
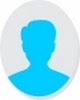
- Open Access
- Authors : El Akili Charaf , Aboubaker Bouayad , Badi Ait El Haj , Hamadellah Abderazzak
- Paper ID : IJERTV10IS040271
- Volume & Issue : Volume 10, Issue 04 (April 2021)
- Published (First Online): 12-05-2021
- ISSN (Online) : 2278-0181
- Publisher Name : IJERT
- License:
This work is licensed under a Creative Commons Attribution 4.0 International License
Grain Refinement and Modification of Hypereutectic Al-Si Alloys Mold by Two Process
El Akili Charaf
Department of materials and process. Laboratory of Engineering Sciences and Trades (LSMI); Research team: Innovative materials and manufacturing processes Mechanical. National School of Arts and Crafts. Moulay Ismail University, Meknes,
Morocco
Aboubaker Bouayad, Badia Ait El Haj, Hamadellah Abderazzak
Department of materials and process. Laboratory of Engineering Sciences and Trades (LSMI); Research team: Innovative materials and manufacturing processes Mechanical. National School of Arts and Crafts. Moulay Ismail University, Meknes,
Morocco
Abstract The solidification process significantly affects the microstructure and mechanical properties of the aluminum- silicon alloys. This article discusses the effect treatment of the
using:
The table below presents the composition of metal
liquid metal, namely the refining and the modification on the microstructure and mechanical properties of a hypereutectic silicon aluminum alloy, molded by two molding processes. Sand mold and shell. The study shows that the microstructure affected
for the two treatments and in the two molding processes. On the other hand, the refining treatment has a reciprocal influence on the mechanical properties. However the modification slightly improves the mechanical properties.
Keywords: Solidification, refinement, process, cast; molding.
I.INTRODUCTION
AlSi alloys are most widely used aluminum alloys due to their castability, high strength to weight ratio, corrosion resistance,etc [1,2].This fosters use is to reduce cars and aeronautic equipments weight and other automotive applications [3,7]. Grain refinement has regarded as one of the most effective techniques to enhance the mechanical properties of metal castings and to improve the formability of metal ingots [810]. The currently available techniques for grain refinement of cast metals include vibration and stirring [11, 12], rapid solidification [13] and inoculation treatment [14]. For solid metals, severe plastic deformation is generally used to refine the grains to micrometer and even nanometer scales [15,16]. In industrial production, inoculation treatment through addition of proper grain refiner is widely used in metal castings [17]. For example, TiB2 and Al3Ti are effective grain refiners to promote heterogeneous nucleation for cast aluminum alloys [18,19]. In This work we are study the effect of inoculation and modification using tow process send shell casting.
-
EXPERIMENTAL PROCEDURE
The objective of our study is therefore to be able to control the microstructure, using liquid metal treatment in order to determine the most suitable treatment and casting process for obtaining high performance, hypersilicon aluminum parts. For this, we will have to carry out a series of experiments such as tensile tests, hardness tests, cooling rate measurements, …
TABLE1: AVERAGE VALUES OF SOME THERMOMECHANICAL PROPERTIES OF ALSI17CU4 ALLOY.
Element
Si
Cr
Fe
Ni
Cu
Zn
Mn
Al
Average
content wt%
16,135
0,035
0,453
0,027
6,580
0,186
0,203
Bal
A. Production of test specimens
We cast different specimens allowing us to subsequently perform the various tests, which are a micrographic analysis, the recording of thermal curves, tensile tests, hardness tests, chemical analysis and measurement of the porosity rate.
B.Material available
To make these specimens, we heated the aluminum hypereutectic AlSi17Cu4 alloy in induction furnace. During all of our castings, the alloy was heater in the same furnace to a temperature of 650 ° C without heating any other metal. We have cast different specimens allowing us subsequently perform the various tests, which are a micrographic analysis, the recording of thermal curves, tensile tests, and hardness tests.
The objective of this study is a comparative the manufacturing of a hypereutectic AlSi17Cu4 sample using tow process.
FIG1: METAL HEATING FURNACE
The test pieces are cast in sand molds (produced by the PEP
SET process) comprising five test pieces and in a shell mold
Comprising four test pieces.
To make the molds, we mixed the sand with 0.5% phenolic resin relative to the sand mass, 4% catalyst and finally 0.5% isocyanate resin.
