
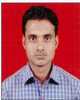
- Open Access
- Authors : Bapu Dada Kokare , Dr. Sanjay A. Deokar , Dr. Mangesh Kale
- Paper ID : IJERTV10IS040003
- Volume & Issue : Volume 10, Issue 04 (April 2021)
- Published (First Online): 07-04-2021
- ISSN (Online) : 2278-0181
- Publisher Name : IJERT
- License:
This work is licensed under a Creative Commons Attribution 4.0 International License
Hybrid Electric Vehicle Fault Diagnosis and Detection Technique
Mr. Bapu Kokare*, Dr. Sanjay A. Deokar ** Dr. Mangesh Kale***
*(Department of Technology, Pune University)
** (Principal, Someshwar Engineering College, Someshwar Nagar )
***(Scientist, Eaton Ltd.)
Abstract:- This paper describes the fault diagnosis and detection methodology for electric vehicle, and its fault severity criteria studied together. Detailed fault studied for transmission, PMSM motor, driveline, and thermal management system. The possible fault of the various subsystems, which influence the vehicle performance & range are listed together to differentiate faulty and Health mode. The proposed fault technique is conventional might be useful to different types of vehicles and faults. With twenty years of electric car design experience, manufacturer are able to manage different fault, defined through well FMEA, PFMEA, and fault study. This helps to expand the business and improve reliability, which promotes the use of electric vehicle powertrain.
Key words: Hybrid electric vehicle [HEV], Fault management, fault diagnosis, fault classification, fault detection, steering, controllability, stability, vehicle dynamics.
-
INTRODUCTION
Diagnosis of vehicle need completes definition, which requires study the all-occurring faults and correlating with current faults. The vehicle's maintenance mechanic knows the well mechanism and could understand the upcoming major issue with the vehicle powertrain fault cause. In same manner before diagnosis every component functionality knowledge is also important.so mechanic requires a tool such as CRO, electric measurement instrument that measures the vehicle's health condition and checks for availability of spare or another prognosis measurement.
-
VEHICLE DYNAMICS
Vehicle lateral acceleration, longitudinal velocity, rolling resistance, steering angle, yaw rate are the important parameter which provides best driving comfort.
Image1. Vehicle different acting forces
= velocity of car
= vehicle tire radius
= angular speed of car
= .2.1
= ..2.2
= 2.3
= 0.5 _ 2 .2.4
=
A= vehicle acceleration
= Air density,
= Frontal surface area of the vehicle,
= Aerodynamic drag coefficient,
= ehicle speed,
= Surface road angle with horizontal road
= _ + _ + _ .2.5
F_tire= Tire force,
F_aero= Aerodynamic resistance, F_slope= Climbing Force.
Forward Traction condition of vehicle is drive wheel torque and transmission torque both should be greater than vehicles total force and more store form of energy[1] [2].
-
PARALLEL HYBRID ELECTRIC VEHICLE
In a Parallel Hybrid, there are two parallel paths to power the wheels of the vehicle: an engine path and an electrical path, as shown in the figure. The transmission couples the motor/generator and the engine, allows either, or both, to power the wheels. Control of a Parallel Hybrid is much more complex than for a Series Hybrid because of the need to efficiently couple the motor/generator and engine in a way that maintains drive controllability and gets observable performance. [3] [5]
The Parallel Hybrid can operate in the following five modes:
-
.Engine only traction
-
Electric-only traction
-
Hybrid traction
-
Regenerative Braking
-
Battery charging from the engine
Image. Parallel hybrid electric vehicle [PHEV]
IV METHOD TO DIAGNOSIS OF ELECTRIC VEHICLE
FAULT:
Fault Detection and diagnosis method
Monitoring Systems (TPMS), road-tire friction monitoring systems, and so rely on models of the underlying vehicle dynamics.[4]
2. Use of artificial intelligence: The mechanic is having a good experience and becomes more capable to solve the critical issues with the fault of the vehicle. It nice to have if artificial intelligence deployed and mimic human activity and understand the vehicle fault together, current alarm. Then the user will remove the future coming faults at the workshop.
-
Indirect tire pressure monitoring model: Indirect Tire Pressure Monitoring Systems (TPMS), the systems that do not have air pressure sensors inside the tires. Rather, they detect a low tire by comparing relative wheel speeds via the Anti-lock Brake System (ABS) wheel speed sensors. When a tire loses air, its diameter decreases slightly. Indirect tire pressure monitoring give relative by how much amount tire deformed for individual drive by accurate measurement. Electric vehicle static and dynamic parameters influence performance in terms of smooth changeover and controllability. Physical performance derived from controllability, comfort; steering ability, Safety, Road surface condition. [6] Four-wheel-drive cars have greater control than the front or rear wheel drives.
