
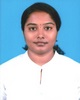
- Open Access
- Authors : Megha Subramanya
- Paper ID : IJERTV10IS080071
- Volume & Issue : Volume 10, Issue 08 (August 2021)
- Published (First Online): 16-08-2021
- ISSN (Online) : 2278-0181
- Publisher Name : IJERT
- License:
This work is licensed under a Creative Commons Attribution 4.0 International License
Electrowinning of Copper from Industrial Waste Streams
Megha Subramanya
Department of Civil Engineering Maharaja Institute of Technology Mysore, Mandya, India
AbstractThe copper plating and several copper emitting industries have their impact on the environment and human health. This research work has an approach for the reduction of the heavy metal concentration that is being discharged from these industries. The
purpose is to reduce the load of the heavy metals (esp. Copper) before it reaches the environment and affects the human health. The problems that have an impact on the human health are of high priority as it disrupts the functions of vital organs. The groundwater contamination and soil contamination are the impacts on the environment. The copper fencing industry discharge a notable amount of wastewater containing copper and fewer heavy metal concentration and cause serious environmental and health damage. The focus is on the applied electrical copper recovery system to recover copper metal. In this work, electrotreatment of the industrial copper wastewater ([Cu]=1350 mgL-1) was studied with titanium coated with a thin layer of RuO2/IrO2 (DSA).The optimal result for industrial copper waste streams was 57% with a current of 4 A and voltage of 10 V. This efficiency drop was due to the presence of chloride and iron ions in the industrial wastewater. Design consisting of a rotating tubular bed reactor with extended cathode surface to
improve the mass transfer in the cell, combination of electrolytic and ion exchange treatments which further reduces the copper content below the ppm level, use of DSA net anode which gives more surface area for the deposition of the copper can be founded by this research work.
KeywordsComponent; formatting; style; styling; insert (key words)
-
INTRODUCTION
Rapid expansion in the industrial sector showcases several industrial processes such as metal plating facilities, printed circuit board, mining operations, etching operation, batteries are giving away byproducts and waste products which are directly or indirectly discharged of large amounts of metal contaminants wastewater, industries bearing heavy metals such as Cu, Cr, Cd, Ni, As, Pb and Zn are considered as the most hazardous among the chemical intensive industries. Non-biodegradability and persistence of heavy metals accumulate in food chain because of high solubility. Once they enter the food chain, large concentration of heavy metal accumulate as body burden. If the metals are ingested beyond the permissible concentrations, it causes serious health disorders (Chen et al., 2013). Therefore, it is necessary to treat metal contaminated wastewater and waste streams prior to its discharge into the aquatic and terrestrial environment.
Increasing metal usage leads inevitably to ecological problems of metal in contamination of our natural environment. The heavy metals which occur naturally in soil, water and living organism can have severe impact on the living system if in excess concentration (Giannopoulou and Panias, 2007). It is important to identify the chemical reactivity and mobility of the heavy metal in different natural environments because it affects redistribution of soils, landscapes and hydrological cycle and passage through the food chain. We can see those impacts through heavy metal soil contamination, ground water contamination and bioaccumulation of heavy metals in aquatic organisms etc.
Heavy metals are generally considered to be those whose density exceeds 5 gcm-3. Heavy metals cause serious health effects,
including reduced growth and development, cancer, organ damage, nervous system damage and in extreme cases may cause death.
Heavy metals disrupt metabolic functions in two ways:
-
They accumulate and thereby disrupt function in vital organs and glands such as the heart, brain, kidneys, bone, liver, etc.
-
They displace the vital nutritional minerals from their original place, thereby hindering their biological function.
Exposure to some metals, such as mercury and lead, may also cause development of autoimmunity, in which a persons immune system attacks its own cells. This may lead to joint diseases such as rheumatoid arthritis, diseases of the kidneys, circulatory system, nervous system, and damaging the fetal brain. At higher doses, heavy metals may cause irreversible brain damage. Wastewater regulations were established to minimize human and environmental exposure to hazardous chemicals. This includes limits on the types and concentration of heavy metals that may be present in the discharged wastewater.
