadvantages of the mixes. The packing factor more than 1.25 is practically difficult to achieve. However, the study of Nan Su method can be extended to design the mixes with higher P.F values even up to 1.28 and the resulting properties of mixes at fresh and harden state are compared with values given by EFNARC and other codes
-
Advantages and need of SCC
Self-compacting concrete also referred as self- consolidating concrete and high performance concrete is one of the most important developments in the construction industry due to the excellent deformability and segregation resistance. It can be compacted under its own weight without any vibration effort, assuring complete filling of formwork with very heavy reinforcement in it. It is not affected by skill of workers, shape and reinforcing bar reinforcement of a structure. It improves quality, durability and reduces honeycombing due to its high fluidity. It is identified [1] that it can be produced economically. The extra expense of super plasticizer in self-compacting concrete can be compensated with the saving made to vibrate the mix. Hence it is creating silent revolution in the construction industry
-
Requirement of SCC
Self-compacting concrete contains more powder and sand than the coarse aggregates as compared to normal concrete. While designing it, the factors are taken into consideration are the limited aggregate content and increasing the paste volume, low water powder ratio, use of the super plasticizer and carefully controlling the maximum size of coarse aggregates not more than 20mm and its volume in total coarse aggregate content.
Self-compacting concrete has to satisfy the self- compaction when it is fresh whereas strength and durability at harden state. Self-compaction and mobility is achieved by using super plasticizer and using limited aggregate content whereas strength and durability can be achieved with low w/c ratio. Through research, it is found that the energy for
flowing is consumed by the increased internal stress resulting in the blockage of aggregate particles. Limiting the coarse aggregates content whose energy consumption is particularly high is brought to a level lower than the normal and is effective in avoiding this kind of blockage. EFNARC[2] limits the maximum size of aggregate to 20mm but in this study its contents is restricted to 20% of total coarse aggregate content by weight whereas for remaining 80%, 12.5mm or 10mm size can be used.
-
-
-
LITERATURE REVIEW
-
Different mix design methods for SCC
Self-compacting concrete was first developed in Japan after 1980 with an aim to produce a highly workable mix to overcome the problem of getting the labors for concreting. Hajime Okamura and Masahiro Ouchi [3] of Japan revised earlier method given by Hajime Okamura and Ozawa [4] to make it a rational mix design method. This method is considered as an empirical method. The guidelines given in EFNARC are based on this method. It is observed [5] that these method procedures are too complicated for the practical implementation, yields the high content of paste therefore higher strength than actually required. This method is suitable for the gravelly rounded aggregates. When crushed aggregates are used, the proportions are to be adjusted by incorporating more fines.
Method introduced by Nan Su et al [5] based on packing theory starts with the packing of all aggregates and later with filling of aggregate voids with paste. This method is easier to carryout and results in less paste. This saves the expensive constituents namely cement and filler material considerably compared to the other methods and making the concrete more economical. But the drawback of this method
[6] is that it is more difficult to achieve the satisfactory workability requirement of the mix due to the less powder content.Many other researchers [7, 8] referred the absolute volume method. This method is derived from the American Concrete Institute Method (ACI) used for design of normal concrete. This method is used as it yields more fines compared to other metods such as Indian Standard Method and Department of Environment (D.O.E) Method.
SCC mix can also be designed [9] by optimizing the paste composition by conducting Punkte test to find out the packing density. The packing density is used to optimize the cement and fly ash combination and the mini slump test is conducted to study the rheology of paste. It is identified that as water-powder ratio increases, there will be increase in super plasticizer dosage needed and slump flow values of the fresh mix whereas there will be the decrease in T50 values.
A method [10] is proposed based on the concept of maximizing the total aggregate volume, reducing powder content as much as possible, using lowest w/p ratio and selecting optimum sand/aggregate ratio. This is required to lead the mix with minimum volume of voids (Sand/Aggregate=0.50 to 0.55) so as to improve the impermeability, durability, to reduce the drying shrinkage and creep. This concept improved paste rheology and gives the best results in the filling height of U-box test of the fresh mix. Other methods are Sedran method (LCPC, Paris
method)[11] and method suggested by Gomes and Ravindra Gettu[11].
Narendra. H et al [12] optimized the mix using Taguchi concept of array by using Nan Su method to prepare mix design input table.
In absence of systematic standards or specifications, a simple tool for mix design [13] is presented in which the relative proportions of key components are considered by volume rather than by mass. This tool is evaluated having 28% of coarse aggregate content, 35% replacement of cement with class F fly ash, 0.36 water/cementitious ratio by weight and 388 litre/m3 of paste volume. Crushed granite stones of size 20mm and 10mm are used with a blending 60:40 by percentage weight of total coarse aggregate.
-
Study made on composition of constituent materials, properties of fresh and the harden mix
The influence of parameter such as packing factor (PF) on the composition of constituent materials, workability of fresh mix and strength of harden mix are discussed in the method given by Nan-Su [5]. These are that as packing factor increases within its range of 1.12 to 1.18, the method yields insufficient powder and paste volume thereby increasing the fine and coarse aggregate content. This makes the fresh mix of insufficient workability decreasing the passing ability through reinforcement and segregation resistance. As packing factor increases from 1.12 to 1.18, the paste volume decreases from 0.368 m3 to 0.3355 m3, the sand content increases from 48.3% to 52% by volume, the slump flow decreases from 710X720mm to 600X600mm, filling height in U-box column decreases from 340mm to 150mm respectively. Normally, the requirement of filling height of fresh mix is above 300mm according to specification given in Japanese society of civil engineering (JSCE). When values of PF are 1.12, 1.14 and 1.16, the slump flow and U-box results satisfies the rank R1 requirement whereas for 1.18 meets R2 requirement of JSCE.As w/b ratio increases from 0.31 to 0.43, the 28 days compressive strength which reads 53.8 MPa for 1.12 packing factor reduces to 38.2 MPa for 1.18. The compressive strength is closely related to packing factor and it decreases with increase in PF.
