
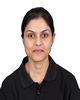
- Open Access
- Authors : Dr. Shilpa Narayanswamy , Nikhil Ghantial
- Paper ID : IJERTV12IS040115
- Volume & Issue : Volume 12, Issue 04 (April 2023)
- Published (First Online): 24-04-2023
- ISSN (Online) : 2278-0181
- Publisher Name : IJERT
- License:
This work is licensed under a Creative Commons Attribution 4.0 International License
Impact of 2D Barcoding on Reverse Supply Chain
Dr. Shilpa Narayanswamy
Associate Professor
Welingkar Institute of Management Development and Research, Mumbai
Nikhil Ghantial
MMS Operations
Welingkar Institute of Management Development and Research, Mumbai
Abstract :- Complexities associated with the supply chain have been increasing day by day. Industries are in a quest to modify their practices to win over the competition and thereby showcase their market presence. Technology has changed lives significantly in supply chain; efforts required to maintain data on register plus maintaining all the register from past in a place changed to maintaining an excel file and many more. Similarly, the focus of this paper is to highlight an aspect focused on traceability. Traceability is critical to quality (CTQ) in some of the industries, specifically pharma, specialty chemicals, automobile sector to name a few. Traceability can be forward and backward. With traceability, the whole history of products can be determined. To gain an insight into this, a case company was selected to study on their practices, and the various challenges were observed. Traceability in reverse supply chain was one among the major issues faced as the company spent a lot of time tracking the returned products. One such application and its benefits are showcased in our study whereby using 2D barcode printing and scanning on a metal part data the organization increased its traceability element as part of reverse supply chain. It also acts as a poka-yoke (mistake proofing) in the assembly line which is one of the benefits. Another one is a customer focused benefit leading to improvement on future products.
Keywords:- 2D Barcoding, reverse supply chain, traceability, defects, critical to quality, scanning, production process
INTRODUCTION
Manufacturing is the process wherein there is an input, process & output. The input is Raw material in which some value-adding activities are done such that the output is the desired product for which my customer will be willing to pay. From a financial perspective the manufacturing process witness increasing raw material costs, manpower costs, depreciating value of machines and plants, increasing power cost per unit and many more, if we drill down to specific word it can be called as inflation, inflation occurs due to many reason the most common one is the mismatch between demand and supply and thereby results in increase in cost, which directly forces the employee to increase his salary and thus create more discretionary income in their hand which results in more spending, all these form a viscous cycle and it continues. These lead to increasing competition across the globe and declining margin for the companies and they compete to capture more and more addressable market, due to which there is a need of more production to capture more market and thus lot of focus is on improving processes in manufacturing since it is one of the measure which can be controlled other such as raw material is affected largely by global cues and is non controllable up to certain extent, in manufacturing process expert are assigned to particular production line to observe and give their quality input to improvise, innovative, deliver the product at a faster pace and meet the increasing demand, the question come to process and improving it lead to penetration of new ideas, methods, technology.
SCM (Supply chain management) is the process wherein there is downstream flow of material, which is unidirectional, but information flow is bidirectional from both upstream and downstream. With increasing globalization, global trade has become possible and, but it has come with its own set of challenges. Information been one of the critical element in SCM, which start from forecast of the demand till meeting the actual demand, visibility about the actual inventory level at various Distribution center(DC) across the globe, understanding the pulse of market sentiment, global factor hindering the supply chain like the covid outbreak and the supply chain issue caused in Suez canal, the ongoing Russia -Ukraine war, rising inflation in US economy, power shortage in Europe, countries such as Sri Lanka which has severe condition of debt and similar other countries which are on the verge of the debt. But in spite of all these issue leading companies in specific segment have risen above all and consistently delivered the product OTIF (on time in full) to customer, they were able to do it by having a lookout in near future and hedging their risk as per the condition which might occur, when we say lookout in the future, they have done it with help of technology, increasing digitization and internet penetration across the globe.