FIG 2: SAND MOLD
FIG 3: SHELL MOLD
The tests carried out are on two treatments, the first Being A refining treatment. The second is a modification treatment.
-
Refining
Reference shell
Rate
E (Gpa)
Rm (Mpa)
A (%)
0,0%
61
160
0,16
Reference shell
Rate
E (Gpa)
Rm (Mpa)
A (%)
0,0%
61
160
0,16
For the refining treatment, we used as an additive element ALUFLUX B (Titanium and Boron) in the form of 200g pellets.
-
-
RESULTS AND DISCUSSION:
To study the effect of refining and modification treatments on the solidification parameters. We have produced test specimens by which to measure, mechanical propriety and microstructure tests using the two treatments for both sand and shell molding processes.
a- Mechanical tests (Rm, E)
The various cast specimens will serve us mainly to determine the mechanical characteristics of this alloy. For this, we carried out tensile tests. Then, in the analysis of the results, we will only consider the test pieces giving consistent data, and we will take an average of these values, considering the standard deviation and the dispersion of the measurements.
TABLE 4: PERCENTAGE OF MODIFIER AND REFINING USED
Reference sand
Rate
E (Gpa)
Rm (Mpa)
A (%)
0,0%
78
156
0,15
Modification_Sand
Rate
E (Gpa)
Rm (Mpa)
A (%)
0,3%
71
160
0,21
0,5%
72,00
159
0,22
1,0%
77
150
0,13
Refining Sand
Rate
E (Gpa)
Rm (Mpa)
A (%)
0,5%
74
118
0,04
0,8%
75
95
0,03
1,2%
73
108
0,05
TABLE 2: PERCENTAGE OF REFINER USED
% of treatment
Number of samples
0.5% of the metal mass in the furnace
1
0.8% of the metal mass in the furnace
2
1.2% of the metal mass in the furnace
3
-
Modification
For the modification treatment, we used as an additive Element SIMODAL 77 (Sodium), in the form of a 200g tablet, 0.2%.
Modification shell
Rate
E (Gpa)
Rm (Mpa)
A (%)
0,3%
59
140
0,17
0,5%
61
151
0,17
1,0%
60
153
0,19
TABLE 3: PERCENTAGE OF MODIFIER USED
% of treatment
Number of samples
0.3% of the mass in the furnace;
1
0.5% of the mass in the furnace;
2
1.0% of the mass in the furnace.
3
-
Degassing treatment
For the degassing treatment, we used as an additive element DEGAZER 701 SM (Nitrogen and without Sodium), in the form of a 200g pellet, 0.5%.
Refining shell
Rate
E (Gpa)
Rm (Mpa)
A (%)
0,5%
60
118
0,06
0,8%
62
114
0,03
1,2%
62
108
0,03
The blue tables serve as references, that is to say, they indicate the characteristics of the test pieces without treatment.
We recall that "A (%)" represents the permanent elongation of the test piece under the stress Rm. To compare these results and to be able to analyze them, let us draw up the following graphs, that is to say:
-
Young's modulus: E (GPa)
-
Tensile strength according to the different treatment rates (refining and modification): Rm (Mpa)
FIG 7: CURVES OF VARIATION YOUNG'S MODULUS, TENSILE STRENGTH AND
ELONGATION AS A FUNCTION OF REFINING FOR USING SHELL MOLD.
E(GPa) Rm(MPa) A(%)
62
160
60
0,18
0,16
-
Permanent elongation: A (%)
58
E(Gpa)
E(Gpa)
FIG 5 CURVES OF VARIATION YOUNG'S MODULUS, TENSILE STRENGTH AND ELONGATION AS A FUNCTION OF REFINING FOR
USING SAND MOLD . 56
E(GPa)
Rm(MPa) 54
A(%)
0,16
150
Rm(MPa)
Rm(MPa)
140
130
120
0,14
A(%)
A(%)
0,12
0,10
0,08
0,06
150
140
130
150
140
130
Rm(MPa)
Rm(MPa)
78 160
77
0,14
A(%)
A(%)
0,12
52
50
0,0% 0,5%
110
100
0,8% 1,2%
0,04
0,02
E(Gpa)
E(Gpa)
76
120
75 110
100
74
90
73 80
70
0,10
0,08
0,06
0,04
0,02
Refining(in %)
With regard to permanent elongation of test pieces, the previous graph reveals some trends. First, the refining treatment does not promote strong permanent elongation, whether in shell casting or sand molding. However, we see a minimum reached for 0.6% ripening.