Copper is found in many wastewater sources including, printed circuit board manufacturing, copper solar fencing industries, electroplating operation, wire drawing, copper polishing, paint manufacturing, wood preservatives and printing operations. Typical concentrations vary from several thousand mgL-1 from plating bath waste to less than 1 mgL-1 from copper cleaning operations. Due to the complexity production processes in electroplating copper manufacturing, acid washing water which contains abundant cupric ions and they are considered to be reclaimed (Chen et al., 2013).
Copper containing wastewaters are produced during the metallurgical operations, copper refining, electrolyte regeneration steps and also in sulphuric acid plants. Taking into account of high outflows of these industrial streams, a large amount of valuable metal copper is potentially lost. They have significant negative impact on the environment and human health since they are highly soluble and can enter the food chain and they have the capacity to bio- accumulate. The concentration levels of the copper metals will have a negative impact on the environment and the human health. They cause serious health effects. Thus, it is of great importance to pretreat the wastewaters so that the contained valuable metals to be recovered (Giannopoulou and Panias, 2007).
-
-
MATERIALS AND METHODS
The raw wastewater was procured from copper solar fencing industry located in Heggana halli Industrial area, Bangalore. The industry produces solar fences which are used in solar water heater panels and in the solar electric fence system which are used in the agriculture, forestry or plantation sectors. The wastewater used for this research work was collected from the first source having a flow rate of 1500- 2000 Ld-1 (after the treatment with HCl and CuSO4 water wash).
The wastewater which was procured from the industry was characterized for various parameters like pH, conductivity, chloride, total dissolved solids (TDS), chemical oxygen demand (COD) and copper concentration as per the standard methods under APHA (American Public Health Association) 2010.
-
Experimental Setup
The experimental setup for the electrowinning of copper from industrial waste streams consists of a single cell batch reactor consisting of electrodes, magnetic stirrer, magnetic bead, power supply unit and an UPS which is as shown in Figure 1.
Figure 1: Schematic representation of the experimental setup
The experiments were carried out in a cuboidal shaped acrylic glass reactor with 1.5 L capacity and it had an arrangement to hold 100 mm x 50 mm x 1 mm electrodes.
The key for an efficient electrolytic treatment is strongly based on electrodes.
Stainless steel as cathode and dimensionally stable anode (DSA) of 1 mm thickness were used for the experiments and it had dimension of 100 mm x 50 mm x 1 mm. DSA was purchased from Titanium anode fabricators Private Ltd #48, Noothanchery, Maambakkam, Chennai-600126. DSA is commonly fabricated from titanium coated with platinum or ruthenium oxide and henceforth are chemically very stable and doesnt introduce impurities into the cell during the reaction. DC power supply was used as a power source for the experiment to supply and maintain current and voltage across the electrode system by means of insulated copper wires. An uninterruptible power supply (UPS) was used to maintain a continuous supply of electric power to the system even during a power failure or any abnormality so that experiments were carried out effectively without any interference. Magnetic stirrer with magnetic bead is used in the experiment to maintain the homogeneity of the solution.
-
Experimental Methodology
Electrochemical reactor of 1.5 L capacity was used for the experiment. The electrodes DSA and stainless steel were washed to remove the impurities present on the surface. Then the initial weight of the electrodes was determined. The two electrodes were placed in the reactor with 1cm inter-electrode spacing. The reactor was filled with 1.5 L of wastewater with the magnetic bead placed at the bottom. The electrodes were connected to the DC power supply with positive terminal connected to anode and negative terminal to cathode. The reactor was kept under completely mixed condition by means of magnetic stirrer with the stirring speed of suitable rpm.
Experiments were carried out with varying cell voltage, pH and stirring speed. In the same way another set of experiments were carried out using four stainless steels in bipolar arrangement. The samples were collected from the reactor at the regular time interval and later it was filtered and analyzed for copper recovery percentage using inductively coupled plasma spectrophotometer (ICP). All the tests were conducted at room temperature and atmospheric pressure. The influence of various operating parameters was studied as a function of percentage copper recovered.
-
Analysis Methods
The analysis methods used for the characterization of parameters are shown in the Table 1. The wastewater was analyzed for various parameters like pH, conductivity, chloride, total dissolved solids (TDS), chemical oxygen demand (COD) and copper concentration as per the standard methods under APHA 2010.
