
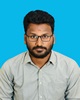
- Open Access
- Authors : Uma Ravi Teja Macherla
- Paper ID : IJERTV12IS040028
- Volume & Issue : Volume 12, Issue 04 (April 2023)
- Published (First Online): 24-04-2023
- ISSN (Online) : 2278-0181
- Publisher Name : IJERT
- License:
This work is licensed under a Creative Commons Attribution 4.0 International License
Evaluation of Bagasse Ash as a Substitute for Fly Ash in the Production of NAAC Blocks
Uma Ravi Teja. Macherla
Department of Civil Engineering
Sri Venkateswara College of Engineering and Technology Etcherla, Srikakulam, India
Abstract This study investigates the use of bagasse ash as a partial replacement for fly ash in the production of non- autoclaved aerated concrete (NAAC) blocks. The study aimed to determine the optimal percentage of bagasse ash to replace fly ash in NAAC blocks. this study demonstrates that bagasse ash can be used as a partial replacement for fly ash in the production of NAAC blocks. However, the optimal percentage of bagasse ash to replace fly ash depends on the desired properties of the NAAC blocks. This research can provide insights for manufacturers to develop more sustainable and eco- friendly building materials. The experiment involved varying the percentage of bagasse ash in increments of 5% (0%, 5%, 10%, 15%, and 20%) to replace fly ash. The properties of the NAAC blocks produced were then evaluated based on compressive strength, water absorption, and density. The results showed that as the percentage of bagasse ash increased, the compressive strength of the NAAC blocks decreased. However, the water absorption and density of the blocks increased as the percentage of bagasse ash increased. The optimal percentage of bagasse ash for partial replacement of fly ash was found to be 20%, as it provided a good balance between water absorption, and density.
KeywordsNon Autoclaved aerated Concrete; Flyash; Bagasse Ash; Water Absorption; Aluminium Powder
-
INTRODUCTION
Non-autoclaved aerated concrete (NAAC) blocks, also known as cellular lightweight concrete (CLC) blocks, are a type of building material used in construction. NAAC blocks are made from cement, water, and an aluminium agent, and are produced without the use of autoclaves, which are high- pressure vessels used to cure some types of aerated concrete. NAAC blocks are lightweight, with a typical density ranging from 400 to 1600 kg/m3, depending on the production method and the mix design. They have good thermal insulation properties, which make them suitable for use in walls, roofs, and floors of buildings. NAAC blocks also have good fire resistance and sound insulation properties, making them a popular choice for use in residential, commercial, and industrial buildings. NAAC blocks can be produced in a variety of shapes and sizes, including standard rectangular blocks, interlocking blocks, and corner blocks. They can also be produced with different surface finishes, such as smooth, textured, or exposed aggregate. The production process for NAAC blocks involves mixing cement, water, and an aluminium agent to form slurry. The slurry is then poured into a mould, and air is introduced into the mixture by mechanical agitation or by the reaction of the aluminium agent with the cement. The mixture then sets and hardens, forming the NAAC block. One of the advantages of NAAC blocks is that
they are environmentally friendly. They are made from readily available and abundant materials, and their production process consumes less energy compared to other types of building materials. Additionally, the use of NAAC blocks can help reduce the carbon footprint of buildings, as they provide good thermal insulation properties, reducing the need for energy- intensive heating and cooling systems. NAAC blocks are a lightweight, environmentally friendly, and versatile building material that offer good thermal insulation, fire resistance, and sound insulation properties. They are suitable for use in a variety of construction applications and can help reduce the carbon footprint of buildings.
-
OBJECTIVE
-
To determine the water absorption characteristics of NAAC blocks with partial replacement of fly ash by bagasse ash.
-
To evaluate the effect of curing time on the properties of NAAC blocks with partial replacement of fly ash by bagasse ash.
-
To identify the energy-effectiveness of using bagasse ash as a partial replacement for fly ash in the production of NAAC blocks.
-
-
LITERATURE REVIEW
Razia Begum et al. researchers explored the potential of using rice husk ash as an aggregate in the production of non- autoclaved aerated concrete blocks mixed with cement. Different replacement amounts of rice husk ash were tested, ranging from 0% to 50%. The goal was to determine how the addition of rice husk ash would affect the final properties of the concrete blocks, including compressive strength, water absorption, and density. The results indicated that the addition of rice husk ash led to a decrease in weight for all replacement ratios tested. Additionally, the compressive strength and water absorption of the concrete blocks were higher when rice husk ash was present, up to an optimum replacement level of 30%. This suggests that using rice husk ash as an aggregate in concrete could have potential benefits for the final product.
Abdul Khaliq AND anuj Verma highlights the benefits and considerations of using AAC blocks in construction. The blocks are made by combining aluminium powder with lime, cement, and fly ash or sand to create a lightweight, easy-to- build, and inexpensive-to-transport masonry material. The
use of AAC blocks can potentially cut building costs by up to 25% due to their low weight, which can decrease the weight of infill walls on beams, columns, and footings, resulting in savings on reinforced steel. Additionally, the light weight and low Young modulus in compression of AAC blocks may help to reduce inertia forces on a building during seismic activity. However, it is worth noting that the masonry compressive strength of AAC blocks is low compared to other conventional masonry types, despite having restricted variability. Therefore, it is important to consider the production method and seismic performance of autoclaved aerated concrete blocks when using them in construction projects.
