
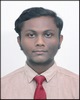
- Open Access
- Authors : Parth Parmar , Darshil Trivedi , Kishan Randhesiya , Ravi Shingala
- Paper ID : IJERTV10IS010263
- Volume & Issue : Volume 10, Issue 01 (January 2021)
- Published (First Online): 04-02-2021
- ISSN (Online) : 2278-0181
- Publisher Name : IJERT
- License:
This work is licensed under a Creative Commons Attribution 4.0 International License
Modeling and Analysis of Different Chevron Nozzle for Noise Reduction
[1] Parth Parmar [2] Darshil Trivedi [3] Kishan Randhesiya [4] Ravi ShingalaB. tech Aeronautical Engineering Student,
Department of Aeronautical Engineering, Parul Institute of Engineering and Technology, Vadodara, Gujarat, India.
Abstract: The purpose of making this project is to reduce the very harmful noise produce by the commercial aircrafts. The most of noise of aircraft is only produce by the aircraft engines. In commercial aircraft usually Turbo-fan use as gas turbine engine for producing thrust. In turbo-fan engines mostly uses convergent type nozzle. Chevron convergent Nozzle in currently very useful as a noise prevent nozzle for passenger aircrafts. The main noise produce sources arise in the Fan or Compressor, Turbine, nozzle and the exhaust jet (jet flows) in jet engine. Jet exhaust noise is created by the disturbance occur in turbulent mixing of the exhaust gases with the surrounding and its effected by the shearing action caused by the relative velocity between the jet exhaust and the surrounding. There are many attempt is made to understand the effect of various geometric parameters (design) of a chevron nozzle and similar like on noise prevention. This project shows the acoustics effects on chevron nozzle with various changes in geometry like including different number of chevrons tooth & changing the shapes of tooths also giving the appropriate nozzle among that which have nice output compare to others.
Keywords: Chevron Nozzle, Number of chevrons, tip angle, Penetration Length, Nozzle Pressure ratio, Sound Pressure Level, Noise Reduction, Acoustic Power level, Static and Total Pressure, Static and Total Temperature.
List of Symbols: = Penetration angle, = Tip angle, b = Base of chevron, h = Height of chevron, D = Exit diameter of nozzle, N = Number of chevron, L = Length of nozzle
-
INTRODUCTION
In today, the commercial engines are significantly more powerful and very less noise produces compare to commercial aircraft which were used in 70s and 80s. Even though, the reducing noise from aircraft in locality surrounding airports (aerodromes) is still in work. Aircraft manufacturers are works more and more to design engine which regulate the noise in airport localities. While aircraft takeoff and landing engine have high load to produce more thrust which will tends to give more noise compare to the aircraft at sky. Most research has been applied on jet engine nozzles to accelerate the mixing of the shear layers without reducing performance.
Out of all noise sources, aircraft noise is considered as the 2nd most disturbing noise (1st Rocket launch noise). People are very much concerned about the quality of their surroundings that noise is quoted as the first reason of bother. Nozzles are used to increase the velocity to get more thrust and also control the uniform direction of air-
fuel mixture flow come from turbine. In nozzle, the static energy (due to flow after turbine) is converted into kinetic energy and that kinetic energy create shear between flow and surrounding because of this noise will produced in jet engine. Thats why its necessary to reduce noise from the exhaust of nozzle for that we can do change in dimensions of nozzle and also we can change geometry of nozzle (like implementing new geometries). Chevron is a triangular tooth pattern on the circumference edge of exhaust nozzles, are being implement on modern jet engine nozzles that help to reduce noise from the resulting jet. Chevrons are used to reduce the acoustic level at the exhaust. The successful application of chevron nozzle to the aircraft engine is Boing747-8 which is powered by GEnx-2B67 engine and also ROLLS-ROYCE Trent 1000 jet engine
-
LITERATURE SURVEY
Malay Suvagiya, S. D. Sharma[1],On the effect of geometric parameters of chevron nozzle on generation of streamwise vortices in high subsonic jets, 20th Annual CFD Symposium, August 9-10, 2018, Bangalore. In this paper they shows the calculation of the exhaust chevron section after that they take various number id chevrons with different angle of chevron models for the analysis purpose & by using those calculation of exhaust section they find out the length of the chevron for that models. After that they perform the effect of the different geometric parameter on evolution of stream wise vortices produced by the chevron in the jet flow by using the software Ansys
cfx. They consider grid independence test in the mesh generation of nozzle. after that they do the numerical analysis of core velocity & circulation of the individual
chevron along jet & plot the graph of it at different position for those various designed nozzles.
