
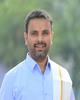
- Open Access
- Authors : Suhas U , Dr. K N Shashidhara , Dr. Bharath L
- Paper ID : IJERTV12IS030071
- Volume & Issue : Volume 12, Issue 03 (March 2023)
- Published (First Online): 21-03-2023
- ISSN (Online) : 2278-0181
- Publisher Name : IJERT
- License:
This work is licensed under a Creative Commons Attribution 4.0 International License
Mechanical Characterization of Copper and Aluminium Powder Reinforced Epoxy Polymer Composites
Suhas U Research scholar, Assistant Professor
Department of Mechanical Engineering
Cambridge Institute of Technology, Bengaluru, Karnataka, India
Dr. K. N. Shashidhara
Professor Department of Mechanical
Engineering Cambridge Institute of Technology
Bengaluru, Karnataka, India
Dr. Bharath. L
Assistant Professor Department of Mechanical Engineering
Cambridge Institute of Technology, Bengaluru, Karnataka, India
Abstract: This article describes the manufacturing process of a polymer composite made with epoxy and reinforced with aluminum and copper powder using the open-mould vacuum technique. A new type of composite material was developed by combining copper and aluminum powders in weight percentages of 5%, 10%, 15%, and 20%. The mechanical properties of the composite were evaluated, including hardness, tensile strength, percentage elongation, flexural strength, and impact strength. The results of the experiments revealed a significant increase in tensile strength, flexural strength, and impact strength for both types of composites up to 15wt.%. However, the percentage elongation decreased as the weight percentage of the metal powder increased for both types of composites.
Keywords – Epoxy, Aluminum, Copper, Hardener, Flexural strength.
-
INTRODUCTION
Casting is a manufacturing process where molten metal is poured into a refractory mould cavity of the shape and size followed by solidifing. When hardened structure is obtained, the object is seperated from the mould [1]. The need for new class of materials to contest wear situation has resulted in the development of polymer based composites [2]. Composite material consists of matrix material and additives as reinforcement so as to enhance the strength of matrix material. Opting of composites depends on various factor which inculdes working life time, number of items to be produced, skill of the designer and complexity of the product [3]. It was stated that, the properties of composites depends on shape and size of particles, physical properties of aprticels, surface area of particle, content of reinforcement materail and adhesion force between metal particle and matrix [4]. Polymer Matrix Composites [5] can exhibit exceptional properties with the combination of particels as filler like toughness, stiffness [6], thermal consudtivity, compression strength, ductility [8] and many more. Reinforcements are typically stiff, hard materials usally of ceramics, glass or metal where as matrix are generally ductile and tough like polymers [7]. Inclusion of hard ceramic particles, such as silicon carbide, boron carbide, and alumina, has been observed to enhance the mechanical and wear properties of epoxy[9]. Thermo-set epoxy resins are
widely employed as a matrix material for composite structures and in aerospace applications due to their high mechanical properties, ease of fabrication, excellent chemical and moisture resistance, and good wettability. [10]. The use of composite structure have flourised recently to include a large number of new applications. Composites materials [11] are now considered to be competitive with other materials in different applicational area [12]. Conventional test methods are initially beign used for determining the mechanical properties of metalsand other homogenous and isotropic construction materails [13]. Many studies have been conducted on the fabrication and structure property of metal oxide nanoparticles. Several studies indicated that the excellent properties of nano composites depends on dispersion of particles and manufacturing method [14]. Segun M. Adedayo and Modupe A. Onitiri [15] reported that better yield strength was recorded for incresing the percentage volume content and at reduced particle size in epoxy reinforced with iron ore. J Stabik et al [16] in their investigation Polymer Graded Materials with different amount and sort of fillers are presented and conculded that composites can be prepared up to 50% vol. of filler powders based on the manufacturing process. Higher amount of filler material in matrix resulted in viscosity being increasesd, which did not allow to cast and fabricate the tolerable sample.
By this circumstantial, even though several investigation done on polymer composites, a systematic investigation with the copper and aluminum as filler for epoxy resin has not been accomplished. So in order to fill this research gap, the objective is to fabricate the epoxy based polymer composite with copper and aluminum as filler by variying 5wt.%, 10wt.%, 15wt.% and 20wt.%. Mechanical properties like hardness, percentage of elongation, tensile strength, and flexural strength were evaluated. Emperical data obtained from the above properties will be compared with Dr. Sihama Issa Salih [4] and K .S. Harishanand [14].
-
EXPERIMENTAL DETAILS
This chapter covers several topics, including the selection of matrix and filler materials, the formation of
Epoxy polymer composites, and the preparation of hardness, tensile, and flexural test specimens.
-
Material selection
In this investigation, Epoxy (LY556) and Hardener (HY951) is used as a matrix material. The filler materials are copper and aluminum powder with average size of 50µ are shown in Figure 1. The properties of filler material are shown in Table 1.
