
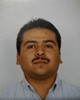
- Open Access
- Authors : Baldomero Villa-Covarrubias , Manuel R. Pina-Monarrez , Manuel Baro-Tijerina
- Paper ID : IJERTV9IS080329
- Volume & Issue : Volume 09, Issue 08 (August 2020)
- Published (First Online): 11-09-2020
- ISSN (Online) : 2278-0181
- Publisher Name : IJERT
- License:
This work is licensed under a Creative Commons Attribution 4.0 International License
Probabilistic Methodology to Determine The Shaft’s Diameter and Designed Reliability
Baldomero Villa-Covarrubias
Doctoral Student of the Technological Doctoral Program at the Engineering and Technological Institute Universidad Autónoma de Ciudad Juárez
Ciudad Juárez Chihuahua, México
Manuel Baro-Tijerina
Doctoral Student of the Technological Doctoral Program at the Engineering and Technological Institute Universidad Autónoma de Ciudad Juárez
Ciudad Juárez Chihuahua, México
Manuel R. Pina-Monarrez
Researcher at the Industrial and Manufacturing Department of the Engineering and Technological Institute, Universidad Autónoma de Ciudad Juárez,
Cd. Juárez, Chih, México.
Abstract In the proposed probabilistic shafts methodology the stress average and the standard deviation are both determined based on the binary synthesis approach. The efficiency of the proposed methodology is compared with the static and fatigue approaches. The application is performed by using a speed reducer. Then the estimated stress average and standard deviation are both used in the stress/strength methodology to determine the reliability of the designed shaft. Additionally, since by applying the probabilistic method, the mean and the standard deviation of the alternating Sa and fatigue Se values are both always determined, then the proposed method is generalized to determine the shafts reliability by considering that both Sa and Se follow either a normal, Weibull or lognormal distribution. Finally, the guidelines to select which distribution we should use in the stress-strength analysis are also given.
Keywords Probabilistic shaft design, Fatigue; Weibull distribution; Binary synthesis; Stress/strength analysis; Torsional rigidity.
-
INTRODUCTION
In machines and equipment a shaft is used to let movement and transmit power [1], [2]. Therefore, its design is based on the applied alternating (Sa) and the midrange stress (Sm) values. However, when a shaft fails due to the Sm value, its failure occurs at the first cycle (or after a few cycles), meaning that the instantaneous applied Sm value was higher than the shafts strength. However, because in the design shafts phase, a security factor is used, then the materials strength (Sy) value is higher enough than the Sm value (say Sy>>Sm), implying no first cycle failure occurs. Consequently, the shaft fails by fatigue. Fatigue is a failure generated by the cumulated damage, generated by the cyclical application of the stress. Therefore, in the analysis the shafts failure is generated by the alternating Sa stress value. Consequently, the shafts reliability is also based on the Sa value. Thus, in this paper the fatigue shafts design as well as the shafts reliability are both determined by using both the nominal Sa value and its corresponding standard deviation. The Sa standard deviation is determined based on the fatigue and binary synthesis methodologies. The efficiency of the proposed method is shown by designing an intermediate shaft of a fan speed reducer, and by comparing the designed shafts diameter with those given by the static and dynamic (fatigue) methodologies.
In the static approach, the speed reducer shafts design is performed based on the bending and torsional stresses that are acting at the critical point of the shaft, in the yield strength Sy and ultimate strength Sut materials values [3]. And to determine if the designed shaft is whether safe or not, the Von Mises and the distortion energy (DE) criteria, with a safety factor of two [4-5] are used. The designed static shafts diameter was ds=0.0235m (0.928 in).
In similar form, in the dynamic fatigue approach [4], the shafts design analysis was based on both the alternating Sa and midrange Sm stresses values at which the shaft is subjected. The applied Sa value was determined based on both the bending loads generated by the gears, and on the radial forces generated by the applied torque. And the Sm value was determined through the Soderbergs fatigue method, were the modified endurance limit (Se) value was determined by using the corresponding endurance modification factors. The designed fatigue shaft diameter was df=0.0375m (1.48 in).
On the other hand, in the binary synthesis approach [5], the shafts design analysis was performed by considering that all the endurance limit modification factors of the above fatigue approach are random [6] [7], and that they can be modeled by a normal distribution [8]. Therefore, after all the modifier factor were synthetized by using the binary synthesis approach. Then from the synthetized average values, the corresponding modified endurance limit (Se) value was determined. And by using the Se value with the corresponding Soderberg line and the stress ratio (r=Sa/Sm) in the Soderbergs diagram, the maximum allowed Sa value was determined. Finally, by using the Sa value of the fatigue analysis, and the addressed binary Sa value and a safety factor of 2, the designed binary shaft diameter was db=0.0381m (1.50 in).
However, here it is important to observe that 1) although in the static, fatigue and binary approaches we conclude the designed shaft is considered safe, and we use a safety factor of two, from neither of these analyses it is possible to determine the reliability that the designed shaft presents. And 2) because db>df>ds (0.0235m>0.0375m>0.0381m), then we have that the robust design is the one given by the binary method with db=0.0381m. 3) because in the binary method, the estimated Sa value is higher than the minimum expected strength Semin value (Sa>Semin), then although we design the shaft with db=0.0381m, failures are expected. Hence in order to avoid failures, in
section VI a probabilistic method to avoid selecting a Sa value higher than the minimum Semin value, is presented. The proposed method is based on the fatigue and binary approaches. And its main contribution consists of 1) given the minimum expected modified endurance limit Semin value, to create a new Soderberg line, and from it to derive the mean and the standard deviation of Sa in such a way that the maximum expected Sa value never will be higher than the minimum expected Semin
Motor
Gear box
Gear A
Gear B
Shaft 1 A
Shaft 2 Gear C
C
B
Gear D D
value (Sa<Semin). And 2) by using the addressed normal distributions families of Sa and Se in the corresponding stress/strength function, the reliability of the designed shaft is
Shaft 3
Side view
determined. Therefore, by applying the proposed method, the designed probabilistic shaft diameter was d=0.0418m (1.647 in), with a designed reliability of R(t)=0.9950. However, at this point, it is important to mention that because the torsional rigidity method requires a minimum shaft diameter of 0.0419m (1.65in), then finally the recommended diameter for shaft 2 was 0.0419m. Finally, since by applying the probabilistic method, the mean and the standard deviation of Sa and Se are both always determined, then the stress-strength analysis is generalized to determine the shafts reliability, for any combination among the normal, Weibull and lognormal distribution, and the guidelines to select the right distribution are also given.
-
DATA OF THE ANALIZHED CASE
In order to perform the comparison between the static, dynamic and binary synthesis design approaches, as well as to formulate the probabilistic proposed method, the intermediate shaft of a speed reducer used for a grain drying process is designed. In the application, it is required to move the fan a 450 rpm with a power of 12 hp. The shaft designs material is an AISI 1020 steel normalized at 925 ° C (1,700 ° F) air cooled, 50 mm (2 in) round with ultimate tensile strength of Sut = 438 MPa (63,500 psi), tensile yield strength of Syt = 319 MPa (46,300 psi), and a shear modulus of G = 72 GPa (10,400 ksi) [9]. Therefore, because the selected motor is a 12 hp motor and a turning speed of 1,800 rpm, then the speed reducer must be designed to decrease the speed from 1,800 rpm to 450 rpm, and this has to be made by conserving the initial motors power of
Fig. 1. Electric motor connected to speed reducer.
On the other hand, due to spur gears B and C, shaft 2 is subjected to bending stresses and constant torsional forces generated by the transmission of power, then in order to avoid plastic deformation, its design must comply with a minimum torsional rigidity of (0.25 °/ m) [14] [15].
