
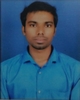
- Open Access
- Authors : Mohammed Imran , Dr. K. Hemalatha
- Paper ID : IJERTV10IS060190
- Volume & Issue : Volume 10, Issue 06 (June 2021)
- Published (First Online): 21-06-2021
- ISSN (Online) : 2278-0181
- Publisher Name : IJERT
- License:
This work is licensed under a Creative Commons Attribution 4.0 International License
Numerical Investigation And Simulation of Impact Energy Absorption by Materials in Ballstic
Mohammed Imran
Mechanical Engineering Department (M.E) Muffakhamjah College Of Engineering And Technology, Hyderabad, India
Dr. K. Hemalatha, Associate Professor Mechanical Engineering Department (M.E)
Muffakhamjah College Of Engineering And Technology, Hyderabad, India
Abstract This report treats terminal ballistics which is the branch of the ballistic science concerning the mechanics of impact. The purpose of this project is to determine the parameters governing projectile failure when impact against a target is achieved and energy loss of projectile in each layer of composite are observed. In the Simulation approach, a model has been derived capable of determining the amount of deformation in the projectile after impact, energy summary in each layer An Simulation method of obtaining the resistance pressure, by which the target resists penetration, and a method of determining the energy loss project tile material are also implemented. A numerical section explaining the main factors and approaches in hydro code and dynamic modeling is also devised along with simulations of projectile impact.
Keywords Ballistics, Projectile and target, Penetration Depth, Projectile failure
- INTRODUCTION
In ballistics the protection from the targeted projectile requires loss of energy or absorption of energy of projectile by protected material. Today modern projectiles are more advanced, powerful, high velocity and high energy objects which can damage the targeted object in seconds. To protect the object from the powerful projectile we require strong and highly advanced material on the surface which can cover the whole body of the object. Modern defense system associated with advanced technology in material science which can be used to selection of materials for design the system.
Material selection plays vital role in the design of any system. Material selection is depend on the type of the object, where can be used and how it can be used. Surrounding systems around the object effect on the object material and it can be leads decreases the life span the object. In Advanced systems most of the materials used are combination materials like alloys and composites. Materials posses different properties based on the conditions it can also effect the system.
In modern system considering all the conditions we require high density, fracture toughness, high stiffness, low density and highly ductile material. Aluminum foam and Kevlar are tested for this purpose.
Table1. Properties of materials
S. No
Layers of armour plate Density (Kg/m3) Youngs modulus (GPa ) Poisson ratio Yield stress (GPa Specific heat (J/Kg k) 1 Kevlar 1440 91 0.3 217 710 2 Aluminiu m foam 700 100 0.33 140 950 Kevlar poses good absorption of energy property, chemically inactive, low thermal conductivity properties. It has high resistance to stop object and it can leads loss of energy in the object which may decrease the damage of system. Aluminum foam is highly ductile and low weight. It can decreases velocity of the object. These two materials are used in ballistic protection system as hybrid composite.
Fig1.Alumuniumfoam
- MATERIALS AND METHODS
Materials requires for system is the important decision for the design. Materials for ballistics requires highly strength and hard. Composites and alloys are widely used for design process. For strong materials can posses high density, low weight, high hardness etc. energy absorption of materials require high density, fracture toughness and strength. Fracture toughness is the important property for absorption of energy. Fracture toughness is determined by impact test.
. Fig 2.kevlar layer
- NUMERICAL CACULATION
Energy absorption by the layer = (fracture toughness of the material x area of penetration by bullet) / (thickness of the layer penetrated by the bullet)
E = F.T x A x L
t
F = Fracture toughness of the layer Ea = Absorption energy by layer
A = Area of cross section of bullet
L =Distance between target and observer t = Thickness of layer
Total energy = Absorption energy by the Kevlar .
+ remaining energy
Remaining energy = Force on the second layer Absorption energy by the layer = kinetic energy absorbed
Absorption energy = ½ M (Vi² Vr²) Vr = Residual velocity of projectile Vi = Intial velocity of projectile
Energy at the present at the surface layer by bullet.
. = ½ MVe
M = Mass of the projectile
Ve= velocity present at the surface . .
In numerical calculation energies and velocities are determined. Energy absorption in the material is appoximated by the given formula. The mass of the bullet taken as 10 grams. The velocity attain by the bullet from the gun barrel taken as 854m/s.
