
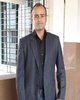
- Open Access
- Total Downloads : 89
- Authors : Shivam Shukla , Subhasini Shukla , Prashant Bajaj
- Paper ID : IJERTV8IS040199
- Volume & Issue : Volume 08, Issue 04 (April – 2019)
- Published (First Online): 17-04-2019
- ISSN (Online) : 2278-0181
- Publisher Name : IJERT
- License:
This work is licensed under a Creative Commons Attribution 4.0 International License
Design and Analysis of Agitator Blade of Pressure Vessel for Variable Loads
Shivam Shukla Subhasini Shukla Prashant Bajaj
SSGB, Bhusawal, India SJCEM, Palghar, India SSGB, Bhusawal, India
Abstract- Agitators are the equipments used for processing products in various pharmaceutical, cosmetic, food & chemical industries with an objective of mixing liquids together, enhancing the reactions of chemical substance, so that uniform liquid can be kept in bulk during storage or it can increase the heat transfer. The alarming drawback of the agitator vessel under consideration is its unwanted deflection of the blades. It is required to check the integrity of the vessel for various operating conditions and also to check the level of deflection of blades so as to impart modifications if necessary to keep the deflection of the agitator blade within the limits from the point of view of proper functioning of the vessel. The calculations are performed for all the vessel parameters as well as Agitator. The new value of thickness for the Blades is 32mm. The load cases for this new Designed blades are considered and Modeling being done. After modeling the analysis on ANSYS is performed. This report consists of structural analysis of blade using ANSYS software to check the integrity of the vessel and to check the deflection level of agitator blade.
Keywords- Agitator Vessel, Integrity, Structural Analysis.
-
INTRODUCTION
A pressure vessel is defined as container with pressure differential between inside and outside [1]. Pressure reactor vessel is one kind of Pressure vessel [2]. It is a part of our everyday life from consumer products to advanced aeronautic systems [3]. Agitator is used for variety of purposes such as to suspend solid particles, to blend miscible liquids, to disperse a gas through a liquid in the form of bubbles & promotion of heat transfer between the liquid and coil. There are some factor affecting the efficiency of agitating, some are related to the liquid characteristics such as viscosity and densities as well as some are related to geometry such as the container diameter (D), impeller length (Y), rotating speed (N), an height of impeller from bottom of the container (H), other Characteristics of mixing include the liquid the necessity of performing the process to make the liquid experience all kind of movement inside container. None of the universal system is valid for all liquids and tanks. Mixing is a very important unit operation in many industries like cosmetic, chemical, biochemical and pharmaceutical applications dairy and food process industry. At the instance, various operations involving consistent mixing, preparation of emulsion, process of extracting, dissolutions, process of crystallizing, phase reactions of various liquids need blending in one form or the other. The process of agitation in mechanical agitator pressure vessels is achieved by the rotation of an impeller which can help in mixing, increment of heat transfer or increment of mass transfer of fluids. The stirred tank reactor with rotary mixers remains the significant part of the chemical process industries (CPI). It is important for the process developers and plant design engineers to
understand the mechanical design aspects of agitator reactors. To get an optimized agitator blade design, there is necessity to identify the optimum balance amongst the process requirements and an economical, mechanical solution of the vessel-agitator system. Mechanical agitators can be divided into seven basic groups, namely Paddles Turbines, Propellers, Helical screws, Cones, Radial flow propellers and High speed disc. Mixing by agitator take place due to momentum transfer. High velocity streams, produced by the impeller, entrain the slower mixing or stagnant liquid areas from all parts of the vessel and a uniform mixing occurs. As viscosity increase, frictional drag forces retard the high velocity stream and confine them to immediate vicinity of the impeller. There is non uniform mixing due to development of stagnant areas. Agitators having a small blade area which rotate at high speed, for instance, propellers, flat or curved blade turbine are used to mix liquids having low viscosities .Various kinds of large impellers, such as FULLZONE (Kobelco Eco-Solutions Co., Ltd.), Super-MixMR205 (Satake Chemical Equipment Mfg. Co., Ltd.), Hi-Fi mixer (Soken Technic Co., Ltd.) and MAXBLEND (Sumitomo Heavy Industries Co., Ltd.), have been developed in Japan. Since these Impellers have a high mixing performance over a wide range of viscosities, they are used in mixing, dispersion, reaction and polymerization processes. Recently, their use in the food and pharmaceutical industries is being considered. For agitation in the turbulent region, these large impellers are usually used with baffles to promote mixing. However, baffles often cause problems for washing and sterilization. Furthermore, in the laminar region, baffles are not effective for mixing, and in fact, they often obstruct mixing. Eccentric mixing is one of the traditional methods of promoting mixing in a vessel without baffles. An eccentrically located impeller generates a vertical flow, which contributes to mixing, without baffles. If a large impeller is used at an eccentric position, it is expected that the high performance of the large impeller can be combined with the advantages of eccentric mixer Separation damage and fracture rock movement reflect.
