
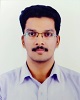
- Open Access
- Authors : Bibin Babu , Alan Varghese , Raveena R Nair , Gokulkrishnan R, Bismi M Buhari
- Paper ID : IJERTV9IS030553
- Volume & Issue : Volume 09, Issue 03 (March 2020)
- Published (First Online): 03-04-2020
- ISSN (Online) : 2278-0181
- Publisher Name : IJERT
- License:
This work is licensed under a Creative Commons Attribution 4.0 International License
Design and Analysis of A Bus Terminal Building
Bismi M Buhari1, Alan Varghese2 , Bibin Babu3, Gokulkrishnan R4, Raveena R Nair5
1Asst. Professor,
2345 Student Civil Department,
Musaliar College of Engineering & Technology, Pathanamthitta, Kerala, India
Abstract- The design and analysis of bus terminal building is carried out. The manual designing of buildings include the design of foundation, design of column, beam, slab, stair etc using a set of procedures and building codes such as IS 456. Here the structural analysis using STAAD Pro V8i SS6 is carried out.
Keywords: Deflection; Bending moment; Shear force; Assembly building.
-
INTRODUCTION
In all spheres of human life buildings are always necessary to satisfy human need. This study mainly focuses on the analysis of an assembly building i.e Municipal bus terminal. Pandalam using STAAD Pro V8i SS6 and manual designing. In this study each structural part is analysed. The bending moment, deflection, shear force etc are analyzed.
-
OBJECTIVES
-
Generate structural frame work
-
Creating model using STAAD PRO V8i.
-
Carry out the structural analysis and manual design, Thus ensure the structural stability.
-
-
BUILDING INFORMATIONS
The proposed bus terminal is a two storey building. It consist of shops, office, staff room, toilet complex etc. there are two openings provided for the entry and exit of buses.
Fig.1 Plan of the analyzing structure
Fig.2 Structural analysis diagram
Fig.3 3D view of structure
-
SPECIFYING LOADS
These are self-weights of the structure to be designed. The dimensions of the cross section are to be assumed initially which enable to estimate the dead load from the known unit weights of the structure. The values of the unit weights of the materials are specified in IS 875:1987(Part-I). Dead load includes self-weight of columns, beams, slabs, brick walls, floor finish etc. The self-weight of the columns and beams were taken automatically by the software. The dead loads on the building are as follows. Here in STAAD the load given to the structure are Dead load ( Self weight and UDL due to brick of 18.6 KN/m), Live load of -3 KN/ m2 and load combinations.
Assume = 0.9
58
Cu = = 29kN/m2 2
Fig.4 Self weight given into the structure
Fig. 5 UDL given into the structure
Therefore, ultimate capacity of a single pile , Qu
= CuNcAp+ CuAs
= 965.726kN
Spacing of pile =2hp =2 × 500 = 1000mm Dimension of column,B × D = 0.45 × 0.45m Factored load =1704.6kN
Factored moment =101.085kN Safe pile load capacity=965.7kN
-
Pile Cap Dimension
Length and breadth of pile cap=1000 + (2 × 250) + (150 × 2)=1.8m
Depth of pile cap=2hp=1000mm=1m
-
Check for pile load capacity
Self weight of pile cap=(1.8 × 1.8 × 1 × 25) × 1.5 = 121.5
Factored load from column, Pu=1704.6kN Total factored load=121.5+1704.6=1826kN No. of pile=4
y-ordinate of pile cap=0.5m Mx=101.08kNm
Pu Compressive load in pile about X axis = +
n
= 953.38kN
Mxy
y2
Design working load = 953.38 = 635.58kN < 965.7,
2
Hence safe.
Fig.6 Live Load given into the structure
-
Bending moment
(1 0.45)
-
-
MANUAL DESIGN AND STAAD ANALYSIS
Mu = 953.38
= 262.18kNm
2
-
Design of pile cap
-
Check for effective depth
Mu = 0.138dfckd2 = 262.2kNm
262.2 × 106
d=410mm
d2 =
0.13 × 25 × 450
drequired < dprovided Hence checked.
-
Check for punching shear
Punching shear at a distance d/2 from face of column=1704.6kN
Perimeter of critical section=2(1800+922)=5444mm
1704.6 × 103
Fig.7 Pile cap arrangement.
