
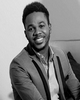
- Open Access
- Authors : Steve Efe , Jacob Oluwoye
- Paper ID : IJERTV9IS020385
- Volume & Issue : Volume 09, Issue 02 (February 2020)
- Published (First Online): 13-03-2020
- ISSN (Online) : 2278-0181
- Publisher Name : IJERT
- License:
This work is licensed under a Creative Commons Attribution 4.0 International License
Multi-Criteria Decision Making for Underwater Concrete Bridge Piles Inspection
Steve Efe1, Jacob Oluwoye2
1 Department of Civil Engineering, Morgan State University, Baltimore Maryland, U.S.
2 Alabama A and M University, Huntsville, Alabama, U.S
Abstract:-The effectiveness of any structural repair or rehabilitation process depends on the proper evaluation of its deterioration state, appropriate repair technology selection from alternatives, and consideration of implementation strategies. Pile repair technologies ranges from replacement and installation of supplemental piles to a wide range of pile wraps and jackets to restore strength and provide added protection from further deterioration. These projects, more often than not, involve significant agency resources of manpower and monetary cost due to possible instances of inaccessibility of these substructures under water and adaptability of repair approach, therefore many agencies continue to seek effective assessment measure that result in longer-lasting and more effective repair strategy that considers site-specific conditions. Since the integrity of these concrete pile structures invariably has an effect on its structural life, underwater cracks must be well assessed for appropriate remediation considering both short and long-term consequences. Although there are sundry of repair and protection techniques adopted by many agencies, decision on appropriate repair solution must consider accessibility of repair and adaptability of the structural repair bearing in mind site-specific conditions. To assist in a rational repair decision-making process for moderate to severe crack damage conditions, this study aims to (1) gather information regarding crack assessment and common repair technology in order to make effective comparisons between rehabilitation methods 2) Utilize Fuzzy AHP method, a multi-criteria decision making model in ranking underwater concrete pile repair technologies based on cost and effectiveness criteria.
Keywords: Fuzzy AHP; Multi-criteria decision making; Condition assessment of piles; Structural health monitoring; Pile repair technology
1.0 INTRODUCTION
Piles are used in several waterfront structures for providing stability and load transferring purpose. The material used for pile construction could be timber, concrete or steel sections. The adverse environmental conditions caused by seawater, high humidity, harsh temperature effects, and freeze-thaw cycles might signifying accelerates the deterioration process (Figure 1). The investigation of the cracks causes, maintenance and possible retrofitting procedures are highly important, especially for the structures exposed fully or partially to water. It is reported that piles should specifically be monitored 10 feet above and 5 feet below the waterline (Hearn, 2007). Cracks are common in new and old piles made of concrete material due to structural and non- structural causes. Since the concrete has an insignificant tensile strength, cracks happen as the volume changes under temperature and humidity variations. However, cracks might occur under overloading, reinforcement corrosion, and structural settlements. Even if the cracks are not large, they are indicators of the early structural deterioration surrounding by the salty water with harmful material accelerating the damaging process. Cracks might also occur during the fabrication, poor installation and overriding processes, which are specifically reported for the piles with under water portions (Davis, et al., 1998).
Fig. 1. Waterfront structures with piles exposed to water
Currently there are over half a million bridges and decent number of subsutural systems in need of evaluations for repair and rehabilitation in the United States. The severity of crack in concrete piles could vary from minor concrete spalls to complete fracture (Safiuddin & Soudki, 2011). Knowing that concrete piles replacement is a non-conservative, costly, time consuming and complex operation, it is necessary for federal and state agencies to develop a safe and appropriate method of assessment and repair. This study investigates and develops new information for developing safe and practical solution for improving piles service life performance through effective repair and rehabilitation techniques. It also provides a selection aid for selecting appropriate of repair technologies. This will also identify cases due to the severity of structural integrity issue which might render retrofitting methods to be counter-productive in terms of cost and time as compared to rebuilding a new structure.
