
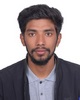
- Open Access
- Authors : Sagar Chhetri , Nirmal Prasad Baral , Baburam Bhandari , Kiran Neupane
- Paper ID : IJERTV10IS030087
- Volume & Issue : Volume 10, Issue 03 (March 2021)
- Published (First Online): 19-03-2021
- ISSN (Online) : 2278-0181
- Publisher Name : IJERT
- License:
This work is licensed under a Creative Commons Attribution 4.0 International License
Effect of Coarse Aggregate Size Variation on Compressive Strength of Concrete along the Length of Seti River
Sagar Chhetri
MSc. Student
(Infrastructure Engineering and, Management), Pashchimanchal Campus
IOE, Tribhuvan University, Pokhara, Nepal,
Kiran Neupane
MSc. Student (Geospatial Engineering) Pashchimanchal Campus IOE, Tribhuvan University,
Pokhara, Nepal,
Nirmal Prasad Baral Lecturer Pashchimanchal Campus
IOE, Tribhuvan University, Pokhara, Nepal,
Baburam Bhandari Lecturer Pashchimanchal Campus
IOE, Tribhuvan University, Pokhara, Nepal,
Abstract:- Coarse aggregate is major constituent of concrete impacting on strength, thermal & elastic properties, dimensional stability & volume stability. The aim of this study was to investigate the coarse aggregate size and source effect on the compressive strength of concrete. For this, four different sources were selected along the length of Seti river. Coarse aggregate from these sources were collected and sieved to obtain desired size of aggregate samples. Physical test i.e., specific gravity and water absorption of coarse aggregate obtained from these sources were determined. Mechanical test such as aggregate crushing strength test, impact value test & Los Angles test were performed. Result from the mechanical test showed that the aggregates from all the source are suitable construction material with slight variation in mechanical properties. Concrete cubes of M20 grade nominal mix by volume was casted by keeping cement, sand and water cement ratio constant for each source and coarse aggregate size as variable. As per the 7 days & 28 days compressive strength result, Hemja source showed relatively higher value of compressive strength compared to Ramghat, Kotre and Damauli sources. Five different batches were casted using aggregate size range 20mm-25mm, 16mm-20mm, 10mm-16mm, 10mm-25mm and 4.75mm-25mm for each source and cube made from well graded aggregate i.e., 4.75mm-25mm showed higher strength compared to others. In term of concrete cube failure mechanism, the major failure mechanism was initiated by bond failure for all the source.
Keywords Coarse Aggregate, Compressive Strength, Grading of Aggregate, Source, Size
-
INTRODUCTION
Cement, water, sand, aggregates and sometimes admixtures are the ingredients of concrete. The mixing of these materials in specified proportions produce concrete. The strength of concrete is influenced by ratio of cement to mixing water, ratio of cement to aggregate, the bond between the mortar & the coarse aggregate and size, grading, surface texture, shape, strength of aggregate particle (Haach et al.2011). Compressive strength defines the load carrying capacity of structure on its surface without any crack or deflection. Cube test provides an idea about all the characteristics of concrete. By this single test one can judge that whether concreting has been done properly or not. Concrete compressive strength for general construction varies from 15Mpa to 20Mpa & higher in commercial & industrial structures.
Aggregates are inert material that comprise two third portion of concrete. Depending upon the size of aggregate, it is classified as fine aggregate and coarse aggregate. Aggregate size less than 4.75mm are fine aggregate whereas greater than 4.75mm are coarse aggregate. The aggregate selection is considered as an important factor in the compressive strength of concrete. Therefore, it is important to evaluate the effect of aggregate size on the strength of concrete. Aggregate characteristics vary with the source from where the aggregate is obtained. Various size of aggregates is used in concreting. Usually, the aggregate in between 9.5mm to 37.5mm are used. The size above 20mm is used in mass concreting only. In context of Nepal, crusher aggregate of size in between 10mm to 20mm is mostly used in construction industry.
