
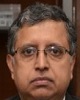
- Open Access
- Authors : Arindam Basu, Neha Kapil, Preeti Kaur Sachdeva
- Paper ID : IJERTV13IS030079
- Volume & Issue : Volume 13, Issue 03 (March 2024)
- Published (First Online): 22-03-2024
- ISSN (Online) : 2278-0181
- Publisher Name : IJERT
- License:
This work is licensed under a Creative Commons Attribution 4.0 International License
Development of Eco-Friendly Automotive Textiles for Acoustic Purpose
Arindam Basu, Neha Kapil, Preeti Kaur Sachdeva
Northern India Textile Research Association, Ghaziabad 201002
Abstract
The increase in personal incomes and continuous development of roads are resulting in increased number of vehicles on the road throughout the world. These vehicles need to be disposed off after their life time and this can cause great harm to the environment. To make the vehicles after life recyclable and environment friendly many parts are being made using ecofriendly biodegradable products. In a vehicle more than forty components are being used in which textile materials form a part. As the car moves at high speed it creates lot of noise due to friction with road, air and due to movement of various moving parts. An effort has been made to develop eco- friendly composites such as roofliner, door panel, package trays etc by using jute composites with poly propylene which will work as sound absorber in the vehicle and produce a commercial sample as per the available vehicles.
KeyWords: Roof liner, Door panel, Package tray, Sound Absorption Coefficient, Sound Transmission Loss, Needle Punched Nonwoven
-
INTRODUCTION
The development of a country is many times identified by its infrastructure development. In India, the continuous development of highways and other roads and increase in Indias GDP resulted in increased number of vehicles on the road. Also the demands for vehicles are growing continuously. As per the latest report of SIAM[1] the domestic sale of passenger vehicles have increased from 30,69,523 to 38,90,114 in 2022-23 as compared to the previous year. Sales of passenger cars increase from 14,67,039 to 17,47,376, utility vehicles from 14,89,219 to 20,03,718 during the same period. This increase in vehicle production results in more load to the atmosphere. In most developed countries the life of a car is fixed and they are supposed to be dumped. In India also in NCR region the life of petrol vehicles have been fixed as 15 years and for diesel vehicles 10 years. Gradually this system will be implemented in all parts of India.
Every year in European Union over six million vehicles reach the end of their life and are treated as waste. When end of life vehicles (ELVs) are not properly managed they can cause environmental problems and the European economy loses millions of tons of materials. On 13th July 2023 the European Commission proposed new regulation on end of life vehicles [2]. In line with European Green Deal and with the Circular Economy action plan, the proposal for ELV regulation builds on and replaces two existing Directives; Directive 2000/53/EL on end of life vehicles and Directive 2005/64/EC on the type approval of vehicles with regard to their reusability, recyclability and recoverability. The proposed new rules cover all aspects of vehicle from its
design and placement on the market until its final treatments at the end of the life.
The advances in new technologies are accompanied by noise pollution, in addition to air, soil and water pollution. Transportation with faster and larger vehicles on the road is a major source of noise pollution. This noise pollution does not affect the people on the road only, also the passenger sitting in the vehicle. In a road vehicles passenger compartment, the engine, wind and the road contact act as the major noise sources. Besides affecting the comfort of the passengers it also negatively affects the driver, thereby, increasing the chance of risking the safety of the passengers. This makes hood insulation, the headline and floor coverings critical elements in terms of noise control.
Among several methods of noise control, sound absorption comes as a preferable one. It is achieved in a vehicle by attaching sound absorbers, which are porous materials, to various auto parts including floor covering, package trays, headliners, trunk liners and door panels. Automobile noise control has conventionally been achieved by sound absorbers of glass fibres and foam materials [3].
