
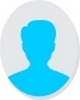
- Open Access
- Authors : Abhijeet Samal
- Paper ID : IJERTV10IS110009
- Volume & Issue : Volume 10, Issue 11 (November 2021)
- Published (First Online): 12-11-2021
- ISSN (Online) : 2278-0181
- Publisher Name : IJERT
- License:
This work is licensed under a Creative Commons Attribution 4.0 International License
Design of Evaporator Cooling Coil for Cooling Load
Abhijeet Samal1
Mechanical Engineering
B.M.S College of Engineering,Bengaluru
Abstract- This Paper consist of the detail design process of a cooling coil which is used in Evaporator of VARC System for given cooling load. The process consists of designing a part using the calculation and various other parameters. Design is made on real world scenario to enhance the optimization in sense of very aspect. It has been designed to perform effortlessly in all the dynamic conditions and consists of the capability of being tuned manually to enhance the cooling performance according to the requirements of a specific cooling load. Psychometric chart data of air and refrigerant R- 134a taken directly which is predetermined Parameters for design procedure
Keywords: Evaporator, Psychometric Chart, Refrigerant, R- 134a.
-
INTRODUCTION
An evaporator is a device that absorbs the heat surrounding it to cause the liquid refrigerant inside it to boil until the refrigerant leaves as a superheated (saturated) gas. Each evaporator operates according to the same basic formula: it absorbs heat while boiling off the liquid refrigerant. The efficient thermal design of the cooling coil leads to a reduction in the coil surface heat transfer area and of course, its capital cost and its weight. On the other hand, the enhancement in the coil thermal performance will usually be established at expense of the hydraulic performance of the cooling coil and in turn, its
running cost. Because the cooling coil is an integral part of the air distribution system, its geometry size, number of rows, fin spacing, and fin profile contributes to the airside pressure drop and affects the sound power level of the fans.
This paper mainly
focuses on Methods to design the cooling and dehumidifying coil or Direct Expansion evaporator
coil. Which are usually based on log mean enthalpy or log equivalent dry-bulb temperature difference.
Direct Expansion Evaporator
An Evaporator or Direct Expansion (DX) Coil works on the refrigeration effect cooling occurs when a fluid under pressure and at a temperature above its normal boiling point has the pressure reduced. This makes the fluid want to boil or flash to a gas. For it to boil (Flash), the liquid must absorb heat from its surrounding environment thus cooling the surroundings. Refrigerants are a mix of Chemicals that boil at low temperatures some down to 100 F by
controlling how much pressure the refrigerant is under the flash point temperature of the liquid refrigerant is controlled
Most refrigeration System use a refrigerant expansion valve at the evaporator coil to sense the temperature of the gaseous refrigerant leaving the coil so as to regulate the amount of liquid refrigerant entering the coil As liquid refrigerant passes through the refrigerant expansion control valve part of the liquid flashes to a gas. Upon exiting the refrigerant stream is mostly liquid but the vapor occupies more space. This causes the two liquid to travel at different rates and separate with the gas at the top and the liquid at the bottom of the stream. If this gas/liquid stream is not properly mixed and distributed, then some coil circuits receives mostly gas and other circuits the liquid. This degrades the heat transfer capabilities of the evaporator coil.
-
MATERIAL SELECTION AND GEOMETRY Aluminum, Copper are preferred material has it is good conductor of heat Round seamless copper tubes are mechanically expanded into the fin collars of the secondary surface. The mechanical expansion provides a permanent metal-to-metal bond for efficient heat transfer. Tubes are staggered in the direction of airflow and only return bends are used NO reduced tube wall in the bend radius by using hairpin bends. Some coil manufacturers fabricate coils from 5/8 inch OD copper tubes, from 1/2inch copper tube and still others use 3/8 inch tubes. Selection of the tube size is a matter of manufacturer's choice and market demand. Price, as always, plays a major part in the tube size selection. In a coil, copper tubes are arranged parallel to one another, either in staggered pattern or non-staggered pattern, along the length L of the coil.
1) A staggered pattern is more commonly used. For 1/2 inch tubes it is 1.25 inch. Plate or ripple fins are used to enhance the heat transfer area. Thus the primary surface area (outside area of bare copper tubes) is enhanced greatly by adding a secondary area of fins. The total area including fins is called outside surface area. The cross-section (L × H) which the air flows is called the face area or the finned area. Thus L is finned length and H is fin height. Fins are arranged perpendicular to the tubes. Where, the fin spacing varies between 8 and 16 fins per inch of tube.
