
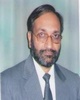
- Open Access
- Authors : Dr. J P Yadav , Dr. Devendra Kumar , Pratyush , Devendra Singh
- Paper ID : IJERTV11IS030128
- Volume & Issue : Volume 11, Issue 03 (March 2022)
- Published (First Online): 31-03-2022
- ISSN (Online) : 2278-0181
- Publisher Name : IJERT
- License:
This work is licensed under a Creative Commons Attribution 4.0 International License
Design, Development and Performance Evaluation of Paddy Thresher
Dr. J P Yadav1, Dr. Devendra Kumar2 , Pratyusp and Devendra Singh4
1,2 Professor, Faculty of Agril Engg & Tech, (C.S.A. Univ of Agri & Tech, Kanpur) Campus Etawah, U.P.
4 Faculty, Faculty of Agril Engg & Tech, (C.S.A. Univ of Agri & Tech, Kanpur) Campus Etawah, U.P.
3 Faculty, Department Civil Engineering, Kamla Nehru Institute of Technology, Sultanpur, U.P.
Abstract:- Manual threshing of paddy in the season have always been cumbersome and drudgerious with so much of postharvest losses. The literature reveals that there are approximate 13-15 % of postharvest grain losses in totality in India. Many times, natural calamities also enforce farmers to suffer the loss for want of traditional old pattern of threshing mechanism. Looking into all the aspect of post-harvest losses and to reduce drudgeries especially for small farmers. A power operated paddy thresher Mk-II with some modification as introducing rocking wheels for transportation and poly sheet cover over paddy thresher Mk-I has been designed and developed whose operating parameter are closer to the standard one. This paddy thresher is also integrated with winnowing mechanism. The performance evaluation is carried out on P10 and PUSA 1509 of paddy varieties available locally. This thresher has the threshing efficiency, cleaning efficiency, grain ratio and percentage of un-threshed grain 97.49%, 86.45%, 0.41 and 2.41% respectively.
Key words: Paddy; paddy varieties; paddy thresher machine.
-
INTRODUCTION
Rice is a staple crop grown in varying climate and altitude across India. Its growing seasons differ based on varying temperature, different rainfall patterns, kind of soils, availability of water and other agro climatic conditions. The temperature of southern and eastern part of the country favours the cultivation of rice round the year. The southern and eastern states of India generally take two to three crops in a year whereas western and northern states receive high rainfall followed by low temperature in winter. Here one crop of rice is cultivated only from May to November. The three seasons of sowing paddy in India are namely autumn, winter and summer. All the three seasons have been kept according to the harvesting season of paddy as autumn paddy is known as pre- kharif paddy. Pre-kharif paddy is harvested between September to October.
Pre-kharif paddy is sown during May to August while the sowing time varies from state to state, depending on the weather conditions and rainfall pattern. Autumn rice crop is known as Bhadai in Bihar, Beali in Odissa, Aus in West Bengal, Ahi in Assam, Sornawari in Tamil Nadu and Virippu in Kerala. About 7 percent paddy is cultivated in this season. The duration of varieties sown in this season is 90 to 110 days. In India, the main paddy growing season is in Kharif season and is known as winter rice. Winter rice is known as Agahani in Bihar and Uttar Pradesh, Sali in Assam, Sarrad in Orissa, Aman in West Bengal, Sarava in Andhra Pradesh and Telangana, Samba in Tamil Nadu and Mundakan in Kerala. About 84% of the country's cultivation is done in this season
and most of the medium to long duration varieties are sown in this season. Paddy which is grown in summer comes under Rabi crop. It is called as Garma in Bihar, Boro in Assam and
West Bengal, Dalua in Orissa, Dalwa in Andhra Pradesh, Navarai in Tamil Nadu and Punja in Kerala. The sowing time of summer paddy is from November to February and the harvesting time is from March to June. The summer rice covers only 9% of the area and quickly maturing varieties are sown in this season.
Paddy can be grown in any diverse soil and climatic conditions, be it alkaline or acidic soil by its physical adaptability. It is seen paddy in India is grown from below the sea-level at Kuttanad area of Kerala to an elevation of two thousand metres in Jammu and Kashmir, hills of Himachal Pradesh, Uttarakhand, and NE states. The rice growing area under cultivation in India can be divided into five zones such as North Eastern, Eastern, Northern, Western, and Southern zones. Paddy crop is the main crop of Uttar Pradesh which is sown in about 5.90mha and accounts for 13.5% share of the whole countrys yield. India trades rice on a large scale in the world. India produces Basmati rice and other varieties. The ten paddy producing states of India are viz. West Bengal, Uttar Pradesh, Andhra Pradesh, Punjab, Tamil Nadu, Bihar, Chhattisgarh, Odisha, Assam, and Karnataka in the descending order. Rathod et al. (2015) studied on Impact of MAVIM activities on empowerment of rural women. Annu et al. (2021) Utilized pattern of social media among the postgraduate students.