Considering the importance of eco-friendliness efforts are being made by various scientists [4-7] to replace many of these synthetic materials. Natural fibre composites offer environmental advantages such as reduced dependence on non-renewable energy and material sources, lower pollutant emissions, lower green house gas emission, enhanced energy recovery and end of life biodegradability of components [4-7]. Jayaraman [8] studied the effects of some materials, production and post treatment methods on the sound absorption of needle punched non-wovens. He observed that the fineness of the fibre, optimum web layer sequencing and flame retardant treatment influenced the noise reduction performance positively.
For interiors of automobiles non-woven composites are generally used. Compression moulding is commonly used to produce large automotive components and it converts planar nonwoven fabrics into a three dimensional component. The process involves compression and heating and effect of compression on sound absorption of porous matters has been studied by various researchers [9]. The nonwoven composites designed for automobile interior applications should be able to withstand the temperatures which can be there inside a vehicle. Some parts of vehicles can reach extreme 550oC for the surface of an exhaust manifold of a passenger vehicle driving uphill. Both temperature and duration of treatment have been found to affect air flow resistivity and sound absorption [6]. With heat treatment it was observed that there may be increase in airflow resistivity and decrease in sound absorption. The difference
between the thermal treatment and the melting point of the thermoplastic constituent of the nonwoven composite is a significant factor on sound absorption. Sengupta et al. [6] observed that the sound reduction through jute based needle punched nonwoven fabrics is quite encouraging. Also it was opined by various workers [10,11] that the glass fibre which is widely used in automotive acoustic nonwovens has got some serious disadvantages such as being unsafe to handle, non recyclable and posing health risks when inhaled.
The modern headliner is a multiple laminate of up to seven or more components joined together. Each layer has its specific functions either for aesthetics, to provide sound insulation, vibration damping or to provide rigidity to the whole structure [12]. The central core is generally a layer of semi-rigid thermo-mouldable polyurethane foam, initially about 15-30 mm thick or alternatively composed of waste fibre bound with semi-cured phenolic resin. The centre core of polyurethane is bonded to two layers of chopped fibreglass rovings, one on each side. The layers of glass roving help impart rigidity to the structure. Attached to the side facing inwards is the decorative material, a non-woven polyester scrim is usually attached to the other side. All layers are joined together by action of the hot melt adhesives in a flat blade laminator, while taking care neither to damage the aesthetics of the decorative material nor to reduce the thickness of the centre core.
Though a number of studies claimed using jute as a part of composite in Automobile use, commercially it is not found in India. Our study was mainly to develop products using jute composites which can be utilised in vehicles commercially. As per the requirement the designed acoustic material should bring about effective sound attenuation in the targeted frequency range but will also need to possess mouldability, flame proofing and durability to elevaed temperature, high speed turbulent flow, high humidity and other hostile environments. It has to be kept in mind that most of the acoustic materials and acoustic textiles are expected to serve multiple tasks, not only in noise reduction but also in thermal insulation, comfort and contribution to safety systems.
-
MATERIALS AND METHODS
As a first step towards development of commercial automotive parts which play very important role in acoustic of the vehicles, presently used materials such as Roof liners and Engine shield used in popular commercial passenger vehicles have been collected. Images of some collected samples are shown in Figure 1 and 2. Collected materials were assessed for physical and acoustic properties (Table 2).
Figure 1: Collected roof liner samples from used cars
Figure 2: Collected engine shield samples from used cars
Table-1 shows the coding of the samples collected from market and the results obtained are shown in Results and Discussion section (Table 3-5). For measurement of Sound Absorption Coefficient (SAC) and Sound Transmission Loss (STL), ISO 10534-2 and ASTM E1050 test methods were used respectively. The results obtained were kept as the standards for the parts to be developed.
Table 1: Coding of samples collected from the market
Sample coding
-
ESA1: Engine shield sample-1
-
ESA2: Engine shield sample-2
-
ESB1: Engine shield sample-3
-
ESB2: Engine shield sample-4
-
SRF1: Roof liner sample -1
-
SRF2: Roof Liner sample-2
-
Sample coding
-
ESA1: Engine shield sample-1
-
ESA2: Engine shield sample-2
-
ESB1: Engine shield sample-3
-
ESB2: Engine shield sample-4
-
SRF1: Roof liner sample -1
-
SRF2: Roof Liner sample-2
-
Table 2: Test methods used for the assessment of physical
and acoustic properties
Sr. No.