Technology has become the key factor supporting the companies in meeting the demand, some of which are ERP(Enterprise Resource Planning) which helps in providing end to end visibility across the supply chain and help in reducing the obsolesce of inventory, forecasting demand which is one of the input of the supply plan, optimizing inventory and since the trend has changed from resource optimization to customer orientation meeting the demand with some capabilities of weekly forecast and capturing the current trends has become essential. Industry 4.0 is the key in manufacturing which includes new technology like cloud computing (Data been stored and retrieved from cloud), Cybersecurity (Reducing the risk of data breach), automation of the machines using IOT (Internet of things) which include sensors, PLC (Programmable logical Controller) like SCADA (Supervisory control and Data Acquisition), 3D printing which is also known as additive manufacturing wherein there is no deduction in material as per traditional manufacturing but addition of material by layer by layer to make the desired product and RFID (Radio frequency identification) which was the gamechanger in many industries from production, distribution, packaging till tracing the product from its origin till the end, RFID includes barcode as the enabler for retrieving the data, one such application of the same is provided in subsequent paper which include barcode technology been used in manufacturing process plus traceability of the
product in upstream flow in manufacturing and when at customer end the reverse flow in case the product is returned back due to some issue. Technology here is used as a hedge for tracking tracing back issue in product if any to the root providing a way for root cause analysis.
LITERATURE REVIEW
Supply chain is management and control of all materials and information in the logistics process from acquisition of raw materials to delivery to end user, The zest to control supply chain is increasing by the day as any change in the world impacts the supply chain for sure. Improvements in supply chain leads to saving in terms of cost and time. In this competitive environment industries are relying on technology; one of which is a barcode. Barcodes are printed horizontal strips of vertical bars used for identifying specific items.
Barcode are now a days used in many places and in streamlining SCM it has become useful but includes use of labor as well. Labor is required as it needs line of sight to scan items. RFID system is one of the replacements of the barcode, but the initial setup cost is high, barcodes on the other hand are easy to install, have low cost and high acceptance rate. A scanning device reads the barcode by moving a beam across the symbol. The first barcode system was developed around the 1940s and 1950s, since then many segments across industris from upstream to downstream have adopted to barcode.
Barcode is in use from many years and is easy to use by the customers at the end and do not take much to time to get accustomed in daily routine and further development in barcode are in progress. It is to be noted that there is no shortage of innovative new applications for barcodes also useful development in the technology [barcodes] continue to be made. Going further, development in barcode includes 2D codes. Unlike standard barcodes, which depend on links to a larger database, 2D barcodes contain a kind of mini database themselves, which includes information on the product and can be encrypted. One of the features of the barcode is that if the code is damaged and over a period the code on a product gets deteriorated but, in that scenario as well, the barcode will be readable.
One of the most used one in barcode technology is 1D barcode & 2D barcode. 2D barcodes are read by a scan engine type known as laser and can read both standard range, medium range or near/far. It can also interpret damaged barcodes and poorly printed one as well. 2D barcodes can be used when space is an issue and the amount of date to be captured is high, 2d barcode perfectly fit both the criteria and can fulfil the value, if we say the one of the most significant differences between 2D and 1D barcode is the amount of data that can be stored in them on one side where 2D barcode can encrypt about 2000-character 1D can only up to 25 characters. It is a win to use 2D code printing since the cost involved is not significant in comparison with 1D, Types of 2D code include QR code, PDF417 and data matrix. Having said that 2D barcode can encrypt visual images, some website address, and binary data. Data has shown that in case of customer preference also 2D barcode is preferred due to amount of the information that can be stored. One of the drawbacks in 2D barcode is visibility of the code, since then only the data can be scanned, stored, and retrieved from the same.
There are various types of 2D barcode some of the most common are QR barcode, these are the matrix barcode that contain various datatype such as alphanumeric (A to Z, 0 to 9) and binary (1,0), in terms of capacity QR code can store up to 7089 numbers. It is also said that they have four error correction levels which means that even if the code is damaged it can be read correctly. Other are data matrix type of 2D code that generate unique patterns of square module. They can store up to 2000 characters which includes both alphanumeric, binary and GS1 data, it is said that data matrix code is still readable even if they are 60% damaged, which is why there are widely used in many manufacturing domains. (Katie T. 2021)
Wal-Mart is certainly the champion as far as the use of 2D Barcodes is concerned. They have managed to keep both the costs and prices down by using barcode systems which benefits not only the company but also provides customer advantage. Wal-Mart, with the use of wireless scanners has introduced flexibility into the system allowing the staff to make price changes and order placements basis the product history.
