
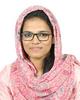
- Open Access
- Authors : Bismi M Buhari , Abhijith S , Aparna B Lal , Joseph Samuel, Sarath S
- Paper ID : IJERTV10IS070113
- Volume & Issue : Volume 10, Issue 07 (July 2021)
- Published (First Online): 16-07-2021
- ISSN (Online) : 2278-0181
- Publisher Name : IJERT
- License:
This work is licensed under a Creative Commons Attribution 4.0 International License
Design and Analysis of Flyover
Bismi M Buhari¹
Assistant Professor Department of Civil Engineering
Musaliar College of Engineering and Technology Pathanamthitta, Kerala,India
Abhijith S2, Aparna B Lal3, Joseph Samuel4, Sarath S5
Student
Department of Civil Engineering Musaliar College of Engineering and Technology
Pathanamthitta, Kerala,India
Abstract- Our project deals with design and analysis of flyover. The manual design of flyover consists of deck slab, longitudinal girder, cross girder, pier, pier cap, abutment, pile cap and pile based on code such as IS: 456-2000 and IRC: 21- 2000. Here the structural analysis is carried out by using STAAD Pro V8i software.
Keywords: Deck Slab; Girder; Pier; Pier Cap; Abutment; Pile; Pile Cap.
-
INDRODUCTION
Flyover may be referred as an overpass, a h high-level road bridge that crosses over a highway interchange or intersection. Flyover is a grade separated structure connects road at different levels for the purpose of reducing vehicle congestion. This project topic deals with the analysis of flyover at Kayamkulam Haripad road using staad pro v8i and manual designing.
-
OBJECTIVE
-
Analyse need of flyover at the proposed site.
-
Creating model using STAAD Pro V8i.
-
Designing the flyover manually and using STAAD PRO.
-
-
STRUCTURAL INFORMATION
The flyover consists of number of spans with columns (piers), deck slab, girders and abutments etc. Total hight of the structure provided as 6.25m. Grade of concrete and steel provided as M35 and Fe415 respectively. Diameter of the pier taken as 2m. Thickness of the deck slab 0.3m provided. Width of the carriage way is 7.5m
Fig. 2: 3D diagram of the structure
-
LOAD SPECIFICATIONS
Dead load includes self-weight of the column, slab, girders, abutments, etc. Self-weight of the structure was automatically taken from the software. Different kinds of loads may be estimated by using respective Indian Standard Codes of practice.
Fig. 3: Dead load diagram
Fig. 1: Structural diagram Fig.4: Loading diagram of moving load at mid span
Live load moment = 61.52× 3.2 28.222 × 4.36 × 4.36
2 4
= 130.13 kNm
Shear force due to live load
For maximum shear at support the jec class AA
b = La (L a ) + bl
0 lg
A = 4.36 = 2.18
2
l0 = 6.4m
bl= 1.01m
b = 2.728 × 2.18 × (1 2.18
+1.01 = 5.1m
0
0
)
6.4
Fig. 5: Loading diagram of moving load at end span
V MANUAL DESIGN AND STAAD ANALYSIS
-
Design of Deck Slab
Centre to center span = 20m
Width of two-way carriage way = 7.5 m (IRC73:1980, clause 6.4
Width of crash barrier = 450mm (IRC5:1998, Page 50) Wearing coat = 80mm
Loading = IRC Class AA Loading
Depth of slab in assumed to be =300mm Wearing coat = 40mm and 20mm channel bar There for, effective depth = 250
Effective Span =6.4m
1) Dead load calculation
