
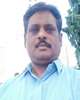
- Open Access
- Authors : Dr. K. Vasantha Kumar , Akula Deep Chander , Alugala Sai Chandu , Anwar Pasha
- Paper ID : IJERTV11IS040002
- Volume & Issue : Volume 11, Issue 04 (April 2022)
- Published (First Online): 14-04-2022
- ISSN (Online) : 2278-0181
- Publisher Name : IJERT
- License:
This work is licensed under a Creative Commons Attribution 4.0 International License
Fabrication of Natural Fibre Composite Material with Problems and Remedies
Dr.K.Vasantha Kumar1, Akula Deep Chander2, Alugala Sai Chandu3, Anwar Pasha4
1 Assistant Professor and Head, Department of Mechanical Engineering, JNTUHUCEJ, Jagitial, Telangana.
2 M-Tech, Department of Mechanical Engineering, JNTUHUCEJ, Jagitial, Telangana.
3 B-Tech, Department of Mechanical Engineering, JNTUHUCEJ, Jagitial, Telangana.
4B-Tech, Department of Mechanical Engineering, Gurunanak Institute of Technology, Ibhrahimpatanm, Hyderabad, Telangana.
AbstractNatural fibre composite material is fabricated by using epoxy resin as a matrix material and natural fibres as reinforcement material. Combination of two or more different material is called composite material. This paperdeals completely about the problems faced in composite fabrication along with the perfect remedies to overcome those problems. For this purpose, different fibre used like sisal fibre (Agave sisalana), coir fibre (Cocas nucifera),Palm leaf sheath fibre (Arecaceae) these are the inorganic material, Araldite LY-556(Resin), Aradur HY- 951(Hardner) these are the organic material used for the preparation of hybrid composite material. Porosity, non- uniformity in surface, Resin wastage, Maintenance of curing temperature and time, Hydrophilicity of fibres etc are discussed in this paper briefly and it includes Remedies for the problems. Composite manufacturing of natural fibre faces some problems these problems are reduced to some extent by this study. This problem analysis helps to improve the quality of hybrid composites and its properties.
KeywordsHybrid composite material, Araldite LY-556, Aradur HY-951, Porosity, Hydrophilicity of Fibres.
-
INTRODUCTION
In present scenario composite material plays a significant role in the industrial applications, it has wide area in theresearch field of material science due to superior properties than the conventional material. Natural fibre composites are most widely used because these fibre exhibits better physical, chemical, Mechanical properties than the artificial fibres. Natural fibre composite are emerging materials in present era due to their properties like less weight, low density, biodegradable, high specific strength and these fibres cannot affect the environment in any circumstance. Official website of international year of natural fibre 2009 states that approximately 500000 tonnes of coir fibre produce mainly in India and Sri Lanka, 300000 tonnes of sisal fibre produced mainly in Brazil,Tanzania, Kenya.
Fibres used for this study are Sisal fibre, Coir fibre and Palm leaf sheath fibre. These fibres are shown in figures 1.1,
1.2 and 1.3 respectively.
Figure 1.2 Coir Fibre Figure 1.1 Sisal Fibre Laminate Laminate
Figure1.3 Palm leaf sheath Fibre Laminate
Sisal plants are mostly available in tropical and sub- tropical region where the temperature is high. The leaves of this plants are in the shape of swords and have different length this is because of the environmental conditions where the plant grows and based on the species of the plant. This fibre is used to prepare ropes, bags, foot wear etc. Coconut fibre it is also known as coir fibre, this fibre is extracted from the coconut tree. Coconut tree plays a significant role in the economy by producing coconut oil, copra and coir fibre. This tree takes more than 16 yearsfor their peak generation of fruits from the fruit only fibre extracted. This fibre is used to prepare ropes wires, floor mats etc. Palm tree is the best producer of two useful fibres, the scientific name of this tree is arecaceae it produces two different types of fibres like palm fruit fibre and palm leaf sheath fibre. This fibre is used for the preparation of gaskets, it is used as a biomass fuel for oil mill plants.