Nishant Kumar1 Suneha Dhiman2 Concrete is one of the most commonly used substances in construction worldwide. However, the production of concrete results in high levels of carbon emissions, contributing significantly to greenhouse gases. To reduce the amount of concrete used in construction and lessen its environmental impact, waste materials such as bagasse ash can be used as partial replacements for concrete. India, for instance, produces 300 million tons of sugarcane annually, resulting in a significant amount of bagasse ash waste. One alternative to traditional concrete is Non- Autoclaved Aerated Concrete (NAAC), which is lightweight and commonly used in construction materials. The aim of this research is to create NAAC blocks that can replace clay bricks in brickwork. By using NAAC blocks instead of clay bricks, it may be possible to reduce the amount of concrete used in construction, leading to lower carbon emissions and a more sustainable approach to building.
-
METHODOLOGY
-
EXPERIMENT STUDY
An experiment was conducted to evaluate the water absorption of Non-Autoclaved Aerated Concrete (NAAC) blocks produced using different mix designs. The study involved varying the amount of cement, bagasse ash, fly ash,
lime, gypsum, aluminium powder and water in the mix, and measuring the resulting water absorption of the blocks.
Mix Calculations:
Volume of Mould: 0.5*0.1*0.1 m3 = 0.005 m3 Density of AAC/NAAC Blocks: 600 Kg/m3
Unit Weight of NAAC Block = Volume of Mould X Density of Block
= 0.005 m3 X 600 Kg/ m3
= 3 Kg/ m3
Total Weight = 3Kgs
Proportions are taken for Non Autoclaved Aerated Blocks Fly ash =50%
Cement: 40%
Lime: 7%
Gypsum: 3%
Aluminium Powder: 0.08% Water Slurry Ratio: 0.65
TABLE I – MATERIAL PROPORTIONS
% of Replac ement
MATERIAL
FLYA SH
BAGAS SE ASH
CEM ENT
LIM E
GYPS UM
ALUMINI UM POWDER
WA TER
0%
1.5 Kgs
0 Kgs
1.2
Kgs
0.21
Kgs
0.09
Kgs
0.0024
Kgs
1.9 L
5%
1.425
Kgs
0.075
Kgs
1.2
Kgs
0.21
Kgs
0.09
Kgs
0.0024
Kgs
1.9 L
10%
1.35
Kgs
0.15 Kgs
1.2
Kgs
0.21
Kgs
0.09
Kgs
0.0024
Kgs
1.9 L
15%
1.275
Kgs
0.225
Kgs
1.2
Kgs
0.21
Kgs
0.09
Kgs
0.0024
Kgs
1.9 L
20%
1.2 Kgs
0.3 Kgs
1.2
Kgs
0.21
Kgs
0.09
Kgs
0.0024
Kgs
1.9 L
Casted 5 Different Proportions of Specimens and De moulded after 24 hrs of Casting. After Demoulding kept specimens under room temperature for 24 Hrs. After 24 Hrs of time Specimens are kept in curing tank for 24 hrs to observe the Water Absorption Rate
-
RESULTS
Weights are taken While Demoulding of fresh sample and Specimens after 24 hrs of time in curing
S.no |
% of Replacement of BA with FA |
Fresh Specimen Weight (W1) |
Specimen Weight After 24 hrs Curing (W2) |
1 |
0% |
4.012 Kgs |
4.416 Kgs |
2 |
5% |
4.090 Kgs |
4.520 Kgs |
3 |
10% |
4.088 Kgs |
4.556 Kgs |
4 |
15% |
4.102 Kgs |
4.604 Kgs |
5 |
20% |
4.062 Kgs |
4.618 Kgs |
TABLE II Weights of Specimens
% of Water Absorption
15.00%
10.00%
5.00%
0.00%
10.57% 10.51% 11.45% 12.24% 13.69%
S.no |
% of Replacement of BA with FA |
% of Water Absorption = ((W2- W1)/W1 )*100 |
1 |
0% |
10.07 |
2 |
5% |
10.51 |
3 |
10% |
11.45 |
4 |
15% |
12.24 |
5 |
20% |
13.69 |
TABLE III Percentage of Water Absorption
0% 5% 10% 15% 20%
% of Replacement of BA with FA
% of Water Absorption
% of Water Absorption
Fig.1 Water Absorption Graph
Fig.2 NAAC Block with 20% replacement of BA with FA
CONCLUSION
With the above results, we can the increase of water absorption graph. But the water absorption shouldnt be more than 15 %.Water Absorption rate was good by comparing all the results with their respective replacements. Up to 20% of replacement it will be acceptable under working on Non Autoclaved Aerated Concrete Blocks.
REFERENCES
[1] Abdul Khaliq, and Anuj Verma. "A Review Study on Non Autoclaved Aerated Concrete." ISJET, 2022: 1-8. [2] DR.K. YUGANDHAR REDDY, SK. SAMEER, M. VENKATESWARLU, and CV. MASTHAN. "PARTIALLY REPLACEMENT OF CEMENT WITH SUGARCANE BAGASSE ASH AND FLY ASH." Mukt Shabd Journal ISSN NO : 2347-3150, 2020: 4488-4501. [3] Karishma Chauhan, and Puneet Sharma. "TO STUDY THE STRENGTH CHARACTERISTICS OF NON-AUTOCLAVED AERATED CONCRETE USING RICE HUSK ASH AND MARBLE POWDER." IJARET Volume 11 Issue 12, 2020: 1052-1063. [4] Ms. Razia Begum, Mr. Ahsan Habib, and Mr. Shah Mostafa. "Effects of Rice Husk Ash on the Non Autoclaved Aerated Concrete." IJEIR Volume 3 Issue 1, 2014: 116-121. [5] Nishant Kumar, and Suneha Dhiman. "PARTIAL REPLACEMENT OF CEMENT USING BAGASSE ASH IN NON – AUTOCLAVED AERATED CONCRETE." IJRET Volume:7 Issue 7, 2020: 1242-1245.