Test Parameters
Test standards
1
Areal Density (GSM)
ASTM D 6242
2
Thickness
ASTM D 5736
3
Tensile strength
ASTM D 5035
4
Elongation %
ASTM D 5035
5
Sound Absorption Coefficient ( SAC)
ISO 10534
6
Sound Transmission Loss (STL)
ISO 10534
Jute fibres were collected from Birla Jute, West Bengal for producing nonwovens. As per the literature review, needle punching technique was used to produce the non-woven fabrics. The developed fabrics were assessed for physical and acoustic properties. The samples were produced using Jute, Viscose and Cotton in various combinations (Table 6). The basic physical parameters such as grams per square metre was varied and kept near to the commercially used ones. The collected samples were initially tested for their acoustic properties. During preparation of sample for acoustic properties (sound absorption coefficient and sound transmission loss) sample of circular diameter of 29 mm and 100 mm size was prepared.
The measurement is based on the Transfer Function Method. The Transfer Function method separates the incident and reflected energy from the measured transfer function, and then estimates the acoustic properties of the test sample. The sound transmission loss module is as per ASTM E2611. Figure 3 and 4 shows the experimental setup for measurement of sound absorption coefficient and sound transmission loss.
After the preliminary trials, composites were made with polypropylene keeping jute nonwoven in the centre and final roof liner was produced using commercially used moulds and hot press method. The developed composite was assessed for physical parameters, flammability and Sound Absorption Coefficient (SAC).
Figure 3: Schematic diagram of the sound absorption testing instrument
Figure 4: Schematic diagram of sound transmission loss measurement instrument
-
-
RESULTS AND DISCUSSION
Currently used acoustic automotive materials such as Roof liners and Engine shield used in popular passenger vehicles were collected and assessed for physical and acoustic properties. The results of physical test parameters of
samples collected from commercially run vehicles are shown in Table 3-5. The acoustic properties of the collected samples assessed in terms of Sound Absorption Coefficient (SAC) and Sound Transmission Loss (STL) are shown in Table 8 and 9.
Table 3: Test results of Engine Shield
Test parameters |
Coded Samples |
|||
ESA1 |
ESA2 |
ESB1 |
ESB2 |
|
Areal Density (GSM) |
1304 |
1554 |
1273 |
1288 |
Thickness (mm) |
10.53 |
10.88 |
6.36 |
6.32 |
Table 4: Test results of Roof liner
Test parameters |
Coded Samples |
|
SRF1 |
SRF2 |
|
Areal Density (GSM) |
784 |
772 |
Thickness (mm) |
5.76 |
6.19 |
Table 5: Tensile properties of the roof liners and engine shields
Test parameters |
Coded Samples |
|||||
ESA1 |
ESA2 |
ESB1 |
ESB2 |
SRF1 |
SRF2 |
|
Tensile strength (N) |
79.86 |
68.12 |
70.13 |
69.02 |
476.41 |
400.08 |
Length wise direction |
||||||
Width wise direction |
55.04 |
70.45 |
95.06 |
76.27 |
456.51 |
471.48 |
Elongation (mm) |
33.20 |
11.91 |
30.41 |
3.71 |
1.75 |
2.08 |
Length wise direction |
||||||
Width wise direction |
21.42 |
34.46 |
49.58 |
46.00 |
2.00 |
2.08 |
Tables 3-5 report the physical properties of the collected samples from the market. It can be seen for Engine shield the mass per unit area (gsm) values ranges from 1273 to 1555, whereas the GSM values for roof liner varies from 772 to784. The tensile strength of engine shields varied from
55.04 to 79.86 Newton and tensile strength of roof liners varied from 400.08 to 476.41 Newton. Keeping these values in mind attempts were made to develop needle punched non woven fabrics and those are identified by code names shown in Table-6. It may be noticed that the trials were undertaken using only natural/ biodegradable fibres at different mixtures. Table 7 reports the physical properties of the developed needle punched fabrics. GSM of the developed needle punched fabrics varied from 450 (J4) to 1368 (V2) and Thickness (mm) varied from 2.93 (J4) to 10.5 (V4). Tensile strength (lengthwise) varied from 84.82 (J4) to
378.62 (V2) and widthwise varied from 17.36 (J4) to 309.94 (V3). Elongation lengthwise and widthwise varied from 18.05 (J3) to 39.74 (C2) and 16.3 (V4) to 41.60 (J1) respectively.