A threshing machine is a part of the farm equipment that separates the paddy grain from the straw. Before the invention of these machines, paddy threshing was done by hand which consumed a lot of effort and time. The mechanisation of the threshing process has reduced the difficulty of farm labour to a great extent. With the Scottish engineer Andrew Meikles first invention of the threshing machine, later developments at threshers and mechanical reapers continued until the 19th century, to the extent that grain production began to be produced at a low cost. Today the work of threshing starts with a cylinder and concave, the cylinder has sharp serrated bars and is rotated at a high speed of about 500 rpm so that the bar continues to beat the paddy and separate the grain from straw. The concave curve is so designed so that it matches the curve of cylinder and serves to hold the beaten grain and release the grain from the straw and chaff. A simple cylindrical drum called threshing tool having wire loop rotates with power attachments separated the grain from the stalk panicles being
stroked between the wire loops and if fan is conveniently fitted does the winnowing also. Such threshers are very popular as this is easily designed by local artisans for small farm farmers.
Various designs and developments have been done in the interest of evaluating the effectiveness of the threshers, in this context some researchers have worked on it and given their finding as Cain and Holmes (1977) developed machine for soybean like paddy thresher and evaluated it on the impact damage of rice grains and concluded that the impact damage depends on grain moisture and velocity of impact. Bartsch et al. (1979) explained that dynamic events occur in threshing and conveying operations during harvesting, often involving a large momentum exchange during grain collisions with machine components. Paulsen (1979) said the common cause of damage in all grain-management studies is the particle velocity just before impact and the hardness of the surface against which the impact occurs. As the impact velocity increased, the percentage of split and finer material increased. Seeds that had a low percentage of post-impact division also had high germination. Nave (1979) explained that a rice producer should be concerned with threshing and separation efficiency while avoiding undue impact damage to the grain. Efforts to reduce threshing losses while increasing efficiency have resulted in the development of rotary threshing equipment. Newberg et al. (1980) designed a machine for threshing rice and also evaluated the damage caused to the rice grains by rotary and conventional threshing mechanisms. Three different combines were tested under field conditions at four circumferential (peripheral) velocities. The percentage of splits was significantly higher for conventional cylinders than for single or doublerotr threshing mechanisms at the same peripheral speed. The percentage of segmentation increased as the peripheral threshing speed increased for all three threshing mechanisms. However, the increase in division was less with the rotary threshing mechanism than with conventional cylinder threshing. Separation loss with rotary combines was significantly higher at the slowest rotor speeds. Vejasit (1991) compared the performance of the rasp bar and peg-tooth threshing drum of axial flow thresher for rice crop. The results indicated that amount of grain placed on threshing unit was not significantly different for both cylinder at all cylinder speeds and feed rates. Rani et al. (2001) studied the plot combine for threshing paddy crop and stated that the maximum threshing efficiency was 97.2% at 8.9% wet bulb grain moisture content and 10.1 metre per second cylinder speed. Yadav et al. (2019) researched prototype paddy thresher cum winnower.
The design of paddy thresher (Mk-II) is a modification over paddy thresher Mk-I by increasing overall dimension, higher tool shaft speed, increased drum size dimension, a greater number of aluminium wire loops, winnowing fan run by motor and robust large size wheels for easy transportation. Poly sheet covers are used to protect the grain flown away and falling on motor.