-
PROBLEM STATEMENT
Reactor pressure vessel (Vertical) is used to have better mixing, cyclic operation & even distribution of the Agitator Blades. To overcome the Inertia forces as a result of stagnant fluids & also the stage wise addition of various fluids in the reactor, agitation which starts from zero RPM requires high initial torque. Over a period of time, fluids which are having various viscosities may cause damage to the blades of agitator, such as bending or fatigue. This problem is observed in one case of the reactor vessels where mixing is done at various speeds handling Emulsion polymer. The viscosity of
the fluid does not remains the same during mixing period and keeps changing. The dimensions which are calculated by using the theoretical formulas may result in bigger dimensions along with increase in thickness of the blades being sized. The case of change in volume or change in capacity of the reactor pressure vessel is being handled in this report. It is certainly that the as per increase in volume the size and type of Agitator may also change. The nature of fluid was same which was handled by former type of agitator but with only 5 KL of capacity. With an increment in capacity from 5 KL to 15 KL, there is a need to work out again on the design of reactor and agitator. The analysis will also be done on the ANSYS software to determine the various failure modes and to make a robust design.
-
BACKGROUND
Industrial agitators are machines used in industries that process products in the chemical, food, pharmaceutical and cosmetic industries, in a view of:
-
mixing liquids together
-
promote the reactions of chemical substances
-
keeping homogeneous liquid bulk during storage
-
increase heat transfer (heating or cooling) Several different kind of industrial agitators exist:
-
Mechanical agitators (rotating)
-
Static agitators ( pipe fitted with baffles)
-
Rotating tank agitators (like concrete mixer)
-
Agitator Mixer Padole Type
-
Agitators working with a pump blasting liquid
The selection of agitator is dependent on the phase that needs to be mixed, viz. Liquids only, liquid and solid, liquid and gas or liquids with solid and gas. Depending on the type of phase and of the bulk, the agitator can be named mixer, kneader, and dough mixer, amongst others. The placement of the agitators can be done on the top of the tank on vertical position, or it can be horizontal or to be very less common, it can be located on the bottom side of the tank.
-
Principle of agitation
The motion of heterogeneous mass (liquid-solid phase), to the impeller causes the process of agitation and it occurs because of mechanical agitators causing the rotation of impeller. Different substances can be composed to form a bulk and the objective of the operation is to improvise the efficiency of a reaction by having a better contact between reactive products or to blend it properly. Or the bulk is already blended and the aim of agitation is to increase a heat transfer or to maintain particles in suspension to avoid any deposit Data of the impeller blade.
The process of agitating of liquids is done by one or more agitation.
Depending on its shape, the impeller can generate:
-
-
The movement of the liquid which is characterized by its velocity and direction.
-
Turbulence which is an erratic variation in space and time of local fluid velocity.