Table 6: Samples developed for the initial trials
Sample coding |
Sample Composition |
J1 |
Jute fibre + Viscose fibre (Fibre Mix) |
J2 |
Viscose fibre + Jute fibre (Single side viscose) |
J3 |
Viscose fibre + Jute fibre + Viscose fibre (Sandwich Jute fibre with Viscose) Both side |
J4 |
Viscose fibre + Jute fibre (Single side viscose) |
C1 |
Cotton fibre web + Jute fibre web (Punch density 100 punches/cm2) 1C/1J |
C2 |
Cotton fibre web + Jute fibre web (Punch density -150 punches/cm2)1C/1J |
C3 |
Cotton fibre web + fibre web (Punch density 200 punches/cm2) 1C/1J |
V1 |
Viscose fibre web + Jute fibre web + Viscose fibre web (Sandwich Jute fibre web with Viscose fibre web) Both side (Punch density 100 punches/cm2) 1V/1J/1V |
V2 |
Viscose Felt + Jute Felt + Viscose Felt (Sandwich Jute fibre web with Viscose fibre web) Both side (Punch density-150 punches/cm2) 1V/1J/1V |
V3 |
Viscose Felt + Jute Felt + Viscose Felt (Sandwich Jute fibre web with Viscose fibre web) Both side (Punch density-200 punches/cm2)1V/1J/1V |
V4 |
2 Viscose Felt + Jute Felt+ Viscose Felt (Sandwich Jute fibre web with 2Viscose fibre web on top and 1 Viscose fibre web on bottom) Both side (Punch density 100 punches/cm2) 2V/1J/1V |
Table 7: Physical properties of the developed needle punched fabrics
Sample coding |
Areal density (GSM) |
Thickness (mm) |
Tensile Strength (Newton) Lengthwise |
Tensile Strength (Newton) Width wise |
Elongation (mm) Lengthwise |
Elongation (mm) Width wise |
J1 |
1032 |
4.85 |
260.9 |
110.3 |
23.74 |
41.60 |
J2 |
663 |
3.45 |
142.84 |
57.68 |
19.842 |
35.24 |
J3 |
775 |
4 |
137.94 |
48.34 |
18.05 |
35.606 |
J4 |
450 |
2.93 |
84.82 |
17.36 |
20.88 |
18.149 |
C1 |
1000 |
7.69 |
208.58 |
104.46 |
21.71 |
39.55 |
C2 |
1074 |
7.66 |
157.38 |
248.7 |
39.74 |
26.003 |
C3 |
1008 |
6.3 |
191.56 |
252.18 |
41.91 |
25.46 |
V1 |
1000 |
7.2 |
191.12 |
123.8 |
27.72 |
24.56 |
V2 |
1368 |
7.1 |
378.62 |
229.7 |
21.62 |
30.83 |
V3 |
1250 |
6.69 |
238.42 |
309.94 |
31.053 |
25.64 |
V4 |
1300 |
10.5 |
188.16 |
74.04 |
25.33 |
16.3 |
Table 8: Sound Absorption Coefficient (SAC) of the collected samples and developed needle punched fabrics
Frequency (Hz) |
Sound Absorption Coefficient () Testing Results |
||||||||||||||||
Collected Samples |
Developed Samples |
||||||||||||||||
ESA 1 |
ESA 2 |
ESB 1 |
ESB 2 |
SRF 1 |
SRF 2 |
C1 |
C2 |
C3 |
V1 |
V2 |
V3 |
V4 |
J1 |
J2 |
J3 |
J4 |
|
Alpha () |
|||||||||||||||||
50 |
0.02 |
0.03 |
0.03 |
0.02 |
0.02 |
0.02 |
0.02 |
0.03 |
0.03 |
0.02 |
0.04 |
0.03 |
0.04 |
0.04 |
0.04 |
0.04 |
0.04 |
250 |
0.04 |
0.05 |
0.03 |
0.03 |
0.03 |
0.03 |
0.03 |
0.03 |
0.03 |
0.03 |
0.03 |
0.03 |
0.04 |
0.03 |
0.03 |
0.03 |
0.03 |
500 |
0.10 |
0.10 |
0.07 |
0.07 |
0.07 |
0.06 |
0.07 |
0.07 |
0.05 |
0.06 |
0.06 |
0.06 |
0.09 |
0.05 |
0.04 |
0.05 |
0.04 |
1000 |
0.26 |