-
DESIGN AND DEVELOPMENT OF PADDY THRESHER (Mk-II)
The thresher comprises of Stand with required dimensions of mild steel angle, drum made of four strips folded circulatory separated at 31.33 cm each and 13 straight strips separated 11 cm from each other. In drum, at circular end, for the support,
thin small strips are connected to the hub. Drum is mounted on the solid shaft through hub and bearings. Wire loops mounted on drum strips are used to remove the paddy from panicle. The mild steel shaft carrying the drum bearing the bending and twisting load is designed for its diameter based on maximum shear stress theory. The wheel, fan, pulley, V-belt, poly sheet and ball bearings are mounted as per required specification. The power required is calculated keeping factor of safety as 2 for induction motor for required maximum tool shaft speed of 578 rpm. A hub of diameter 5cm is supported by six strips of equal length of 18 cm and is welded at the centre of circular ring at each end. Aluminium alloy wire loop are welded on two consecutive strips at angle of 7 degrees from the right side of normal in such pattern that these teeth are separate from each other at distance of 2 cm and total number of teeth in these two strips are 12. The design parameters of shaft, motor power, pulley, length of the belt; etc. are calculated using following formulae and the complete specification of the proto type Paddy Thresh (Mk-II) is tabulated below
D3 = 16/Ss[(Kb×Mb)2 +(Kt×Mt)2]1/2
Assuming, Kb, Kt as 2 and factor of safety 2 T = F×R
Speed ratio =D2/D1 = N2/N1
L = { (r2 + r1) + 2x + (r2 – r1)2/x} P = 2NT/60
HP = P×1000/746
Table 1: Specifications of Paddy Thresher Mk-I & Mk-II
Particulars
Specifications.
Type of machine
Power operated paddy thresher cum
winnower (Mk-I)
Stand (Frame), MS angle
Dimension: 1120mm x 620mm x
850mm
Overall dimension (in mm)
Length x width x height
1130 x 695 x 1304
Power Unit
Power Unit
Electric motor
Horse power (HP)
2 HP, 1.5 kw, Single phase induction
motor
Revolution per minute (rpm)
1440 RPM
Required maximum tool shaft speed from 1440rpm electric
motor
530 rpm (calculated)
Pulley
Number of Pulley
2
Diameter of Driving pulley
76.70 mm
Diameter of Driven pulley
203.2 mm
Bearing
Type of bearing
Ball Bearing.
Number of bearings
2
Diameter of bearings
80/80 (internal diameter of ball bearing is 40 mm)
Shaft
Uniform cross-section transmission shaft (hollow) made up of mild steel
Diameter of transmission shaft
40 mm (outer dia), 38mm (inner dia)
Electric blower
With regulators, fans dust flown out
Blades size
406 mm
Speed
1440 rpm
Belt: Size
A55 (length and width 1397×12.7mm)
Wheel: No. of wheel
4
Specifications of Paddy Thresher (Mk-I)
Specifications of Paddy Thresher (Mk-II)
Particulars
Specification
Types of machines
Power operated paddy thresher cum winnower (Mk-II)
Overall Dimension
Stand (Frame), MS angle
Dimension: 1240mm x 760mm x 885mm
Power Unit
Power Unit
Electric motor
Horse power (H.P.)
2 HP, 1.5 kw, single phase induction motor
Revolution per min (R.P.M.)
1440
Required maximum tool shaft speed
578 rpm
Pulley
No of pulley
3
Diameter of motor pulley (mm)
102
Diameter of shaft (mm)
254
Diameter of fan pulley (mm)
102
Bearing
Types of bearing
Ball Bearing
No of Bearings
2, dia 25.4 mm
Shaft
Uniform cross-section solid transmission shaft made up of mild steel
Diameter of transmission Shaft
40 mm, length 114 cm
Fan
Blades size (mm)
340
Speed (R.P.M)
1440
Belt
No of Belts
2
Size of Belts
B55 and B66 included angle 30 to 400
Wheel
No of Wheel
4
Threshing Tool
Types
Cylindrical drum having 13 strips (25mm x 3 mm) longitudinally mounted straight, spaced 11 cm apart and 4 strips circularly spaced at 31.33 cm
No of cylindrical drum
1
Length (mm)
940
Diameter (mm)
460
Types
Wire loop
Length of wire loop (mm)
180
Corner length (mm)
1 mm on both side
Total no. of aluminium alloy wire loop on drum
156 twisted at 45O
Poly-sheet
Length (mm)
1219.2
Width (mm)
914.4
Fig. 1a Paddy Thresher (Mk-I)
Fig. 2b Paddy Thresher (Mk-II)
-
EXPERIMENTATION AND EVALUATION
The experimentation and evaluation carried out following the Indian Standard Test Cde for power thresher IS: 6284-1985 for the testing of Paddy Thresher (Mk-II) on two varieties of paddy P10 and 1509 PUSA. The test samples were taken after dust and dirt removed from thresher before starting the testing. P10 variety is known for light in weight and weaker than 1509 PUSA variety but 1509 PUSA variety of paddy is heavier and stronger than P10 variety of paddy. Moisture content is expressed in percent by weight of water contained in paddy or rice. Moisture content is commonly referred to as the wet base which means the total weight of the grain including water. Here the moisture content in paddy stalk and grain is used to
be within range. The threshing machine is ensured continuous and regular feeding without introducing excessive quantities of product to prevent too many un-threshed panicles and plant residues to avoid. a second threshing. With permissible relative humidity, sunny weather and local temperature of 35.5 °C the testing carried out.