To accomplish this, the objectives of this research are:
-
Conduct an extensive literature review of existing research and review information from DOTs on rehabilitation techniques and utilized repair technologies.
-
Conduct a sensitivity analysis on repair options for underwater concrete piles.
2.0 LITERATURE REVIEW
-
Condition assessment of Concrete Piles:
As most piles are buried and not accessible for visible inspection, it is sometimes difficult to inspect the pile directly for integrity or cracks. A load test and quality check of a concrete pile can evaluate the satisfactory performance of the support given by the pile-soil interaction, and the quality, installation and defects in the pile (Shanafelt & Horn, 1985). One of the two most successful and commercially available methods are the sonic-echo method and the transient shock method (Brown, Turner, Castelli, & Americas, 2010). Severity of damage in concrete piles varies from minor to concrete spalls to complete fracture. In some cases, replacement of a pile is a conservative and safe method of repair. However, this can be both costly and time consuming, and such replacement may be a complex operation. At present, there are little or no published information available for guidance on the repair of moderately to severely damaged underwater concrete piles. Repair-in-place techniques have been successfully used by a few states for restoring strength of concrete piles but there is lack of actual testing of these repair methods. Some of the assessment techniques are shown in the Table 1.
-
General Repairs for Concrete Pile Structures
There are a variety of repair methods that can be done on underwater pile structure. Cathodic protection, simple surface repairs and sprayed-on concrete are typically conducted repair approaches. While the precise specification for these repairs may change depending on where they are located on the pile, the theory behind the repairs remains the same. Concrete cracking is a common problem for both substructures and superstructures. Cracking can be considered to be an important indicator of deterioration of concrete or possible steel reinforcement corrosion. Cracking can be due to a variety of reasons including corrosion of reinforcement, sulfate attack, alkali aggregate reactivity, shrinkage, thermal and load effects, frost and salt attack, impact forces, overloading, or faulty construction ( (Davis, et al., 1998). Not all cracks are considered to be structurally significant. For repair purposes, there are two types of cracks that are of significance: static and live cracks. Static cracks are inactive while live cracks are susceptible to movement due to applied loads and temperature changes. Static cracks can be repaired through epoxy injection, grouting, routing and sealing, drilling and plugging, stitching, adding reinforcement, and overlays and surface treatments. Live cracks can be repaired using flexible sealants ( (Safiuddin & Soudki, 2011). Determining the best approach for crck repair can be a difficult course of action. Depending upon the structural implications of the cracking, and the width of the cracks, the deterioration may require different solutions (Table 1).
Table 1. Rehabilitation techniques for Concrete pile repair
Reference Sponsoring Agency Findings
1. Visual Inspection
1. Visual Inspection
(Shanafelt & Horn, 1985)
(Mehta & Monteiro, 2006)
-
Radiography
NCHRP 12-21 This report provides detailed assessment of damage such as damage caused by corrosion of strands or the remaining effective prestress was not mentioned. The initial damage inspection is conducted visually with the help of some tools such as a chipping hammer, magnifying glass, ultrasonic test equipment, concrete coring equipment,
etc.
A simple method of assessing the condition of concrete is to tap the surface with a hammer and listen to the resulting tone. A high frequency pitch indicates a sound concrete whereas a lower frequency pitch indicates the presence of flaws. This simple method combined with visual inspection of concrete surface for cracks extending over the reinforcement length may provide preliminary information about the structure.
While yielding tremendous results, this approach is currently impractical for field application. Petrou et al. (2000)
(Ali & Maddocks, 2003)
GHD Company Radiographic examination involves the use of a powerful radiation source to produce x- rays. Access to both sides of the structure is required in this method. Visualization may be achieved by either radiographs or real-time imaging. For radiographs, radiographic film is exposed for up to 30 minutes. The practical limit of concrete thickness for this method is 600 mm. For real-time imaging, French Scorpion System is available.
-
Computed Tomography
This approach is currently impractical for field application.
