
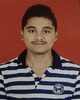
- Open Access
- Authors : Gangappa K. Ingalgi , A. H. A. R. Shaikh , Payal S. Pawar
- Paper ID : IJERTV10IS060383
- Volume & Issue : Volume 10, Issue 06 (June 2021)
- Published (First Online): 01-07-2021
- ISSN (Online) : 2278-0181
- Publisher Name : IJERT
- License:
This work is licensed under a Creative Commons Attribution 4.0 International License
Increases the Superconductivity and Mechanical Power for Open Body Type Electrical Motors
Mr. Gangappa K. Ingalgi.
Electrical Engineering, VVPIET solapur, Dbatu University, Solapur, India.
Prof. A. H. A. R. Shaikh Electrical Engineering, VVPIET solapur,
MSBTE Mumbai. Maharashtra, Solapur, India.
Prof. Payal S. Pawar. Electrical Engineering, VVPIET solapur, Dbatu University, Solapur, India.
Abstract- The super conducting mode is important role in three phase induction motor. Efficient performance of three phase induction motor depends on losses due to internal resistance of copper and losses due to friction and some losses is due to heating effects due to heavy load. Superconducting mod is works on principle of to avoid the various losses like friction loss, heat loss, internal resistance of copper loss, weekends of flux density due to various reasons like carbon present on copper conductors, increase the resistance of copper conductors, internal resistance of material of rotor, Eddy current loss, axial structure loss, etc. Superconducting mode is activated modern expert cooling is involved in three phase induction motor. All rotating electrical machines generate heat as a result of the electrical and friction losses inside the motor. Losses are high during starting or dynamic variation load. The system used to describe the method of cooling is currently being changed by expert cooling. Another to avoid the losses techniques is also used by using sound intensity graph, that sound is taken from bearings to determine the Grease level increases or decreases. This technique for that method are many benefits like to know about how much heat is produced inside the motor to determine the discharge rate of cooling air to motor. The efficiency can be increased by reduction in temperature, cooling performance as well as by using convalescent materials or by improving electromagnetic performance a good motif. This paper presents the relationship between the efficiency or the losses and the temperature of coils by changing the framework such as the load, the flow rate of cooling air. Coil temperatures variation affects much on the efficiency. The inner cooling technique is better than that of outer cooling for the coil temperature scaling down. Several cooling methods are compared concentrating on the fan efficiency and performance, from which the values of the efficiencies of the motors are expected. The fan logicality furthermore the fan performance should be considered for the most advantageous fan design to increase the total logicality of a motor.
Keywords- Superconductivity technique, filter pads, oscillation distortion, cooling design, losses detect.
-
INTRODUCTION
Conductors lose their entire electrical phenomenon when cooled to super-low temperatures. It must be recognize that superconductivity is not merely an extrapolation of most conductors tendency to moderately lose resistance with diminish temperature; rather, it is a without warning, quantum leap in resistivity from finite to nothing.[1] A superconducting material has absolutely zero electrical resistance, not just some minor amount. Various types of cooling methods are involved to avoid the resistance for
superconductivity due to super low temperature. Various types are used like the ring shaped water cooling treatment, by using sound variation waves to determine the greasing level in bearings, various types of fans and their materials, atmospheric cooling method and also used efficient techniques in cooling method proportional to heat variation, some cooling methods are used from solar energy, all combinations cooling methods are in one implemented on three phase induction motors to avoid the insulation and conductor and friction losses are decreases for to active the superconducting mode in three phase motors.
When various types of cooling methods are used to three phase induction motors but power consumption of cooling methods are attached to external line supply in this paper how to efficient method without any lime energy is used.[4] In this paper to study about how to efficient cooling method are used without any external line supply. Efficient cooling methods like solar refrigeration method; how to cool the heated water i.e. heat dissipates water (HDW) by using atmospheric cooling is used.
-
WHY PURE AIR IS NECESSARY FOR COOLING. Pure air is very important role in cooling of three phase induction motors. Many contains are involved in an unpuredair like harmful gases, nitrogen dioxide, sulphur dioxide, carbon monoxide, particulate matter, etc. Air is zilch but a concoction of a multifariousness of gasses. The air in the atmosphere is formed of nitrogen, oxygen, which is the life preserving substance for beasties and humans, carbon dioxide, water vapor and small amounts of other elements. [2]
Figure 1: Effects due to impure air
Unfortunately many facts on metal body of induction motors due to polluted air or unpurified air. The materials most responsive to pollutants are calcareous building ferrous metals. Demonstration of damage includes losses of mass, changes in porosity, discoloration and brickie. Some of the effects of erosion incorporate a significant deterioration of natural and historic monuments to increase the risk of fatal disastrous equipment failures.
