
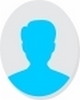
- Open Access
- Authors : W. A. Akpan , O. W. Obot , E. M. Ekpo , E. J. Awaka-Ama, E. O. Usungurua
- Paper ID : IJERTV11IS090122
- Volume & Issue : Volume 11, Issue 09 (September 2022)
- Published (First Online): 01-10-2022
- ISSN (Online) : 2278-0181
- Publisher Name : IJERT
- License:
This work is licensed under a Creative Commons Attribution 4.0 International License
Modeling of Cumulative Damage Degradation and Random Shocks for a Constant- Interval Preventive Maintenance System
W. A. Akpan1 O. W. Obot2; E. M. Ekpo3; E. J. Awaka-Ama4 ; E. O. Usungurua 5
1,2,3,4 5.Mechanical and Aerospace Engineering Department, University of Uyo, Nigeria.
Abstract:- This research work presents the modeling of total expected maintenance cost of a system subjected to cumulative deterioration and random shocks under constant interval preventive maintenance (PM). An accelerated life testing methodology was used to study the functional deterioration of a centrifugal pump subjected to cumulative damage and random shocks situations. A constant interval policy was used to evaluate the optimum time interval that will reduce the total expected cost of the unit. Results obtained from the study shows that, random shocks raises the number of failures and therefore, reduces the reliability of the system. The total expected cost ranges from two thousand naira only (N2000.00) to sixteen thousand naira only (N16,000.00), depending on the shock and shocks duration. The model and method adopted are very useful and thus recommended as a tool for studying similar mechanical systems.
Key words: Modeling, constant- interval, degradation, cumulative damage, random shocks.
I INTRODUCTION
Modeling is an abstract mathematical representation of the behavior of a system. It postulates how systems will behave in a particular situation. Deterioration can be described as a kind of reduction in value. A deteriorating state depicts state of a system in which the system performs only limited function, which are lower than the specified functions [1].Degraded system will produce excessive noise and vibration [2]. Failure is the end of performance of the functions of the system. Failure can be reduced by preventive maintenance. Preventive maintenance is the weaving together of technical and engineering actions to keep an item or system or bring it back to a functional state, whereby it can perform the needed functions. Failure of an asset terminates reliability, thereby leading to costs or unreliability [3]. In summary, maintenance is all the actions which have the objective of returning a system to another state- a functional and acceptable state [4]. Machines failures are normally caused by poor maintenance practice and inability to predict future problems during usage [5].
[6] described machine deterioration as the irrecoverable accumulation of damage in the system over its useful life that leads to its breakdown in a later time. There exist many stages of deterioration which make the efficiency of the machine to decrease, this type of breakdown is known as soft failure. Hard failure occurs without warning.Note that in spite of planned preventive maintenance measure, failures are bound to occur but they can be reduced to a minimum extent [7].A degradation model usually gives two relevant information, such as deterioration processes of the indicators and the linkage between the indicators and the failure events [8].
Deterioration models can be divided into two groups: normal degradation and accelerated degradation models. Normal degradation models are employed to determine the degradation applied at normal operating conditions. Accelerated degradation models make use of data gotten under stressed conditions. Normal degradation come with stress and without stress factors [9]. An example without stress factor is the general degradation path models and Markov models. An example of stressed factor is the accumulative damage [10].
Continuous- time model is a stochastic process that allows the index values to take a continuous set of values, such as Weiner processes [11].
. [12] studied the optimal reliability maintenance policy for a system subject to cumulative shock model [13]
investigated an optimal maintenance practice for system subject to random shocks and showed by a .
In this research, constant interval preventive replacement policy was modeled and data generated under accelerated system
failure condition and applied on the mode for verification.
II METHODLOGY
The items that were used in the research study include: A
0.015m3 holding tank, fixed with a stirrer 0.745kW centrifugal
pump, coupled to a single phase electric motor, a ball valve with 0.0254m hoses. A pressure guage was provided to measure the inlet and outlet pressures of the pump. Figure 1 shows the top view of the experimental setup used for the research work.