Self-weight of deck slab =24× 0.3 = 7.2KN/m2 Self-weight wearing coat =22× 0.08 = 1.76 Total dead load =7.5+1.76 =8.96KN/m2 Maximum dead load of shear force
Total width = 2.55 +2.05+2.55 =7.15m
Average Live Load = 700× 1.197 × 4.36 = 26.89 kNm2
7.15
R1 = 77.29 kN
R2 = 40 kN
Maximum live load for shear force Vq = 77.24kN
-
Load Calculation
Design Bending Moment,Mu = 1.35 Mg+1.5 Mq
= 1.35 × 45.88 + 1.5 × 130.13
= 257.133 kNm
Design Shear Force,Vu= 1.35 Vg +1.5 Vq
= 1.35 × 28.67 + 1.5 × 77.24
= 154.56 kN
-
Design
Mu limit = 0.138 f1u bd2
d = Mu limit
0.138 fck b
d = 257.133 × 106 = 230 < 300mm
.138×1.5×1000
Hence safe
Ast fy Mu = .87 fy Ast d {1 b d f }
ck
= wl 6.4 2
= 8.96 × = 28.67KN
2
2
2 2
Maximum dead load for Bending Moment =WL
8
6.42
Ast = 2651.88 mm
Use 20mm Ø bars,
Ast = × 202 = 314.15 mm2
4
= 8.96 ×
8
= 45.88 KNM
Spacing = 1000×314.15 = 100mm
2651.88
2) Live load calculation
Angle = 45°
Ast
provided
1000 × 314.15
= = 314.15 mm2
100
Total width of d = 4.36m
Moment = 0.3 Mul + .2Mud = 72.3 kNm
Impact factor (IRC: 6:2016 clause20.6.3 page 50)
Impact factor = 25 – 2510
Astd
Astprovided
=
M
× Moment = 883.2mm2
Impact factor =1.197
9.5
u
Provide 12mm Ø
bar @ 110mm c/c
Effective width load b = × a(1- a ) + b
-
Check for ultimate flexural strength
Ast fy
Ast fy
M = .87 f Ast d {1 } = 298.1 kNm >
lo l
lo = 6.4m
a = lo = 3.2m
u y b d fck
Mu
-
Check for ultimate shear strength
2 V = (. 12 × K (80
U).33)bd
bl=0.85+2× 0.08 = 1.01mm
Width of slab; b = 8.4m
b = 8.4 = 1.31
rdc 1 1
= 197.13 > Vu
Hence safe
lo 6.4
By interpolation, = 2.728
b = 2.728× 3.2 (1 3.2) + 1.01 = 5.37m
6.4
length = 2.075+2.05+2.685 =6.81m
average live load = 700×1.19 = 28.224kN/m
6.81×4.36
K1 = 61.52kN
K2 =61.52kN
Fig. 6: Cross section along shorter span
Fig.7: Cross section along longer span
Impact allowance 20m span above 9m =10% The live load is placed centrally on the span. Bending moment = (5+4) × 700 = 3185 KNm
2
Area of one side = 0.5×1.8×(5+4.1) =8.19 Area of two side = 2× 8.19 =16.38m Mmax = (700/3.6) × 16.38= 3185KNm
Bending moment including impact and reaction factor for
outer girder
= 3185 × 1.197× 0.5536 =2110.6KNm
Bending moment including impact and reaction factor of inner girder B = 3185 × 1.197 × 0.3333
=1270.7KNm
1) Live load shears in girder
For estimating the maximum Live load shear in the girder, the IRC class AA loads
Reaction of w2
Reaction of w1
on girder B = (350×0.45) = 63 KN
2.5
on girder A = (350×2.05) = 287 KN
2.5
Fig.8: Bottom span
Total load on girder B = 350 + 63 =413KN Total load on girder A = 350 – 63 =287KN Maximum reaction in girder B
Reaction on girder B =(470×18.2) = 375.83 kN
20
Girder A
Reaction on girder A = (287×18.2)
20
= 261.17 kN
Fig. 9: Top span
-
-
Design of Longitudinal Girder
-
Reaction factors
Using Courbons theory,
-
Reaction factor at outer girder(A)
Maximum Live load shear with impact factor in Inner girder B = 375.83 × 1.197 =449.87 kN Outer girder A = 261.71×1.197 = 313.27 kN
-
Dead load moments and shear force in main
girder
The depth of girder is assumed as 1400mm Depth of rib = 1.4m
Width of rib = 0.5m
Weight of rib/m = 24×1.4 ×0.5 = 16.8 kN/m
The cross girder is assumed to have the same cross section dimensions of the main girder.