Similarly, due to the bending and torsional stresses at which shaft 2 is subjected (see Fig. 2), the expected failure mode of the shaft is due to fatigue. This implies that for the dynamic design, the modified endurance limit Se has to be calculated [3][4]. And according to [16], the endurance limit modification factors that affect Se are surface factor ka = 0.8, size factor kb, load factor kc = 1 and temperature factor kd = 1. Also, due to the concentration of stresses generated by the loads at which the shaft is subjected, the holes for the assembled gears and the type of material, the fatigue stress concentration factors for bending KFF and for torsion factor KFT must be considered also. However, since in this stage neither the dimensions of the geometry nor the shafts diameter are known, then following
[15] KFF = 2 and KFT = 1.6 were used.Shaft 2
Gear B
Gear C
Bearing Bearing
0.1778 m
12 hp.
0.0762 m
0.0762 m
The scheme of the reducer, coupled to the motor, the position of the spur gears in the shafts, and the shafts length are all presented in Figure 1. This system can transfer motion and torque via two accurately stages of configuration and efficiently [10]. The selected motor has a shaft diameter of 0.035m(1 3/8 in) [11] [12]. The motor is connected to the shaft 1 of the reducer by using a flexible coupling. The spur gear A is mounted on shaft 1, which engages with spur gear B of shaft
2. A spur gear C is mounted on shaft 2, which is connected to spur gear D that is mounted on the shaft 3. And according to [12], the main characteristics of the 4 spur gears to reduce the engine speed are shown in Table 1. From Table 1, we have that due to the relationship between spur gears A and B, the initial angular velocity of shaft 1 of 1,800 rpm is reduced in shaft 2 to 900 rpm. Similarly, note due to the relation between spur gears C and D, this angular velocity in shaft 3 is finally reduced to the required 450 rpm.
Fig. 2 Top view of shaft 2.
Table 1. Spur gears characteristics of the speed reducer
Spur gear
Diametral Pitch (in-1)
Pitch diameter (in)
Number of teeth
Face width (1.5)
A
8
2.5
20
1.5
B
8
5
40
1.5
C
8
3
24
1.5
D
8
6
48
1.5
Finally, before to present the design analysis of shaft 2 through the static, dynamic and binary synthesis approaches, it is necessary to determine the critical point where the shaft could fail. And because the selection of the critical point depends on
1) the applied torque generated by the torsional forces of the gears B and C and on 2) the maximum applied bending moment generated by both the radial forces and their corresponding reactions, then let first present the torque analysis.
-
Torque Calculations for Shaft 2
The torque generated on shaft 2 depends on the angular velocity () at which the shaft will rotate, and on the power (P) that the shaft has to transmit. Hence, the generated torque is given by:
= 63000
(1)
= (tan ) (3)
In (1), P is the power measured in horse power hp units, 63,000 is a conversion factor from hp to pounds, is given in revolutions per minute (rpm), and T is measured in pounds per inch (lb in). Therefore, under the assumption that there is no loss of power, P=12 hp, and due to the ratio of gears A and B (see Fig.1), =900 rpm, then the generated torque in shaft 2 is
63,000 (12 )
Numerically, by using from Table 1 rB=0.0635m (2.5 in), for gear B the tangential and the radial forces are
= = 94.90.0635 = 1494.48
= (tan ) = 1494.48 (tan 20°) = 543.94
Similarly, since from Table 1 rC=0.0381m (1.5 in), then for gear C the tangential and the radial forces are
=
= 840 = 94.9
(900 )
=
= 94.90.0381 = 2490.81
And because the analyzed system is in equilibrium, then as it is shown in Figure 3 and in Figure 4, the torque in gear B of TB = 94.9Nm is equal to that in gear C, but in the opposite direction, Tc = -94.9Nm. It is to say; the generated torque is constant through the shaft at T=94.9Nm.
-
Maximum Bending Moment for Shaft 2
Since the radial and tangential forces generated by the spur gears generate bending moments in the shaft, and because these generated moments by themselves generate bending stress on the shaft, then the maximum bending moment at which the shaft is subject is determined from the bending moments diagram
= (tan ) = 2490.81 (tan 20°) = 906.58
Now let present the reactions calculations.
Fr F
=20°
Ft
Fig. 5. Forces and reactions acting on the bearings and gears
[17][18]. However, because the bending moment diagram is based on the shear forces diagram, which is built based on the radial and tangential forces, and on the corresponding reactions forces, then let us first calculate the radial, tangential and reaction forces. The analysis is as follows.+Y
RAZ
-Z
FRB
FTC
RDY
A B C D + X
TA
A Tc
TB C x
RAY
+Z
FTB
FRC
RDZ
-Y
B Fig. 6. Generated forces on the gear teeth
Fig. 3. Gear torque direction
T (Nm)
94.9
X (m)
D. Bearing reactions calculations
The calculation of the reactions, generated in the bearings by the radial and tangential forces, depends on the axis of symmetry in which these forces are being generated. In our case, since these forces are in different axis of symmetry, then in the analysis we have to consider that the forces are acting in two different planes; the x-y and the x-z planes (see Fig. 6). Thus, the analysis is based in the force and reaction diagrams given in Figure 7 and Figure 8.
A B C D
Fig. 4. Shaft 2 torque diagram.
-
Radial and tangential forces calculation
The calculation of the radial and tangential forces, and reactions (see Fig. 5) that are acting on the teeth of gears B and C depends on their corresponding pressure angle () (see Fig.
+Y
F
F
F
F
RB RC
A B C D X
6). In this case the pressure angle of spur gears B and C is = 20 °. Thus, the generated tangential force, which is in function
RAY
RDY
of the torque and the spur gear radius is given by [3][19]
Figure 7. Force and reaction in x-y plane
=
(2)
Hence, in function of and Ft, the radial force [3][20], is given by
-Z
RAZ
A
RDZ
B C
D X
F(N)
-1724.40
z
z
-229.92
x
FTB
+Z
FTC
+2260.89
igure 8. Force and reaction in x-z plane
As it is shown in Fig. 7, the forces and reactions which are acting in the x-y plane are.
+ = 0 = (543.94 )(0.254) +
(906.58 )(0.0762) (0.3302)(); =
627.62
= 0 = 627.62 543.94 906.58 + ;
= 822.9
Similarly, as it is shown in Fig. 8, the forces and reactions which are acting in the x-z plane are.
A B C D
Figure 11. Shear force diagram for x-z plane.
M (Nm)
172.27
131.39
x
A B C D
+
= 0 = (
)(0.3302 ) (1494.48 )(0.254)
Fig. 12. Flexing moment diagram for x-z plane
(2490.81 )(0.0762 );
= 1724.40
Similarly, for the x-z plane, the shear force diagram and the bending moment diagram are given in Figure 11 and Figure 12 respectively. Thus, based on the bending moments diagrams of
= 0 = 1724.40 + 1494.48 + 2490.81 ;
= 2260.89
Now based on these forces and reactions let present the shear forces and maximum flexion moment calculations.
-
Shear forces and maximum flexion moment diagram
Using the reaction forces and the estimated radial loads, the shear force diagram for the x-y plane is given in Figure 9. Therefore, based in these forces and on the distances of the shear force diagram, the corresponding bending moments diagram for plane x-y is given in Figure 10.
F(N)
y
627.62
83.67
Figures 10 and 12, the maximum bending moment to be used in the design of shaft 2 is
= 2 + 2 ,
= (62.70 )2 + (172.27)2,
= 183.32
Finally, from the torque diagram given in Fig. 4 and from the flexion moment diagrams given in Figs. 10 and 12, we have that the critical point for the analysis in the design of shaft 2, is the point C. In the same way, we have that to avoid plastic deformation by torsion, then if the size of the designed diameter from either of the three design approaches is smaller than the diameter given by the torsional rigidity approach, then the recommended diameter size must be the one given by the torsional rigidity approach.
0.0762
0.1778
-822.9
0.0762
x (m)
-
Torsional Rigidity Angle Approach for Shaft 2
To avoid plastic deformation, the materials strength used in the shaft design has to withstand the applied torsional forces.