It is evident from history that products are recalled even if they are top class brand in its segment, or a new entrant with all the latest technology. In 2020 in India alone approximately 3.4 lakh unit of automobiles including sedans, SUVs, hybrids, and the like were recalled due to issue in the system. (Lijee P. 2021, Apr 16). The Countrys largest car maker had recalled around 1.81 lakh vehicles due to issues in some parts. This was done keeping in mind customer safety and proactive recalling was better to avoid any fatal incident which might occur. Recalling vehicles included set of cost which was taken by the company. The idea used by the carmaker was to upload the vehicle chassis no. on company website and to check whether their car was in the list of vehicles. (Yuthika B. (2021, Sep 3). One of the two-wheeler manufacturers as well recalled around 2.4 lakh vehicle due to issue in some ignition cell in the vehicles (Subhro N. (2021, May 20)
Costs associated with product recall in case of any issue can be associated to overall capability of the company in traceability. The amount of information included on unit-of-use packaging can make the difference between a general, mass recall with notices going out in newspapers and TV news, and a highly targeted, limited recall where customers may receive notification by a phone call from their supplier (Zebra, 2004a). Quality control at the company level significantly reduces the chances of product recall, making granularity in data like diversifying lot by lot by different details reduces the cost in case of product recall otherwise whole bunch of products need to be recalled and checked. This degree of traceability limits the logistics handling costs and administrative burden, so recalls can be resolved more quickly and creates a system that would limit liability exposure and prevent lawsuits from unaffected individuals (Zebra, 2004a). General Motors saved millions and specially its reputation with high tracing capability installed at their end.
These is not the first-time recalls have been happened nor it is 100% sure that it will not occur in nearby future, there are chances that issue might occur, the things which are in control is to do PPA (Potential Problem Analysis) and prepare and contingency plan such that as and when the problem occur it can be tackled the root of these method can be traced back to FMEA (Failure Mode and Effect Analysis) which is also called as a quality tool. It is a method of inductive reasoning wherein all possible risk scenarios that might occur are listed down, associated RPN (Risk Priority No.) is calculated, and accordingly contingency and preventive plans are defined.
Table 1 FMEA Table
Problem |
Likelihood of Occurrence |
Severity |
Difficulty of Detection |
RPN (Risk Priority No.) |
Preventive Action |
Contingency Action |
Problem 1 |
||||||
Problem 2 |
||||||
Problem 3 |
Contingency action is used in the eventuality when the problem will occur. Preventive action is used such that the problem should not occur in first case. (FMEA, Wikipedia)
To understand the value addition of barcode, understanding reverse supply chain become essential, reverse supply chain is a process in which no. of activities are carried out to trace used product from customer and reuse it or do some testing on it. Reverse supply chain has become integral part of many manufacturing firm ranging from steel to computer, they do it for recycling and using the product or due to government regulation in the country owing to the sustainability norms. For instance tyre manufacturer retrieve used tyre and using them in manufacturing new tyre which is beneficial for the manufacturer, either way setting up reverse supply chain comes with its own set of challenges and risk associated, customer need to be educated point of contact of customer need to be established or use the current one for example plastic bottle recycling is done by placing the machine on railway station where there is more human footfall and the people are given coupon in return for disposing plastic bottle, manufacturer need to figure out how to keep cost minimum and in that recover some value. Making a structured reverse supply chain requires set of rational decision to be made, there are five keys component to be seen in relation to quality, cost, option, and benefits.
