
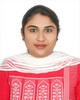
- Open Access
- Authors : Anusha T M , Sadashiv Avaradi , H S Jagadeesh
- Paper ID : IJERTV10IS090095
- Volume & Issue : Volume 10, Issue 09 (September 2021)
- Published (First Online): 28-09-2021
- ISSN (Online) : 2278-0181
- Publisher Name : IJERT
- License:
This work is licensed under a Creative Commons Attribution 4.0 International License
Effective Utilization of Reclaimed Asphalt Pavement by using Rejuvenator in Stone Mastic Asphalt For Binder Course
1
1
2 3
Anusha T M , Sadashiv Avaradi , and H S Jagadeesh
1Department of Civil Engineering, BMS College of Engineering, Bangalore, India 1Department of Civil Engineering, BMS College of Engineering, Bangalore, India 1Department of Civil Engineering, BMS College of Engineering, Bangalore, India
Abstract:- Road construction crossing the world created huge demand for construction materials. Natural aggregates is the prime material for the road construction use of aggregates leads to question about the preservation of natural resource. In other hand use of recycled pavement asphalt (RAP) as an alternative material in place natural aggregate which makes environmental friendly construction material. This research investigated the feasibility of using reclaimed asphalt pavement in stone mastic asphalt mix by modifying the binder with waste engine oil and elastomer modifier. RAP is replaced with aggregates at 10%, 20%, 30% & 40%. Further in order to increase the percentage of RAP in SMA mix waste engine oil is added to binder course i.e., RAP of 50%, 60% and 70%. The results indicated that 60% of RAP is found to be feasible through laboratory investigation for SMA mixes and 70% RAP is found to be feasible to use in SMA mix through laboratory investigation by modifying binder with waste engine oil.
Keywords: RAP, Bituminous mix, Waste Engine oil, Fatigue, Rutting.
INTRODUCTION
The India road network evolved tremendously in 5 decades to become the main transportation system in the country. India is the second largest country by area in terms of geographical area (32 million square km) and it takes fourth place in world in terms of motor vehicle (3.8 million). But it has very small paved roads with respect to overall area, which in turns leads to increase in transportation cost in the world market.
With more number of vehicles or traffic volume and load of vehicle on the pavement. It becomes very important to provide a pavement meeting the required standards. In order construct the road highly durable, safe, with good riding comfort. By using high-durable asphalt mixtures which will help in reducing the vehicle operation cost and maintenance cost (pavement service life). In developing countries above mention parameters becomes very important to use durable asphalt mixture in the surface layer, e.g., SMA (vale et al. 2006).
These SMA mixtures are gap graded mixes with high structural and functional performance. They are discontinuous gradations with higher coarse aggregates of about 70-80% by weight to give stone to stone contact (Skelton like structure) of high stability with high binder content of about 6-7% and air voids approximately 4%, it requires the addition of fibers of about 0.3% of weight of the mix to prevent the drain down through the air voids.
This research aims to determine the feasibility of using reclaimed asphalt pavement in SMA mix, due to more percentage of RAP materials available in the southern part of India. RAP material constitute the potential alternative material to natural aggregates. To evaluate the performance characteristics of SMA mix with elastomer modifier, following tests have been carried such as marshall stability, indirect tensile strength, rutting, fatigue, drain down and moisture susceptibility. The obtained test results are compared with conventional SMA mix, SMA mix with RSP and SMA mix with RAP and elastomer modifier.
BACKGROUND
Stone mastic asphalt (SMA) was first used by Germans in 1960s as a mix would resist the wear and tear of studded tyre. Main advantages of SMA were found to be improved low-temperature performance, highly rut resist, reduced noise of tires and increased service life (cooley and Hurley 2004). Due to its successful performance in Germany the mix started to use in different part of the world like USA, Spain, France and North America. SMA application has been carried mainly on the high-volume roads as a high resistance and high durable layer which helps in noise reduction and light reflection during rainy season.