A B C D
Figure 9. Shear force diagram for x-y plane.
M (Nm)
y
62.70
47.82
x (m)
0.0762 0.1778 0.0762
A B C D
Fig. 10. Bending moments diagram for x-y plane
This is determined by measuring the torsion angle caused by the applied torque along the entire length of the shaft. Thus, to avoid plastic deformation the shafts diameter given by the rigidity approach has to be used as the minimum allowed diameter in the shaft design [4]. And because the minimum torsional rigidity value to be used in the shaft design depends on the precision of the analysis that the application requires, then in this paper the used value was selected from the classification given in [14][15].
On the other hand, although in practice the procedure to design a shaft, consists of first to determine the shaft diameter, and then based on its value, to determine the torsion angle. And finally, by comparing the torsion angle with the rigidity angle of the used material, we determine if the selected shaft diameter
is whether safe or not to fail by plastic deformation. Therefore, because using the torsion angle is equivalent to using the shafts
1
diameter [4], then in this article the conformance of the material
with the torsional rigidity, is made through the comparison of = [
32(2)
6
2 (183.32)2 +
3
3
(94.9)2]
the designed diameter with the diameter given by the torsional rigidity approach, which is calculated as
(31910
= 2.35102
/ ) 4
= [
1
32 4
]
()
(4)
Thus, because the designed static shafts diameter of ds=0.0235m (0,928in) in is lower than the minimum acceptable diameter of the torsional rigidity of sec. IIF of dr=0.041m
Based on Table 4 in [14], in this case of study a torsion angle of 0.0001108 radians in each inch, is recommended. Hence, by replacing this value in (4), the shafts diameter of the torsional rigidity approach is
1
(1.65in), then the recommended diameter for shaft 2 is the one given by the torsional rigidity of 0.041m.
Here it is important to notice that although (5) was derived based on the Von Mises criteria, and we used a SF=2, as in the rigidity approach, it is not possible to determine the reliability
]
]
32(94.9) 4
= [(72109 /2)(0.00463 /)
= 0.041
that the designed shaft presents. However before present the method to determine the reliability of the designed shaft, let present the shafts design through the fatigue method.
Thus, to avoid plastic deformation dr = 0.041m (1.65in)
represents the minimum allowed diameter value for shaft 2. And therefore, the shaft diameters given by the static, dynamic and probabilistic design approaches have to be compared with it. And in all cases if the designed diameter is lower than 0.041m, then Shaft 2 must be designed at 0.041m.
Here notice that although this torsional rigidity diameter prevents us to have failures by plastic deformation, it does not prevent us of failures generated by fatigue, and neither let us know the reliability that the designed shaft presents. However, before present the method to determine the shafts reliability, let first present the static shafts design approach.
-
-
STATIC DESIGN APPROACH
The static shafts design method offers the initial steps to design a shaft. In this static method, the shafts diameter is determined based on the principal stress values generated by the forces that are acting on the shaft. And the determination if the designed shaft is whether safe or not, it is performed by using the Von Misses [distortion energy (DET)] and Tresca [Maximum stress shear (MSST)] theories [5] [3] with a selected
-
FATIGUE DESIGN APPROACH
The fatigue in a mechanical component is caused by the loads repetitiveness. These loads being of lesser magnitude than those that can cause plastic deformation in ductile materials or rupture in fragile materials. Thus, the design of a shaft by the fatigue approach is based on the alternating stress (Sa) and on the mean stress (Sm) values generated by the bending and torsional loads that are acting on the shaft. And while Sa is variant because it is generated by the bending stresses, Sm is constant because it is generated by the applied constant torque (see Fig. 13). However, because initially the shafts diameter is unknown then at this stage Sa and Sm are both unknown, and therefore they are determined by using a fatigue failure theory. The most common used theories are the Soderberg, Goodman, Gerber and ASME theories. However, because in the shaft 2 design, an AISI-1020 steel is used, which is a ductile material and plastic deformation is not allowed, then in the analysis Sa and Sm are both determined based on the Soderberg theory [3][4]
safety factor value. The static design analysis is as follows.
A. Static Shaft Design
Based on the Von Mises criteria, the determination of the designed shaft diameter through the static method is given by the formula
1
Tensile
Stress
Compressive
smax
sa
Sm
smin
time
= (32
2
3
+ 34 2)
(5)
Stress
Fig. 13. Alternating and mean stresses.
In (5), SF is the safety factor which from [4] is recommended to be SF=2. Sy is the tensile yield strength of the used material, which from sec. II is Sy=319 MPa 46,000 lb/in2). M is the maximum bending moment estimated in sec. IIE as M=183.32Nm. And T is the applied torque estimated in sec. IIA as T=94.9Nm. Thus, by substituting these values in (5), the estimated static shaft diameter is
Similarly, based on the Whöler S-N curve of the used material, the endurance limit S'e to be used in the fatigue analysis is determined. And then, through the application of the endurance limit modification factors, the S'e value is lowered to the called modified endurance limit Se, which in the fatigue analysis is taken as the real fatigue limit of the analyzed case. In our case, the used modifier endurance limit factors are surface, size, type of load, temperature, and fatigue. And because axial forces are not acting on shaft 2, then the designed shafts diameter is determined based on the Soderberg and Von Mises theories. Hence, due to the lack of axial forces, the shafts diameter is only in function of the bending and torque moments [4], and its diameter is given by
1 In the same way, by using the modifier factors, the bending
3
= [
32
( +
2
)
3
+ 4 ( +
2
) ]
(6)
modified endurance limit is
[(0.8)(0.85)(1)(1)(219 )]=
= 74.46
2
In (6), Mm is the mean bending moment, Ma is the mean alternating bending moment, Tm is the mean torque, Ta is the
Finally, by substituting these values in (7) the estimated fatigue shaft diameter is
alternating torque, Sy is the yield strength for bending loads, Sys
[ [3
3
is the shear yield strength for torsional loads, Sef is the modified 1
endurance limit for bending and S
is the shear modified
32(2)
(319106 /2)(183.38) 2 3
et = { 6 2
6 2 ] +
(94.9)2}
endurance limit for torsional loads. Numerically the shafts 2 diameter is as follows.
(31910 / )
74.4610 / 4
= 0.036
A. Fatigue Shaft Design
For the determination of the diameter of the shaft 2, notice first from Figure 13 that when the shaft rotates, the bending moment Mm, which is generated due to radial and tangential loads of the spur gears (see Fig. 5), produces the alternating stresses shown in Fig.13. Then the alternating stress Sa at which the shaft is subjected is equivalent to the maximum stress Smax. Also notice that this implies that because in (6) the force moments will be used to determine the shafts diameter, then the alternating moment Ma is equivalent to the maximum moment of section IIE (Ma=Mmax=183.32Nm). In the same way, notice from Fig.13 that because the mean stress Sm is zero, then the mean moment Mm is equal to zero (Mm = 0) also. And since the torque on the shaft is constant because the power and angular velocity remain constant, then the mean torque Tm is equivalent to the torque at the critical point C (Tc). That is, Tm
= Tc =94.9 Nm. This implies that because there are no variations in the torque, then in (6) the alternating torque Ta element is also zero. And as a consequence, that both Mm and Ta are zero (null), then the terms Sys and Sse can also be omitted from (6). Therefore, the final formula to determine the fatigue diameter is given by
1
Thus, because the designed fatigue shafts diameter of df=0.036m(1.45in), is lower than the minimum acceptable diameter of the torsional rigidity value of sec. IIF of dr=0.0419m(1.65in), then as in the static approach, the recommended diameter for shaft 2 is 0.0419m. Here it is important to notice that although (7) was derived based on the Von Mises criteria, and we used a SF=2, then as in the static and rigidity approach, in this fatigue analysis it is not possible to determine the reliability that the designed shaft presents. Now let present the shaft design through the binary synthesis method.
