
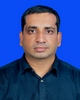
- Open Access
- Authors : Karthik Krishnaswamy , Dr. Srikanth Salyan
- Paper ID : IJERTV10IS080055
- Volume & Issue : Volume 10, Issue 08 (August 2021)
- Published (First Online): 13-08-2021
- ISSN (Online) : 2278-0181
- Publisher Name : IJERT
- License:
This work is licensed under a Creative Commons Attribution 4.0 International License
External and Internal Cooling Techniques in a Gas Turbine Blade – An Overview
Karthik Krishnaswamy
Research Scholar National Institute of Technology
Tiruchirappalli, India
Dr. Srikanth Salyan
Assistant Professor Department of Aeronautical Engineering
Dayananda Sagar College of Engineering, Bengaluru, India
Abstract Gas turbine engines are widely used in propulsion of aircraft and power generation. The thermal efficiency and power output of these engines predominantly depend upon the turbine inlet temperature (TIT). Increase or decrease in TIT affects the efficiency and power output to a great extent. Gas turbine engines currently operate at TIT ranging from 1200°C to 1500°C which is way above the melting point of blade material. Safe operation of these engines at elevated temperatures have been made possible by efficient cooling of blades, protection of blade surfaces by application of thermal barrier coatings (TBC) and advancement in blade metallurgy. Due to rapid economic and industrial growth, engines with the capability to operate at higher TIT would be required in future. Also, the metallurgy of the blade and thermal barrier coatings are required to be developed further to ensure reliable operation under harsh conditions. Different blade cooling techniques and the influence of various parameters on the effectiveness have been discussed in the literature. This paper aims to holistically address the various facets of turbine blade cooling and its operational parameters as available in the literature.
KeywordsAirfoil; Thermal Efficiency; Power output; Nusselt number; Reynolds number
-
INTRODUCTION
Gas turbines are internal combustion engines which operate on the principle of Joule-Brayton thermodynamic cycle. Gas Turbines generally have a high power to weight ratio, high reliability, reduced maintenance and compact design and hence is used in the propulsion of aircraft, marine, and land- based vehicles as well as for power generation. The thermal efficiency and power output of these engines predominantly depend upon the Turbine Inlet Temperature (TIT), compression ratio and mechanical efficiency of the compressor and turbine. Increase in compression ratio and mechanical efficiency of the rotating components will enhance the power output. However, the overall turbine efficiency is largely proportional to the TIT and therefore increasing the TIT will result in an appreciable increase in the thermal efficiency and power output [1]. With an aim to achieve higher power output, continuous efforts are being made by the designers to achieve higher TIT with reduced NOx emissions, by optimizing the blade cooling techniques, improved thermal barrier coatings (TBC), blade metallurgy and manufacturing technology.
Advanced gas turbine engines operate at temperatures ranging between 1200ºC to 1500ºC [2]. In the near future, the turbine inlet temperature may reach as high as 1700 ºC for utility turbines and 1900ºC for advanced military engines [1].
These operating temperatures are far above the melting point of the turbine blade material and hence it is considered critical to continuously cool the internal and external surfaces of the turbine blades to prevent catastrophic failure. In addition to cooling, it is also essential to protect the blade surfaces by application of TBC to prevent failure due to oxidation, corrosion, erosion creep and thermal fatigue. The life of a turbine blade can be reduced to 50% if the prediction of blade temperatures is off by only 30ºC [3].
The complex flow pattern around the airfoil increases the difficulty to predict the temperatures and therefore, it is very important to generate localized data to design appropriate and efficient cooling technique [4]. Combustor generated turbulence, laminar to turbulent transition, accelerated fluid flows, film cooling flows, secondary flows, surface roughness, rotational forces, blade tip clearance, Reynolds number and Mach number affect the heat transfer on the airfoil surface, and therefore it is necessary to know the flow physics, heat transfer distributions and potential hot spots on the airfoil surface for development of cooling schemes.
-
EXTERNAL AND INTERNAL COOLING THEORY This paper primarily focuses on the gas turbine blade cooling concepts and the factors that influence the blade cooling. The gas turbine blades are required to be cooled in order to prevent catastrophic failure of the turbine. The blades are either cooled externally and/or internally using coolant air extracted from the last stages of the compressor. The extraction of air from the compressor has an impact on the thermal efficiency and output of the engine. Therefore, the objective of various cooling techniques should be to achieve optimal thermal protection with minimal use of coolant air (3-5%) and minimized pressure drop [5]. The cooling technique varies for every engine based on the geometry and thermal load on the components subjected to the hot gas path. The coolant air extracted from the compressor is of the temperature range between 450 to 650ºC, this relatively low- temperature coolant reduces the blade temperatures to about 1000ºC, which is considered permissible for reliable operation of engines [6].
Based on the thermal load and flow conditions, the blade geometry can be classified into five major sections namely the leading edge, main body, trailing edge, end wall and the blade tip. The coolant enters the airfoil cooling passages through the blade root and then passes through several narrow serpentine passages cast on to the internal surface of the blade. The heat is conducted from the blade outer surface to the inner surface, and from the inner surface, the heat is extracted by the coolant predominantly by convection and
advection. The internal cooling techniques commonly employed in turbine blades are impingement cooling, rib turbulated cooling, pin-fin cooling, dimple cooling, swirl chambers, surface roughness and protrusions. These techniques lead to increase in secondary flows and turbulence levels thus enhancing mixing which in turn increased the advection of heat from the surface. These techniques also result to heat transfer augmentation by increasing surface areas for convective heat transfer [7]. The coolant after passing through these internal passages exits through cooling holes or slots on the blade surface forming a thin insulating layer over the external surface of the airfoil, this method of external cooling is known as film cooling. Different surfaces of the airfoil and corresponding cooling techniques are illustrated in figure 1 [2].
Figure 1: Schematic of External and Internal Cooling techniques [2].
Typically, in a gas turbine airfoil, impingement cooling coupled with film cooling is employed at the leading edge, and the rib turbulators are employed in the middle section of the airfoil. The pin-fins and dimples are used in the trailing edge of the airfoil [3].
-
FILM COOLING
Development of gas turbine components over the years has resulted in complex hot gas path component geometries and fluid surface interactions. The heat flux distribution around the inlet guide vane and rotor blade is illustrated in figure 2 [3].
Figure 2: Heat Flux distribution of a cooled Vane and Blade [3].
The external surface of the turbine vanes and blades are exposed to very high-temperature gases which result in high thermal stresses. The thermal stresses, if not effectively managed, will result in catastrophic failure of the turbine airfoils due to creep and thermal fatigue. Prolonged exposure of the turbine blades to hih temperature results in high stress levels which in-turn causes creep failure. Besides this, exposure of turbine blades to repeated and cyclic high thermal stresses induces thermal fatigue which causes plastic deformation of the turbine blade. Failure due to thermal stresses can be controlled by effectively and aggressively cooling the internal and external surfaces of the airfoil [8]. Film cooling is the most established external cooling technique to cool the surfaces of the turbine blades and vanes. The primary aim is to achieve highest overall cooling effectiveness with a minimum penalty on the thermodynamic cycle performance. The film cooling effectiveness is defined as the ratio of the difference between the mainstream hot gas and the coolant film temperature to the difference between the mainstream hot gas and the coolant temperature [9].