Unfiltered air is most effects on bearings. Greasing level present in bearings and when cooling is attached or internal cooling system is attached to the induction motor solid contains are present in unpurified air to causes the sound or increase the frictional losses in the motor. Pure air cooling system is the most important role in inter cooling system or air force internal cooling system is used for open body motors. Maintenance life of three phase induction motors is less due to an impure air used for cooling system.
Many disadvantages due to of this air for cooling method like performance of motor decreases, heat is produced, life of bearings are reduced, rusting of copper windings slowly, weak the insulation level, week or change the size or dimensions of bearing balls due to the unbalanced load, vibration of motors is increases, load current increases on cables or terminal cables, motor consumes more current, slowly rusting of metal body, etc.
-
FRICTIONAL LOSS IN BEARING
Bearings are the most important role in the induction motor or three phase induction motor. Many types of bearings are available in markets. A heap force is requires between the rotating shaft and the part that supports the rotation. Bearings perform the function of put a stop to damage from being done by this force to the part that supports the rotation, and also of keep in existence the correct position of the rotating shaft. Most bearings smooth the desired motion by minimizing abrasion. Lubrication is used to reduce friction. In the ball bearing and reel bearing, to lessen sliding friction, rolling elements such as reels or balls with a circular section are located between the races or digest of the bearing assembly
The main importance is greasing level in bearings, suppose greasing level is decreases in bearings various effects on bearings. Without lubrication or greasing bearings can be expected to fail early and possibly cause other apparatus to stall. Rolling element bearings operate at their optimum temperature when the minimum amount of emollients used. Causes of greasing dry out.
-
Incompatible Grease:
Accidental mixing of grease can lead to accelerate de- gelling and oil separation. There are many Grecian examples of this, inclusive of the come into conflict of organic clay grease with soap-thickened grease.
Figure 1: Rusting due to low life grease in bearing
-
Extreme heat dryness:
Grease made from low-viscosity base oils is at the highest risk of boiling away. At adequately high temperatures, oil can boil out of the thickener matrix, causing solidifies of the grease over time. I.e. lower oil-to-thickener quantitative relation and higher base-oil viscosity.
-
Conflicting Grease:
Accidental mixing of grease can lead to accelerate de- gelling and oil separation. There are many classical examples of this, including the come into the conflict of biotic clay grease with soap-thickened grease.
-
-
HOW TO SENCE THE LEVEL OF GREASE
Figure 3: More distortion at low greasing level
In above picture, grease level is low so to produce unbalance the waveform from taken mobile (at 92% accuracy) oscilloscope. This image is taken from the motor at works long time so grease level is slow down. In this oscilloscope, distortion is mores.
Grease is mostly used for electric motors because bearings are smoothly run.
Figure 4: less distortion at high greasing level
In this above picture, this motor is greased so distortion is small while running condition. The friction losses are less compare to the ungreased motors so this main matter of maximum efficiency of motors.
The consequence of an electric motors bearing grease is to:
-
Reduce friction and prevent wear.
-
Protect bearings against corrosion.
-
Act as a seal to prevent entry of contaminants Tackiness: Grease tackiness should be appropriate for the
load and Speed of the application at operating temperature. This will help to maximum protection and constituent life. The typical mineral oil Tackiness in Electric motor grease is in the range of 499 to 599 SUS at 100°F.
-
-
SPECIFIC RECOMMENDATION.
-
Evenness: Greases evenness is one of its most visible characteristics. Greases consistency is stated in terms of its NLGI (National Lubricating Grease Institute) grade, which ranges from 000 to 5.8. The evenness of grease should be appropriate to the Application as it affects pump ability and ability to reach the Areas to be lubricated. NLGI 2 grade grease is the most commonly used in electric motor.
-
Tarnish Resistance: Electric motor greases should have outstanding resistance to tarnish. This lengthens the life of bearings running at high speeds and high Temperatures. ASTM D 3336 High Temperature Grease Life test give a good indication when operating under extreme situation. Choose grease with a high ASTM D 3336 tarnish life.
-
Anti-wear: Unless a motor is mounted so there is a thrust Load on the bearings, it is generally advisable to use Grease without extreme pressure (EP) additives. EP Additives minuscule the life of the grease and should not be approving where they are not needed. On the other Hand, bearings designed to handle heavy stab loads may require grease with an EP additive.
-
-
ABOUT OPEN BODY MOTORS.
Open body motors yoke is made up of cast iron. But yoke structure is different according to decrease the weight of the motor. Ending two covers are also different structure according to same to decrease the weight of the motor. Has shown in below figure, this type of motors is very useful for high torque. But this type of motors is not useful for dusty area because dust is inserted into the motor body in rotor and stator air gaps and decrease the efficiency of open body motors, so in this paper how to use of this motors dusty area with helpful of filtered air passing for cooling purpose.
Figure 5: open body motors
-
COOLING DESIGN FOR OPEN BODY MOTORS.