Coarse aggregate obtained from the 5 different source of Kathmandu valley were used for the preparation of cubes of 3 different grades of nominal mixes M1(1:2:4), M2(1:2:3) & M3(1:1.5:3) by weight. Water cement ratio, cement, sand & water were kept constant while coarse aggregate source was variable. Due to variation of source only, variation in 28 days target compressive strength is found up to 47%(Prajapati & Karanjit, 2019). Coarse aggregate of size 10mm, 14mm, 20mm & combined size of this three based on percentage proportion were used for the preparation of concrete cubes keeping w/c ratio, cement, sand constant. In combined size aggregate the percentage proportion of 20mm aggregate was constant i.e. 50% but that of 10 mm & 14mm size aggregate were varied. The result showed that the combined coarse aggregates which contained 30% 10mm, 20% 14mm & 50% 20mm had the highest compressive strength(Ramonu et al., 2018).
Three different batches using well graded, uniformly graded & gap graded aggregate for M20 garde of concrete were casted and result showed that gap graded aggregate have better performance than well graded and uniformly graded aggregate(Titiksh, 2017).The effect of aggregate size 9.5mm, 13.2mm, 19mm & control on compressive strength was studied. It was concluded that with the increase in aggregate size up to 19mm both concrete compressive strength and workability increased(Vilane, & Sabelo, 2016). The effect of aggregate size 6mm, 10mm, 12.5mm ,20mm & 25mm for two nominal mixes 1:2:4 & 1:3:6 on compressive strength were investigated. The result showed that the compressive strength increases with increasing aggregate size up to 12.5mm, while the concrete produced using 20mm had greater strength than those produced using 25mm aggregate(Moses, Olufunke, & Segun, 2018).
Seti river lies in western part of Nepal as a left tributary of the Trishuli river. It rises from the base of the Machhapuchhre and Annapurna massif, and flows south & south-east past Pokhara & Damauli to join the Trishuli river near Devghat. Its major tributary are mardi khola, kali khola, phedi khola, bijayapur khola, pudi khola, suraudi khola, bange khola & the largest tributary Madi. Pokhara, Lekhnath, Suklagandaki, Bhimad & Damauli are the cities though which seti river flows. Seti river is the main source of construction material in Gandaki zone. Source of the aggregate taken are from the Seti river at different places after it meet with stream as Pokhara valley is fully dependent on it for aggregate. Coarse aggregates are collected from Hemja, Ramghat, Kotre & Damauli. Aggregate properties depend on the minerals by which aggregate is made up of. Physical and mechanical properties of aggregate mainly determine the aggregate characteristics. As aggregate characteristics are directly related to the concrete performance, it is essential to evaluate those properties of coarse aggregate.
Generally, the concrete grade used in the structural components of residential buildings is M20 (1:1.5:3). As per the drawings approved from municipal and IS 456:2000, the grade of concrete used in structural member using reinforcement must not be below M20. So, the nominal mix used for the study is M20.
Fig. 1: Map Showing Hemja, Ramghat, Kotre, Damauli Source
-
MATERIALS and METHODS
-
Materials Required
The basic constituent of concrete are cement, coarse aggregate, fine aggregate and water. The ingredients of following properties were used to make the nominal mix of M20.
Cement: The fresh ordinary Portland Shivam cement of 43 grade available locally was used.
Fine Aggregate: Crusher run fine ggregate of Kotre source was used in this study.
Coarse Aggregate: In this study coarse aggregate was collected from the four different locations along the length of seti river as shown in table below.
Table 1:- Different Source and its Location
Source
Source Code
Coordinate in Google Map
Latitude
Longitude
Hemja
H
281728.9 N
835603.6 E
Ramghat
R
281247.0 N
835939.8 E
Kotre
K
280425.1 N
840403.9 E
Damauli
D
285759.1 N
841552.1 E
Thus, collected aggregate was sieved to obtain different sample of coarse aggregate. The aggregate fraction combination adopted for study is tabulated below.
Table 2: – Mix Proportion of Aggregate and its Representation
Aggregate Combination Code
Mixture Code as per Source
Percentage of Particular Size Aggregate
4.75-10mm
10-16mm
16-20mm
20-25mm
1
H1, R1, K1, D1
–
100%
–
–
2
H2, R2, K2, D2
–
–
100%
–
3
H3, R3, K3, D3
–
–
–
100%
4
H4, R4, K4, D4
–
33.33%
33.33%
33.33%
5
H5, R5, K5, D5
25%
25%
25%
25%
Fig. 2: Coarse Aggregate Sample Obtained after Sieving
Water: The portable fresh water available in the lab was used. The water cement ratio used was 0.5.