Film cooling protects the airfoil surface directly when compared to internal cooling techniques that remove heat from the inside surface. The film holes are drilled on the blade surface by various methods namely EDM, abrasive waterjet machining and laser drilling [11].A typical film cooled airfoil with cooling holes is illustrated in figure 3 [10].
Figure 3: Film cooled airfoil [10].
The film hole size is desired to be as small as reasonably possible to ensure better coolant distribution and uniform boundary layer across the region. Generally, the film hole nominal diameter ranges from 0.9 to 1.1 mm. However, real- time challenges exist in manufacturing small holes due to chocking of debris [12]. Film cooling effectiveness depends upon various parameters namely coolant-to-hot mainstream velocity ratio (blowing ratio), coolant-to-hot mainstream temperature ratio, coolant-to-hot mainstream density ratio, film cooling hole location, shape, configuration, and distribution. In addition, certain external parameters which affect the effectiveness of film cooling are oncoming
mainstream flow, blade wakes, rotation, secondary flows, and tip flows.
3.1 Effect of Blowing Ratio and Density Ratio
In a typical gas turbine airfoil, the coolant-to-hot mainstream pressure ratio varies from 1.02 to 1.10, and the corresponding velocity ratio (blowing ratio) ranges from 0.5 to 2.0. Further, the coolant-to-hot mainstream temperature ratio varies from
0.5 to 0.85, and the corresponding density ratio ranges from
2.0 to 1.5 [5]. For any given angle and hole shape, the effectiveness increases with increase in blowing ratio, however, beyond the critical blowing ratio the effectiveness declines [13]. The reduction in effectiveness is due to film lift-off from the boundary layer wherein the film cooling jet fails to attach to the surface [14].
-
Effect of Film Hole Shape and Geometry
Reference [11] shows that various parameters like film hole diameter (D), film hole length-to-diameter (L/D) ratio, film hole angle to the surface tangent, film hole orientation to the external flow, film hole orientation to the internal flow, film hole pitch-to-diameter (P/D) ratio and film hole exit shape affects the performance of the film cooling. For increased effectiveness and performance, the nominal hole diameter is desired to be around 1mm, and the ratio of hole length to diameter is desired to be minimum 5. To achieve effective film cooling, the angle to the surface tangent is typically 30º, and the orientation of film hole to internal flows is around is 45º. It is seen from the literature that, the best cooling coverage is achieved when the coolant is injected parallel to the mainstream gas flow. However, due to manufacturing constraints, the holes are at an angle to the mainstream gas flow. Injection of coolant at 90º results in very low film cooling effectiveness hence to balance out the film performance and manufacturing challenges, the holes are angled at 35º [18]. The shape of film cooling hole influences the performance of film cooling. The exit hole shape may be a cylindrical or a fan-shaped diffuser. Experiments indicate that the fan-shaped diffuser hole improves the film cooling performance when compared to other shapes due to lateral spreading of the jet, which results to better film cooling coverage.
-
Effect of Multiple Rows, Unsteady Wakes and Secondary Flows
Multiple film cooling rows are conventionally used in a gas turbine. It was found that, at lower blowing ratios (<0.5), the effect of number of rows had very less influence on the effectiveness. However, beyond blowing ratio of 0.5, the effectiveness was found to increase [20]. Two rows of film cooling holes with opposite orientation and internal supply geometry showed higher film cooling effectiveness due to the cancellation of counter-rotating Kidney vortices, produced due to the interaction of jet with mainstream [21]. Multi-hole film cooling (uniform array of holes) is desired where very high effectiveness (>0.6) is required.
-
End Wall, Blade Tip, and Trailing Edge Film Cooling The blade tip experiences very high heat loads and complex flow patterns due leakage flows between the pressure and
suction surfaces. It is evident from experiments that, high blowing ratio and small tip clearances result to better film cooling effectiveness [25]. Film cooling protects the tip from adverse conditions by forming an insulating layer over the tip which in-turn reduces the leakages between the pressure and suction surfaces. Ejection of coolant into the mainstream flow causes a net loss in the overall turbine performance. This is because of entropy generation due to mixing and availability of coolant for a lower time to cool the internal surface of the trailing edge [26].
-
Effect of Rotation on Film Cooling
Reference [27] shows the effects of rotation on film cooling effectiveness. The results showed that, the effectiveness on the pressure surface with rotation was lower than the non- rotating case, however, the effectiveness on the suction surface was the same for rotating and non-rotating case. The film cooling effectiveness reduced in the pressure surface due to deflection of the film cooling jet by the centrifugal force.
-
Effect of Thermal Barrier Coating Spallation
The thermal barrier coatings are applied to the external surfaces of the turbine blades to protect the metal surfaces from harsh operating conditions. TBC insulates the airfoil from impinging hot gases resulting to higher TIT and in-turn higher efficiency. TBC is coated on the airfoil surface using coating techniques namely air plasma spray, chemical vapor deposition and physical vapor deposition. The coatings are generally zirconia based ceramics and the performance of the same depends on the coating technique and the nominal thickness which varies between 0.45 to 0.55 mm [11]. Prolonged exposure to high temperature and high velocity combusted gases leads to peeling of TBC from the blade surface which is termed as spallation. The spallation can occur at random location on the blade surface and can be of different size and shape. The presence of spallation enhances the local heat transfer coefficients up to 2 times the values measured on a smooth surface [28]. Due to spallation, the bare metal surface of the blade is continuously exposed to hot gases which accelerate deterioration resulting in reduced service life of the blade [29].
-
-
RIB TURBULATED COOLING
Gas turbine blade are internally cooled by one or more of these technique namely impingement cooling, rib turbulated cooling and pin-fin cooling. Impingement cooling is applied to the leading edge of the blade where the cooling rate requirements are very high. The middle section or the mid- chord of the blade is cooled by rib turbulators which are cast on to the opposite walls of the internal serpentine passages and the trailing edge is cooled by pin-fins. In advanced gas turbines, the ribs or the turbulence promoters are cast on two opposite walls of internal cooling passages to enhance heat transfer. The narrow serpentine chnnels are connected to each other by a 180º bend. The various rib shapes used in the internal cooling passages to generate heat transfer enhancement are illustrated in figure 4 [30].
Figure 4: Various rib shapes used in rib turbulated flow [30].