0.28 |
0.13 |
0.14 |
0.11 |
0.09 |
0.15 |
0.16 |
0.11 |
0.02 |
0.02 |
0.03 |
0.15 |
0.03 |
0.03 |
0.02 |
0.03 |
2000 |
0.63 |
0.66 |
0.30 |
0.34 |
0.30 |
0.23 |
0.36 |
0.39 |
0.26 |
0.29 |
0.36 |
0.30 |
0.52 |
0.20 |
0.17 |
0.20 |
0.12 |
4000 |
0.94 |
0.96 |
0.62 |
0.72 |
0.79 |
0.55 |
0.77 |
0.76 |
0.64 |
0.69 |
0.81 |
0.73 |
0.87 |
0.59 |
0.55 |
0.54 |
0.41 |
5000 |
0.98 |
0.97 |
0.67 |
0.78 |
0.97 |
0.72 |
0.98 |
0.89 |
0.89 |
0.94 |
0.93 |
0.89 |
0.96 |
0.86 |
0.71 |
0.81 |
0.53 |
Table 9: Sound Transmission Loss (STL) of the collected samples and developed needle punched fabrics
Frequency (Hz) |
Sound Transmission Loss Testing Results |
||||||||||||||||
Collected Samples |
Developed Samples |
||||||||||||||||
ESA 1 |
ESA 2 |
ESB 1 |
ESB 2 |
SRF 1 |
SRF 2 |
C1 |
C2 |
C3 |
V1 |
V2 |
V3 |
V4 |
J1 |
J2 |
J3 |
J4 |
|
STL in dB |
|||||||||||||||||
50 |
8.09 |
6.25 |
5.26 |
3.45 |
37.08 |
44.18 |
4.06 |
6.16 |
4.39 |
2.66 |
6.24 |
6.16 |
6.37 |
5.02 |
3.29 |
3.95 |
.68 |
250 |
8.04 |
4.92 |
4.68 |
3.37 |
30.21 |
37.16 |
4.96 |
6.29 |
4.70 |
3.86 |
6.55 |
6.76 |
6.78 |
5.54 |
3.93 |
4.46 |
2.10 |
500 |
7.51 |
5.66 |
4.52 |
3.64 |
26.67 |
31.08 |
4.98 |
6.29 |
4.78 |
3.93 |
6.54 |
6.71 |
6.98 |
5.62 |
3.98 |
4.46 |
2.13 |
1000 |
8.41 |
6.17 |
5.04 |
3.99 |
16.52 |
21.44 |
5.04 |
6.29 |
4.79 |
4.09 |
6.52 |
6.64 |
7.35 |
5.59 |
4.12 |
4.50 |
1.75 |
2000 |
9.20 |
6.86 |
5.45 |
4.53 |
20.16 |
22.39 |
5.29 |
6.30 |
5.21 |
4.57 |
7.04 |
7.09 |
7.69 |
5.53 |
4.37 |
4.77 |
2.40 |
4000 |
10.69 |
8.08 |
5.90 |
5.18 |
25.85 |
27.45 |
6.03 |
7.24 |
6.64 |
4.57 |
7.68 |
7.12 |
8.70 |
6.31 |
5.03 |
5.16 |
2.76 |
5000 |
10.15 |
7.60 |
7.15 |
7.94 |
24.91 |
33.37 |
6.48 |
7.83 |
6.03 |
5.32 |
8.05 |
7.83 |
10.02 |
6.84 |
5.54 |
5.53 |
2.99 |
Results of Acoustic Properties of Collected and developed Samples:
According to ISO 10534-2 Sound Absorption coefficient (SAC) and ASTM E1050 Sound Transmission Loss (STL) was measured for the collected samples. Table 8 and 9 reports the SAC and STL of the collected and developed nonwoven samples respectively. Figure 5 and 6 shows sound absorption and sound transmission characteristics of the collected samples. The maximum sound absorption coefficient among the engine shield samples is 0.28 for lower frequency (f < 1000 Hz) and 0.98 for higher frequency (f > 1000 Hz) and in case of roof linear samples it is 0.1 for lower frequency (f < 1000 Hz) and 0.97 for higher frequency (f > 1000 Hz).
It was observed that maximum absorption coefficient for engine shield samples is 0.98 at 5000 Hz (ESA1), 0.97 at 5000 Hz (ESA2), 0.67 at 5000 Hz (ESB1) and 0.78 at 5000
Hz (ESB2), respectively. It was observed that maximum absorption coefficient for Roof liner samples is 0.97 at 5000 Hz (SRF1), 0.72 at 5000 Hz (SRF2), respectively (Refer table 8).