Punching shear =
= 0.399N/mm2 5444 × 922
Datas
Number of piles = 4
Pile Diameter = 500 mm Spacing of piles 2 hp = 2 x 400 = 800 m Concrete Mix = M20
Steel Grade = Fe 415
Length of pile = 23m. Soil type is weak clayey soil
Assume unconfined compressive strength as0.058N/mm2
Allowable shear stress for M25=0.25fck = 1.25N/ mm2 > 0.339/mm2
Hence safe.
-
Main reinforcement
Mu=262.2 KNm
Mu
k = = 0.17135
bd2
0.12
i.e UCS =58kN/mm2
Ast min =
100
× 1800 × 922 = 1991.52mm2
No. of bars =
1991.52
= 9.905 10 bars
201.1
Column no.380
Therefore provide 16mm, 10 bars at bottom. Reinforcement at top,
Minimum Ast =1991.52mm2
Therefore provide 16mm, 10 bars at top.
-
Check for one way shear
Maximum shear force at facing of column=958.38kN Shear stress=0.577N/mm2
For Pt=0.2%,
c from IS456 = 0.33N/mm2
Shear to be carried by stirrups,
Vu = (0.577 0.33) × 1800 × 922 × 103 = 409.92kN
Vu
= 4.446kN/m
d
Provide 10mm, 4 legged stirrups at 120mm c/c
spacing.
Grade of Concrete = M30 Grade of Steel = Fe415
Characteristic compressive strength of concrete , fck ( N/mm2 ) = 30
Characteristic yield strength of steel , fy ( N/mm2 ) = 415
Unit weight of concrete , c( kN/m3 ) = 25 Partial safety factor for concrete = 1.5 Exposure condition = Mild
Nominal Cover to exposure condition ( mm ) = 40 Assumed effective cover all around, d' ( mm ) =40
-
Dimensions of the Column Breadth of the column B (mm) = 450 Depth of the Column D (mm) = 450 Least lateral dimension = 450 mm
-
Design Factors
Factored load, Pu =2208kN
Factored moment acting parallel to the larger dimension , Mux = 36kNm
Factored moment acting parallel to the shorter dimension, Muy =48 kNm
Assume percentage of steel =1.5 %
-
Moment in X-X Direction
d 40
=
D 450
= 0.09 0.1
Pu
fckbD
2208 × 1000
=
25 × 450 × 450
= 0.436 0.44
p
=
fck
Mu
1.5
25
= 0.06
fckbD2 = 0.07
Mux = 0.07 × 25 × 450 × 4502
= 159.46 × 106Nmm
-
Moment inY-Y Direction
d 40
Fig. 8 Pile cap detailing
= = 0.09 0.1
D 450
Pu 2208 × 1000
-
-
-
Design of column
= = 0.436 0.44
fckbD 25 × 450 × 450
p
fck
1.5
=
25
= 0.06
Mu
fckbD2 = 0.07
Muy = 0.07 × 25 × 450 × 4502
= 159.46 × 106Nmm
-
Calculation of Puz
p = 1.5%
100Asc
= 1.5
bD
Asc
1.5 × 450 × 450
= = 3037.5mm2
100
Fig. 9 Column no. 380 in the structure
Ac = Ag Asc = 199462.5mm2
Puz = 0.45fckAc + 0.75fyAsc = 3189.37kN
Pu
Puz
2208.36
=
3189.37
= 0.69
Check
From IS 456, value of = 1.82
Mux n
( )
Mux
Muy n
+ ( ) 1
Muy
36.03 × 106
1.82
47.95 × 106
1.82
( )
159.46 × 106
+ ( )
159.46 × 106
< 1
= 0.1789
Fig.12 Shear bending diagram of Member 380 in the structure
Therefore , the column is safe. 1.5% of steel is sufficient.
-
Calculation of reinforcement
p = 1.5%
100Ast
= 1.5
bD
Ast
1.5 × 450 × 450
=
100
= 3037.5mm2
No. of bars = Ast
A
Assume 16 mm bars.
= 15.11 16 bars
Provide 16 bars of 16 mm diameter.