The flow pattern over the ribs is characterized by separation of boundary layer upstream and downstream of the ribs. Several studies have shown another separation region on top of the rib. At the point of reattachment, the boundary layer is very thin and hence the heat transfer enhancement is very high. The performance of a stationary ribbed channel primarily depends upon the channel aspect ratio, rib configuration, and Reynolds number. The rib configuration includes the type of rib, rib pitch-to-height ratio (P/e), rib height-to-hydraulic diameter of the channel (e/Dh), rib spacing and the number of ribbed walls. Typically, the P/e values vary between 5 to 15, the e/Dh values, also called as the blockage ratio varies between 5 to 10% and the rib flow attack angle varies between 30-60° [2].
-
Rib Induced Secondary Flows
Rib turbulators, also known as trip strips are often in the form of rectangular cross-sectional bars cast along the cooling channel surface. They are either placed perpendicular or at an angle to the bulk fluid flow. Since they protrude into the flow, they alter the flow characteristics, generate vortices and three-dimensional velocity gradients [31]. The unsteady secondary flows and vortices generated by the ribs increase the secondary advection and turbulent transport over the entire crosssection. The secondary flow vortices induced by angled and V-shaped ribs are illustrated in figure 5 [2].
Figure 5: Rib induced Secondary flow for Angled and V-shaped ribs [2].
The angled ribs induce secondary flows which move parallel to the ribs from the inner (bottom) surface to the outer (top) surface. The ribs are generally angled at 30º or 45º or 60º to the fluid flow. The fluid moves along the rib from the inner to the outer surface and then returns to the inner surface along the center line of the inclined cross-stream plane. The temperature distribution in the stream-wise direction is dependent on the flow separation and re-attachment of the secondary flows induced by the ribs. Due to flow separation at the rib, the wall temperatures immediately downstream of the rib are high however, the wall temperatures are low between the ribs due to reattachment of the coolant. Unlike angled ribs where the rib induced secondary flow pattern moves the coolant from one side of the channel to the other side along the ribbed surface, the secondary flow patterns generated by the V-shaped ribs direct the coolant from the center of the channel towards the side walls along the ribbed surface. When compared to the angled rib, the secondary flow induced by the V-shaped rib travels a shorter distance before impinging on the side walls. The pair of vortices induced by each V-shaped rib is stronger than the vortex induced by the angled rib. It is seen that the wall temperatures in the V-shaped ribbed channel are significantly lower and more uniform in the core region which results in an increase of overall heat transfer enhancement in comparison with the angled ribs for the same AR channels.
-
Rotation Induced Secondary Flows
Rotation induces two types of forces namely Coriolis force and centrifugal buoyancy force both of which can alter the flow and temperature profiles in the serpentine passages [32]. In a two-pass channel, the effects of rotation induced secondary flows are different for both the passes. The rotational effects developed in the first and second pass of the channel are illustrated in figure 6 [2].
Figure 6: Coolant flow through two-pass rotating channel [2].
For radially outward flow in the first pass, the core flow is shifted towards the trailing wall by the Coriolis force. In the second pass where the fluid flow is radially inwards, the
Coriolis force pushes the coolant towards the leading wall, however, the centrifugal buoyancy force effects on the heated coolant are slightly low in the second pass. Overall, the rotation enhances the heat transfer in the first pass trailing wall for radially outward flow and the second pass leading wall for radially inward flow. In general, it is seen that the rotational effects on the heat transfer enhancement is dominant in the first pass when compared to the second pass [33].
-
Bend Induced Secondary Flow
As the cooling air flows through the 180º bend, pair of symmetric counter rotating vortices are formed due to the bend and the pressure gradients between the inner and outer surface. The strength of the secondary flow in the bend region depends on the bend geometry and AR. For large turning radius, the flow remains attached downstream of the bend, however, separation of the flow is observed for sharp bends. For square and wide AR channels, the counter-rotating vortices generated by the bend expand in the horizontal direction due to the limited spacing between the leading and trailing surfaces [34]. For 1:1 and 1:2 AR channels, the counter-rotating vortices occupy the entire channel and carry the cooler fluid in the core region towards the outer surface.
-
Effect of Channel Aspect Ratio and Varying Ribbed Wall
Reference [37] shows the effects of heat transfer and pressure drop characteristics for five different AR channels (1:4, 1:2, 1:1, 2:1, and 4:1) with different rib angles. Results indicate that, the heat transfer augmentations for the ribbed walls do not vary significantly, however, pressure drop penalties increase significantly for the wide AR channels (2:1 and 4:1) when compared to the narrow AR channels (1:4 and 1:2) due to more interaction of rib induced secondary flows. The thermal performance with angled ribs are higher in the narrow AR channel, however, in the wide AR channel, since the ribbed walls are very close to each other, the secondary flow vortices cancel each other leading to a lower thermal performance. The pressure drop penalties for 30º, 45º, and 60º ribbed channels increased from 2 times to 18 times as the AR of the channels varied from narrow (1:4) to wide (4:1). In general, the thermal performance of the narrow AR channels is higher than the wide AR channels view high pressure drops experienced in the wide AR channels.
In a rectangular channel, the heat transfer is improved with the increase in the number of ribbed walls. The heat transfer enhancement is increased by 20-30% with an increase in the number of ribbed walls from one to four and the enhancement increased by 5-10% with an increase in the number of ribbed walls from one to two [38].
The location of different AR channels in an airfoil is shown in figure 7 [2].
Figure 7: Schematic of blade airfoil with different AR internal cooling channels [2].
Reference [40] shows the effects of rotation on heat transfer in a multi-pass square cross-section channel with 45º angled ribs. The results indicated that the rotation, in general, did not produce a significant effect on the ribbed channels as the heat transfer enhancements in a non-rotating ribbed duct were already 3-3.5 times higher than the smooth wall enhancements. Rotational effects were pronounced only at low Reynolds number (10000-25000). At high Reynolds number, the heat transfer enhancements were influenced more by the rib induced secondary flows than the rotation induced secondary flows.
Experiments conducted on a rotating two-pass rectangular channel with AR 2:1, 45° angled and V-shaped ribbed walls indicate that the rotational effects are very similar to the square channel except that the leading wall heat transfer coefficient does not vary much with rotation when compared with square channel [41].
For a cooling channel with a triangular cross-section, the heat transfer coefficients were observed to be similar to a square cross-section in the radially outward flow first pass, however, for the second pass where the flow was radially inward, the heat transfer coefficients on the leading wall were up to 120% higher than the corresponding square channel. The increase in heat transfer coefficients was due to the additional mixing and secondary flows generated by the 180º turn of the triangular channel geometry [44].
The heat transfer distribution in the stream-wise direction is dependent on the channel orientation with respect to the plane of rotation. The rotational effects in a ribbed square channel oriented at 45º were less in comparison to the effects in a ribbed square channel oriented at 0°. Due to the reduced rotational effects, the difference in heat transfer enhancements between the trailing and leading walls reduced [40]. For a narrow AR ribbed channel oriented at 135º to the plane of rotation, the heat transfer enhancement was observed on the leading and trailing walls, which is different from the ribbed square channels [30].