Testing of P10 and 1509 PUSA variety of paddy
The observation of threshing of P10 variety of paddy-on- paddy thresher (Mk-II) is tabulated below in the form of independent and dependent parameters like total weight of paddy (W), weight of grain (Wg), weight of dust (Wd), weight of straw (Ws), weight of un-threshed grain (Wu), threshing efficiency (t), cleaning efficiency (c), grain ratio (GR), and percentage of un-threshed grain using following formulae.
C=W/T, where, C = Capacity of machine, kg/h; W= Weight of paddy fed in the machine, kg; T= Time taken for threshing;
t = [Wg/ (Wg + Wu)] ×100
c = [Wg/ (Wg + Wd)] ×100
G.R. = Wg/ W
Percentage of un-threshed grain = [Wu/ (Wg + Wu)] ×100% Paddy Thresher (Mk-II) trial on P10 and PUSA 1509 variety of paddy
Paddy thresher (Mk-II) is tried on different variety of paddy like P10 and Pusa 1509 for its parametric performances like threshing efficiency, cleaning efficiency, cleaning efficiency, grain ratio, and percentage of un-threshed grain is shown at Table 2 and 3.
Table 2, 3 and fig. 3 reveal that the dependent threshing parameter like threshing efficiency and cleaning efficiency is higher for Pusa 1509 variety of paddy than P10 variety of paddy whereas grain ratio is same in both varieties. It also revealed the threshing capacity for P10 is higher than Pusa 1509 i.e., 1484.54 kg/h and 13.78.54 kg/h respectively when the tool shaft speed (drum speed) is 578rpm.
Comparison of Paddy Thresher Mk-I and Mk-II
The power operated paddy thresher Mk-II is compared in terms of capacity, thermal efficiency, cleaning efficiency and percentage of un-threshed grain which are shown at table 6. The table reveals that paddy thresher Mk-II has higher threshing capacity than paddy thresher Mk-I however its cleaning efficiency is lesser than Mk-I. This is because Paddy thresher Mk-I has winnowing system having two blowers whereas Mk-II has only one fan for winnowing (cleaning). The portability of Mk-II is better than Mk-I as the wheels fitted in Mark-II is larger size for easy maneuverings.
Table 2: Data obtained on Paddy Thresher (Mk-II) from P10 variety of paddy
Exp. no.
Speed of drum (rpm)
Total weight of Paddy, (kg)
Time (min.)
Weight of Grain, (kg)
Weight of un- threshed grain, (kg)
Weight of Dust, (kg)
Weight of Straw, (kg)
Threshing efficiency (t)
Cleaning efficiency (c)
Grain ratio
Percentage of un-threshed grain
1.
578
80
4.07
30.50
1.05
5.31
43.74
96.60%
85.19%
0.38
3.32%
2.
578
136
5.08
54.06
0.92
7.11
73.48
98.33%
88.32%
0.40
1.66%
3.
578
160
6.15
66.80
1.20
9.28
82.72
98.23%
86.12%
0.42
1.76%
4.
578
200
8.00
87.50
1.00
13.75
97.75
98.23%
86.41%
0.42
1.12%
Average values
144
5.82
59.71
1.04
8.86
74.42
97.84%
86.54%
0.41
1.96%
Table 3: Data obtained on Paddy Thresher (Mk-II) from 1509 PUSA variety of paddy
Exp. no.
Speed of drum (rpm)
Total weight of Paddy, (kg)
Time (min)
Weight of Grain, (kg)
Weight of Un- threshed grain (kg)
Weight of Dust, (kg)
Weight of Straw, (kg)
Threshing efficiency (t)
Cleaning efficiency (c)
Grain ratio
Percentage of un-threshed grain
1.
578
120
5.01
53.40
1.38
8.10
57.12
97.48%
86.82%
0.45
2.51%
2.
578
144
6.01
68.40
1.69
10.58
63.32
97.58%
86.59%
0.48
2.41%
3.
578
160
7.09
47.20
2.00
8.00
102.80
95.93%
85.50%
0.30
4.06%
4.
