
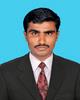
- Open Access
- Authors : Siva Kumar A , Ebinesh V , Sugumar E , Vijay A D
- Paper ID : IJERTV10IS030206
- Volume & Issue : Volume 10, Issue 03 (March 2021)
- Published (First Online): 30-03-2021
- ISSN (Online) : 2278-0181
- Publisher Name : IJERT
- License:
This work is licensed under a Creative Commons Attribution 4.0 International License
Experimental Investigation of Wheel Alignment Tool Using Laser Level Mini Beam Led Light
Mr. Siva Kumar A
Assistant Professor Department of Mechanical Engineering Loyola institute of technology, Chennai.
Mr. Ebinesh V
Final year student Department of Mechanical Engineering Loyola institute of technology, Chennai.
Mr. Sugumar E
Final year student Department of Mechanical Engineering Loyola institute of technology, Chennai.
Mr. Vijay A D
Final year student Department of Mechanical Engineering Loyola institute of technology, Chennai.
Abstract:- To ensure stability of the vehicle and reduce unnecessary wears on tyre, wheel alignment of the vehicle plays a major role and Misalignment of wheels can also lead to accidents .Using machines Wheel alignment of the vehicle
usually checked at the final stage before trial run or test tracks. Many companies developed and developing the wheel alignment tool with less cost and more effective. We are taking the projects to produce the wheel alignment tool with facility following less cost, user friendly, economical and with simple Design.
Keywords: Stability of the vehicle, unnecessary wear, misalignment.
INTRODUCTION:
Wheel alignment refers to adjusting wheels in a manner so that they are in line with the manufacturers specifications. This is important to ensure the two wheelers wheel balancing and make sure its travelling in a straight line. In this article, we will tell you how to check the alignment of the front and rear wheel of your bike. The purpose of these adjustments is to reduce tire wear and to ensure that vehicle travel in straight and true (without pulling to one side). Alignment angles can also be altered beyond the makers specifications to obtain a specific handling characteristic. Alignment assures your tires meet the road at the proper
angle, your wheels are pointing straight and your tires are centered in the wheel wells. It adjusts the angles of your vehicles wheels to original specs for best gas mileage, proper road contact, a smooth ride, and the longest tire life. It is advisable to check the alignment of your bike wheel
after few rides for a smooth experience. It is recommended to get the bike wheel alignment checked when you get new tires. After all, you are also going to drive it through some rough terrains. So, it is best to get the new wheels aligned. If not taken care of, misaligned tires can: – Cause tires to wear asymmetrically. – Disturb the handling of your bike. – Strange noises from the chains. Although it is recommended to maintain the bike wheel alignment. But if, in any case, they are unaligned, it can lead to a plethora of problems. – Misalignment of wheels can greatly affect the stability of your bike. – If there is a misalignment in the wheels of your bike, it can lead to uneven wearing out of tires. – Misalignment of wheels can also lead to accidents on the
road. Here we are designing the wheel alignment tool using the laser level mini led light in which our tool is low in cost and more effective.
The laser monkey is the wheel aligning tool, which is already existing. In which the point laser is using to find the misalignment. Whereas our tool consist of the line laser which shows us the accurate alignment of the wheel.
I. LITERATURE REVIEW
John Yurko, suggested that vital need to conserve the nation's resources, there is an increasing demand for vehicle fuel economy. One factor that may considerably affect fuel consumption is tire rolling resistance. This report analyzes the effect of toe-in and toe-out on rolling resistance, based on the road load results of an EPA test program. It also correlates these results with the results of slip angle vs. rolling resistance data, found in the existing literature. Then a survey of vehicle safety inspections is used to approximate the number of vehicles in a misaligned state, and finally an estimate of the effect on fuel economy is discussed.