RA = 2W1[1+ 3
3I×2.5×1.1
2I×2.52 ]
Weight of cross girder = 16.8 kN/m
Reaction on main girder = 16.8 × 2.5 = 42 kN/m
= 1.107 w1
-
Reaction factor at inner girder (B)
Reaction from the deck slab = 22.64 kN/m
Total dead load / m on girder = 22.64 + 16.8 = 39.44 kN/m
RA= 2W1[1+ 3
If w = axle load + 700kN
3I×2.5×1.1
2I× ]
Total downward load = (42×3) + (39.44×20) = 914.8 kN
Ra=Rb= 914.8/2= 457.4 kN
Where,w1= 0.5w
p>RA = 1.107 × .5w = 0.5536w [reaction factor =0.5536]
RB= 2×.5W= 0.3333w
3
-
Dead load from slab for girder
Dead load of the deck slab Parapet railing = 1kN/m
Wearing coat = (22×1.197×0.08) = 2.1KN/m Deck slab = (24×1.197×0.3) = 8.61KN/m
Total load = 11.71 KN/m
Total dead load of deck = (2×11.71) + (8.96×5.3)
= 70.91 kN/m Considering the girder to be rigid Dead load = 70.91 = 23.64 KN/m
girder 3
-
Live load bending moment in girder
Span of the girder = 20m
M max at center = (457.4 ×10) – (39.44×10×(10/2)) –
(42×5) = 2392 kN-m
Dead load shear at the support = (39.44×20) + 42 + (42/2)
2
=457.4 KN
-
Design moments and shear force
Table 1: Design Moments and Shear Force
B.M
DL B.M
LL B.M
TOTAL B.M
Outer Girder Inner Girder
2392 kNm
2392 kNm
2110.6KNm
1270.7 kNm
4502.6 kNm
3662.7 kNm
S.F
DL S.F
LL S.F
TOTAL S.F
Outer Girder Inner Girder
457.4 kN
457.4 kN
313.27 kN
449.87 kN
770.67 kN
907.27 kN
Max B.M = 4502.6 kN-m Max S.F = 907.27 kN
Effective depth = 1450mm
Approximate Lever arm = 1400-100 = 1300mm
Ast = (4502.6 × 10^6)/(200 × 0.9 × 1300)
= 19241.88mm2
Provide 32mm bars
Live load shear including impact =
2×271.25 × 1.25
No of bars = 19241.88/((3.14×322)/4) = 24
-
Design of section for maximum B.M and S.F
3
(reactio
n on each longitudinal girder) = 226.04KN
Nominal shear stress, =
Dead load shear = 51.33 kN Total shear = 226.04+51.33
= (907.27× 103)/ (500×1400)
= 1.3 N/mm
= 100As/bd = (100×19241.88)/ (500×1400) = 2.75
= 0.6 N/mm2
>
Hence safe provide shear reinforcement
= 277.37 kN
-
Design moments and shear force Maximum bending moment = 375.05 kN-m Maximum shear force = 277.37 kN
Effective depth = 1400 mm Approximate lever arm = 1300mm
Assume 2 bars of 32mm Ø is bent up
= (sin )
Ast = 375.05×10
6
6
200×0.9 ×1300
= 1602.782
= 45°
2 1
Provide 32 mm Ø bars
No of bars = 1602.78= 2
4
4
= 200×2× × 32
× = 227.36KN
2
×32 4
Balance shear = 907.27 – 227.36 = 679.91 KN
Using 10mm Ø, 4 legged stirrups
-
Design of shear
-
-
-
3
3
Nominal shear stress,
=
=
= 277.37×10
(277.37×10^3)/ (500×1400) =0.4N/mm2
= (200×4×(3.14/4)× (102)×1400)/679.91= 130mm
Provide 10mm Ø 4 legged stirrups at 120 mm c/c
500×1400
100 = 100×1602.78) = 0.23
500×1400
= 0.224 N/2
>
Hence safe provide shear reinforcement Assume 2 bars of 32mm Ø as bent up Us= (in )
= 45
Us = 200×2× × 322 × 1 = 227.36 KN
4 2
