
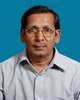
- Open Access
- Authors : S. K. Lakshmana Moorthy, B. Prakash
- Paper ID : IJERTV9IS050396
- Volume & Issue : Volume 09, Issue 05 (May 2020)
- Published (First Online): 19-05-2020
- ISSN (Online) : 2278-0181
- Publisher Name : IJERT
- License:
This work is licensed under a Creative Commons Attribution 4.0 International License
Design and Analysis of Crane Hooks of Different Cross Sections Made of Hardened-Tempered Alloy Steel AISI 6150 and AISI 4140
S. K. Lakshmana Moorthy
Associate Professor,
Dept of Mechanical Engineering,
K. Ramakrishnan College of Engineering, Tiruchirapalli, India.
B. Prakash
Assistant Professor,
Dept of Mechanical Engineering,
-
Ramakrishnan College of Engineering, Tiruchirapalli, India.
AbstractA crane hook is a part of a hoist or a crane for the purpose of lifting and holding to transport from one place to another. A crane hook is always subjected to concentrated load at its curvy inner surface, where maximum stresses are developed. This curvy inner surface is considered critical where failure can occur. To study the stress, strain and deformation of crane hook in its loaded condition, a solid model of crane hook is developed with the help of SOLIDWORKS software. Stress distribution, Strain distribution and total deformation in 3D model of crane hook is obtained using ANSYS 15.0 software by providing loading condition, supports and necessary material properties. In this present work, the obtained stresses are compared with different models to reduce the stress formed in hook by changing the shape of cross section of hook. High strength material is selected and heat treated to have enhanced properties and optimized results. From the analysis, it can be concluded that trapezoidal shaped crane hook made of hardened and tempered alloy steel is well suitable for crane hook.
KeywordsCrane hook, design, analysis, different cross sections, optimization.
-
INTRODUCTION
Crane hooks are applied in industries for picking and transporting heavy loads [1-3]. Crane hooks are designed to be connected usually to rope wound over a pulley controlled by electric motor. Crane hooks undergo rigorous stress at the time of loading. Usually loading is applied at the bottom most inner curve of the hook that distributes the induced stress to the remaining section of the hook. In this work, analysis is done by varying the shape of cross section of hook with constant static load in it. Firstly 3D hook model is prepared using SOLIDWORKS [1, 3, 4]; secondly, the static analysis on the hook is preceded by FEM software ANSYS 15.0 [1-7]. From the view point of safety, the stress induced in crane hook must be analyzed in order to reduce failure of hook [4]. Hooks are available in different cross section of area [6]. In this work, three cross sections are used to design and analyse hooks, namely, circular cross section, rectangular cross section and trapezoidal cross section. These three models can be compared using the stress developed for a common loading applied on it. The hook can be supported at the top most point and the load can be applied at the bottom most inner curvature point of the hook [1-3].
In general, composition of material, shape of cross section and moment of inertia are key design parameters that affect the strength and load carrying capacity of crane hook [2, 6]. In this work the discussion of the results of ANSYS stresses and comparing it with different shapes and materials are carried out.
-
SELECTION OF MATERIAL
Some common materials used to make the crane hook are Carbon steel, Alloy steels, Wrought iron, HSLA (High Speed Low Alloy), Chromium steel, Stainless steel and Gray cast iron [3, 6]. The material selected should have very high strength, hardness and some other mechanical properties to meet load requirements such as work hardening. In this work, the materials selected for design and analysis are spring grade Chromium-Vanadium alloy steel AISI 6150 and Chrome alloy AISI 4140. Hardened-tempered AISI 6150 is used to attain optimized material properties [8, 9]. Hardness of materials is found to be HRC 44 before hardening, whereas it is HRC 63 after hardening by heating material to 850oC and quenching in oil bath. Besides being strong, both hardened and tempered AISI 6150 steel and AISI 4140 steel are resistant to atmospheric corrosion and are better suited to welding than carbon steels [9, 10].