-
Shearing given by a velocity gradient between two filets of fluids.
These two phenomena provide energy consumption.
-
Impellers
Propellers (marine) gives an inlet and outlet which are on axial direction, preferably downward, they are characterized by a nice pumping flow, low energy consumption and low shear value and low turbulence turbines in which the inward flow is axial and the outward flow is radial will definitely provide turbulence, shearing and require near around 20 times more energy than propellers, for the same diameter and same rotation speed.
-
Mechanical features
An agitator is composed of a drive device (motor, gear reducer, belt), a guiding system of the shaft (lantern fitted with bearings), a shaft and impellers. The agitator must be equipped with such a tough sealing system, when the operating conditions are under high pressure or high temperature, to keep the inside of the tank tightened when the shaft is crossing it. If the shaft is long (> 10m), it can be guided by a bearing located in the bottom of the tank (bottom bearing).
-
-
-
PROPOSED SYSTEM
This problem is observed in Agitators of mentioned reactor vessels where Emulsion polymer is to be produced. The viscosity of the mixing fluid varies during mixing period. Due to which the calculated values using the theoretical formulas lead to a bulky design & failure because of bending as well as high stress concentration, also more load applied on the Motor. In order to avoid these troubles the approach of Design by analysis or FEA must be adopted, where stimulation of the existing Agitator model being developed & being analyze using the various loads and pressure being applied. The result of the analysis will help to figure out; optimum size of the failure loads acting on Blades, avoiding bending of the blades with new design Agitator with optimum dimensions.
-
SOLID MODELLING
Solid modeling is a consistent set of principles for mathematical and computer modeling of three-dimensional solids. Solid modeling is distinguished from related areas of geometric modeling and computer graphics by its emphasis on physical fidelity. Together, the principles of geometric and solid modeling form the foundation of 3D- computer-aided design and in general support the creation, exchange, visualization, animation, interrogation, and annotation of digital models of physical objects. Solid Works is a solid modeling computer-aided design (CAD),computer-aided Engineering (CAE) computer program that runs on Microsoft Windows Solid Works is published by Dassault Systems.
Applied Material Modeling is non linear since the behavior such as large deflection, strains, stresses and reactive forces are to be simulated.
Fig.1. Dimensions of Agitator Blade of Pressure Vessel
-
FEA ANALYSIS
The Old techniques of Design by formulae (DBF) methods were used to give design on safer side & thereby lead to more thick materials or rather more strong material selections. Because of which the overall cost of Vessels or Tanks etc., was too high & design used to be very Bulky & heavy. In any Process industry the Cost is more important & safety associated with the same. Here in this design the analysis are performed on ANSYS software & the Table given below shows how agitator is safe as the selected parameters is justifying the overall safety of Vessel. The higher strength material which are having allowable stress equal to that of the material in the vessel wall, even lower strength material can be used if higher strength material is not available, taking into consideration with increment in area of thickness or reinforcement.
The above analysis is performed under static loading condition since we are focusing only on the deformation, strains and stresses induced in the blade. We have not considered dynamic analysis since our scope of the project is restricted to only the above mentioned parameters.
Sr.
No.
Young's Modulus (MPa)
Poisson's Ratio
Bulk Modulus (MPa)
Shear Modulus (MPa)
1
2e+005
0.31
1.693e+005
82000
Sr.
No.