-
Test and Laboratory Procedure
The different physical & mechanical properties of coarse aggregate such as specific gravity, water absorption, aggregate crushing value, aggregate impact value & aggregate abrasion value were found out for the coarse aggregate obtained from the different
sources i.e. Hemja, Ramghat, Kotre, Damauli. These values helped to identify the strength and toughness of aggregate from different sources.
-
Specific Gravity and Water Absorption
The specific gravity and water absorption of aggregates are important properties that are required for the mix design. The specific gravity of an aggregate is the ratio of its mass to that equal volume of distilled water at specified temperature. For this, the sample of coarse aggregate was washed thoroughly to remove fines. Then the sample was placed in the vessel and filled with water and left for 24 hrs. This combination was weighted and noted as W1 grams. Now the sample was taken out and the vessel and water filled to previous level was weighted and noted as W2 grams. The sample taken from water was weighted in saturated surface dry condition and noted as W3 grams. Then the saturated and surface dry sample was oven died and weighted after 24hrs. noted as W4 grams. Similarly, the next sample was taken and repeat the above process. Finally, the water absorption and specific gravity were calculated as the average of two samples value using below formulas.
Specific Gravity = W4 / (W3-(W1-W2)) Apparent Specific Gravity = W4 / (W4-(W1-W2)) Water Absorption = (W3-W4)/W4 *100
-
Aggregate Crushing Test
The crushing strength of aggregate was calculated by adopting the procedures as standardized in IS:2386 part IV. In a cylindrical measure of 11.5 cm diameter & 18 cm height the dry aggregate passing through 12.5mm size sieve & retained in 10mm size sieve was filled in three layers. For measuring the resistance of aggregates to crushing under gradually applied load, the specimen was compressed by 40 tones gradually applied load at the rate of 4 tones per minute. Then crushed aggregate were sieved through 2.36mm sieve and weight of passing material (W2) was calculated. The ratio of weight of passing material (W2) to the weight of the total sample (W1) gave aggregate crushing value.
Aggregate Crushing Value =(W2/W1) *100
-
Abrasion Test
The hardness of the coarse aggregate was determined by Los Angeles abrasion test as per IS:2386 Part IV. The percentage of wear due to rotation of aggregate and steel balls in a drum helped to determine the Los Angeles Abrasion Value. As per the grading B, 11 number of abrasive spheres, 2.5 kg of aggregates passing from 20mm and retained in 12.5mm sieves and 2.5 kg of aggregates passing from 12.5mm and retained in 10mm sieves were kept in circular drum of internal diameter 700mm and length 520mm mounted on horizontal axis enabling it to be rotated. After the 500 revolutions, the material wass sieved through 1.7mm and the weight passing material (W2) was calculated. The ratio of weight of passing material (W2) to the weight of the total sample (W1) gave aggregate abrasion value.
Aggregate abrasion Value =(W2/W1) *100
-
Impact Value Test
The resistance to impact of aggregate was evaluated by impact value test. Aggregates passing 12.5mm sieve and retained on 10mm sieve was weighted and filled in cylindrical cup that was attached to metal base of impact testing machine. The material was filled in 3 layers by tamping each layer for 25 number of blows. Metal hammer of weight 13.5 to 14 kg was allowed to drop with a free fall of 38cm by vertical guides for 15 numbers of blows. The impact value was measured as percentage of passing 2.36mm sieve (W2) to the total weight of sample (W1).
Aggregate Impact Value =(W2/W1) *100
-
Compressive Strength Test
-
For cube test, cubical moulds of size 15cm x 15cm x 15cm are commonly used. In this research work mould of 15cm x 15cm x 15cm was used. 30 cubes for each source Hemja, Ramghat, Kotre and Damauli i.e. 6 for each aggregate sample were casted. The concrete of nominal mix M20 (1:1.5:3) by volume was prepared by hand mixing keeping coarse aggregate sample as variable while other ingredients cement, sand and w/c ratio as constant. The concrete was poured in the mould and tempered properly to avoid voids. After 24 hours these moulds were removed & test specimens were put in water for curing before one day of its testing.
The top surface of these specimens was made even & smooth by using cement paste & spreading smoothly on whole area of specimen. These specimens were tested by compression testing machine after 7& 28days. Load was applied gradually at the rate of 140 kg/cm2 per minute till the specimens fails. Load at the failure divided by area of specimen gave the compressive strength of concrete.