P. Kaleeswaran, P. Shanmughasundaram[2],Experimental and Statistical analysis on the noise reduction using chevron nozzle in supersonic free jet, U.P.B. Sci. Bull., Series D, Vol. 78, Iss. 3, 2016 ISSN1454-2358. In this research paper the authors consider a supersonic free jet test rig with compressor & air tank. They consider nozzle as CD nozzle to produce supersonic flow. In the design purpose they consider 3 models one without chevrons 2nd 10 number of chevrons & 3rd 14 number of chevrons. They put sound level meter at the nozzle exit to measure the sound level for various pressure condition.& plot a graph of NPR to NOC for various condition of noise(dB).for the statical analysis they consider the three methods (a) Taguchi method, (b)ANOVA method & (c)multiple linear regression model. In which Taguchi method we find out S/N ratio for the measuring the sound & plot the diagram of response of s/n ratio w.r.t NPR &NOC. ANOVA technique is totally based on the software named as mini-tab for variance was employed to find statically significant parameters of noise level. In the last in MLR model they found the formula of noise with consideration of NPR & NOC. By comparing all 3 methods they conclude the result.
Daniel Crunteanu, Petre-Claudiu[3],Acoustic Characteristics of the flow over different shapes of nozzle chevrons, COJAN, DOI: 10.13111/2066-8201.2013.5.3.6.
In this paper authors analyzed four different shapes of chevrons to find out acoustic characteristics like acoustics power level . After the results they have been able to reveal that which is most efficient shape of chevron regarding noise reduction which attributing importance to research problem.
Vance Dippold III[4], CFD Analyses and Jet-Noise Predictions of Chevron Nozzles With Vortex Stabilization, Glenn Research Center, Cleveland, Ohio, NASA/TM2008-215150 March 2008 AIAA2008
0037. In this paper the wind computational fluid dynamics codes were used for perform a sequence of analysis on a single-flow plug nozzle with contains chevrons. Air was Entering from tubes tangent to the nozzle outer surface on three different points along with the chevron at the exit of nozzle: near at chevron notch, at the chevron middle-point, and near at chevron tip. Three entering pressures were used for each injection tube location10, 30, and 50 psig giving entering mass flow rates of 0.1, 0.2, and 0.3 percent of the nozzle total mass flow.
R. Kanmaniraja, R. Freshipali, J. Abdullah, K. Niranjan, K. Balasubramani, V. R. Sanal Kumar[5],3D Numerical Studies on Jets Acoustic Characteristics of Chevron Nozzles for Aerospace Applications, World Academy of Science, Engineering and Technology,
4 various type of the chevron nozzle & one simple nozzle. The numerical studies have been carried out using a validated steady 3D density based implicit, sandard, k- epsilon turbulence model using standard wall functions. This model uses a control-volume based technique to convert the governing equations to algebraic equations. The viscosity is determined from the Sutherland formula. The nozzle geometric variables and material properties are known a priori. They do the modeling of that various type of nozzles. For the analysis purpose At the exit, far field boundary condition is prescribed. Ideal gas was selected as the working fluid. they include the analysis like static pressure analysis, velocity effect analysis, turbulent kinetic energy analysis, acoustic intensity analysis. From this analysis they conclude some results.
Nevis Jenifer , Selva Preethi[6],Numerical Analysis of Chevron Nozzle with Various Configurations for Noise Reduction, International Journal of Innovative Research in Science, Engineering and Technology (An ISO 3297: 2007 Certified Organization) Vol. 5, Issue 5, May 2016. In this research paper author performing simulation for five different nozzle models- plain and chevron nozzle. Authors find out velocity magnitude and acoustic power level of all five types of nozzle. The expected graphical results are set to Acoustic power level along the full domain and Velocity Magnitude along the length of nozzle of five different cases. The analysis was carried out for nozzle with various type of chevron in CFD software.
