
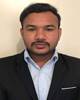
- Open Access
- Authors : Ashish Khule , Anantharama Baipadithaya
- Paper ID : IJERTV10IS060311
- Volume & Issue : Volume 10, Issue 06 (June 2021)
- Published (First Online): 29-06-2021
- ISSN (Online) : 2278-0181
- Publisher Name : IJERT
- License:
This work is licensed under a Creative Commons Attribution 4.0 International License
Modeling and Analysis of Solid Vessel and Multilayered Composite Pressure Vessel
Ashish Khule
Department of Mechanical Engineering Dhole Patil College of Engineering Pune, India
Prof. Anantharama Baipadithaya Department of Mechanical Engineering Dhole Patil College of Engineering Pune, India
Abstract A pressure vessel is designed to work under a high internal pressure condition, so the selection of material and the design of the vessel are the most important part.
In this paper, we are comparing the solid pressure vessel made of a steel s515-gr70 and composite material pressure vessel made of epoxy s-glass, epoxy e-glass and epoxy carbon. The static deformation, von-mises stress and strain energy for a pressure vessel are calculated with multilayered composite material. The main objective of the work is to compare the solid pressure vessel with composite material pressure vessel and multilayered composite pressure and find out the best suitable material and design for the pressure vessel. To reduces the stress on the object here we are designing one more model i.e., multilayer vessel and calculating the deformation and stress and strain energy values from all these values and all other material combinations we conclude which composite is the most suitable and efficient pressure vessel.
KeywordsDesign, Analysis, Solid & Multilayer Composite pressure Vessel
-
INTRODUCTION
In Process Industries, like chemical and petroleum, boiler industries there are design restrictions for large volumes of high internal pressures in metallic single-wall cylindrical vessels. As the pressure of the operating fluid rises, an increment in the thickness of the vessel intended to hold that fluid is an automatic choice. The increment in the thickness beyond a certain value will possess fabrication difficulties as well as demands stronger material for the vessel construction. Due to increasing demands from the process industry for higher operating pressures and temperature, new technologies have been developed and underdeveloped to handle the present-day specialized requirements. Multilayer Pressure Vessels have broadened the art of pressure vessel fabrication or construction and introduce the process designer with a genuine piece of equipment useful in a wide range of operating conditions for the problems generated by the storage of hydrogen and hydrogenation processes the term pressure vessel referred to those reservoirs or containers, which are subjected to internal or external pressures.
Pressure vessels find wide applications in thermal and nuclear power plants, process, and chemical industries, in space and ocean depths, and in water, steam, gas and air supply system in industries. The pressure vessel material may be brittle such as cast iron, or ductile such as mild steel. Multilayer composite vessels are built up by wrapping and combining a series of sheets over a core tube to give a unique combination of properties. The construction involves the use of several
layers of material, like metals, alloys, plastic co-polymers, minerals, and wood, usually for quality control and optimum properties. Multilayer construction is used for higher pressures. It provides inbuilt safety, high stiffness, and strength-to-weight ratio, long fatigue life, utilizes material economically, no stress relief is required. The finite element method is especially versatile and efficient for the analysis of complex structural behaviour of multilayered composite laminated structures. Using the finite element method, a significant amount of research has been devoted to the analysis of deformation, stress, and strain energy.