Figure 1: Side View of Experimental Setup
An accelerated life testing procedure was applied in this study. The holding tank mounted with a stirrer, initially had 0.015m3 of water pumped and circulated back to the tank. The inlet and outlet pressures of the water from the pump were measured. Some fixed amount of sand was put into the tank and the stirrer switched on while pumping activity was performed and the inlet pressure, outlet pressure, vibration of the pump measured .This was repeated with different amount of sand at a constant interval and also repeated at random intervals.
Modeling of PM Policy
Optimal constant-interval preventive replacement (PR) policy was modeled . Under the policy, PM was performed on the
system after it had operated a total of t p
hours, irrespective of the number of occurring failures within the interval. In a
situation where failure happened prior to t p , minimal repair was carried out. PM renewed the system to become as good as new. Minimal repair did not change the failure rate of the system, as emphasized in [2]. The choice of the horizon or planning period in the study was important, a position maintained also according to [4] which, they had presented earlier and solved a planning horizon problem.
The model for PM is presented in Equation (1):
Cp C f H (t p )
t
EC (t p ) =
p
where,
(1)
EC(t p ) is total expected cost due to PM and minimal repair cost per expected length of interval,
Cp is the preventive maintenance cost,
Cf is the failure cost, and
H( t p ) is the failure cost function.
The failure cost function is given in Equation (2):
t p
H (t p ) r(t)dt , (2)
0
Which is the expected number of failures in the interval [0, t p ] . The failure rate function is given by Equation (3):
f (t)
r(t) =
1 f (t)
, (3)
where,
f(t) it the probability density function and is given in Equation (4):
1
f(t)=
N
0<t N
(4)
where N is uniformly distributed in the interval [0<t N ]. Substituting N into Equation
(4) gives, Equation (5) given below.
1
r(t) = N 1
(5)
1 1 t
N
N t
Equation 5 is substituted into Equation 2, resulting into Equation (6 ) given below
cp
H( t p ) =
1
0
N t
dt ln[( N t p )]
(6)
When Equation 6 is substituted into Equation (1), Equation (7) is obtained:
Cp
EC (t p ) =
-
C f
ln N N t p
t p
(7)
The magnitude of the shock can be calculated from Equation (8):
s f 2 f1
f1
(8)
where,
f1 is the measured frequency when there is no sand in the system and system. 0 s 1.
f 2 is the measured frequency when sand is put into the
A Golden section method was employed to find t p which minimizes the expected maintenance cost for Equation (7) under this policy.
The value of
Cp varies from N1,00000 to N1,500.00only, and Cf
varies fromN,1000.00 to N10,000.00only. The projection
was for seven series: from one to six under random studies and one for a constant interval method. The purchase price of the pimp was N4,0000.00 only.
RESULTS
III RESULTS AND DISCUSSION
The results obtained at the end of the research are presented under sub-section 4.1. Table 1 presents the data obtained from the experimental setup
Table 1: Normal working condition (2.97 hours)
Time (hours) |
Sum time (hours) |
Inlet Pressure x105 N / m 2 |
Outlet Pressure x105 N / m 2 |
Amount of sand (kg) |
Sum of sand (kg) |
Flow rate m3 / hr |
Vibration value Hz |
No. of failures |
0.33 |
0.33 |
0.50 |
0.50 |
0.00 |
0.00 |
120 |
51 |
0 |
0.33 |
0.66 |
0.50 |
0.50 |
0.00 |
0.00 |
120 |
51 |
|
0.33 |
0.99 |
0.50 |
0.50 |
0.00 |
0.00 |
120 |
51 |
|
0.33 |
1.32 |
0.50 |
0.50 |
0.00 |
0.00 |
120 |
51 |
|
0.33 |
1.65 |
0.45 |
0.45 |
0.00 |
0.00 |
120 |
51 |
|
0.33 |
1.98 |
0.45 |
0.45 |
0.00 |
0.00 |
120 |
51 |
|
0.33 |
2.31 |
0.45 |
0.45 |
0.00 |
0.00 |
120 |
51 |
|
0.33 |
2.64 |
0.45 |
0.45 |
0.00 |
0.00 |
120 |
51 |
|
0.33 |
2.97 |
0.45 |
0.45 |
0.00 |
0.00 |
120 |
51 |
In Table 2 results with cumulative damage and random shock at1.08 hours is shown.