LASER:
The term laser is an acronym for light amplification by stimulated emission of radiation. Lasers have the following properties:
-
Outstanding monochromaticity (the beam consists of light waves of a single unadulterated wavelength),
-
Outstanding directivity (the beam consists of parallel light waves that dont spread apart as they travel), and
-
High coherence (the beams light waves are all in phase
The term laser is an acronym for light amplification by stimulated emission of radiation. Lasers have the following properties:
-
Outstanding monochromaticity (the beam consists of light waves of a single unadulterated wavelength),
-
Outstanding directivity (the beam consists of parallel light waves that dont spread apart as they travel), and
-
High coherence (the beams light waves are all in phase
with one another).
Lasers emit beams of light with high directivity, which means that the component light waves travel together in a straight line with almost no spreading apart. Ordinary light sources emit light waves that spread apart in all directions. The light waves in a laser beam are all the same color (a property known as monochromaticity). Ordinary light (such as the light from a fluorescent bulb) is generally a mixture of several colors that combine and appear white as a result.
Lasers emit beams of light with high directivity, which means that the component light waves travel together in a straight line with almost no spreading apart. Ordinary light sources emit light waves that spread apart in all directions. The light waves in a laser beam are all the same color (a property known as monochromaticity). Ordinary light (such as the light from a fluorescent bulb) is generally a mixture of several colors that combine and appear white as a result.
As the light waves in a laser beam travel, they oscillate with their peaks and troughs in perfect synchronization, a characteristic known as coherence. When two laser beams are superimposed on each other, the peaks and troughs of the light waves in each beam neatly reinforce each other to generate an interference pattern.
The following chart lists the various classifications of lasers according to class and also the precautions that users should be aware of when operating each type.
As the light waves in a laser beam travel, they oscillate with their peaks and troughs in perfect synchronization, a characteristic known as coherence. When two laser beams are superimposed on each other, the peaks and troughs of the light waves in each beam neatly reinforce each other to generate an interference pattern.
The following chart lists the various classifications of lasers according to class and also the precautions that users should be aware of when operating each type.
IEC standard |
|||
Laser class |
Class Definition |
||
Class 1 |
Lasers that are safe under reasonably foreseeable conditions of operation, including the use of optical instruments for intrabeam viewing. |
||
Class 1M |
Lasers emitting in the wavelength range from 302.5nm to 4,000nm which are safe under reasonably foreseeable conditions of operation, but may be hazardous if the user employs optics within the beam. |
||
Class 2 |
Lasers that emit visible radation in the wavelength range from 400nm to 700nm where eye protection is normally afforded by aversion responses, including the blink reflex. This reaction may be expected to provide adequate protection under reasonably foreseeable conditions of operation including the use of optical instruments for intrabeam viewing. |
||
Class 2M |
Lasers that emit visible radiation in the wavelength range from 400nm to 700nm where eye protection is normally afforded by aversion responses including the blink reflex. However, viewing of the output may be more hazardous if the user employs optics within the beam. |
||
Class 3R |
Lasers that emit in the wavelength range from 302.5nm to 106nm where direct intrabeam viewing is potentially hazardous but the risk is lower than for Class 3B lasers, and fewer manufacturing requirements and control measures for the user apply than for Class 3B lasers. The accessible emission limit is within five times the AEL of Class 2 in the wavelength range from 400nm to 700nm and within five times the AEL of Class 1 for other wavelengths. |
||
Class 3B |
Lasers that are normally hazardous when direct intrabeam exposure occurs. (i.e. within the NOHD). Viewing diffuse reflections is normally safe. |
||
Class 4 |
Lasers that are also capable of producing hazardous diffuse reflections. They may cause skin injuries and could also constitute a fire hazard. Their use requires extreme caution. |
||
The CO2 laser marker (ML-G Series) and YAG laser marker (MD-H9800 Series) are classified as Laser Class 4. |
||
Examples of physical processing using laser markers |
||
Type of processing |
Typical target materials |
|
Melting surface |
Resin |
|
Burning |
Paper, resin |
|
Peeling off surface |
Plated metal, printed paper |
|
Oxidizing surface |
Metal |
|
Engraving |
Glass, metal |
|
Discoloration |
Resin |
The CO2 laser marker (ML-G Series) and YAG laser marker (MD-H9800 Series) are classified as Laser Class 4. |
||
Examples of physical processing using laser markers |
||
Type of processing |
Typical target materials |
|
Melting surface |
Resin |
|
Burning |
Paper, resin |
|
Peeling off surface |
Plated metal, printed paper |
|
Oxidizing surface |
Metal |
|
Engraving |
Glass, metal |
|
Discoloration |
Resin |
Line lasers are offered with a red beam or a green beam. A green beam is easier to see with the human eye because the green wavelength is larger than red. Green is also more visible in sunlight, so it is easier to see outside. When it comes to the visibility range, it depends on the lighting conditions. In dim, dusk-like conditions, it is possible to see a green beam for over 100 feet. One thing to keep in mind is that green beams do require more battery power than red beam lasers.
