
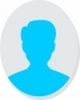
- Open Access
- Authors : Athulya Vijay N. , Saji K. P.
- Paper ID : IJERTV10IS070067
- Volume & Issue : Volume 10, Issue 07 (July 2021)
- Published (First Online): 13-07-2021
- ISSN (Online) : 2278-0181
- Publisher Name : IJERT
- License:
This work is licensed under a Creative Commons Attribution 4.0 International License
Experimental Investigations on the Performance of Particle Dampers Attached to A Multi Storey Frame Undergoing Horizontal Support Motion
Athulya Vijay N
Computer Aided Structural Engineering Government College of Engineering Kannur, Kannur, Kerala, India
Saji K. P
Computer Aided Structural Engineering Government College of Engineering Kannur, Kannur, Kerala, India
Abstract The main challenge faced by these high-rise building is the control of structural vibration during a seismic event. To ensure the safety and comfort of occupants several seismic protection systems are available. Particle damper is a new passive control method applied to civil engineering, structures and the technology is in a developing stage. Compared to other vibration control technologies, the installation process of particle damper is very easy. The inelastic collision of particles present in the damping cavity and friction between particles defines the effectiveness of particle damper. This study encompasses the experimental investigations on the performance of particle dampers attached to a multi-storey frame under varying parameters. The efficiency of particle dampers in mitigating seismic responses of vertically regular structure is studied in detail. The influence of various parameters such as variation in the type of particles, combination of particles, variations in the mass ratio of particles, were studied in detail using horizontal shake table apparatus. The response of the structure to seismic excitation in terms of story drift has been studied. The advantages of nature of different particle to control the seismic vibration are also included in this study. Results obtained from these studies were compared with the behaviour of a base frame without damper.
KeywordsParticle damper, Passive vibration control, Shake table, Damper cavity, Mass ratio
-
INTRODUCTION
The concept of particle damper, an innovative passive vibration control system, intended to reduce the vibration of multistorey framed structures under support motion is developing in the present stage. Particle damping technology is a form of an auxiliarymass type vibration damper. This type of damper consists of small particles, placed in the cavity of the primary structure which is likely to be subjected to vibration. Compared to other passive vibration control methods, particle damper can be effectively introduced into structure without significant modification of primary structure. Due to simplicity, moderate cost, better durability, and temperature insensitivity, importance of particle damper is drastically increasing in present stage.
The idea of particle damping is originated from the concept of impact damper which consists of a mass moving between the walls of the container. Masri S.F. et.al (1967) [1] conducted an analytical investigation of the steady-state motion of a two-particle, single-container impact damper which was attached to a sinusoidally excited primary system.
From 1985 onwards researchers are more focused on particle damper. Araki Y. et.al (1985) [2] studied the vibration reduction effect of impact damper consisting of a bed of granular materials moving in container fixed to primary vibrating system. Due to the impact, friction and shear mechanisms of multiple particles in particle damper, better damping performance can be achieved and it is effective in broad frequency range. Overall, it proves the efficiency of using in structural vibration control. [4, 5]
Based on development of particle damping technology, several studies were carried out in the division of configuration improved type, material improved type, and combination type of particle damper. Configuration improved particle dampers have wide range applicability and it can effectively control the vibrations in the structure [3, 6, 8]. And by combining the traditional method of particle damping with some predominant technologies, the damping performances can be improved [9, 10].
Several researchers compared the performance of particle damper over other types of passive dampers [7, 11, 12]. Their studies show that particle dampers are effective over types of dampers on various perspectives.
-
EXPERIMENT SETUP
-
Three Storied Aluminium Base Frame
The present study is mainly focused on the behavior of a three storied frame with particle damper. The frame is made of four Aluminum columns of total height of 1200mm with each floor having a height of 400mm. The aluminum column used is of cross section 25.4mm×3mm. The three storied frame used for the study is shown in Fig.1.