Table 1: Methods used for characterizing parameters
-
Inductively coupled plasma-atomic emission spectrometry
The copper present in the procured wastewater was measured using inductively coupled plasma spectrometer (ICP). The argon gas is used in the system. Plasma temperature ranges between 6000K – 10000K. 0.1 mL and 1 mL of 1000 mgL-1 Cu stock solution was pipetted into 100 mL standard flask and milipore distilled water was used to make up the solution to 100 mL. These solutions were used to calibrate the instrument. Later a complete elemental analysis was carried out over a period of 30 seconds by injecting 0.5 mL of wastewater sample with a wavelength of 324.7 nm.
-
pH
Standardization of pH meter was done by using standard buffer solution of pH 4, 7 and 9.2. The pH of the sample was measured by dipping the glass electrode in the wastewater sample.
-
Conductivity
Electrical conductivity meter was used to measure the electrical conductivity in a solution. The conductivity was measured by dipping probe of the conductivity meter in
the wastewater sample and has a unit of mScm-1. The relationship between the TDS and the conductivity is shown below,
TDS (mgL-1) = 0.67 x Conductivity (Scm-1)
-
Chloride – Argentometric method
Chloride is analyzed by argentometric method. The reagents used for this analysis are silver nitrate solution (0.0141 N) and potassium chromate indicator. Take 25 mL of sample in a conical flask and add 2 to 3 drops of potassium chromate indicator. Titrate against standard silver nitrate (AgNO3) precipitate to be consistent in end point recognition. (Color changes from yellow to pale brick red). Chloride content of the wastewater is calculated by,
Where,
A is the mL of silver nitrate consumed by sample B is the mL of silver nitrate consumed by blank N is normality of silver nitrate (0.0141 N)
-
Chemical oxygen demand (COD) – Closed reflux titrimetric method
Chemical oxygen demand of the wastewater was analyzed by closed reflux titrimetric method. The reagents used for this analysis are standard potassium dichromate (K2Cr2O7) digestion solution (0.1M), standard ferrous ammonium sulfate
solution (0.1M), sulfuric acid reagent and ferroin indicator. Wash the cultured tubes and caps with 20% H2SO4 before to prevent contamination. Transfer the 2.5 mL sample to
culture tubes and add 1.5 mL K2Cr2O7 digestion solution to the vials. Carefully run down 3.5 mL of H2SO4 reagent in to the vials (such that an acid layer is formed under the sample digestion solution). Tighten the cap of the vials and invert it several times to mix completely. Also prepare a blank in the same procedure. Place the vials in the COD digester preheated to 1500C and reflux for 2 hours. Cool down the temperature. Titrate against standard ferrous ammonium sulphate solution (0.1M) by adding 2-3 drops of ferroin indicator until the color changes from green to reddish brown although blue green reappears within a minute. COD in the taken waste water sample was calculated by,
Where, A is mL of FAS consumed by blank
B is mL of FAS consumed by the sample
M is molarity of FAS
-
Total dissolved solids (TDS)
A known volume of sample was filtered using Whattman filter paper and then transferred into a crucible, which was previously dried and weighed (W1). The crucible was kept in a hot air oven maintained at temperature of 105oC for 24 hours and was kept in a desiccator to cool the crucible to room temperature. Then weight of the crucible (W2) was found out, Total dissolved solids (TDS) present in the wastewater was calculated using the formula shown below,
-
X-Ray diffraction
The mineralogical composition of the deposited copper was determined using X-ray diffractometer. The samples were placed in the sample holder. The XRD patterns were recorded at room temperature using Cu K radiation as a source and Kb as a filter and 2 scan rate of 5o min-1 operated at a tube current of 15 mA. The goniometer speed and the chart speed were maintained at 10min-1, and 1 cm/min respectively. The range of scanning angle 2 was kept at 20 – 80o. The intensity peaks indicates the values of 2, where Braggs law was applicable. Braggs law says that, when x-rays are scattered from the crystalline lattice, peaks of
scattered intensities are observed which corresponds to the following conditions,
Angle of incidence is equal to the angle of scattering.
The path length difference is equal to an integer number of wavelengths.
-
Scanning electron microscope (SEM)
-
The SEM is done mainly to know the morphology and texture of the electrodes and deposited copper. The electrodes used for the experiments were cut into 1 mm x 1 mm dimension and the recovered copper powder, flakes were analyzed using SEM at various magnifications.