It is investigated that the cement content as calculated by Nan Su method is insufficient to achieve the design cube strength. So increase in the cement content is recommended [14] by using suitable correction factors depending upon the grade of mix.
It is reported [15] that viscosity of the SCC mixture decreases with an increase in water powder ratio. The decrease in viscosity is indicated by the drop in T50 and V- funnel flow time. A data is presented that suggest a linear relationship between V-funnel flow time and T50 slump flow. Thus these two tests can be used interchangeably in the field.
It is investigated by Jagdeesh Vengala et al that as Aggregate-Cement ratio [16] of a mix reduces from 3.85 to 3.47, slump flow values and L-box co-efficient increases from 0.50 to 0.80.
-
Choice of the super plasticizer
Poly carboxylate ether (PCE) based super plasticizers[17] are effective at lower dosages compared to sulfonated condensates of melamine (SMF) or naphthalene
formaldehyde (SNF) to achieve excellent flow at low water content. So in this study, it is proposed to use Glenium B233, a Poly Carboxylate Ether based super plasticizers of recent origin. It avoids the use of viscosity modifying agent (VMA) that was earlier used to enhance the stability of fresh mix. New generation super plasticizers decrease the viscosity and increase the fluidity of fresh mix. However the level of fluidity is mainly governed by its dosage.
-
Choice of the filler material
Self-Compacting Concrete requires a relatively large quantity of powder material of the order of 450-600 kg/m3. Powder is made of cement and filler material. High flow requirement of SCC allows the use of mineral admixtures in its manufacture. The mineral admixtures such as fly ash, ground granulated blast furnace slag (GGBS), silica fume (micro silica), metakaolin and rice husk ash can be used as filler material. Now days, efforts were made to use non pozzolanic materials such as granite powder and crushed rock fines as filler material in place of fly ash.
The local construction industry prefer to use GGBS as filler material which replaces the cement even up to 60% to attain the strength same as with fly ash which replaces the cement only up to 30% only. Hence GGBS is economically compared to the use of fly ash. It also improves the rheological properties of the mix. The other fillers such as silica fume and meta-kaolin help in attaining a high early strength which is very useful in pre-cast applications. These will provide high durability when used along with fly-ash. Silica fume improve the mechanical properties, increases the strength but reduces the workability up to the maximum extent.
The incorporation of one or more mineral admixture/powder material having different morphology and grain size distribution improves the particle packing density and reduces the inter particle friction and viscosity. This improves deformability, self compaction and stability of SCC. However, it is proposed to use fly-ash as filler material as is available in our country as industrial waste in abundant quantity. Study of properties of the mix with other filler material can be taken up as a separate study. Most of the fly ashes available in our country are low calcium fly ash with class F.
Use of mineral admixture such as fly ash could increase the slump of concrete mix. It also results in the reduction of the cost of concrete. Fly ash is used as the filler material as it will improve the rheological properties and reduces cracks due to the reduced heat of hydration. The fly ash is responsible to yield more strength only at later ages.
It is reported (18) that as fly-ash increases in relation to cement, the tensile strength and compressive strength decreases. Increase in fly ash content in place of cement from 48 kg/m3 to 144 kg/m3 reduced the water requirement of mix thereby decreasing 28 days strength from 52 MPa to 39 MPa.
The use of high volume of fly ash(19) in SCC can be encouraged as it has advantages of improved rheological properties and reduced cracking in concrete due to the reduced heat of hydration of concrete, enhanced workability, long term strength and durability.
It is identified (20) that the use of low-lime
(calcium) fly-ash in cement and concrete is beneficial in view of the ecological and cost saving benefits in the one hand and improvements in a variety of properties of concrete on the other. The low lime class F fly-ash available in the country is compositionally much suited for use in blended cement and concrete. The use of fly-ash in concrete decreases its permeability thereby enhancing the durability of concrete.
The cement replacement (21) levels of 25% with fly ash (class-F) in concrete mixes can be possible if strength at later stages such as 90 days could be considered for design and is the optimum level for obtaining compressive strength of 80 MPa. Besides this, it will render the concrete more durable and corrosion resistant. However it is found that as the fly ash increases in relation to the cement, the compressive and tensile strength decreases.
It is found (22) that the use of finely ground fly-ash resulted in an increase of 28 days compressive strength of concrete by about 28% which is highly significant. When VMA is added, this strength increase was not maintained fully. It is also reported that the limitations suggested by various researchers on use of powder can be relaxed to obtain SCC.
It is reported (23) that the fly ash can be used in large quantities in SCC and cement content can be reduced to as low as 200 kg/m3 without losing the requisite characteristics of SCC. The SCC can be obtained for widely differing fly-ash contents or cement content as long as the paste volume constituted by the powder and water is kept unchanged. These investigation shows that fly-ash can be used in large quantities in SCC and the cement content can be reduced to as low as 200 kg/m3 without losing the requisite characteristics of SCC. However, the resulting concrete will be low grade (strength) concrete. As fly ash content increases in relation to cement, the compressive and tensile strength at all ages decrease. But greater the fly ash content, the rate of development of strength increases, thus indicating the pozzolanic effect of fly ash. High strength SCC can be obtained through the incorporation of metakaolin.