Table 2 : Results with cumulative damage degradation and random shock at1.08 hours
Time (hours) |
Sum time (hours) |
Inlet Pressure x105 N / m 2 |
Outlet Pressure x105 N / m 2 |
Amount of sand (kg) |
Sum of sand |
Shock Magnitude (kg) |
Flow rate m3 / hr |
Vibration Hz |
No. of failures |
0.33 |
0.33 |
0.35 |
0.35 |
0.0010 |
0.0010 |
0.18 |
120 |
60.1 |
2 |
0.25 |
0.58 |
0.25 |
0.25 |
0.0020 |
0.0030 |
0.18 |
120 |
60.0 |
|
0.17 |
0.75 |
0.25 |
0.20 |
0.0030 |
0.0060 |
0.18 |
112 |
60.0 |
|
0.17 |
0.92 |
0.15 |
0.12 |
0.0040 |
0.0100 |
0.24 |
112 |
63.2 |
|
.08 |
1.00 |
0.10 |
0.05 |
0.0050 |
0.015 |
0.24 |
112 |
63.3 |
|
0.08 |
1.08 |
0.10 |
0.05 |
0.0060 |
0.0210 |
0.24 |
112 |
63.3 |
Accordingly, various results obtained for cumulative damage degradation and random shocks in are as presented in Table 4, Table 5,Table 6,Table7,Table 8, Table 9 and Table10 respectively at 1.00hour, 1.41 hours, 1.08 hours, 1.08 hours, 0.84 hours,
1.98 hours,1.98 hours and1.98 hours, respectively.
Table 3 : Data with cumulative damage degradation and random shock at1.00 hours
Time (hours) |
Sum time (hours) |
Inlet Pressure x105 N / m 2 |
Outlet Pressure x105 N / m 2 |
Amount of sand (kg) |
Sum of sand (kg) |
Shock Magnitude |
Flow rate m3 / hr |
Vibration Hz |
No. of failure |
0.25 |
0.25 |
0.25 |
0.25 |
0.003 |
0.003 |
0.27 |
108 |
65.0 |
2 |
0.25 |
0.50 |
0.20 |
0.45 |
0.005 |
0.008 |
0.27 |
108 |
65.0 |
|
0.17 |
0.67 |
0.15 |
0.60 |
0.007 |
0.015 |
0.28 |
100 |
65.4 |
|
0.17 |
0.84 |
0.10 |
0.70 |
0.009 |
0.024 |
0.29 |
100 |
65.9 |
|
0.08 |
0.92 |
0.00 |
0.70 |
0.01 |
0.035 |
0.29 |
100 |
65.9 |
|
0.08 |
1.00 |
0.00 |
0.70 |
0.01 |
0.038 |
0.31 |
96 |
67.0 |
Table 4 : Results obtained with cumulative damage degradation and random shock at1.41 hours
Time (hours) |
Sum time (hours) |
Inlet Pressure x105 N / m 2 |
Outlet Pressure x105 N / m 2 |
Amount of sand (kg) |
Sum of Sand (kg) |
Shock Magnitude |
Flow rate m3 / hr |
Vibration Hz |
No. of failures |
0.33 |
0.33 |
0.25 |
0.22 |
0.0020 |
0.002 |
0.31 |
96 |
67.0 |
3 |
0.33 |
0.66 |
0.20 |
0.18 |
0.004 |
0.006 |
0.32 |
96 |
67.2 |
|
0.25 |
0.91 |
0.10 |
0.08 |
0.006 |
0.012 |
0.32 |
96 |
67.5 |
|
0.25 |
1.16 |
0.05 |
0.03 |
0.008 |