DEWALT offers these lasers on a 12V MAX* battery platform as well as with Alkaline batteries. Plus, our line lasers offer an integrated magnetic bracket to make them easy to mount during use. Suggested SKUs include our 12V MAX* 3 X 360 Green Line Laser (DW089LG) and our Green Cross Line Laser (DW088CG).
SPOT LASERS:
Spot lasers differ from line lasers in that they project a small circle of light onto the surface your laser is focused on. They are intended for transferring points from one surface to another. This could be for making sure a joist or wall is plumb (vertical) or to ensure pipes traveling from floor to floor are plumb. Spot lasers are most commonly used for plumbing installation, electrical work, HVAC, and framing applications.
LINE LASERS:
Lets begin with the most common laser found on a jobsite, the line laser. A line laser projects an accurate horizontal or vertical illuminated line onto the surface at which the laser is pointed. Use line lasers indoors when installing cabinetry, tile, a drop ceiling, or for basic leveling. They can also be used outdoors when framing or installing a deck.
There are two types of projections, a forward projection and a 360 projection. The forward projection does just what it sounds like, it projects a line directly onto the surface where the laser is pointed. Similarly, the 360 projection will project a line 360 degrees surrounding the laser.
For example, when using a line laser in a room, the forward projection would provide you with a line on one wall whereas the 360 would project that line on all four walls of the room.
DEWALT offers spot lasers in both 3-spot and 5-spot. A 3- spot provides plumb and forward-facing dots whereas the 5- spot adds a right and left dot for transfer of points from wall to wall. A suggested SKU is our Green Beam 3 Spot Laser (DW083CG) with a high-visibility green beam. This laser includes a single lever power switch that locks the pendulum in the off position, as well as a built-in magnetic pivoting bracket to easily mount the laser onto metal surfaces.
SELECTION OF LINE LASER: As our wheel aligning tool is the manual operating tool which need not the skilled operator. If we use the spot laser in the tool for inspecting the proper alignment, the accuracy can be vary by the user to user. In the spot laser the user have to move the spot of the laser beam through the chain from the wheel to the small end where there is a gears. While laser travels it can be vary by shaking. Whereas in the line laser, there is no need to move the laser beam, as it is visible like a line through out the chain.
SCREW :
A screw is a mechanism that converts rotational motion to linear motion, and a torque (rotational force) to a linear force.[1] It is one of the six classical simple machines. The most common form consists of a cylindrical shaft with helical grooves or ridges called threads around the outside.
The screw passes through a hole in another object or medium, with threads on the inside of the hole that mesh with the screw's threads. When the shaft of the screw is rotated relative to the stationary threads, the screw moves along its axis relative to the medium surrounding it; for example rotating a wood screw forces it into wood. In screw mechanisms, either the screw shaft can rotate through a threaded hole in a stationary object, or a threaded collar such as a nut can rotate around a stationary screw shaft.[4][5] Geometrically, a screw can be viewed as a narrow inclined plane wrapped around a cylinder.[1]
Like the other simple machines a screw can amplify force; a small rotational force (torque) on the shaft can exert a large axial force on a load. The smaller the pitch (the distance between the screw's threads), the greater the mechanical advantage (the ratio of output to input force). Screws are widely used in threaded fasteners to hold objects together, and in devices such as screw tops for containers, vises, screw jacks and screw presses.