-
sha Bharathi, B.Balamanikandan, J.Blessing sam paul, V,Naveen Sundar, Vikash[7],Effect of Chevron on Transonic Nozzle, International Journal of Engineering Research & Technology(IJERT), Vol. 4, Issue 04. In this research paper authors wants to find effect on transonic nozzle with using the different penetration length by keeping the diameter of exhaust & number of chevron fixed. The main results which mention is in the transonic nozzle with the chevron it also use for reducing the noise of the nozzle & it can be observed that by implement the chevron in the transonic nozzle the efficiency of the engine is not compromised. Practical applications of chevron nozzles on full-scale engines were investigated by this paper.
-
-
NOZZLE CONFIGURATION
In this Portion we calculated dimensional parameters like length of nozzle, inlet and exhaust diameter of nozzle, number of chevron, length of chevron for design of baseline and chevron nozzle (Any chevron nozzle).
Simple triangular chevrons are used for present configuration study. Geometry of a chevron nozzle is defined by parameters such as number of chevrons (N), length of chevron (L), tip angle () and penetration angle (). Figure represents the simple schematic of the chevron geometry with its shape defining parameters.
Base of the individual chevron (b) can be calculated as,
International Journal of Aerospace and Mechanical Engineering Vol:8, No:9, 2014. In this paper they take various nozzle exhaust shape for the analysis purpose exact
b =
(1)
Relation between tip angle, base and length of chevron can be represented as
=
tan () =
(2)
2 2
So that , b= ×50.8 = 19.54 mm
8
For the length of chevron(L)
60
19.54
tan (
2
) =
2 ×
By combining and rearranging these equations, it gives
= 17.26
For the length of nozzle
= 4.25 ×
= 4.25 × 50.8
= 215.9
We consider the inlet diameter (Di) as 152.5 mm
() × tan () × = (3)
2 2
Length of the nozzle which is dependent on the exhaust diameter of the nozzle thats given as,
= 4.25 × (4) Height of the chevron
=
2
Where,
b = Base of chevron,
h = Height of chevron,
(5)
D = Exit diameter of nozzle, N = Number of chevrons,
Nozzle Pressure ratio(NPR):
= tip angle,
1
= Penetration angle,
NPR = = ( )
L = Length of nozzle
Form this formulas we can say that the length of the chevron is depends on the No. of chevron and tip angle for showing chevron configuration we can write simply as Nxy.
This relation suggests these basic parameters defining the geometry of chevron are interdependent and changing individual parameter without changing the other is not possible. Hence, chevron configurations are choose very carefully such that effect of individual parameter can be deduced from that.
For example designing of chevron nozzle we consider the exhaust diameter of nozzle is 50.8 mm, tip angle() as 60, penetration angle() as 5 and number of chevron (N) as 8 so the configuration will be N860.
For that nozzle the base of the nozzle, from Eq.(1)
Where, Pti = nozzle inlet pressure
Pte = nozzle exit pressure
Tti = nozzle inlet temperature Tte= nozzle exit temperature = Specific heat ratio
-
MODELING AND ANALYSIS
Nozzle design (Model): In this we are showing the design of various chevron nozzles used for analysis along with Base line nozzle too.
Design of BSL, Pallet and Inverse Pallet chevron nozzle
Design of chevron nozzle(NOC- 6,8,10)
Acoustic Power Level contours:
Acoustics power level gives the amount of noise produced as shown in figures where the analysis carried out. The acoustics power level is higher at the end of nozzle because of hot and cold air mixture and strength vortices.
