
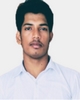
- Open Access
- Authors : Arun V , Dr. Balaji B , Rallapalli Chanukya R , Yashwanth B S
- Paper ID : IJERTV10IS100158
- Volume & Issue : Volume 10, Issue 10 (October 2021)
- Published (First Online): 08-11-2021
- ISSN (Online) : 2278-0181
- Publisher Name : IJERT
- License:
This work is licensed under a Creative Commons Attribution 4.0 International License
Design & Performance Evaluation of 3- Blade Propeller for Multi-Rotor UAV
Arun V
Department of Mechanical Engineering
K.S School of Engineering & Management Bangalore-India
Rallapalli Chanukya R
Department of Mechanical Engineering
K.S School of Engineering & Management Bangalore-India
Yashwanth B S
Department of Mechanical Engineering
K.S School of Engineering & Management Bangalore-India
Prof. Dr. Balaji B
HOD, Department of Mechanical Engineering
-
School of Engineering & Management Bangalore – India
Abstract This work emphasis on research, designing and development of an 3-blade efficient propeller for an existing UAV to produce maximum thrust in an operating range of 2000 rpm to 3000 rpm. And CFD analysis will be performed to determine the performance characteristics of the propeller.
KeywordsUAV, Quadcopter, Propellers, Multirotors, VTOL
-
INTRODUCTION
A propeller is a device that converts mechanical energy into a force, which we call thrust, and is used to propel the vehicle to which it is attached. The propeller features one or more lifting surfaces called propeller blades1 that are rotated rapidly using an engine. The thrust is the aerodynamic lift force produced by the blades and is identical to the force produced by a wing. Propellers are, by far, the most common means of generating thrust for any general Aviation aircrafts or modern UAVs.
-
3-BLADE PROPELLER GEOMETRY
A.
Figure 1 Propeller Helix
A three-bladed propeller is shown in Figure 1, rotating about an axis. The spinner is an aerodynamically shaped cover, whose purpose is to reduce the drag of the hub of the propeller and to protect it from the elements. The propeller blades are what generate the thrust of the device, denoted by
-
The pressure differential between the front and aft face of the propeller blade results in a vortex that is shed from the tip of the blade and is carried back by the airflow going through
the propeller. This forms the typical helical shape shown in the figure-1. A frontal projection of the three-bladed propeller is shown below.
Figure-2 Frontal projection of the 3-blade propeller
Where R is the blade radius, r is the radius to an arbitrary blade station, and U is the rotation rate, typically in radians per second or minutes. The blade of a propeller is really a cantilevered wing that moves in a circular path rather than along a straight one. Just like an airplanes wing, the plan form of the propeller blade has a profound impact on the magnitude of the thrust force created, as well as at what cost. What constitutes cost is the amount of power required to rotate it, as well as side effects such as noise.
-
-
GEOMETRIC PROPELLER PITCH Consider the propeller in Figure – 3, whose diameter is
D and radius is R. As the propeller rotates through a full circle, its tip rotates through an arc length (circumference) of C = 3.14xD = 2×3.14xR. As the propeller rotates it screws itself forward a certain distance P for each full rotation. The distance it would cover in one full revolution is called the geometric pitch or pitch distance, PD, of the propeller. It is commonly specified in terms of inches of pitch. Thus a propeller designated as a 42-inch pitch prop would move 42 inches forward in one revolution (using the metal screw through wood analogy). The angle the helix makes to the
rotation plane is called the geometric pitch angle and is denoted by .
Figure-3 schematic showing propeller properties
Pitch distance in inches
Figure-4 the propeller will advance a shorter distance (pitch distance) in a low-viscosity fluid than the geometric pitch indicates
-
FUNDAMENTAL FORMULATION Considering the geometry shown in figure-3 we can now define the following characteristics of the propeller:
(Eq. 1)
Where;
= reference radius, usually 75% of the propeller radius R PD = Pitch distance of the propeller
Generally, the value of PD ranges from 60% to 85% of the diameter of the propeller. The pitch-to-diameter ratio is also used to identify propellers
Pitch-to-diameter ratio
(Eq. 2)
Figure-5 Definition of propeller pitch angle
A propeller moving through a low-viscosity fluid like air will cover less distance per revolution than the geometric pitch would indicate. Therefore, the angle formed between the rotation plane and a tangent to the blade tip helix at each blade station is less than the geometric pitch angle. This angle is called the helix angle and is denoted by . It can be estimated if the forward speed of the propeller is known using the following expression:
Helix angle:
(Eq. 3)
-
DESIGN STATEMENT
Propellers for UAVs operate under various operating conditions, ranging from the sea level to stratosphere altitudes. Apparently, it is appropriate to adopt a variable pitch system to provide the optimal propulsive efficiency under the aforementioned conditions. However, its adoption imposes additional weight and complexity due to the addition of actuators and pitch links. Additionally, these pitch links and actuators will practically be exposed to external flows at low temperatures from 70 to 80° C at stratospheric altitudes. The extreme environment and mechanical complexity may lead to an increased possibility of malfunctions and uncertainty. Consequently, the demand for reliability and being ultra-lightweight, which are top-level constraints of UAVs, makes it difficult to adopt the variable pitch system. Therefore, fixed-pitch propellers are generally used. When the fixed-pitch propellers are optimized for aerodynamic performance at high-altitude operation, the required torque, approximately at sea level, becomes considerably large and exceeds the specification for electric motors. This can lead to low climbing performances or, sometimes, the inability to climb. On the other hand, as altitude increases, the rotational speed of the propeller gradually increments, which consequently results in an increase of the required power. Thus, the maximum required power occurs under high-altitude climbing conditions. In this respect, the design of UAV propellers must not only take into account the two conflicting constraints but also simultaneously maximize efficiency under the desired operating condition.