Epoxy resin is used for the preparation of hybrid composite material. Compared to other resins this is better due to their properties like it give excellent strength and hardness to the material, it gives chemical, heat and electrical resistance. The only disadvantage of this resin is processing is difficult it can be rectified by proper mixing of resin and hardener and cost is also more compared to other resins. Due
to its better properties, it is mainly used in aerospace, defence and marine applications. For this study Resin LY-556 and Hardener HY-951 are used these have low viscosity and water resistant, curing time varies with curing temperature maintained in the laboratory. So many researches are going on in the field of natural fibre composite material manufacturing because of these fibres does not affect the environment and exhibits better properties.
Properties of composite depends upon the pre- processing of natural fibres [1]. Properties of the composite varies with respect to in what environment material is fabricated and exposed. Fracture behaviour of composite laminate under different environmental conditions like water, 5% of NaOH, vegetable oil and petrol play a major role in natural fibre composite fabrication [2]. Mechanical properties of natural fibre composite are affected by the curing temperature of the composite material, as the curing temperature increases mechanical properties increases. [3]. Water absorption increases with increase in the weight percentage of fibre [4]. Thermal conductivity of composite increases as the water content in the palm fibre mesh is more [5]. At lowest temperature and time performance reduction of composite material is small [6].
Only disadvantage of natural fibres is poor wettability this is due to high moisture absorption of fibres and adhesion between fibre reinforcement and matrix these can be reduced by surface modification of natural fibres. Chemical treatment of the fibre improves the properties of the composite material [7]. Micro compressive defects presence in the fibre reduces the mechanical properties of the material. Use of different cross-sectional fibres reduce the layer-by-layer rejection of composite material [8]. Glass-sisal-banana fibres reinforced composites show better properties than synthetic fibres. Maximum tensile, flexural and impact strengths are hold by hybrid composite material [9]. Untreated fibres achieved more insulation rate than treated fibre because voids are present in the untreated fibre these voids act as good insulators, as the volume fraction of fibre increases insulation rate also increases [10].
Most of the authors mainly explain about the effect of different parameters on the properties of the composite material but the main aim of this paper is to give brief description about the problems occur during thefabrication of hybrid composite material along with their remedies.
-
METHODOLOGY
Methodology involves the sequential steps that are involved in the hybrid composite manufacturing by using sisal, coir and palm leaf sheath fibres as a reinforcement materials and Resin along with hardener used as a matrix or binding material. Resin main function is to transfer stress developed during fabrication of composite.
-
COLLECTION OF FIBRES
Fibres are directly or indirectly extracted from the plants and trees but for this study fibres like sisal fibre were extracted from the sisal plant leaf. Coir and palm leaf sheath fibres are extracted from the coconut tree and palm tree.
-
PREPARATION OF FIBRES
Fibre preparation includes two stages that is extraction of fibres from the source like trees and plants and another one is preparation of fibre laminate on the basis of required dimensions. Extraction of fibres from the plants inludes different stages these are depends on the type of fibre to be extracted from the plant as well as trees.
Sisal fibre extraction process is somewhat lengthier than coir and palm leaf sheath fibre extraction process because this involves cutting of leaf from the plant, crushing of the leaf, washing of the crushed leaves and finally drying. Sisal plant leaves are removed from the plant and then sent these leaves into the crushers wherethe pulpy content in the leaves are removed and those crushed leaves are washed with fresh water in order to remove remaining pulpy content, cleaned fibres are dried in sunlight for 3-4 days in order to get good fibre.
Coir fibre is extracted from the husk of the coconut fruit. In order to remove the copra from the coconutfruit it is necessary to remove husk from the fruit this husk contains the fibre this is extracted by manually or by using machines. In order to get good fibre, it is necessary to remove soft fibrous content from husk and expose fibre to sunlight.