Eight SCC trials [7] were carried out by incorporating 20% and 30% fly ash for each with total powder content being 400,450,500 and 550 kg/m3 in SCC400, SCC450, SCC500 and SCC 550 mixes respectively using water content of 180 liters/m3 in all the mixes. It is found that the slump flow of 640mm for SCC400 mix with 20% fly ash goes on increases to the maximum value of 780mm for SCC550 with 30% fly ash content. The 28 days cube strength for 20% replacement increases from 33MPa for SCC400 to 54MPa for SCC 550 mix. Similarly for 30% replacement, the same mixes increased from 32.7 to 49.5MPa.This shows that as fly ash increases, the slump improves but cube strength decreases marginally. The same study was carried by them using granite powder.
Fly ash [24] can even be used as sand replacement material in cement concretes. This type of fly ash concrete has a lower density and manufacturing cost, a reduced coarse aggregate content, a lower degree of permeability and increased durability than those of cement concrete. It is feasible to substitute up to 60% sand by fly ash without affecting the workability and strength requirement of
concrete. However, this concept can also be extended to the manufacture of SCC.
The influence of processed fly ash [25] with fineness residue retention on 325 mesh sieve less than 12% was studied on the properties of self-compacting concrete. The total binder content is replaced by fly ash 30%, 40% and 50%. The slump flow, L box and U box ratio values satisfied the EFNARC values except V funnel flow test. The mechanical properties showed increase in strength with increase in curing ages and marginal reduction in strength by increasing processed fly ash levels.
-
-
RESEARCH SIGNIFICANCE
SCC is sensitive [1] especially to the variations in moisture content due to the use of lower w/c ratio and viscosity. In the absence of precise and Codal procedure for the mix design, different methods[3,4,5,7,8,9,10,11,12,13] were introduced by many investigators. Of all the existing methods, the method suggested by Nan-Su [5] is popular among concrete makers as it is simple to adopt. However, there is a need to review, reinvestigate and compare the merits and demerits of this method at higher packing factor as discussed by Nan-Su earlier and the influence of different parameters as studied by many other investigators [14.15 and 16] on properties of fresh and harden mix. Hence, the properties of the mix such as the composition of constituent materials, workability of fresh mix and strength of harden mix can be studied either by varying packing factor beyond the range of 1.12 to 1.18 as suggested in the method [5] or by varying the w/p ratio of the mixes systematically beyond the range of 0.30 to 0.50 as suggested [8].
Mixes
M-1
M-2
M-3
M-4
M-5
M-
5m
Parameters
P.F.
factor
1.08
1.12
1.16
1.20
1.24
1.24
S/a ratio
0.54
Cement
350
Fly ash
203.70
177.61
149.05
121.72
94.40
94.40
Powder
553.70
527.61
499.05
471.22
444.44
444.44
Fine aggregate
849.14
880.59
912.04
943.49
974.94
974.94
20mm(20% ofCA)
139.70
144.87
150.05
155.22
160.40
12.5mm(80% of CA)
558.80
579.50
600.20
620.89
641.59
641.59
Water after correction for SP
178.51
169.64
159.93
150.64
141.35
150
SP dosage(1.2% of cement)
4.2
SP dosage(% of powder)
0.759
0.796
0.842
0.891
0.945
0.945
w/p ratio
0.322
0.322
0.321
0.320
0.318
0.318
Agg/Cement ratio
4.422
4.586
4.750
4.913
5.080
Mixes
M-1
M-2
M-3
M-4
M-5
M-
5m
Parameters
P.F.
factor
1.08
1.12
1.16
1.20
1.24
1.24
S/a ratio
0.54
Cement
350
Fly ash
203.70
177.61
149.05
121.72
94.40
94.40
Powder
553.70
527.61
499.05
471.22
444.44
444.44
Fine aggregate
849.14
880.59
912.04
943.49
974.94
974.94
20mm(20% ofCA)
139.70
144.87
150.05
155.22
160.40
12.5mm(80% of CA)
558.80
579.50
600.20
620.89
641.59
641.59
Water after correction for SP
178.51
169.64
159.93
150.64
141.35
150
SP dosage(1.2% of cement)
4.2
SP dosage(% of powder)
0.759
0.796
0.842
0.891
0.945
0.945
w/p ratio
0.322
0.322
0.321
0.320
0.318
0.318
Agg/Cement ratio
4.422
4.586
4.750
4.913
5.080
Selecting lower PF values of 1.20 and 1.40, efforts were made to study its influence on the various properties of the mix. So this study helps in re-affirming the investigations made earlier on the influence of PF on the different properties of the mix before the method is to be introduced to local construction industry with higher values of P.F up to 1.40.Hence it is very interesting the observe the influence of higher P.F values on the performance of mix actually conducting the experiments because the experimental evidence is much stronger than that which was previously obtained by analyzing a large amount of test results from the literature.
specific gravity of aggregates is 2.68 and the bulk density is 1406kg/m3 for loosely packed state.
Water: Water suitable for drinking confirming to IS 3025-1983 (water for construction purpose) of IS 456-2000 is used .Its pH value is 7.170.
Super Plasticizer: Glenium B 233, poly corboxylated ether (PCE) based super plasticizer confirming to IS 9103- 1999 is used. Its pH value is 6.82 and dry material content is 34.51%.
Super plasticizer Dosage: This is found by using marsh cone in the laboratory. It is a conical brass vessel that has a smooth aperture of diameter 5mm at its bottom. The test is performed as per the procedure given in the text book [26]. A graph of SP as % by wt of cement on x-axis V/s Time in sec for flow of paste through cone on Y-axis is drawn. From the graph, the optimum dosage of super plasticizer is found to be 1.2% by weight of cement.
-
RESULTS AND DISCUSSIONS
-
Mix design and Mix proportions
Four mixes are designed using the combination of each of two values of packing factor 1.2 and 1.4 beyond the range of
1.12 to 1.18 as given by Nan Su with the two values of S/a ratio in its range from 0.50 to 0.57 for strength of 50MPa.This combination is given in Table1.