A typical SMA mix consists 70% of coarse aggregates on or above 2.36mm sieve, filler in SMA is about 10% of weight of mix passing on 0.075mm sieve (Dong and Tan 2011).cellulose fibre of about 0.3% of weight is added to prevent drain down, if fibers are not added to the mix it will leads formation of fat patch on the pavement surface (Michael et al. 2003) stone on stone contact formed in the mix makes the more rut resist and highly durable mixture.
Stabilizer additive, Fibers are added due to high binder content, drain down of bitumen from SMA mix during production, transport and laying of the mix occurs. Hence, in order to prevent the drain down fibers are added which may be organic or inorganic or mineral materials. Fibers such as coconut coir, glass, minerals and cellulose fibers (only pelletized) can be utilized.(Neves Filho et al.2004). Addition of fibers should not exceed more than 0.3% by weight of the mix. Mix is designed as
per ASTM D 6390. Length of fiber is about 8mm, ash content is max 20% nonvolatile, oil absorption is 4 times more than the fiber weight and moisture content should be less than 5% then by weight of the fiber.
Many researchers have show that SMA mix design been developed by marshall mix design method (Muniandy and Huat 2006) by adopting marshall method of mix design performance results such as dynamic stability, fatigue life and water sensitivity of SMA mix is evaluated.
In the present research studies RAP is replaced with natural aggregated by adopting marshall mix design to evaluate the performance characteristics of SMA mix.
MATERIALS
Aggregates and Filler
In the present study for the design and production SMA mix, granite and dust of rock was used, with bag house dust as a filler. The natural aggregates were procured from KMS crusher-Bagalur, Karnataka India. Filler material used in the research is bag house. Which, is the final product obtained by washing stone dust during production of M-sand. Bag house for the research is provided by Sri venkateshwara crushes, Bangalore, Karnataka, India.
Fibers
Most commonly used fiber in SMA mix is cellulose which are physiologically and toxicologically safe, and they are purely natural cellulose resources (Bose et al. 2006). Small amount of about 0.3% is added to the mix to prevent drain down of asphalt and to increase stability and durability of the mix. Cellulose fiber used in the present research is provided by SMART Technology, Peenya, Bangalore, Karnataka, India. and Table 3 shows the properties of fiber which is used for the SMA mix.
Reclaimed Asphalt Pavement
Reclaimed asphalt pavement are the materials derived from reprocessed pavement which contains asphalt and aggregates. The derived materials are subjected to crushing and screening to obtain RAP of well graded aggregates coated with bitumen. Recycling of existing asphalt pavements allows the industry to produce new pavements with effective utilization of material and energy making it cost effective [7]. For this study, RAP is procured from Chittoor district where some part of Bengaluru- Tirupati Highway (NH-206) was scarified for construction of cement concrete pavement.
Bitumen (CRMB 55)
Binder content required for the SMA mix is higher when compared to other bituminous mixes. In this studies Crumb Rubber Modified Bitumen of grade 55 (CRMB-55) is used. CRMB was procured from the M D Constructions, Rajajinagar, Bengaluru. Procured itumen is tested for penetration, softening point, flash point, elastic recovery and results obtained should meet the required specifications as per IRC SP: 53:2010.