Fig. 10: Detailing of longitudinal girder
Balance shear = 277.37 – 227.36 = 50.01 KN Using 10mm Ø, 4 legged stirrups
× ×
=
-
-
-
Design of Cross Girder
200×4××102×1450 200×4×(3.14 )×(102)×1400)
)
)
= 4 2 = 317mm
-
Dead load calculation
256.92
277.37×103
Self-weight of the cross girder (same as longitudinal girder size) = 16.8 KN/m Dead load from slab
= 2×(1/2)×2.5×1.25×8.96 = 28 KN
Uniformly distributed load = 28/2.5= 14 KN/m Total load on cross girder = 16.8+14 = 30.8 KN/m Assuming the cross girder to be rigid
Reaction on each cross girder = (30.8×5)/3 = 51.33 kN Dead load shear = 51.33 kN
-
Live load calculation
Load coming on the cross girder =271.25KN
Assuming the cross girder as rigid, reaction on each longitudinal girder is = 2 ×271.25
Provide 10mm Ø 4 legged stirrups at 300mm c/c
Fig.11: Detailing of cross girder
3
Live load bending moment in
= 1.25×180.53×1.475
cluding impact
-
-
Pier cap
-
Design Procedure
Design of hammer head portion over circular pier for the
{for 5m span for c/s is 25%} =332.85KNm
Dead load bending moment at 1.475m from support
= 51.33×1.475-(30.8×1.475) × (1.475/2)
= 42.2 KNm
Total bending moment
= 332.85+42.2 = 375.05
kNm
following details
Live load: IRC Class AA Tracked vehicle Materials: M35 grade concrete and Fe 415 steel
-
Data
Clear projection of cantilever slab = 3200mm Thickness of wearing coat =80 mm
Materials: M35grade concrete and Fe 415 steel.
Live load is IRC class AA tracked vehicle.
-
Permissible stresses (IRC: 21): For M35 grade concrete and Fe415 steel.
= 11.67 N/mm, m =10, = 200N/mm, j = 0.9, Q = 1.93
-
Calculations of moments
Total dead load moment,
Mg = 70.56+105.84+4.2+15.52+30.24+508.032+432.36
=1166.752 kNm
-
-
Live load moment
The live load is IRC class AA tracked vehicle. This is placed with its edge 1200 mm from the kerb.
Effective width of dispersion perpendicular to span is given by
= 1.2x + x = 0.1m
=[0.85+2×0.075] =1m.
Therefore be= (1.2×0.1) +1=1.12m.
Live load per meter width including impact =2110.6 KNm
-
Design moment Design moment, M=1166.752+2110.6 Factored moment = 4916.028 KNm
-
Reinforcements
Effective depth required
2 = maximum bending moment d = [(4916.028×106) ] = 1595.98mm
(1.93×1000))0.5
Effective depth required =2200 – 50
= 2150 mm > 1595.98 mm
6
6
Hence adopted depth is adequate
Ast =[ (4916.028×10 ) ] = 127022
(200×0.9×2150)
-
-
-
Pier
Live load: IRC Class AA tracked vehicle Materials: M35 grade concrete and Fe 415 steel
-
Calculation of loads Data
Effective span of girder bridge = 20 m Clear width of roadway = 7.5 m
Live load on bridge class AA Height of pier = 6.250 m Height of flood level = 2 m
Dead load of super structure per span equal to dead load coming outer girders and inner girders.