-
For electric vehicle tire MOTOR torque – speed control and Torque prediction: In an electric car
Hybrid approach Model Driven method
Data Driven
Method
Expert approach
Individual speed correction done by direct torque control of PMSM MOTOR and individual speed, control stabilized well with physical condition maintained in good condition. During emergency braking, antilock braking system[ABS]
Fuzzy logic Statistics Artificial intelligence
Image: fault diagnosis and detection method Development of electric vehicle (EV) design process
implemented with a minimum cost and time with vehicle
component design. The model-based design create details insight into a systematic approach to estimating the power flow of the electric vehicle propulsion and dynamic load. An electric Vehicle specification and driving cycles are the two main inputs for the simulation. As a result, the approach is capable of estimate state space and predict EV characteristics and design parameters, such as motor power, EV performance, battery power, torque-speed characteristics, driving range, and charge/discharge, which is the necessity for the design and sizing selection of the main EV components. ECU design did fast in model-based design. In this fault, co-simulation is easy with Matlab and IPG carmakers.
1. Expert Approach: Rule Based, Case based Reasoning(CBR): There are the following important parameters that detect the electric vehicle deteriorating performance such as Yaw, Roll, Pitch, irregular acceleration, deceleration in between changing operating mode idling behaviour. Many new vehicle features like Electronic Stability Programs (ESP), indirect Tire Pressure
activate ensure wheel lock prevention or in electronic stability control[ESP] unit continuously monitor individual wheel speed and steering angle, estimated or tuned brake force applied to wheel drum in HEV. ABS comes in the picture only if the driver applies brake in an emergency or active safe but for sport utility vehicle car individual wheel speed feedback to ESP unit controls speed by braking to derive the best comfort [7]
As shown in the IMAGE1 different forces act on vehicles and maintain the center of gravity with ESP unit avoids slip of vehicle high hill hold in idle condition which gives similar comfort like IC SUV
-
Data Driven method:
On-board computer sample sensor data input within 10 milliseconds of steering angle, wheel speed, acceleration, pedal brake and estimate how vehicle individual wheel sped should be operated. On-Board equipment monitoring systems have direct and discrete or continuous access to sensor readings, collecting time series.
To characterize a system or a physical process for detecting faults or deviations, various types of physical properties can be measured.
At corner speed, vehicle control Switching characteristic performance table of speed and steering angle is calculated during calibration of motor current and particular torque table changeover defined brake force magnitude applied to the car as well ABS also tuned respectively. ABS function ensures the vehicle wheel should[8] not be locked continuously and avoid
skidding roll or pitch like. Continuous-time data with supervised learning techniques can capture interesting characteristics. Extraction from heterogeneous fleet data alarms the user if detecting a statistical deviation in measurement.
Hatchback type electric car demand is for the reason of easy to allocate all safety to manufacture the car, battery area proper allocation, and safe against the physical damage to electric convertor damage
-
Battery fault model:
In Matalab battery series fault Simulated as battery all cell are arranged in series and fault introduced by voltage difference in single one cell 10 which impact battery performance. [9] The fault is represented by changing the parameters for the Cell 10 Fault subsystem, reducing both capacity and open-circuit voltage, and increasing the resistance values.
Image : Matlab Battery fault Simulink model
Image: Charging and discharging cycle state
3.2 Function of Battery management system in case one cell fault:
Handle each battery sub cell voltage to balance and whichever cell voltage is lower than normal cell, charge first the cell using contractor switch logic. After required voltage reached then switch on the power to charge normal cell then battery cell life is increased for a year or more.
Each battery cell ageing factor are different will not have exact same voltage due to temperature distribution , ion oxidation or deposition at electrode & internal resistance.