(Ali & Maddocks, 2003)
(Mehta & Monteiro, 2006)
GHD Company Measures the attenuation of an incident beam that travels in a straight path in an object. The method can only be used when there is significant loss of section due to corrosion. Surface temperature variations and other climatic conditions affect results. The resolution limit of 1 mm and also the contrast resolution should be improved in order to use it for corrosion determination. Data collection and processing is slow.
Computed tomography using x-rays, electrical impedance tomography, and backscattering microwave imaging are methods applicable to concrete. X-ray computed tomography shows promise in detection of cracks and in locating rebar in moderate size structures. However, it requires elaborate work and is costly for setup and operation. Electrical impedance tomography is fast, inexpensive, easy to use, and has the potential
for locating rebar, water-filled fractures, and possibility of gaining information about
-
Surface Penetrating Radar
corrosion around reinforcement. Microwave imaging can be used to locate rebar within 6 cm of the surface. Although it is limited to shallow sections, it is fast, simple and relatively inexpensive.
Not well suited to assessing state of deterioration/damage although appropriate for identifying in situ conditions if these are not known.
(Ali & Maddocks, 2003)
-
Impact-Echo
GHD Company Works on the principle of reflection of high frequency electromagnetic pulses from interfaces between materials with different dielectric constants such as steel, concrete and voids. The transducer is passed over the section to locate the position and depth of tendons. However, this technique can only give relative results and is not suitable for detecting corrosion. It should be used together with destructive methods for an estimation of tendon loss.
Not currently practical for field implementation although deterioration of concrete beam subject to fatigue loads has been successfully demonstrated (Zein et al. 2008)
(Ali & Maddocks, 2003)
(Gassman & Zein, 2008)
-
Acoustic Emission
-
-
GHD Company A stress pulse is introduced in the structure by a small impact. A transducer nearby collects the reflected stress wave. The time of travel is calculated from the reflected stress wave and the corresponding frequencies denote the locations of the reinforcement or voids. The main difference from radar is the use of low frequency waves (up to 60 kHz) which solves some problems related to non-homogeneity of concrete. Although the method is relatively successful in locating voids and reinforcement, it is not suitable for the use of assessing corrosion.
NSF Demonstrated impact-echo method to determine deterioration of decommissioned 40- year-old Interstate girders subject to fatigue loads in a laboratory environment.
Apparent deterioration of concrete modulus as function of load correlated well with physical measures of accumulated damage (strain and displacement).
Acoustic emission is a viable method of continuous structural health monitoring. Alternate approaches using known applied loads (trucks) have been demonstrated to be viable methods of inspection (as different from monitoring). The methods are very promising and viable for
problem structures, although some technical hurdles remain before widespread deployment is practical.
(Ali & Maddocks, 2003)
GHD Company. Several sensors are
attached on a structure
The method is based on the principle that waves are emitted when damage occurs to a strand. Continuous monitoring is carried out with sensors. Monitoring can be used to determine new cracks but will not provide information on previously existing damage.
(Ali & Maddocks, 2003)
GHD Company. Several sensors are
attached on a structure
The method is based on the principle that waves are emitted when damage occurs to a strand. Continuous monitoring is carried out with sensors. Monitoring can be used to determine new cracks but will not provide information on previously existing damage.
Repairs to concrete substructure members are notoriously unreliable and have a high failure rate. A study was conducted to determine how effective concrete repairs are, and which repairs are the most reliable (Tilly, 2011). Engineers were surveyed throughout Europe to collect the necessary repair data. It was found that the majority of concrete bridges require repair within the first 11 to 20 years of their service life. After all of the repairs were considered, only 50% were reported as successful, with a 25% failure rate. It was also discovered that 65% of the cracking repairs were successful, whereas only 25% of the freeze-thaw repairs were successful. Repairs ranked in order of effectiveness were restoration of strength, crack injection, cathodic protection, coatings, patches, and spray. Crack injection was mostly utilized where corrosion was still in the initial stages, and may have resulted in a higher result due to the minimal corrosion. Cementitious patches, the most common repair in Maryland, were found to only be 45% successful. The use of cathodic protection provided one of the more reliable repairs throughout Europe. Cathodic protection repairs were successful 60% of the time, which was 10% higher than the average repair success rate (Tilly, 2011). The increased reliability of the cathodic protection repair may make the repair more desirable despite the initial increase in cost. Reliability of repairs is a very important concern, especially because the success rate of repairs decreases by 30% between 5 and 10 years after they are implemented (Tilly, 2011).