In this design fully concentrated on how to minimize the dust present in air. In this below diagram, cooling design for open body motors. Cooling method is inbuilt structure in cooling tubes. The expectable things our air is cooled and cooling air passing through the filter pads and to decrease the dust occur in air.
Construction of cooling design for open body motors 1.Open or close cover: when air is, enter to filter pads dust is trapped in filter pads so to block the air that is open or closed cover to helps them to change the filter pads.
-
Water cooling tube: water cooling tube helps for cool the air. In this diagram cylinder type tubes are present. Water is filled out to cool the tubes so when air is collapse on tubes, air temperature is decreases. [3]
-
Primary filter pad: this filter helps for to remove the starting air dust and trip the water contains present in air due to cooling tubes.
Figure 6: Primary filter pad
-
Super filter adjustable pad: in this filter to trap the 90% dust removed so is known as super filter pads this pad is made up of honey gear filter pads.
Figure 7: Super filter pad
-
Breather: breather is useful for breathing the air at air blocking condition. When filter pads are so air is not passing through pads so vacuum is created and some occurs load on motor cooling fan so that condition helps the breathing.
VIII MODEL DESIGN OF COOLING
Figure 8: model design of cooling
-
Working principal of cooling design for open body type motors.
-
When the motor is start, cooling fan is also starting to rotate at that time to create the vacuum in cooling chamber, so air is flows from higher pressure to lower pressure. High- pressure air is collapse on water cooling tubes is known as water cooling tube. That cooling tubes are made up of zinc coated iron material. When high-pressure air is collapse on water cooling tubes, in high pressure air, heat contains are available so that heat particles are removed by water cooling tubes i.e. temperature is always flow from higher temperature to lower temperature. That cooler air is flowing to honeycomb cooling pad. This pad is made up of honeycomb, so filter the cooling air and also remove the water contains due to humidity. Some minor dust particles are present in this stage.
Then air is flowing to another filter pad is known as super filter pads. The main advantages of two filter pads is hybrid type means to remove easily or to holding easily due to external removable cover.External removable cover helps to remove filter pad when two major particles are trapped in filter so to maintenance of two filter pad. High-pressure air entire to directly into the motor cooling fan and that fan to increase the pressure of low pressure air collapse into the motor Body with pure air, but one breather attached to near the cooling fan in some away from filter pads. Breather is helps to breathing theair at air blockcondition due to low permeability of filter pads. When first and second filter pad are jammed due to dust contains present in air after some long time that situation air is trap towards the cooling fan of motor so vacuums is created, air is not flow to high pressure to low pressures, so that condition to helps the breather. Normal position of breather is high permeability.
-
ADVANTAGES
-
This type of motors is light in weight compared to conventional motors.
-
Performance is better.
-
Cooling air is circulates inner body of motors so conductor temperature is decreases so resistance is also decreases.
-
Superconductivity mode is up to 90% occur due to conductor temperature is decreases and runs at higher efficiency. [5]
-
-
DISADVANTAGES
-
Minor dust is flow in dusty area.
-
When filter pad is blocked vacuum is created and extra load is occurring on fan shaft if defect the breather.
-
Attachment contact between motor cooling cover and cooling design cover creates gaps if nut bolts are not tight.
-
-
CONCLUSION
-
We have concluded that, when fresh cooling air is used for directly on th conducts for open body motors, temperature is decreases so resistance goes also decreases and insulation resistance goes increases. Main think, the air is directly forced on the conductor with specific pressure so to get high superconductivity mode. Detect grease level by using oscilloscope, to help to know frictional losses because when filtered air is directly into rotor so some air is contact to bearing grease so viscosity is increases but due to rotational of rotor or shaft to maintain the viscosity.
REFERENCES
-
Benamrouche N, Haddad S, Bousbaine A, Low FW.Quantification of iron and stray load losses in induction motors using the temperature- time system. Quantification 1997; 20(2):91-6. ISSN 0263-2241.
-
miller p. reducing heavy-duty long haul combination truck fuel utilization and carbon-dioxide emissions. Boston: northeast states center for a clean air future; 2009.
-
Sun Yalong, Zhang Shiwei, Chen Gong, Tang Yong, Liang Fuye. Experimental and numerical investigation on a novel heat pipe based cooling strategy for motors. ApplThermEng 2020; 2020:170. Doi: https://doi.org/10.1016/j.applthermaleng.2020.114970.
-
Drofenik U, Stupar A, Kolar JW. Analysis of theoretical limits of forced- air cooling using filtering materials. IEEE Trans ComponPackagManufTechnol 2011:4.11(2011):528-35.
-
Laloya E, LucÃa Ó, Sarnago H. Heat removing process methods with high efficiency systems. IEEE Trans Power Electron 2016; 31.11(2016):7896-908.