Fig.1. Three story frame
-
Particle Damper
Particle damper is a new passive control method applied to civil engineering. It consists of small particles placed in the cavity of the primary structure. Particles used in this study are metallic (steel balls), non-metallic (sand) and viscoelastic polymer (silicone rubber balls), as shown in Fig.2. Steel and silicone rubber ball of 8mm diameter is used for this study. The mass ratio used in this study is 2%, 3% and 5%. Damper cavity used for this study is made of acrylic plates, with dimension 300mm × 150mm × 100mm. And partitions are provided along the length with spacing of 100mm. Damper cavity with and without partitions are shown in Fig.3.
-
(b) (c)
Fig.2. a) Silicone rubber b) Steel, c) Sand
-
(b)
-
-
Fig.3 a) Damper cavity without partition,b) damper cavity with partitions
-
-
SHAKING TABLE TESTS
-
Base frame under horizontal excitation
The horizontal excitation given to the base of a three storied Aluminium frame was studied on the shake table. The experimental set up is as shown in fig.4.
Fig.4. Experimental setup
The displacement frequency data obtained were as shown in fig.5. From graph it is clear that maximum displacement occurred at the third floor and minimum occurred at first floor. The maximum displacement was 131.191mm for a frequency of 2.46094Hz. Hence the damped natural frequency of the base frame is taken as 2.46094Hz. Displacements at each floor level are measured. The input frequency is varied from zero to the first and second natural frequencies.
Fig.5. Frequency Displacement Graph of Base Frame
-
Base frame with steel particle damper
Shake table test was conducted on the same three storied Aluminium frame with steel particle damper. 8mm diameter steel particles were used for the study. Damper was placed in one of the storey levels respectively and the responses were taken with 2%, 3% and 5% mass ratios. The experimental setup with steel particle damper at top floor is shown in Fig.6.
Fig.6. Experimental setup with steel particle damper at top floor
Fig.7 represents the frequency displacement graph of particle damper at top storey level with mass ratio 2%, 3% and 5%. The maximum top storey displacement of base frame with particle damper with mass ratio 2%, 3% and 5% is reduced by 49.85%, 53.44%, and 63.4% respectively (in first mode of vibration) compared to base frame without damper.
Fig.7. Frequency Displacement Graph of top floor with steel particle damper
Interstorey drift ratio (IDR) is the ratio of the relative displacement of two consecutive floors to height of that floor. Fig.8 shows IDR v/s storey no. plot for base frame with and without steel particle damper. The maximum value of IDR for base frame without damper is 0.2075 at storey 1. Whereas the maximum value for base frames with damper is 0.1037 at 3% mass ratio at storey 1. The drift for frame with dampers is comparaively lower than the drift for base frame without damper, except in the case of 2% mass ratio at storey 2
Fig.8. IDR v/s Storey No. plot for base frame with and without steel particle damper
-
Base frame with sand particle damper
Experiment was repeated on the same frame with sand particle damper. sand particles were used for the study. Damper was placed in one of the storey levels and the responses were taken with 2%, 3% and 5% mass ratios respectively. Fig.9 represents the frequency displacement graph of particle damper at top storey level with mass ratio 2%, 3% and 5%. The maximum top storey displacement of base frame with particle damper with mass ratio 2%, 3% and 5% is reduced by 38.1%, 46.8% and 55.3% respectively (in first mode of vibration) compared to base frame without damper. And for sand particle damper the resonant frequency is found to increase
Fig.9. Frequency Displacement Graph of top floor with sand particle
damper
Fig.10 shows IDR v/s storey no. plot for base frame with and without particle damper. The maximum value for base frames with damper is 0.107325 at 3% mass ratio at storey 1. It is comparatively lower than the drift for base frame without damper.
