
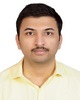
- Open Access
- Authors : Narayan V. Naik , Tanmay U. Naphe , Anmol A. Raut , Sagar G. Somvanshi, Ajay Kashikar
- Paper ID : IJERTV10IS050207
- Volume & Issue : Volume 10, Issue 05 (May 2021)
- Published (First Online): 22-05-2021
- ISSN (Online) : 2278-0181
- Publisher Name : IJERT
- License:
This work is licensed under a Creative Commons Attribution 4.0 International License
Design and Development of Active Aerodynamic Winglet
Narayan V. Naik1, Tanmay U. Naphe1, Anmol A. Raut1, Sagar G. Somvanshi1, Ajay Kashikar2
1Student, Department of Mechanical Engineering, LTCoE, Navi Mumbai, India
2Asst. Professor, Department of Mechanical Engineering, LTCoE, Navi Mumbai, India
Abstract This project (concept) is an attempt to increase the performance of high-speed motorcycles used in road-racing events such as MotoGP by focusing on factors such as improving the safety and working on critical aerodynamic properties such as lift and drag produced due to the force of air on the vehicle when in motion. This is to be achieved by attaching an active aerodynamic winglet on either side of the motorcycle which will move according to the requirement concerning the different angle of attacks of wind. The main functions of the winglets are to improve the traction of the motorcycle by increasing its downforce and improving the cornering ability of the vehicle. It contributes to the braking effect by acting as an air-brake when the drag on the winglet is maximum. Testing of many aerofoil shapes has been done in analysis software and the best suitable shape has been selected as per our need. Supportive components such as gear and bearings have been designed, and the electrical circuit required for the actuation of the winglet has been made. Proto-type of the above model has been made by three dimensional (3D) printing process for demonstration and all required steps are carried out to obtain the desired results.
Keywords High-speed motorcycles, active aerodynamics, traction, aerofoil, ANSYS, Proto-type, 3D Printing.
-
INTRODUCTION
This project is intended for use in high-performance motorcycles or road racing motorcycles. which includes all types of motorcycles that may compete by doing laps or sprint races on paved, closed down, purpose-built race tracks. The cornering ability and the straight-line characteristics of a motorcycle are both tested on the racetracks. These winglets on these motorcycles used in races like MotoGP will help in increasing the traction and thereby gaining the high speed of the motorcycle on the road. The automatic airbrake based on the acceleration of the motorcycle slows down the motorcycle more as when compared to the brakes acting alone by increasing the drag. The shape of the aerofoil has the greatest impact on the aerodynamic performance of the motorcycle. The effect of the various shapes of aerofoils has been studied and also the angle of attack of the aerofoils has been studied for their effect on the drag and lift magnitude produced by them. The modeling aspects of active aerodynamics concepts are been studied. The rapid prototyping is done using a 3D printing tool. To find the relevance of this topic in day-to-day life it is been found that motorcycles have led to a large number of accidents per year as compared to those involving 4 wheeled vehicles. According to motorcycle crash statistics produced every year, the majority of motorcycle crashes are caused due to facing unexpected obstacles in the path causing collisions due to insufficient braking time. Thus, this paper
serves as a means to overcome this issue and provide a technological solution to the problems of motorcyclists.
-
Problem definition
The existing active winglet technology only exists in cars and requires complex mechanical design for actuation. The winglet technology in motorcycles is limited to MotoGP motorcycles with fixed wings. The amount of downforce is lesser in existing fixed winglets are lesser than the active winglets as its angles cant be changed. Therefore, to increase the downforce and improve the braking effect of the vehicle, modifications should be done in the design and try to add winglets with variable angles of attack on every motorcycle. This will result in increased safety of the rider and also improving the performance of a motorcycle.
-
Objective
To build an active aerodynamic winglet that increases the downforce of motorcycles in case of straight-line riding and helps in the cornering performance of a motorcycle and acts as an airbrake in case of brake being applied by the rider. Compare different types of National Advisory Committee for Aeronautics (NACA) aerofoil for their characteristics of lift and drag produced by them for the same chord length. Build the electronics that control the actuation of the motors automatically based on the acceleration of the motorcycle.