Fig. 3: Concrete Cube Under Compressive Strength Testing Machine
-
-
RESULTS AND DISCUSSIONS
Coarse aggregate from the four different source Hemja, Ramghat, Kotre and Damauli were collected and various tests were performed. The result obtained from the tests are tabulated below.
-
Physical Properties of coarse aggregate.
The physical properties of coarse aggregate i.e., specific gravity and water absorption capacity were performed as per the standard stated in IS: 2386 (Part III)-1963. The result showed that the coarse aggregate had relatively similar specific gravity but water absorption capacity goes on decreasing towards the downstream.
Table 3: Physical Properties of Aggregate
Source
Specific Gravity
Water Absorption
Hemja
2.7
0.68
Ramghat
2.69
0.6
Kotre
2.67
0.47
Damauli
2.66
0.42
The specific gravity of aggregate normally used in construction ranges from about 2.5 to 3.0 with an average value of about 2.68. Whereas water absorption value ranges from 0.1 to about 2% for aggregate generally used in construction.
-
Mechanical Properties of coarse aggregate.
16%
16%
18%
18%
14%
14%
10% 9%
10% 9%
Mechanical properties of coarse aggregate were evaluated by following IS: -2386 Part IV-1963 performing major three types of tests: Los Angeles Abrasion Test, Aggregate Impact Value Test and Aggregate Crushing Value Test. In this section, the test results obtained from the laboratory test were presented. Los Angeles Abrasion (LAAV) value for the hardness of aggregate, Aggregate Impact Value (AIV) for toughness of aggregate and Aggregate Crushing value (ACV) for Crushing Strength of aggregate is presented herein.
35%
30%
25%
20%
15%
10%
5%
0%
32% 30%
26% 24%
25%
23%
20%
35%
30%
25%
20%
15%
10%
5%
0%
32% 30%
26% 24%
25%
23%
20%
Hemja Ramghat Kotre Damauli
Hemja Ramghat Kotre Damauli
Hemja Ramghat Kotre
Damauli
Hemja Ramghat Kotre
Damauli
Los Angeles Abrasion Value Aggregate Impact Value 32% 16%
30% 14%
26% 10%
24% 9%
Los Angeles Abrasion Value Aggregate Impact Value 32% 16%
30% 14%
26% 10%
24% 9%
Aggregate Crushing Value 25%
23%
20%
18%
Aggregate Crushing Value 25%
23%
20%
18%
Fig. 4: Mechanical Properties of Coarse aggregate
The coarse aggregate of Hemja has the maximum Los Angeles Abrasion Value, Aggregate Impact Value and Aggregate Crushing Value of 32%, 16% and 25% respectively.
-
Compressive Strength Test
20
19
18
17
16
15
14
13
12
11
10
20
19
18
17
16
15
14
13
12
11
10
18.89
18.89
17.89
17.89
17.22
16.22
17.22
16.22
17.11
17.11
17.11
16.3
17.11
16.3
19.33
18
17
19.33
18
17
16.89
16.89
16.27
16.11
16.27
16.11
15.78
15.78
15.67
15.67
14.33
14.33
14.22
14.22
14.67
14.67
14
14
Compressive Strength N/mm2
Compressive Strength N/mm2
The nominal mix M20 was prepared from each type of aggregate size represented by numerical value 1,2,3,4&5 for uniform graded aggregate size in between 10mm-16mm, 16mm-20mm, 20mm-25mm and well graded aggregate size in between 10mm-25mm & 4.75mm-25mm respectively. IS: 516-1959 was followed to cast and test the concrete cubes prepared from above mentioned aggregate samples of Hemja (H), Ramghat(R), Kotre(K) and Damauli(D) sources. 7 days and 28 days compression test were carried by placing the cubes in compression testing machine and gradually applying the compressive load until failure. The result of compressive strength for each type of aggregate sample in shown in Fig.5 and Fig.6.