Acoustic power level of BSL, Pallet and Inverse Pallet nozzles
Acoustic Power Level of Chevron nozzle(NOC-6,8,10)
Mach number contours:
Mach contour of BSL, Pallet and Inverse Pallet chevrons
Mach contour of Chevron nozzle(NOC-6,8,10)
Static Pressure contours:
Static Pressure of BSL, Pallet and Inverse Pallet chevrons
Static Pressure of Chevron nozzle(NOC-6,8,10)
Total Pressure contours:
Total Pressure of BSL, Pallet and Inverse Pallet chevrons
Total Pressure of Chevron nozzle(6,8,10)
Static Temperature contours:
Static Temperature of BSL, Pallet and Inverse Pallet chevrons
Static Temperature of Chevron nozzle(6,8,10)
Total Temperature contours:
Total Temperature of BSL, Pallet and Inverse Pallet chevrons
Total Temperature of Chevron nozzle(NOC-6,8,10)
Turbulent Kinetic Energy contour:
Turbulent Kinetic Energy of BSL, Pallet and Inverse Pallet
chevrons
Turbulent Kinetic Energy of Chevron nozzle(NOC-6,8,10)
Acoustic Power Level & Mach number graph: This Graph is showing the comparison of Acoustic Power level and Mach number of all Nozzles (BSL, Triangular chevron nozzle (NOC-6, 8, 10), Pallet and Inverse pallet Nozzle).
-
RESULT AND CONCLUSION
The result of this project is shown as the table defined below,
From this Result we conclude that increment of Number of Chevron will be decrease Acoustic Power level of the nozzle and in this project the NOC = 10 giving the lowest Acoustic power level comparing other nozzles so this type of chevron nozzle helps in noise reduction. From the result, the static pressure of chevron nozzle attains the optimum condition like the baseline round nozzle (little bit changes only). From Acoustic power level analysis we can conclude that it having the less value at the exit compare to the baseline nozzle. So thats how we can say chevron nozzle will produce less noise compare to Base line nozzle.
REFERENCES:
-
Malay Suvagiya, S. D. Sharma,On the effect of geometric parameters of chevron nozzle on generation of streamwise vortices in high subsonic jets, 20th Annual CFD Symposium, August 9-10, 2018, Bangalore.
-
P. Kaleeswaran, P. Shanmughasundaram, Experimental and Statistical analysis on the noise reduction using chevron nozzle in supersonic free jet, U.P.B. Sci. Bull., Series D, Vol. 78, Iss. 3, 2016 ISSN 1454-2358
-
Daniel Crunteanu, Petre-Claudiu, Acoustic characteristics of the flow overdifferent shapes of nozzle chevrons, COJAN, DOI: 10.13111/2066-8201.2013.5.3.6
-
Vance Dippold III, CFD Analyses and Jet-Noise Predictions of Chevron Nozzles With Vortex Stabilization, Glenn Research Center, Cleveland, Ohio, NASA/TM2008-215150 March 2008 AIAA20080037
-
R. Kanmaniraja, R. Freshipali, J. Abdullah, K. Niranjan, K. Balasubramani, V. R. Sanal Kumar, 3D Numerical Studies on Jets Acoustic Characteristics of Chevron Nozzles for Aerospace Applications, World Academy of Science, Engineering and Technology, International Journal of Aerospace and Mechanical Engineering Vol:8, No:9, 2014
-
Nevis Jenifer , Selva Preethi, Numerical Analysis of Chevron Nozzle with Various Configurations for Noise Reduction, International Journal of Innovative Research in Science, Engineering and Technology (An ISO 3297: 2007 Certified Organization) Vol. 5, Issue 5, May 2016
-
A.Usha Bharathi, B.Balamanikandan, J.Blessing sam paul, V,Naveen Sundar, Vikash, Effect of Chevron on Transonic Nozzle, International Journal of Engineering Research & Technology(IJERT), Vol. 4, Issue 04, April 2015.
-
Grigore Cican, Virgil Stanciu, Daniel-Eugeniu Crunteanu, Acoustic control study of turbofan nozzles with triangular chevrons, INCAS bulletin, ISSN 2066 8201, Volume 6, Issue 1/ 2014, pp. 13 20.
-
Sasi kumar M., Abirami K., Sandhiya K., Vijay G. and Vishnu Varthan S., Noise reduction and thrust enhancement in various modified chevron nozzle, International Journal of Development Research, Vol. 08, Issue, 01, pp.18540-18544, January, 2018.
-
G. A. Sivasankar, S. Balamurugan, Virtual Analysis of Chevron Nozzle Lobe Design Modification, Asian Journal of Research in Social Sciences and Humanities Vol. 7, No. 1, January 2017, pp. 79-86.