-
-
LITERATURE REVIEW
The purpose of this study is to find the way the aerodynamics of the motorcycle affect the vehicles ride quality and what effects do the winglets used have on the motorcycle. The goal is to find how different characteristics of the winglets affect the performance of the motorcycle, finding out the benefits these winglets provide in the safety of the rider.
The author Vojtech Sedlak[1] worked on the shape of the motorcycle during the early days of the Industrial revolution which would give the maximum aerodynamics. He tested basic and complex designs such as bi-plane wings, multiple anhedral angled wings, etc. in Computational Fluid Dynamics (CFD) softwares experimenting for various wing geometrys and concluded that the aerofoil design and its position affect the results most.
K.K. Koay and W.C. Tan[2] had published and presented a paper on Computational Fluid Dynamics study for aerofoil in the Second National Conference in Mechanical Engineering organized by University Malaysia Pahang. The whole idea behind the paper was the study of different boundary conditions for CFD software to generate different flow patterns. Also, the lift and drag coefficient was found
out through CFD and verified with the theoretical results for the angle of attack ranging between 0° to 20°.
Venkata Aditya Sripathi [3] studied [the impact of active aerodynamics on motorcycles using computational fluid dynamics simulations] in which he estimated the lift and drag forces for an angle of attack (0º,15º,90º) in CFD software.
Mustafa Cakir[4] studied the effects of spoiler on cars and concluded that the spoiler increased the cornering ability and traction of the vehicle.
Nawan Rosli & Rosli[5] tested a total of 4 spoilers and obtained the results that the spoiler of aerofoil shape has the best effect on the downforce and increase the lift up to 20%.
Devang Nath, Prashant Pujari, Amit Jain, and Vikas Rastogi[6] have worked on Drag Reduction by Application of Aerodynamics Devices in a race car which deals with the new trends and innovations related to the improvement of working and performances of vehicles used for racing. While doing this they have focused on various factors such as the ever-growing hike in fuel prices, stringent norms over environmental policies which are todays major concerns for automotive manufacturers to produce efficient vehicles with low emissions. They have concluded that the most efficient way to deal with this issue is to improve the aerodynamics of the vehicles.
The conclusion that is derived after studying these papers is that the constant evolution in the field of aerodynamics has led to the development of certain devices which has led to the enhancement of the overall aerodynamic characteristics of the vehicles. Our project is also be done with the same objective which will contribute to the safety of the rider and increase its efficiency and vehicle life. Another advantage that will be obtained due to this concept is the reduced fuel consumption and the turbulence caused will be reduced to a fair extent.
- p>METHODOLOGY
The mechanism was decided and the gears were selected as the method to transfer the power from the motor to the aerofoils. The aerofoil along with shaft and gear was attached to the main plate with help of bearings used for smooth operation. The main plate is intended as the mounting on the chassis of the motorcycle. The servo motor was selected for the positioning capability and small size and relatively high torque for its size. The machine elements were designed by calculations and Computational Fluid Dynamics (CFD) software and modeled into 3D Computer-Aided Design (CAD) software. Electronics were designed and modeled on Easyeda circuit design software.
-
Aerofoil shape selection
Aerofoil shape is the cross-section design of wing and is a shape capable of creating lift or an upward force due to difference in velocity of air on two of its surfaces. The aerofoil shape is used to counter the effects of wheelie keep the front wheel firmly on the ground in our project. As all these will be encountered by this shape. Also, various terminologies such as angle of attack, chord, leading and trailing edge, lift and drag co-efficient, and lift and drag forces need to be addressed. The Standard NACA[7] aerofoils were used because of their good documentation, ease of production, and high reliability as they are already in use in the industry.
-
Analysis of aerofoil
Analysis was done for the best shape of aerofoil and the effect of the aerofoil on a motorcycle. Softwares used were XFLR5 and Ansys (Fluent). Due to the CFD analysis, we got to know the forces on the mechanical components such as bearings.
