
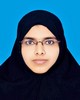
- Open Access
- Authors : Aziya Umaruddin , Aliya A , Ajmiya S , Ajmal Mohammed S , Rajula I
- Paper ID : IJERTV11IS080144
- Volume & Issue : Volume 11, Issue 08 (August 2022)
- Published (First Online): 05-09-2022
- ISSN (Online) : 2278-0181
- Publisher Name : IJERT
- License:
This work is licensed under a Creative Commons Attribution 4.0 International License
Development of Geopolymer Brick using Laterite Soil and Ceramic Dust
Ajmal Muhammed1, Ajmiya S1, Aliya A1, Aziya Umaruddin1, Rajula I2
1Students, Department of Civil Engineering MES Institute of Technology & Management, Chathannoor, Kollam, Kerala, India
²Assistant professor , Department of Civil Engineering MES Institute of Technology & Management, Chathannoor, Kollam, Kerala, India
Abstract Geopolymer bricks are the new innovation in the field of brick industry. Geopolymer bricks contain fly ash as the source material and an alkaline activator for the activation of polymerization reaction. The results revealed that clay- based geopolymer bricks can reduce CO2 emissions by up to 55% compared to fired bricks and provide the required mechanical strength for structural works. Furthermore, geo polymers based on waste bricks reduce up to 29.5% of CO2 emissions with twice compressive strength as fired bricks. This paper offers a review on production of geopolymer bricks incorporating ceramic dust and small amounts of laterite soil. In Geopolymer bricks, main ingredients of brick will be totally replaced by the waste coming out from Thermal power plants, waste of burnt coal known as fly ash, ceramic dust, produced as waste from ceramic bricks, roof and floor tiles and stoneware waste industries and naturally occurring laterite soil. Materials rich in (Si) silica and (Al) alumina are the requirements for the geo polymer synthesis. The activator used is sodium hydroxide (Na OH) with Sodium silicate (Na2SiO3) solution. The main advantages of using these materials are good compressive strength and durable bricks. The effective utilization of industrial wastes like fly ash and GGBS helps in reducing the hazardous waste and makes the brick environment eco friendly. The study will be carried out on (200* 100* 100) mm size of geopolymer brick with 100% replacement of sand in bricks using ceramic dust and clay mixed with laterite soil
Keywords :- Laterite soil,ceramic dust,fly ash,compressive strength
-
INTRODUCTION
An increasing environmental issue has forced industries to develop materials that are more environmentally friendly and leads to zero impact environment eco-friendly construction. The material from natural resources and industrial waste by products are very important. This review focuses more on bricks, one of the most required materials for construction. Current demand is over 1000 billion bricks a year. The common practice of firing clay bricks in kilns large quantities of coal and fuels were consumed. The Indian brick industry, which is the second largest producer in the world consumes more than 150 million tons of coal annually without counting the electricity used in brick production , the diesel for transporting the bricks alone produces roughly one-third of the total CO2 emissions of the global airline industry (550 million tons of CO2) . In the 1970s, Davidovich started the discovery and show of the research in geopolymer binders. Geo polymers are a type of materials formed by the polymer synthesis of silicon (Si) and aluminum (Al) which are ingredients of coal waste known as fly ash… Geo polymers are chain structures formed on a keystone of Al and Si ions. This technology is considered as
new technology, but it has ancient roots and has been used as the building material in the erection of pyramids in ancient times. Geo polymer binder can be used in applications to fully or partially replace OPC in cement based fly ash bricks with environmental and technical benefits, including an 80 – 90% reduction in CO2 emissions. Brick is the most commonly used building material in India for more than 1000 years. But nowadays fly ash bricks have been tremendously being used due to the reduction in cost as well as its lightweight. Geopolymer bricks are the latest innovation in the brick industry which consist of supplementary cementitious materials such as fly ash and GGBS activated by an alkaline activator. The application of geopolymer technology gained importance due to the reduction of the CO2 emissions by utilizing the Supplementary cementitious materials. The geopolymer bricks using ceramic dust waste acquire high compressive strength. Along with ceramic dust, laterite soil is also used. Laterite soil layers rich in iron oxide and derived from a wide variety of rocks weathering under strongly oxidizing and leaching conditions. They found that there was substantial reduction in the strength of the geopolymer bricks immersed in pH=4 and seven solutions. The development of geopolymer bricks using industrial wastes and reported that the variation in the source materials can significantly affect the physical, chemical and mechanical properties of alkali-activated bricks. In this research work, we aimed at developing geopolymer bricks and studying its properties such as compressive strength, water absorption and acid resistance test.