-
-
PIN FIN COOLING
The pin-fin cooling arrangement in the trailing edge of airfoil is illustrated in figure 8 [47]. The narrow cross-section at the trailing edge imposes a great challenge to design a reliable and durable cooling technique. Due to space constraints, a limitation exists in employing rib-turbulated cooling and
impingement cooling in the trailing edge, hence pin-fin cooling is considered to be the most appropriate cooling technique in this region. Further, at the trailing edge, the structural integrity of the thin airfoil is very critical which is managed by casting dense pin-fin arrays between the suction and pressure surfaces [48]. The dense arrangement of pin-fins resulted in increased surface area for enhanced heat transfer and also ensured adequate coolant pressure throughout the serpentine passages by providing necessary restriction. The heat transfer enhancement with pin-fins depends on various geometric and flow parameters. The parameters are pin-fin shape, pin-fin height, configuration, stream-wise and span- wise pin-fin spacing and Reynolds number [31].
Figure 8: Schematic of trailing edge pin-fin cooling [47].
5.1 Effects of Pin-fin shape and Orientation
The pin-fins are usually cylindrical, circular, cubical, diamond, pyramidal or hemispherical in shape [49]. As the fluid flows around a pin-fin, just upstream of the base of the pin-fin, horse-shoe vortex is formed and the vortex wraps around the pin. The secondary flows within and around the vortex are intense resulting in enhanced heat transfer [6].
The diamond and cubic shaped pin-fins display superior heat transfer enhancement than circular pin-fin due to strong vortices generated by the sharp edges. The sharp edges result in high-pressure drops (10 to 40%) in comparison to circular pin-fins [50]. Due to the reduced weight of semi-circular and triangular pin-fins, the overall efficiency of the turbine system increases in comparison to the system employing cubic and diamond-shaped pin-fins [51]. Partial shaped pin- fins resulted in reduced pressure drops thereby enhancing heat transfer performance.
The pin-fin arrays are either in-line or staggered. The pin-fin height-to-diameter ratio ranges from 0.5 to 4 and nominal spacing between the pin-fins is typically 2.5 times the diameter of the pin-fin. Pin-fins inclined at ±45º to the flow generate higher heat transfer enhancements due to increase in overall surface area by 1.4 times [52]. Reference [53] shows that for Reynolds number between 10000-25000, the averaged heat transfer in a triangular pin-fin array increased by 4-5 times. However, the pressure drop was 10-15% higher than the circular pin-fin array.
Heat transfer enhancements with pin-fins are influenced by rotation. In stationary condition, the heat transfer enhancement with pin-fins was 3-4 times to that of a smooth
channel, however, with rotation the enhancement was reduced to 1.5 times to that of a smooth channel [55].
-
JET IMPINGEMENT COOLING
Jet impingement is an aggressive cooling technique which is employed where the thermal load is the highest. The impingement cooling is best suited for the leading edge which by design is thick in cross-section. The primary factors that are required to be optimized to achieve effective cooling are the jet hole size and distribution, the cross-section of the cooling channel, target surface shape, jet-to-target spacing, spent air cross flow and jet center-to-center spacing. In a typical gas turbine, the nominal jet hole size is about 0.75 mm with a variation of ± 10%, the center-to-center spacing nominal values are about 6 with a tolerance of ± 10% and the jet-to-target spacing nominal values are about 2.5 with a variation of ± 10% [57].
Figure 9: Schematic representation of impinging jets on airfoil surfaces [56].
-
Single Jet Impingement Cooling
At the impingement location, the convection effects are negligible because of zero velocity of the jet (stagnation point). The boundary layer develops around the stagnation region. The developing boundary layer is thin and highly turbulent around the impingement region which results to heat transfer enhancement.
Also, a smaller gap between the jet and the target surface significantly improves the cooling effectiveness for a single jet [9].
-
Multiple Jet Impingement Cooling
The performance of multiple jets is different from single jet striking the surface [58]. For multiple jet impingement cooling, the Nusselt number is fully dependent on the Reynolds number and not on the jet-to-target plate spacing. The cross-flows induced by the multiple jets strongly influence the heat transfer at the leading surface. Strong cross-flows and sufficiently large jet-to-target plate spacing resulted in decreased heat transfer enhancement due to deflection of the jet away from the impingement surface.
-
Jet Impingement on Curved Surface
The heat transfer coefficients on the curved surface due to jet impingement differed from that of a flat surface. The average Nusselt number increases with increase in curvature of the
target plate [60]. Further, the target surface with sharp-nose radius results to uniform Nusselt number distribution in comparison to the smooth-nosed surface [61].
-
Effect of Rotation on Jet Impingement Cooling
Rotation influences the impingement heat transfer on a target surface. Due to the rotation, the jet is deflected away from the target surface resulting in reduced effectiveness. Effect of rotation is reduced up to 40% when the jet angle is at 45º to the direction of rotation. The rotational effects are highest when the jet angle is perpendicular to the direction of rotation.
enhanced the heat transfer in the trailing surface and reduced the heat transfer in the leading surface. Schematic of orientation and rotation induced vortices in a rectangular channel is shown in figure 11[65].
-
-
DIMPLE COOLING
Dimples are an array of indentations or depressions along surfaces. Most commonly they are spherical in shape however, various other dimple geometries employed are tear- drop, square, triangular, circular and V-shaped [64]. The thermal performance of dimpled cooling depends on the dimple size, shape, channel height-to-dimple diameter ratio, dimple channel orientation, inter dimple spacing and dimple depth-to-diameter ratio. Dimple cooling is considered a good alternative to other cooling methods at locations when the coolant pressure is low. Dimples are produced by removal of material from the surface which results in the reduction in blade weight thereby resulting in a higher power to weight ratio [1]. Schematic of secondary flow patterns over a dimpled surface is as shown in figure 10 [65].
Figure 10: Schematic of fluid flow over a Dimpled surface [65].
Fluid flow over a dimpled surface is characterized by shredding of multiple vortex pairs followed by re-attachment downstream of the dimple. The strong secondary fluid motions within these vortex pairs are associated with vortical fluid motions resulting to local heat transfer augmentations [66].
Typically, the heat transfer enhancement in a spherical dimpled surface is 30-40% higher than that of a smooth surface with negligible pressure drop [67]. Increase in relative dimple depth resulted in increased heat transfer rates and pressure drop penalties in the stream-wise direction [68]. The heat transfer enhancement in a dimpled surface is influenced by rotation. Reference [65] shows the heat transfer performance of a dimple array in a rotating rectangular channel (AR=4:1) with dimple array on both the leading and trailing surfaces. The results indicated that the rotation
Figure 11: Schematic of Orientation and Rotation induced vortices in a Rectangular channel [65].