-
-
RESULTS
The wastewater which was procured from the industry was characterized for various parameters like pH, conductivity, chloride, total dissolved solids (TDS), chemical oxygen demand (COD) and copper concentration as per the standard methods under APHA 2010 and is shown in Table 2.
Table 2: Characteristics of the raw wastewater
-
Batch Electro-Sorption studies
The batch study was conducted using reactor with a working volume of the 1.5 L and it had an arrangement to hold 100 mm x 50 mm x 1 mm electrodes. Two sets of experiments were performed, one by using two electrodes (DSA and stainless steel) in a mono polar arrangement and in another by using four stainless steel electrodes in bipolar arrangement.
-
Effect of Voltae on Copper recovery percentage
In each set of experiment voltage was varied to find out the optimum voltage at which maximum copper recovery occurs. Voltage being a predominant parameter is found to influence the copper recovery percentage during electro precipitation process. The experimental results of copper recovery using two electrodes are shown in Table 3 and using 4 electrodes are shown in Table 4.
In the first set, experiments were carried out starting from 1 V to 4 V at 510 rpm and are shown in Table 3. The maximum copper recovery of 32.62% was observed at an
applied voltage of 2 V for 120 min. Copper deposited on stainless steel was shiny in appearance.. As seen from the Table 3 and Table 4 the copper recovery percentage removal efficiency increased with more contact time. For 1 V there was no change in concentration of copper in the solution, also bubble generation rate was comparatively less and for 3 V light blackish layer was formed on top of the deposited copper on stainless steel and for 4 V complete black deposits were formed due to high potential voltage and bubble generation rate was higher than previous voltages. So, 2 V was considered as optimum.
In the second set, using bipolar batch arrangement experiments were carried out at 5 V, 10 V and 15 V. The maximum copper recovery of 56.99% was observed at an applied voltage of 10 V and recovered copper is shown in Fig 2 (b). For 15 V copper deposited in initial stage but appeared black after 2 min, also color of the wastewater completely changed to green and the results are illustrated in Table 4.
Table 3: Variation of voltage on copper recovery percentage at 510 rpm using DSA and Stainless steel
Table 3: Variation of Voltage on Copper recovery percentage at 510 rpm using four stainless steel (bipolar batch arrangement)
Figure 2: Copper deposited on the electrodes during the experiment
-
Effect of contact time
Contact time or reaction time being an important factor influences copper recovery efficiency in the electrowinning process. In monopolar batch studies, experiments were conducted for various contact time 15 min, 30 min, 45 min, 60 min and 120 min for 2 V at 510 rpm. Copper rate of recovery was slow at the initial stage. As the reaction time increases rate of copper recovery efficiency also increases (Chen et al., 2013). At 2 V for 120 min copper recovery percentage was found to be 32.62%. Effect of contact time as a function of copper recovery percentage for 2 V at 510 rpm can be seen in Figure 3.
Figure 3: Effect of contact time as a function of copper recovery percentage for 2 V at 510 rpm.
Figure 4: Effect of contact time as a function of residual Cu concentration at 2 V for 120 min at 510 rpm in monopolar arrangement
Figure 5: Effect of contact time as a function of residual Cu concentration at 10 V for 60 min at 510 rpm in bipolar arrangement
-
Effect of pH
It has been established by previous researches that the influent pH is an important operating factor influencing the performance of electro deposition process. To examine its the effect, experiments were conducted at varying pH of 0.93, 1.06, 2.42 and 4.25. Since the procured wastewater was acidic in nature, pH was adjusted by adding 0.1 N sodium hydroxide to get the desired pH for the experiment. The Figure 6 shows amount of copper deposited on the cathode was 0.0519 g, 0.1213 g, 0.1599 g and 0.1786 g for 0.93, 1.06, 2.42 and 4.25 of pH respectively. Amount of copper deposition increased as the pH was increased further. It was not economical since amount of sodium hydroxide consumption also increased as the pH was increased. Also it can also be noted that the experiments conducted in previous researches which showed maximum removal had pH in the range of 6 to 8.