Assume weight of bearing, plate etc. as 10 KN Dead load of pier cap:
The pier cap is divided into two cantilevers and one rectangular section Weight (moment)of two trapezoidal sections = area × unit weight of concrete =322.56 KNm Dead load moment of circular pier
3.14 × 2
3.14 × 2
2
= [ ] ×6.250×24=471.24 KNm
4
-
Stresses Due to Live Load
Reaction due to live load class AA loading including impact = 1.197×70 = 83.79 kN
Maximum bending moment = 83.79× 0.5 = 41.895 KNm Maximum and minimum stresses at the base due to this load will be
= 5.74 kN/2 and -0.916 kN/2
-
Stresses Due to Longitudinal Force
Maximum longitudinal force will occur due to class AA loading = 14 kN
Moment at base of pier due to this force = 100 × 14 = 140 kNm
Use 32 mm Ø bars
Stress at base =140 ×14 = 12.106 kN/2, Assume
Ast = [( 3.14×32 )
Ast = [( 3.14×32 )
2
] = 804.242
4
No of bars = 12702 = 16
coefficient of friction as 0.25 at one bearing and 0.22 at
other bearing Total resistance at one set of bearing with DL
804.2
However, provided
required.
more for effective reinforcement than
and LL
= 0.25 (166.85 + 1.197×700) = 234.212 kN
Total resistance at other set of bearings due to DL only
-
Top reinforcement:
Provide 30 numbers of 32mm bars n 2 layers
-
Side reinforcement:
Provide 10 numbers of 16mm bars on each face equally spaced
-
Inclined reinforcement:
Provide 10 numbers of 16mm bars on each face equally spaced.
-
Shear reinforcement:
Provide reinforcement 12mm 4-legged stirrups
@ 150 mm/cc.
= 0.22 × 166.85=36.707 KN
Unbalanced force at top of the pier = 234.212 36.707 =
197.505 kN
Moment at base = 197.505 ×1.4 = 13.932 kN/2
19.847
-
Stresses Due to Wind Loads Exposed height of the structure
= depth of girder + thickness of slab + height of railing
= 1.4 + 0.23 + 1.45 = 3.05 m
Exposed area contributing wind pressure per pier
= span × height
= 20 × 3.141 = 62.831 m
Assume average height of about 5 m
The wind pressure from table is 76.96kg/2
-
Wind force on exposed surface = 62.831 ×76.96
1000
= 4.83 kN
-
The design wind load should not be less than 450 kg/m of the loaded chord.
Hence minimum design wind force = 20 ×450 =9
1000
KN
Fig. 12: Detailing of Pier cap
-
The wind force for design purposes should be less than 240 kg/m2
For the unloaded structure = 62.831 ×240 =15.079KN
d is the clear cover = 60 mm
By referring chart number 55 of SP 16
Where P is the percentage of steel reinforcement
Condition (iii) gives maximu
1000
d force. Hence this is
P = 0.01 × 20 = 0.2
considered in design.
m win
Area of steel = 0.2 × 2000² = 6283.18 mm²
4
Assume this to act at mid height,
3.141 = 1.57m from the top of pier
2
Moment at base about Y axis Mw = 15.079 × (10 + 1.57)
= 174.964 kNm
The bending takes place about Y axis.
Maximum stresses at the base at end of straight portion.
Use 25 mm Ø bar
2
2
Ast =3.14×25 = 490.87 mm²
4
Number of bars = 6283.18 = 14
490.87
However, provide 32 numbers of 25 mm bars around the
circular pier.