Table 2: Repair Technologies for Crack Assessment
Repair Technologies |
Research Article |
Findings |
1. Epoxy Injection |
Raina 1996 |
Epoxy injetion should only be utilized with cracks up to 1.0mm thick. |
ODOT 2012 |
Use epoxy injection with cracks up to 1/8-inch thick Epoxy injection typically costs around $10 per square foot and is expected |
|
to last 20 years |
||
ARTC 2003 |
Cracks up to 0.3mm in width have no adverse effect when reinforcement |
|
cover is adequate. However, cracks that are caused by severe deterioration require removal and replacement of concrete instead of typical crack |
||
repairs. |
||
ARTC 2003 |
Inactive or dead cracks can be repaired through epoxy injection, grouting, routing and sealing, drilling and plugging, stitching, adding reinforcement, |
|
and overlays and surface treatments. Active or live cracks can be repaired |
||
using flexible sealants |
||
2. Cathodic Protection Systems |
Sohanghpurwala 2009 |
Cathodic protection systems are the only existing technology that is capable |
of completely stopping corrosion of reinforcement within concrete. |
||
Sohanghpurwala 2009 |
The corrosion of steel reinforcement can be very detrimental to the strength of concrete structures. Cathodic protection is the only existing technology |
|
that can directly stop further corrosion, even in the most corrosive |
||
NYSDOT 2008 |
environment Galvanic protection systems use sacrificial anodes, typically composed of |
zinc, which provide a protective current for the steel reinforcement. The
sacrificial anodes will provide less protection over time due to the corrosion of the anode, which is expected to last from 5 to 15 years |
||
3. Simple Surface Repair |
Raina 1996 |
Simple surface repair is the most common repair. Sprayed-on concrete may |
be used for either forming new concrete or for creating a concrete encasement |
||
4. Fiberglass Jackets |
Wipf et al. 2003 |
If a concrete pile is severely deteriorated, and pile replacement is not viable, |
the deteriorated portion of the pile can be encased in new concrete using a |
||
Fox Industries/Simpson |
fiberglass or steel form jacket Fiberglass jacket systems also do not require dewatering, are effective in |
|
Strong Tie 2011 |
all water types, work above and below the waterline, and involve relatively |
|
simple installation The depth of deterioration on the pile will have a direct result on how large |
||
the fiberglass jacket needs to be for the repair to be most effective |
||
5. FRP Wrapping for Concrete Piles |
(Sen and Mullins 2007). |
They are lightweight, have high strength and stiffness, include flexibility to fit any shape, and are also corrosion free. Therefore, they have been favored |
for conducting emergency bridge repairs where speed is of the essence. For |
||
surface preparations, depressions and voids on the concrete surface have to be patched using suitable material that is compatible with the concrete |
||
substrate. |
||
For non-circular piles, the corners of the piles need to be ground to a minimum of 3/4 in. radius to avoid stress concentration in the wrapping |
||
material |
||
6. Mini Piles |
Raina 1996 |
If access to the existing piles is an issue, then adding new piling through the use of mini piles may be an effective. |
7. Pile-Underpinning |
Raina 1996 |
Underpinning should be utilized only if the existing piles or foundation are |
not capable of being repaired by less invasive methods |
-
Underwater Inspection and Repair of Concrete Piles
The inspection of underwater structures highlights issues with concrete bridges, some of which might need urgent attention such as extensive damage below the waterline not noticeable from the surface. There are different methods to repair pile region under water such as surface spalling repair, large scale repair, preplaced aggregate concrete, injection techniques, guniting or shotcrete method for repair underwater concrete structure, and steel sleeve repairing technique (McLeish, 1994; Safiuddin & Soudki, 2011).