Table 1: Physical properties of natural aggregates and RAP aggregates
Properties |
Natural aggregates |
RAP aggregates |
Combined flakiness & Elongation indices, % |
11.19 |
16.83 |
Aggregate Impact value, % |
16.08 |
16.27 |
Los Angeles abrasion value, % |
17.52 |
19.84 |
Water absorption, % |
0.2 |
0.55 |
Specific gravity |
||
20 mm down |
2.68 |
2.62 |
12 mm down |
2.69 |
2.66 |
6 mm down |
2.71 |
2.69 |
Stone dust |
2.72 |
– |
Table 2: Properties of CRMB-55
Properties |
Result |
Test methods |
Penetration value at 25 C (mm) |
57 |
IS 1203-1978 |
Softening point (C) |
56 |
IS 1205-1978 |
Specific gravity |
1.03 |
IS 1202-1978 |
Flash Point (C) |
279 |
IS 1209-1978 |
Elastic Recovery in ductilometer at 15C, (%) |
68 |
– |
Thin Film Oven tests and test on residue: |
||
a) Percentage loss in mass |
0.115 |
IS 9382 |
b) Increase in softening point value, (C) |
4 |
IS 1205 |
c) Reduction in penetration of residue, at 25 C, (%) |
33 |
IS 1203 |
d) Elastic recovery in ductilometer at 25 C, (%) |
56 |
– |
Separation difference in softening point, max, (C) |
2.85 |
– |
Filler Material
In the present research work Baghouse dust is used as mineral filler in SMA mix. Baghouse mineral filler used for the study was obtained from S L V Crushers, Periyapatna, and Karnataka. The gradation is carried out as per MoRTH Table 500-36.
Table 3: Properties of filler
Sl.no |
Test |
Result |
1 |
Specific Gravity |
2.59 |
2 |
Fines by 75µ sieve |
90% |
Waste Engine Oil (WEO)
Reclaimed asphalt pavement (RAP) consists of aggregates coated with the bitumen content, the coated binder will be of aged one and its properties are not as good as original binder. The aged binder present in RAP will be lack in oily compounds and doesnt behave as fresh bitumen. In the present study Waste Engine Oil is used as a rejuvenators and which was procured from the motor cycle Garage Bengaluru.
MARSHALL MIX DESIGN
Once the gradation is fixed, Marshall Method is used to determine the OBC (optimum binder content) in SMA mix. The SMA mix will be designed using AASTHO MP8 standard specification for designing SMA and AASHTO PP41. For preparing Marshall Samples 50 blows are given on both side of the sample. The optimum binder content shall be determined by corresponding to the design air void content Va of 4.0% and minimum VMA of 17%. The minimum bitumen content for SMA mix is 6% by the weight of the mix. The results were tabulated in Table 4.
Table 4: Marshall test Results
Types of mixes |
OBC (%) |
Density (kg/m3) |
Stability (kN) |
Flow (mm) |
Airvoids (%) |
Voids in minral aggregates (%) |
Conventional SMA mix |
6.3 |
2450 |
11.108 |
3.187 |
4.1 |
17.64 |
SMA mix with 60%RAP replacement without WEO |
6.2 |
2430 |
12.65 |
3.8 |
3.99 |
17.38 |
SMA mix with 70%RAP and 25% WEO |
6.2 |
2430 |
13.01 |
3.14 |
3.99 |
18.27 |
MOISTURE SUSCEPTIBILITY AND INDIRECT TENSILE STRENGTH (ITS)
Moisture susceptibility is done in order to know the ability of SMA mix to resist the moisture damage. Around 6 samples were prepared, 3 samples were tested for conditioned and 3 were tested for controlled. The compaction of the specimen should be so, that it should have air voids 7±0.5%. Here controlled samples were subjected to freeze-thaw cycle. Then specimens are tested for ITS. The TSR (Tensile Strength Ratio) for SMA mix should be minimum 85% (IRC:SP:79-2008).
The Indirect Tensile Strength (ITS) test was conducted as per ASTM D4123. Here, the specimens were loaded diametrically and the load at failure was noted down. The failure load obtained from the test was used to fix the stress level in the repeated fatigue load test.
Tensile Strength of each specimen were calculated as.
St =
Where, St = tensile strength, P = maximum loads (N), t = specimen thickness (mm), d = specimen diameter (mm) Calculating the Tensile Strength Ratio (TSR) as follows,
TSR = S2/S1
Where, S1 = average tensile strength of controlled subset (kPa), S2 = average tensile strength of conditioned subset (kPa).