= × 3.6 = 174.464
× 3.6 = 3.345 /2
Using 10 mm Ø lateral ties
1
184.711
Spacing is the least of the following
Maximum stress at the edge of the pier = × 5 = 174.464
-
Least lateral dimension = 2000 mm
× 5 = 4.722 /2
-
Total Stresses
Under dry conditions Total stress = DL + LL + WL At end of straight portion,
184.711
2. 16×25 = 400 mm
3. 300 mm
Hence provide 10 mm bars of lateral ties @ 300 mm c/c
Maximum = 9.409 + 5.741 + 12.106 + 142.144 – 3.345 +
4.722 = 177.467 kg/m2
Minimum = 9.409 – 5.741 – 12.106 – 142.144 – 3.345 –
4.722 = -158.649 kg/m2
At end of pier,
Maximum = 9.409 + 4.722 = 14.131 kg/m2
Minimum = 9.409 – 4.722 = 4.687 kg/m2
Under wet conditions, Total stress = DL + LL + WL At end of straight portion,
Maximum = 9.409 – 6.609 + 5.741 + 12.106 + 142.144 +
3.345 +1.373 = 1464.673 kg/m2
Minimum = 9.409 – 6.699 – 0.916 – 12.106 – 142.144 –
3.345 – 1.373 = -157.174 kg/m2
At end of pier,
Maximum = 9.409 – 6.699 + 4.722 – 1.907 = 9.339 kg/m2
Minimum = 9.409 – 6.699 – 4.722 – 1.907 = -3.919 kg/m2
Allowable compressive stress in 1:3:6 concrete is 2000 kg/m2& 250 kg/m2 intension. The stresses in pier are within these permissible limits.
Fig.13: Detailing of pier
-
-
-
-
Design of Pile Cap
-
Data
Total Load on the column pu =10517.556 KN Diameter of column = 2m
Pile diameter = 300mm
Allowable load on each pile = 1350KN Grade of concrete for pile cap = M50
-
Size of pile cap
Number of piles required, N=10517.5 = 8
Weight of IRC Class AA tracked vehicle is 700 KN
Let us provide 8 nos of pile
1350
Total load = dead load + live load = 1929.389+700
= 20629.389 KN
Total load with impact = 20629.389 ×2= 5258.778kN Factor of safety = 2
Factored load = 5258.778×2 = 10517.556 kN Factored load =10517.556 kN.
e is the eccentricity of the wheel load from center.
e = 1.1m
Live load = 700×2 = 1400 KN
Maximum moment = 1400×1.197 = 1675.8 KN Moment with impact = 700×1.197= 837.9 KN Factored moment = 1675.8 ×2.2 = 3686.76KN-m Therefore, factored moment = Mu = 3686.76 KN-m
1) Non dimensional parameters
Spacing of piles: (IS 2911:1/2, 2010) S= 4×300=1200mm
-
Overhang portion of the pile cap
overhang = 2×300=0.6m
Thus, the total width and breadth of the pile cap is
Bcap = (2×1.2) +(2×0.6) =3.6 m
Wcap= Bcap
Hence let as assume pile cap size 3.6 m x 3.6 m
-
Thickness of pile cap based on shear
Pile reaction; R= 10517.556 = 1314.69 kN
8
One way shear,
The critical section is at a distance d from the face of the column
6
6
PU = 10517.553 × 103
= 0.1
Clear distance c = 2.4-2-0.3=0.1m
Fck d2
35 × 20002
Considering tolerance of 50mm
MU
Fck 3
=3686.76 × 10
35 × 20003
= 0.02
Clear spacing = 100+50=150mm
150+300
Ratio () = 60 = 0.03 r =
2000
300
Where D is the diameter of the circular pier = 2000 mm
=3×R×r = 3× (150+300) × 1.3 × 106
300
=5916105-13146.9d
Assuming percentage of steel 0.25& for M50 grade
Aassumed = 0.0025×b×D = 6156 mm2 Assuming 16 mm bars
concrete =0.38 N/mm2
No of bars required = 6156
= 31
a) One way shear resistance
162
= 0.38×3600×d = 1368d
×( 4 )
Spacing =3600(31×16)2×75 = 98.466 mm
>
D >407.588mm
S = 90 mm c/c
311
therefore d = 408mm Since, computed value of d
e) Development length.
Tbd = 1.9 N/ mm2
c=150 mm c+d=450 mm
=
(0.87×)×16 = 0.475 m
4× 1.6×
d > 487 mm
Hence assumption is correct
-
Two-way shear
The critical face is at a distance from the face of the
2
column.
Let us assume that
=c
2
Factored shear force.
2 =8×1314.69 = 10517.52kN
Two-way shear resistance
= 1
Length available; L =0.8 m Ld < L
f) Transfer of force at column base
Column to pile cap intraction
-
For column face.