TABLE 1. COMPOSITION OF HARDENED-TEMPERED AISI 6150 AND AISI 4140 [8, 9, 10]
Composition (in mass %)
Hardened- tempered AISI 6150
Hardened- tempered AISI 4140
Carbon
0.50
0.42
Silicon
0.25
0.30
Manganese
0.64
0.90
Chromium
1.01
1.00
Nickel
0.18
—–
Molybdenum
0.29
0.20
Sulphur
0.03
0.04
Phosphorous
0.03
0.03
Vanadium
0.19
—–
Chromium improves corrosion resistance and hardenability [11]. Manganese gives work hardening property [11]. Vanadium improves wear resistance properties [11]. Molybdenum helps in deep and thorough hardening, increases hot hardness and creep strength [11]. Silicon improves oxidation resistance and hardness [11].
TABLE 2. PROPERTIES OF HARDENED-TEMPERED AISI 6150 AND AISI 4140 [8, 9, 10]
Property (Unit)
Hardened- tempered AISI 6150
Hardened-tempered AISI 4140
Ultimate strength (MPa)
1200
1080
Yield strength (MPa)
1160
990
Hardness (HRC)
63
54
Density (kg/m3)
7830
7850
Poissons ratio
0.29
0.29
Youngs Modulus (GPa)
190
190
Shear Modulus (GPa)
73
73
Melting point (oC)
1460
1416
-
MODELING OF CRANE HOOK
A 2D drawing for designing of the crane hook is performed as per the standards of ASME [4, 5]. The 3D model is developed in SOLIDWORKS based on the shape and dimensions represented in the 2D drawing.
SOLIDWORKS modelling of the crane hook of circular cross section, rectangular cross section and the trapezoidal cross section are developed separately as per the dimensions represented in the 2D drawing. Circular cross section is of 50mm diameter at critical loading section. Rectangular cross section is of 50mm×50mm at critical loading section. Trapezoidal cross section is of 68mm×40mm at critical loading section. Since three different sectional shapes possess different cross sectional area and moment of inertia, stress developed, strain, and deformation in the crane hook can be different.
Fig. 1. 2D sketch of hook with circular cross section (All dimensions are in mm).
Fig. 2. 2D sketch of hook with (a) rectangular cross section and (b) trapezoidal cross section (All dimensions are in mm).
Fig. 3. 3D model of Crane Hook made of (a) circular (b) rectangular and (c) trapezoidal cross section.
-
ANALYSIS OF CRANE HOOK
The developed 3D model is imported into the ANSYS
15.0 software [1-6]. A load of 8 tonnes is applied on the hook by firmly holding the head portion. The physical and mechanical properties for the analysis are supplied as per the values in th table 1. The stress value, equivalent strain value and total deformation of the crane hook are obtained for the three different cross sections separately.
By considering static loading, a factor of safety of 3 on yield strength can be incorporated [2, 4]. The allowable stress
value in the crane hook is calculated as ratio of yield strength to factor of safety [2].
-
ANSYS analysis for circular shape
Fig. 4. Equivalent stress in hook of circular cross section in (a) AISI 6150 (b) AISI 4140.
Fig. 5. Equivalent strain in hook of circular cross section in (a) AISI 6150 (b) AISI 4140.
Fig. 6. Total deformation in hook of circular cross section in (a) AISI 6150
-
AISI 4140.
-
-
ANSYS analysis for the rectangular shape
Fig. 7. Equivalent stress in hook of rectangular cross section in (a) AISI 6150
-
AISI 4140.
Fig. 8. Equivalent strain in hook of rectangular cross section in (a) AISI 6150
(b) AISI 4140.
Fig. 9. Total deformation in hook of rectangular cross section in (a) AISI 6150 (b) AISI 4140.
-
-
ANSYS analysis for the trapezoidal shape
Fig. 10. Equivalent stress in hook of trapezoidal cross section in (a) AISI 6150 (b) AISI 4140.
Fig. 11. Equivalent strain in hook of trapezoidal cross section in (a) AISI 6150 (b) AISI 4140.
Fig. 12. Total deformation in hook of trapezoidal cross section in (a) AISI 6150 (b) AISI 4140.