-
BINARY SYNTHESIS DESIGN APPROACH
In the binary synthesis method, the shafts diameter is determined in function of the maximum applied alternating Sa value determined from the maximum moment Ma value given by the static analysis, the average Se value, the yield strength of the used material Sy and the Sm values caused by the torque. And because in this approach, Se is considered to be random, then not only its mean µSe, but also its standard deviation Se are both determined by applying the synthesis method to each one of the modifier factors. And once the Se and Sy values are known, by using them in the Soderberg diagram with the
2
= [32 ( )
+ 3 (
3
)2]
(7)
corresponding stress ratio r (see Fig. 14), the Sa and Sm values
4
are both determined. Here, the SolidWorks routine was used (see Fig. 14).
Where the bending modified endurance limit Sef is given by
Alternating stress
=
(8)
Soderberg
In (8), the values of k =0.8, k =1 k =1 and K
Se
=2 were given
Line
a c d FF
S
S
in II. On the other hand, the value of the size factor kb was not Sf
provided because the shaft diameter is unknown. Therefore, the a
kb value is selected by using as a reference, the static shafts r diameter determined in sec. IIIA of ds = 0.023m. From [3] it is determined as
S
Sy Midrange stress
or
= 0.85 (0.0127 < < 0.0508)
= 0.70 ( > 0.0508)
m
Fig. 14. Soderberg diagram
Now let present the functional relationships to perform the binary synthesis analysis.
Hence, the selected value is kb = 0.85. And because the
bending endurance limit (Sef) is given as
, = 0.5 (9)
Then by substituting it in (9), with the Sut value given in sec. II, the Sef value to be used to determine the shaft diameter is
, = 0.5(438 MPa ) = 219
-
Alternating and endurance binary synthesis analysis
The input variables to determine the shafts diameter through the binary synthesis method and the Soderberg diagram, are the Sa, Sm, Sy, and Se values. Where the Sa and Sm values are determined from their ratio (r), their angle and from their real endurance limit Se values, then let first, calculate the
functional relationship between Sa and Sm (r and ). And then to present the binary synthesis analysis to determine the average and standard deviation of Se. And finally, to determine the diameter of the designed shaft. The functional relationships that determine the Sa value are as follows.
-
Alternating stress estimation
The functional relationship for Sa is given as Sa=(Mc)/I where M is the maximum bending moment (Ma), c is the shafts radius and I is the inertia moment given by I=d4/64. Hence Sa in terms of M and d is given as
being already synthesized. Finally, it is important to mention that because the synthetization process is performed according with the functional relationship that the synthetized variables have among them, e.g. addition, subtraction, product, division, square root, etc., then in the synthetization process, the Table
4.2 given in [5] p.162 and p.163 were used.
=
=
The analysis to determine the corresponding modified endurance limit Se is as follows. From (8) the surface factor ka and the size factor kb are synthesized. It is done by using x to represent ka and y to represent kb. Hence their corresponding mean are µx for ka and µy for kb and their mean values are
= = = =
= = = =
2
64
32
10.18
= 0.8 and = = 0.85. Thus, since from (8), the
=
4 23 3 64
3 (10)
relation between ka and kb is a product, then from the operation number 6 of Table 4.2 in [5] p.162, the mean of thesynthesized
Finally, by substituting the maximum moment M
=183.38Nm, addressed in sec. IIE in (10), the equation of Sa in function of the unknown shafts diameter is given as
binary variable is
= = (16)
=
10.18
3 =
10.18(183.38)
3 =
1866.8 (11)
3
Numerically it is
( )( ) = ( )( ) = (0.8)(0.85) = 0.68
Similarly, the equation to determine the mean stress Sm, in terms of the shear stress is given by
= 3 (12)
Where =Tc/J, with T representing the torque estimated in sec.2.1 of T=94.9Nm and J is the inertia moment given as
J=1/2 c4. Thus, by using T=94.9Nm the shear stress
Similarly, by using x to represent the standard deviation of ka and y for kb, their numerical values are; x=(0.8)(0.1)=0.08 and y=(0.85)(0.1)=0.085. Therefore, following the operation number 6 (product) of Table 4.2 of [5] p.162, with =0 (the finished surface ka is independent of the size element kb), the standard deviation of the synthesized variable (kakb) is
1
function it is given as
= [(22 + 2 2 + 22)(1 + 2)]2 (17)
= =
= 16 = 5.093(94.9) = 483.32
(13)
Numerically it is
14 2
3
3
3
(
) = {[(0.8)2(0.85)2 + (0.85)2(0.08)2
Therefore, the equation to estimate Sm in function of the unknown shafts diameter is given by
+ (0.08)2(0.085)2][1 + (0)2]}12
() = 0.0964
483.32 837.13
= (3 ) ( ) =
(14)
3 3
The next step is to synthesize the load factor kc with the synthesized variable (kakb). Doing this, the mean of ( )( )is
And since both Sm and Sa are in function of the unknown
diameter, then in the analysis its ratio is used. It is given as
1866.8
taken as µx=0.68, and from sec. IVA () = 1 is taken as y. Thus, since the relation of kc with (kakb) is also a product, then
= =
3 837.13
= 2.22 (15)
= 2.22 (15)
3
following the operation number 6 (product) of Table 4.2 of [5]
p.162, the mean of the synthesized variable is
Thus, the angle to be used in the Soderberg diagram to
( )() =
= (0.68)(1) = 0.68
determine the maximum allowed Sa and Sm values is
= tan1 = tan1(2.22) = 65.75°
Similarly, taking the 10% of y as its deviation, the standard deviations to be synthesized are
= = 0.0964
Now to estimate the Sa and Sm values let present the determination of the endurance limit Se value to be used in the estimation process.
-
Endurance fatigue limit estimation
and = = (1)(0.1) = 0.1
And following the operation number 6 (product) of Table
4.2 of [5] p.162 with =0 (the load is independent of kakb), given in (16), the standard deviation of the new synthesized binary variable (kakbkc) is
The Se value used in the Soderberg diagram to estimate the Sa and Sm values, is determined by applying the binary synthesis
= {[(0.68)2(0.1)2 + (1)2(0.0964)2 +
1
method as follows. All the modifier factors are considered to
follow a normal distribution. Therefore, their standard deviation is estimated as the 10% of their average value [5]. After that, two factors are synthesized by using their corresponding mean and standard deviations, a new binary factor with its own synthesized mean and standard deviation is determined. Then another factor is synthesized with the one obtained previously. The process is repeated until all factors are
(0.0964)2(0.1)2][1 + (0)2)]}2 = 0.1183
The next step is to synthesize the temperature factor kd with the synthesized variable (kakbkc). Thus, since the relation of kd with (kakbkc) is also a product, then because
( )( )() = = 0.68
and from sec. IVA ( ) = = 1 then the mean of the synthesized variable is
the corresponding standard deviation of the new synthesized binary variable with =0 (variables are independent each other) is
( )( ) = = (0.68)(1) = 0.68
2
2
2
2
= {[()2()
+ ()2()2 + ()2()
13
] [1 + ()2]}
And by using = (
) = 0.1183
and y=(kd)=(1)(0.1)=0.1, the standard deviation of the new synthesized binary variable (kakbkckd) is
2 2 2
(21)
2
= {[(0.34) (21.9)
+ (219) (0.07604)
= {[(0.68)2(0.1)2 + (1)2(0.1183)2 +
1
1
2 2 2
+ (0.07604)2(21.9)2][1 + (0)2)]}2
(0.1183) (0.1) ][1 + (0) )]}2 = 0.1369
The next step is to synthesize the fatigue factor KF with the synthesized variable (kakbkckd). Thus, since the relation of KF with (kakbkckd) is a quotient then by using
= 18309786.41
Therefore, the modified endurance limit Se value to be used to determine the corresponding Sa and Sm values is Se=74428904.94Pa, with expected standard deviation of (Se)=
=
= 0.68
and from form sec. IVA = = 2, then by using operation 7 (quotient) of Table 4.2 by [5] (17) p.163, the mean of the synthesized binary variable is
µ = (18)
µ
Numerically it is
/ = µ = 0.68 = 0.34
18309786.41. The numerical analysis to determine the Sa and
Sm values as well as the shaft diameter is as follows.