Figure 6: Effect of pH as a function of amount of copper deposited on stainless steel for 2 V at 510 rpm
-
Effect of agitation speed
To examine the effect of agitation speed on the amount of copper deposition, experiments were conducted at 2 V for varying speed of 50 rpm, 100 rpm, 300 rpm and 500 rpm. As indicated in the Figure 7 the amount of copper deposition increases with increase in agitation speed, reaching a maximum at 300 rpm. After reaching its maximum, it decreases with further increase in agitation speed. The drop in amount of copper deposition is probably a result of a substantial decrease of mass transfer rates of copper, which is probably behaving as rigid spheres. This phenomenon causes molecular diffusion to govern the system and therefore the amount of copper deposition decreased (Mostaedi et al., 2008).
Figure 7: Effect of stirring speed as a function of amount of copper deposited on stainless steel for 2 V for 45 min
-
Effect of DSA as cathode
To examine the effect of using DSA as cathode on the percentage of copper recovered, experiment was conducted at 8 V using stainless steel as anode and DSA as cathode for 15 min out of curiosity. Bubble generation rate was higher than all the previous experiments conducted at monopolar as well as at bipolar arrangement. There was 29.26% copper recovery for 15 min and 0.2523 g of copper deposition can be seen. Copper deposited on the DSA initially appeared spongy. Formation of thin copper film layer was observed later which can be seen in the Figure 8.
Figure 7: Copper deposition on DSA
-
Effect of supporting electrolyte
Supporting electrolytes are widely used in electrochemical measurements when control of electrode
potentials is required. This is done to increase the conductivity of the solution. Experiments were conducted in order to investigate the effect of the supporting electrolyte. Sodium chloride (NaCl) was used as supporting electrolyte. Experiment was conducted in bipolar arrangement using 4 stainless steel at 10 V for 60 min at 300 rpm. The conductivity was increased from 12 mScm-1 to 30 mScm-1 by the addition of NaCl. Increase in conductivity has also increased copper recovery percentage. About 14% of copper recovery difference can be seen in experiments with and without supporting electrolyte conducted at similar conditions. Figure 8 shows the effect of supporting electrolyte as a function of copper recovery percentage.
Figure 8: Effect of supporting electrolyteas a function of copper recovery percentage at 10 V for 60 min at 300 rpm
-
-
Material characterization
The recovered copper was characterized using powder X-ray Diffraction and in Scanning electron microscope (SEM) to know the mineralogical and morphological information of copper deposited during the experiment. Also electrodes used were characterized using SEM.
-
Powder X ray Diffraction (PXRD)
-
Powder diffraction is a scientific technique using the x-ray on powder samples for structural characterization of materials. Powder diffraction data are usually represented as diffractogram in which diffracted intensity is a function of scattering angle 2. Figure 9 shows the diffractogram of the deposited copper obtained at 2 V 120 min at 510 rpm, which had the maximum copper recovery percentage of 32.62% in monopolar batch study. It shows very broad and shallow diffraction peaks with one high diffraction peak.
Bragg reflections possessing very broad humps and low intensity indicate that the analyzed phase possesses short range order i.e., amorphous or very poor crystalline in
nature and the high peaks indicates high crystalline nature. The deposited copper showed both crystalline phase as Cu and poorly crystalline phase as Cu2O.
Also the XRD results obtained from this experiment are similar to results obtained in the previous researches of Wolberg et al., (1996) and Calvo et al., (2009).
The diffractogram of the deposited copper obtained at 2 V
120 min at 510 rpm, which had the maximum copper
recovery percentage of 32.62% in monopolar batch study is shown in Figure 9.
Figure 9: X-Ray Diffracton analysis of deposited copper at 2 V for 120 min at 510 rpm
Figure 10 shows the diffractogram of the deposited copper obtained at 4 V for 30 min at 510 rpm, which had the copper recovery percentage of 7.93% in monopolar batch study. In this experiment copper initially deposited in reddish color but turned black after 15 min. This may be due to over potential or high applied voltage, the deposited copper got burnt during the experiment. Compared to Figure 9 this has less shallow peaks and has two high peaks. The deposited copper showed both crystalline phase as Cu and poorly crystalline phase as Cu 2O
Figure 10: X-Ray Diffraction analysis of deposited copper at 4 V for 30 min at 510 rpm.
Figure 11 shows the diffractogram of the deposited copper obtained at 10 V for 60 min at 510 rpm, which had the maximum copper recovery percentage of 56.99% in bipolar
batch study. During the experiment copper deposited in the initial stage was shiny in appearance but later it used to turned brick red. The possible reason for this is due to oxidation of Cu to Cu 2O.The deposited copper showed both crystalline phase as Cu and poorly crystalline phase as Cu 2O. Also Figure 11 shows the highest peak compared to all other results at intensity of 24000 cps.