(a) Copper Powder (b) Aluminum Powder Figure 1: Filler Materials
Properties
Aluminum
Copper
Density (g/cc)
2.68
8.96
Tensile strength (GPa)
0.3
0.2
Tensile Modulus (GPa)
70
119
Thermal Conductivity (W/m- K)
237
401
Bulk Modulus (GPa)
76
140
Table 1: Properties of Aluminum and Copper filler material
-
Processing of polymer composite
Composite samples were prepared using open mould vacuum casting technique to obtain test specimens by loading filler material (Copper and Aluminum powder) at 5wt.%, 10wt.%, 15wt.% and 20wt.%. An open mould cavity as shown in figure 2 have the cavity dimensions of 225×225×3mm is used to fabricated the epoxy-based polymer composites. The powders are subjected to a preheating process at 80 for 2 hours to eliminate any moisture that may be present, after which they are cooled to ambient temperature. The weighed quantity of the powder is added into the liquid epoxy resin and stirred gently for 10min. After preparing the resin and filler mixture, it is placed in a vacuum chamber as shown in figure 3 for 2 hours to eliminate any trapped air. The hardener is then added to the resin in a 1:10 ratio and thoroughly mixed. The resulting mixture is poured into an open metallic mould that has been coated with wax material, and cured for 24 hours. The resulting polymer composite is then removed from the mould, with dimensions of 225x225x3mm. Finally, the composite is post-cured in a hot air oven at 50°C for 2 hours.
Figure 2: Open Mould Cavity
Figure 3: Vacuum chamber
-
Epoxy without reinforcement
-
Epoxy with 5wt.% Cu (c) Epoxy with 10wt.% Cu
(d) Epoxy with 15wt.% Cu (e) Epoxy with 20wt.% Cu
Figure 4 (a-e): Fabricated samples of Epoxy and Epoxy/Cu composites.
(a) Epoxy with 5wt.% Al (b) Epoxy with 10wt.% Al
(c) Epoxy with 15wt.% Al () Epoxy with 20wt.% Al
Figure 5 (a-d): Fabricated samples of Epoxy and Epoxy/Al composites.
-
-
Preparation of test specimens
The fabricated samples of Epoxy and its polymer composites were prepared for Vickers Hardness test, Tensile test, and Flexural test specimens as per D785, D638, and D790 ASTM standard size to evaluate the experimental values.
-
-
RESULTS AND DISCUSSION
In this section, Vickers hardness number, Tensile strength, Impact strength, Flexural strength and percentage elongation
were discussed by varying wt.% of filler material in epoxy material.
-
Percentage of elongation
-
Vickers Hardness Number
Percentage Elongation (%)
2.5
2
100
95
90
85
80
75
Hardness (VHN)
1.5
wt.% of Al
wt.% of Cu
1
0.5
0
0 5 10 15 20
wt.% of metal powder
wt.% of Al wt.% of Cu
0 5 10 15 20
Wt.% of metal powder
Figure 6: Variation of Hardness v/s wt.% of filler material.
Figure 6 reveals that as wt.% of filler material increased in epoxy base the hardness of the polymer composite increases. It is observed that for copper filler material exhibits more hardness value when compared to aluminum filler material. Polymer composites show higher hardness when compared to unreinforced composite or epoxy material alone. This increase in hardness is due to the presence of metal particles in the epoxy matrix material.
-
Tensile Strength (MPa)
-
Figure 8: Variation of percentage elongation v/s wt.% of filler material.
Figure 8 shows the decreasing trend for percentage elongation with increase in wt.% of filler material in both copper and aluminum powder. This decreasing trend is due to the increase in hardness of metal powder in epoxy. As wt.% increases the polymer composite will become harder which resulted in decreasing trend. These results are contrary to the observation made by K.S. Harishanand et al [14] in metal oxide content in neat epoxy study.
D. Flexural Strength
Tensile Strength (MPa)
80
70
60
50
40
30
20
10
0
0 5 10 15 20
wt.% of metal powder
100
80
60
40
20
0
wt.% of
Al
wt.% of Cu
Flexural Strength (MPa)
wt.% of Al
wt.% of
0 5 10 15 20
wt.% of metal powder
Cu
Figure 7: Variation of Tensile Strength v/s wt.% of filler material.
It is observed from figure 7 that the tensile strength of formed polymer composite exhibits more value than the epoxy material. It is due to the homogeneous distribution of filler material and hard metal powder. For 15wt.% of filler material shows higher tensile strength for both copper and aluminum powder in epoxy material. Beyond 15wt.% tensile strength found to be decreased which is attributed due to nonuniform mixture between filler material and epoxy. Similar results were obtained by Dr. Sihama Issa Salih et al [4] in their findings.
Figure 9: Variation of Flexural Strength v/s wt.% of filler material.
Figure 9 shows the plot of Variation of Flexural Strength v/s wt.% of filler material. It is observed that the flexural strength of epoxy reinforced polymer composite with aluminum and copper exhibits increasing trend up to 15wt.%. Beyond 15wt.% the flexural strength decreased which is attributed due to the density variation and also non uniform dispersion of metal powder in the epoxy material. These findings agreed with previous reports on polymer composites [4 & 14].