It was also observed that Engine Shield with areal density of 1273 g/m2 (ESB1) has lowest sound absorption and engine shield with the areal density of 1554 g/m2 (ESA2) has higher sound absorption for the entire frequency range. Similar trend has been observed in collected samples of Roof liner. Thickness of the material is another factor which influences the sound absorption characteristics of any material. It was observed that thickness 10.88 mm (ESA2) has higher sound absorption coefficient values at low- and medium frequency range compared to others. Low-frequency sound absorption has a direct relationship with thickness of material. When thickness of the material increases, the sound absorption characteristics increase and absorption curve also shifts towards lower frequencies. Figure 6 shows sound transmission loss of collected samples. Here also, sample of Engine shield and roof liner with higher areal density and thickness shows the higher sound transmission loss. The developed samples had similar level of sound absorbency and transmission loss properties. However, as we wanted to produce roof-liner it was expected that the nonwoven fabrics will have higher values than the collected samples. Those collected samples were already compressed and it is reported that the sound absorption and sound transmission loss values reduce due to compression and application of heat [5].
1
0.9
0.8
0.7
ESA-1
1
0.9
0.8
0.7
ESA-1
0.4
ESB-2
SRF-1
0.4
ESB-2
SRF-1
0.3
0.3
SRF-2
SRF-2
0.2
0.1
0
0.2
0.1
0
0
1000
2000
3000
Freuency (Hz)
4000
5000
6000
0
1000
2000
3000
Freuency (Hz)
4000
5000
6000
0.6
0.6
ESA-2
ESA-2
0.5
0.5
ESB-1
ESB-1
Sound Absorption Coefficient (SAC)
Sound Absorption Coefficient (SAC)
Figure 5: Sound absorption characteristics of collected samples from used cars
ESA-1 ESA-2 ESB-1 ESB-2 SRF-1 SRF-2 |
Figure 6: Sound transmission loss of collected samples from used cars
It was observed that though the samples made by using natural fibres only there was a problem of forming composites. As per the experience of earlier workers [7] it was decided to produce sandwich composites using fibrous nonwoven material in the middle. In this case the glass fibre, which is widely used in automotive acoustic nonwovens, was replaced with jute and some thermoplastic fibre blends. Jute & Polyester blended nonwoven samples were developed using bio-degradable polyester fibre, received from Reliance Industries Ltd. These samples were tried on roof liner moulds for automobile application. Trials were made at various moulding temperatures but the results werent satisfactory. During the moulding process, it was noticed that the moulded shape of the polyester and jute roof liner samples didnt retain well. The jute-polyester non- woven blend didnt furnish satisfactory results, so a new blend was tried.
