
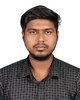
- Open Access
- Authors : G. Mohamed Hussain , K. Kathick Kumar , M. Vishnu Prasath , B. Senthilkumar
- Paper ID : IJERTV11IS060246
- Volume & Issue : Volume 11, Issue 06 (June 2022)
- Published (First Online): 20-07-2022
- ISSN (Online) : 2278-0181
- Publisher Name : IJERT
- License:
This work is licensed under a Creative Commons Attribution 4.0 International License
Increasing The Properties of Steel by Diffusing Intermetallic Substance
-
Mohamed Hussain1, K. Kathick Kumar2, M. Vishnu Prasatp, B. Senthilkumar4
1 2 3 UG Students,
4Associate Professor Department of Mechanical Engineering,
Kumaraguru College of Technology, Coimbatore, Tamil Nadu, India
Abstract Surface coating is an efficient and cost-effective way to achieve desirable surface properties. Among the surface modification techniques diffusion is the most cost-effective way incorporate desired properties to surfaces. Current investigation is focused on This study investigated aluminizing the steel surface through hot dip coating technique. Experiments were carried out on mild steel substrates with a thickness of 5mm. The substrates were immersed in molten aluminium kept at 750C for a duration of 30, 60, and 90 minutes. This investigation included hardness survey across the specimen. The hardness of the steel found to vary with the change in the depth, dipping temperature and time. As a result of this treatment improved surface properties were observed in the specimens after treatment.
Keywords: Diffusion, Surface coating, Intermetallic, Fe-Al, Microstructure
-
INTRODUCTION
Steel is a versatile Engineering material preferred by the design engineers because of its strength, ductility, ease of fabrication and low cost. Even though new advanced materials have been developed nowadays, steel remains preferred choice in construction, automobiles, appliances, industrial machinery as well as in the nuclear industry. The limitations of Steel are low corrosion resistance, hardness and wear characteristics. These properties can be improved by expensive alloying additions. Most of the Engineering failures do originate from the surface, so these surface properties play a vital role in deciding the durability of the components used in the aggressive environments like earth moving equipment and agricultural equipment. In this context, it has been proposed to modify the surface alloy content to meet the necessary service requirements demanded in the aggressive environments. Surface coating is another avenue to impart desirable surface properties like hardness and corrosion resistance economically. Various methods adopted to modify the surface properties are classified into thermal, thermomechanical, ion implantation, plating and coating. Some of these processes result in increased material build also, need to be considered when dimensional stability is an important criterion. Diffusion based surface alloy modification techniques offers attractive alternative over plating and coating techniques. It is important to identify the element to diffuse ranges from Carbon (Carburizing), Nitrogen (Nitriding), Carbo nitriding, Chromizing, Aluminizing, Boronising etc., In which, Aluminizing offers comparatively low cost and better surface characteristics over other materials [4]. In hot dip aluminizing, when steel is in contact with a
molten aluminium maintained at a temperature for a specific period, diffusion occurs to form a brittle interlayer of intermetallic compounds. The intermetallic layer develops between the steel substrate and the coated aluminium [3]. The intermetallic layer grows and dissolves concurrently into the molten aluminium, which is directly associated with the loss of the steel substrate [5-7]. The growth and dissolution rates of the intermetallic layer determine the thickness of the layer. The rates are closely related with the temperature of the molten aluminium and dipping time of the steel. The thickness of the layer also varies depending on chemical composition of the molten aluminium [2]. Aluminium is very successful as a protective coating for steel because of its self-healing passive layer. Any improvement in the wear and corrosion properties will result in significant cost saving. However, the adhesion between coating and substrate by formation of the intermetallic phase is important to be investigated to produce strong and durable coating. The wear behaviour of the Fe-Al intermetallic coating was found to vary significantly with temperature and load [1].
-
OBJECTIVE
The properties of low carbon steel meets most of the strength- based requirements except wear and corrosion resistance. The objective of this investigation is to improve the surface properties like wear and corrosion resistance. The hard intermetallic layer produced through diffusion It will result in the improvement of durability of the component by coating intermetallic coating using diffusion method.
-
METHODOLOGY
-
Material Selection
Specimens were made from low carbon steel substrate (IS:2062). This has high tensile and good yield strength, good mechanical strength, flexibility, hardness and toughness. This is the most common substance that used in construction, automobile industry and in nuclear industry. The composition of the substrate material is presented in the table 1.
Material
Elements (% wt.)
C
Mn
Si
S
P
Cr
Ni
Mo
N
Fe
Base metal (IS: 2062. GR. B, ASTM A36)
0.196
1.12
0.293
0.011
0.0044
0.128
0.336
0.275
—
Balance
Table 1 Substrate composition
-
Specimen Preparation
The specimen preparation is described as follows. The specimens were annealed at 750C to remove any residual stresses and refine the grain structure. The surface oxide layer is removed by grinding and followed by polishing by abrasive papers of coarse, medium and fine grades. At the end of surface preparation,
Figure 1. Specimen
the surface roughness was measured and presented in the table
2. The figure 1 and figure 2 shows the specimens before and after grinding. The holes were made in specimens for the purpose of immersion and retrieval during diffusion process. Also, the specimens were numbered for the identification during post diffusion characterization.