Figure 11: X-Ray Diffraction analysis of deposited copper at 10 V for 60 min at 510 rpm
Figure 12 shows the diffractogram of the sludge obtained at 8 V when DSA was used as cathode and stainless steel as anode for 15 min at 510 rpm, which had the copper recovery percentage of 29.26%. Even though copper deposited on DSA electrolysis reaction took place in the reactor which led to formation of greenish blue color sludge. It showed very broad and shallow diffraction peaks with two high diffraction peaks. It showed both crystalline phase Cu well as poorly crystalline phase Cu 2O.
Figure 12: X-Ray Diffraction analysis of the sludge at 8 V for 15 min at 510 rpm
-
Scanning Electron microscope Analysis
Electrodes used and copper recovered from the experiment is analyzed and is shown below
Figure 13: Surface morphology of DSA electrode at 1000 X
Figure 13 shows the SEM image of the surface of DSA electrode at 1000 X. The surface modifications include mixed metal oxide coating on titanium metal.
The solids deposited (recovered) as flakes on the electrode was characterized for a close morphology using SEM as shown in Figure 14. As can be seen from the figure, numerous spherical ingot like structures were seen in sizes of
1 3 micrometer at 1000X and 5000 X magnification, identified as pure copper. The inset in the pictograph shows the copper flake like thin sheets of Cu recovered from the copper rinse waste stream. XPS (X-ray photoelectron spectroscopy) provides further confirmation of the purity of Cu recovered. Good deposits had less dendrite formation and were easily removed from the electrodes without crumbling.
Figure 14: SEM pictographs of Copper deposited as flakes
Figure 15 shows the SEM image of copper deposits on the electrodes while using SS as electrodes in the Cu rinse water.
The quality of the copper deposits was related by visual observation (inset picture) on the electrodes and the morphology of powder CuO on SEM.
Not so good deposits showed more dendrite formation and were easily removed from the electrodes with crumbling; which turned black when kept overnight.
Figure 15: SEM pictographs of powder form of copper deposited on electrodes
C. Quantitative analysis
Electrochemistry offers promising approaches for the prevention of pollution in the industry. The inherent advantage is its environmental compatibility, due to the fact that the main reagent, the electron, is a clean reagent. Since most of the metal ions present in wastewater can be removed by cathodic deposition, electrochemical processes have been developed for the successful removal and recovery of metal ions from wastewater through cathodic deposition.
Table 4: Quantitative analysis of electrowinning of copper
In this aspect quantitative analysis was done on stainless steel which was used as cathode during electrowinning of copper at 2 V for 120 min at 510 rpm. It is observed from the results presented in Table 4 there was an increase of weight of 0.6006 g on cathode indicating copper deposition taken place on cathode surface.
-
Energy Consumption
Chen et al., 2013 described that the specific energy consumption (EC) can be calculated from the formula
Where,
EC is Energy Consumption, KWhKg-1 A is operational current, A
V is operational voltage , V T is operational time, hours
Co is initial concentration, mgL-1 C is Final concentration , mgL-1 Vr is operational volume, L
Figure 16 shows the energy consumed during the experiments conducted at 2 V for 15 min, 30 min, 45 min, 60 min and 120 min. As the time increases the energy consumed for copper recovery also increases (Chen et al, 2013). Energy consumption of 1.98 KWhKg-1, 2.14 KWhKg-1, 3.24 KWhKg-1, 6.32 KWhKg-1 and 8.62 KWhKg-1 of copper recovered was consumed for 15 min, 30 min, 45 min, 60 min and 120 min respectively at 2 V at 510 rpm.
Figure 16: Energy consumption for the recovery of copper at 2 V at 510 rpm
Addition of supporting electrolyte not only increases conductivity but also increases energy consumed by the system. At 10 V experiments were conducted with and without addition of supporting electrolyte. It can be illustrated in the Figure 17.
Figure 17: Effect of supporting electrolyte on energy consumption at 10 V 60 min at 510 rpm.