Other mechanisms that use the same principle, also called screws, don't necessarily have a shaft or threads. For example, a corkscrew is a helix-shaped rod with a shrp point, and an Archimedes' screw is a water pump that uses a rotating helical chamber to move water uphill. The common principle of all screws is that a rotating helix can cause linear motion.
SCREW THREADS:
Main articles: Screw thread, Metric thread, and ISO metric screw thread
Different shapes (profiles) of threads are used in screws employed for different purposes. Screw threads are standardized so that parts made by different manufacturers will mate correctly.
THREAD ANGLE:
Main article: Thread angle
The thread angle is the included angle, measured at a section parallel to the axis, between the two bearing faces of the thread.
The angle between the axial load force and the normal to the bearing surface is approximately equal to half the thread angle, so the thread angle has a great effect on the friction and efficiency of a screw, as well as the wear rate and the strength. The greater the thread angle, the greater the angle between the load vector and the surface normal, so the larger the normal force between the threads required to support a given load. Therefore, increasing the thread angle increases the friction and wear of a screw.
The outward facing angled thread bearing surface, when acted on by the load force, also applies a radial (outward) force to the nut, causing tensile stress. This radial bursting force increases with increasing thread angle. If the tensile strength of the nut material is insufficient, an excessive load on a nut with a large thread angle can split the nut.
The thread angle also has an effect on the strength of the threads; threads with a large angle have a wide root compared with their size and are stronger.
Standard types of screw threads: (a) V, (b) American National, (c) British Standard, (d) Square, (e) Acme, (f) Buttress, (g) Knuckle
Standard types of screw threads: (a) V, (b) American National, (c) British Standard, (d) Square, (e) Acme, (f) Buttress, (g) Knuckle
TYPES OF THREAD:
In threaded fasteners, large amounts of friction are acceptable and usually wanted, to prevent the fastener from unscrewing.[5] So threads used in fasteners usually have a large 60° thread angle:
-
(a) V thread – These are used in self-tapping screws such as wood screws and
sheet metal screws which require a sharp edge to cut a hole, and where additional friction is needed to make sure the screw remains motionless, such as in setscrews and adjustment screws, and where the joint must be fluid tight as in threaded pipe joints.
-
(b) American National – This has been replaced by the almost identical Unified Thread Standard. It has the same 60° thread angle as the V thread but is stronger because of the flat root. Used in bolts, nuts, and a wide variety of fasteners.
Further information: National pipe thread
-
(c) Whitworth or British Standard
Main article: British Standard Whitworth
-
Very similar British standard replaced by the Unified Thread Standard.
In machine linkages such as lead screws or jackscrews, in contrast, friction must be minimized.[5] Therefore threads with smaller angles are used:
-
-
(d) Square thread
Main article: Square thread
-
This is the strongest and lowest friction thread, with a 0° thread angle,[5] and doesn't apply bursting force to the nut. However it is difficult to fabricate, requiring a single point cutting tool due to the need to undercut the edges.[5] It is used in high-load applications such as jackscrews and lead
screws but has been mostly replaced by the Acme thread. A modified square thread with a small 5° thread angle is sometimes used instead, which is cheaper to manufacture.
-
-
(e) Acme thread
-
With its 29° thread angle this has higher friction than the square thread, but is easier to manufacture and can be used with a split nut to adjust for wear.[5] It is widely used in vises, C-clamps, valves, scissor jacks and lead screws in machines like lathes.
-
-
(f) Buttress thread
Main article: Buttress thread
-
This is used in high-load applications in which the load force is applied in only one direction, such as screw jacks.[5] With a 0° angle of the bearing surface it is as efficient as the square thread but stronger and easier to manufacture.