The first step was to find the best NACA aerofoil for lift generation in XFLR5. The second step was to use the best- found aerofoil to do an analysis of its effects on the motorcycle and the components of the mechanism in ANSYS
-
Analysis to find the best shape
The analysis was done to find the best aerofoil that will generate the maximum lift. Firstly the digit no 1 was compared to find the best lift producing aerofoil. Several aerofoils were compared all with the same last 3 digits but the different first digits (see figure 1). Comparing NACA1405, NACA 2405, NACA 3405, NACA 4405, NACA 5405,
NACA 6405, NACA 7405, NACA 8405, NACA 9405.Off all
the aerofoils the NACA9405 was found to produce the best lift (see figure 2)and thus the first digit chosen was 9.
Fig. 1 Aerofoils
Fig. 2 NACA first digit analysis
Then another batch of aerofoils was tested namely NACA9005, NACA 9205, NACA 9405, NACA 9605, NACA
9805. These had the best first digit found i.e. 9 commons in all and the second digit was changed in all aerofoils within regular increments. The best one in the batch analysis of the aerofoils was found to be NACA9405 (see figure 3) and the second digit 4 was obtained the best. The NACA9805 had no clear peak visible hence it was not chosen for our purpose.
Fig. 3 NACA second digit analysis
The last step was to find the third and fourth digits of the best aerofoil with maximum lift. Again a batch analysis of NACA 9402, NACA 9404, NACA 9406, NACA 9408,
NACA 9410, NACA 9412 was performed. These contained the best first and second digits 9 and 4 respectively. The best overall aerofoil was found to be NACA9412(see figure 4).
Fig. 4 NACA third and fourth digit analysis
-
Analysis to find the effect on the motorcycle
The models of the motorcycle with and without various aerofoils were created and were analyzed in CFD software for the changes in effect due to aerofoil at speed of 220 km/h. The following steps were involved in the analysis.
-
Model creation
Model of the aerofoil and the motorcycle with and without aerofoil were modeled in Autodesk Fusion 360 software. The aerofoil is designed in Fusion 360 by importing the curve with a built-in add-on. The aerofoil is then imported in Ansys Fluent and then an enclosure of a cushion of 0.25m is added around the aerofoil on all sides and the motorcycle model with 0.01m on the bottom for every case. The Aerofoil and motorcycle model is then subtracted from the enclosure for obtaining the test surfaces.
-
Meshing
Meshing takes place next with the mesh element size of 1.5. .The various sections and planes of the model are named for further use like the velocity inlet which provides the airflow of 61.111m/s ie 220kmph. the pressure outlet acts as an outlet of the air, the wall is the outer enclosure to contain the flow of air and aerofoil or motorcycle body for the simulation of the flow of air.
-
Setup for CFD calculation
The setup used for the simulation has the model k epsilon and the fluid used is air and velocity of 61.111m/s or 220kmph is set in the software Ansys fluent. The calculations are run for 150 iterations to get accurate results and processing of the system takes place.
-
Solution
The result is obtained in form of velocity magnitude contour which represents the flow of air around the aerofoil and helps us visualize how the flow of air and formation of vortexes takes place.
The form of solution is the report generated can be obtained for moment, forces, and center of pressure. The report for various angles of aerofoils and motorcycle with and
without aerofoil was arranged in a tabulated form for purpose of ease of understanding.
Table 1 Downforce increase on the motorcycle
AEROFOIL ANGLE
DOWNFORCE(N)
DRAG(N)
DOWNFORCE INCREASE (N)
NO AEROFOIL
-2.7857759
-718.42878
0
-91.552754
-722.78061
88.7669781
12
-237.7718
-726.12141
234.9860241
60
-4.9138654
-910.90951
2.1280895
70
133.04268
-978.81463
N/A
80
122.91557
-1044.8332
N/A
90
298.34162
-1079.1288
N/A
Table 2 Drag increase on the motorcycle
AEROFOIL ANGLE
DRAG(N)
DRAG INCREASE (N)
NO AEROFOIL
-718.42878
60
-910.90951
192.48073
Table 3 Analysis on the aerofoil only.