As packing factor [5] increases, the compressive strength of self compacting concrete decreases. The disadvantages of higher PF are that the harden mix yields low strength, yields less powder material that will make the fresh mix to reduce its workability. However, the mixes designed for lower values of PF yields more powder.
TABLE 1.COMBINATION OF PARAMETERS USED IN THE MIX DESIGN
Mix
M-1
M-2
M-3
M-4
M-5
P.F
1.08
1.12
1.16
1.20
1.24
S/a
0.54
TABLE 2.MIX PROPORTIONS BY WEIGHT IN
-
MATERIAL PROPERTIES
Cement: Ordinary Portland Cement (OPC) of 53 grade of specific gravity 3.15 and that confirms in accordance with IS12269:1987 is used in this study.
Fly Ash: Class F-fly ash of specific gravity 2.15 confirming to IS 38122003.
GGBS: Specific gravity 2.90 confirming to 12089-1987.
Fine Aggregates: Locally available river sand of specific gravity 2.58 and fineness modulus 2.80 is used. It confirms to zone II of I.S.383-1970 .The bulk density of aggregates is 1456 kg/m3 for loosely packed state.
Coarse Aggregates: Crushed aggregates of maximum sizes 20mm and 12.5mm are mixed in the proportions of 20:80 by weight in total coarse aggregates respectively. The fineness modulus of the combined aggregates is 7.15.The
The quantity of cement required depends on the grade of concrete and is 350 for all the mixes and super plasticizer for all the mixes is same for M50 strength. It is
observed from Table 2 that as the values of packing factor of the mixes increases, the quantity of the fly ash and water required decreases whereas the quantities of aggregates increase. This may make the fresh mix less flow able .The EFNARC recommends to use the total powder material ranging from 400 to 600 kg/m3.All the mixes designed for packing factor range up to 1.28 satisfies this requirement.
Self-compacting concrete mix requires minimum of 160 litres /m3 and maximum of 200 liters /m3 of water. This much of water is required to wet not only the powder material but also aggregates. Thus the proportions for mixes M-5 and M-6 can be slightly modified by increasing the water quantity to 150 liters/m3 from their earlier estimated quantities. EFNARC also suggest adjusting the fresh mix proportions by varying super plasticizer dosage and filler material if required so as to improve the workability of fresh mix. The increase in the volume of fly ash and water content if made in any mix, then are compensated by reducing the same volume of coarse aggregates only to aim at improving the flow properties. However Mehta and Neville [27] suggest for replacing 4% to 5% of coarse aggregates by sand to avoid segregation. Here the reduction of the same volume of coarse aggregate is performed equal to the increased volume of the water.
Mixes
M-1
M-2
M-3
M-4
M-5
M-
5m
Parameters
P.F
1.08
1.12
1.16
1.20
1.24
1.24
S/a ratio
0.54
V Cement
0.111
V Fly ash
0.164
0.143
0.120
0.098
0.076
0.076
V Powder
0.275
0.254
0.231
0.209
0.187
0.187
V Fine aggregate
0.329
0.341
0.354
0.366
0.378
0.378
V C.A
0.264
0.273
0.283
0.293
0.303
0.294
V Total agg
0.593
0.614
0.637
0.659
0.681
0.672
V Water
0.178
0.17
0.160
0.151
0.141
0.150
V Paste
0.453
0.424
0.391
0.360
0.328
0.337
V Mortar
0.782
0.765
0.745
0.726
0.706
0.715
V Water / V Powder
0.647
0.669
0.693
0.722
0.754
0.802
V Water / V Paste
0.293
0.400
0.409
0.419
0.430
0.445
V Total agg / V Cement
5.342
5.52
5.739
5.937
6.135
6.055
Mixes
M-1
M-2
M-3
M-4
M-5
M-
5m
Parameters
P.F
1.08
1.12
1.16
1.20
1.24
1.24
S/a ratio
0.54
V Cement
0.111
V Fly ash
0.164
0.143
0.120
0.098
0.076
0.076
V Powder
0.275
0.254
0.231
0.209
0.187
0.187
V Fine aggregate
0.329
0.341
0.354
0.366
0.378
0.378
V C.A
0.264
0.273
0.283
0.293
0.303
0.294
V Total agg
0.593
0.614
0.637
0.659
0.681
0.672
V Water
0.178
0.17
0.160
0.151
0.141
0.150
V Paste
0.453
0.424
0.391
0.360
0.328
0.337
V Mortar
0.782
0.765
0.745
0.726
0.706
0.715
V Water / V Powder
0.647
0.669
0.693
0.722
0.754
0.802
V Water / V Paste
0.293
0.400
0.409
0.419
0.430
0.445
V Total agg / V Cement
5.342
5.532
5.739
5.937
6.135
6.055
TABLE 3. MIX PROPORTIONS BY VOLUME
Self-compacting concrete can be made with cement content as low as 200 kg/m3.The IS 456-2000 code restricts the use of cement not more than 450 kg/m3 due to the problems such as drying shrinkage and creep of the mix. All mixes designed by Nan Su method will satisfy this aspect.
The modified mix proportions for M-5m and M-6m mixes by weight and volume are given in Table2 and 3 respectively. It is observed from Table3 that the mixes M-1 to M-5 designed for packing factor up to 1.24 are unable to satisfy the EFNARC requirement such as the water-powder ratio by volume to be between 0.80 to1.10.However M-6 mix designed for P.F =1.28,M-5m and M-6m satisfy this condition.