0.020 |
0.33 |
96 |
67.9 |
|
0.17 |
1.33 |
0.05 |
0.00 |
0.010 |
0.030 |
0.37 |
88 |
70.0 |
|
0.08 |
1.41 |
0.00 |
0.00 |
0.012 |
0.042 |
0.37 |
88 |
70.0 |
Table 5: Results obtained with cumulative damage degradation and random shock at1.08 hours
Time (hours) x10 1 |
Sum of time (hours) x10 1 |
Inlet Pressure x106 N / m 2 |
Outlet Pressure x106 N / m 2 |
Amount of sand (kg) x10 3 |
Sum of sand (kg) 10 3 |
Shock Magnitude x10 1 |
Flow rate m3 / hr x101 |
Vibration Hz x101 |
2.5 |
2.5 |
2.5 |
2.0 |
1 |
1 |
3.3 |
8.8 |
7.00 |
5.0 |
7.5 |
2.0 |
2.0 |
3 |
4 |
3.9 |
8.8 |
7..0 |
7.5 |
15.0 |
1.5 |
1.2 |
5 |
9 |
4.0 |
8.8 |
7.14 |
9.2 |
24.2 |
1.0 |
0.5 |
7 |
16 |
4.0 |
8.4 |
7.14 |
10.9 |
35.1 |
0.5 |
0.0 |
9 |
25 |
4.1 |
8.0 |
7.20 |
11.7 |
46.8 |
99.9 |
0.0 |
11 |
36 |
4.1 |
8.0 |
7.20 |
Table 6: Results Obtained with cumulative damage degradation and random shock at1.08 hours
Time (hours) |
Sum time (hours) |
Inlet Pressure x105 N / m 2 |
Outlet Pressure x105 N / m 2 |
Amount of sand (kg) |
Sum of sand (kg) |
Shock Magnitude |
Flow rate m3 / hr |
Vibration Value Hz |
Number of failures |
0.25 |
0.25 |
0.20 |
0.20 |
0.002 |
0.002 |
0.47 |
72 |
75.1 |
|
0.17 |
0.42 |
0.20 |
0.15 |
0.003 |
0.005 |
0.48 |
72 |
75.3 |
|
0.17 |
0.59 |
0.15 |
0.15 |
0.004 |
0.009 |
0.48 |
60 |
75.3 |
|
0.17 |
0.76 |
0.10 |
0.05 |
0.005 |
0.014 |
0.48 |
60 |
75.7 |
|
0.08 |
0.84 |
0.05 |
0.00 |
0.006 |
0.020 |
0.49 |
60 |
76 |
|
0.08 |
0.92 |
0.00 |
0.00 |
0.007 |
0.027 |
0.49 |
60 |
76 |
Table 7: Results obtained with cumulative damage degradation and random shock at 0.84 hours
Time (hours) |
Sum of time (hours) |
Inlet Pressure x105 N / m 2 |
Outlet Pressure x105 N / m 2 |
Amount of sand (kg) |
Sum of sand (kg) |
Shock Magnitude |
Flow rate m3 / hr |
Vibration Value Hz |
Number of failures |
0.17 |
0.17 |
0.15 |
0.15 |
0.4 |
0.4 |
0.51 |
60 |
77 |
2 |
0.17 |
0.34 |
0.15 |
0.15 |
0.8 |
1.2 |
0.57 |
60 |
80 |
|
0.17 |
0.51 |
0.10 |
0.10 |
1.2 |
2.4 |
0.61 |
60 |
82 |
|
0.17 |
0.68 |
0.00 |
0.00 |
1.6 |
4.0 |
0.63 |
0 |
83 |
|
0.08 |
0.76 |
0.00 |
0.00 |
2.0 |
6.0 |
0.67 |
0 |
85 |
|
0.08 |
0.84 |
0.00 |
0.00 |
2.4 |
8.4 |
0 |
– |
(-): shows that the pump stopped working or seized. is a sign of a very high shock value
