
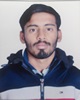
- Open Access
- Authors : Kunal Kalal , Saubhik Jaiswal , Darshan Joshi , Malay Vagadiya, Dr. Sweta Shah
- Paper ID : IJERTV9IS050308
- Volume & Issue : Volume 09, Issue 05 (May 2020)
- Published (First Online): 19-05-2020
- ISSN (Online) : 2278-0181
- Publisher Name : IJERT
- License:
This work is licensed under a Creative Commons Attribution 4.0 International License
Modern Technique for APFC of Single Phase Systems
1 Dr. Sweta Shah, 2 Saubhik Jaiswal, 3 Kunal Kalal, 4 Darshan Joshi, 5 Malay Vagadiya
1 Assistant Professor Electrical Engineering, 2345 B.Tech Student
12345 IITE, Indus University, Rancharda, Ahmedabad-382115
Abstract-: This paper proposed automatic power factor correction technique for industrial applications. Power factor correction is essential for power quality, energy efficiency and electrical costs. It is also done for stability and economical operation of the system. The goal of power factor correction is to have safe, efficient and trustful power system.
-
INTRODUCTION
The power factor is described in such a way that how efficient the electrical power is used. Power factor is the ratio of Real power (kW) to apparent power (kVA). As the circuit is purely resistive and there are no inductive loads than the power factor will be unity but it is not possible practically. Normally electrical power system operates in their steady state but when the industries consume power the electrical power system get disturbed and which effects whole system. The one factor majorly gets disturbed is power factor for which the calculation is to be done and need to improve the power factor because it's imbalances the whole system and the industries are getting fine for not maintaining the power factor.
Installing power factor correction will affect in stabilization, heat, voltage drop, power quality, life expectancy, and transformer and distribution losses, supply capacity this all thing will come in effect and helps to improve the power factor by placing the power factor correction unit.
-
THEORY
The method will be mainly used in industries because large machines are used there and because of that power may get disturbed so to control and make system reliable will be using this method as explained.
-
There are different methods to improve the power factor are
-
Capacitor banks
-
Synchronous Condensers
-
Phase Advancers
-
Conventional methods
-
Static Capacitor: For power factor improvement the static capacitors are placed in industries which generally connected in parallel. The industries and system loads are inductive so that they take inductive current which reduced the power factor.
The capacitors connected in parallel provide leading current which almost balances the lagging inductive component which effects in the improvement of power factor.
-
Synchronous Condenser: To improve the power factor we use a synchronous motor, whose shaft is running freely without any load. The purpose of this motor is to improve power factor of the voltage grid. It can absorb or generate reactive power by varying the excitation of its field winding. In such case it absorbs reactive power and injects reactive power.
It can compensate either a lagging or leading power factor by supplying or absorbing reactive power to the line voltage regulation.
. Phase Advancer: For improvement of the power factor of an induction motor, we use an ac exciter to the rotor circuit. The main reason of the low power factor of an induction motor is due to the fact that its stator winding draws more current. Phase advancer is used to improve reactive power, or we can say to improve power factor of the induction motor. As the stator winding of induction motor takes lagging current 90 degrees out of the phase with voltage, thats the reason of low power factor of an induction motor.
-
-
Proposed method
Firstly consider a system having n number of loads, that n number of loads consumes n kw power. To know the system how it is working we have to calculate power factor for that. Now for calculating power factor there are different methods, but here details are provided about the specific method to calculate pf. Hence, to calculate pf readings taken from the load side because the input voltage will not be varied because there is no disturbance but at the same time because of the load the system will get disturbed so readings will be taken from that side.
Generally the readings are taken directly and calculation is done but here sensors are used to take readings because they are rapid and can take quick decisions. So how it works is explained in the flowchart below
Here first of all there are two sensors which came into effect
Sensors:
Sensors are basically a device which can sense or identify and react to certain types of electrical or some optical signals. Implementation of voltage and current sensor techniques has become an excellent choice to the conventional current and voltage measurement methods.
Advantages of sensors:
-
Small in weight and size
-
Degree of accuracy is very high
-
Wide dynamic range
-
Eco-friendly
-
It is non-saturable
As per the circuit coding is done and the electrical parameters like voltage, current, power factor, frequency are sense by the sensing circuit. In the coding voltage and current value are set by us. If the measured current and voltage value are equal to the set voltage and current value then it will sense this value every time interval but if they are not equal then the sensing circuit sense another electrical parameter which is power factor. In this coding we set the power factor at 0.95 now if the practical measure value of the power factor is less than 0.95 the signal goes to the microprocessor and microprocessor select the appropriate capacitor bank to switch on but if the power factor is equal to or more than 0.95 than there is no need of switch on any capacitor bank.
The signals provided to the microcontrollers, and they convert the signals and provide the information to the relays. The relays are associated with the microcontrollers. Further these relays are attached to the capacitor banks and according to the calculation and need of the system, the relays will select the bank
in such a way that it will compensate and fulfil the power factor.
-
-
-
SIMULATION AND RESULT :
For the simulation coding is done in aurdino then the current and voltage sensor circuit is firstly designed in proteus software and then the same code is given in the proteus which have inbuilt aurdino, so after that we have checked the result.
-
Software based circuit designed in proteus
After that the same circuit is designed for current and voltage sensing and one aurdino is also kept and the same code is installed in that aurdino, after connecting the load (motor). Practically performing the actual circuit and provides you an information about that.
-
Actual Circuit
-
Result
So this was the result and it almost matched the result performed on software. The results are check thrice and verified so that there are no mistakes in coding and also practical circuit behaves as similar as the software based circuit.
-
CONCLUSION AND FUTURE SCOPE:
The method used is a new technique which will have a great impact and may used all the industries in near future. This technique is the energy saving, efficient and have a great precision to an extent. The main advantage of this method it will improve your power factor and does not give a chance to have a penalty on pf. This is fully automatic process and even the life expectancy of machines will increase because the losses will be deducted.
REFRENCES:
-
Switchgear protection nd power system, Sunil S Rao, Khanna publishers.
-
Power System Protection and Switchgear, Bhuvanesh A Oza, Nirmal Kumar C Nair,Rashesh P Mehta, Vijay H Makwana, Tata McGraw Hill Education Private Limited.
-
"POWER FACTOR CORRECTION." www.nhp.com.au. NHP Catalogue- PFC-SFC, Nov. 2007. Web. 14 July 2016.
-
"Power Factor Correction: A Guide for the Plant Engineer." www.eaton.com/. Eaton Corporation, Aug. 2014. Web. 14 July 2016.
-
"Hobbyist.co.nz." Interfacing the Relay Modules to the Arduino [http://www.hobbyist.co.nz/interfacing-relay-modules-to- arduino]. N.p., n.d. Web. 14 July 2016.
-
"Design and Implementation of Microcontroller-Based Controlling of Power Factor Using Capacitor Banks with Load Monitoring." Ali, Murad. Global Journal of Researches in Engineering Electrical and Electronics Engineering Version 1.0
13.2 (2013): n. page. Web. Online ISSN: 2249-4596 & Print ISSN: 0975-5861