A. Significance of study
To enhance the properties like compressive strength, water absorption and also study the properties of geopolymer brick with ceramic dust and laterite soil. To determine the Engineering property of ceramic dust and laterite soil based Geopolymer brick with conventional geopolymer brick.
-
MATERIALS
-
Fly Ash
Fly Ash is a composition of silica and alumina material. The major constituents of fly ashes are Silicon dioxide (Si02), aluminum oxide (Al203), ferric oxide (Fe203) and calcium oxide (Coo). Other minor constituents are MgO, Na2O, K2O, SO3, MnO, TiO2 and unburnt carbon. The variation in main constituents – Silica (25- 60%) and Alumina (10- 30%).When the sum of these principal constituents is 70% or more and reactive calcium oxide is less than 10% technically the fly ash is named as class F fly ash. Class F
Fly ash (FA) was being used in this study. Specific gravity of fly ash (FA) is 2.7
Fig 2.1 Fly ash
-
Ground granulated blast furnace(GGBS)
GGBS was observed in the form of powder from iron wastes. This may cause environmental problems and making disposal problems at the disposal sites, this has been changed into a useful resource and used for making bricks. The cost and other properties of the bricks are equalized to the normal bricks. GGBS was being used in this study. Specific gravity of GGBS is 2.7.
Fig 2.2 GGBS
-
Ceramic dust
Ceramic dust is produced as waste from ceramic bricks, roof and floor tiles and stoneware waste industries. The specific gravity of tile dust is found to be 3.02 and the fineness is found to be 92.50%.
-
Laterite soil
Laterite soil layer that is rich in iron oxide and derived from a wide variety of rocks weathering under strongly oxidizing and leaching conditions. It forms in tropical and subtropical regions where the climate is humid. By testing, the specific gravity of laterite soil is 2.7.
E.Alkaline activator solution
The alkaline solution used was a combination of sodium silicate solution (SSS) and sodium hydroxide solution (SHS). The sodium silicate solution hasNa2O=13.7%, SiO2=29.4%, and water=55.9%by mass. The sodium hydroxide solution was prepared by dissolving pellets in water. The SSS and SHS were mixed together one day prior to the actual day of mixing.
F. Clay
Clay soil has very fine mineral particles and not much organic materials. It develops plasticity when in wet conditions. Clay minerals are composed of silica, alumina, magnesia or both and water. Clay is a soft, loose, earthy material containing particles with a grain size of less than 4 micrometers (m). It forms as a result of the weathering and eroson of rocks containing the mineral group feldspar (known as the 'mother of clay') over vast spans of time.
-
-
EXPERIMENTAL PROCEDURE
There are four steps involved in the brick manufacturing process. They are preparation of materials for the production of bricks, moulding of bricks, drying of bricks, burning of the bricks.
At first the clay mixed with laterite soil is excavated and then laid on a leveled ground. This weathered soil is then mixed with different proportions of fly ash and GGBS. This mix is thoroughly mixed to prepare a good brick earth. Small amount of water is sprinkled to make the mix tempered. The prepared mix is put into the rotary part of the machine for fine blending. Along with blending the alkaline activator solution is also added.
In plastic clay machines the clay in plastic state is forced to rectangular openings of a size equal to length and breadth of a brick and is then cut into strips of thickness of brick with wires in frame. In dry clay machines, dry clay is reduced to powder, filled dry into mould by machine and then subjected to high pressure to form hard and well-shaped bricks drying is usually done in placing the bricks in the shed with open sides so as to ensure free circulation of air the drying period is usually 7 to 14 days. Burning is the most important step in the manufacture of brick. Kilns are permanent structures consisting of many chambers. There are intermittent and continuous kilns. Moulded clay is stacked in the champers and they are slowly dried and burned to high temperature and cooled.