-
-
(g) Knuckle thread
Main article: Knuckle thread
-
Similar to a square thread in which the corners have been rounded to protect them from damage, also giving it higher friction. In low-strength applications it can be manufactured cheaply from sheet stock by rolling. It is used in light bulbs and sockets.
USES:
A screw conveyor uses a rotating helical screw blade to move bulk materials.
A screw conveyor uses a rotating helical screw blade to move bulk materials.
Because of its self-locking property (see below) the screw is widely used in threaded fasteners to hold objects or materials together: the wood screw, sheet metal screw, stud, and bolt and nut.
-
-
The self-locking property is also key to the screw's use in a wide range of other applications, such as the corkscrew, screw top container lid, threaded pipe joint, vise, C-clamp, and screw jack.
-
Screws are also used as linkages in machines to transfer power, in the worm gear, lead screw, ball screw, and roller screw. Due to their low efficiency, screw linkages are seldom used to carry high power, but are more often employed in low power, intermittent uses such as positioning actuators.
-
Rotating helical screw blades or chambers are used to move material in the Archimedes' screw, auger earth drill, and screw conveyor.
-
The micrometer uses a precision calibrated screw for measuring lengths with great accuracy.
The screw propeller, although it shares the name screw, works on very different physical principles from the above types of screw, and the information in this article is not applicable to it.
SINGLE ANGLE SCREW: The Wheel alignment tool is to be mounted on the chain sprocket of the bike wheel. Using the single angle screw to tight the holder is not firm. While using the single angle thread, the position of the tool over the chain sprocket may vary depends on the user handling.
DOUBLE ANGLE SCREW: Replacing the single angle screw with the double angle screw is the best option for us. While using the double angle screw on the holder of the wheel alignment tool, the position of the tool over the chain sprocket of the motor cycle will not be varied depends on the users handling. As the screw has the thread over the both sides of the screw in the opposite direction to each other, the holder gets closed evenly and there will be no variation while Tighting the screw.
So, that here we select the double angle screw for this wheel alignment tool.
MATERIAL SELECTION: MILD STEEL
Mechanical Properties of Mild Steel
Mechanical Properties of Mild Steel
Steel is made up of carbon and iron, with much more iron than carbon. In fact, at the most, steel can have about 2.1
percent carbon. Mild steel is one of the most commonly used construction materials. It is very strong and can be made from readily available natural materials. It is known as mild steel because of its relatively low carbon content. Chemistry
Mild steel usually contains 40 points of carbon at most. One carbon point is .01 percent of carbon in the steel. This means that it has at most .4 percent carbon. Most steels have other alloying elements other than carbon to give them certain desirable mechanical properties. 1018 steel, a common type of mild steel, contains approximately .6 percent to .9 percent manganese, up to .04 percent phosphorus, and up to .05 percent sulphur. Varying these chemicals affects properties such as corrosion resistance and strength.
Physical Properties: Stength
Mild steel is very strong due to the low amount of carbon it contains. In materials science, strength is a complicated term. Mild steel has a high resistance to breakage. Mild steel, as opposed to higher carbon steels, is quite malleable, even when cold. This means it has high tensile and impact strength. Higher carbon steels usually shatter or crack under stress, while mild steel bends or deforms.
Quantitative Physical Properties
Mild steel has a density of .248 pounds per cubic inch. It melts at 2,570 degrees Fahrenheit. It has a specific heat of around .122 British Thermal Units (BTU) per pound, per cubic inch.
Usability
Mild steel is especially desirable for construction due to its weldability and machinability. Because of its high strength and malleability, it is quite soft. This means that it can be easily machined compared to harder steels. It is also easy to weld, both to itself and to other types of steel. It takes on a nice finish and is polishable. However, it cannot be hardened through heat treatment processes, as higher carbon steels can. This is not entirely a bad thing, because harder steels are not as strong, making them a poor choice for construction projects.
percent carbon. Mild steel is one of the most commonly used construction materials. It is very strong and can be made from readily available natural materials. It is known as mild steel because of its relatively low carbon content. Chemistry
Mild steel usually contains 40 points of carbon at most. One carbon point is .01 percent of carbon in the steel. This means that it has at most .4 percent carbon. Most steels have other alloying elements other than carbon to give them certain desirable mechanical properties. 1018 steel, a common type of mild steel, contains approximately .6 percent to .9 percent manganese, up to .04 percent phosphorus, and up to .05 percent sulphur. Varying these chemicals affects properties such as corrosion resistance and strength.