-
(b)
-
Fig. 2. Long span bridge showing (a) pile in water (b) repair of spalled concrete piles
Surface spalling repair technique include flushing damaged region with fresh water completely, applying a bonding coat, apply the repair mortar before the coat is set, applying a curing membrane to the applied repair mortar and protecting the repaired area against wave action until it hardened adequately (Popovics & McDonald, 1989).
Concrete spall, delamination, and scale repairs are similar to crack repairs, however, they usually require a larger area to be cleaned and chipped out, steel reinforcement added and addition of more repair material.
(a) (b)
Fig. 3. Bridge showing (a) exposed reinforcement in pile (b) divers inspecting for cracks underwater
Large Scale Repair technique is a suitable option when damages caused by structural overloading, ship impact, or reinforcement corrosion especially in the splash zone. In the case where large areas are required to be restored, repair method and material selection is considerably important if shrinkage or bleeding lead to leakage path at the top of parent concrete and repair material interface. When repairing materials have great thickness, thermal cracking may develop due to rise of temperature even though surrounding water decline the temperature rise. Furthermore, repair of reinforcement is frequently needed because of distortion and considerable corrosion of reinforcement. Steel repairs include proper assessment and cleaning of corroded members to precede the coating of anti-corrosive underwater epoxy paint or other approved products. Additional strength stiffeners can also be added and encased within an FRP jacket filled with epoxies and corrosion inhibitors (Safiuddin & Soudki, 2011).
-
(b)
Fig. 4. Bridge showing (a) section loss in piles (b) severe concrete support conditions
There are high-performance epoxy systems designed for underwater grouting and pile encapsulation where a longer life system is required. The grouts, which may be pumped or poured in place, are a low viscosity epoxy which is mixed with graded sand aggregate to encapsulate concrete pilings (Shanafelt & Horn, 1985).
-
(b)
Fig. 5. Bridge showing repair using pile jacketing
3.0 METHODOLOGY
Many approaches such as Multi-Criteria Decision Making (MCDM), mathematical programming and Artificial Intelligence (AI) have been used for solving selection problem (Setak et al., 2012). There are many multi-criteria models which include Technique for Order Preference by Similarity to Ideal Solution (TOPSIS), Analytical Hierarchy Process (AHP), Analytic Network Process (ANP) and Multi-Attribute Utility Technique (MAUT).
Every MCDM methods consists of four principal steps:
-
Structuring the decision problem by specifying the objectives and the attributes needed to be measured.
-
Generating alternatives and assessing their consequences in terms of the attributes identified.
-
Determining the preferences of the decision maker(s)
-
Evaluating and comparing the alternatives.
Fig. 6. Schematic Representation of Decision Analysis
Fuzzy AHP which was introduced by Saaty (1980) and has been one of the most extensively used approaches for solving multi- criteria selection problem that describes the whole decision system by decomposing a complex problem into a hierarchical multi- level structure (Fig. 7). It involves the following:
Step 1: Define the decision-making problem.
The criteria and sub-criteria for evaluating the underwater concrete pile repair alternatives using fuzzy AHP is illustrated in Figure
1. Decision makers needs to evaluate the performance of an repair measure based on the established two important criteria of cost and performance characteristics. Each criterion is then broken down into sub-criteria. There are two sub-criteria as illustrated in Figure 7. For this problem, four sub-criteria were considered. For example, repair cost is the a sub-criteria under Cost criteria which explains the incurred cost due to maintenance and impact damage repair while initial cost of the repair scheme represents the estimated cost sustained during the installation of the repair technology.
Step 2: Decompose the problem in a hierarchical structure with decision elements.
In this stage, the goal, criteria and sub-criteria of the problem are put in a hierarchical form as shown in Fig. 7.