-
LITERATURE SURVEY
Zhang et al. [1] derived an analytical solution for determining the stress distribution of a multi-layered composite pressure vessel subjected to internal fluid pressure and a thermal load. The stress distribution of the pressure vessel was computed using the FE method. Ali, Ghosh, and Alam [2] investigated the effect of the auto frottage process in strain hardened thick-walled pressure vessels theoretically by FE modelling. Wang and Ding [3] obtained the thermoelastic dynamic solution of a multilayered orthotropic hollow cylinder in the state of axisymmetric plane strain. Atefi and Mahmoudi
[4] offered an analytical solution for obtaining thermal stresses in a pipe caused by periodic time-varying of the temperature of the medium fluid. Jabbari, Sohrabpour, and Eslami [5] developed a general analysis of one-dimensional steady-state thermal stresses in a hollow thick cylinder made of functionally graded material. Shao, Wang, and Ang [6] carried out a thermomechanical analysis of functionally graded hollow cylinder subjected to axisymmetric mechanical and transient thermal loads. Thick-walled cylinders subjected to internal heat flow are used in many engineering applications. Typical examples are nuclear engineering structures, nozzle sections of rockets, gun tubes, and dies of hot forming tools. The study of thick-walled cylinders subjected to internal heat flow and/or internal pressure is a problem of great practical interest. Industrial demands for such applications have focused the attention of the investigators on this point of research. However, most investigators have only dealt with the analysis of thermal stresses of thick-walled cylinders under steady-state conditions [7]. conductivity as a function of temperature. They concluded that the effect of thermal conductivity on the temperature and stresses is slight for small values of internal heat flow. However, for large heat flow, the difference in temperature and stresses between temperature-dependent and – independent thermal conductivity can be as much as 20%.Vollbrecht [8] has analyzed the stresses in both cylindrical and spherical walls subjected to internal pressure and stationary heat flow.
3. Meshing (FE Modelling)
-
PROBLEMS DEFINITION
This paper is mainly carried out to compare the solid pressure vessel and multilayered pressure vessel and find out the best suitable material and design for pressure vessel. It is modelled using CREO and analysis is carried out into Ansys software using the structural analysis method. The von-mises stress, deformation and strain energy are found for various pressure vessel materials.
The pressure vessel material taken for analysis is M.S. steel and composite material such as glass epoxy fiber and epoxy carbon.
-
METHODOLOGY
Modelling of the pressure vessel:
A virtual model of solid pressure vessel and the composite pressure vessel is created using CREO software and then the model was imported to ANSYS for analysis and the results of deformation, stress and strain analysis of different materials are compared with each other.
The line diagram of the pressure vessel is shown in Fig. 1. The 3D model of the pressure vessel created in CREO is shown in Fig. 2.
-
GEOMETRY AND BOUNDRY CONDITION
1. Geometry of reference model for creating an object:
Fig. 3. FE Tetra-Mesh of Pressure Vessel in Ansys Workbench
4. Boundary Conditions
Fig. 4. Boundary Conditions of the Pressure Vessel
-
STATIC STRUCTURAL ANALYSIS RESULT The goal of this paper is to determine the static analysis of
the pressure vessels like deformation, stress, and strain energy. Effects of the different materials of steel and different composite materials as well as multilayered composite material on static deformation, stress and strain energy are investigated, including comparison with results using Creo and Ansys.
The material propertes of various materials with which the pressure vessel is made are:
2. 3D Model
Fig. 1. Line Diagram of the Pressure Vessel
Mild Steel:
Youngs modulus -205 x 109 Pa, Poissons ratio – 0.29, Density – 7850 Kg/m3.
Epoxy e-glass:
Density – 2000 kg/m3, Youngs modulus in x-direction: 45x 109 Pa, Youngs modulus in y-direction: 10×109 Pa, Youngs modulus in z-direction: 10×109 Pa, Poissons ratio in xy- 0.3, Poissons ratio in yz- 0.4, Poissons ratio in zx- 0.3.
Fig. 2. 3-D CAD model of the Pressure Vessel
Epoxy s-glass:
Density – 2000 kg/m3, Youngs modulus in x-direction 50 x 109 Pa, Youngs modulus in y-direction 8 x109 Pa, Youngs modulus in z-direction – 8 x109 Pa, Poissons ratio in xy – 0.3, Poissons ratio in yz – 0.4, Poissons ratio in zx – 0.3.
Epoxy carbon:
Density – 1480 kg/m3, Youngs modulus in x-direction –
91.820 x 109 Pa, Youngs modulus in y-direction – 91.820 x 109 Pa, Youngs modulus in z-direction 9 x109 Pa, Poissons ratio in xy – 0.05, Poissons ratio in yz – 0.3, Poissons ratio in zx – 0.3.