7 Days Compressive Strength
7 Days Compressive Strength
Ramghat(R)
Kotre(K)
Damauli(D)
Ramghat(R)
Kotre(K)
Damauli(D)
13
1
(10mm-16mm)
13
1
(10mm-16mm)
2
2
3
3
4
4
5
5
(16mm-20mm) (20mm-25mm) (10mm-25mm) (4.75mm-25mm) Size of Aggregate
Hemja(H)
(16mm-20mm) (20mm-25mm) (10mm-25mm) (4.75mm-25mm) Size of Aggregate
Hemja(H)
Fig.5: – 7 days compressive strength for different size and source of coarse aggregate
The line graph illustrates the 7 days compressive strength of cubes made using different size of coarse aggregate 1(10mm-16mm), 2(16mm-20mm), 3(20mm-25mm), 4(10mm-25mm) and 5(4.75mm-25mm) quarried from Hemja, Ramghat, Kotre and Damauli along the length of Seti river. The 7 days compressive strength of cube consisting well graded aggregate of 5(4.75mm-25mm) had relatively higher and that made up of 3(20mm-25mm) had relatively lower compressive strength for all the source. Hemja Source showed relatively higher where as Damauli Source showed relatively lower 7 days compressive strength for different size of aggregate samples.
28 Days Compressive Strength
28 Days Compressive Strength
31
29
27
28.44
27.56
31
29
27
28.44
27.56
3
4
5
3
4
5
(20mm-25mm) (10mm-25mm) (4.75mm-25mm) Size of Aggregate
Hemja(H)
(20mm-25mm) (10mm-25mm) (4.75mm-25mm) Size of Aggregate
Hemja(H)
26.33
26.33
27.56
26.67
27.56
26.67
25
25
25
23.78
25
23.78
25.67
25.67
21.89
21.89
21
21
21.44
21.44
24.33
23.33
22.44
24.33
23.33
22.44
24.56
22.78
21
24.56
22.78
21
25.33
25.33
24.22
24.22
23.89
23.89
23
23
20
20
19
17
15
19
17
15
1
(10mm-16mm)
1
(10mm-16mm)
2
(16mm-20mm)
2
(16mm-20mm)
Ramghat(R)
Ramghat(R)
Kotre(K)
Kotre(K)
Damauli(D)
Damauli(D)
Compressive Strength N/mm2
Compressive Strength N/mm2
Fig.6: – 28 days compressive strength for different size and source of coarse aggregate
The line graph illustrates the 28 days compressive strength of cubes made using different size of coarse aggregate 1(10mm-16mm), 2(16mm-20mm), 3(20mm-25mm), 4(10mm-25mm) and 5(4.75mm-25mm) quarried from Hemja, Ramghat, Kotre and Damauli along the length of Seti river. The 28 days compressive strength of cube consisting well graded aggregate of 5(4.75mm-25mm) had relatively higher and that made up of 3(20mm-25mm) had relatively lower compressive strength for all the source. Hemja Source showed relatively higher where as Damauli Source showed relatively lower 28 days compressive strength for different size of aggregate samples.
-
Statistical Analysis for coarse aggregate size with 28 days compressive strength
From the 7 days and 28 days compressive strength test it was found that the Hemja source gave the highest compressive strength. So, for Hemja source single factor or one-way ANNOVA tool was used to test the null hypothesis that coarse aggregate size variation doesnt show effect on the compressive strength of M20 nominal mix. Here, the null hypothesis is rejected as F critical value 3.47 is less the F calculated value 4.5 as shown in table below. Hence, it can be stated that coarse aggregate size causes significant variation in 28 days compressive strength.
Table 4: One Way ANOVA for Coarse Aggregate Size of Hemja Source with 28 days compressive strength
ANOVA: Single Factor
H1
H3
H2
H4
H5
24.33
24
25
26.33
26.89
25.67
24.67
26
26.67
30.11
25
25
28
29.67
28.33
SUMMARY
Groups
Count
Sum
Average
Variance
H1
3
75
25
0.4489
H3
3
73.67
24.55667
0.259633
H2
3
79
26.33333
2.333333
H4
3
82.67
27.55667
3.378533
H5
3
85.33
28.44333
2.601733
ANOVA
Source of Variation
SS
df
MS
F
P-value
F crit
Between Groups
32.61897
4
8.154743
4.519299
0.02418
3.47805
Within Groups
18.04427
10
1.804427
Total
50.66324
14
-
Statistical Analysis for coarse aggregate source with 28 days compressive strength
From the 7 days and 28 days compressive strength test it was found that the well graded aggregate of size in between 4.75mm- 25mm containing equal volume of aggregate of size in between 4.75mm-10mm, 10mm-16mm, 16mm-20mm & 20mm-25mm gave the highest compressive strength. So, for well graded aggregate of size in between 4.75mm-25mm single factor or one-way ANOVA tool was used to test the null hypothesis that variation in coarse aggregate source doesnt show effect in 28 days compressive strength of concrete. Here, the null hypothesis is rejected as F critical value 4.06 is less than F calculated value 4.98 as shown in table below. Hence, it can be stated that coarse aggregate size causes significant variation in 28 days compressive strength.