Step 3: Establish pairwise comparison matrix of the criteria using Triangular Fuzzy Numbers and calculate the weight of criteria. A 9-point scale will be used to describe the relative importance of criteria with respect to the goal (Tsaur et al., 2002) as shown in Table 2. The weights of criteria are calculated using geometric mean method (Buckley, 1985).
Step 4: Convert to crisp value.
Let the fuzzy evaluation for criterion i be ( , , ), where l represents lower value, m is middle value and u is upper value. Each fuzzy evaluation of every criterion has to be converted into crisp value. It was done as in the following step.
Table 2: Saatys Crips Scale and Fuzzified Scale for Pairwise Comparison
Saatys Crips Scale
Judgment Definition
Triangular Fuzzy Scale
Triangular Fuzzy Reciprocal Scale
1
Equal Importance
(1,1,2)
(1/2,1,1)
2
Least Important
(1,2,3)
(1/3,1/2,1)
3
Weak Importance
(2,3,4)
(1/4,1/3,1/2)
4
Less Strong Importance
(3,4,5)
(1/5,1/4,1/3)
5
Strong Importance
(4,5,6)
(1/6,1/5,1/4)
6
More Strong Importance
(5,6,7)
(1/7,1/6,1/5)
7
Very Strong Importance
(6,7,8)
(1/8,1/7,1/6))
8
Extremely Importance
(7,8,9)
(1/9,1/8,1/7)
9
Very Extremely Importance
(8,9,9)
(1/9,1/9,1/8)
The relative weight of all evaluation criteria are still in the form of triangular fuzzy number and need to defuzzify using Center of Gravity (Chou & Chang, 2008)
= +
= +
()+()
(1)
3
Finally, in order to effectively compare the relative importance of the evaluation criteria, the defuzzified priority values are normalized using
=
(2)
Step 5: Consistency check.
Consistency ratio (CR) is required to determine whether the weight assign by the decision maker is correct or not. CR< 0.1 indicates consistent judgment in pairwise comparisons. CR is calculated using equation 3, equation 4 and Table 3.
= max
1
=
Table 3: Random Consistency index (CI)
(3)
(4)
n
1
2
3
4
5
6
7
8
9
10
RI
0
0
0.58
0.9
1.12
1.24
1.32
1.41
1.45
1.49
Step 6: concrete pile repair technology
Now, once both criteria weights and performance of each alternative on each criterion has been assessed and defuzzified, the overall or final performance of each repair measure can be calculated by the weighted sum method. Ranking of the selection type was done based on the final score of the criteria
Fig. 7. Proposed Decision Making Matrix Framework
4.0 RESULTS AND DISCUSSION
Fuzzy AHP Method
In this section the results from applying the Fuzzy AHP method to the decision problem are presented.
-
Weights of Goals and Measures in the Decision Problem
As discussed in previous section, various elements of the decision making problem that served as the input for the Fuzzy AHP method were identified, the decision making problem was structured, and the values of the alternatives for each criterion the weight of criteria were obtained. The weight of each criterion and the contribution of sub-criteria in the decision problem are presented in Table 4.
Table 4: Weights from Synthesis of repair technology alternatives with respect to noise abatement goal
Barrier Type
Cost (Initial & Maintenance)
Rank
FRP Wrap
0.235
1
Fiberglass Jacket
0.137
3
Concrete Encasement
0.073
4
Anodes
0.059
8
Underpinning
0.077
6
Mini Piles
0.233
2
Epoxy Ejection
0.079
5
Mortar
0.069
7
Simple Surface Repair
0.038
9
-
Weight of Repair Technology Alternatives from Synthesis of Objective with Respect to Criteria
The first set of results obtained was the weight for every measure, or criteria, in the decision problem. Thisvalue indicates the desirability of the alternatives in relation to each measure, i.e. how well the alternatives perform with regard to each criterion. These values are presented in Table 5. It shows the weight values for each alternatives with respect to cost and effectiveness criteria. The weights of the alternative shown in Table 5 range from 0 to 1, with the alternative with the highest weight being the most desirable option (the one the decision maker should select). In addition, these criteria weights are integrated into the decision problem to determine the weights of the goal for the decision problem i.e. the overall repair technology option selection.