Palm leaf sheath fibre is extracted directly from the trunk case of the palm tree. This fibre produced in the form of sheets of fibre and surrounds the tree. No need of meshing for this fibre it produced as fine meshed sheet. Preparation of fibre laminates includes the dimensions of the laminates as well as pre-processing of fibres like meshing in case of sisal fibre. All the three fibre laminates are prepared with the dimensions of 30×30×1 cm.
-
MOLDS PREPARATION
Mould preparation includes the preparation of mould box that useful during the fabrication of hybrid composite material. Mould box with the dimensions of 32×32×3 cm is prepared. It prevents the wastage or spoilage of resin mixture during fabrication process.
-
FABRICATION OF HYBRID COMPOSITE MATERIAL
Composite materials are prepared by using three different manufacturing methods those are Injection moulding, compression moulding and resin transfer moulding. For this composite preparation compression moulding is used because it gives good composite. Fabrication process of hybrid composite as follows
-
Resin and hardener with proper proportions that is 10:1 was mixed.
-
Compression moulding method is employed for the fabrication of hybrid composite material because of its simplicity and less time for moulding.
-
By using hand layup technique composite was prepared, it includes layer by layer application of resin mixture and placing reinforcement material one on the above. Stacking of layers are in the form of sisal-coir-palm-coir-sisal.
-
After completing hand layup process composite layers were subjected to load condition (20KN) on universal testing machine up to 48 hours under the room temperature as shown in the figure 2.1.
Figure 2.1 Compression of Fibre Laminates on UTM
-
-
-
PROBLEMS AND REMEDIES OF NATURAL FIBRE COMPOSITES
Every manufacturing process has its own advantages as well as limitations, natural fibre composite are emerging and most widely used material because of their extensive properties. During the fabrication process of these materials different type of problems occur those problems are as follows.
-
Porosity occurs in the material.
-
Maintenance of curing temperature.
-
Maintenance of curing time.
-
Lack of uniformity of resin.
-
Fibre preparational problems.
-
Mixing of resin with hardener.
-
Maintenance of load.
-
Formation of uneven surfaces.
-
Fibre rejection.
-
Resin wastage.
-
Hydrophilicity of fibres.
-
POROSITY OCCURS IN THE MATERIAL
Porosity is defect in manufacturing process, this can cause by air trapped in the material during fabrication. In case of fibre composites, porosity occurs due to the improper meshing of fibres, non-uniformity of layers and incomplete spread of resin mixture on the surface of the fibre layers.
In case of fibres like sisal, banana, jute, flax etc meshing is needed, during meshing gaps are occur due to the uneven surfaces of the fibre and non-uniformity in the individual fibre layers these two effects caused onlybecause of fibre extraction, this cause porosity of composite material as shown in figure 3.1.
Figure 3.1 Porosity in Composite Material
Remedies for this problem are proper meshing of natural fibres, uniform application of resin throughout the composite material and by taking proper dimensions for the fibre laminates. Proper meshing in the sense do the mesh in any type either cross mesh or straight mesh without a gap between the fibres, these gaps can be reduced by following some techniques like use the water and dip the fibre in it and then start meshing this method works effectively for manual meshing. This method reduces the maximum gaps in the fibre laminates.
-
EFFECT OF CURING TEMPERATURE
Curing temperature is the minimum or maximum temperature that is used to cure the material in perfect form. Curing is the process in which the atoms in the material bonded tightly together, this increases strength of the material. In case of fibre composite manufacturing curing temperature plays an important role, each and every resin has different curing temperatures. If the curing temperature is not maintained properly the material will faildue to the weak bond formed in between the fibre laminates. And resin mixture does not spread completely throughout the composite material and there may be a chance of losing viscosity of resin due to improper maintenance of curing temperature. It is best or acceptable to maintain room temperature as a curing temperaturebecause of at the minimum temperature of curing, time taken for curing is more so there is less chance to get
failure of material.