AEROFOIL ANGLE
DOWNFORCE(N)
DRAG(N)
AXIAL FORCE(N)
0
-12.577205
-3.1361697
-0.35306082
12
-29.595873
-7.5205875
-0.54912262
60
-42155766
-64.884985
10.234824
Table 1 shows the improvements in lift produced by different angles of the aerofoil on the wing. The angle of aerofoil of 12 degrees produced the maximum downforce as found earlier in XFLR5 software is found true in the Ansys software. Angles 90, 80, 70, 60were chosen to be analyzed for air brake function but 90, 80, 70 degrees produced an upward force as indicated by the positive force produced in the report. The upward force can reduce the braking capacity by reducing the normal reaction from the ground thereby reducing the friction in the wheels thus these angles were not preferred. Angle 60 degrees produced a satisfactory result and a downward force indicated by negative force in report and drag produced to act as air brake was also found good (see table 2). Table 3 shows the forces acting on the aerofoil alone. They were calculated to find out the forces on components such as bearings.
-
-
-
Calculation and design of machine components
Fig. 5 Gearing arrangement
Following are the calculations included in the design of the components used in the gearbox i.e. gears and bearings that can be seen in figure 5.
-
Gear Calculations
The gears and pinions in the mechanism are designed according to the following formulas
Maximum tensile stress=t = yt / FOS
-
-
Design and assembly of electronic components
Electronics is the main brain behind the working of the system and is the most essential part for it to work correctly. The components used in it are:-
-
Servo motor
Servo motor Mg995r is intended to be used for the actuation of the wings due to its relatively high torque of 15kgcm as compared to other servo motors. It consists of
Reduction ratio – = 2
1
(1)
wires with a gnd, vcc (positive), and a signal wire for
Lewis form factor: Yp= [ 0.154 0.912 ], (2)
connection with the microcontroller, and coding is done with
It was found that [b ] p x Yp
1
< [
b ]g x Yg (3).
the help of the servo library [8].
-
Microcontroller (Arduino Nano)
Hence, when the pinion is a weaker element it should be designed first.
The module was verified using :
Arduino nano board is being used as a microcontroller for the project because of the board being the standard Arduino and the ability of improvement and upgradability in the circuitry being provided by the board. The A5 and A4 pins
m 1.263
[](4)
on the Arduino are used for connection with the accelerometer
[b ]1Then the gear was Checked for surface contact compressive strength, dynamic load, and wear load using formulae:
±1 1 ±1
module and the d3 and d5 pins are used for connections with the servo motor.
-
Accelerometer (MPU6050 module)
MPU6050 is an accelerometer and gyroscope module
c = 0.74
[]
(5)
used for the accelerometer to find the acceleration in the Y direction i.e. in our case the forward and backward direction
Fd = Ft x Cv (6)
to find when the motorcycle has accelerated or decelerated and actuates the motors according to it and needs a library to
Fd = Ft [ 0.164 (+)
0.164 +1.485+
] (7)
be installed in Arduino IDE.
-
XL4015 voltage converter
Fw = Dp x Q x k x b (8)
In our case, we took Acrylonitrile Butadiene Styrene (ABS) material for our gears with no of teeth of gear equal to 25 and teeth on pinion equal to 15 with a diameter of gear and pinion equal to 38mm and 25 mm respectively with both having face width equal to 12mm. The gears and pinions were found safe with our application with a motor of power equal to 5.79W
-
Design of Deep Groove Ball Bearing
The design of bearing is done with the following formulas of finding the life in million revolutions, equivalent load, etc.
The life in million revolutions and hours can be found out using the below formulas
This component is a step-down buck converter used for the function of regulating the higher voltage of the motorcycle battery of 12v to constant 5v for the microcontroller, servo motor, and accelerometer to function.
-
-
Copper clad sheet (for circuit board)
This will be used for the assembly of electronic components
2) Schematic of the circuit
L mr = 60NLhr
6
6
106
(9)
Lhr
= Lmr10
60N
(10)
Pe = [X V Fr + Y Fa]s (11)
1
C =Pe (L90 )k (12)
For our application with Fa and Fr values of 10.235N and 803.861N bearing SKF607 was found the best with necessary dimensions and life of bearing was found to be 7527 hours.