-
Analysis of Solid Pressure Vessel
(Existing material (steel s515-gr70))
-
Deformation
Fig. 5. Static Structural Deformation of Steels515-gr70
-
Stress
Fig. 6. Static Structural Von-Mises stress of Steels515-gr70
-
Strain Energy
Fig. 7. Static Structural Strain Energy of Steels515-gr70
When we applied 30Mpa pressure on the vessel it produces nearly 256Mpa stress to reduces the stress on the body here we are changing material. We have chosen 3 composite materials now we are going to analyze these 3 materials with the same boundary conditions.
-
-
Analysis of Composite Material
-
Epoxy s-glass
-
Deformation
Fig. 8. Static Structural Deformation of Epoxy s-Glass
-
Stress
Fig. 9. Static Structural Von-Mises stress of Epoxy s-Glass
-
Strain Energy
Fig. 10. Static Structural Strain Energy of Epoxy s-Glass
-
-
Epoxy e-glass
-
Deformation
Fig. 11. Static Structural Deformation of Epoxy e-Glass
-
Stress
Fig. 12. Static Structural Von-Mises stress of Epoxy e-Glass
2. Strain Energy
Fig. 13. Static Structural Strain Energy of Epoxy e-Glass
-
-
EPOXY CARBON
1. Deformation
TABLE I. RESULT OF SOLID AND COMPOSITE MATERIAL VESSEL
Material
Deformation (mm)
Stress (Mpa)
Strain energy (mJ)
Steel-s515-gr70
1.6143
264.48
9.3644e5
Epoxy s-glass
31.223
295.07
4.0391e7
Epoxy e-glass
26.249
283.79
3.7792e7
Epoxy-carbon
29.096
405.29
4.1917e7
We can say that the deformation values are low for steel- s515-gr70 and high for epoxy e-glass. The stress has been increasing for all materials and in this steel-s515-gr-70 have fewer stress values and epoxy carbon has high-stress values.
From the above solid vessel (162mm thickness) results when we change material from ss515-gr70 to composite materials no other material gave fewer stress values. By these changes, the stress has been increased so we cannot use complete composite material for a vessel and here we follow another concept i.e., multilayer vessel in this process we have created the original model with the same dimensions but here we created two layers for a vessel which are those 162mm and 18mm respectively and here we are applying the outer layer as same steel-s515-gr70 but inner material we are adding composite materials.
-
STEEL-S515-GR70 AND EPOXY-CARBON COMPOSITE MATERIAL
-
Geometry Modification of model for creating the object:
Fig. 14. Static Structural Deformation of Epoxy Carbon
-
Stress
Fig. 15. Static Structural Von-Mises stress of Epoxy Carbon
-
Strain Energy
Fig. 16. Static Structural Strain Energy of Epoxy Carbon
Fig. 17. Line Diagram of the Multi-layered Composite Pressure Vessel
We are going to create one newer model of multilayer composite pressure vessel. The line diagram of the multilayer composite pressure vessel is shown in Fig. 17.
The construction of the multilayer composite pressure vessel is:
Total No. of layers: 26, (25 shell layers +1Liner) Total Thickness: 162 mm
Liner thickness: 12 mm &
Each Shell layers Thickness, t: 6 mm.
-
Deformation
Fig. 17. Static Structural Deformation of Steel-s515-gr70 and Epoxy Carbon
-
Stress
Fig. 18. Static Structural Von-Mises stress of Steel-s515-gr70 and Epoxy Carbon
-
Strain Energy
Material
Deformation (mm)
Stress (Mpa)
Strain energy (mJ)
Steel-s515-gr70 & epoxy-s-glass
1.6152
264.49
9.3705e5
Steel-s515-gr70 & epoxy-e-glass
1.4772
256.6
2.0283e6
Steel-s515-gr70 & epoxy-carbon
2.1842
230.25
9.27e5
Material
Deformation (mm)
Stress (Mpa)
Strain energy (mJ)
Steel-s515-gr70 & epoxy-s-glass
1.6152
264.49
9.3705e5
Steel-s515-gr70 & epoxy-e-glass
1.4772
256.6
2.0283e6
Steel-s515-gr70 & epoxy-carbon
2.1842
230.25
9.27e5
Fig. 19. Static Structural Strain Energy of Steel-s515-gr70 and Epoxy Carbon TABLE II. RESULT OF STEEL-S515-GR70 AND EPOXY MATERIAL
Deformation- values for all multi-layer models and in this steel-s5155 epoxy e-glass has produced less deformation among all and steel-s515-gr70 epoxy carbon-producing high deformation.