The Coarse Aggregate content for the mixes M-3 to M-6 designed for P.F greater than 1.16 satisfy the range from 28% to 35% by volume of mix. The mixes designed for lower
P.F values do not satisfy this condition.
The volume of fine aggregates in a mix should be more than 38% of mortar volume. Only M-6 mix satisfies this condition laid down by EFNARC.
Hence, to mixes designed for lower P.F will be unable to satisfy the mix proportion ratios put by EFNARC.
-
-
Properties of fresh self-compacting concrete mixes
Different tests conducted on all eight fresh mixes to examine workability requirements as per EFNARC and are tabulated in Table 4.
To prepare fresh mix, drum mixers are used to make plasticizer properly and intimately mixed in concrete to bring about proper dispersion with cement particles. Pan Type mixer is used for the volume of mix nearly 0.05 m3 and rotating drum mixer for volume of mix nearly 0.20m3. However, the mixing time for self-compacting concrete need to be longer than normal concrete due to more powder content in it. The dry materials are mixed for 1 minute. Later a solution containing water and super plasticizer is added and mixed for 10 minutes only.
It is also observed throughout the process of mixing that fresh mix is very sensitive to excessive water content beyond its saturation level. This tends to make the fresh mix bleeding with segregation. This is due to low w/c ratio used in the mix. Hence, depending upon the prevailing temperature and humidity of the day, the quantity of water beyond 95% of the estimated water was added in stages till the fresh mix of required workability is obtained.
Due to the addition of super plasticizer such as Glenium B233 in the fresh mix results in reduced bleeding, segregation in fresh mix. This will help to reduce creep and permeability of harden mix free from honey combing. Benefits due to improved cohesion of paste matrix will lead to less segregation and less difficulties in concrete placement.
Throughout the test that the slump flow and U-box tests are identified as good qualitative measurements of acceptability of mixes that helps to identify the mix to accept. Different tests on the fresh mix are conducted in the order of slump flow, U-box, L-box, J-ring, V-funnel and Orimet as suggested [15]. All the tests on fresh mix are completed within a short period soon after the water is added to mix in order to get a true measurement of the performances in various tests.
TABLE 4.PROPERTIES OF FRESH SELF-COMPACTING CONCRETE
Flow properties
Range
M- 1
M- 2
M-3
M-4
M-5
M-
5m
Slump flow
650
800mm
685
675
635
540
445
465
T50 cm
25 sec
3.4
3.0
2.6
2.2
–
–
J-ring
010mm
5.1
5.7
6.5
7.3
8.4
8.0
V-funnel
812 sec
8.2
7.3
6.3
5.2
4.2
3.9
V-funnel (5 min)
+3sec
10.3
9.2
7.9
6.6
5.4
5.0
L-box(H2/H1)
0.8 1.0
0.82
0.74
0.65
0.56
0.47
0.50
U-box(H1 H2)
030 mm
20
24
29
32
37
34
Orimet
0-5sec
4.1
3.8
3.1
2.8
2.4
2.1
From Table 4, it is identified that the mixes M-1 and M-2 containing more fly ash will yield satisfactory results for all the tests including slump flow, U-box and L-box readings compared to M-3m and M-4m mixes even though these mixes are modified.
EFNARC recommends the minimum slump flow of 650mm.Slump flow [11] ranging from 500mm to 700mm is considered as necessary for a concrete to be self- compacted. At more than 700mm the concrete might segregate and at less than 500mm, the concrete may have insufficient flow to pass through the congested reinforcement. The M-1 and M-2 mixes containing the powder content of around 500 kg/m3 than the other mixes will give satsfactory slump flow more than 650mm, L-box ratio above0.80 and difference of columns in U-box less than 30mm.But M-3m and M-4m mixes will not able to do so due to the less powder material. However all the four mixes will yield satisfactory results for T50 .V-funnel and the Orimet within the range suggested by the EFNARC. But there are no systematic variations in any of these values.
a) Slump flow test b) J-ring test c) U-box test
d) Orimet test e) V-funnel test f) L-box test Fig1. Tests on fresh SCC for various workability requirements as per EFNARC
From Table 2, it is known that for the M-1 and M-2 mixes, the aggregate/cement ratio by weight which is nearly
4.69 increases more than 5 for M-3m and M-4m mixes. Then it can be correlated from Table 4 that as Aggregate/Cement ratio of a mix increases, there will be decrease in average diameter of the slump flow less than 650mm, , L-box ratio less than 0.80 and filling height difference in U-box values less than 30mm,J-ring values increases from nearly 5.5mm to8.1mm, Orimet value from3.2sec to 3.8 sec. But there are no systematic variations in any of the T50, V-funnel values.
It is confirmed that mixes designed by Nan-Su method for higher values of packing factors such as 1.40 needs the modification in proportions of filler material and water to satisfy EFNARC recommendations. In such case, it is very difficult to correlate water/powder ratios with the properties of fresh mix.
-
Compressive strength of self-compacting concrete
The tests are conducted in the laboratory as per IS 516- 1959 and the results for 7 and 28 days compressive strength of cubes of size 150mm are given in Table 5.