Table 8: Results obtained with cumulative damage degradation and random shock at 1.98 hours
Time (hours) x10 1 |
Sum time (hours) x10 1 |
Inlet Pressure x106 N / m 2 |
Outlet Pressure x106 N / m 2 |
Amount of sand (kg) x10 3 |
Sum of sand (kg) x10 3 |
Shock Magnitude x10 1 |
Flow rate m3 / hr x101 |
Vibration Value Hz x101 |
3.3 |
33 |
3.5 |
3.0 |
1 |
1 |
1.8 |
12 |
6.01 |
3.3 |
6.6 |
3.0 |
2.7 |
2 |
3 |
1.9 |
12 |
6.09 |
3..3 |
9.9 |
3.0 |
2.5 |
3 |
6 |
2.4 |
11.2 |
6.30 |
33 |
1.32 |
2.5 |
2.0 |
4 |
10 |
2.5 |
11.2 |
6.39 |
3.3 |
16.5 |
2.5 |
1.5 |
5 |
15 |
2.6 |
10.4 |
64.3 |
3.3 |
1.98 |
1.5 |
1.0 |
6 |
21 |
2.7 |
10.4 |
6.49 |
Table 9: Results obtained with cumulative damage degradation and random shock at1.98 hours
Time (hours) |
Sum time (hours) |
Inlet Pressure x105 N / m 2 |
Outlet Pressure x105 N / m 2 |
Amount of sand (kg) |
Sum of sand (kg) |
Shock Magnitude |
Flow rate m3 / hr |
Vibration Value Hz |
Number of failures |
0.33 |
0.33 |
0.30 |
0.25 |
0.001 |
0.001 |
0.24 |
112 |
63.0 |
2 |
0.33 |
0.66 |
0.30 |
0.20 |
0.002 |
0.003 |
0.25 |
112 |
63.6 |
|
0.33 |
0.99 |
0.25 |
0.17 |
0.003 |
0.006 |
0.26 |
104 |
64.2 |
|
0.33 |
1.32 |
0.25 |
0.15 |
0.004 |
0.010 |
0.27 |
104 |
65.0 |
|
0.33 |
1.65 |
0.20 |
0.10 |
0.005 |
0.015 |
0.28 |
96 |
65.5 |
|
0.33 |
1.98 |
0.10 |
0.00 |
0.006 |
0.921 |
0.37 |
96 |
70 |
Table 10: Results obtained with cumulative damage degradation and random shock at1.98 hours
Time (hours) x10 1 |
Sum time (hours) x10 1 |
Pressure inlet x106 N / m 2 |
Outlet Pressure x106 N /m 2 |
Amount of sand (kg) x10 3 |
Sum of sand (kg) x10 3 |
Shock Magnitude x10 1 |
Flow rate m3 / hr x101 |
Vibration Value Hz x101 |
3.3 |
3.3 |
2.5 |
2.1 |
1 |
1 |
3.1 |
9.6 |
6.70 |
3.3 |
6.6 |
2.0 |
1.3 |
2 |
3 |
3.3 |
9.6 |
6.80 |
3.3 |
9.9 |
2.0 |
1.0 |
3 |
6 |
3.5 |
8.8 |
6.88 |
.33 |
13.2 |
.15 |
.08 |
4 |
10 |
3.6 |
8.0 |
6.96 |
3.3 |
16.5 |
1.0 |
0.5 |
5 |
15 |
3.9 |
8.0 |
7..08 |
3.3 |
19.8 |
0.5 |
0.0 |
6 |
21 |
4.0 |
7.2 |
7.1.6 |
The cumulative data set for the centrifugal Pump is presented in Table 11.Table 12 presents the summary of random readings and Table 13 presents the summary of steady readings taken during the experiment.