578
200
9.08
83.50
2.10
13.00
101.40
97.54%
86.52%
0.42
2.45%
Average values
156
6.79
63.12
1.79
9.92
81.16
97.13%
86.35%
0.41
2.85%
Lot-I: Comparision of parameters of p10 and pusa 1509 paddy variety
p-10 Pusa-1509
180
160
140
120
100
80
60
40
20
0
156
Total wt of Time, min Weight of Weight of Weight of Weight of Threshing Cleaning Grain ratio Percentage of
paddy, kg grain, kg unthreshed dust, kg straw, kg efficiency (t) efficiency (c) un-threshed
grain, kg grain
Fig. 3 Threshing Parameters of Paddy Thresher (Mk-II)
144
81.16
74.42
97.84 97.13
86.54
86.35
59.71
63.12
9.92
0.41
5.29
0.41
5.82
1.04
1.79 8.86
1.96
2.85
Parameters values
-
CONCLUSION
The design and fabrication of Paddy Thresher (Mk-II) has been successfully carried out following Indian Standard Test Code for power thresher IS: 6284-1985. The parameters obtained for threshing different varieties of paddy are quite closer to the standard paddy threshing. The machine is compared for its performance with paddy thresher Mk-I with following conclusions-
-
The performance of Paddy Thresher Mk-II is better than Paddy Thresher Mk-I, its threshing capacity is more than paddy thresher (Mk-I) and the total losses (damged + un-threshed grains) decreased.
-
The threshing efficiency and cleaning efficiency of Paddy Thresher Mk-II is higher than Paddy Thresher Mk-I. The un-threshed grain percentage by Paddy Thresher Mk-II is lower than Paddy Thresher Mk-I.
-
Paddy thresher is simple, robust, cost effective and much useful for small farm. This can be modified to solar power.
ACKNOWLEDGEMENT
The author is thankful to Shri Sarvesh Tripathi, Lab Technician (welding) and B. Tech. students, viz. Abhishek Pandey, Atul Singh, Jishan Siddqi, Gaurav Pratap Yadav, Vinod Kumar Patel, and Abhishek Kumar Soni, for their contribution in designing and fabrication of Paddy Thresher Mk-II for its performance evaluation under my supervision. The author also gratefully acknowledges the UPCAR, Lucknow, for financial support under "Central of Excellence in Farm Machinery".
CONFLICTS OF INTEREST
The authors declare that they have no conflicts of interest.
REFERENCES
[1]. Annu, G. and Sisodia, S.S. (2021). Utilization pattern of social media among the postgraduate students. Indian Res. J. Ext. Edu. 21 (2&3): 26-32. [2]. Bartsch, J. A., C. G. Haugh, K. L. Athow and R. M. Peart. (1979). Impact damage to soybean seeds. Transactions of the ASAE, 79(15):3037-3042. [3]. Cain, D. F., and R. G. Holmes. (1977). Evaluation of soybean seed impact damage. Transactions of the ASAE, 71(8):1552-1556. [4]. Nave, W. R. (1979). Soybean harvesting equipment: Recent innovations and current status. In F.T. Corbin (Ed.) World soybean research conference II: Proceedings. Westview Press, Boulder, Co. pp.433-449. [5]. Newberg, R. S., M. R. Pualsen and W. R. Nave. (1980). Soybean quality with rotary and conventional threshing. Transactions of the ASAE, 23(2):303-308. [6]. Paulsen, M. R. (1979). Fracture resistance of soybeans to comprehensive loading. Transactions of the ASAE, 21(6):1210-1216. [7]. Rathod, M.K. and Damodhar, P. (2015). Impact of MAVIM activities on empowerment of rural women. Indian Research Journal of Extension Education. 15 (1), 8-11. [8]. Rani, M., N. K. Banal, B. S. Dahiya and R. K. Kashyap. (2001). Optimization of machine-crop parameters to thresh seed crop of chickpea. International Agricultural Engineering Journal, 10(3&4):151-164. [9]. Vejasit, A. (1991). A comparison between peg-tooth and raspbar cylinders for soybean threshing using axial flow thresher. M. Eng. Thesis, Khon Kaen University, Khon Kaen, Thailand (unpuplished). [10]. Yadav JP, Manoj Kumar, Devendra Kumar, Evaluation of Prototype Paddy Thresher cum Winnower Procc. of International Conference on Advancement in Mechanical engineering: challenges towards sustainable development (ICAME 2019), Jyoti Engineering College, Thrissur, Kerala, India. April 10-11, 2019