Stress- For steel-s515-gr70 producing high deformation but in this stress values it has exceptionally low stresses among all other materials.
Strain Energy- From all results here steel-s515-gr70 epoxy e-glass having high energy compares to others. But it also has high-stress values which are not safe for a model.
-
-
CONCLUSION
-
-
In this project, we have analyzed one solid vessel (180mm thickness) of existing material steel-s515-gr70 and applied
30Mpa pressure on it. We got nearly 256Mpa stress on the whole body to reduce these stress values we completely use composite materials which are epoxy carbon and epoxy e-glass and epoxy s-glass, respectively. But these changes will not satisfy our condition. These composite materials have incredibly good strength compare with existing material, but it also produces remarkably high stress on the body.
To avoid these stresses on the model we have done one more model which is called multi-layer vessel (162mm thick & 18mm thick) with steel-s515-gr70 and composite material respectively and analyses with the same boundary conditions and calculated results for all combinations.
From all combination results steel-s515-gr70 with epoxy carbon produces fewer stress values 230Mpa only compared to a solid vessel by this change we have been reduced 35Mpa stresses on the body and composite materials are lightweight, so we reduce component weight in this case.
Finally, we conclude that multi-layer vessel with (steel- s515-gr70&epoxy carbon) gave fewer stress values compare to solid vessel with steel-s515-gr70 materials.
REFERENCES>
-
Q. Zhang, Z. W. Wang, C. Y. Tang, D. P. Hu, P. Q. Liu, and L. Z. Xia, Analytical solution of the thermo-mechanical stresses in a multilayered composite pressure vessel considering the influence of the closed ends, International Journal of Pressure Vessels and Piping 98, pp. 102110, 2012.
-
A. R. Ali, N. C. Ghosh, and T. E. Alam, and L. Z. Xia, Optimum Design of Pressure Vessel Subjected to Autofrettage Process, World Academy of Science, Engineering and Technology 46, 2010, 667672.
-
H. M. Wang, and H. J. Ding, Transient thermoelastic solution of a multilayered orthotropic hollow cylinder for axisymmetric problems, Journal of Thermal Stresses 27; 2004, pp. 11691185.
-
G. Atefi, and H. Mahmoudi, Thermal stresses in the wall of pipes caused by periodic change of temperature of medium fluid, The 4th International Meeting of Advances in Thermofluids AIP Conf. Proc. 1440; 2011, pp. 7289.
-
M. Jabbari, S. Sohrabpour, and M. R. Eslami, Mechanical and thermal stresses in a functionally graded hollow cylinder due to radially symmetric loads, International Journal of Pressure Vessels and Piping 79; 2002, pp. 493 -497.
-
Z. S. Shao, T. J. Wang, and K. K. Ang, Transient thermomechanical analysis of functionally graded hollow circular cylinders, Journal of Thermal Stresses 30:1; 2007, pp. 81 104.
-
S. T. Stasynk, V. I. Gromovyk and A. L. Bichuya, Thermal-stress analysis of hollow cylinder with temperature-dependent, Aead. of Sciences of the Ukrainian SSR, LVOV. USSR, Vol. 11, No. 1, PP. 41- 43, Jan. 1979, Translated in" Strength of material, vol. 11, No. 1, PP. 50- 52, Sep. 1979.
-
H. Vollbrecht, Stress in cylindrical and spherical walls subjected to internal pressure and stationary heat flow, Verfahrenstechnik 8, 109-12 (1974).