Table 11: Cumulative Result set
S/N |
TBF x101 |
Number of failures |
Sum Time (TBF) |
Sum Failure |
Down time (hours) |
Number of Replacement |
Maintenance Time Spent (hours) |
Remarks |
1.0 |
0.297 |
2.0 |
2.97 |
2.0 |
0.00 |
0 |
0 |
Without sand |
2.0 |
0.108 |
2.0 |
4.05 |
4.0 |
3.00 |
0 |
1 |
With sand |
3.0 |
0.100 |
2.0 |
5.05 |
6.0 |
1.15 |
0 |
1 |
With sand |
4.0 |
0.141 |
3.0 |
5.46 |
9.0 |
6.00 |
1 |
1 |
With sand |
5.0 |
0.117 |
2.0 |
6.63 |
11.0 |
0.30 |
0 |
0.5 |
With sand |
6.0 |
0.092 |
2.0 |
7.55 |
13.0 |
1.00 |
0 |
1 |
With sand |
7.0 |
0.084 |
2.0 |
8.39 |
15.0 |
0.00 |
0 |
0 |
With sand |
Table 12: Tabulation of Random Readings
S/N |
Time before Failure TBF (hours) |
Number of Failures (n) |
Failure rate ( ) per hour x10 1 |
1.0 |
1.08 |
2.0 |
5.4 |
2.0 |
1.00 |
2.0 |
5.0 |
3.0 |
1.41 |
3.0 |
3.8 |
4,0 |
1.17 |
2.0 |
5.9 |
5,0 |
0.92 |
2.0 |
4.5 |
6,0 |
0.84 |
2.0 |
4.2 |
Table 13: Summary (Steady Readings)
S/N |
Time TBF (hrs) |
Number of Failures (N) |
Failure rate ( ) Per hour |
1 |
2.97 |
0 |
0 |
2 |
1.98 |
2 |
0.99 |
3 |
1.98 |
2 |
0.99 |
4 |
1.98 |
2 |
0.99 |
IV DISCUSSION
From Table 1, the time of 0.33 hours was used to measure the required parameters in the accelerated experimental setup. The inlet and outlet pressures had the same value and remained the same throughout the study period. No sand was added to the
water and the volume flow rate of120m3 / hr
was constant at operating vibration frequency of
51Hz .
As shown in Tables 2 to Tables 7, randomly selected time interval was used with a fixed amount of sharp sand put into the tank and pumping was done and some parameters were measured. In Table 2, when 0.0010kg of sharp sand was put into the system during 0.33 hours, the volumetric flow rate recorded was 120 x105 N / m 2 and the vibration of the pump rose from 51Hz to
60.1 Hz. This gave a shock of 0.18. At the inlet and outlet pressures of 0.15
x105 N / m 2
and 0.12
x105 N / m 2
the shock
was 0.24 with vibration magnitude of 63.2Hz. At the inlet and outlet pressures of 0.10
x105 N / m 2
and 0.05
x105 N / m 2
the shock was still 0.24 and the vibration magnitude of the pump rose to 63.3Hz. At this instance the system failure two. Similar behaviours were obtained in Table 3 by randomly adding of sharp sand at the span of 1.00 hour. The peak vibration magnitude frequency of 67Hz and the lowest vibration magnitude frequency of 65Hz were recorded. In Table 4 the highest shock magnitude was 0.37 at a vibration magnitude of 70Hz and the lowest vibration magnitude of 67Hz at a span of 1.41hours with three failures.
In Table 5 and Table 6, respectively the lowest volumetric flow rate were 80m3 / hr , 60m3 / hr
at a vibration magnitudes of
70Hz and 76 Hz and 88m3 / hr , 72m3 / hr
at a vibration magnitudes of 72Hz and 75.1Hz at spans of 1.08 hours and at a
shock magnitudes of 0.41 and 0.49, respectively.
Other results are given for pressures, quantity of sand, shock magnitude, vibration frequency and number of failures for random methods in Tables, 7, 8, 9 and 10 for 1.98 hours respectively.