-
Binary synthesis diameter determination
Since from the plotted Soderberg diagram (see Fig.15), no mathematical function exists to determine the Sa and Sm values directly from the known = 74428904.97 Pa, = 320 MPa and = 65.75°, then the SolidWorks routine was used (any other routine can be used). The found Sa and Sm values are Sa
Similarly, by using
µ 2
=66945197.51Pa and Sm=30156634.18Pa.
Therefore, by using a safety factor of 2 [14,19] and the estimated Sa value in (10) the designed diameter is
() = = 0.1369
and () = = (2)(0.1) = 0.2
in the operation 7 (quotient) of Table 4.2 of [5] (17) p.163,
Numerically it is
3 10.18
=
/SF
(22)
the standard deviation of the new synthesized binary variable
(kakbkckd/KF) is given as
1
1
22+2 2 2
3
=
113922419.49
66945197.51Pa/2
= 0.038
=
( )
(19)
2 +2
Numerically it is
2
1
2 2 2
Here it is important to notice that although from (22) the shaft diameter was determined by considering Se to be random and we used a SF=2, as in the static, fatigue and rigidity
approach, in this binary synthesis analysis is not possible to
1 (0.68) (0.2)
+ (2) (0.1369) 2
determine the reliability that the designed shaft presents.
2
2
= [
(2)2 + (0.2)2 ]
= 0.07604
Therefore, now let present the proposed method which will let
Finally, to obtain the modified endurance limit Se, the binary synthesis method is performed between the synthesized binary variable = () and the endurance limit y=Se' of the used material. The endurance material limit is Se'=0.5Sut=0.5(438MPa) =219MPa. Thus, the means to be synthesized are = () = 0.34 and Se'=µy=219MPa. And because the relation of Se' with = () is a product, then from operation 6 of Table
-
of [5] p.162, the mean of the synthesized variable is
= = (µ)() (20)
us both to perform the analysis by considering a probabilistic behavior and to determine the reliability of the designed shaft. The proposed Probabilistic method is as follows.
-
-
PROPOSED SHAFT DESIGN METHOD
In this section the method to probabilistically to determine the diameter of the designed shaft as well as its corresponding reliability is given. In the method the applied alternating stress Sa and the material strength Se, are random variables. And based on the minimum expected strength Semin value, the maximum allowed Samax value, for which zero failure are expected is
Numerically it is
= (0.34)(219 ) = 74.46
Similarly, by taking
= = 0.07604
and
= = (219)(0.1) = 21.9
determined. However, first let start showing that in our analyzed case, because the addressed Sa value is higher than the minimum expected Semin value (Sa > Semin), then failures are expected. The analysis is as follows.
-
Overlapping of Sa and Semin
Since in the analyzed case, the addressed alternating value was Sa =66945197.51Pa, and because the endurance limit value is Se = 74428904.97Pa, with standard deviation of =
18309786.41Pa, then the minimum expected Se value is Semin
=Se , which numerically is Semin = 56119118.56Pa. Thus, we have that because 66945197.51Pa >56119118.56Pa (see Figure 15), then failures are expected [21]. And therefore, a
2 =
Step 7. Determine the shafts diameter as
3 10.18
(27)
lower S´a value which does not overlapping with Semin has to be determined and used to determine the shaft diameter. The steps
=
Sa2
(28)
are as follows.
Step 8. Determine the reliability of the designed shaft by
using (29) and (30)
Alternating Stress (Pa)
= 2
2 +2
(29)
´
Se=74428904.97 Sa= 66945197.51
Semin =56119118.56
SF
=65.75°
Soderberg Line
() = 1 () (30) Now let present the application of the proposed method.
C. Numerical Application of the Proposed Method
Step 1. From (21) the mean of Se is (Se)=74428904.97Pa. And from (20) and (21) its standard deviation is (Se
Sm=30156634.1
S = 320X106
yt
yt
Midrange
Stress (Pa)
)=18309786.41Pa.
Note 1: Notice that although here (Se) and (Se), were both determined by using the synthesis binary method, in practice
Fig. 15. Overlap of Sa and Semin
-
Steps of the Proposed Method
Step 1. By using the modified factors, determine the mean value of Se and its respective standard deviation (Se).
Step 2. Determine the minimum expected value of Se as
= (23)
Step 3. Draw a new Soderberg line parallel to the original one, but now starting at the Semin value of step 2 (see Fig.16).
Alternating stress
S
they can be determined by any other method.
Step 2. From (23) the minimum expected endurance limit (Semin) is
Semin = 74428904.97Pa 18309786.41Pa = 56119118.56Pa.
Step 3. The new Soderberg line is drawn starting at Semin=56119118.56Pa and being parallel to the original one (see Fig.17).
Alternating Stress (Pa)
Se=
SF
e
SF
Semin
New Soderberg Line
S =56119118.56 New Soderberg Line
emin
emin
S´a= 51017380.5
Sa
Sm
Midrange
S
S
y
=65.75
Sm= 22981605
y
y
S = 320×106
Midrange
Fig. 16. New Soderberg Line
stress
Fig. 17. New Soderberg Line with values
Stress (Pa)
Step 4. Based on the Semin value of step 2, determine the maximum allowed S'a value as
, = /1.1 (24)
Step 5. Determine the standard deviation of S'a as
= 0.10 (25)
Here notice that 1) by its own construction Samax and Semin are always equals
Step 4. From (24) the maximum allowed alternating stress value is Sa = (56119118.56Pa) /1.1 = 51017380.5Pa
Step 5. From (25) the standard deviation of S'a is S´a = 0.10 S'a= 0.10 (51017380.5Pa) = 5101738.05Pa.
Step 6. From (27), and by using a safety factor of 2 [14,19] the alternating stress (Sa2) value to determine the shaft diameter is
+ =
(26)
2 = 51017380.52 = 25508690.25
And that 2) as shown in Fig. 16, it implies we are using a safety factor of 1.
Step 7. From (28) the shafts diameter is
d= 3 1866.84=3
1866.84
= 0.0418m
Step 6. If a different safety factor value is used, determine the corresponding Sa2 value to be use as
2
25508690.252
Step 8. From (29) and (30), the shafts reliability is as follows
proposed method is generalized to use the Weibull distribution to determine the designed shafts reliability. This is done
2
25508690.2574428904
because due to its flexibility, the Weibull distribution can model
=
= = 2.57.
2 2 (18309786.41)2+(5474023.6)2
also the normal distribution behavior. Weibull distribution has
+´
Therefore, since this Z value corresponds to P(Z)=0.005 cumulative failure probability, then from (29) the deigned reliability is R(t)=1-P(Z) = 1 0.005=0.9995.
been applied to solve a variety of problems in different areas
[22] and is frequently adopted to reflect lifetime distribution to assess system reliability [23]. This approximately occurs for a Weibull shape parameters close to =3.44. The Weibull density function is given byAs a summary of this section, we have that by considering that the applied stress S´a and inherent strength Se are both
1
( ) = ( )
{ ( ) } (32)
random, by applying the proposed probabilistic method, the
designed shafts diameter is d=0.0418m(1.647in). And that because it was determined by using the S´a value which does not overlap with the Semin value, then shaft 2 can be considered safe. Even more, from step 8, we conclude the designed reliability of the shaft is R(t)=99.95%.
Where is the scale parameter and j=a,e, with a representing the alternating stress Sa, and e representing the modified endurance limit Se. The corresponding Weibull reliability function is given as
Now let compare the designed R(t) index of the proposed
() = { (
)
} (33)
method with those given by the static, fatigue, and binary synthesis approaches.