1 2
1 2
= = ×20002 4
Fckcolumn= 50 N/mm2
(1) = 1
2
Fbr max column = 0.45×50×1 = 22.5 N/2
-
For pile cap face.
1 =3600×3600
= 0.25× Fck=1.77 N/2
2
2
= ×20002 4
2 = Ks×Tc×(4×(2000+d) d) = 14160d+7.08d
2 >2
FckPILECAP= 50 N/2
1 () = 4.125 (limited to 2)
d=577mm
> c
2
Fbr max pilecap
= 0.45×
50×
2 = 45 N/2
2
assumption that full pile reaction is not valid
2 = R-(R×(1-1)×(1-2))
Evidently the column face governs Limiting bearing resistance
Fbr = 9232.5 kN
=
= (150+300)
P= 10517.556 KN
1 2 300
2
2
=8×1.3×106×(1-(1- 1)2)
2 >2
d = 651 mm
-
-
Around the pile punching shear
Factored shear force, = 1000kN
Two-way shear resistance, = 1×1.77×(pi×(300+d)×d)
>
Here, Fbr< pu
Excess force; P = 1285 kN
If column bars are extended into the footing, then, force per bar
3
3
Fbar = 1285/32= 40.15 kN
2
2
corresponding stress in bar = 40.15 × 10 = 81.79 N/2
× 25
4
development length required to take the stress
d = 376 mm
ld = 81.79 ×25
4 ×1.6 ×1.25 ×1.9
= 134.5 mm
-
Shear around the pile along ABCD Vcp = 1×1.77× (+300+)+2×600)
4
d = 488 mm
hence the effective depth is considering critical case of two-way shear around the column d = 651 mm
Available vertical embedment in the footing d=654 mm more than Minimum
ld= 135 mm
Astinterface_min=0.005× × 20002= 15.7 ×103 mm2
4
Ast interface provided = 32× × 242 =31.41×103 mm2
D= 651+16+150 =817 mm
Let us assume D = 850 mm
hence area provided is reinforcement required.
4
well
over minimum interface
d = 850-16-150=684 mm
-
Design of flexural reinforcement
Mu=3×R(c+)= 1183.221 kNm
2
B= 3600 mm
D = 684 mm
Ast required=f
(12 14.598× mu
-
Transfer of force at pile-to-pile cap
Factored reaction from pile; Pupile =1000kn Column to pile cap interaction:
For pile face
A1= A2 = × 3002
4
Fckpile = 50 N/mm2
A1
ck×b×d×
2×fy
fck×b×d2
root(
F
)= 1
A2
= 0.45 50
1 = 22.5 N/ 2
= 4871.48 mm2
Amin = 0.0012×b×D = 2954.88 mm2
br max pile
× × mm
-
Pile cap face
-
-
1
1
A =
4
× 12002
2
2
A = × 3002
-
Earth pressure
4 Lateral earth pressure k = 0.408
FckPILECAP= 50 N/mm2
root(A1) = 4 (limited to 2)
A2
Fbr max pilecap = 0.45×50×2 = 45 N/mm2
a
Horizontal component of earth pressure = total earth pressure × cos ( + )
Total Earth pressure = 1 × × p × cos × k
Evidently the column face governs 2 a
Limiting bearing resistance Fbr = 1590.43 kN
P= 10517.556 KN
Here, Fbr>pu Hence Safe
Fig.14: Detailing Pile and pile cap
E. Design of Abutment Density of soil = 16.42 kN/m3 Coefficient of friction = 0.6
Angle of repose = 30°
Live load on bridge = IRC Class AA load
Angle of friction between soil and concrete = 18° Longitudinal girder = 3 number of 1.4 m × 0.5 m Deck slab = 0.3 m depth
=0.5×16.42×4.42 ×cos15.25×0.408 = 62.56 KN
Horizontal component = 62.56 cos (16.42 + 15.255)
= 53.24 kN
Vertical component = 62.56 sin (16.42 + 15.255)
=32.85KN
R = V2 + H2 = ((32.852)+(53. 852)) × 0.5
=63.07KN
-
Overturning
Earth pressure is acting at 0.42 of height from base
= 0.42 × 4.4 = 1.848 m
Moments due to overturning = 1.848×53.24= 98.39 kNm Restoring moments= (0.5×1.2×4.4×24×3.0)
+(0.6×4.4×24×2.3) + (0.8×3.7×24×1.6)
+(0.5×1.2×3.7×24×0.8) +(858.68×1.6) =1865.984 kNm
Factor of safety against overturning =1865.984/98.93
= 18.86
-
Sliding
Factor of safety = (0.6×858.68)/53.24 = 9.6
-
Base pressure
-
Distance of the resultant from the toe.