Young's Modulus (MPa)
Poisson's Ratio
Bulk Modulus (MPa)
Shear Modulus (MPa)
1
2e+005
0.31
1.693e+005
82000
TABLE.I MATERIAL PROPERTIES (MATERIAL SS-316)
-
MESHING
ANSYS Meshing is a general-purpose, intelligent, automated high-performance product. It produces the most appropriate mesh for accurate, efficient multiphysics solutions. A mesh well suited for a specific analysis can be generated with a single mouse click for all parts in a model. Full controls over the options used to generate the mesh are available for the expert user who wants to fine-tune it. The power of parallel processing is automatically used to reduce the time you have to wait for mesh generation. Creating the most appropriate mesh is the foundation of engineering simulations. ANSYS Meshing is aware of the type of solutions that will be used in the project and has the appropriate criteria to create the best suited mesh. ANSYS Meshing is automatically integrated with each solver within the ANSYS Workbench environment. For a quick analysis or for the new and infrequent user, a usable mesh can be created with one click of the mouse. ANSYS Meshing chooses the most appropriate options based
on the analysis type and the geometry of the model. Especially convenient is the ability of ANSYS Meshing to automatically take advantage of the available cores in the computer to use parallel processing and thus significantly reduce the time to create a mesh. Parallel meshing is available without any additional cost or license requirements.
Sizing: Fine mesh Relevance: 100
Mesh Type: Uniform Prisms Mesh Method: Tetrahedron Hole-edge sizing: 5mm Number of nodes: 18085
Fig.2. Meshing of 32 mm thick blade
-
BOUNDARY CONDITIONS
To define a problem that results in a unique solution, you must specify information on the dependent (flow) variables at the domain boundaries z Specify fluxes of mass, momentum, energy, etc. into the domain. Defining boundary conditions involves: z Identifying the location of the boundaries (e.g., inlets, walls, symmetry) z Supplying information at the boundaries The data required at a boundary depends upon the boundary condition type and the physical models employed. You must be aware of the information that is required of the boundary condition and locate the boundaries where the information on the flow variables are known or can be reasonably approximated z poorly defined boundary conditions can have a significant impact on your solution
-
Force components of Load of the charge & equivalent resistance offered due to the viscosity of the fluid are converted to the external load factor and applied in Y direction with respect to equivalent Load for exerted conditions.
-
Blade rim & holes are fixed so that the extreme failure conditions can be satisfied with respect to Fixed support
condition. The Fig 3.shows the Boundary conditions applied to 32 mm thick blade.
Fig.3. Boundary conditions applied to 32 mm thick blade
-
Failure Modes Of Agitator: Load Value Is 30.625 KN (28mm, 30mm, 32mm, 34mm, 36mm):
Fig. 4. Blade failure for 30.625 KN (28 MM)
Fig. 5 .Blade failure for 30.625 KN (30 MM)
Fig. 6. Blade failure for 30.625 KN (32 MM)
Fig. 7. Blade failure for 30.625 KN (34 MM)
Fig.8..Blade failure for 30.625 KN (36 MM)
-
Graphical Representation of Analysis outcomes
-
Graph.1. Comparison for Deflection
Graph.2 .Comparisons for Shear Stress
Graph 3. Comparisons for Equivalent of Stress
Graph 4. Comparisons for Factor of Safety
TABLE .II. COMPARATIVE RESULT ANALYSIS FOR A MAXIMUM LOAD OF 38KN (32 MM)
Sr.
No.
Parameter
Analytical Calculation
Experimental Evaluation
FEA
Simulation
1
Deflection (mm)
1.6544
12
0.0212
2
Shear Stress (MPa)
4.166
NA
2.032818
3
Equivalent Stress (MPa)
NA
333.375
20.036
4
FOS
–
1.757
25.703
-
Optimization of Blade Thickness for a load of 38KN: From the analysis, the agitator blade with 32 mm thickness is selected due to the following reasons:
-
For 28 mm thick blade, as the thickness is less, the resistance to deformation will be minimum; hence there will be maximum deformation from TABLE II.
-
For 30 mm thick blade, as the thickness increases the inertia increases, still the resistance to deformation is less, hence again there is some deformation for 32 mm & 34 mm thick blade, as the thickness increases, there is minimum deformation.
-
For 36 mm thick blade, as the thickness increases the inertia increases, there is maximum resistance to the application of load but there is again increase in deformation due to increase in self-weight of the blade.