-
Methodology
-
Materials collection
-
Materials testing
-
Mix design
-
Brick making
-
Tests to determine the properties of bricks
-
Analysis of results
-
-
Material Testing Laterite soil
-
Specific gravity test
Specific gravity is the ratio of the density of a substance to the density of a reference substance equivalently, it is the mass of the substance to the mass of the reference substance for the same given volume .The specific gravity of laterite soil passing through 4.75 mm IS sieve is found out by pycnometer. First step is to wash, dry and weigh the pycnometer (w1).Then place about 200-400g of dry sample in pycnometer .Weigh the bottle with dry sludge(w2).Add sufficient amount of water to cover the dry soil, and mix thoroughly with glass rod and add more water and stir it. Fill the bottle
with water with up to the calibration mark. Then clean the exterior surfaces of bottle pycnometer with dry cloth and weigh the bottle with contents(w3).Empty the bottle and clean it and fill it with distilled water up to the hole of the conical cap and record its weight(w4) and then conduct the test times.
Determination no.
1
2
3
w1 g
0.662g
0.662g
0.662g
w2 g
1.092g
1.092g
1.092g
w3 g
1.726g
1.726g
1.726g
w4 g
1.450g
1.450g
1.450g
Specific gravity ,G
2.7
Table 3.1 specific gravity test
SPG = (w2 -w1) / (w2-w1)-(w3-w4)
= 2.7
The specific gravity of the soil particles lie within the range of 2.65 to 2.85. Soils containing organic matter and porous particles may have specific gravity values below 2.0. Soils having heavy substances may have values above 3.0.Hence it is found to be consistent in the range of 2.65-2.85.
-
Sieve analysis
A sieve analysis is a practice or procedure used to assess the particle size distribution of granular particles. The size distribution is often of critical importance to the way the material performs in use. The mass of the sample required for each test depends on the maximum size of material. Clean the sieve to be used and record the weight of each sieve and the pan .Arrange the sieves to have the largest mesh sire at the top of the stack. Pour carefully the soil sample into the top sieve and place the lid over it. Place the sieve stack on the mechanical shaker, screw down the lid, and vibrate the sample for 10min.Remove the stack and re-weigh each sieve and the bottom pan with the soil sample fraction retained on it.Initial mass of soil sample taken for analysis (kg) = 1.000kg
Sieve no.
Weight of sample retained(g)
%
retained
Cumulative% retained
%finer
4.75mm
12
1
1
99
2 mm
248
24.8
25.8
74.5
1 mm
248
24.8
50.6
49.9
600
microns
120
13.2
63.8
37.2
300
microns
190
18.2
82
18
150
microns
160
15.6
97.6
2.4
75
microns
22
2.4
100
0
Table 3.2 sieve analysis
Fig.3.1
The results obtained are as follows: Effective size = 0.229 Uniformity coefficient = 7.22
Coefficient of curvature = 1.69 Percentage of gravel = 100- 99 = 1% Percentage of silt and clay = 0%
According to IS specification for well graded soil uniformity coefficient should be more than 4 and coefficient of curvature should be between 1 & 3
-
Hydrometer analysis
In the wet mechanical analysis or sedimentation analysis, soil fraction finer than 75 microns size is kept in suspension in liquid medium. The method for determining grain size distribution of such soils are based on Stokes law.It defines the rate of free fall of the sphere through liquid.