Table 5 Indirect tensile strength ratio
Types of mixes |
Moisture susceptibility (kPa) |
Tensile strength ratio (TSR %) |
|
Unconditioned |
Conditioned |
||
Conventional SMA mix |
340.66 |
312.86 |
91.84 |
SMA mix with 60%RAP replacement without WEO |
776.48 |
724.49 |
93.30 |
SMA mix with 70%RAP and 25% WEO |
388.42 |
377.65 |
97.23 |
REPEATED LOAD FATIGUE TEST
Pavement distress of flexible pavements due to repeated application of heavy wheel loads is one of the major pavement failures. It is necessary to find the fatigue behaviour of the bituminous mix under repeated dynamic load as in-situ. The diametrical dynamic loading fatigue test is an indirect tensile test on a cylindrical specimen in which a repeating compressive load is applied along the vertical diametrical plane in a half sine wave pattern. The test is conducted for conventional SMA mix, SMA mix with optimum RAP material content and SMA with RAP material and bitumen modifier at 10%, 20%, 30% and 40% of failure load which is obtained from ITS test. The apparatus is shown in below figure consist of LVDT (Linear variable differential transducer), loading piston, loading frame, position controller and data acquisition system with a loading rate capacity up to 5 tonnes. Load is applied over the specimen through two stainless steel plates using loading frame. When the specimen starts deforming, then horizontal and vertical deformation of the sample were measured using two sets of (i.e 4no) of LVDTs. The recording job of the applied load, deflection of both horizontal and vertical LVDT's for every cycle and the total number of repetitions before failure for each individual test was done by a data acquisition system. In the present study, the following test conditions were adopted such as loading frequency of 1 Hz (1 cycle per second),failure deformation of 5mm, pressure around 30-35 Pascals. The following expressions from Kennedy (1978), Gupta and Veeraragavan (2009) etc. were used for the computation of resilient modulus and initial tensile strain values from the experimental data.
Resilient poisson ratio is calculated using,
µr = 3.59*(Hr/Vr)-0.27
The resilient modulus is calculated using,
Mr = P*(0.27+ µr)/(Hr*h)
Initial tensile strain,
= i(1+3 µr)/ Mr
The maximum horizontal tensile stress is calculated using,
max = 2P/dt
Where, µr = Resilient Poisson ratio, Hr = average horizontal deformation in mm,
Vr = average vertical deformation in mm, Mr = Resilient Modulus of Elasticity (MPa), P = applied load in N, h = height of specimen in mm, d = diameter of specimen in mm, t = thickness of specimen in mm
14000
12000
10000
8000
6000
4000
2000
0
9764
Average number of cycles 12963 13131
Conventional mix
60% RAP replacement without WEO
70% RAP replacement
with 25% WEO
Conventional mix
60% RAP
replacement without WEO
70% RAP
replacement with 25% WEO
Fig 1 Fatigue test Results
Resistance to rutting
Immersion wheel tracking test is carried out to examine the permanent deformation characteristics of SMA mix. One of the main reasons for premature failure of pavement is rut formation due to movement of heavy traffic loads. Immersion wheel tracking machine consists of loaded wheel of 5.6 kg/cm2 pressure and confined mould of dimension 60*10*20 cm in which specimen was placed and it was confined from all sides. In immersion wheel tracking machine, wheel is made to move back and forth on the specimen at the rate of 25 passes per minute which exactly simulates the practical condition of vehicles movement on pavement. Specimens were subjected 10000 passes and rut depths at regular intervals were noted down. Graphs are plotted number of passes versus rut depth for 45 and 75mm thickness specimens and were shown below.