-
From the above mentioned points, the blades with thicknesses 28 mm & 30 mm are under designed while the blades with thicknesses 34 mm & 36 mm are overdesigned. Hence the optimum thickness of the blade is 32 mm with optimum deformation along with minimum load acting on the motor, which also matches the suggested design of the agitator blade by the customer i.e., 32 mm blade thickness.
-
-
RESULTS & DISCUSSIONS
The Project concept is developed based on the Failure occurred in one of the Agitator handling Emulsion polymer in reactor vessel with 10KL volume. The blades of agitator were not designed considering the viscosity of the mixture taking place during the cycle time of mixing process. Also there were no Analytical studies being done, before actual fabrication is performed. The relationship between the highly viscous fluid and Blades are studied, considering the Load (N) being acted on the Blades. There were various
loading conditions being studied for the failure of Blades of Reactor vessel with 10KL volume. The result obtained from the analysis performed using ANSYS and the deflection occurred in the Blades observed to me equivalent. The conclusion can be made out of the analysis is, using the analysis on ANSYS gives the failure report for the Blades as the value of Loads or Load cases gradually increased. The Viscosity is defined as ratio of Shearing stress to Velocity gradient. In simple words it is resistance offered to the motion.
The calculations are performed for all the vessel parameters as well as Agitator. The new value of thickness for the Blades is 32mm. The load cases for this new Designed blades are considered and Modeling being done. After modeling the analysis on ANSYS is performed. The result is to be plotted on the basis of the Total deformation (in mm), The Equivalent stress (MPa) and The Max. Principal Stress (MPa) etc.
-
The Design calculations for the Reactor pressure vessel (R-110 & R-120) capacity 15KL are done.
-
The Design calculations for the Agitators for reactor pressure vessel are done.
-
The results of analysis have been checked by Design consultant (i.e. MDP solutions Pvt. Ltd. Mumbai).
-
The results of analysis have been approved by the Client (I.e. Voice engineering, Mumbai).
-
PV-lite calculations are performed, and design is safe.
-
The range load cases for analysis are confirmed.
-
-
CONCLUSION
Boundary Conditions were identified successfully after a thorough study of clients requirement & Case study 1. The same conditions were used for Theoretical Calculations, FEA Analysis & the optimization.
Solid Works 2012 was used for the Modeling of agitator blade of the Case Study concern. The IGES, Parasolid, STEP, etc formats were created & used for FEA Analysis in the software Ansys-Workbench.
Preprocessing was performed using studied Boundary Conditions & the model using Ansys. Discretization settings were applied (as mentioned earlier) for more accurate results. During Post Processing, using Parametric Optimization method (Ansys), optimum blade thickness was determined for the proposed product which is in line with the suggested dimensions of the blade (by Client). This will minimize loads on shaft & motor (Maximum Torque & Self weight are considered during analysis to take care of this).
To support the robust design as decided in methodology, appropriate material properties were studied, verified through experimental tests, applied during theoretical calculations & FEA Simulation. This 3 level filtration & application has made sure the correct way of solution finding (Comparative analysis mentioned earlier).
The optimum design is submitted successfully to the Design Consultant of the product manufacturer (Certificate from the consultant is attached). This has served the most important objective to reduce material & Labor cost & time of
fabrication by avoiding unnecessary material & time wastage in trial & error methods of manufacturing.
It is found that there are various types of agitators available. In various process industries, the agitating process of pulp is not uniform and proper. Different stresses are produced in the agitator like bending stress, deformation stress. The parametric study can give the new design which can increase the mixing percentage. Due to various joining methods present to join the arms & hub together the weight of the agitator is very high. The power consumption can be reduced and efficiency and mixing percentage can be improvised by reducing the weight of the impeller.
The Stress induced in various components of the agitator vessel are computed using ANSYS and are found to be below the maximum allowable stress values as per ASME. The changes in the dimensions of the blade confirm to the shape of the blade. Sinc the blade do not fail for the operating conditions, the integrity of the blade is intact and is safe to operate.