Fig.3.2 Hydrometer
Dry weight of particles put in 1000 ml suspension =50g
Volume of hydrometer (cc) = 79.4c3 Test temperature = 31 degree Celsius
Cross section area of sedimentation jar= 29.412c2
Viscosity at test temperature = 7.205 × 105/c2
Composite correction, c =3
Specific gravity of soil, G =2.65 Area x height= volume
A = V/HT =100/3.4 = 29.412c2
He = 11cm t = 2 min = 120s
= 7.805 × 105/cm2
G= 2.65
D mm = 1200he/((G1) t) = 0.0223 mm
R =24.67 cm
WD =50 g
G =2.65
N= (GR×100)/ (d (G1)) =79.24%
% of silt (0.075-0.002) = 41%
% of clay (< 0.002mm) =37%
-
Liquid limit
Liquid limit is the water content on which the soil starts to behave as a liquid. About 200g of fine grained soil sample was taken and some amount of water was added to the soil sample and thoroughly mixed the soil using a spatula and uniform paste was obtained. Then the paste was applied on the brass cap of Casagrande apparatus and leveled with a spatula and depth of layer at the center was 1cm .Groove was cut by using a Casagrande grooving tool. Handle of the apparatus was rotated at a rate of two revolutions per seconds and the groove was closed. Collect a representative specimen of the soil from the center of the soil paste for water content determination. The no. of blows is noted. Some amount of water was added to the paste and the procedure was repeated till the no. of blows in the range of 30-63 is obtained. A graph was plotted between no. of blows on X axis and moisture content on Y axis on a semi log sheet. From the graph, moisture content corresponding to 25 blows was obtained as liquid limit.
OBSERVATIONS AND CALCULATONS
SPG= 2.78
The specific gravity is found to be 2.78 which is in the range of inorganic clay classification (2.70-2.80).
Fly ash
1. Specific gravity
Only kerosene which is free of water shall be used. At time of weighing, the temperature of the apparatus will not be allowed to exceed the specified temperature. All air bubbles can be eliminated in filling the apparatus and inserting the stopper.
Weighing shall be done quickly after filling the apparatus and shall be accurate to 0.1mg…Precaution shall be taken to prevent expansion and overflow of contents resulting from heat of hand when wiping the surface of the apparatus.
Weight of specific gravity bottle, W1 = 226g Weight of bottle + fly ash, W2 = 283 g
Weight of bottle + fly ash + kerosene, W3 =470g Weight of bottle + kerosene, W4 = 439 g
SPG = 2.19
The specific gravity is found out to be 2.2.
-
-
MIX DESIGN
The mix design for the present study was taken from literature review. The details of materials are given below in table 3.4.
Sample number
1
2
3
4
Number of blows
15
18
27
32
50
50
50
50
65.1
68.6
73.8
72.4
58.9
61.3
65.2
65.0
6.2
7.3
8.6
7.4
15.1
18.6
23.8
22.4
41.1
39.2
36.1
33.0
Table 3.4 mix design
% of clay + laterite soil
GGBS (%)
Fly ash (%)
Ceramic dust (%)
50
10
25
40
50
20
20
60
50
30
15
80
Fig.3.3
Liquid limit from graph, LL=36%
Clay
1. Specific gravity
Determination no.
1
2
3
w1 g
679
679
679
w2 g
854
858
880
w3 g
1602
1600
1598
w4 g
1488
1490
1486
Specific gravity ,G
2.87
2.59
2.89
Table 3.3 specific gravity test
-
BRICK MANUFACTURING
The first step involved in brick manufacturing is the mixing of raw materials used in brick making. The raw materials are fly ash ,ground granulated blast furnace slag, laterite soil
,ceramic dust and clay .and adding premixed alkaline activator solution to enhance the polymerization reaction and sufficient amount of water is sprinkled over the mixture to attain plasticity .After this brick is made to its shape and size by using mouldings .Then dry the brick in air for about 24 hours and for about 1 week the brick should be dried in presence of sunlight .After drying ,the brick should be fired in a kiln at 900 degree Celsius .Then natural cooling is taking place after firing and the brick ready for testing.
Fig 3.4 Mixing of raw materials
Fig 3.5 Moulding of bricks
Fig 3.6 Bricks are kept for dried
-
-
RESULTS AND DISCUSSIONS
To study the possibility of using laterite soil and ceramic dust in brick making. Water was added to these mixes along with normal geopolymer brick contents to produce a homogeneous paste having enough consistency to mould it into the brick shape by hand. Bricks were fabricated from these pastes using mould and soft extrusion technologies as carried out in the brick making industry. The bricks were air dried under shade and burnt at 900°C in a muffle furnace. The burnt bricks, so obtained, were subjected to standard tests viz., hardness test, efflorescence test, water absorption test and compressive strength test as per I.S: 3495-1976 (Part I to IV). Each test was conducted and noted its values.