Fig.1. Utility of barcode in reverse logistics
-
Product acquisition (Retrieving the used product is a key to create profit in reverse supply chain, the quality, timing matters in these case or else if quality is deteriorated to such level where they cannot be reusabe it become difficult to generate value there is a need to work with retailer in these space)
-
Reverse Logistics (Post collection product need to be shipped for quality checks, segregation, and disposal, purely the supply chain is based on product as heavy product will need different method of handling and small product will need different)
-
Inspection and Disposition (Testing, sorting process take time includes lot of manpower involvement, disposition decision is made depending on quality and other factors taken into consideration)
-
Reconditioning (Checking the current state of the product, includes inspection of the quality of the returned product and reusing the same with some activity performed)
-
Distribution and Sales (Plan to sell recycle product, need to find the demand or new market for sales, the scenario can be new product is costly and can be afforded by few customers although recycled one will have less price and can be used by other potential customer) (V. Daniel & Luk.N, 2002)
Technology helps in both preventive and contingency but in the case described ahead technology is an enabler for the contingency action such that the amount of time spends on finding the root cause of the problem can be drastically dropped by significant value.
LIVE CASE: 2D BARCODE APPLICATION
Companies now a days are more customer oriented; customer want what they want when they want, the focus is to reduce the turnover time from order to delivery (O2D). Time and cost are important factor and both are valuable asset for customer, aligning to it many application can be seen such as the POC (Proof of concept) of barcode can be seen in retail store wherein at the checkout the code is scanned and automatically price is displayed on the system which help in faster checkout for the customer, decreasing the queue for the retailer, these scenario is at the customer end which is the last mile a downstream end, similarly in upstream process of manufacturing barcode is used for other purposes one such POC(Proof of Concept) is as follows.
To elaborate on how barcode technology has solved a case we need to understand the problem. The company was a manufacturing company acting as a supplier to a major OEM (Original Equipment Manufacturing) from the Automobile sector. The company has a B2B model and has no direct customer interaction. The assembly of the product was critical, and the product specifications were L*B*H (Length *Breath*Height) not more than 100 mm. There are about 25 to 30 small parts been assembled in the product, some of which are too small to be clearly visible to the naked eye. This made assembling them critical with high levels of accuracy as an expectation.
High accuracy in assembly required precision machine to be used for assembly. Demand was high and the criticality of assembly kept many players outside the zone of competition as initial setup cost was high. Thus, chances of error could have a huge impact on the CAPEX (Capital Expenditure) deployed on the assembly line.
Also, any loss of part in the assembly by mistake or improper fitment would cause a lot of performance issues in the product which may cost the company safety related issues related to customer. Another reason for this study was if some critical quality issues occur at the customer end, then checking the possibility of the product being traced back to the line along with the root cause analysis, to find whether there were issues in the machine due to which the error might have occurred or to reuse the product with some modifications. The study focused on studying various aspects of the 2D barcoding technique and how can it help improve reverse supply chain of the products.
The research problem statement from the assembly perspective was How to improve Traceability of all parts in the assembly plus solving/ rejecting the product there itself if found with any discrepancies and not passing it to next station thereby acting as a JIDOKA
The research problem statement from customer perspective was How quickly is a returned product which has been sent back to a plant traced back to check issues in assembly line to make changes
Enterprises using reverse logistics process have an essential criterion that is time of return, which may significantly depend on the barcode utilization.
In the company under study, the researchers carried out an in-depth observation and study to understand the process time before 2D barcode implementation and post 2D barcode implementation. The details of the same are mentioned with the help of VSM (Value stream Mapping) listed as follows.
Fig 2. Before Barcoding VSM
Fig 3. After Barcoding VSM
As we can see in Figures 2 and 3, based on the Value Stream Mapping, there is a difference in process time. The difference has occurred due to changes in process and addition of barcoding as a start point.
Table 2. Difference before & after barcoding VSM
Before Barcoding VSM |
After Barcoding VSM |
|
Operation 1 |
Post machine has performed the operation, operator manually checks with naked eye whether the desired parts are fit or not. |
Post machine has performed the operation, operator quickly unloads the part and passes on for next operation. |
Operation 2 |
Operator 2 checks the prerequisite parts which need to be there before performing the operation. Post machine has performed operation2, operator checks whether the part is properly fitted or not. |
Operator 2 directly loads the part in machine and once the operation is done, unloads the part and passes on to next operation. |
The Difference in Cycle time has occurred due to addition of barcoding, which makes sure that correct piece is passed on to next cycle and if any defect is there in part, it is straight away passed on to rejection bin.