Table 5: One Way ANOVA for Coarse Aggregate Source with 28 days compressive strength
ANOVA Single Factor
H5
R5
K5
D5
26.56
25.33
26.67
24.33
30.11
26
27.33
25.67
28.33
25.67
28.67
26
SUMMARY
Groups
Count
Sum
Average
Variance
H5
3
85
28.33333
3.150633
R5
3
77
25.66667
0.112233
K5
3
82.67
27.55667
1.038533
D5
3
76
25.33333
0.782233
ANOVA
Source of Variation
SS
df
MS
F
P-value
F crit
Between Groups
19.00556
3
6.335186
4.98477
0.030811
4.066181
Within Groups
10.16727
8
1.270908
Total
29.17283
11
-
-
CONCLUSIONS
In the present study, the physical and mechanical properties of coarse aggregate at different location of seti river was found out. The 7 days and 28 days compressive strength of cubes made from 5 different aggregate samples from each source were determined.
-
The mechanical properties of coarse aggregate of Seti river decreases from upstream to downstream as gravel carried by action of flowing water encounters different geological boundaries causing its surface wear and tear and making it harder and smoother.
-
As per the 7-days & 28-days compressive strength test result, Hemja source gave relatively higher compressive strength to other source. The coarse aggregate found on the Hemja Source had rough surface where as other source has smooth surface. A smooth surface can improve workability, yet a rougher surface generates a stronger bond between the paste & the aggregate creating a higher strength.
-
From the 7 days and 28 days compressive strength result for different aggregate sizes, the well graded aggregate of size in between 4.75mm-25mm i.e., containing equal volume of aggregate of size in between 4.75mm-10mm, 10mm-16m, 16mm-20mm & 20mm-25mm gave higher compressive strength for both 7 days and 28 days than other size of aggregate. By having aggregate of various size air voids between the materials are filled with particles maintaining grain to grain contact resulting densely packet concrete cube with higher compressive strength.
-
Coarse aggregate size and source has significant effect on the compressive strength of concrete based on the 7 days and 28 days compressive strength test result that is also verified by statistical test result.
REFERENCES
-
Guades, E. J. (2019), Effect of coarse aggregate size on the compressive behaviour of geopolymer concrete, European Journal of Environmental and Civil Engineering, 23(6), 693709.
-
Moses, O., Olufunke, A., & Segun, E. (2018), Effects of Coarse Aggregate Size on the Compressive Strength of Concrete, Civil Engineering Journal, 4(4), 836842.
-
Paultre, A. L. (2003), Effect of aggregate type and content on concrete strength & fracture, University of Kansas Center for Research, 45(10), 7.
-
Prajapati, J., & Karanjit, S. (2019), Effect of Coarse Aggregate Sources on the Compressive Strength of Various Grade of Nominal Mixed Concrete, Journal of Science and Engineering, 7(November), 52-60.
-
Ramonu, John, A. L., Ilevbaoje, J. O., Olaonipekun, O. A., Modupe Abayomi, E., & Saleh, J. Y. (2018), Comparative analysis of the combination of coarse aggregate size fractions on the compressive strength of concrete, International Journal of Civil Engineering and Technology, 9(11), 14471457.
-
Roy, B., Vilane, T., & Sabelo, N. (2016), The Effect of Aggregate Size on the Compressive Strength of Concrete, Journal of Agricultural Science and Engineering, 2(6), 6669.
-
Titiksh, A. (2017), Gap Grading of Aggregates & Its Effect on the Inherent Properties of Concrete, International Journal of Advance Engineering and Research Development, 4(03), 1-8.
-
Valdimir G.Haach, Graca Vasconelos & Paulo B.Lourenco (2011), "Influence of Aggregate Grading & Water/Cement ratio in Workability & Hardened Properties of Concrete", Construction & Building Materials,25, 2980-2982.
-
Woode, A., & Ballow, P. (2015), The Effect of Maximum Coarse Aggregate Size on the Compressive Strength of Concrete Produced in Ghana, Civil and Environmental Research, 7(5), 713.