-
ACKNOWLEDGMENT
This research was supported carried out by MDP Solutions Pvt. Ltd and Industrial Metal Test Lab , Andheri ,Mumbai. We thank the reviewers for their helpful, constructive comments
IJSART – Volume 3 Issue 3 MARCH 2017 ISSN [ONLINE]: 2395-
1052.
-
Mr. X. Charles, Stress Analysis of Pressure Vessel Due to Load and Temperature, Middle-East Journal of Scientific Research 20 (11): 1390- 1395, 2014ISSN 1990-9233
-
Mr. Pravinkumar Nase, Mr. P. Srinivasa Kumar , P. H. V. Sesha TalapaSai ,Analysis Of Pressure Vessel, Vol-1 Issue-4 2015 IJARIIE- ISSN(O)-2395-4396 1357
REFERENCES
-
Sumit V. Dubal, Dr.S. Y. Gajjal, Finite Element Analysis of Reactor Pressure Vessel under Different Loading Conditions, 2015 International Conference on Computing Communication Control and Automation, 978-1-4799-6892-3/15 $31.00 © 2015 IEEE
-
Shivam Shukla,Prashant S Bajaj, Detection of Failure mode of Pressure Vessel Agitatordue to variable load , International Journal of Engineering Development and Research(IJEDR1801055),Volume 6,Issue 1,Januray 2018 ISSN: 2321-9939
-
Christopher J. Evans, Timothy F. Miller, Failure Prediction of Pressure Vessels Using Finite Element Analysis, Journal Of Pressure Vessel Technology, Copyright VC 2015 by ASME OCTOBER 2015, Vol. 137 / 051206-1.
-
Saeed Asiri, Design and Implementation of Differential Agitators to Maximize Agitating Performance, International Journal of Mechanics and Applications 2012, 2(6): 98-112 DOI: 10.5923/j.mechanics.20120206.01
-
Sumit R.Desai ,S.Y.Gajjal and Kulloli, Redesign and Structural analysis of agitator shaft for reactor pressure vessel , MIT College of Engineering, Pune, India, AMET 2016, INPRESSCO IJCET Special Issue-4 (March 2016).
-
B.S.Thakkar, S.A.Thakkar, Design Of Pressure Vessel Using Asme Code, Section Viii, Division 1, International Journal of Advanced Engineering Research and Studies E-ISSN22498974, IJAERS/Vol. I/ Issue II/January-March, 2012/228-234
-
V. V. Wadkar, S.S. Malgave, D.D. Patil , H.S. Bhore , P. P. Gavade, Design And Analysis Of Pressure Vessel Using Ansys , Journal of Mechanical Engineering and Technology (JMET) Volume 3, Issue 2, July-Dec 2015, pp. 01-13.
-
Arnab Choudhury, Samar Chandra Mondol , Susenjit Sarkar, Finite element Analysis of thermo mechanical stresses of two layered composite cylindrical pressure vessel , International Journal for Research in Applied Science & Engineering Technology (IJRASET), Volume 2 Issue XI, November 2014 ISSN: 2321-9653.
-
Harshad Narvekara, Vijay Bhosale, Integrity check & vibration study for agitator pressure vessel by FEA, International Journal Of Innovative and emerging Research in Engineering(IJIERE), Volume 2, Special Issue 1 MEPCON 2015 e-ISSN: 2394 – 3343 p-ISSN: 2394 – 5494 .
-
Mr. AP Shastri, Prof N P Borkar,A Review on Nomenclature of agitator, International Journal of Research in Advent Technology (IJRAT) Special Issue08 March 2015(E-ISSN: 2321-9637).
-
Mr. Samadhan A Ambhore, Prof. D A Deshmukh, Prof. Ravindra S Surase, Geometry and Architecture of Mixing Agitator AReview,