Fig2: Various stages of Cube testing
TABLE 5.THE 7, 28 AND 120 DAYS COMPRESSIVE STRENGTH OF SCC WITH FLY ASH IN MPa
7 days
28days
120 days
Cube strength
Av strength
Cube strength
Av strength
Cube strength
Av strength
M- 1
27.16
26.20
43.54
44.45
59.26
58.71
25.75
44.35
58.65
26.23
45.78
59.44
26.42
46.02
57.52
25.88
42.56
58.68
M- 2
24.67
25.14
44.85
43.71
55.74
54.77
25.05
44.57
53.35
25.71
43.95
55.20
26.18
42.30
53.24
24.06
42.88
56.32
M- 3
23.50
22.89
37.37
38.41
46.68
48.35
23.22
39.04
50.14
22.74
39.55
49.05
22.31
38.64
48.44
22.68
37.45
47.44
M- 4
21.40
20.32
35.11
34.33
42.75
42.38
19.54
35.09
40.37
18.85
34.56
43.42
19.71
33.88
42.07
22.10
33.01
43.29
M- 5
16.35
15.65
28.46
28.50
36.22
34.50
15.64
27.85
35.78
15.21
29.71
34.31
16.15
27.60
32.64
14.90
28.88
33.55
M-
5m
16.06
16.25
30.45
30.21
37.45
36.22
16.40
30.95
35.45
15.86
28.58
35.85
17.12
29.04
36.32
15.81
32.03
36.03
It is observed from the Table 5 that all the four mixes are unable to achieve the designed 28 days characteristic strength of 50MPa.Eventhough the fresh mixes M-1 and M-
-
yields the better flow results, but unable to yield considerable increase in compressive strength. This is due to more fly ash content in the mixes as compared to M-3 m and
M-4 m mixes. The increase in strength due to fly ash is possible only at later ages. Nan Su observed that as packing factor increases, the compressive strength decreases. For M- 3m and M-4m mixes designed for the higher values of packing factors, there is no appreciable fall in compressive strength as stated by Nan Su. In such cases, it is difficult to correlate the compressive strength results with packing factor as stated by Nan-Su.
However, for mixes designed for packing factors greater than 1.18, it is necessary to realize the Nan-Su observations regarding the influence of packing factor on compressive strength.
Based upon observations made on workability performances of fresh mix (Table 4) and strength performance (Table 5) of harden mixes, it is proposed to prefer M-2 mix for further investigation. The cement content in M-2 mix is increased by using the correction factor of 1.26 as recommended [14] with aim to improve the compressive strength of the hardened concrete. The mix proportions are given in Table 6 by weight as well as volume. Let this mix is identified as M-2 mc mix.
Mixes
M-1
M-2
M-3
M-4
M-5
M-
5m
Parameters
P.F.
factor
1.08
1.12
1.16
1.20
1.24
1.24
S/a ratio
0.54
Cement
350
60% Fly ash
129.99
113.34
95.11
77.68
60.24
60.24
40% GGBS
86.69
75.56
63.41
51.78
40.16
40.16
Powder
566.65
538.90
508.52
479.46
450.40
450.40
Fine aggregate
849.14
880.59
912.04
943.49
974.94
974.94
20mm (20% ofCA)
139.70
144.87
150.05
155.22
160.40
111.70
12.5mm (80% of CA)
558.80
579.50
600.20
620.89
641.59
641.59
Water after correction for SP
182.91
176.23
163.15
153.29
143.41
150
SP dosage
(1.2% of cement)
4.2
SP dosage(% of powder)
0.759
0.796
0.842
0.891
0.945
0.945
w/p ratio
0.323
0.327
0.321
0.320
0.318
0.333
Agg/Cement ratio
4.42
4.59
4.75
4.91
5.08
4.94
Mixes
M-1
M-2
M-3
M-4
M-5
M-
5m
Parameters
P.F.
factor
1.08
1.12
1.16
1.20
1.24
1.24
S/a ratio
0.54
Cement
350
60% Fly ash
129.99
113.34
95.11
77.68
60.24
60.24
40% GGBS
86.69
75.56
63.41
51.78
40.16
40.16
Powder
566.65
538.90
508.52
479.46
450.40
450.40
Fine aggregate
849.14
880.59
912.04
943.49
974.94
974.94
20mm (20% ofCA)
139.70
144.87
150.05
155.22
160.40
111.70
12.5mm (80% of CA)
558.80
579.50
600.20
620.89
641.59
641.59
Water after correction for SP
182.91
176.23
163.15
153.29
143.41
150
SP dosage
(1.2% of cement)
4.2
SP dosage(% of powder)
0.759
0.796
0.842
0.891
0.945
0.945
w/p ratio
0.323
0.327
0.321
0.320
0.318
0.333
Agg/Cement ratio
4.42
4.59
4.75
4.91
5.08
4.94
TABLE 6: MIX PROPORTIONS FOR ALL THE MIXES WITH FLY ASH AND GGBS BY WEIGHT IN KGS
Due to the increase in the cement content [14], there is a decrease in the fly content from 147 kg/m3 to 82.05 kg/m3. However the total powder content is increased from 501.142 kg/m3 to 523.050 kg/m3.The 28 days compressive strength is increased from 34.67 kg/m3 to 62.11 kg/m3( % increase of 79.15MPa).
From Table 6 and 2, it is observed that the increase in cement content in M-2mc mix reduces the quantity of fly ash from 141.595 kg/m3 to 67.07 kg/m3, but increases the powder content from 498.737 kg/m3 to 517.07 kg/m3 and in the water content from 159.621 liters to 163.263 liters. It is also noted that the M-2mc mix tends to satisfy the EFNARC requirement regarding coarse aggregate content and fine aggregate content but unable to satisfy the requirement that the water -powder ratio by volume to be between 0.80 and