The residual velocity of the bullet calculated by the theoretical formulation. Thickness of the layers of material is varied and absorption energies are calculated. The distance between the targeted object and gun barrel taken as one metre and it is taken as length in the formula. Fracture toughness is the material property used in the formula and other values are depends on geometry and velocity.
Fig 4.2 mm thickness Energy absorption
Fig 5.4 mm thickness Energy absorption
- DESIGN AND SIMULATION
Kevlar layer:
Fig 3. kevlar layer meshing
Fig 6.6 mm thickness Energy absorption
Fig 7.8 mm thickness Energy absorption
Fig 8.10 mm thickness Energy absorption
Aluminum foam:
Fig 9.2 mm thickness
Fig 10.30 mm thickness Energy absorption
Fig 11.28 mm thickness Energy absorption
Fig 12.26 mm thickness Energy absorption
Fig 13.24 mm thickness Energy absorption
Fig 14.22 mm thickness Energy absorption
Fig 15.15 mm thickness Energy absorption
- RESULTS AND DISCUSION
Energy absorption of material determined by numerical investigation and simulation methods. In numerical method fracture toughness is the important property for calculations. Energy absorption is varies by thickness of layer and increasing the layer thickness increases the loss of energy of the projectile. In numerical and simulation methods we also calculate velocities of the projectile which is used calculate energies.
For simulation method we are used LS AutoDyna in ansys workbench. Initial conditions, boundary conditions plat predominant role to get exact values.
Energy absorption of material increases the thickness of the material but it leads increases the thickness and weight of the system. Considering the conditions we optimize the thickness and weight, it leads increases the efficiency of the system performance.
Table2. Kevlar energy absorption at various thickness
/tr>
S no
Layer thickness (mm) Energy loss (Joules) Velocity reduction(m/s) 1 2 251 29.3 2 4 370 45.1 3 6 585 72.3 4 8 710 88.6 5 10 861 109.2 6 15 945 120.5 Fig 16. Thickness vs Velocity
Table 3. Aluminum foam energy absorption at various thickness
S no Layer thickness (mm) Energy loss (Joules) Velocity reduction(m/s) 1 30 469 306.3 2 28 442 297.1 3 26 418 289.2 4 24 386 278.5 5 22 352 265.2 6 15 258 227.6 Fig 18. Thickness vs Velocity
Fig 19. Thickness vs Energy absorption
- CONCLUSION
This is aims towards better efficiency of material layers and also identifies the optimum thickness of layers which also effect on weight reduction of ballastic armour. Efficiency of performance is maximum at optimal conditions. Kevlar and aluminum foam are the materials used for ballistic protection system. High density, stiffness, elastic strength, high ductility, fracture toughness are the properties considering for design process.
Fig 17. Thickness vs Energy absorption
Considering all the results of the materials we can conclude that aluminum foam, Kevlar are suitable ballstic protection system. They can resist the high projectile efficiently.
REFERENCE
D. Hotza.Research Article Alumina-Based Ceramics for Armour
Application: Mechanical Characterization and Ballistic Testing(2014
absorption efciency of each layer in ballistic armour panel for applications in hybrid design , University of Manchester,
Manchester, UK, 19 December 2016
Piercing Projectile , Defence Science Journal, Vol. 64, No.5,
September 2014, pp. 477-483, DOI : 10.14429/dsj.64.6745 2014.
[1] | Armand Lewis, Mattapoisett, MA (US); Yong K. Kim, North | [4] | M. V. Silva, D. Stainer, H. A. Al-Qureshi,O. R. K. Montedo, and |
Dartmouth, PANEL FOR ABSORBING MECHANICAL | |||
IMPACT ENERGY AND METHOD OF MANUFACTURING, Pub. No.: US 2016/0368240A1, US 201603.68240A1 Dec. 22, | |||
2016 | [5] | Yanfei Yanga,b, Xiaogang Chenb Investigation on energy | |
[2] | K.L. Edwards, C.A. Abel, M.F. Ashby, Optimal selection of composite materials in mechanical engineering design Engineering | ||
Design Centre, University of Cambridge, Department of | |||
[3] | Engineering, Trumpington Street, Cambridge, CB2 1PZ,
M.M. Shokrieh , G.H. Javadpour, Penetration analysis of a |
[6] | S.G. Savio, V.Madhu, and A.K. Gogia, Ballistic Performance of Alumina and Zirconium toughened Alumina Against 7.62 Armour |
projectile in ceramic composite armour Composites Research | |||
Laboratory, Department of Mechanical Engineering, Iran University of Science and Technology, Narmak, 16844 Tehran, | |||
Iran, 30 January 2007 |