-
TURBINE BLADE TIP HEAT TRANSFER
Gas turbine blades by design have a clearance gap between the tip of the blade and the shroud (stationary casing) to cater for thermal expansion. While it is important to ensure reasonably small clearance gap, the gap is required to be optimized to avoid the reduction in overall efficiency and failure of the turbine blade due to tip leakage flow.
The blade tip by design is extremely difficult to cool. The pressure difference between the airfoil surfaces results in leakage flow which is considered undesirable due to increase in thermal loads on the blade tip and reduction of the work done due to the generation of secondary flow. Increase in tip gap clearance further increases the leakage flow thereby accelerating the blade tip failure. In modern gas turbines, the recessed tip with squealer sealing rim is utilized to reduce the leakage flow thereby ensuring better thermodynamic performance [69]. The tip clearance gap and the leakage flow between the pressure and the suction surfaces are illustrated in figure 12 [70].
Figure 12: Schematic of tip gap clearance and leakage flows [70].
The effectiveness of the tip film cooling depends on the coolant-to-hot mainstream velocity ratio (blowing ratio), temperature ratio, coolant hole location, hole configuration (hole size, spacing, number and angle), hole distribution (leading edge, trailing edge, pressure side, suction side, end- wall and tip), Reynolds number, Mach number, un-steadiness and free-stream turbulence [70]. Higher blowing ratio enhances the cooling performance, however, blowing ratio beyond the critical value results to jet lift-off which in-turn reduces the effectiveness. Lower blowing ratio leads to inadequate cooling performance due to the insufficient velocity of the coolant to penetrate the mainstream. Also, rotation decreased the plane tip film cooling effectiveness. However, the rotational effect on squealer tip was minimal due to large cavity depth.
-
COMPOUND COOLING TECHNIQUES
In order to achieve maximum cooling effectiveness, both the internal and external cooling techniques in various forms are employed together. It is important to combine the cooling features appropriately for ensuring optimized thermal performance.
The presence of multiple cooling features involving pin-fins, rib turbulators, and dimples within the channel results in an increased surface area which in-turn enhances the heat transfer with a marginal increase in pressure loss. Pin-fin and dimple combination exhibits superior heat transfer performance in comparison to an only pin-fin array. In addition to heat transfer enhancement, the pin-fin and dimple combination produced 25% lower pressure loss since the presence of dimples did not induce flow resistance [77]. In comparison to a pin-fin array, the combination of detached pin-fin and rib-turbulator enhanced the local heat transfer coefficient near the end wall significantly by 20% to 50% with negligible pressure loss [78]. Impingement effect on a dimpled (depression) and pinned (protrusion) surface showed that, the pinned surface performed better for low Reynolds number, and for high Reynolds number, the dimpled surface performed better. Also, significant heat transfer enhancement was observed on a curved surface roughened with conical bumps [80]. The screw-shaped swirl significantly improved the heat transfer coefficients and the same is not dependent on the temperature ratio and rotational forces [81].
-
CONCLUSION
Gas turbine airfoils are required to be effectively and optimally cooled to achieve higher thermal efficiency and power output. The thermal performance of various cooling techniques has been discussed in the literature. It is seen from the literature that, the heat transfer data for different internal cooling techniques have been generated by performing experiments in stationary channels with different cooling features and Reynolds number ranging from 10000-60000. In actual conditions, due to the high RPMs, the coolant flow inside the channel is influenced by the rotational effects, and therefore the heat transfer enhancements on the external and internal surfaces of an airfoil are different for stationary and rotating conditions. To generate realistic heat transfer data, more experiments are required to be performed at high Rotation numbers and Reynolds numbers (> 100000).
Further, the experimental data available in the literature are mainly for single or two pass channels with rectangular or square cross-sections. Since the internal serpentine passages are of different shapes, there is a need to study the performance of trapezoidal or triangular cross-sectional channels with more than three passes.
Also, it is seen that the data primarily available in the literature are for the main airfoil external and internal surfaces however, there is a need to study the flow and temperature patterns to generate local heat transfer data at the trailing edge, blade end wall and tip regions to eliminate hot spots for ensuring durable and reliable operation of the engines at higher TIT. Prediction of local heat transfer data rather than averaged data is the key for the successful design of rotor blades. More experimental data are required to be generated for blade-shaped channels with or without film cooling holes under realistic flow and thermal conditions. Further, the experimental results have been generated with reasonably acceptable assumptions and constraints which may differ from real-time applications. Therefore multi- disciplinary issues such as aerodynamic losses, frictional losses, airfoil shape, channel shape, channel orientation to the plane of rotation and manufacturing limitation need to be evaluated thoroughly prior making assumptions.
Sufficient data is available in the literature to comprehend the performance of traditional cooling techniques namely impingement cooling, film cooling, rib turbulated cooling and pin-fin cooling. More studies are required to be undertaken with compound cooling features under stationary and rotating conditions. Due to inherent constraints and challenges associated with the manufacturing of prototype channels for performing experiments, efficient CFD tools should be effectively utilized for validation of experimental data and also generate local data for actual airfoil profiles and blade- shaped channels under realistic operating conditions.
Abbreviations TIT Turbine Inlet Temperature TBC Thermal Barrier Coatings EDM Electro Discharge Machining AR Aspect Ratio
RPM Revolutions Per Minute
Nomenclature
P Pitch (m)
e Rib height (m)
d Film hole diameter (m)
Dh Hydraulic diameter of the channel (m)
Angular velocity of the channel (rad/sec)
v Stream-wise velocity of the coolant (m/sec)
REFERENCES
-
Chyu, Minking K., and Sin Chien Siw. 2013. Recent Advances of Internal Cooling Techniques for Gas Turbine Airfoils. Journal of Thermal Science and Engineering Applications 5 (2): 021008. https://doi.org/10.1115/1.4023829.
-
Han, Je-Chin, and Hamn-Ching Chen. 2006. Turbine Blade Internal Cooling Passages with Rib Turbulators. Journal of Propulsion and Power 22 (2): 22648. https://doi.org/10.514/1.12793.
-
Han, Je-Chin, and Lesely M. Wright. 2006. 4.2.2.2 Enhanced Internal Cooling of Turbine Blades and Vanes. NETL The Gas Turbine Handbook, 32152.
https://www.netl.doe.gov/File/Library/Research/Coal/energy/system s/turbines/handbook/ 4-2-2-2.pdf.
-
Nealy, D. A., M. S. Mihelc, L. D. Hylton, and H. J. Gladden. 1983. Measurements of Heat Transfer Distribution over the Surfaces of Highly Loaded Turbine Nozzle Guide Vanes. Journal of Engineering for Gas Turbines and Power 106 (January 1984): 149 58. https://doi.org/10.1115/1.3239528.