Rut Depth for 45 mm thickness specimans
Rut Depth for 45 mm thickness specimans
6.00
6.00
5.00
5.00
1.00
1.00
0.00
0
2000 4000 6000 8000 10000 12000
0.00
0
2000 4000 6000 8000 10000 12000
Number of Passes
Number of Passes
4.00
4.00
3.00
2.00
3.00
2.00
conventional SMA mix SMA+ RAP
SMA+RAP+WEO
conventional SMA mix SMA+ RAP
SMA+RAP+WEO
4.00
4.00
3.00
3.00
Rut Depth in mm
Rut Depth in mm
Rut Depth in mm
Rut Depth in mm
Fig 2 Rutting Characteristics for 45 mm thickness specimens
6.00
Rut depth for 75 mm thickness specimans
6.00
Rut depth for 75 mm thickness specimans
5.00
5.00
CONVENTIONAL SMA MIX
SMA+RAP
CONVENTIONAL SMA MIX
SMA+RAP
1.00
SMA+RAP+WEO
1.00
SMA+RAP+WEO
0.00
0.00
0
2000
4000
6000
Number Of Passes
8000
10000
12000
0
2000
4000
6000
Number Of Passes
8000
10000
12000
2.00
2.00
Fig 3 Rutting Characteristics for 75 mm thickness specimens
CONCLUSIONS
-
Laboratory tests have been carried out in order to determine the physical properties of natural aggregate, Crumb Rubber Modified Bitumen (CRMB), baghouse dust and the results obtained were found to be well within the specified limits as per MoRTH.
-
From the marshal stability test optimum binder content for conventional SMA mix is found to be 6.3%.
-
From marshal test results it is observed that optimum RAP replacement percentage for SMA mix with RAP and WEO (i.e. 70%) is high compared to SMA mix using RAP without waste engine oil (i.e. 60%) at OBC 6.2%.
-
Draindown test results obtained for conventional SMA mix, SMA mix using RAP without WEO, and SMA mix using RAP and WEO are found to be within the limit as per the MoRTH.
-
From the Moisture susceptibility test results it is found that SMA mix with 70% RAP and 25% WEO shows higher TSR values compared to conventional SMA mix and SMA mix with 60% RAP without adding waste engine oil.
-
From rutting test results it is observed that SMA mix using 70% RAP and 25% waste engine oil shows higher rut resisting property when compared to conventional SMA mix and SMA mix with 60% RAP without adding waste engine oil.
-
From the fatigue test results, it is observed that SMA mix with 70% of RAP and 25% of waste engine oil shows more fatigue life value when compared to conventional SMA mix and SMA mix with 60% RAP without waste engine oil.
-
From the cost analysis, it is observed that cost per cubic meter for SMA mix using RAP and WEO is less because of high percentage of RAP replacement when compared with conventional SMA mix and SMA mix with 60% RAP without waste engine oil.
-
Hence by using RAP as an alternative material along with rejuvenator makes the pavement sustainable, durable and economical.
-
REFERENCE
-
Al AI-Hadidy, Yi-qiu Tan (2011). Performance of the SMA mixes made with the various binders. Construction and Building Materials 25, 3668 3673.
-
Aline Colares do Vale, M.Sc.; Michéle Dal Toé Casagrande, Ph.D.; and Jorge Barbosa Soares,Ph.D (2014). Behavior of Natural Fiber in Stone Matrix Asphalt Mixtures Using Two Design Methods. Journal of Materials in Civil Engineering/Volume 26 Issue 3.
-
Baha Vural Kök and Mustafa Akpolat () Effects of Using Sasobit and SBS on the Engineering Properties of Bitumen and Stone Mastic Asphalt. Journal of Materialsin Civil Engineering/Volume 27 Issue 10.
-
Gholamali H Shafabakhsh, O Jafari An. (2015). Experimental investigation of effect of Nano TiO2/SiO2 modified bitumen on the rutting and fatigue performance of asphalt mixtures containing steel slag aggregates. Construction and Building Materials.
