
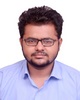
- Open Access
- Authors : Pawan Kumar Singh , Sweekriti Shukla , Kumar Mayank , Akash Singh, Shrikant Vidya
- Paper ID : IJERTV9IS040196
- Volume & Issue : Volume 09, Issue 04 (April 2020)
- Published (First Online): 02-05-2020
- ISSN (Online) : 2278-0181
- Publisher Name : IJERT
- License:
This work is licensed under a Creative Commons Attribution 4.0 International License
Development of Smart Vehicle with Counterbalance Controlling System
Pawan Kumar Singh, Sweekriti Shukla, Akash Singh, Kumar Mayank, Shrikant Vidya
School of Mechanical Engineering, Galgotias University Gr. Noida, India
Abstract Vehicles Are more intended to Rollovers to Various extents. Generally, Rollover Tendency Increases with following factors
-
Height of The Center of Mass
-
Narrowness of The Axle Track
-
Steering Sensitivity
-
Increased Speed
Rollovers Usually Occur in One Of The Two Ways, Namely Tripped and Untripped. Tripped rollovers are caused by forces from an external object, such as a curb or a collision with another vehicle On the Contrary, An Untripped Rollover occurs Due to High Lateral Acceleration in a Sharp Turn and Not occurs Due to External Tripping.
KeywordsRollover; controlling system; balancing; weight displacement.
-
INTRODUCTION.
-
In India, total deaths in road accident is 1,50,000 every year which means 400 accidents every day. In 2018, Road Accidents Led To 3 Deaths Per Day. Further If You Categorize These Accidents Based on The Vehicles, Then Four Wheelers Accounted for The Most Terrific Accidents. Most of These Accidents Are Rollover Type. In This Type of Accidents, A Vehicle Jumps Over onto Its Side or Roof. Various Types of Actuation Systems Can Be Used for Prevention of Rollover. The Differential Braking System Has Received Most Attention from Researches. It Is Used to Prevent Rollover by Reducing Yaw Rate and Speed of The Vehicle. Also, Steer by Wire Systems and Active Suspensions Can Be Used for Prevention of Rollovers. But These Systems Are Only Developed for Untripped Rollovers Cannot Be Used for Preventing Tripped Rollovers. So, We Are Doing This Project with A View to Prevent Accidents Caused Due to Tripped Rollover.
-
-
LITRATURE REVIEW
There were many researchers conducted researches on rollover accidents and their prevention some of which are:
-
This paper investigates about a system includes a set of tire pressure sensors for tire of vehicles a control module and a user interface. [horst theuss, et all (2015)].
-
This paper investigates that about vehicle dynamics and a control design to improve stability and minimise the rollover risk of the vehicle in critical situations.in this paper changes in roll lateral forces and roll angle is considered. [Hamid dhamani, et all (2013)].
-
The paper investigates about accident control system and number of accidents in India to not using safety precautions in this paper they discuss about how to find out the solution to overcome this problem. [ ugale v.j, et all (2017)].
-
-
COMPONENTS
-
MECHANICAL COMPONENTS
-
Dc gear motor.
-
Pulley / sliding mechanism
-
Counter weight
-
4 wheels
-
8mm wheel rode
-
Hinges
-
Iron body frame
-
-
ELECTRONIC COMPONENTS
-
Accelerometer
-
controller
-
Led
-
Relay
-
Regulator
-
Wire
-
Switch
-
Pcb
-
-
ACCELEROMETER
The accelerometer which we are using is Small, Low Power, 3-Axis ±3 g Accelerometer. The accelerometer is a small, thin, low power and using three axis accelerometer with signal attempting to find voltage outputs. The accelerometer measures acceleration with a minimum range of ±3 g. the accelerometer can capable of measuring the static acceleration of gravity in tilt-sensing applications, shock or vibration, and dynamic acceleration which is from motion. the features of the accelerometer we are using is 3-axis sensing, Low power: 350 A (typical), Single-supply operation: 1.8 V to 3.6 V,10,000g shock survival, excellent temperature stability.
Fig 1: Accelerometer
-
CONTROLLER
we are using high performance, low power 8-bit microcontroller. It works on 8 bits at a time and suitable for low power and less compute intensive application. The specifications of this controller are as follows: –
512 bytes EEPROM, it has 1k byte internal SRAM, it can operate up to 16MIPS throughout 16MHz.it has
132 powerful instructions with a 32*8 common purpose registers with fully static operations.it has also 8k bytes self-programmable memory. If we execute powerful instructions in a single cycle, this controller achieves 1MIPS/MHz by allowing the whole system designer to control or optimize power consumption vs processing speed.
Fig 2: Controller
-
RELAY
Relay is essential to isolate one circuit electrically from another circuit, but it allows to first circuit to control another circuit. For Example, if I want to control high volt circuit from my device so I do not connect directly to low voltage port in my device because if something bad happens mains connection could destroy my costlier parts inside my device, so to avoid this wrong happening we can provide electrical isolation between two circuits by adding relay between those circuits, here is circuit diagram of isolation between two circuits.
Fig 3: relay barrier
-
-
METHODOLOGY
This is quite simple concept. we plane to implement our idea on nonmoving dummy vehicle which is suspend hang on iron
frame with help of hinges and hollow pipe frame washer. Now we construct a sliding mechanism on vehicle body frame, which provide X plus and minus sliding rotation. This sliding rotation is providing by worm gear dc motor (In reality we will use double X and Y sliding mechanism which control two dc motors). After that we place a heavy mass (iron cubes) on that sliding mechanism, this sliding mechanism is placed on Centre of vehicle body frame, whenever vehicle is in high speed turning or rollover condition, this iron mass slide on opposite side to mention counter balancing. All this mechanical movement is control by simple electronic circuit. This turning or rollover movement is sense by accelerometer sensor. This accelerometer sensor always senses vehicle ground surface position. If vehicle face high speed imbalance or rollover accident condition sensor immediately inform to controlling unit and controlling unit immediately shift mass to opposite side to stop rollover vehicle to adjust counter weight balancing. This action can reduce rollover accidents.
fig 4: Side Look of Our Dummy Vehicle
-
DESIGN
The Model was designed using the 3D modelling software SOLIDWORKS.
Fig. 5 front and top view
-
CONCLUSION
Our system is combination of both electrical and mechanical components that will sense and give real time data of turnover and rollover of vehicle This counterbalance system can be used to reduce and prevent the rollover accidents in real vehicle, this idea can be used in realistic vehicle that can cause the minimum destruction of real vehicle so called passengers in that vehicle our system sense and take necessary steps to control the balance of the vehicle.
-
REFERENCES
-
-
Gridsada Phanomchoeng and Rajesh Raja Mani (December 2012). "Prediction and Prevention of Tripped Rollovers". Department of Mechanical Engineering, University of Minnesota.
-
B. Winkler and R. D. Ervin (2016). "Rollover of Heavy Commercial Vehicles" (PDF). The University of Michigan Transportation Research Institute.
-
Race Descriptions: Rollover Contest". Evergreen Speedway.
"2018 Tesl Model S 5 HB RWD" National Highway Traffic Safety Administration.
-
website: www.googlescholar.com
-
Theory of machine (ss rattan).