-
Han, Je-Chin. 2013. Fundamental Gas Turbine Heat Transfer. Journal of Thermal Science and Engineering Applications 5 (2): 021007. https://doi.org/10.1115/1.4023826.
-
Gupta, S., A. Chaube, and P. Verma. 2012. Review on Heat Transfer Augmentation Techniques: Application in Gas Turbine Blade Internal Cooling. Journal of Engineering Science and Technology Review 5 (1): 5762.
-
Ligrani, P. M., M. M. Oliveira, and T. Blaskovich. 2003. Comparison of Heat Transfer Augmentation Techniques. AIAA Journal 41 (3): 33762. https://doi.org/10.2514/2.1964.
-
Gardon C.O. Aerothermodynamics of Aircraft Engine Components, AIAA Education Series, 1995, pp.273-328. https://doi.org/10.2514/4.861338.
-
Han, Je-Chin., Dutta, S., and Ekkad, Srinath V. Gas turbine heat transfer and cooling technology, CRC Press, 2012.
-
Han, Je-Chin, and Michael Huh.Recent studies in turbine blade internal cooling, Heat Transfer Research, Vol.41(8), 2010.
DOI: 10.1615/HeatTransRes.v41.i8.30
-
Bunker, Ronald S. 2008. The Effects of Manufacturing Tolerances on Gas Turbine Cooling. Volume 4: Heat Transfer, Parts A and B 131 (October 2009): 8196. https://doi.org/10.1115/GT2008-50124.
-
Bunker, Ronald S. 2000. Effect of Partial Coating Blockage on Film Cooling Effectiveness, no. C: 17.
https://doi.org/10.1115/2000-GT-0244.
-
Goldstein, R. J., E. R G Eckert, and F. Burggraf. 1974. Effects of Hole Geometry and Density on Three-Dimensional Film Cooling. International Journal of Heat and Mass Transfer 17 (5): 595607. https://doi.org/10.1016/0017-9310(74)90007-6.
-
Pedersen, D. R., E. R. G. Eckert, and R. J. Goldstein. 1977. Film Cooling With Large Density Differences Between the Mainstream and the Secondary Fluid Measured by the Heat-Mass Transfer Analogy. Journal of Heat Transfer 99 (4): 620. https://doi.org/10.1115/1.3450752.
-
S. Ito, R. J. Goldstein, E. R.G. Eckert, Film Cooling of a Gas turbine Blade, Journal of Engineering for Power, Vol.100(3), 1978, pp.476-481.
-
Rodi, W. 1992. The Influence of Density Difference Between Hot and Coolant Gas on Film Cooling by a Row of Holes: Predictions and Experiments. Journal of Turbomachinery 114 (October 1992): 74755. https://doi.org/10.1115/1.2928028.
-
Ou, S., J.-C. Han, A. B. Mehendale, and C. P. Lee. 1994. Unsteady Wake Over a Linear Turbine Blade Cascade With Air and CO2 Film Injection: Part IEffect on Heat Transfer Coefficients. Journal of Turbomachinery 116 (4): 721. https://doi.org/10.1115/1.2929465.
-
Goldstein, R. J. 1971. Film Cooling. Advances in Heat Transfer, 32179. https://doi.org/10.1016/S0065-2717(08)70020-0.
-
Gritsch, M., Schulz, A., and Wittig, S. 2006. Adiabatic Wall Effectiveness Measurements of Film-Cooling Holes With Expanded Exits. Journal of. Turbomachinery 3 (98): 93138.
https://doi.org/10.1115/97-GT-164.
-
Ligrani, P. M., J. M. Wigle, and S. W. Jackson. 1994. Film-Cooling From Holes With Compound Angle Orientations: Part 2Results Downstream of a Single Row of Holes With 6d Spanwise Spacing. Journal of Heat Transfer 116 (2): 353. https://doi.org/10.1115/1.2911407.
-
Kusterer, Karsten, Dieter Bohn, Takao Sugimoto, and Ryozo Tanaka. 2006. Double-Jet Ejection of Cooling Air for Improved Film-Cooling. Volume 3: Heat Transfer, Parts A and B 2006 (October 2007): 67787. https://doi.org/10.1115/GT2006-90854.
-
Sauer, H., R. Muller, and K. Vogeler. 2001. Reduction of Secondary Flow Losses in Turbine Cascades by Leading Edge Modifications at the Endwall. Journal of Turbomachinery 123 (2): 207. https://doi.org/10.1115/1.1354142.
-
Ames, F E. 1998. Aspects of Vane Film Cooling With High Turbulence: Part I Heat Transfer. Journal of Turbomachinery 120 (October 1998): 76876. https://doi.org/10.1115/97-GT-240.
-
Langston, L. S. 1980. Crossflows in a Turbine Cascade Passage. Journal of Engineering for Power 102 (4): 866. https://doi.org/10.1115/1.3230352.
-
Kwak, Jae Su, Jaeyong Ahn, Je-Chin Han, C. Pang Lee, Ronald S. Bunker, Robert Boyle, and Raymond Gaugler. 2003. Heat Transfer Coefficients on the Squealer Tip and Near-Tip Regions of a Gas Turbine Blade With Single or Double Squealer. Journal of Turbomachinery 125 (4): 778. https://doi.org/10.1115/1.1626684.
-
J. Hartsel. "Prediction of Effects of Mass-Transfer Cooling on the Blade-Row Efficiency of Turbine Airfoils", 10th Aerospace Sciences Meeting, Aerospace Sciences Meetings, https://doi.org/10.2514/6.1972-11.
-
Takeishi, K, S Aoki, and T Sato. 1991. Film Cooling on a Gas Turbine Rotor Blade. ASME Paper 91-GT-279 114 (October 1992).
-
Ekkad, Srinath V. 1997. Detailed Heat Transfer Distributions on a Cylindrical Model with Simulated TBC Spallation, no. January.
-
Bons, J. P. 2010. A Review of Surface Roughness Effects in Gas Turbines. Journal of Turbomachinery 132 (2): 021004. https://doi.org/10.1115/1.3066315.
-
Lee, Eungsuk, Lesley M Wright, and Je-chin Han. 2017. GT2003- 38900, 110.
-
Ligrani, Phil. 2013. Heat Transfer Augmentation Technologies for Internal Cooling of Turbine Components of Gas Turbine Engines. International Journal of Rotating Machinery 2013. https://doi.org/10.1155/2013/275653.
-
Dutta, S., and J.C. Han. 1996. Local Heat Transfer in Rotating Smooth and Ribbed Two-Pass Square Channels with Three Channel Orientations. Journal of Heat Transfer 118 (3): 57884. https://doi.org/10.1115/1.2822671.
-
Johnson, B V, J H Wagner, G D Steuber, and F C Yeh. 1994. Heat Transfer in Rotating Serpentine Passages With Selected Model Orientations for Smooth or Skewed Trip Walls. Journal of Turbomachinery-Transactions of the ASME 116 (4): 73844. https://doi.org/10.1115/1.2929467.