Table 11 shows cumulative data set for the centrifugal pump without sand and with sand. The synopsis of random readings for each of pump activity is given in Table 12.
Similarly, Table 13 shows the values under steady readings. From Table 13, it can be observed that the reliability obtained was high compared to the ones obtained from Tables 2 to 10; indicating that random shocks are most devastating than cumulative degradation damage.
The failure rate under each condition was computed and used to obtain the reliability theof the pump from one to twelve months during the systematic search for t p -the optimum interval. From Figure1 presented below, the total expected cost varies from two thousand naira (N2,000.00) only to sixteen thousand naira (N16,000.00) only.
Figure 2 shows the expected cost over time interval.
Figure 2 : Expected Cost Versus Time
IV CONCLUSION
The cumulative degradation damage shock for a system operating under a normal operating condition is less devastating than that with random shocks conditions. The amount of sharp sand put into the system affects the, pressures, volumetric flow rate and the vibration magnitude. This is depicted in the magnitude of the shock obtained. A system operating under shock conditions will have many number of failures compared to a system without shock conditions and this will affect the reliability of the system and hence the total expected cost of the system will rise. A high reliability will reduce the total xpected cost of the system and increase the availability of the overall system. The model and methodology presented are useful in determining the cumulative damage degradation and random shocks for a given system.
RERERENCES
[1] SS..EN 13306: Maintenance Terminologies (Swedish Standard) ,2010 [2] S.O Duffuaa,., A. Raouf, and J.D. Campbell,.Planning and Control of MaintenanceSystems Modeling and Analysis. John Wiley and Sons. Canada, 1999 [3] W.A Akpan and T. M Ogunsola. Optimization of Preventive Maintenance Practice in Maritime Academy Oron International Journal of Engineering Research and Applications(IJERA) Volume 5 issue 5 (Part-6) May, 2015. Pp 103-109. [4] W.A Akpan; A.O.; Odukwe, O.I Ani and O.U Enefiok,. Planning Horizon and Its Effect on CBM System International Journal of Engineering Research and Technology (IJERT) Volume 9 issue 3, March, , 2020. Pp 366-371 [5] W.A Akpan; A.O. Odukwe, O.I.; Ani, and E.J Awaka-Ama,. Increasing Reliability and Availability in CBM System. International Journal of Engineering Science Invention (IJESI) 9 issue 1 series iii, January, 2020. Pp 09-13. [6] A. Lehmann, 2008. Joint Modeling of Degradation and Failure Time Data. Journal of Statistical Planning and Inference, 139, Pp1693-1706. [7] W.A. Akpan; A.O Odukwe,. and O.I Ani,. Combinatorial Optimization in Condition Based Maintenance System International Journal of Research Studies in Computer Science and Engineering (IJRSCSE) Volume 4 issue 3,March, 2019 Pp 16-23. [8] W Wang; P. A Scarf and M. A.( Smith, 2000) On the Application of a Model Condition Based Maintenance Vol. 51 No 11 Pp 1218-1227. [9] N. Gorijian; L., Ma, M Mittinty; P Yarlagadda and Y. Sun, A review on degradation in Reliability Analysis . Proceedings of the 4th World Congress on Engineering Asset Management, Athens, Greece, 2009.pp 28-30. [10] W Kahle and H Wendt On a Cumulative Damage Process and Resulting First Passage Times. Applied Stochastic Models in Business and Industry, 2010,pp 17-26. [11] A. Gut and J. Husler: Realistic Variation of Shock Models. Statistic and Probability Letters, 74, 2005 pp 187-204. [12] J.A.M. Vander Wiede, M.D Pandey and J.M., Van Noortwijk, Discounted Cost Model for Condition Based Maintenance Optimization . Reliability Engineering and System Safety, 95, 2010, Pp 236-246. [13] T Lam and Y. L.Zhang, A Shock Model for the Maintenance Problem of a Repairable System. Computers and Operations Research, Romania-cluj- Napoca 31, Pp1807-1820.