Fig.10. IDR v/s storey no. plot for base frame with and without sand
particle damper
-
Base frame with silicone rubber particle damper
Experiment was repeated on the same frame with silicone rubber particle damper. 8mm diameter silicone particles were used for the study. Damper was placed in one of the storey levels respectively and the responses were taken with 2% and 3% mass ratios. Fig.11 represents the frequency displacement graph of particle damper at top storey level with mass ratio 2% and 3%. The maximum top storey displacement of base frame with particle damper with mass ratio 2% and 3% is reduced by, 41.1% and 45.48% (in first mode of vibration) compared to base frame without damper respectively. At 3% mass ratio, the frequency at which maximum displacement
occurs is increased; thereby the resonance condition is delayed.
Fig.11. Frequency Displacement Graph of top floor with silicone rubber
particle damper
Fig.12 shows IDR v/s storey no. plot for base frame with and without particle damper. The maximum value for base frames with damper is 0.101025 at 3% mass ratio at storey 1. It is comparatively lower than the drift for base frame without damper, except in the case of 2% and 3% mass ratio at storey 2.
Fig.12. IDR v/s storey plot for base frame with and without silicone rubber particle damper
-
Base frame with combination of particle
Experiment was repeated with combination of particles. A 50-50 combination of steel-silicone rubber, steel-sand and silicone rubber-sand were used. Damper was placed in top storey level and the responses were taken with 3% mass ratios. Fig.13 represents the frequency displacement graph of top floor with particle damper at top storey level with mass ratio 3%.
Fig.13. Frequency Displacement Graph of top floor with combination of
particle (mass ratio 3%)
When the steel-silicone rubber particle damper was placed at top storey level, the maximum top storey displacement is reduced by 45.8% (in first mode of vibration) compared to base frame without damper. And for steel-sand particle damper and silicone rubber-sand particle damper, the reduction is about 40.8% and 31.8% respectively with respect to base frame. From graph it is clear that maximum vibration reduction is for steel-silicone rubber combination at 3% mass ratio.
-
particle Base frame with multi-cell damper cavity
Shake table test was conducted on a three storied aluminium base frame by providing partitions in the damper cavity. Partitions were provided along the length with spacing of 100mm. Damper was placed in top storey level with steel particles, sand particles and silicone rubber particles and the responses were taken with 3% mass ratios. Particles in partitioned damper cavity are shown in fig. 14.
Fig.14. Particles in partitioned damper cavity
For steel particles in partitioned damper cavity, the maximum top storey displacement of base frame with particle damper at 3% mass ratio is reduced by 55.3% and the resonance frequency is increased to 2.56455 Hz (in first mode of vibration) compared to base frame without damper. In the case of steel particles, maximum vibration reduction is almost the same, for damper cavity with and without partitions at 3% mass ratio.
By providing partitions in the damper cavity, the maximum top storey displacement of base frame with silicone rubber particle damper at 3% mass ratio is reduced by 61.4% (in first mode of vibration) compared to base frame without damper. In the case of silicone rubber particles maximum vibration reduction is 29.1% more than for damper cavity with partitions compared to damper cavity without partition at 3% mass ratio.
By providing partitions in the damper cavity, the maximum top storey displacement of base frame with particle damper at 3% mass ratio is reduced by 51% (in first mode of vibration) compared to base frame without damper. In the case of sand particles, maximum vibration reduction is almost the same, for damper cavity with and without partitions at 3% mass ratio, the improvement being about 8%. Fig. 15 represents the frequency displacement graph of top floor with particle damper with and without partitions in the damper cavity with mass ratio 3%.
Fig.15a) Frequency Displacement Graph of top floor with steel particle damper with partitions in the damper cavity
Fig.15 b) Frequency Displacement Graph of top floor with silicone rubber particle damper with partitions in the damper cavity
Fig.15 c) Frequency Displacement Graph of top floor with sand particle damper with partitions in the damper cavity
-
-
CONCLUSIONS
This experimental investigation is intended to study the behaviour of particle damper with parameters varying. Parametric study investigates the efficiency of particle dampers in mitigating dynamic responses of MDOF structures, and the following conclusions can be drawn from this investigation.
-
From the results obtained, it has been found that particle damper with metallic particles, non-metallic particles and viscoelastic polymers can effectively control the vibration of MDOF structures.