x = (restoring moment moment due to overturning)
resultant
= 1865.98698.39 = 2.058m
858.68
Eccentricity of the resultant from the centre of the base. e= b x = 0.022
2
Maximum pressure, P =858.68 × (1 + 6×.022 ) =233.82k
Span of the bridge =20 m
= 233.82km/m2
max
3.8
3.8
Self- weight,
W1 = ((0.5×1.24×.4) +(0.5×1.2×3.7) +(0.6×4.4)
+(0.8×3.7)) ×24= 251.04 kN
-
Dead load W2 = L1 + L2
L1 = Load from longitudinal girder
= 3 × 1.4 × 0.5 × 20 × 24 = 1008 kN
L2 = Load from slab and wearing course
= (0.3 × 8.4× 20 × 24) + (0.8 × 7.5 × 20 × 22) = 3849.6KN
W2 = 4857.6 kN
Considering dead load (super structure) shared by an abutment and a pillar
= 4857 = 2428.8 kN
Pmin= (858.68/3.8) (1-((6×0.022)/3.8) = 218.12 km/m2
VI CONCLUSION
-
The proposed project could help rectify the traffic conjunction problems and improve safe driving.
-
Project is designed manually and using STAAD Pro V8i.
-
Amount of steel provided for the structure is economic.
-
Structure is designed on the basis of IRC class AA loading.
REFERENCE
-
S. Chandra; P.K. Sikdar; Factors Affecting Pcu In Mixed Traffic
2
Dead load per meter span of abutment W2=
2428 =
84
Situations on Urban Roads P. 40-50: ILL.; Includes Bibliographical References (P. 49). Road & Transport Research.
Live load reaction = W × L
= 289.14 KN
Vol. 9, No. 3 (Sept. 2000)
-
Rasheed Saleem Abed; Experience on Using Total Station
For Class AA tracked vehicle, W = 350 Kn
R 20Wheel load
Surveying for Mapping and Contouring ISSN 0976 6308 (Print) ISSN 0976 6316(Volume 4, Issue 3, May – June (2013), pp. 155-167 IAEME: www.iaeme.com/ijciet.asp Journal Impact
A=350 × (
R
20 )
20 3.6
Factor (2013): 5.3277
-
Narabodee Salatoom; Pichai Taneerananon; A Study of a
A=350 × ( 2 )
20
= 318 kN
Total load carrying on the abutment W = W1 + W2 + RA
= 251.04+ 289.14 + 318.5 = 858.68 kN
Flyover Bridge – Improved Intersection ENGINEERING JOURNAL Volume 19 Issue 1 Received 28 May 2014 Accepted
8 September 2014 Published 30 January 2015
-
A Nithin Chandra; An Overview Towards Flyover Construction for Lessening Congestion of Traffic (IJITR) INTERNATIONAL JOURNAL OF INNOVATIVE TECHNOLOGY AND
RESEARCH Volume No.4, Issue No.3, April May 2016, 2934
2937.
-
IRC 21-2000 Standard specification and code for practise for road bridges section II
-
IRC 5-2000 Standard specification and code for practise for road bridges section I.
-
IRC 6-2000 Standard specification and code for practise for road bridges section II.
-
IS 456- 2000 Plain and reinforcement concrete code of practise