-
-
Electric Vehicle steering system
While driving a car at high speed, requires more effort to control steering and enable comfort. In this driving comfort at cornering achieved by steering sensor speed feedback input to ESP controller, apply individual different forces to all-wheel. Ackermann's condition is the steering system control and enables directional velocity without a change in vehicle speed. The purpose of this steering at a tight angle and less friction coefficient with the road must maintain the pure rolling motion of the tire. Wheel tires should not be skids tires. The steering system must make an adequate feel to the driver while turning. The steering mechanism improves tire life by maintaining angles between the tires while turning and braking at the corner along with directional velocity. Steering allows the driver to turn the vehicle with less effort and directionally stable conditions provided or fulfilled. The steering system designed in a unique way by compelling many factors and formulating mathematical model introduces lean angle if required.[10] [11] Advanced steering system helps to keep the car in lane track, avoidance lane departure track, collision detection, and car parking, require less forces to steering control and Provide good controllability of steering. For this driver required an intelligent
driver assistance system (ADAS).
Image: Embedded system control system of the hybrid electric transmission
-
Hybrid Electric car Braking system
All-electric car and hybrid car converts kinetic velocity to the electrical energy with regenerative brakes. Since the internal combustion engine store energy in the flywheel and get, back potential energy in electric energy through the crankshaft. Hybrid Vehicles offer the possibility of fuel-saving by regenerative braking, where the electric motor is used as a generator that converts the kinetic energy of the moving vehicle into electric energy when decelerating the vehicle. [12]
The combined brake control system is more reliable with the electronics brake and antilock brake system [ABS] for the hybrid electric car.
During emergency braking the hydraulic system and the regenerative braking system work co-association manner, ensures regenerative efficiency to be high.
Logically front braking pressure to be less than the max up- to half of the rear-wheel-drive pressure. To avoid front wheel skidding this criteria also needed. Brake modelling help to
improve event understand during braking, vehicle sleep, and longitudinal sleep.
-
Co- operative brake for HEV:
In electric vehicles, two types of braking available as friction and regenerative braking. Both types should implement in a co-operative manner that gives more confidence as energy conservation and stopping the vehicle within with a wheel lock similar to ABS.
One case study suggests that if the battery is fully charged then what to do with available regenerative braking, At that time hydraulic brake calliper are activated by ABS which is signalled by IDAS and ECU.
-
-
Electric vehicle faults lists:
Error/Fault
Effect
Drive line Fault
Cant run HEV
Control system fault
Entire vehicle operation affect and depend on severity
transmission fault
Engine plant affected
Drive Fault
Partial operation affect
Wiring Harness fault
Auxiliary operation halted
Battery cell Fault
Electric source extract not possible
Wheel Fault
Cat run plant model
Mechanical Assembly Fault
observation will be correct after sometime
Mechanical component Defective
Cant run entire plant
Transmission Backlash
Energy loss and cant run vehicle using 2ndary power
Eccentricity mismatch
Stability and energy loss
Gearbox Fault
Energy loss or may not run transmission plant
Power converter fail
Replace power sourcing switch element
Drive control fail
Traction power source not available to run
User interface fault
Cant run system blindly
Diagnosis log fault
Cant trace or track back all sequence of failure
-
VEHICLE FAULT MANAGEMENT
Ideal fault methodology includes 5 steps process
-
Fault detection: fault detection after the complete or partial occurrence of the error
-
Fault location: find the exact location of error by CAN OR OBD2 device
-
Restoration of service: corrective measure action taken for error resolution
-
Identification of root cause of the problem: action taken not to occur repeat problem
-
Problem resolution: completely up the machine with corrective action.
The vehicle faults are classified according to fault location with area location, log data of fault statistical computation done for understanding varying behaviour the change in time and condition. In this individual component and electric devices reliability, controllable parameter estimated, remaining useful life calculate. These different sensor data collected and trained. The data used for further analysis and compared with health and fault condition based on this fault ranking is defined as called controllable ranking method in classification. Individual fault groups defined and collcted faults, which act in a similar way on the vehicle behaviour.
-
-
Fault classification
Fault classification was done according to the bellow criteria as
-
Stationary evaluation: In this electric vehicle, powertrain signals are easy to correlate with previous and current data.
-
Non-stationary evaluation: these signal are difficult to correlate this parameter in a more dependent and instant change in unexpected value
-
Controllable ranking method: Component individual function are defined in three criteria as A. highly controllable, medium controllable, lightly controllable,
With reaction, time, and braking performance reliability will be insured.
Class |
C0 |
C1 |
C2 |
C3 |
Definition |
Low critical |
Critical |
Medium critical |
High critical |
Marking |
1 |
2 |
3 |
4 |
There are two method to handle the fault
-
Fault detection
-
Fault isolation
9. Motor Eccentricity:
Fault Kalman Filter able to detect and isolate error using auto regression. Kalman filter used to detect error related to eccentricity and bearing fault, chassis vibration due to unequal distribution, unbalance, and oil lubrication, off road or lane keeping. It also able to detect the error related to Gearbox and transmission. Fault detection, isolation, and diagnosis studies are important to prevent probable failures in advance.