-
50% Jute and 50% PP blended non-woven fabric was developed
-
GSM of 1500 was developed in calendared and non- calendared forms
The weight per unit area (GSM) has been selected based on the commercial specifications of automobile components manufacturers. The composites mechanical performances are highly impacted by the fibre division and cell wall stiffness. Practically it was observed that when direct jute fibres are used in composite the final material does not have enough toughness as compared to similar composite with glass fibre. The raw jute fibre was replaced with sliver waste from jute draw frames, which have better fineness and are shorter in length. Rask et al. [13] recommended fibres well separation for composite reinforcements. This modification helped in development of roof liners of commercial vehicles. Similar observation was made by Doumbia, Castro, Jouannet et al. [14], where they observed that use of longer fibres is not a priority for the improvement of mechanical performance. Polypropylene was chosen as thermoplastic component in the composite as it is of low cost, low density, easily processable, easily recyclable and non-toxic in nature.
Trials were taken for developing the roof liner for commercial vehicles. Two roof-liner samples were developed as per the specification. Samples were developed for the following commercial vehicle manufacturers:
-
Sonalika tractors
-
Volvo India Pvt ltd
Figure 7 (a): Front side of moulded rof liner
Figure 7 (b): Developed Roof Liner made up of 50% Jute and 50% Polypropylene (PP)
for M/s Sonalika Tractor
Table 10: Physical test parameters of Jute PP Roof liner
Sr . N o. |
Test Paramet ers |
Test Meth od |
Unit |
Test Resul ts |
1. |
Areal Density (GSM) |
AST M D638 |
gm/ m2 |
1933 |
2. |
Thicknes s |
mm |
3.77 |
|
3. |
Tensile Strength |
Mpa |
16.23 |
|
4. |
Elongati on |
% |
3.08 |
Table 11: Flammability properties of Jute PP Roof liner
Figure 8: Sample for Sound Absorption Coefficient (SAC)
The results shown in Table 10-12 belong to the Jute/PP acoustic roof liner materials developed in this study. It can be seen from Table 11 and 12 that the material has near to zero flammability (as per FMV SS302 Standard) and the average value of sound absorption co-efficient is 0.508, which is very close to the values obtained for the commercial roof liner SRF2 for higher frequency f > 1000 Hz (refer table 8).
Sr . N o. |
Test Paramet ers |
Test Meth od |
Unit |
Test Resu lts |
1. |
Flammab ility |
FMV SS 302 |
mm/ min |
0 (Zero ) |
Table 12: Sound Absorption Coefficient test parameter of Jute PP Roof liner
Sr. No. |
Test Parameters |
Test Method |
Frequency ( Hz) |
Sound Absorption |
1. |
Determination of sound absorption coefficient Sample Thickness 3-4 mm |
ISO 10534-2 |
5000 |
0.508 |
The highest Sound Absorption Coefficient value recorded was 0.667 and 0.508 is the average SAC value for the developed roofliner that meets the requirements as per commercial benchmark.