-
Barcode will be scanned at start and end of every operation
-
At the start of the process the data in it is read and at the end the data of operations performed in any machine will be saved in barcode
-
Thus, manual inspection of data by operators is removed and thereby difference in cycle time is seen in Figure 3.
The idea which was used the methodology for Error proofing can be categorized under POKAYOKE and JIDOKA. JIDOKA refers to the problem being solved there itself without passing it to next station which increases the chances of mistake. POKAYOKE on the other hand is mistake proofing which says that operations should be designed such that the chances of mistake occurring is less. The idea was the assembly should not be carried forward until and unless the product is inspected at source itself. This will ensure that there are no last-minute rework occurring on the product, which might result in cost, time and effort by the people involved including customer dissatisfaction cost.
One of the reason to use 2D barcode is the size of barcode can vary and can be printed as per user configuration and product complexity, barcode can be configured in the given area provided, barcode can also meet the efficiency and effectiveness as the time taken to print a code on the product is less and if printed by good machine the chances of the barcode been damaged while handling are less thus effective as well plus no additional cost required to fit anything on the product or to change any design of product.
Fig.4 Barcode utility flow
Barcode technology was used and 2D barcode of data matrix type was being preferred and wherein the barcode printing machine is kept at the start of assembly line where in first process on the machine will be printing the barcode and inspecting whether barcode is printed correctly or not, if no issue is found then product is sent to next station wherein as per design the desired part will be assembled on the product andthe same information will be feed on to barcode. The process on second machine will be scan the barcode and check the product details, if everything is correct then assembly of part and feeding the information in the code is carried out, if code is improper or desired details are not there then product will be placed in rejection tray. Considering everything is as per desired expectation then the product is passed on to machine 3 wherein again the code is read, and information is captured if found ok, then assembly is carried out and information is fed on the code, if not ok then again, the part is placed in rejection tray and thus the process is carried out similarly on to the next station. Now at the customer end in case the customer returns the product due to malfunctioning and the product is in warranty phase, then the retailer sends back the product to the distributor and the distributor to the company. The quality team in the company did visual inspection on the product and if not reason for malfunctioning was found then it read the barcode and traced it back to the machine wherein the problem might have occurred. In this way if there is any need for improvisation in the machine it can be done with quick traceability.
Thus, a win-win situation was created by methodology of POKAYOKE and use of technology of barcode wherein process was intact, errors were reduced, and zero-defect product could be achieved. Any defective product when it reaches the customer end might change the customer image towards brand perspective and hinder the sales of the company in long run, technology is a helping hand for manufacturing without which many operations cannot be carried out in today fast pace changing world.
Fig.5 Reverse Logistics
The process of collection of the product start at the retailer end followed by distributor and so on where 2d barcode is used as the reference for tracing back the product back to the plant where it is been manufactured, following are some of the details which are stored back in the 2D barcode as shown in Table 3.
Table 3. Data Stored in 2D Barcode
Details |
Description |
Part Name |
FG126 |
Part ID |
AB34567 |
Process Details |
Date, Time, Process |
9/16/2022,15:29:15,1.1 Clamping, 1.2 Crimping, 1.3 Pressing |
|
Machine no. |
M12, M13 |
Operator ID |
DI123 |
Table 3. contains the tabular description of the data stored in barcode, which will eventually increase over as and when the operations are performed on the product. Coding is done to provide unique name to each product for e.g., FG represent Finished Goods followed by a number which becomes the name of the product. Similarly, part id is provided to the part on which all the operations are performed, and process details contains all the name of the processes done. Similarly, machine number and operator ID is provided.
There are two scenario which will come to picture once the product is in the plant one can be QA teams find the chances of reconditioning the product and can fix the issue in the product with some new part addition or repairing another being the problem which occurred in the product can be traced back again to the machine and machine can be calibrated or some changes can be made in the machine. In both cases there is value addition; one being the customer is served better for their products and in second; production related issues are also solved, both are ideal.