-
For the vibration control technologies viscoelastic polymer particle damper is a better alternative compared to metallic particle damper.
-
As mass ratio increases the damping performance increases, but it may cause increasing the overall structural weight and there by affect the economy. In such situations viscoelastic polymer damper is more effective.
-
At 3% mass ratio Silicone rubber particle in partitioned damper cavity reduces the maximum top storey displacement by 61.4%, which is comparable to steel particle damper at 5% mass ratio.
-
For silicone rubber particle damper (at 3% mass ratio), partitioned steel particle damper (at 3% mass ratio) and sand particle damper (at 2%, 3% and 5% mass ratio), the frequency at which maximum displacement occurs is increased; thereby causing a delayed resonant condition, which is advantageous.
-
At 3% mass ratio, a 50-50 combination of steel- silicone rubber particle damper shows better vibration reduction. The maximum top storey displacement of base frame with steel-silicone rubber particle damper is reduced by 45.8% compared to base frame without damper.
-
The response of the structure to seismic excitation in terms of story drift has been studied. By providing particle damper the storey drift can be reduced significantly.
-
The given experimental set up allows the measurement of horizontal displacement of each floor by changing the frequency of support displacement. More insight could have been developed had there
REFERENCES
-
Masri, S. F. and Ibrahim, A.M. (1967) Response of the impact damper to stationary random Excitation Journal of the Acoustical Society of America V.53 PP. 200-211
-
Arki, Y., Yokomichi, I. and Inoue, J.(1985) Impact damper with granular materials The Japan Society of Mechanical Engineers V. 28(241) PP. 1466- 1471
-
Popplewell, N. and Semerc Gil, S. E. (1988) performance of the bean bag impact damper for a sinusoidal external force Journal of Sound and Vibration V. 133(2), PP. 193-223
-
Xu, Z., Yu, M. Wang and Chen, T. (2005) Particle damping for passive vibration suppression: numerical modelling and experimental investigation Journal of Sound and Vibration V. 279 PP. 10971120
-
Trigui, M., Foltete, E., Abbes, M. S., Fakhfakh, T., Bouhaddi, N. and Haddar, M. (2009) An experimental study of a multi-particle impact damper Mechanical Engineering Science, V. 223(9), PP. 2029.
-
Binoy, M.S. , Davy, P. , Bai, X. , Leon, M. K. , Wang, Q. J. and Snurr,
R. Q. (2009) Construction and characterization of a particle-based thrust damping system Journal of Sound and Vibration V. 326 PP. 489502
-
Lu, Z., Xilin Lu, Wensheng Lu and Sami, F. Masri (2012) Shaking table test of the effects of multi-unit particle dampers attached to an MDOF system under earthquake excitation Earthquake engineering and structural dynamics V. 41 PP. 9871000
-
Gharib, M. and Saud Ghani (2013 )Free vibration analysis of linear particle chain impact damper Journal of Sound and Vibration V. 332 PP. 62546264
-
Yan, W., Xu, W., Wang, J., and Chen, Y. (2014) Experimental Research on the Effects of a Tuned Particle Damper on a Viaduct System under Seismic Loads Journal of Bridge Engineering 04013004 PP. 1-10
-
Lu, Z., Chen, X. and Zhou, Y. (2017 ) An equivalent method for optimization of particle tuned mass damper based on experimental parametric study Journal of Sound and Vibration V.419, PP. 571-584
-
Lu, Z., Huang, B. Wang, Z. and Zhou, Y. (2018) Experimental Comparison of Dynamic Behavior of Structures with a Particle Damper and a Tuned Mass Damper Journal of structural Engineering,
V.144(12) PP. 04018211
-
Fu, B., Jiang, H. and Wu, T.(2019) Comparative studies of vibration control effects between structures with particle dampers and tuned liquid dampers using substructure shake table testing methods Soil Dynamics and Earthquake Engineering V.121 PP. 421435