An attempt was made to use eco-friendly fibres, i.e. Jute, Cotton and Viscose for producing nonwovens in various combinations and tested for physical and acoustic properties in comparison to the used roof liner and engine shield samples drawn out from passenger cars. Nonwovens made of solely natural fibres faced the problem of forming composites. Thus, to overcome this drawback of natural fibres an eco-friendly automotive textile composite for acoustic purpose was successfully developed using sustainable and recyclable fibres like jute and polypropylene. Sliver waste from jute draw
frames was used to curb wastage and polypropylene was chosen as thermo plastic component in the composite as it is of low cost, low density, easily processable, easily recyclable and non-toxic in nature. Two roof liner samples were developed from 50/50 jute/ polypropylene blend and compressed into a composite using commercial moulds and hot press method. The developed roof liner samples were assessed for physical, acoustic parameters and flammability and were found to meet the requirements as per the commercially set benchmarks.
5. ACKNOWLEDGMENT
The authors are thankful to the National Jute Board, Ministry of Textiles, Govt. of India for sponsoring the project on Development of Jute Composite for Automotive Acoustic Insulation & Other Uses. Under the project, this research paper is published.
REFERENCES:
-
https://www.siam.in/statistics- aspx?mpgid=88pgidtrail=9.#:text=Domestic%Sales&text=Sales%20Passen ger%20cars%20
-
https://environment.ec.europa.ev/topics/waste-and-recycling/end-life- vehicles- en#:~:text=The%20EU%20has%20rules%20on,2022%20for%20the%20ye ar%202020)
-
N. D. Wilnaz, Acoustical properties of biodegradable nonwoven, Ph.D. Dissertation, NC State University, Raleigh, 2009.
-
S. V. Joshi, L. Drzl, A. K. Mohanty & S. Arora, Are natural fibre composites environmentally superior to glass fibre reinforced composites, Composite Part A: Applied Science and Manufacturing, 2004, 35(3), 371- 376.
-
N. D. Yilmaz, N.B. Powell, P. Banks Lee & S. Michelin, Multifiber needle-punched nonwoven composites: Effects of heat treatment on sound absorption perfrmaance, J Textile Inst, 2012, 43(2), 231-246.
-
Y. Chen, O Chiparus, L Sun et al., Natural fibres for automotive nonwovens, J.Inudstrial Textiles, 2005, 35(1), 47-62.
-
S. Sengupta, G. Basu, M. Datta, S. Debnath and D. Nath, Noise control material using jute (Corchorus olitorius): – Effect of bulk density and thickness, J. Textile Inst, 2021, 112(1), 56-63.
-
K. Jayaraman, Acoustic absorptive properties of Nonwovens, M.S. Thesis, N C State University, Raleigh, 2005.
-
B. Castgenede, A Akine, B. Bronard et al., Effects of compression on the sound absorption of fibrous materials, Appl. Acoust, 2000, 61(2), 173- 182.
-
N. D. Yilmaz, N. B. Powell, S. Michielsen & P. Banks Lee, Hemp fiber based nonwoven composites: Effects of alkalisation on sound absorption performance, Fibers & Polymers, 2012, 13(7), 915-922.
-
A. K. Mohanty, M. Misa, L. T. Drzal, S. E. Selke, B.R. Harte and H. Hinrichsen, Chapter 12, Natural Fibers, Biopolymers and Biocomposites, Ed. A K Mohanty, M. Misra and L.T. Drzal, CRC Press, Boca Raton, 2005.
-
W. Fung and M. Hardcastle, Product Engineering interior trim, Chapter 6, Textiles in Automotive Engineering, Woodhead Publishing Ltd, U.K.,2001.
-
M. Rask, B. Madsen, B.F. Sorensen, J.L. Fife, K. Martyniuk & E.M. Lauridsen, In situ observations of microscale damage evolution in unidirectional natural fibre composites, Compos. A: Appl. Sci. Manuf. 2012, 43, 1639-1649.
-
A.S. Doumbia, M. Castro, D. Jouannet, A. Kervoclen, T. Falher, L. Cauret & A. Bourmand, Flax/Polypropylene composites for lightened structures: Multi scale analysis of process and fibre parameters, Materials & Design, 2015, 87, 331-341.