D. A Reliability Comparison Among the Shaft Design Methodologies
The comparison among the design approaches is given in Table 2, where the given reliability indices were determined by
Therefore, because as demonstrated in [24] the Weibull shape and scale parameters, both can be determined directly from the maximum and minimum stress values, then in this section, the mean and the standard deviation of Sa are used to determine the maximum and the minimum expected stresses values of Sa as
using (29) and (30). The corresponding standard deviation were
= +
(34)
determined by using (25). In all approaches, the mean value of
the endurance limit (se) of 74428904Pa and standard deviation and =
(se) of 18309786.41 were used.
From Table 2, we observe that higher the shaft diameter, the higher the reliability. And that the higher diameter is generated by considering the standard deviation in the analysis. Also note that without using (29) and (30), for the static, fatigue, and binary synthesis approach it is not possible to determine their designed reliaility. Now let generalize the proposed probabilistic method to use the lognormal and the Weibull distribution in the analysis. The generalization is as follows.
Table 2. Reliability of the shaft diameter determined by different approaches.
Here observe that this imply that 1) because the failure will be generated by fatigue, and not by the first cycle then the addressed Sm value is not being considered in the analysis, and therefore. 2) we are taking S 'a max , and S 'a min as the principal stresses 1 and 2 values to perform the Weibull analysis (if Sm is going to be considered, then the corresponding 1 and 2 values must be estimated using the Sm also) and 3) that the standard deviation value is being used as the amplitude stress value as plotted in Fig.16. Thus, following [24], the corresponding Weibull stress a and a parameters are given as
4
Approach
Average (sa)
S. Dev.
Diameter
R(t) (29-
30)
Static
142549382.8
28509871
0.0235
0.0222
Fatigue
36605852.26
7321172.5
0.037
0.9724
Synthesis
51853608.01
10370660
0.3302
0.8583
Proposed
25508690.25
5101706.7
0.0418
0.9950
Torsional Rigidity
25360503.11
5072095.1
0.4191
0.9951
Approach
Average (sa)
S. Dev.
Diameter
R(t) (29-
30)
Static
142549382.8
28509871
0.0235
0.0222
Fatigue
36605852.26
7321172.5
0.037
0.9724
Synthesis
51853608.01
10370660
0.3302
0.8583
Proposed
25508690.25
5101706.7
0.0418
0.9950
Torsional Rigidity
25360503.11
5072095.1
0.4191
0.9951
= (0.97161)(
(35)
)
= {( )() } (36)
In (35), the constant 0.971611 value was determined following the method given in sec.4.1 in [24], pg.236 (there the key formula is (48)). And µY is the mean value of the Y vector given by linearizing (33). Its linear form is given as
= ((1 ())) = [() ()] (37)
-
-
GENERALIZATION OF THE PROPOSED METHOD TO THE WEIBULL DISTRIBUTION
Since a random variable is said to follows a normal
Where F(Si)=1-R(Si) is the cumulated failure percentile estimated by using the median rank approach [25] given by
distribution only when its variation coefficient given as
=
(31)
() = ( 0.3)( + 4)
With n being estimated as [26]
(38)
is equal or lower than 0.10 (CV0.10) [5] pg.159, then because from the above analysis the C.V of Sa of
= 1
(())
(39)
CVa=5101706.7/25508690.25=0.20 and the C.V of Se of
CVe=0.24, are both higher than 0.10, then in this section the
In (39), R(S) is the desired reliability of the analysis. Here observe that although here R(S)=0.9535 was used to n be an
integer (n=21), any desired percentile can be used. Additionally, observe from (39), that because n only depends on R(S), then y is constant end for n=21 its value is y= 0.545624125.
On the other hand, by using the maximum and minimum Se values given by
= 25508690.25 5101738.5 = 20426951
And from (41)
= 74428904.97 + 18309786.41 = 92738691.37
= 74428904.97 18309786.41 = 56119118.56
= + (40)
and =
And by using the method given in the sec.4.1 of [20] in pg.236, the corresponding e and e parameters are determined as
4
Step 2. By using n=21 in (38) and then the F(ti) values in
(37) determine the Yi elements and its corresponding mean µY
value.
Note. Remember, that for n=21, the analysis is performed with a reliability of R(ti)=95.35% and that for n=21 the µY value is µY= 0.545624125. Hence, R(ti)=95.35% could be seen as
= (0.971611)(
(41)
)
the confidence interval used in quality. For example, since in Table 2 we used n=21, then as can be seen from (39) the
= {( )() } (42)
Therefore, by using the Weibull stress parameters of (35) and (36) or the Weibull strength parameters of (41), (42) and (38), the corresponding logarithm of the expected stress (or strength) values are given as
() = = + () (43)
And therefore, the expected stress (or strength) values are given as
= { } (44)
Finally, by using the addressed Weibull families W( , ),
analysis in Table 2 was performed with R(ti)=95.35%. Therefore, from Table 2 we say with reliability of 95.35 that the reliability of the shaft is of R(t)=99.50%.
Step 3. By using the maximum and minimum Sa and Se values of step 1, and the µY value from step 2 in (35) and (36), determine the corresponding stress Weibull family, and by using them in (41) and (42), determine the corresponding strength Weibull family.
The Weibull stress family is W(a=5.5399696, a=27580143.64Pa (4000.16164 lb/in2)). And the Weibull strength family is W(e=4.45324405, e=81545114.98Pa (11827.119 lb/in2)) (see Table 3).
a a
called Weibull stress family, and the W(e, e), called Weibull strength family in the general reliability stress/strength function given by
Step 4. By using the addressed Weibull parameters in (45b) if a e, or in (45c) if a = e, determine the designed reliability of the designed shaft.
(| , ) = () [ ()] (45a)
Since
, then by solving (45b) by using the Weibull++
0 a e
The corresponding Weibull/Weibull reliability stress/strength function is given by
(|,, )
software routine, the designed reliability is R(t)=0.992579.
As a conclusion we have that because the variation coefficient of S´a and Se are both higher than 0.10, then the shaft
1
1
reliability must be determined by using the Weibull
distribution. Hence the shafts reliability is of R(t)=0.992579,
= ( )
{(
) }[ ( )
{ (
) } ]
0
(45b)
and due to the torsional rigidity approach, the shafts diameter has to be of d=0.4191m (1.65 in).
Here, it is very important to notice that for a e, (45b) has not a close solution and thus, it must be solved by using a numerical method as the one given in [27], and that for a = e
= , the solution of (45b) [21] is given as
Now let show that the addressed Weibull families completely represents the normal parameters from which they were derived. The analysis is as follows.
B. Weibull and Normal Parameters Relationships
(|, , ) =
(45c)
The Weibull and normal parameters relationship are direct.
+
Therefore, based on the formulation from the above, the steps to determine the reliability of the designed shaft by using the Weibull distribution are as follws.
-
Steps of the proposed generalization form of the normal to the Weibull distribution
Step 1. Based on the mean and standard deviation of Sa and Se, from (34) and (40) determine their corresponding maximum and minimum expected values.
From (35)
= 25508690.25 + 5101738.5 = 30610428.75
Therefore, they can easily be addressed by using the expected stresses values defined in (43) and (44), and numerically given in Table 3.
-
From Table 3 we observe the normal averages values of (S´a)= 25508690.25Pa (3699.72 lb/in2) and (Se)= 74428904.97Pa (10,795lb/in2) of the S´a and Se variables, are given as the average values of columns S´a and Se. Therefore, the addressed Weibull families completely represent the normal average values.