III. CONCLUSION
This paper deals with fabrication of epoxy-based polymer composite reinforced with copper and aluminum powder. Open vacuum casting technique can be adopted for processing of polymer composite material. Highest hardness, Tensile strength, flexural strength was observed
for 15wt.% of filler material for both the copper and aluminum reinforced polymer composite. It is clear that copper reinforced polymer composites show higher mechanical properties when compared with aluminum reinforced polymer composite which is due to higher tensile modulus and density of copper. Significant improvement was observed for tensile strength and flexural modulus for copper reinforced polymer composite when compared with unreinforced epoxy material. i.e 83.66% and 83.47% respectively. However, improvement in hardness on copper reinforced epoxy material is only 15.62%.
ACKNOWLEDGEMENTS
I want to convey my heartful thanks to my research supervisor Dr. K N Shashidhara for the valuable suggestions and guidance during every stage of my research work.
I thank Mr. Bharath L for providing vital inputs in the preparation of write up of this research article to meet the requirement of journal standard.
We thank Visvesvaraya Technological University (VTU), Belagavi for the continuous support for carrying out the research work.
[13] Yibowei Moses, Ichetaonye Simon, Idehenre Maxwell, Mechanical Properties of Carbon Fibre and Metal Particles Filled Epoxy Composite IJETAE, ISSN:2250-2459, Vol.3, Issue 11, pp.664-667. [14] K.S. Harishanand, H. Nagabhushana, B.M. Nagabhushana, Parimesh Panda, Richeek Gupta, M.S. Muruli, N. Raghavendra, and K.R. Vishnu Mahesh, Comparitive Study on Mechanical Properties of ZnO, ZrO2 and CeO2 Nanometal Oxides Reinforced Epoxy Composites Advances in Polymer Science and Technology: An International Journal, ISSN:2277-7164, Vol.3(1), pp.7-13. [15] Segun M. Adedayo a and Modupe A. Onitiri, Tensile Properties of Iron Ore Tailings Filled Epoxy Composites The West Indian Journal of Engineering Vol.35, No.1, July 2012, pp.51-59. [16] J. Stabik, A. Dybowska, M. Chomiak, Polymer composites filled with powders as polymer graded materials JAMME, Volume 43, Issue 1, November 2010, pp.153-161.REFERENCES
[1] Danuta Matykiewicz, Hybrid Epoxy Composites with Both Powder and Fiber Filler: A Review of Mechanical and Thermomechanical Properties, Materials 2020. [2] B. Suresha, B.N. Ramesh, K.M. Subbaya , B.N. Ravi Kumar, andG. Chandramohan, Influence of graphite filler on two-body abrasive wear behaviour of carbon fabric reinforced epoxy composites Materials and Design 31 (2010) 1833-1841.
[3] Samjid Bava T, P. Lingeswaran, Synthesis and Characterisation of Epoxy Matrix Composites Filled with Aluminium Powder, IRJET, Volume: 05 Issue: 06, June 2018, pp 219-223. [4] Dr. Sihama Issa Salih, Safaa Nayyef, Alyaa H .Abd Alsalam and Ammar Mousa Hasan, Evaluation Mechanical Properties of Polymer Composites Reinforced by different Metal Powders ICNAMA 2013 (3-4 Nov.2015), Eng. & Tech.Journal, Vol.33, Part (B) No.7, pp.1348-1360. [5] Anshul Verma and V.K. Srivastava, mechanical behavior of metal particles reinforced polymer matrix composites IJMPE,Volume-3, Issue-6, ISSN:2320-2092, pp.104-108. [6] Amal Nassar and Eman Nassar, Study on Mechanical Properties of Epoxy Polymer Reinforced with NanoSiC particles Nanoscience and Nanoengineering 1(2), pp.89-93. [7] Mohammed Abdulsattar Mohammed, Mechanical Behavior for Polymer Matrix Composite Reinforced By Copper Powder NUCEJ, Vol.14, No.2, 2011, pp.160-176. [8] P.Amuthakkannan, K.Arunprasath, W.Santhosh, S.Ragurajan, S.Saravanan, Experimental Investigation on Mechanical Properties of Copper Slag Powder Reinforced Particulate Polymer Composite, International Conference on Engineering and Technology (ICET), 2016. [9] Mudradi Sudheer, Ravikantha Prabhu, Kandavalli Raju, and Thirumaleshwara Bhat, Effect of Filler Content on the Performance of Epoxy/PTW Composites Advances in Materials Science and Engineering, Volume 2014, pp.1-11. [10] J. S. Sidhu, G. S. Lathkar, and S. B. Sharma, Mechanical properties of micro tungsten disulphide particles filled epoxy composite and its resistance against sliding wear Malaysian Polymer Jurnal, Vol. 9 No. 1, 2014, pp. 24-32. [11] L. Bharath, M.S. Reddy, H.N. Girisha, G. Balakumar, Influence of process parameters on tensile strength and hardness of AW2024/B4C composite using Taguchis technique Materials Today: Proceedings, Elsevier ISSN:2214-7853. [12] Ranganatha S R, Dr.V.S.Ramamurthy, Investigation on mechanical behavior of filler Al2O3 in CFRP composites IJAET, E-ISSN 0976-3945, PP.105-107.