-
Effect of Curing Time
Curing time is the time which is given to the material to cure under the optimal conditions. Improper maintenance of curing time leads to fail the material structure and also it leads to increase the boundary size of the molecules in the fibre material. In case of natural fibres, it is necessary to maintain curing time according to the resin considerations.
In order to get good composite material, it is necessary to allow the material for curing 24-48 hours. Thisis completely depending on the temperature where the composites were manufacturing.
-
LACK OF UNIFORMITY OF RESIN
Resin plays a key role in the natural fibre composite manufacturing. It is used as binding material in order to bind two or more different material. Application of resin must be uniform throughout the composite material in order to get good composite. non-uniformity of resin on the fibre layers reduces the strength of the composite material.
Natural fibres are mostly affected by this non- uniformity of resin in material because these fibres absorb more resin than synthetic fibres. Improper application of resin in the natural fibre composite material shown in the figure 3.2.
Figure 3.2 Improper Resin Application
This non-uniformity of resin in the natural fibre composite materials can be reduced by applying maximum amount of resin on to the fibre laminates. Best way of applying resin in hand lay-up method is to pour the resin mixture on the laminates and then apply by using brush after that using roller spread resin throughout the laminate. Hand lay-up method needs good application of resin in composite in order to get better strength of material.
-
FIBRE PREPARATIONAL PROBLEMS
Natural fibre extraction is somewhat difficult because these fibres are extracted from plant leaves, fruits of trees etc so during these extractions so many preparational problems occur. For study sisal, palm and coir fibresare used. In case of sisal fibre extraction some amount of fibre will be lost in the crushing and cleaning stages of fibre extraction. Meshing is also one of the preparational problem.
In case of coir fibre extraction maximum amount of fibre wasted because fibre must be removed from the husk of the coconut fruit. In case of palm leaf sheath fibre, during the extraction of sheath from the palm tree sheath may be damaged. These sheaths sometimes contain girt and some unusual layers this cause to reduces bonding of fibres. These all problems increase time for fibre preparation and affects the strength of the composite material because of if these fibres contain any unusual matter, it will affect the bonding capacity of fibres.
All the above preparational problems can reduced by following way of fibre preparation. In case of sisalfibre during extraction, remove the pulpy content completely and care must be taken to loss of fibre in this step and mesh the sisal fibres properly by following method discussed in section 3.1 as shown in figure 3.3.In case of coir fibre remove the soft content from the fibre as shown in the figure 3.4 and for laminate preparation take correct amount of coir fibre on the basis of thickness of laminate care must be taken in order to reduce voids in the laminates. Remove the unusual layers from the leaf sheath as shown in the figure 3.5 and extract
fibre from tree in easy way do not apply more force during extraction.
Figure 3.3 Meshed Sisal Fibre Laminate
Figure 3.4 Fibre Containing Soft Matter
Figure 3.5 Unusual Matter on the Palm Leaf Sheath Fibre
-
MIXING OF RESIN WITH HARDENER
Proper mixing of resin with hardener plays a major role in the natural fibre composite manufacturing. If this mixture is not in proper proportion, there may be chance of composite material damage. If resin quantity is more in the resin mixture than hardener binding capacity of the resin mixture decreases, if hardener quantity is more than resin quantity in the resin mixture it will solidify fast. It is better to take ratio of the resin o the hardener is 10:1, one part of hardener mixes with ten parts of the resin.
-
MAINTENANCE OF COMPRESSION LOAD
Generally natural fibre composite materials are fabricated by using compression moulding and hand lay- up technique, these two methods give the good strength to the composite material. In compression moulding method, compressive load is necessary for the proper compression of
the fibre laminates. If compressive load is too high the laminates of fibres are compressed more than its deformation of compressive limit at that time there may be chance of breakage in the fibre laminates individually, If the compressive load is too low there is improper formation of composite material as shown in the figure 3.6.