-
Effect of mixing sewage with wastewater
Experiments were conducted at 10 V for 60 min at 510 rpm in order to examine the effect of mixing sewage with the copper wastewater. Sewage with the pH of 6.8 and wastewater with the pH of 0.98 was mixed in the proportion 1:1 and 3:1. Copper deposition was observed initially within 2 – 3 min and the formation of foam took place. The bubble generation rate was also high. Copper was deposited on the 3 electrodes except the anode. pH was increased to 2.2 in both the proportions. Even though the copper deposition occurred
on the electrodes, energy consumption was high and the rate of copper recovery was not desirable.
-
Salvage cost calculation
0.83 g of copper was recovered from the experiment conducted at 10 V for 60 min at 510 rpm. Considering the recovery factor of 0.8, then the amount of pure copper recovered is 0.66 g. So 0.66 g of copper is recovered from 1.5 L of wastewater. The present cost of copper is Rs 410 per Kg of copper.
Considering an electroplating industry which discharges copper rinse wastewater having a flow rate of 2000 L d-1, with the cost of copper per Kg being Rs 410, the amount of copper that is recovered from the process has a good value. The cost of the copper that is recovered has a value of Rs 360 per day. This process has a recovery profit of Rs 10,800 per month.
-
-
CONCLUSIONS
Electrosorption batch studies were carried using Dimensionally Stable Anode (DSA) and stainless steel electrodes for various operating parameters such as variation in applied cell voltage, pH and agitation speed and also in bipolar arrangement using stainless steel electrodes in an acrylic reactor of 1.5 L capacity. Part of this chapter
focuses on the conclusions drawn from the above set of experiments and also on suggestions for the further improvement in this research work.
The following conclusions have been drawn from the conducted batch electro-sorption studies:
-
The experiments were conducted in monopolar arrangement at 1 V, 2 V, 3 V and 4 V. Comparatively higher copper recoveries of 32.62% was achieved at 2 V for 120 min at 510 rpm.
-
The experiments were conducted in bipolar arrangement at 5 V, 10 V and 15 V for 60 min. Higher copper recovery of 56.99% was achieved at 10 V at 510 rpm.
-
As the contact time increases the copper recovery percent also increases.
-
Amount of copper recovered increases as the pH increases near the neutral range.
-
Recovered copper was in the form of flakes or film when DSA was used as cathode and stainless steel as anode at 8 V for 15 min.
-
Addition of supporting electrolyte increases percentage copper recovered.
-
PXRD reveals that the deposited copper shows both crystalline phase as Cu and poorly crystalline phase as Cu2O.
-
Electrowinning method not only recovers the copper present in wastestream but also reduces the pollutant load on environment.
-
-
REFERENCES
-
Aroua M K, Zuki F M, Sulaiman N M. Removal of chromium ions from aqueous solutions by polymer-enhanced ultrafiltration. J. Haz. Mat., 2007, (143), 752-758.
-
Adhoum N, Monser L, Bellakhal N, Belgaied J. Treatment of electroplating wastewater containing Cu2+, Zn2+and Cr (VI) by electrocoagulation. J. Haz. Mat., 2004, (B112), 207213
-
Babel and Kurniawan. US EPA Project summary Recovery of metals from wastewater and sludge, Chemosphere 2008, (54), 951 967.
-
Barakat M A and Schmidt E. Polymer-Enhanced Ultrafiltration Process for Heavy Metals Removal from Industrial Wastewater. Int. Conference. Wat. Res., 2008.
-
Barakat M A. New trends in removing heavy metals from industrial wastewater, Arabian J. Chem, 2010, (4), 361377.
-
Bieszczad T, Rydlewska S. Electrowinning of copper and lead from ammonium acetate solutions. J. Min. Process. 2001, (35), 181-193.
-
Borbely G, Nagy E. Nickel and zinc removal by complexation- Ultrafiltration method. Hungarian J. Industrial Chem., 2008, (36), 17-22.
-
Calvo B, Canoiraa L, Moranteb F, Jose M. Continuous elimination of Pb2+, Cu2+, Zn2+, H+ and NH4+ from acidic waters by ionic exchange on natural zeolites. J. Haz. Mat., 2009, (166), 619-627.
-
Chen T, Priambodo R, Huang R and Huang Y. The Effective Electrolytic Recovery of Dilute Copper from Industrial Wastewater. J. Waste. Mnt., 2013, 208-212.