-
-
RESULTS AND DISCUSSION
From the results obtained from ANSYS, in case of hook made of AISI 6150, the trapezoidal shape develops relatively low stresses, though the stresses developed in the crane hook with all three shapes fall within allowable limit. In case of hook made of AISI 4140, the trapezoidal shape develops stress within allowable limit, but circular and rectangular cross sections develop stresses beyond allowable stress. Equivalent total strain and deformation in the hook is relatively lesser in the trapezoidal cross section compared to other cross section for both materials. It is observed that moment of inertia of trapezoidal section is higher than other section so that it develops minimum stress for the same load conditions. Hence the trapezoidal shape is selected as the best cross sectional shape for the design of crane hook [6]. Also the crane hook is capable of withstanding high loads because of its optimized mechanical properties by means of hardening and tempering [11]. Also crane hook exhibits excellent load capabilities due to enhanced properties and improved strength to weight ratio. Hence AISI 6150 trapezoidal crane hook is capable of withstanding more loads compared to crane hooks of the conventional materials and conventional shapes.
TABLE 3. RESULTS FROM THE ANSYS ANALYSIS
Shape of cross section
Material
ANSYS results
Allowable stress =
{Yield strength/3} (MPa)
Elastic strain (mm/mm)
Total deformation (mm)
Stress (MPa)
Circular
AISI 6150
0.0019052
1.3752
377.45
386
AISI 4140
0.0021637
1.3992
431.82
330
Rectangular
AISI 6150
0.0018272
1.5357
363.80
386
AISI 4140
0.0018565
1.5604
369.64
330
Trapezoidal
AISI 6150
0.0017888
0.71438
317.78
386
AISI 4140
0.0018175
0.72584
322.88
330
-
CONCLUSION
-
A Crane hook has been designed and analyzed using circular, rectangular and trapezoidal cross sections and optimized by enhancing material properties by means of oil quench hardening and tempering the selected AISI 6150 alloy steel material. Thus crane hook of trapezoidal cross section has been effectively designed with improved efficiency, strength to weight ratio, load carrying capacity and reliability.
REFERENCES
-
G Bhagyaraj, K Suryaprakash, K Subba Rao (2017) Crane Hook Design and Analysis. International Research Journal of Engineering and Technology 4(9):61-65.
-
E. Sai Krishna, Dr. S. Suresh kumar (2018) Design and analysis of crane hook with different materials. International Journal of Mechanical Engineering and Technology 9(4):786791.
-
Dr. P.Ravikanth Raju, Somagani Upendar (2018) Design and analysis of a crane hook. International Journal of Current Engineering and Scientific Research 5(4):1015.
-
Vikky Kumhar, Pradip Kumar Talapatra and Novel Kumar Sahu (2015) Design and analysis of crane hook trapezoidal cross-section using finite
element analysis. VSRD International Journal of Mechanical, Civil, Automobile and Production Engineering 5(5):89-94.
-
M.Amareswari Reddy, M.N.V. Krishnaveni, B.Nagaraju , M. Raja Roy (2015) Static Analysis of Crane Hook with I- Section and T- Section using Ansys. International Journal of Engineering Trends and Technology 26(2):72-77.
-
Abhijit Devaraj (2015) Design of a Crane Hook of Different Materials and Stress Analysis Using ANSYS Workbench. International Journal for Research in Applied Science & Engineering Technology 3(7):310- 314.
-
Stalin B., Ravichandran M., Ramesh Kannan C., Sathiya Moorthi K. (2019) Design and Analysis of Stringer on the Chassis Frame in Load Carrying Vehicle. In: Hiremath S., Shanmugam N., Bapu B. (eds) Advances in Manufacturing Technology. Lecture Notes in Mechanical Engineering. Springer, Singapore. pp.219-225
-
D.Rajamani 1, A.Tamilarasan (2005) Finite Element Machining Simulation of AISI6150 Steel. International Journal of Innovative Research in Science, Engineering and Technology 4(8):7959-7966
-
Material Properties of Quenched and Tempered AISI 6150 Steel. https://www.makeitfrom.com/material-properties/Quenched-and-
Tempered-6150-Chromium-Vanadium-Steel
-
Material Properties of Quenched and Tempered AISI 4140 Steel. https://www.makeitfrom.com/material-properties/Quenched-and-
Tempered-4140-Cr-Mo-Steel
-
S.K. Lakshmana moorthy (2014) Engineering Materials and Metallurgy. Nandhini Publications, Tiruchirapalli, India. First Edition. ISBN:9788192549347