If we drill down how barcode has helped in the reverse supply chain following are some of the benefits
-
Reduced turnover time from customer to plant (C2P) Effectively & Efficiently been done due to easy traceability and product details in barcode
-
Automated data gathering reduces dependance on the operators and thereby provides better accuracy and operators on the other hand can focus on other activities and provide more value addition in the same.
-
Capturing the data in no time and access to complete information. Barcodes record product codes, lot numbers, order numbers, invoice codes,
-
Decreased human error Dependency on operator is reduced by providing POKAYOKE and JIDOKA in the process itself with use of barcode technology
-
Decreased cost of maintaining record, manpower with skilled expertise to understand the problem if any in SPM (Special Purpose Machine)
-
Inventory management of product Maintaining the date of assembly in Barcode provide better Handling of dispatch using FIFO (First in First Out) such that obsolescence of product is reduced
-
Traceability From Customer to Plant anyone can scan the details although the nomenclature of the details would be specific to plant & distributor, and they will be able to articulate the meaning
-
Customer education -Providing details of the product which is used which includes details of how to install, assembly and if any issue in functionality what to check first.
CONCLUSION
Globalization has come with its own pro and cons, pros been increasing use of technology to meet customer demand, brainstorming among companies to effectively use of technology in there process, barcode in our case has proved to be boom in meeting the safety standard, reducing redundance for the operator, reducing NVA (Non value adding) activities of discussion among peers to find out the issue on gut bases instead of that thus believing in data which is in line with the saying that Data is the new oil.
Data of the product is stored in barcode and retrieved when required in our case helping to reduce the redundant activity in reverse logistics and thus enabling proper shipment of product back to plant and there after another activity of tracing the root cause of the issue in product and technology has become an enabler to achieve desired result as technology has helped in improving the process and result is the byproduct of the process.
Returns are now a part of everyday business operations for both manufacturers and distributors. Numerous national and international regulations will demand safe transportation, documentation, and traceability of returns management. Technology and ease of use in the form of barcodes will provide the much-needed solution to collect information and provide an audit trail. This information can help manufacturers determine the root cause of the returned products. It can also help them decide if they need to redistribute returned products or dispose them or do they require special handling procedures.
Like with all research topics where there is scope of further improvement, the scope of this research paper can be further extended by measuring in terms of time taken for reverse shipment of product from customer to plant and again plant to customer in case of warranty and what all other details can be captured such that it has more granular details of where actually the product is in the value chain post-dispatch from the plant which might also help to reduce the time of delivery to the customer by identifying bottlenecks in the value chain.
REFERENCES.
[1] Katie T. 2021 from https://www.techtarget.com/searchmobilecomputing/definition/2D-barcode [2] Lijee P. (2021, Apr16), India auto industry, ET Times from https://auto.economictimes.indiatimes.com/news/industry/indian-auto-industry- voluntarily-recalls-376536-vehicles-this-year-more-than-double-of-2019/85362225 [3] Yuthika B. (2021, Sep 3) from https://www.thehindu.com/business/Industry/maruti-suzuki-to-recall-over-181-lakh-vehicles/article36268169.ece [4] Subhro N. (2021, May 20) from https://timesofindia.indiatimes.com/business/india-business/royal-enfield-to-recall-2-4l-bikes-to-fix- snag/articleshow/82781336.cms#:~:text=Kolkata%3A%20Royal%20Enfield%2C%20the%20Indin,ignition%20coil%20that%20has%20the [5] Zebra Technologies, (2004a). Bar Coding and RFID: The Key to Traceability and Safety in the Foodservice Supply Chain. [6] Failure mode & effect Analysis (FMEA, Wikipedia). from https://en.wikipedia.org/wiki/Failure_mode_and_effects_analysis [7] The reverse supply chain, Harvard Business Review (V. Daniel R. Guide Jr. and Luk N. Van Wassenhove, Feb. 2002)