-
Das N, Vimala R and Karthika P. Biosorption of heavy metals-An overview. Ind. J. Biotech., 2008, (7), 159-169.
-
Dermentzis K, Christoforidis A, Valsamidou E. Removal of nickel, copper, zinc and chromium from synthetic and industrial wastewater by electrocoagulation. Int. J. Environ. Sci., (1), 696-710.
-
Ehsani A, Yazici E Y, Deveci H. The influency of impurity ions on the electrowinning of copper from waste PCBs leaching solutions. Karadeniz Tech. Uni., 2012.
-
EPA Project summary Recovery of metals from wastewater and sludge, Sept.2004. EPA/600/S2-91/041.
-
Farooq U, Kozinski J A, Khan M, Athar M. Biosorption of heavy metal ions using wheat based biosorbents A review of the recent literature. J. Biores. Tech., 2010, (101), 5043-5053.
-
. Giannopoulou I, Panias D. Copper and nickel recovery from acidic polymetallic aqueous solutions . J. Min. Engg 2007, 20(8), 753-760.
-
Golder A K, Samanta A N, Ray S. Removal of trivalent chromium by electrocoagulation. J. Chem. Tech. and Biotech., 2007, (82), 496-503.
-
Jack F, Bostock J, Tito D, Harrison B and Brosnan J. Electrocoagulation for the removal of copper from distillery waste streams. J. Inst. Brew., 2013, (120), 60-64.
-
Lazaridou A, Dermentzis K, Christoforidis A, Valsamidou E, Kokkinos N. Removal of hexavalent chromium from electroplating Wastewater by electrocoagulation with iron electrodes. J. Glob. Nest., 2011, (13), 412-418.
-
Lee S, Jung C H, Chung H, Lee M Y and Yang J. Removal of heavy metals from aqueous solution by apple residues. J. Proc. Biochem. 1998, (33), 205- 211.
-
Mostaedi M T, Safdari, Moosavian A, Maragheh M G. Mass transfer coefficients in a hanson mixer-settler extraction column. Brazilian J. Chem. Engg., 2008, (25), 508-515.
-
Nassar N N. Rapid removal and recovery of Pb (II) from wastewater by magnetic nanoadsorbents. J. Haz. Mat. 2010, (184), 538-546.
-
Njenga T G, Home P G, Kinuthia T G, Kimutai, Mango H and Kaluli J W. Assessing the efficiency of subsurface constructed wetlands planted with different macrophytes in removing heavy metals from wastewater. Biochem. And Environ. Engg, 715-725.
-
Nouri J, Mahvi A H and Bazrafshan E. Application of electrocoagulation process in removal of zinc and copper from aqueous solutions by aluminum electrodes. Int. J. Environ. Res., 2010, 4(2), 201-208.
-
Pandharitande S L and Rohit P Kalnake. Tamarind fruit shell adsorbent synthesis, characterization and adsorption studies for removal of chromium and nickel from aqueous solution. Int. J. Engg. Sci. and emerging Tech., 2013, (4), 83-89.
-
Peng C S, Song S X and Juan A O Copper and Nickel Recovery from Electroplating Sludge by the Process of Acid-leaching and Electro-depositing. Int. J. Environ. Res., 2011, (5), 797-804.
-
Smith S R A critical review of the bioavailability and impacts of heavy metals on environment 2009, (35), 142-156.
-
Sorme L and Lagerkvist R, Sources of heavy metals in urban wastewater in Stockholm. Sci. Total Environ 2002, (298), 131-145.
-
Tarley C R T, Arruda M A Z. Biosorption of heavy metals using rice milling byproducts: characterization and application for removal of metals from aqueous effluents. Chemosphere 2004, (54), 987- 995.
-
Wolberg A, Roth F J. Copper oxide supported on alumina: III. X- ray Kabsorption edge studies of the Cu2+ species, J. Catalysis, 1996, (15), 250-255.
-
Yadav A K, Abbassi K , Kumar N , Satya S , Sreekrishnan T R , Mishra B K. The removal of heavy metals in wetland microcosms: Effects of bed depth, plant species, and metal mobility. J. Chem. Engg., 2012, (211212), 501-507.
-
Yasemin B, Zeki T. Removal of heavy metals from aqueous solution by sawdust adsorption. Journal of Environ. Sci. 2007, (19), 160-166.