0,000 0,002 0,004 0,006 0,008 0,010 0,012
Refining(in %)
FIG 6 CURVES OF VARIATION YOUNG'S MODULUS, TENSILE STRENGTH AND ELONGATION AS A FUNCTION OF MODOFICATION FOR USING SAND MOLD .
E(GPa) Rm(MPa) A(%)
FIG 8: CURVES OF VARIATION YOUNG'S MODULUS, TENSILE STRENGTH AND ELONGATION AS A FUNCTION OF MODOFICATION FOR USING SAND MOLD
E(GPa)
Rm(MPa) A(%)
160
160
Rm(MPa)
Rm(MPa)
61,0
0,19
80
160
75
60,5
A(%)
A(%)
0,18
0,20
A(%)
A(%)
70
60,0
150
E(Gpa)
E(Gpa)
Rm(MPa)
Rm(MPa)
E(Gpa)
E(Gpa)
65 155
59,5
0,17
60
55
150
50
0,15
59,0
140
0,0% 0,3% 0,5% 1,0%
Modification (in %)
0,16
0,0% 0,3% 0,5% 1,0%
Modification (in %)
With regard to permanent elongation of test sample, the previous graph reveals some trends. First, the refining treatment does not promote strong permanent elongation, whether in shell casting or sand molding. However, we see a minimum reached for 0.6% ripening.
As regards the modification, the specimens cast in shells exhibit an increasingly important permanent elongation as the rate of modifier increases. Contrary to this behavior, the test pieces cast in a sand mold make it possible to demonstrate an
optimum point of maximum permanent elongation, reached
for a modifying rate of 0.5%. We can explain the phenomenon B of increased elongation in the case of a modification treatment
through the consequence of the modifier on the microstructure of the material. Indeed, as explained in the section presenting the modification, this treatment of the liquid metal will, among other things, modify the eutectic (initially as a needle) to result in a globular morphology. However, this morphology offers more ductility to the material, hence an increase in the permanent elongation of the modified specimens.
b- Micrographic analyzes:
The object of this study will be the characterization of the microstructure of the different Al-Si 17 alloys, each of which has undergone either a modification or a refining.
For this on the micrographs taken, we sought to define:
-
The density of primary Si B
-
The density of eutectic Si
-
The density of Al
-
Porosity
-
The size of the porosities
-
-
We will now present the results that we obtained. For the sake of clarity, they will be presented treatment by treatment and with their respective casting process.
Eutectic silicon
Eutectic silicon
1-Control samples (A0)
Primary Silicon
Primary Silicon
Intermetallic
Sand mold reference sample (x200) Shell mold reference sample (x200)
FIG 9: MICROGRAPHIC IMAGE OF THE REFERENCE SAMPLE FOR TWO PROCESSES
FIG 10: MICROGRAPHIC IMAGE OF SEND MOLD REFINING A0.5% B 0.8%
AND C 1,2 % (X 200)
A
A
A
B
B
C
C
C
C
FIG 11: MICROGRAPHIC IMAGE OF SHELL MOLD REFINING A0.5% B 0.8% AND C 1,2 % (X 200)
from the above micrographs it is concluded that the most adequate refining percentage is 0.8% for both processes. especially for shell molding. this may be justified by the reverse effect of the refining agent as its percentage increases. such that the refining element plays the role of germination for the intermetallic.
After studying the effect of refining on the microstructure in both processes. we will proceed to study the effect of the modification. the micrographs below show the reults obtained
A
B
FIG 12: MICROGRAPHIC IMAGE OF SEND MOLD MODIFICATION A
0.3% B 0.5% AND C 1 % (X 200)
A
A
B
B
C
C
FIG 13: MICROGRAPHIC IMAGE OF SHELL MOLD MODIFICATION
A0.3% B 0.5% AND C 1 % (X 200)
In the sand casting we note that from the first levels of Si modifying agent of the eutectic phase, initially present in acicular form, transformed into globular form, For a high rate of modifying agent, we can notice that the primary Si's have disappeared in favor of the eutectic Si's. The modifying agent therefore also has the properties of a refining agent. On the other hand we shell molding. on the other hand, for shell casting, it is noted that in the presence of the modifying agent that there is a presence of aluminum dendrites which, based on the phase equilibrium diagram should not be present (alloy hypersilicon). in the second part we note that from 0.3% of the eutectic modifying agent changes morphology. moreover, the modifying agent acts as a refining agent for a rate of less than 0.5%. It therefore allows the primary Si to be refined in addition to the eutectic, which improves hardness.