Physical Properties: Strength
Mild steel is very strong due to the low amount of carbon it contains. In materials science, strength is a complicated term. Mild steel has a high resistance to breakage. Mild steel, as opposed to higher carbon steels, is quite malleable, even when cold. This means it has high tensile and impact strength. Higher carbon steels usually shatter or crack under stress, while mild steel bends or deforms.
Quantitative Physical Properties
Mild steel has a density of .248 pounds per cubic inch. It melts at 2,570 degrees Fahrenheit. It has a specific heat of around .122 British Thermal Units (BTU) per pound, per cubic inch.
Usability
Mild steel is especially desirable for construction due to its weldability and machinability. Because of its high strength and malleability, it is quite soft. This means that it can be easily machined compared to harder steels. It is also easy to weld, both to itself and to other types of steel. It takes on a nice finish and is polishable. However, it cannot be hardened through heat treatment processes, as higher carbon steels can. This is not entirely a bad thing, because harder steels are not as strong, making them a poor choice for construction projects.
or rotary table. The chuck holds the material in place while it is being worked on. It can do this one of two ways: ferromagnetic pieces are held in place by a magnetic chuck, while non-ferromagnetic and nonmetallic pieces are held in place by vacuum or mechanical means. A machine vise (made from ferromagnetic steel or cast iron) placed on the magnetic chuck can be used to hold non-ferromagnetic workpieces if only a magnetic chuck is available.
Factors to consider in surface grinding are the material of the grinding wheel and the material of the piece being worked on.
Typical workpiece materials include cast iron and mild steel. These two materials don't tend to clog the grinding wheel while being processed. Other materials are aluminum, stainless steel, brass and some plastics. When grinding at high temperatures, the material tends to become weakened and is more inclined to corrode. This can also result in a loss of magnetism in materials where this is applicable.
The grinding wheel is not limited to a cylindrical shape and can have a myriad of options that are useful in transferring different geometries to the object being worked on. Straight wheels can be dressed by the operator to produce custom geometries. When surface grinding an object, one must keep in mind that the shape of the wheel will be transferred to the material of the object like a reverse image.
SURFACE GRINDING:
Surface grinding is the most common of the grinding operations. It is a finishing process that uses a rotating abrasive wheel to smooth the flat surface of metallic or nonmetallic materials to give them a more refined look by removing the oxide layer and impurities on work piece surfaces. This will also attain a desired surface for a functional purpose.
The surface grinder is composed of an abrasive wheel, a work holding device known as a chuck, and a reciprocating
Surface Grinder with electromagnetic chuck, inset shows a Manual magnetic chuck
A surface grinder is a machine tool used to provide precision ground surfaces, either to a critical size or for the surface finish.
The typical precision of a surface grinder depends on the type and usage, however ±0.002 mm (±0.0001 in) should be achievable on most surface grinders.
The machine consists of a table that traverses both longitudinally and across the face of the wheel. The longitudinal feed is usually powered by hydraulics, as may the cross feed, however any mixture of hand, electrical or hydraulic may be used depending on the ultimate usage of the machine (i.e., production, workshop, cost). The grinding wheel rotates in the spindle head and is also adjustable for height, by any of the methods described previously. Modern surface grinders are semi-automated, depth of cut and spark- out may be preset as to the number of passes and, once set
up, the machining process requires very little operator intervention.
Depending on the workpiece material, the work is generally held by the use of a magnetic chuck. This may be either an electromagnetic chuck, or a manually operated, permanent magnet type chuck; both types are shown in the first image.