1.10. However, the Aggregate / Cement ratio by weight decreases from 4.692 to 3.724.
TABLE 7: PROPERTIES OF FRESH MIXES WITH FLY ASH AND GGBS
Properties of fresh mixes
Flow properties
Range
M-1
M-2
M-3
M-4
M-5
M-
5m
Slump flow
650800
718
708
660
565
460
490
T50 cm
25 sec
3.8
3.4
2.9
2.4
–
–
J-ring
010 mm
4.3
5.1
5.9
6.8
7.9
7.5
V-funnel
812 sec
9.3
8.1
6.8
5.6
4.7
4.2
V-funnel (5 min)
+3sec
11.6
10.1
8.6
7.1
6.0
5.5
L-box (H2/H1)
ratio
0.8 1.0
0.89
0.80
0.70
0.61
0.51
0.54
U-box (H1H2)
030 mm
16
21
25
30
35
31
Orimet
05 sec
4.6
4.1
3.5
3.2
2.7
2.3
TABLE 8.THE 7, 28 AND 120 DAYS COMPRESSIVE STRENGTH OF SCC WITH FLY ASH AND GGBS IN MPa
Curing period
7 days
28days
120 days
Mixes
Cube strength
Av strength
Cube strength
Av strength
Cube strength
Av strength
M-1
30.21
29.65
54.55
53.12
64.44
63.35
27.23
51.84
63.98
30.11
52.65
64.03
29.45
53.30
62.11
31.00
53.26
62.19
M-2
27.88
28.65
52.44
51.81
60.08
59.74
28.90
53.00
59.45
29.45
50.28
59.87
28.93
51.71
58.60
28.09
51.62
60.70
M-3
24.76
25.10
46.61
45.14
52.83
51.92
23.97
45.81
54.10
26.10
45.00
51.00
25.33
43.38
50.89
25.33
44.90
50.78
M-4
22.45
21.77
38.45
38.33
4.58
44.30
20.58
36.85
44.02
20.97
39.52
43.92
21.65
39.23
44.70
23.20
37.60
45.28
M-5
15.85
16.75
28.28
29.40
34.50
35.73
16.94
27.50
34.87
16.63
28.84
36.94
16.92
32.47
36.50
17.41
29.91
35.84
M-5m
18.20
17.80
30.45
31.63
38.28
38.57
17.80
32.21
39.40
18.88
33.03
40.31
17.68
30.69
37.79
16.44
31.77
37.12
From Table 7 and 3, for M-2mc mix, the slump flow increases marginally from 685mm to 690 mm,T50 decreases from 3.5 sec to 3 sec, J-ring value changes from 5.75mm to 5.8mm,V-funnel value from 9.4sec to 8.8 sec, L-box ratio reduces from 22mm to 16mm and Orimet from 3.2sec to 3 sec.
Due to the decrease in aggregate cement ratio, there will be an increase in the slump flow and the marginal increase in L-box ratio and the filling height in U- box.
From Table 8 and 5, it is observed that there will be the better improvements in 7 days and 28 days compressive strength of the hardened mix. The 7 days strength increases from 31.34 MPa to 40.77MPa (% increase of 30.09 MPa) and 28 days strength increases from 40.79 MPa to 56.16 MPa (% increase of 37.68MPa).
-
CONCLUSIONS
-
-
-
-
Self-compacting concrete mixes M-1 and M-2 designed by Nan Su method for lower packing factor of 1.2 will be able to yield sufficient quantity of filler material with cement more than 400kg/m3 as suggested by EFNARC and the mixing water nearly 160 liters/m3. But for mixes designed using higher values of packing factors such as 1.4 and onwards, there will be insufficient quantity of powder and water required for mixing. So such mixes requires modification in their design.
-
The fresh mixes designed by Nan Su method for all packing factors ranging from 1.2 to 1.4 for S/a ratios from
0.50 to 0.57 will be unable to satisfy the EFNARC requirement that the w/p ratio by volume to be in the range of 0.80 to1.10 .
-
The fresh mixes M-1 and M-2 containing more fly ash and the powder content nearly 500 kg/m3 compared to other mixes such as M-3m and M-4m mixes, there will be slump flow diameter more than 650mm, L-box ratio more than 0.80 and the difference of columns in U-box less than 30mm.The mixes M-3m and M-4m containing less powder are unable to satisfy these properties.
-
It is observed throughout its mixing that the fresh mix is very sensitive to water content added in excess of the saturation level required to produce a workable mix. This may lead the mix with segregation and bleeding. So while mixing; only 95% of the estimated water with super plasticizer is added first. Then the remaining water is added later, depending upon the weather conditions (atmospheric temperature and humidity other than standard values) so as to produce a mix free from segregation.
-
For mixes M-3m and M-4m Aggregate/cement ratio by weight more than 5 reduces nearly to 4.6 for M-1 and M-2 mixes, Thus it may be correlated that as aggregate cement ratio of a mix increases, there will be decrease in average diameter of slump flow from around 680mm to nearly 610mm, L-box ratio less than 0.80 and U-box height difference reads less than 30mm. J-ring values increases from nearly 5.5mm to8.1mm, Orimet value from3.2sec to
3.8 sec. But there are no systematic variations in any of the T50, V-funnel values.
-
All the mixes M-1, M-2, M-3 and M-4 designed by Nan Su method will be unable to achieve the 28 days design strength of 50 MPa. So extra cement as suggested [14] depending on grade of mix has to be added to achieve this strength.
-
The mixes designed by Nan Su method need the addition of extra cement as suggested using appropriate value of correction factor more than one. Due to the addition of extra cement in M-2 mix to make it as M-2 mc mix, the water powder ratio by volume will again less than 0.80,the
aggregate cement ratio decrease from 4.692 to 3.724 by weight. Hence slump flow slightly increases. The 7 days and 28 days compressive strengths increase by 30.09% and 37.68% expressed in MPa respectively. So it re-affirms the recommendations made by the investigators earlier that there is a need of extra cement more than that obtained by Nan Su method to not only to improve but to get sufficient compressive strength more than the design strength.