Fig. 6 Schematic of the circuit
The connections of the parts can be seen in the schematic diagram as seen in figure 6. The screw connector will be used to connect the circuit board to the battery with a 12v lead acid battery which is present inside the motorcycle .it is used due to its ability to carry a large amount of current and being able to be mounted on a circuit board. The XL4015 is used to convert 12v to a stable and precise 5v dc voltage needed for
sensitive electronics as the motors, Arduino, and the Mpu6050 accelerometer. The Arduino is powered through the vin and gnd pins and communicated with the motors through D6 and D9 pins capable of outputting a pulse-width modulated or PWM signal needed for the servo motors. The accelerometer is communicating with the Arduino through the A4 and A5 pins of the Arduino which are connected to SDA and SCL pins respectively communicating with the i2c protocol of the Arduino which enables multiple sensors to share data with only 2 pins of the Arduino. All the components are to be mounted on the circuit board manufactured with the header pins to be able to remove a single component without unsoldering the component in case of damage to the component in any case of a motorcycle accident or mishap. The code is written in the Arduino ide software and executed first before uploading on the microcontroller. The microcontroller can also communicate with the computer is connected to it with the help of a USB and communicate about a damaged component or a misbehaving component.
Model of the PCB design
The 3D model and 2d model of the PCB have been designed with EasyEDA circuit design software. The Printed circuit board will be manufactured using the toner transfer method to print the circuit on blank copper clad board and then treating the board using chemical etching with ferric chloride FeCl3.All the components will be soldered using solder wire and a soldering iron. The code has been designed with the Arduino ide software and using the adafruit servo library and accelerometer library which helps the accelerometer communicate with the Arduino nano.
Fig. 7 Circuit prototype on a breadboard.
The prototype has been made on a breadboard as in figure 7 and tested with servo motors and is found to work. The mpu6050 which is an accelerometer provides the value of acceleration to the Arduino and Arduino is controlling the motors according to the value provided by the accelerometer. The motor when accelerating ie having acceleration in a forward direction greater than zero has a position that corresponds to the aerofoil shape being flat. The motor makes the aerofoil move to an angle of 60 degrees when the motorcycle is decelerating.
-
-
CAD modeling
All parts were modeled and digitally assembled using Fusion 360 CAD software. The aerofoil add-in for generating a cross-section sketch of aerofoil NACA 9412 was used. The
side shield for reducing the formation of the vortex was also modeled.
We used top, front and side view images of a motorcycle and the images were imported into the CAD software Fusion 360. We made a sketchoverlay using these images and made all of the views. Extrusion was used and obtained intersecting model from all three sketches. The wheels were made separately and added to the body. The aerofoil was then added to the motorcycle body at different angles of attack. This model was used for analysis in Ansys software
Custom mounting for gears, bearings, shaft, and motor on the rectangular pipe was printed on a 3D printer and then assembled. We used rectangular pipe and squared U bolt for mounting on the motorcycle and we cut a small section of the rectangular pipe to ease the installation process with nut and bolt.
-
3D printing of the parts
The parts were modeled and 3D printed using a 3D printer at a local 3D printing services shop using PLA filament and the settings explained below. The 3D-printed parts were printed with supports for the holes to maintain their accuracy. Slicing for 3D printing custom mounting was done using the Flash Print slicer as seen in figure 8.
The preprocessing takes place before the manufacturing of the aerofoil .the orientation of the model selected is vertical because it provides the best possible strength in a Fused Deposition Modeling (FDM) 3D printer. The orientation provides strength to the gear and reduces the support material required to a lesser extent than when horizontal. The slicing is the technique to divide the model into several layers and the specifying of the amount of infill needed for the optimal strength is decided .infill is the actual amount of the model which is filled with the thermoplastic like a Polylactic Acid (PLA) or (ABS) filament used in case of FDM 3D printing in our case.
The following parameters were set in the 3D printer to obtain a good quality print as seen in figure 9.
-
Material PLA
-
Infill density 20% with the 3D pattern.