Figure 3.6 Effect of Load on Composite
Load must be calculated based on individual strength of each fibre. And consider the load based on individual and collective thickness of fibres. If thickness of the laminates is less applied small amount of load and if the thickness is more apply more load.
-
ORMATION OF UNEVEN SURFACES
This is the primary problem in the natural fibre composite manufacturing process, uneven surfaces formed due to the high compression load, improper preparation of fibre laminates and non-uniformity in the resin application as shown in the figure 3.7, Formation of uneven surfaces lead to reduce the strength of composite material and uneven surfaced material does not give better results in testing like impact test, tensile test and flexural test. Uneven surface of the composite material can be reduced by maintaining optimal load application and apply the resin until laminate completely absorb the resin mixture.
Figure 3.8 Fibre Rejection
Fibre rejection in the natural fibre composite fabrication by using the same form of fibre as a laminate for the composite, reduce the adhesion between the fibre laminates by applying large amount of resin in between the laminates and select the fibres which must have same structural properties as smoothness.
-
RESIN WASTAGE
Resin is the binding material in the natural fibre composite fabrication process, the main function of thisresin is to transfer stress developed during fabrication between the fibre laminates. During natural fibre compositemanufacturing resin wasted more, because natural fibre laminates absorb more resin quantity. This lead increase of fabrication cost of the natural fibre composite material.
Resin wastage can be reduced by preparing mould box which is having the same shape of the fibre laminates and dimension also same but 3-5 mm clearance on each side is needed, this box prevents wastage of resin and spread this resin back between the laminates of fibres.
-
HYDROPHILICITY OF FIBRES
Hydrophilicity is nothing but ability to absorb the water and easily attracted to the water. This hydrophilicity of fibres reduces the strength of each fibre and weakens the complete fibre laminate. This causes the formation of white layer on the upper surface of the composite material because of water absorption and heat generated inside the composite material. This heat generation draws the water content from the fibre laminates and form white layer as shown in figure 3.8.
Hydrophilicity of fibres can be reduced by exposing fibres to sunlight before fabrication process starts, maintain room temperature as a curing temperature and do not use the hardener proportion in the resin mixture more than one part in ten parts of resin.
Figure 3.7 Uneven Surface on Composite
-
FIBRE REJECTION
Fibre rejection in the sense layers or laminates of the fibres may be rejected to bind from the other fibrelaminate as shown in figure 3.8, this will cause due to the adhesion between two different fibre material. It leads to improper binding of natural fibre laminates this effect on the complete composite material. This is mainly because natural fibre is of different kind, some natural fibres are soft, and some are hard in structure, so it is difficult to bind these two materials.
Figure 3.8 White Layer Formation on the Surface of Composite
-
-
-
CONCLUSION
In this study natural fibres are used to prepare the hybrid composite material; these natural fibres have comparable properties with the synthetic fibres.
-
Natural fibre composite fabrication gets more
problems during process because of their structure,physical and chemical behaviour.
-
Porosity is the main problem in the natural fibre composite fabrication, this can be reduced by proper meshing and uniform application of resin mixture on the fibre laminates.
-
Hydrophilicity weakens the strength of the fibre and composite material; it can be reduced by maintainingproper curing temperature.
-
Uneven surfaces and non-uniformity of the resin reduces the ability of material to with stand external loads, this can be reduced by proper laminate arrangement and proper application of resin mixture.
-
Resin wastage can be reduced by using mould box during fabrication of natural fibre composite material.
-
Resin and hardener proportion are necessary in order to get better composite, the proportion must be10:1.
-
Cross meshing of fibres gives more strength and less porosity for the composite material.
-
Fibre rejection reduced by proper application of resin on to the fibres.
-
-
REFERENCES
15645.
[10] A. Shalwan, M. Alajmi and A. Alajmi Insulation Characteristics of Sisal Fibre/ Epoxy Composites International Journal of Polymer Science, Volume 2017., pp.1-6.