The STAAD digrams are the following,
Fig.10 Dimensional details of Member 380 in the structure
Fig.13 Deflection diagram of Member 380 in the structure
-
-
Design of beam
Beam no.4
Fig. 14 Beam no. 4 in the structure
Clear span=4.2m Live load=12kN/m fck=25N/mm2
fy =415N/mm2
1) ( )
xu 700
Fig.11 Reinforcement details of Member 380 in the structure
=
d 1100 + 0.87fy
= 0.48
Assumptions of cross sectional dimensions
l
= 15
d
d=280mm 300mm
D=d+50=350mm
4200
= d
15
D
= 2
b
b=175mm 200mm
-
Load calculation
Self weight = b × D × con = 1.75N/mm
Dead load =1.75N/mm
Design load =(DL+LL)con=20.63N/mm
-
Design bending moment
Wl2
BM =
8
= 52.22kNm
-
Calculation of limiting value of moment
(M )
xu xu
= 0.36 [1 0.42 ] f
bd2
u lim
BM< (Mu)lim
d
=62.08 kNm
d ck
Fig.16 Reinforcement details of Member 4 in the structure
Therefore under reinforced.
-
Reinforcement calculation
fyAst
f
f
Mu = 0.87fyAstd [1 ]
ckbd
Ast=572.60mm2 Assume 16mm bars.
total area
No. of bars = = 2.84 4 bars area of one bar
-
Design for shear
Fig.17 Shear bending diagram of Member 4 in the structure
Wle
Vu = = 46417.5N/mm2 2
Vu
v = = 0.77N/mm2 bd
-
Design shear strength
100Ast
Percentage of steel =
c = 0.64N/mm2
c max = 3.1N/mm2
= 1.0048
bd
Fig.18 Deflection diagram of Member 4 in the structure
-
-
Design of slab
Fig.15 Dimensional details of Member 4 in the structure
Slab no.707 Size 4.2 × 2.4m
Fig.19 Slab 707 in the structure.
M25 and Fe415 are used.
-
Type of slab
ly 4.2
= = 1.75
lx 2.4
Therefore it is a two way slab.
-
Depth of slab
Ast = 234.422mm2 1000A
l s = A
= 20
d
st
=334.994mm
4200
d =
20 × 1.5
= 136.66 150mm
330mm
Provide 10mm dia bars at 330mm c/c.
Effective span = clear span + d
= 4200 + 150
-
Check for deflection
= 4350mm
Depth ,D = 150 + 20 = 170mm
( l )
d min
= ( l )
d basic
× kt
× kf
× ks
-
Design load Design load= 1.5(DL + LL)
= 1.5(4.25 + 3)
= 10.875 kNm2
l
( )
d max
= 20 × 1.7
=34
4350
=
150
= 29 < 34
-
M along X and Y
-
T he slab is restrained, From IS 456, = 1.75
Therefore the slab is safe.
9) Check for shear
wl
=0.1
Vu =
= 23.65kN
2
=0.056
Vu 23.65 × 103
Mx =x wlx2
= 0.1 × 10.875 × 4.3502
= 20.577kNm
My =y wly2
= 0.056 × 10.875 × 4.352
= 11.523kNm
Shear Force= wl
2
= 10.875×4.35
2
= 23.65kN
-
Check for depth
Mx
d = 0.138fckb
20.577 × 106
u = bd = 1000 × 150
=0.157
Percentage of steel = 100Ast
bd
-
-
-
Design of stairs
= 0.264.
=
0.138 × 25 × 1000
= 77.229mm
Hence , drequired < dprovided.
-
Calculation of Ast (short san)
(Mu)lim
= 0.87fyAst
Astfy
d (1 )
bd×fck
Ast = 397.27mm2
Assume 10mm dia bars.
1000A
Fig.20 Stair case details.
s =
Ast
= 197mm
195mm
Provide 10mm dia bars at 195mm c/c along shorter span.
-
Calculation of Ast (long san)
d = effective depth (0.5 dia of mai bar
+ 0.5 dia of main bar)
Material Constants Concrete, f ck = 25 N/mm2 Steel, f y = 415 N/mm2
1) Dimensioning
4.35
Height of each flight =
2
= 2.175m
=140mm
Astfy
Let the tread of steps be 300 mm.