-
High surface quality with layer height 0.12 mm.
Fig. 8 Slicing Fig. 9 3D printed part
-
-
Final assembly
3D printed parts were cleaned and threaded brass inserts were fitted by heating with soldering iron. Aerofoil was also meant to be 3D printed but was manufactured using foam core and plastic skeleton to provide lightweight construction. U-
bolt and rectangular aluminum tubes were used for assembling every part of the motorcycle as can be seen in figure 10.
All parts were assembled according to our model and fitted on the motorcycle as in figure 11 and powered using an external power source because voltage converter couldnt be obtained due to lockdown and code was uploaded to the microcontroller and tested and found to be working as per requirements.
Fig. 10 Winglet assembly
Fig. 11 Winglet assembly mounted on the motorcycle
-
-
CONCLUSION
It was found that the use of NACA9412 aerofoils helped to increase the downforce at the regular position while accelerating by 234.986024N and increase the drag while at the braking position by 192.48073N.
NACA9412 was the best shape of aerofoil found during the analysis and was manufactured successfully using foam and plastic skeleton methods.
Arduino Nano and MPU6050 were successfully used to automatically actuate the servo motors and the Arduino development platform was found tremendously helpful in our project.3D printing greatly reduced the manufacturing time as well as the cost to build a custom part in PLA plastic.
NOMENCLATURE
T – Torque of the motor used.
Np and N1 Speed of pinion in rpm. Ng and N2 Speed of gear in rpm.
P Power in Watts.
i Reduction Ratio of gears.
Z1 Number of teeth on Pinion. Z2 Number of teeth in gear.
Pressure angle of Standard tooth profile. b Design Bending Stress in kgf/cm2.
c Design surface stress in kgf/cm2.
Yp, Yg Lewis form factor for pinion and gear. m Module in mm/cm.
[ Mt ] Design twisting moment. Mt Nominal twisting moment. Kd Dynamic load factor.a Centre distance between pinion and gear. E Youngs Modulus.
Fd Dynamic load in kgf. Ft Transmitted load in kgf.
Fs Strength of gear tooth in kgf. Cv Barth velocity factor.
Vm Mean velocity in m/s. b Width of the tooth.
Dp, Dg Diameter for pinion and gear. k Load stress factor.
h Height of the tooth. Fa Axial load.
Fr Radial load. N Speed in rpm.
Lmr Life of bearing in million revolutions. Lhrs Life of bearing in hours.
Pe Equivalent Dynamic load. X Radial factor.
Y Thrust factor.
V Inner or Outer race factor. S Service factor.
Co Static capacity of bearing in kgf. C Dynamic capacity of bearing in kgf.
REFERENCES
-
Vojtech Sedlak, Motorcycle Cornering Improvement: An Aerodynamically Approach based on Flow Interference, Royal Institute of Technology (2012).
-
Wee Choon Tan, Computational fluid dynamics study for aerofoil, University Malaysia Pahang, December 2010.
-
Aditya Sripathi, The Impact of active aerodynamics on motorcycles using computational fluid dynamics simulations theses, dissertations, and other Capstone projects,721(2017).
-
Mustafa Cakir, Cfd study on aerodynamic effects of a rear wing/spoiler on a passenger Vehicle, December 2012.
-
Nawam, Muhammad & Mohd Rosli, Mohd Afzanizam & Mohd Rosli, Zulkifli & Azwar, Nor & Rosli, Syahila & Akademia Baru, Penerbit. Simulation Study on the Effect of Rear-Wing Spoiler on the Open Aerodynamic Performance of Sedan Vehicle. 146-154 (2018).
-
S. Nath, Devang & Pujari, Prashant & Jain, Amit & Vikas, Rastogi., Drag Reduction by Application of Aerodynamic Devices in a Race Car. 10.21203/rs.3.rs-60516/v2 (2020).
-
Marzocca, Pier. "The NACA airfoil series" (PDF). Clarkson University. July 2016.
-
Shah, Jainil, Arduino-based servo motor control. 10.13140/rg.2.2.19317.06883 (2016).