-
Water Absorption test
To find the amount of moisture content on bricks, bricks are taken and weighted. Then immersed in water for 24 hrs, weigh the wet brick and note down its values. Difference between dry and wet brick weights gives the amount of water absorption.
Fig 3.1 Brick immersed in water for absorption test
It is found that the water absorption decreases with varying proportions of ceramic dust, fly ash and GGBS
-
Compressive Strength
When bricks are used as masonry units, especially in load bearing structures, they are meant to carry loads .The load carrying capacity is determined by compressive strength .It depends on composition, method of brick manufacturing and degree of firing .Place two plywood sheet each of 5mm
.Carefully center between plates of testing machine .Apply load axially at uniform rate till failure occurs. Note maximum load at which the specimen fails .No further increase in indicator reading on machine.
Fig 4.2 Compressive strength testing of brick
Size of brick = 20 x 10 x 10 Failure load (N/mm2) = 250 x 103 Length = 20 cm
Breadth= 10 cm Area = lxb = 20 x103
Compressive strength =12.5 N/mm2
Compressive strength of the bricks will be affected by the addition of ceramic dust and fly ash. The addition of ceramic dust into the brick will reduce the quantity of material by burning and addition of ceramic dust and fly ash increased the strength of brick.
3. Hardness Test
A sharp tool or fingernail was used to make scratch on brick. Resisted scratches against sharp things. There is no scratch impression on brick then it is hard brick.
4. Efflorescence Test
Efflorescence is caused by alkalise present in bricks. Place the end of bricks in a dish, depth of immersion in water being 25mm. Place the arrangement in a warm ventilated room until all water in the dish is absorbed by specimen and surplus water evaporates. Cover the dish containing brick with a suitable glass cylinder. When water has been absorbed and the brick appears to be dry. Place a similar quantity of water in the dish and allow it to evaporate. Examine the bricks for efflorescence.
The efflorescence of the specimen bricks was nil for all the studied mixtures of laterite soil, ceramic dust and fly ash.
V.CONCLUSION
Based on the preliminary investigations, the following can be concluded.
*Highest compressive strength is exhibited by the geo polymer with higher ceramic dust compared to other combinations.
*The water absorption of geopolymer bricks shows water absorption up to 6% whereas the normal clay bricks it will be around 20%.
*Acid resistance increased with respect to the increase in GGBS content in the mix proportion.
* Due to adaptation of dry oven curing method and geo- polymerization process, a substantial amount of water is conserved in this geopolymer brick production.
This shows that the results were satisfactory for 80% Ceramic dust, 30% GGBS and 15% fly ash. The laterite soil and clay percentages are kept constant in all mix designs. The compressive strength obtained was 12.5N/mm2.
Henceforth, it can be easily concluded that geopolymer bricks incorporated with ceramic dust are durable and eco- friendly in nature. It has the higher compressive strength parameter and reduced water absorption factor when compared to conventional clay bricks.
REFERENCES
[1] A. A. Kadar and A. Mohajerani, Bricks: An Excellent Building Material for Recycling Wastes A Review, in Environmental Management and Engineering conference (EME 2011), Calgary, Canada, pp. 108115, July 4-6, 2011. [2] M. F. Sarah, R. A. Gad, N. Feltin, S. Courteous, and L. Deville, Recycling and utilization assessment of waste fired clay bricks (Grog) with granulated blast-furnace slag for geo polymer production, Process Safe. Environ. Prot., vol. 103, pp. 237251, 2016. [3] F. Puertos, Waste glass in the geo polymer preparation. Mechanical and micro structural characterization, J. Clean. Prod., vol. 90, pp. 397408, 2015. [4] H. Cheng, Reuse Research Progress on Waste Clay Brick, Proscenia Environ. Sci., vol. 31, pp. 218 226, 2016. [5] A. Fernandez Jimenez, a. Palomar, J. Y. Pastor, and Martin, New Cementations Materials Based on Alkali-Activated Fly Ash: Performance at High Temperatures, J. Am. Ceram. Soc., vol. 91, no. 10, pp. 33083314, 2008. [6] D. M. Roy, Alkali-activated cements Opportunities and challenges, Cem. Concur. Res., vol. 29, pp. 249254, 1999.