-
-
CONCLUSION
At the end of this work, we were able to establish some optimum rates: namely a rate of 0.5% modifying agent and a rate of 0.8% refining agent. We have noticed the overall degrading effects of the refining on the mechanical strengths and the microstructure. On the other hand, the modifying agent proves to be effective because from the rate of 0.5%, we obtain a suitable microstructure, which improves the mechanical resistance.
In a more general way, we were able to determine the effects of refining and modification treatments on a hypersilicon aluminum alloy which was relatively little known until then.
ACKNOWLEDGMENT
This work was carried out at ENSAM Meknes. is part of Moulay Ismail University in Morocco. I would like to thank all the technical and administrative staff who have helped us to achieve.
REFERENCES
-
L.F. Mondolfo, Aluminum Alloys: Structure and Properties, Butterworth,London, 1979.
-
S.G. Shabestari, S. Ghodrat, Mater. Sci. Eng. A 467 (2007) 150158.
-
L. Anantha Narayanan, F.H. Samuel, J.E. Gruzleski, Metall. Mater. Trans.A 26A (1995) 21612174.
- [4] C.M. Dinnis, J.A. Taylor, A.K. Dahle, Scripta Mater. 53 (2005) 955958.
-
Quan-Zhi Dong 1, Young-Sim Choi 2, Jun-Ho Hong 2 and *Ho-Young Hwang Prediction of mechanical properties of Al alloys
with change of cooling rate J. Overseas Foundry November 2012 p.381
-
S.G. Shabestari, M. Malekan, Assessment of the effect of grain refinement on the solidification characteristics of 319 aluminum alloy using thermal analysis. Journal of Alloys and Compounds 492 (2010) p.134
-
Y. Ali, D. Qiu, B. Jiang, F. Pan, M.X. Zhang, Current research progress in grain refinement of cast magnesium alloys: a review article, J. Alloys Compd. 619 (2015) 639651.
-
R.G Guan, D Tie, A review on grain refinement of aluminum alloys: progresses, challenges and prospects, Acta Metall. Sin. Engl. 30 (2017) 409432.
-
T Quested, Understanding mechanisms of grain refinement of aluminium alloys by inoculation, Mater. Sci. Technol. 20 (2004) 1357 1369.
-
K Kocatepe, C Burdett, Effect of low frequency vibration on macro and micro structures of LM6 alloys, J. Mater. Sci. 35 (2000) 3327 3335.
-
L. Zhang, Ultrasonic processing of aluminum alloys, (2013).
-
A Singer, Principles of spray rolling of metals, Met. Mater. 4 (1970) 246250.
-
J.G Kaufman, E.L Rooy, Aluminum Alloy Castings: Properties, Processes, and Applications, ASM International, 2004.
-
A Babaei, M Mashhadi, Characterization of ultrafine-grained aluminum tubes processed by Tube Cyclic ExtrusionCompression (TCEC), Mater. Charact. 95 (2014) 118128.
-
N Su, R Guan, X. Wang, Y Wang, W Jiang, H Liu, Grain refinement in an Al Er alloy during accumulative continuous extrusion forming, J. Alloys Compd. 680 (2016) 283290.
-
A Greer, A Bunn, A Tronche, P Evans, D Bristow, Modelling of inoculation of metallic melts: application to grain refinement of aluminium by AlTiB, Acta Mater 48 (2000) 28232835.
-
H Ghadimi, S.H Nedjhad, B Eghbali, Enhanced grain refinement of cast aluminum alloy by thermal and mechanical treatment of Al5TiB master alloy, Trans. Nonferrous Met. Soc. China 23 (2013) 15631569.
-
B Murty, S Kori, M Chakraborty, Grain refinement of aluminium and its alloys by heterogeneous nucleation and alloying, Int. Mater. Rev 47 (2002) 329.