Rise of stair =0.145 m
bd×f
bd×f
(Mu)lim = 0.87fyAstd (1 )
ck
Width of stair =1.9 m
Effective span, le =8.4 m
Let the thickness of waist slab be 150 mm. Use 12 mm bars.
Assume, clear cover= 25 mm Effective depth =119mm
Hence, Provide 8 mm diameter bars at 350 mm c/c.
6) Check for shear
(As per IS 456:2000, Clause 40) Maximum Shear force, V= 49.626 kN
-
Loads on landing slab
Nominal shear stress, v
Vu
= = 0.417N/mm2
bd
Self weight of Slab = 0.15 × 25 = 3.75 kN/m2 Finishes = 1.25 kN/m2
Live Load on Slab = 4 kN/m2 Total = 9 kN/m2
Factored load = 1.5 × 9 = 13.50 kN/m2
-
Loads on waist slab
Dead load of waist slab = thickness of waist slab×25×R2+T2
T
= 0.15×25×0.1452+0.32
0.3
= 4.165 kN/m2
Self weight of step = 0.5 × R × 25 = 1.8125 kN/m2
Floor finish = 1.25 kN/m2
As per IS: 875(Part 2),1987, Table-1. Live load = 4kN/m2
Total service load =11.228 kN/m2 Consider 1 m width of waist slab.
Total service load / m run = 11.228 × 1
= 11.228kN/m
Factored load, Wu = 1.5 × 11.228 = 16.842kN/m As per the UDL of the landing slab and waist slab, Reaction RA =45.414kN
Reaction RB = 49.626 kN
-
Bending moment
To get maximum Bending Moment, take Shear Force at x distance from support B=0. Thus obtained X is 2.95 m.
Maximum moment at X =2.95m, Mu =73.1187kNm
-
Reinforcement calculations.
Mu
= 5.16 N/mm2
bd2
Percentage of steel, pt =1.19% (From SP16, Table 3)
ptbd
Therefore, Ast = = 1416.1 mm2
100
Minimum steel=0.12% cross sectional area
= 142.8mm2
Use 12mm Ø bars,
1000A
Max. value of shear stress, max=3.1N/mm2 To get design shear strength of concrete, 100As
= 0.09 < 0.15
bd2
From IS 456: 2000, Table 19
c = 0.64 N/mm2, v < c < c max
So, shear reinforcement is not required.
VI . 3D MODEL OF BUS TERMINAL
The 3D model of the bus terminal building is prepared. The model is prepared as per the plan and other details.
Fig.21 Elevation of model.
Fig. 22 Model of bus terminal
Spacing =
Ast
= 79.82mm
Provide 12mm Ø bars at 80 mm c/c.
Maximum Spacing = 3d = 3 × 119
=357mm or 300mm (less)
Hence, provide reinforcement of 12 mm Ø bars at 80 mm c/c
Distribution steel= 0.12% cross sectional area=142.8mm2 Provide 8mm Ø bars.
1000A
Spacing = = 351.82mm Ast
Maximum Spacing = 4d = 476mm
VII . CONCLUSION
-
The structure is completely analysed using STAAD PRO v8i.
-
The structural components of the building are safe in shear and flexure.
-
Amount of steel provided for the structure is economic.
-
Proposed sizes of the elements can be used in the structure.
REFERENCES
[1]. Mahesh Ram Patel; R.C. Singh; Analysis of a tall structure using staad pro providing different wind intensities as per 875 part-iii, IJERST , International Journal of Engineering Sciences & Research Technology, May 2017. [2]. Aman; Manjunath Nalwadgi ; Vishal T; Gajendra Analysis and design of multistorey building by using STAAD Pro IS 456-2000,International Research Journal of Engineering and Technology (IRJET),Volume: 03 Issue: 06 , June-2016. [3]. Anoop A ; Fousiya Hussian; Neeraja R; Rahul Chandran; Shabina S; Varsha S; Anjali A; Planning, analysis and design of multi storied building by staad.pro.v8i, International Journal of Scientific & Engineering Research, Volume 7, Issue 4, April-2016. [4]. IS: 875 (Part 1) 1987( Dead Load ). [5]. IS: 875 (Part 2) 1987( Live Load ). [6]. Design Aids For Reinforced Concrete to IS: 456-1978 []. IS. 456: 2000