Tao = 10.5 oC,
Wao = 0.86*10-3 kgv/kga]
QC = 60 kW
CSHF = 0.75
-
CALCULATION PROCEDURES
= ( )
60
= (54 33)
= 2.857Kg/s
=
( )
Fig 1 Evaporator Configuration
Coil construction parameters
-
Outside tube diameter, do = 13.41 mm
-
Inside tube diameter, di = 12.09 mm
-
Longitudinal tube spacing, SL = 26.16 mm
-
Transverse tube spacing, ST = 31.75 mm
1
T
= 1.7KJ/Kg
(+14)+(+1.4)2+0.184(1+0.76)
=
0.092
Ts1 =14.23 < Td.point=15
(+14)+(+1.4)2+0.184(2+0.76)
=
-
No. of fins/m, Nf
= 554
s2 0.092
-
Aluminum fin thickness, tf = 0.15 mm
-
Exchanger compactness, = 1060 m2/m3
-
Outside area/inside area, (Ao/Ai) = 23
-
Aflow/AFace on the air-side = 0.529
Calculation of
Ts2 =9.21 0C
-
Finned-surface weighted efficiency = 0.85
-
Number of tube-passes
= (
)
per water loop, Np = 6
Moist air Conditions
-
Total cooling load at full load, Qc = 60 kW
-
Latent Load at full load, QL = 20 kW
-
Inlet air conditions = 26 0C
=
[(1 ) (2 )]ln (1 ) (2 )
= 5.33 0C
-
Dry and wet bulb temperatures are = 19 0C
-
Air face velocity, V = 2.8 m/s
-
Air heat transfer coefficient, hc = 60 W/ (m2 oC)
-
Air mean specific heat, cpm =1.001 kJ/(kg. K)
R-134a
Evaporating temperature, Tev =7 oC Heat transfer coefficient on
refrigerant side, hi = 2000 W/ (m2 oC)
Number of tube-passes
per water loop, Ntp = 6
Air Condition From Psychometric-chart Inlet Air Condition
Hain = 54 kJ/kg
Wain = 0.011 kgv/kga
Outlet Air Condition
Haou = 33 kJ/kg
Where, Tevm = mean temperature difference on the refrigerant-side.
Calculation of Ai & Ao
=
= 5.63 2
= ( )
= 129.5 m2
Calculation of Exit air calculation
(1 )
2 = [ 2 ] × 1 (1 )
The Length of the Tube (Coil), L
2
1 2
=
+ [ ] × ( 2 ) 1 + 2
= 1.54 m
= 10.75 0C
=
Height of the Coil, H
Air face area,
=
= 2.30
Air is saturate at this temperature with
ha2 = 31.5 kJ/kg
Aface = HL
= 0.882 m2
2 2
2
2
2 = 2501 + 1.8
=0.00823 Kgv/Kga Calculation of Latent load and CSHF
Number of Rows, Nr
= 0.572 m2
= =
Qc = ma(ha1-ha2)
= 64.28 KW
Ql = Qc Qs
= 64.28 -2.857*(26-10.72)
Depth of the Coil, D
= 5.35 ~ 6 Rows
=
= 0.157 m
= 20.62 KW
CSHF =64.2820.6
64.28
= 0.68
Calculation of Dx-Coil Size
Number of Coil Tubes Nt for DX-coil the number of tubes is determined by applying the continuity equation for the refrigerant at the exit of the coil where the velocity attains its maximum value at this exit section. Assuming the refrigerant as saturated vapor, and the maximum velocity of vapor ~10 m/s, Nt is given as:
=
= 0.33 Kg/s Nt = 4
2
~ 96
-
-
CONCLUSION
A multi-Row Evaporator was developed based on the the requirement of cooling load with ambient air and exhaust air. An evaporator was newly designed by considering various parameters The device was designed to cope with misdistribution on air and refrigerant side. Subsequently this new evaporator is best surrounded by all condition. simulation of the cooling coil using a discrete technique "row-by-row method" has been presented. The main advantage of this method is to trace the air and coil surface temperature locally. In addition, this method gives more accurate results for the cooling coil design or simulation compared with those given by ordinary method such as log mean enthalpy method. This concludes through calculation for given cooling load. This method gives optimized result compared to simulation testing result therefore most preferable method.
-
REFERENCES
-
Corberan, J.M., Gonzalvez, J., Montes, P., Blasco, R.: ART A Computer Code to Assist the Design of Refrigeration and A/C Equipment. In: Proceedings of International Refrigeration and Air- Conditioning Conference, Paper ID 507, Purdue (2003)
-
Hewitt, G.: Churn and Whispy Annular Flow Regimes in Vertical Gas-Liquid Flows. Energy & Fuels 26(7), 40674077 (2012)
-
ASHRAE Systems and Equipment Handbook (SI), 2000, Chapter 21
-
ASHRAE Fundamental Handbook (SI), 2001, Chapter 6
-
The author designed his first shell and tube heat exchanger, FastPrint Publishing, New York NY,1965
this pdf was very helpful but understanding the shortforms and symbols are difficult it would be great to know all that in detail