Table 5. Weight for each Alternative Considering Criteria
Alternative ID
Barrier Type
Cost (Initial & Maintenance)
Effectiveness
Alternative 1
FRP Wrap
0.112
0.237
Alternative 2
Fiberglass Jacket
0.120
0.119
Alternative 3
Concrete Encasement
0.081
0.079
Alternative 4
Anodes
0.055
0.059
Alternative 5
Underpinning
0.225
0.059
Alternative 6
Mini Piles
0.230
0.257
Alternative 7
Epoxy Ejection
0.044
0.079
Alternative 8
Mortar
0.063
0.079
Alternative 9
Simple Surface Repair
0.070
0.032
-
Dynamic Sensitivity Analysis
A dynamic sensitivity and performance analysis were carried out to examine the performance of repair technology alternatives considering the overall objective of selecting a repair technology for a moderately damaged underwater pile. As shown in Figure 8, FRP wraps have an overall highest weight performance (0.239), followed by mini piles (0.237) and fiberglass jacket (0.125). The use of epoxy (0.07), high strength mortar (0.067), concrete encasement (0.065), and underpinning (0.062) are better options to anode (0.058) and simple surface repair (0.032) alternatives. In terms of effectiveness of repair options, the use mini piles (0.86) seems the best alternative followed by FRP wraps (0.79), concrete encasement (0.27), fiberglass jacket (0.4), epoxy injection (0.27), anodes (0.2) and simple surface repair (0.12) as seen in Figure 9. In relation to cost, mini piles (0.337) and underpinning (0.169) are deemed the less cost effective repair technology as shown in Figure 10. Simple surface repair (0.006) is the best option in terms of cost followed by anodes (0.075), FRP wraps (0.096), fiberglass (0.15), and concrete encasement (0.161).
Figure 11 shows the sensitivity analysis plot of the effectiveness of each repair technology alternative against cost. It can be seen that at lower cost and lower effectiveness of repair technology, simple surface repair, mortar, epoxy injection, anodes are preferable while mini piles are preferred at lower cost and high effectiveness; FRP wraps are best options at higher effectiveness and high cost; and fiber glass jacket at higher cost and considerable effectiveness.
Fig. 8. Performance Sensitivity Analysis for Underwater Pile Repair Selection for Moderate to Extreme Cracks Damage
Fig. 9. Performance Sensitivity Analysis with respect to Cost
(a)
-
-
Fig. 10 (a) and (b). Performance Sensitivity Analysis with respect to Effectiveness
Fig. 11. Sensitivity Analysis of Effectiveness versus Cost
Decision Aid Tool
The multi-criteria decision analysis tool for underwater inspection of piles (UWI-Piles) shown in Figure 12 is a spreadsheet-based decision making tool designed to help practitioners apply a set of decision criteria to a variety of alternatives or strategic options. It is particularly useful for decisions that require substantial judgment and for which numbers may not be available. By working through a series of decision-process steps, practitioners can establish criteria for the assessment and comparison of different possible alternatives and then compare choices. The most desirable noise abatement option can be identified in the spreadsheet. Making judgment-based decisions` among a variety of viable options is made easier when a systematic process is utilized such as
the one offered in this tool. There are three steps for the multi-criteria decision making based on cost, effectiveness, feasibility, acoustic longevity criteria. Users can select the sub-criteria that are relevant to the specific conditions.