Table 2: Surface roughness measurement details
Specimen No
Direction
Surface roughness ()
1
Longitudinal
0.12
Transverse
0.17
TABLE 3 Specimen dimensions
Length
55mm
Breadth
30mm
Thickness
5mm
Volume
8250mm3
Figure 2. Specimen after surface grinding
-
-
HARDNESS TEST
The hardness of the specimens was tested before the diffusion. It is required to compare hardness values before and after the diffusion process. Rockwell and Vickers hardness tests were performed before diffusion treatment of the specimens.
Hardness of each specimen was taken at three different locations and average value is for better understanding of the hardness value. All those values were tabulated below in table 4.
TABLE 4 Rockwell Hardness Values before Difussion
Specimen No
Average hardness HRC
1
61.3
2
60.
3
61.3
4
60
5
59
6
59
7
60.3
8
57.6
9
58.6
10
60
11
59
The graphical representation of the hardness test of the specimens is shown in the figure 6. It is observed seen that the overall average of the hardness is 59.6.
Figure 6. Graph of hardness test values
-
DIFFUSION
Diffusion is carried out using STIR CASTING FURNACE. The aluminium is placed inside a crucible and melted at 750C using the furnace. Once the aluminium is melted the steel specimen is placed inside the furnace and the diffusion is conducted at three different timings 30, 60 and 90 minutes at 750C. Once the diffusion is finished the specimen is quenched in water. The unwanted aluminium coatings were
removed by SiC sheets.
-
VICKERS HARDNESS TEST
The hardness test is performed by using vickers hardness testing machine. The diffused specimen hardness values are tabulated in table 5.
Specimen
Position
Scale
VHN
Untreated
1
0.718
17.99209154
2
0.742
16.84700598
3
0.695
19.20263961
4
0.689
19.53853948
5
0.736
17.12280504
30 min
1
0.436
48.79300459
2
0.553
30.33054946
3
0.652
21.81902546
4
0.6
25.764875
5
0.424
51.59395581
1
0.3
103.0595
2
0.563
29.2626566
TABLE 5 Vickers Hardness Values after diffusion
60 min
3
0.7
18.92929592
4
0.618
24.28586577
5
0.3
103.0595
90 min
1
0.3
103.0595
2
0.323
88.90485867
3
0.621
24.05178651
4
0.523
33.90995105
5
0.287
112.6073523
It is found that the surface properties of the steel specimens are improved by diffusing FeAl intermetallic coating. The purpose of this project is to incorporate this method into the industry. This mainly focuses on agricultural equipments where the wear and tear are more which needs to be replaced over and over. By implementing this technique, the life span of the equipments are improved.
The formula used for calculating the VICKERS HARDNESS NUMBER is,
VHN= (2P sin136/2)/d2 VHN= 1.8544 (P/d2)
Where,
P= load applied,
d2=square of total scale value.
From the table we can able to understand that the hardness improves with more dipping time of diffusion and the hardness is diffused specimen is greater than that of untreated specimen. This proves that the properties of steel is improved by diffusion.
-
ELEMENTAL ANALYSIS
Element analysis is done by using SPECTROMAXx . The result shows that the aluminium has diffused into the steel by the means of diffusion. The composition of diffused specimen is presented in the table 6.
TABLE 6 Composition of diffused specimen
REFERENCES
[1] Q.Y. ZHANG et al, Wear Behavior and Mechanism of Fe-Al Intermetallic Coating Prepared by Hot-Dip Aluminizing and Diffusion Metallurgical and Materials Transactions A 47, no. 5 (2016): 2232-2242., Published: 03 March 2016
[2] Naoki Takata et al, Morphology and formation of Fe Al intermetallic layers on iron hot-dipped in Al Mg Si alloy melt, Intermetallics 54 (2014): 136-142. [3] Zimu Shi , Preparation and characterization of FeAl intermetallic layer on the surface of T91 heat-resistant steel , Journal of Nuclear Materials 447, no. 1-3 (2014): 77-81. [4] Y. B. Lin, T. F. Chen Et al, Diffusion and plasma oxidation mechanism of FeAl coatings, Surface Engineering 31, no. 5 (2015): 329-334. [5] Tomasz Chmielewski et al, "Structure and selected properties of arc sprayed coatings containing in-situ fabricated Fe-Al intermetallic phases." Metals 8, no. 12 (2018): 1059. [6] T Varol, E. M. E. L., A. Y. K. U. T. Canakci, S. Ozsahin, F. A. T. . H.Erdemir, and S. Ozkaya. "Artificial neural network-based prediction technique for coating thickness in Fe-Al coatings fabricated by mechanical milling." Particulate Science and Technology 36, no. 6 (2018): 742-750.
[7] Krzysztof Karczewski, Crystalline oxalic acid aided FeAl intermetallic alloy sintering. Fabrication of intermetallic foam with porosity above 45% Materials letter 164 (2016) 32-34.Fe
Al
C
Cu
Mg
98%
0.58%
0.012%
0.214%
0.0190%
The presence of Aluminium in Steel is 0.58%.
-
RESULT AND CONCLUSION
-
The hardness value for the specimens after diffusion is greater than that of before diffusion. This will prove that the diffusion coating of FeAl intermetallic coating improves the surface properties. The elemental analysis shows that the Aluminium is merged with the Steel forming a stronger bond.
Figure 7. Graph of Vickers Hardness Number