-
DESIGN REQUIREMENTS
Static Rotating
The ultralight weight aircraft, has a total length, total width and design total weight of approximately 1.2 m, .5 m, and 2.5 kg, respectively. It uses 4-propellers mounted on each arm. The maximum available torque should correspond to the climb condition at sea level, requiring the highest thrust. The maximum power condition should correspond to the climb operation where the highest rotational speed is required. Considering the motor diameter, the design propeller diameter was fixed at 0.25 m. as a geometry constraint. In conformance with the mission profile, which is mainly aimed at climbing to high altitudes, the climb condition of 4 km was set as the propeller design point.
-
AIRFOIL SELECTION & POSITIONING[1]
-
CFD ANALYSIS PREPARATION
Considerations Speed 3000 rpm Inlet Velocity 15m/s Angle of attack =
Propeller Dia = 250 mm Number of Blades = 3
Propeller Material = Carbon fiber
Step-1
Creating Enclosures Cylindrical Enclosures
Step 2
Creating Enclosures Box Enclosure
Step -3
Creating Boolean-1 Tool Body: Propeller
Target Body: Cylndrical Enclosure Now we have only 2 Bodies i.e.
-
Rotating Domain
-
Static Domain
Creating Boolean-2
Tool Body: Rotating Domain Target Body: Static Domain
VIII. CAD MODEL PREPARATION
Figure-7 10 inch Propeller cad model
Step-4
-
Meshing
-
Inserted Mesh sizing for rotating domain
Max- Element size 8 mm
-
Mesh Settings Static Domain Max- Element Size 15 mm
Step-5
Creating named Selections
Propeller Inlet Outlet
Step-6
Updating the Mesh Step-7
Step-8
Setup
Selecting Transient and Gravity
Step-9
Model Viscous Laminar
Step-10
Cell Zone Conditions
Rotating Domain
Static Domain
Step-11
Boundary Conditions
Inlet velocity magnitude = 5 m/s
Reference Values
Step-12
Report Definitions
Create new force report- Thrust Force
-
-
Step-13
-
Calculation Activities
Create- Solution Data Export
Step-14
Initialization Initialization method Hybrid
Step-15
Initialize
Step-16
Run Calculation Time Steps 0.00015 Number of Steps 10
Max. Iterations / step 1 (selected for less computing time)
Step- 17
Run Calculation
Drag Force
-
-
RESULTS
Total pressure
Thrust Force
Dynamic Pressure
Static Pressure
Counter plots Velocity contour
Pressure Flow trajectory
-
CONCLUSION
A 3 blade propeller of diameter 254mm and a 3D CAD model is prepared with the combination of airfoils and radial distribution of NACA 4309, NACA 4410, NACA 4510, NACA 4512, NACA 5513 & NACA 5521 is prepared. The model is been analyzed through Ansys CFD following the steps as discussed above. Its been found that the developed propeller with carbon fiber material is capable of producing
-
N of thrust force at 3000 rpm. Hence we can use the developed propeller in any mini UAVs with the 1200 KV motor with an 11.1 v Lipo battery.
-
-
REFERENCES
-
-
-
Design and Performance Evaluation of Propeller for Solar- Powered High-Altitude Long-Endurance Unmanned Aerial Vehicle. International Journal of Aerospace Engineering, Volume 2018, https://doi.org/10.1155/2018/5782017
-
Glassock, R.R. Design, Modelling and Measurement of Hybrid Powerplant for Unmanned Aerial Vehicles (UAVs), Masters Thesis, 2012, Queensland University of Technology.
-
Ansys 18 Fluent Tutorial Guide