Step 1: Data Selection: Users can choose abatement measure sub-criteria (Figure 13) by clicking on the cells in column D e.g. Select cell D27 to decide what option to consider in the multi-criteria decision (MCDA) under Effectiveness Criteria. Users can select no option (N/A) if any sub-criteria will not be considered in the MCD Analysis
Step 2: Data Analysis: Figure 14 shows the data obtained from Fuzzy AHP multi-criteria decision making analysis of responses from transportation professionals of various DOT's and agencies
Step 3: Final Selection: This step provides the best abatement option for the Type 1 project based on the sub-criteria selection made in Step 1 (Figure 15).
Fig. 17. Selection from sub-criteria for multi-criteria decision analysis
Fig. 17. Selection from sub-criteria for multi-criteria decision analysis
Fig. 12. Interface for the multi-criteria decision analysis tool for type 1 project
Fig. 13. Data selection from sub-criteria for multi-criteria decision analysis
Fig. 14. Data analysis of fuzzy weights based on criteria and sub-criteria selection
Fig. 15. Final ranking of abatement alternatives based on multi-criteria decision analysis
CONCLUSIONS
Analyzing the results from the dynamics analysis of repair technology selection for medium to large scale repair indicates that the effectiveness of the repair technology is the most influential factor on the ranking of alternatives. This result is valid for similar cases, especially concrete piles where financial concerns are not the major issue and the project is intended to provide reliable support for traffic during its life cycle. The following can be deduced from the result in Table 2.
-
The FRP wrap repair option is the most favorable amongst the alternatives considered (weight = 0.235), possibly due to its lightweight option, strength and stiffness, corrosion-free and workability around large areas. It is favored in emergency bridge repairs where speed is important and for corrosion-damaged submerged concrete piles. Due to lower initial cost of construction compared to mini piles, it achieves a better overall goal of repair technology for underwater concrete pile substructure.
-
Mini Piles was ranked second in preference (weight = 0.233) for cases where deterioration in concrete piles has led to significant loss in strength and load carrying capacity. Mini piles is believed to provide additional strength and mitigate expensive repairs of the old concrete pile and a better alternative to FRP wrap when considering effectiveness criteria.
-
Fiberglass jacket are good repair technology option where section or strength loss is noticeable. They are ranked behind FRP wrap due to higher initial cost and mini piles due to their overall effectiveness (weight = 0.119).
-
Simple surface repairs are the least effective (weight = 0.038) for medium to large crack repairs as they are incapable of restoring the long-term structural capacity of the concrete piles and maintenance cost over its continued life span.
REFERENCES
-
Ali, M., & Maddocks, A. (2003). Evaluation of corrosion of prestressing steel in concrete using non-destructive techniques. 40(5), 42-48.
-
Brown, D. A., Turner, J. P., Castelli, R. J., & Americas, P. B. (2010). Drilled shafts: Construction procedures and LRFD design methods. United States Federal Highway Administration.
-
Davis, A. G., Ansari, F., Gaynor, R., Lozen, K., Rowe, T., Caratin, H., & Hertlein, B. (1998). Nondestructive test methods for evaluation of concrete in structures. American Concrete Institute, ACI, 228.
-
Gassman, S., & Zein, A. (2008). Change in impact-echo response during fatigue loading of concrete bridge T-girder. 105(4), 395.
-
Hearn, G. (2007). Bridge inspection practices. Transportation Research Board.
-
McLeish, A. (1994). Underwater concreting and repair. CRC Press.
-
Mehta, P., & Monteiro, P. (2006). Materials. Mehta, P. Kumar, and Paulo JM Monteiro. "Materials." McGrawHill, (2006).: McGrawHill.
-
Popovics, S., & McDonald, W. (1989). Inspection of the engineering condition of underwater concrete structures. Army Engineer Waterways Experiment Station Vicksburg MS Structures Lab.
-
Safiuddin, M., & Soudki, K. (2011). Sealer and coating systems for the protection of concrete bridge structures.
-
Shanafelt, G., & Horn, W. (1985). Guidelines for Evaluation and Repair of Prestressed Concrete Bridge Members. NCHRP Report, (280).
-
Tilly, G. (2011). 14 Durability of concrete repairs. Concrete repair: A practical guide.
-