Fig. 18. Input and output of the Weibull++ routine
Table 3. Weibull and Normal Data relationships
Stress Data W(e =4.45324405, e =11827.11901 lb-in2)
Strength Data W(a
=5.5399696, a
=4000.16164 lb-in2)
n
Eq.(40)
Yi
Eq.(38)
ln(S'a i )
Eq.(44)
S'a i
Eq.(45)
n
Eq.(40)
Yi
Eq.(38)
ln(Se i )
Eq.(44)
S'e i
Eq.(45)
1
-3.40348334
8.613879831
5507.575741
1
-3.40348334
7.679739504
2164.0559714
2
-2.49166198
8.818634241
6759.027118
2
-2.49166198
7.844329101
2551.2254736
3
-2.00346322
8.928261909
7542.145047
3
-2.003463219
7.932452104
2786.2506118
4
-1.66164593
9.005018828
8143.854136
4
-1.661645928
7.994152315
2963.5771517
5
-1.39439830
9.065030726
8647.544842
5
-1.394398299
8.042392224
3110.0442202
6
-1.17205365
9.114959418
9090.265709
6
-1.172053652
8.082526857
3237.4033649
7
-0.97938116
9.158225066
9492.194100
7
-0.97938116
8.117305476
3351.9765838
8
-0.80744734
9.196833734
9865.841677
8
-0.807447338
8.148340632
3457.6368110
9
-0.65049212
9.232078875
10219.765059
9
-0.650492124
8.176672054
3556.9974447
10
-0.50450882
9.264860215
10560.334314
10
-0.504508816
8.203022976
3651.9734647
11
-0.36651292
9.295847939
10892.698037
11
-0.366512921
8.227932119
3744.0834221
12
-0.23412230
9.325576967
11221.388989
12
-0.234122302
8.251829474
3834.6347711
13
-0.10528508
9.354508062
11550.777869
13
-0.105285078
8.275085418
3924.8578688
14
0.02192840
9.383074535
11885.501023
14
0.021928399
8.298048265
4016.0265213
15
0.14952577
9.411727213
12230.978252
15
0.149525769
8.321080408
4109.5976526
16
0.27984500
9.440991101
12594.192842
16
0.279845003
8.344603864
4207.4155917
17
0.41596210
9.47155693
12985.088370
17
0.415962097
8.369173872
4312.0722665
18
0.56250196
9.504463248
13419.487868
18
0.562501963
8.395625256
4427.6544636
19
0.72761583
9.541540458
13926.384115
19
0.727615827
8.425429366
4561.6029571
20
0.92931067
9.586832124
14571.635212
20
0.929310672
8.461836578
4730.7383938
21
1.22965981
9.654277145
15588.319227
21
1.22965981
8.516051521
4994.2949067
µy=
-0.545624125
µx= 9.2556276
µt= 10795.0000
µy=
-0.545624125
µx= 8.1956014
µt= 3699.7200
y=
1.175116938
x= 0.2638789
t= 2629.6350
y=
1.175116938
x= 0.2121161
t= 734.8660
+
Normal distribution
1
Fatigue Area
Mohr Analysis
2
Fig. 19. The normal standard deviation as the alternating stress and Mohr radio
-
Since the standard deviation (S´a)=5101738.05Pa (739.9444lb/in2) and (Se)=18309786.41Pa (2,655.51lb/in2) values of the S´a and Se variables where used as the alternating stress value (radio of the corresponding Mohr Circle) to determine the principal stress values (See Fig. 19) used to estimate a and e in (35) and (41), then from (14) of [24], by using data of Table 3, they are given as
corresponding log parameters always can be determined also. However, it is important to mention that because in the lognormal distribution the damage is cumulated in multiplicative form, then the lognormal distribution is generally used when a chemistry reaction is involved. Or also when the variation coefficient of the analyzed data tends to be the log- standard deviation x. Therefore, since the CVa= 0.27864493 and x=1462.48Pa (0.2121161 lb/in2) and CVe= 0.25379319
(, ) = ( )2 ( )( ) = ( )2 (
)2 (46a)
and xe=1819.38Pa (0.2638789 lb/in2), then the use of the
lognormal distribution to determine the reliability of the
() = ()2 ()() = ()2 ()2 (46b)
Numerically
( ) = (25508690.25)2 ({8.1956014})2
designed shaft is not recommended.
Even though, in the next section the reliability of the designed shaft using the normal, Weibull, lognormal, and the combination among them is given.
and
= 51017380.5
D. Reliability Comparison Among the Normal, Weibull and Log-Normal Distributions
() = (74428904.97)2 ({9.2556276})2
= 18309786.41
-
The general conclusion is that the Weibull distribution always can be used to model the normal behavior, and that the Weibull distribution should be used instead of the normal one, when the variation coefficient of the analyzed data is higher than 0.10.
-
Now since the Weibull and the lognormal distribution are both completely related each other [29], then let present the corresponding analysis to base on the Weibull parameters to determine the log-normal ones.
C. Weibull and Log-Normal Parameters Relationships
Here it is important to mention that because the Weibull distribution is generated by a non-homogeneous Poisson process [27], and the lognormal distribution is generated by a geometric Brownian motion [29], then one distribution should not be used instead of the other to determine the reliability of the analyzed element. However, because in practice the environment on which the element is performing its function, generally is lognormal [30], then in this section the determination of the log-normal parameters, directly from the Weibull analysis is given. The analysis is based on the (41) and
-
formulated in section 3.2 in [28]. Equations on which the Weibull and parameters and the log-mean x and the log- standard deviation x parameters are directly related as
Using the stress/strength formulation given in (46a) with the normal, Weibull and log-normal distributions, as well as with their combinations, the designed reliability of the shaft are given in Table 4. From Table 4, and as a conclusion we have the reliability of the shaft designed is the one given by the Weibull/Weibull approach of R(S)=0.992579. And that ones we know the mean and standard deviation of the stress and strength analyzed data; we can perform either of the above stress/strength reliability analysis. The final conclusions are as follows.
Table 4. Reliability indices for the normal, Weibull and Log-Normal approaches.
Approach
Stress Parameters
Strength Parameters
R(S)
index
Normal/Normal
=3699.72
=739.944
=10795
=2655.51
0.994881
Weibull/Weibull
=5.5399696
=4000.16164
=4.45324405
=11827.1190
0.992579
Log-Normal/Log- normal
x=8.1956014
x=0.2121161
x=9.2556276
x=0.2638789
0.999126
Normal/Weibull
=3699.72
=739.944
=4.45324405
=11827.1190
0.990113
Weibull/Normal
=5.5399696
=4000.16164
=10795
=2655.51
0.994979
Norma/Log-Normal
=3699.72
=739.944
x=9.2556276
x=0.2638789
0.999558
Log- Normal/Normal
x=8.1956014
x=0.2121161
=10795
=2655.51
0.994469
Log- Normal/Weibull
x=8.1956014
x=0.2121161
=4.45324405
=11827.1190
0.989532
Weibull/Log- Normal
=5.5399696
=4000.16164
x=9.2556276
x=0.2638789
0.999613
-
-
CONCLUSION
From the above methodologies the following conclusion
=
= { } = {
(47)
} (48)
were drawn.
-
The static analysis let us to efficiently determine the maximum and minimum stresses values on which the shafts diameter is determined.
Therefore, since y is constant (for n=21 its value is y=1.175116938), then given any Weibull parameters, the corresponding lognormal x and x parameters can directly be determined. From Table 3 for the S´a variable they are xa= 56506.68Pa (8.1956014 lb/in2), and x=1462.48Pa (0.2121161
lb/in2). And for the Se variable they are xe=63815.30Pa (9.2556276 lb-in2) and xe=1819.38Pa (0.2638789 lb/in2).
As a summary we have that due to the direct relationship between the Weibull and the lognormal distribution parameters given in (47) and (48), given any Weibull analysis the
-
The failure modes of a shaft can be either, by yielding when the mean stress Sm is higher than the yield material strength Sy, or from fatigue, generated by both the Sm and the alternating stress Sa values, or from plastic deformation given by the torsional forces.