-
Al-Qahtani, M., Y. J. Jang, H. C. Chen, and J. C. Han. 2002. Flow and Heat Transfer in Rotating Two-Pass Rectangular Channels (AR=2) by Reynolds Stress Turbulence Model. International Journal of Heat and Mass Transfer 45: 182338.
-
Su, Guoguang, Hamn Ching Chen, Je Chin Han, and James D. Heidmann. 2004. Computation of Flow and Heat Transfer in Rotating Two-Pass Rectangular Channels (AR = 1:1, 1:2, and 1:4) with Smooth Walls by a Reynolds Stress Turbulence Model. International Journal of Heat and Mass Transfer 47 (26): 566583. https://doi.org/10.1016/j.ijheatmasstransfer.2004.07.019.
-
Han, J C, Y M Zhang, and C P Lee. 1991. Augmented Heat Transfer in Square Channels With Parallel, Crossed, and V-Shaped Angled Ribs. Journal of Heat Transfer 113 (3): 59096. https://doi.org/10.1115/1.2910606.
-
Park, J. S., Je-chin Han, Y. Huang, and S. Ou. 1992. Heat Transfer Performance Comparisons of Five Different Rectangular Channels with Parallel Angled Ribs. International Journal of Heat and Mass Transfer 35 (11): 28912903. https://doi.org/10.1016/0017- 9310(92)90309-G.
-
Chandra, P. R., M. E. Niland, and J. C. Han. 1997. Turbulent Flow Heat Transfer and Friction in a Rectangular Channel With Varying Numbers of Ribbed Walls. Journal of Turbomachinery 119 (2): 374. https://doi.org/10.1115/1.2841121.
-
Wagner, J. H., B. V. Johnson, and F. C. Kopper. 1991. Heat Transfer in Rotating Serpentine Passages With Smooth Walls. Journal of Turbomachinery 13 (July 1991): 31230. https://doi.org/10.1115/1.2927879.
-
Wagner, J. H., B V. Johnson, R. a. Graziani, and F. C. Yeh. 1992. Heat Transfer in Rotating Serpentine Passages With Trips Normal to the Flow. Journal of Turbomachinery 114 (January 1994): 847 57. https://doi.org/10.1115/1.2928265.
-
Al-Hadhrami, Luai, Todd Griffith, and Je-Chin -C Han. 2003. Heat Transfer in Two-Pass Rotating Rectangular Channels (AR=2) with Five Different Orientations of 45 Deg V-Shaped Rib Turbulators. Journal of Heat Transfer 125 (2): 23242.
https://doi.org/10.1115/1.1561455.
-
Griffith, Todd S., Luai Al-Hadhrami, and Je-Chin Han. 2002. Heat Transfer in Rotating Rectangular Cooling Channels (AR=4) With Angled Ribs. Journal of Heat Transfer 124 (4): 617. https://doi.org/10.1115/1.1471525.
-
Kim, Kyung Min, Yun Young Kim, Dong Ho Rhee, and Hyung Hee Cho. 2004. An Investigation of Duct Aspect Ratio Effects on Heat/Mass Transfer in a Rotating Duct With 90° Ribs. Volume 3: Turbo Expo 2004, 48392. https://doi.org/10.1115/GT2004-53533.
-
Dutta, S., J.-C. Han, Y. Zhang, and C. P. Lee. 1996. Local Heat Transfer in a Rotating Two-Pass Triangular Duct With Smooth Walls. Journal of Turbomachinery 118 (3): 435. https://doi.org/10.1115/1.2836685.
-
Han, J -C, Y -M Zhang, and K Kalkuehler. 1993. Uneven Wall Temperature Effect on Local Heat Transfer in a Rotating Two-Pass Square Channel with Smooth Walls. Transactions – ASME: Journal of Heat Transfer 115 (4): 91220.
https://doi.org/10.1115/1.2911387.
-
Parsons, J.A., Je-Chin, H. and Yuming, Z., 1994. Wall heating effect on local heat transfer in a rotating two-pass square channel with 90° rib turbulators. International Journal of Heat and Mass Transfer, 37(9), pp.1411-1420.https://doi.org/10.1016/0017-9310(94)90187-2.
-
Ostanek, Jason K. 2013. Improving Pin-Fin Heat Transfer Predictions Using Artificial Neural Networks. Journal of Turbomachinery 136 (5): 051010. https://doi.org/10.1115/1.4025217.
-
Phillip M. Ligrani and Gazi I. Mahmood. "Variable Property Nusselt Numbers in a Channel with Pin Fins", Journal of Thermophysics and Heat Transfer, Vol. 17, No. 1 (2003), pp. 103- 111. https://doi.org/10.2514/2.6740
-
Chyu, M. K., and V. Natarajan. 1996. Heat Transfer on the Base Surface of Three-Dimensional Protruding Elements. International Journal of Heat and Mass Transfer 39 (14): 292535.
https://doi.org/10.1016/0017-9310(95)00381-9.
-
Chyu, M. K., C. H. Yen, and S. Siw. 2007. Comparison of Heat Transfer From Staggered Pin Fin Arrays With Circular, Cubic and Diamond Shaped Elements. Volume 4: Turbo Expo 2007, Parts A and B, 99199. https://doi.org/10.1115/GT2007-28306.
-
Siw, S., Chyu, M.K., and Alvin, M., 2012. Heat Transfer Enhancement of Internal Cooling Passage with Triangular and Semi- Circular Shaped Pin-Fin Arrays. ASME Paper No. GT2012- 69266.1-11
-
Takeishi, K, Y Oda, Y Miyake, and Y Motoda. 2012. Experimental and Numerical Study on the Convective Heat, 112.
-
Chang, S W, T Liou, and T Lee. 2012. Gt2012-6 Array At High Rotation Numbers, 110.
-
Cunha, F.J., Dahmer, M.T., and Chyu, M.K. Analysis of Airfoil Trailing Edge Heat Transfer and its Significance in Thermal- Mechanical Design and Durability, Journal of Turbomachinery128 (4): doi:10.1115/GT2005-68108.
-
Lesley M. Wright, Eungsuk Lee, and Je-Chin Han. "Effect of Rotation on Heat Transfer in Rectangular Channels with Pin- Fins", Journal of Thermophysics and Heat Transfer, Vol. 18, No. 2 (2004), pp. 263-272. https://doi.org/10.2514/1.4723.
-
Poitras, G. J., A. Babineau, G. Roy, and L. E. Brizzi. 2017. Aerodynamic and Heat Transfer Analysis of a Impinging Jet on a Concave Surface. International Journal of Thermal Sciences 114: 18495. https://doi.org/10.1016/j.ijthermalsci.2016.12.019.
-
Bailey, J C, and R S Bunker. 2002. GT-2002-30 of Dense and Sparse Extent, 110.