-
Transmission Fault:
Electric motor have an ideal torque and power curves regarding vehicle operation. Due to these favourable characteristics, the transmission of an electric vehicle is simpler, presenting itself as a conventional reducer with respect to the overall geometry, having usually only one speed ratio between the input and the output.
There are many faults related to transmission. In the development of the Transmission Fault-tolerant control system [FTC],
-
Gear fault & Lubrication Fault:
The tight housing of gearbox does not allow for a lot of oil flow movement. Consequently thermal analysis show increased temperature of bearing. Therefore critical and oil starved area needed to identify the error in these using nanoFluidX
Fixed gear ratio Transmission: it provides high stall torque, low cost at adequate speed
Differential gear:
All-electric vehicles need some sort of differential to gain full control instead of individual wheel speed control, which ensures reliability. It is important at turning a vehicle. To safely turn, the outside wheels must spin faster than the inside wheels, which is provided by the differential. At the same time, they act as the final gear reduction in a vehicle and transmit the power to the wheels.
Torque vectoring: A torque-vectoring differential has the capability to transmit torque independently between the wheels. This capacity brings advantages such as increased stability and responsiveness.
In an electric vehicle powertrain, the individual motor speed can be controlled can improve the vehicle transient response.
Fault derived during consequence of accident:
During electric car design, it is necessary to keep track of ISO standards that must be followed properly and implemented in the hybrid car. IC engine car is less critical handling operation and but complexity increases usage risk.
ISO standards are defined for the design of electric cars. ISO has defined many standards for chargers, and their type, charge connector, battery location on chassis.
NCAP define all acceptance parameter of car design. It defines how braking consequence should be, define brake capability, passenger safety also defined
ECU Experimental Setup:
We setup hardware for the vehicle sensor and real time monitored through web portal with wireless remote access on MEGA2560 server and microcontroller communication. We were able to monitor vehicle condition of tire pressure, fault system designed to log all error on server
Fig: Model ECU using microcontroller
Image: live display of fault log data ACKNOWLEDGMENT
Special thanks to Prof. Sanjay Deokar and Mangesh kale the Department of technology University of Pune, for the experimental data log and its setup in lab.
REFERENCES
-
Professor CS Shankar Ram, IIT Madras, and his PhD student VS Kesavan who have explored various strategies to study and incorporate the effect of different dynamic characteristics of friction brake and regenerative brake.
-
Ananchai Ukaew (November 5th 2018). Model Based System Design for Electric Vehicle Conversion, New Trends in Electrical Vehicle Powertrains, Luis Romeral MartÃnez and Miguel Delgado Prieto, IntechOpen, DOI: 10.5772/intechopen.77265.
-
2020 International Conference on Emerging Trends in Information Technology and Engineering (ic-ETITE) 1 978-1-7281-4141- 1/$31.00 ©2020 IEEE Model Based Fault Classification Method For Electric Vehicle Pertained Lithium-Ion Batteries Using Multi Layer Perceptron.
-
Fault Detection and Isolation of Vehicle Driveline System M. shahab1,* and M. Moavenian
-
MATHWORKS.COM
-
WIKIPEDIA.COM
-
A Hybrid Electric Vehicle Powertrain withFault-Tolerant Capability Yantao Song Bingsen Wang 2012 IEEE
-
Modelling and control of hybrid electric vehicles (A comprehensive review) Wisdom Enang Chris Bannister University of Bath, Bath,
UK 2017 ELSEVIER
-
Hitatchi drive system Qiyao Wang R&D Division, Hitachi America, Ltd.
-
Hybrid Electric Vehicle Powertrain Controller Development Using Hardware in the Loop Simulation
-
Sciarretta Antonio, Back Michael, and Guzzella Lino. Optimal Control of Parallel Hybrid Electric Vehicles. IEEE Transactions On Control Systems Technology, Vol. 12, No. 3, May 2004
-
Conference paperHybrid Electric VehicleSafi Ahamed Khan Dept. of Mechanical, PITS. Sanjay Kumar Dept. of Mechanical PITS. B. Jagadesh Assistant Professor Dept of Mechanical-PITS
-
I needs more news about it