ACKNOWLEDGEMENTS
The author would like to acknowledge the financial support and encouragement given through grants (Research grant no- RRCE/Admin/SM/2015-2016 dated 13-09-2016) from the management of Rajarajeswari College of Engineering (RRCE) Bangalore. This research program is undertaken to promote the research activities in the institute. Thanks to the Principal and the Superintendent, RRCE for their kind help for their assistance throughout the work.
The authors are also thankful to Managing Director, Assistant General
.Manager and other supporting staff of the A.V.S. R.M C. Plant, Bangalore for their support to carry out this project.
The content of this paper reflect the views of the author who is responsible for the facts and accuracy of the data presented within.
REFERENCES:
[1]. Samir Surlaker, Self compacting concrete, Indian Concrete Journal,January-Marcp002,pp5-9. [2]. EFNARC (European federation of natural trade associations representing producers and applicators of specialist building product), Specifications and Guidelines for self-compacting concrete, February2002, Hampshire, UK. [3].Hajime Okamura and Masahiro Ouchi, self-compacting concrete, Journal of Advanced concrete technology, Vol 1, No 1,April 2005, pp 5 -15. [4]. Okamura H, and Ozawa, K, Mix-design for self-compacting concrete, Concrete Library of JSCE, 25,1995, pp107-120. [5].Nan Su, Kung chung Hsu,His Wen Chai, A simple mix design for self- compacting concrete ,Cement and Concrete Research, Vol 31(2001), pp1799-1807. [6]. Brouwers H.J.H and Radix H.J, Self Compacting Concrete: Theoretical and Experimental study, Cement and Concrete Research, Vol 35(2005), pp2116- 2136. [7]. Nagendra R and Sharadha Bai, Self compacting concrete containing granite powder, Indian Concrete Journal, April 2013, pp 22-26. [8]. Girish.S and Arjun.H.R, Development of SCC with crushed rock fines as filler Journal of Structural Engineering, Vol 38,No 1,April-May 2011,pp 60-66. [9]. Prakash Nanthagopalan and Manu Santhanam, A new approach to optimization of paste composition in self-compacting concrete, Indian Concrete Journal, November 2008, pp11-18. [10]. Loani . A,Domsa J, Mircea C, and Szilagyi H.Durability requirements in self-compacting concrete mix design, Concrete repair, Rehabilitation and Retrofitting II–Alexander et al (eds) © 2009,Taylor and Francis Group, London , ISBN 978-0-415-46850-3, pp 159-165. [11]. Vengala,J.and Ranganath, R.V., Mixture proportioning procedures for SCC Indian Concrete Journal, August 2004, pp 1321. [12]. Narendra. H, Muthu .K. U,Hashem Al Mattarneh, Naidu N. V. R, and Soumya. B.S, Optimization of self-compacting concrete mixes using Taguchi Method, ICCBT2008-A-(17)-pp191-204. [13].Guru Jawahar.J, Sashidhar.C, Ramana Reddy.I.V, and Annie Peter. J,A simple tool for self-compacting concrete mix design, International journal of Advances in Engineering and Technology(IJAET)ISSN:2231-1963,Vol.3,May 2012,Issue2,pp550- 558. [14].Karjinni V.V and Annadinni. S.B, A comparative Study on the mixture proportions and properties of high performance self-compacting concrete with fly ash, silica fume and metakoalin as mineral admixtures, Journal Of Structural Engineering, Vol 36,No 6, Feb- March 2010, pp 401-408. [15]. Mahesh. Y.V.S.U. and Manu Santhanam,Simple test methods to characterise the rheology of SCC, Indian Concrete Journal, June, 2004, pp 39-43.
[16]. Jagdeesh Vengala,Sudarshan.M.S and Ranganath. R.V, Experimental study for obtaining SCC , Indian concrete journal, August 2003,pp1261-1266. [17]. Manu Santhanam and S.Subramanian, Current Developments in SCC, Indian concrete journal, June 2004. [18]. Prajapathi, K.R., Chandak and Dubey, S. K., Development and properties of SCC mixed with fly ash, Research Journal of Engineering sciences, Volume1 (3), September 2012, pp 11-14. [19]. Rakeshkumar,and Rao,M.V.B., SCCAn emerging technology in construction industry, Indian concrete journal, July-September 2002,pp 912. [20]. S.A.Khadilkar and V.R.Kulkarni, Engineered fly ash based blended cement for durable concrete: A review, Indian concrete journal, April 2003, pp1009-1021. [21]. S. Gopalkrishnan,N.P.Rajmane,M.Neelmangalam,J.A.Peter and J.K.Dattatreya., Effect of partial replacement of cement with fly-ash on strength and durability of HPC, Indian concrete journal, May 2001,pp335-346. [22]. Jagdeesh Vengala,M.S.Sudarshan and R.V. Ranganath, Experimental study for obtaining SCC,,Indian concrete journal August 2003,pp1261- 1266 [23]. Naveenkumar, Kiran.V.John, Jagdeesh Vengala and R.V.Rangnath, SCC with fly ash and metakaolin, Indian concrete journal, April 2006, pp 33-39 [24]. N.P.Rajamane and Ambily P.S, Fly ash as a sand replacement material in concrete- a study,The Indian concrete journal, July 2013, pp 11-17. [25]. B.Mahalingam and K.Nagamani, The influence of processed fly ash on self-compacting concrete in fresh and hardened state. Journal of structural concrete, Volume 39, No 6 February-March 2013, pp 645-656.
[26].Shetty,M.S., Concrete technologytheory and practice published by Chand S and Co Ltd ,New Delhi,Reprint-2008,pp 528529. [27]. Dr. Rakeshkumar,and Rao,M.V.B., SCCAn emerging technology in construction industry, Indian concrete journal, July-September 2002,pp 912. And all other relevant codes