-
The dynamic fatigue analysis let us to determine the shafts diameter by considering the endurance limit modified factors.
-
The binary synthesis approach let us to determine the shafts diameter by considering the endurance limit Se to be random, as well as to determine the mean Sm and maximum alternating stress S´a values at which the shaft will be subjected.
-
From section VII, we observe that the proposed method can be used to easily determine the reliability of the deigned shaft by using the Weibull distribution. And that this is made by simple using the addressed mean and standard deviation of S´a and Se as the maximum and minimum principal stresses values, used to determine the Weibull parameters of the stress and strength distributions.
-
The proposed method given in section VI, let us to determine the shafts diameter by considering that S´a and Se are both random. As well as to determine the designed reliability by using the selected stress/strength approach as in Table 4.
-
For variation coefficients higher than 0.10, the Weibull/Weibull stress/strength function defined in (44b) and (44c) is recommended.
-
Notice that a random variable follows a lognormal distribution only if it is generated by a geometric Browmian motion [29], or equivalently when the generated damage cannot be cumulated by using an additive damage model [31]. Or in practice, if the variation coefficient of the collected data tends to be the log-standard deviation.
-
Due to the variation coefficient of the stress and strength data were not lower than 0.10 nor close to the log- standard deviation, then the reliability of the designed shaft is the one given by the Weibull/Weibull stress/strength approach.
REFERENCES
-
S.M.O. Tavares, P.M.S.T. de Castro, A comparison of methodologies for fatigue analysis of shafts: DIN 743 vs. approaches based on Soderberg criterion, Cienc. e Tecnol. Dos Mater. 29 (2017) e76e81. doi:10.1016/j.ctmat.2016.06.014.
-
B.O. Schmid, S.R.; Hamrock, B. J.; Jacobson, Fundamentals of Machine Elements, 2014. doi:10.1016/B978-0-08-097759-1.00004-6.
-
A.J.B. Gonzalvez, E.G. Maravilla, J.J.R. GarcÃa, J.E.T. Caro, F.J.V. Chulia, Componentes de Maquinas Fatiga de Alto Ciclaje, 2nd ed., Pearson, Madrid, 2003.
-
D.B. Kececioglu, D. Ph, Robust Engineering With Emphasis On Mechanical Components & Structural Reliability VOLUME 1, 1st ed., Pennsylvania, 2003.
-
D.B. Kececioglu, D. Ph, Robust Engineering With Emphasis On Mechanical Components & Structural Reliability VOLUME 1, 1st ed., Pennsylvania, 2003.
-
D.S. Paolino, G. Chiandussi, G. Belingardi, Uncertainty in fatigue loading: Consequences on statistical evaluation of reliability in service, Probabilistic Eng. Mech. 33 (2013) 3846.
doi:10.1016/j.probengmech.2013.02.001.
-
G. Shi, X. Zhu, H. Ban, Material properties and partial factors for resistance of high-strength steels in China, J. Constr. Steel Res. 121 (2016) 6579. doi:10.1016/j.jcsr.2016.01.012.
-
Matweb, AISI 1020 Steel, normalized at 925°C (1700°F), air cooled, 50 mm (2 in.) round, (2003). http://www.matweb.com/search/DataSheet.aspx?MatGUID=4072670e 291540e5971a2cf398f06610.
-
Xiuzhi He, Xiaoqin Zhou, Zhen Xue, Yixuan Hou Qiang Liu and Rongqi Wang, (2019). Effects of gear eccentricity on time-varying mesh stiffness and dynamic behavior of a two-stage gear system, Journal of Mechanical Science and Technology 33 (3) (2019) 1019~1032
-
Baldor, General Purpose, (2018). https://www.baldor.com/brands/baldor-reliance/products/motors/ac- motors/general-purpose.
-
Ecatalog.weg.net, Weg Selección de Motores Eléctricos, (2018). http://ecatalog.weg.net/TEC_CAT/tech_motor_dat_web.asp.
-
B. Gear, Open Gearing, (2018). https://www.bostongear.com/products/open-gearing.
-
M.. Ivanov, Elementos de Maquinas, in: Elem. Maquinas, Moscu, 1984.
-
R.L. Mott, Applied strength of materials, 6th ed., CRC Press, New York, 2002.
-
M. L., Machine elements in mechanical design, 4th ed., Pearson, New Jersey, 1987. doi:10.1016/0301-679X(87)90097-1.
-
O.A. Zambrano, J.J. Coronado, S.A. RodrÃguez, Failure analysis of a bridge crane shaft, Case Stud. Eng. Fail. Anal. 2 (2014) 2532. doi:10.1016/j.csefa.2013.12.002.
-
H.Y. Ahmad, D. Bonnieman, Fundamental Recommendations for the Design Configuration of Rotor Shafts for Use in Electric Motors and Generators, Procedia Eng. 160 (2016) 3744.
doi:10.1016/j.proeng.2016.08.860.
-
A.C. Ugural, Mechanical design an integrated approach.pdf, (2004). doi:0 07 242155-x.
-
C. Moolwan, S. Netpu, Failure Analysis of a Two High Gearbox Shaft, Procedia – Soc. Behav. Sci. 88 (2013) 154163.
doi:10.1016/j.sbspro.2013.08.491.
-
F.M. Burdekin, General principles of the use of safety factors in design and assessment, Eng. Fail. Anal. 14 (2007) 420433.
doi:10.1016/j.engfailanal.2005.08.007.
-
Chen Huitao, Fan Junkai, Jing Shuangxi and Wang Xianhui, (2019). Probabilistic design optimization of wind turbine gear transmission system based on dynamic reliability. Journal of Mechanical Science and Technology 33 (2) (2019) 579~589
-
Hee Yang Go, Si-Il Sung and Yong Soo Kim, (2018). Prediction of system reliability using failure types of components based on Weibull lifetime distribution. Journal of Mechanical Science and Technology 32 (6) (2018) 2463~2471
-
Piña-Monarrez, M. R. Weibull Stress Distribution for Static Mechanical Stress and its Stress/strength Analysis. Qual Reliab Engng Int. 2018;34:229244. DOI:10.1002/qre.2251.
-
Mischke C R (1979). A distribution-independent plotting rule for ordered failures. Journal of Mechanical Design; 104: 593-597. DOI: 10.1115/1.3256391.
-
PiñaMonarrez MR, RamosLópez ML, AlvaradoIniesta A, Molina Arredondo RD (2016). Robust sample size for Weibull demonstration test plan. DYNA.; 83:5257.
-
Rinne H. Distribution the Weibull distribution a handbook. CRC PRESS; http: //dx.doi.org/10.1201/9781420087444.
-
OrtizYañez JF., PiñaMonarrez MR. Discrimination between the Weibull and the lognormal distributions by using multiple linear regression. DYNA.; 85 (205):918, june, 2018. DOI: http://doi.org/10.15446/dyna.v85n205.66658
-
Marathe RR, Ryan SM. On the validity of the geometric Brownian motion assumption. The Engineering Economist 2005; 50:159192. doi:10.1080/00137910590949904.
-
ReliaSoft. Considering use a stress distribution in a quantitative accelerated life testing analysis. Retrieved from http://www.weibull.com/hotwire/issue172/hottopics172.htm [04 Apr 2019]
-
PiñaMonarrez MR, OrtizYañez JF. Weibull and lognormal Taguchi analysis using multiple linear regression. Reliab Eng Syst Safe. 2015;144:244253. https://doi.org/10.1016/j.ress.2015.08.004
-
Nakagawa T. Shock and Damage Models in Reliability Theory. SpringerVerlag: London, 2007. DOI: https://doi.org/10.1007/9781 846284427
N. Yu, Q. Li, Failure theory via the concept of material configurational forces associated with the M-integral, Int. J. Solids Struct. 50 (2013) 43204332. doi:10.1016/j.ijsolstr.2013.09.001.