-
Metzger, D E, L W Florschuetz, D I Takeuchi, R D Behee, and R A Berry. 1979. Heat Transfer Characteristics for Inline and Staggered Arrays of Circular Jets with Crossflow of Spent Air. Journal of Heat Transfer 101 (August 1979): 52631.
https://doi.org/10.1115/1.3244224.
-
Florschuetz, L. W., and C. C. Su. 1987. Effect of Crossflow Temperature on Heat Transfer within an Array of Impinging Jets. Journal of Heat Transfer 109 (February 1987): 7482.
-
Mcfadden, Peter W, and Tony R Brown. 1969. Evaluation of Internal Heat-Transfer Coefficients for Impingement-Cooled Turbine Airfoils. Journal of Aircraft 6 (3): 2038. https://doi.org/10.2514/3.44036.
-
Metzger, D. E., and R. S. Bunker. 1990. Local Heat Transfer in Internally Cooled Turbine Airfoil Leading. Journal of Turbomachinery 112 (July 1990): 45966.
https://doi.org/10.1115/1.2927681.
-
Epstein, A.H., Kerrebrock, J.L., Koo, J.J. and Preiser, U.Z., 1987. Rotational effects on impingement cooling. In Heat Transfer and Fluid Flow in Rotating Machinery (pp. 86-102).
-
Parsons, James A., and Je Chin Han. 2001. Rotation Effect on Jet Impingement Heat Transfer in Smooth Rectangular Channels with Film Coolant Extraction. International Journal of Rotating Machinery 7 (2): 87103.
https://doi.org/10.1155/S1023621X01000082.
-
Zhou, Fuguo, and Sumanta Acharya. 2009. Experimental and Computational Study of Heat/Mass Transfer and Flow Structure for Four Dimple Shapes in a Square Internal Passage. Volume 3: Heat Transfer, Parts A and B 134 (November 2012): 93953.
https://doi.org/10.1115/GT2009-60240.
-
Griffith, Todd S., Luai Al-Hadhrami, and Je-Chin Han. 2002. Heat Transfer in Rotating Rectangular Cooling Channels (AR=4) With Dimples. Volume 3: Turbo Expo 2002, Parts A and B 125 (July 2003): 55160. https://doi.org/10.1115/GT2002-30220.
-
Mahmood, G I, M L Hill, D L Nelson, and P M Ligram. 2017. 2000-Gt- 230, no. C: 111.
-
Afanasyev, V. N., Ya P. Chudnovsky, A. I. Leontiev, and P. S. Roganov. 1993. Turbulent Flow Friction and Heat Transfer Characteristics for Spherical Cavities on a Flat Plate. Experimental Thermal and Fluid Science 7 (1): 18. https://doi.org/10.1016/0894- 1777(93)90075-T.
-
Gortyshov, Yu.F., Popov, I.A., Amirkhanov, R.D. and Gulitsky, K.E., 1998. Studies of Hydrodynamics and Heat Exchange in Channels With Various Types of Intensifiers. Heat Transfer, 6, pp.83-88.
-
Ronald S. Bunker. "Axial Turbine Blade Tips: Function, Design, and Durability", Journal of Propulsion and Power, Vol. 22,
No. 2 (2006), pp. 271-285. https://doi.org/10.2514/1.11818
-
Sunden, Bengt, and Gongnan Xie. 2010. Gas Turbine Blade Tip Heat Transfer and Cooling: A Literature Survey. Heat Transfer Engineering 31 (7): 52754.
https://doi.org/10.1080/01457630903425320.
-
Metzger, Performed B Y D E, Y W Kim, J P Downs, F Soechting, West Palm Beach, G D Steuber, S Tanrikut, and East Hartford. 1994. A Summary of the Cooled Turbine Blade Tip Heat Transfer and Film Effectiveness Investigations.
-
Huitao Yang, Hamn-Ching Chen, and Je-Chin Han. "Film-Cooling Prediction on Turbine Blade Tip with Various Film Hole Configurations", Journal of Thermophysics and Heat Transfer,
Vol. 20, No. 3(2006), pp. 558-568. https://doi.org/10.2514/1.18422
-
Mochizuki, S., Murata, A., Shibata, R. and Yang, W.J., 1999. Detailed Measurements of Local Heat Transfer Coefficients in Turbulent flow through Smooth and Rib Roughened Serpentine Passages with a 180° Sharp Bend. International Journal of Heat and Mass Transfer 42: 81423.
-
Ekkad, Srinath V., Gautam Pamula, and Manoj Shantiniketanam. 2000. Detailed Heat Transfer Measurements inside Straight and Tapered Two-Pass Channels with Rib Turbulators. Experimental Thermal and Fluid Science 22 (34): 15563.
https:/doi.org/10.1016/S0894-1777(00)00022-4.
-
Pamula, Gautam, Srinath V. Ekkad, and Sumanta Acharya. 2001. Influence of Crossflow-Induced Swirl and Impingement on Heat Transfer in a Two-Pass Channel Connected by Two Rows of Holes. Journal of Turbomachinery 123 (2): 281. https://doi.org/10.1115/1.1343467.
-
Iacovides, H, D C Jackson, G Kelemenis, B E Launder, and Y Yuan. 2001. Flow and Heat Transfer in a Rotating U-Bend with 45° Ribs.Pdf 22: 30814. https://doi.org/10.1016/S0142- 727X(01)00093-5.
-
Rao, Yu, Chaoyi Wan, and Shusheng Zang. 2016. Comparisons of flow friction and heat transfer performance in rectangular channels with pin fin-dimple, pin fin and dimple arrays. GT2010-22442.
-
Siw, Sin Chien, Minking K. Chyu, Tom I.-P. Shih, and Mary Anne Alvin. 2010. Effects of Pin Detached Space on Heat Transfer and From Pin Fin Arrays. Volume 4: Heat Transfer, Parts A and B 135 (March 2013): 491500. https://doi.org/10.1115/GT2010-23227.
-
Murata, A., Nishida, S., Saito, H., Iwamoto, K., Okita, Y. and Nakamata, C. 2011. Heat transfer enhancement due to combination of dimples, protrusions, and ribs in narrow internal passage of gas turbine blade. GT2011-45356,doi:10.1115/GT2011-45356.
-
Taslim, M. E., L. Setayeshgar, and S. D. Spring. 2001. An Experimental Evaluation of Advanced Leading Edge Impingement Cooling Concepts. Journal of Turbomachinery 123 (1): 147. https://doi.org/10.1115/1.1331537.
-
Glezer, B., H. K. Moon, J. Kerrebrock, J. Bons, and G. Guenette. 1998. Heat Transfer in a Rotating Radial Channel With Swirling Internal Flow. Volume 4: Heat Transfer; Electric Power; Industrial and Cogeneration, V004T09A055. https://doi.org/10.1115/98-GT- 214.