-
H.T. Tai Nguyen, T. Nhan Tran (2018). Effects of crumb rubber content and curing time on the properties of asphalt concrete and stone mastic asphalt using dry process. International Journal of Pavement Research and Technology 11, 236244.
-
IRC-SP-79(2008). TENTATIVE SPECIFICATIONS FOR STONE MASTIC ASPHALT.
-
J. RETTENMAIER & SOHNE (2014) Technical Manual for Laboratory Tests. Rosenberg. Business Unit Road Construction.
-
Lillian Gungat, Meor Othman Hamzah (). Green Road Construction Using Reclaimed Asphalt Pavement with Warm Mix Additive. international journal on advanced science engineering information technology vol. (8).
-
Mohd Rasdan Ibrahim, Herda Yati Katman, Mohamed Rehan Karim, Suhana Koting, and Nuha S.Mashaan, (2013). A Review on the Effect of Crumb Rubber Addition to the Rheology of Crumb Rubber Modified Bitumen. Hindawi Publishing Corporation Advances in Materials Science and Engineering Volume 2013.
-
Mario Manosalvas-Paredes, Juan Gallego, Leticia Saiz, José Ma Bermejo (2016). Rubber modified binders as an alternative to cellulose fiber SBS polymers in Stone Matrix Asphalt. Construction and Building Materials 121, 727732.
-
Mohammad Nasir Mohamad Taher and Mohamad Yusri Aman (2016). An Overview Of Reclaimed Asphalt Pavement (Rap) Materials in Warm Mix Asphalt Using Foaming Technology. ARPN Journal of Engineering and Applied Sciences VOL. 11, NO. 16.
-
MoRT&H (2013). Specifications for Roads and Bridge Works. Indian Road Congress, 5th Revision New Delhi, India.
-
Nurul Hidayah, Mohd Rosli, Norhidayah, Mohd Ezree (2016). A SHORT REVIEW OF WASTE OIL APPLICATION IN PAVEMENT MATERIALS. 4Faculty of Civil and Environmental Engineering, UniversitiTun Hussein Onn Malaysia,86400 Parit aja, BatuPahat, Johor, Malaysia.
-
Rouzbeh Ghabchi , Manik Barman , Dharamveer Singh , Musharraf Zaman , Muhammad Ali Mubaraki (2016). Comparison of laboratory performance of asphalt mixes containing different proportions of RAS and RAP. Construction and Building Materials 124, 343351.
-
S.K Khanna & C.E.G Justo (2000). Highway Engineering. Nem chand and Brothers publicatins.
-
S.K Khanna and C.E.G Justo(2000). Highway material testing laboratory manual. Nem Chnd & Bros, Roorkee, Fourth edition.
-
Schedule of rates, PW, P&IWTD, Bengaluru circle, Govrnment of Karnataka (2017-18).
-
Tao Ma, Hao Wang, Xiaoming Huang , Zilong Wang , Feipeng Xiao (2015). Laboratory performance characteristics of high modulus asphalt mixture With high-content RAP. Construction and Building Materials 101, 975982.
-
V. Sharma, and S. Goyal. (2015). Comparative study of performance of natural fibres and crumb rubber modified stone matrix asphalt mixtures. Civil Engineering Department, Thapar Institute of Engineering and Technology, Patiala, Punjab-147004, India.
-
Xiaoyang Jia, Ph.D.1; Baoshan Huang, Ph.D., P.E., M.ASCE2; Jason A. Moore3; and Sheng Zhao, Ph.D. (2015). Influence of Waste Engine Oil on Asphalt Mixtures Containing Reclaimed Asphalt Pavement. Journal of Materials in Civil Engineering.
-
Zeiaolhagh Kordi, Gholamali Shafabakhsh (2017). Evaluating mechanical properties of stone mastic asphalt modified with Nano Fe2O3. Construction and Building Materials 134, 530539.
-
IS 73 🙁 2013). Paving Bitumen-specification (Fourth Revision). B urea of Indian Standards.