The machine has provision for the application of coolant as well as the extraction of metal dust (metal and grinding particles).
As with any grinding operation, the condition of the wheel is extremely important. Grinding dressers are used to maintain the condition of the wheel, these may be table mounted or mounted in the wheel head where they can be readily applied.
JIG BORING:
Jig boring is used to accurately enlarge existing holes and make their diameters highly accurate. Jig boring is used for holes that need to have diameter and total runout controlled to a high degree. Typically, a part has holes machined on regular equipment and then the part is transferred to a dedicated jig boring machine for final operations on the especially accurate holes. Jig boring can also maintain high accuracy between multiple holes or holes and surfaces. Tolerances can be held readily within ±.005 mm (±0.0002 inches). Dedicated jig boring machines are designed to machine holes with the tightest tolerances possible with a machine tool.
When designing a part with holes, it is important to determine what holes must be jig bored. The reason for this is that jig boring requires extra time and attention, and the jig boring machine at the machine shop may have a back log of jobs. Jig boring can therefore have a big impact on the lead time of a part. A cross section of a hole being jig bored is shown below.
PROBLEM STATEMENT:
In existing method of wheel alignment tool the point laser is used to find whether there is any misalignment. The head of the tool in which the laser present has to be moved front and back to make the laser beam travel over the surface of the chain. It affects the accuracy of the system. The error will come due to the shake during the manual operation.
In order to avoid the error due to shaking, we can use the line laser (Laser level mini beam LED light).
In the tool that existing contains the one way thread for adjusting the holder. The tool has to be holded on the chain sprocket with the help of the holder of the alignment tool. There can be the variation in the position of the tool holding while tightening the screw.
In order to avoid the problem we can use the double angle screw, so that the holder can be tighten evenly on both side.
RESULT AND DISCUSSION:
The line of the line laser will fall straightly over the chain, so that there is no need of moving the head of the alignment tool. The accuracy is maintained by using the line laser.
The double angle thread makes the holder to hold the chain sprocket firmly and properly. As the opposite sides of the holder moves constantly there will not be a change in the position of the tool.
Constant value in the result of the system. It will not be changed by user to user.
Accuracy is maintained in this tool by measuring the wheel alignment. Easy to hold in the chain sprocket and measure the accuracy at minimum time.
CONCLUSION:
The wheel alignment angles have the extraordinary influences on automobiles operational performance, such as traveling security and riding stability. To keep vehicle performance, ordinary examination and adjustment of wheel alignment angles are needed by using the capability of a wheel alignment system. Using the Line laser wheel alignment tool alignment can be inspected quickly with more accuracy .
Standard boring can be carried out on a mill fitted with a boring head or on a lathe. Boring is most accurate on a lathe since a lathe is dedicated to solids of revolution (axially symmetric parts).
REFFERENCE:
-
DÃaz, V.; RamÃrez, M.; Muñoz, B. The wheel model for the study of the wheel angle measurement in the periodic motor vehicle inspection. Int. J. Veh. Des. 2004, 34, 297 308.
-
Furukawa Y, Yuhara N, Sano S, Takeda H, Matsushita Y (1989) A Review of Four Wheel Steering Studies from the Viewpoint of Vehicle Dynamics and Control. Vehicle System Dynamics.
-
Implementation of Machine Vision System for finding Defects in Wheel Alignment Akshay Padegaonkar, MadhuraBrahme, Mohit Bangale, International Journal of Computing and Technology.
-
F. Lévy, in Encyclopedia of Condensed Matter Physics, 2005
-
Gabriele Vajente, … David H. Reitze, in Advances In Atomic,
Molecular, and Optical Physics, 2019
-
Toshihiko Yamauchi, … Shinichi Itoh, in Free Electron Lasers 2003, 2004.
PICTORIAL REPRESENTATION:
SAMPLE PICTORIAL VIEW OF WAT-WHEEL ALIGNMENT TOOL WITHOUT LASER ATTACHMENT
******