
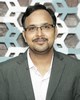
- Open Access
- Authors : Kuldeep Kumar , Devika Nayal
- Paper ID : IJERTV9IS020407
- Volume & Issue : Volume 09, Issue 02 (February 2020)
- Published (First Online): 07-03-2020
- ISSN (Online) : 2278-0181
- Publisher Name : IJERT
- License:
This work is licensed under a Creative Commons Attribution 4.0 International License
Critical Review of use of Glass Fiber Reinforced Gypsum (GFRG) Panels in Housing in India
Kuldeep Kumar
Masters in Building Engineering and Management School of Planning and Architecture,
New Delhi
Devika Nayal
Masters in Building Engineering and Management School of Planning and Architecture,
New Delhi
AbstractThe rural housing shortage in India stands at 44 million dwelling units. Indias urban housing shortage is 18.78 million units, of which 96% pertains to Economically Weaker Section (EWS) and Low-Income Group (LIG) type. Hence, the use of rapid techniques for time and cost-effective delivery of construction projects by adopting alternate building materials and fast construction methodologies is essential in India, given the tremendous housing shortage. Use of Glass Fiber Reinforced Gypsum (GFRG) panels (also known as the rapid wall) construction is considered as one of the innovative solutions to meet this challenge. This product was originally developed and used since 1990 in Australia for mass-scale building construction.
GFRG Panels are developed from gypsum which is abundantly available as an industrial by-product waste. These lightweight panels are fire-resistant, thermally insulated, earthquake tested waterproofed, rot-resistant, termite resistant, and 100% recyclable this conforming to eco-friendly or green building concept with savings in energy.
This paper elaborates the critical reviewing the use of GFRG panels in the Indian construction industry through its comparison with Conventional construction system based on various functional, structural as well as economical parameters
Keywords Rapid wall, Gypsum, Affordable Housing, GFRG, Sustainable
gypsum, reinforced with glass fibers and are prefabricated to a size of 12 m length, 3 m height and 124 mm overall thickness (with cavities), and are relatively light-weight (44 kg/m2). These panels can be cut to the required size. Each 1.0 m segment of the panel has four cells (cavities). Each cell is 250 mm wide and 124 mm thick, containing a cavity 230 mm x 94 mm. (Refer figure 1). The cavities / formed cells within the panel can be used to accommodate building services such as plumbing and electrical conduits or they can be fully filled, partially filled or unfilled with concrete as per the structural requirement. (Shinto, et al., 2016)
These integrated composite GFRG panels are suitable for load-bearing up to 8 -10 storeys without the use of beams and columns. Although the main application of these panels is in the construction of walls, it can also be used in floor and roof slabs in combination with reinforced concrete. The panel contains cavities that may be filled with concrete and reinforced with steel bars to impart additional strength and provide ductility. (Mujeeb & Udhayasakthi, 2017)
-
INTRODUCTION
The demand for conventional materials, used as major building components in the housing sector like clay, sand, stone, gravels, cement, brick, block, tiles, distemper, paint, timber and steel is growing every year. The cost of construction materials is increasing incrementally. Also due to the high transportation costs of these raw materials, demand, environmental restrictions, it is critical to find functional /innovative substitutes for conventional building materials in the construction industry. Reduction in the use of these energy-intensive construction materials and the speedy delivery of housing units at affordable cost is the key challenges faced in the mass housing sector today.
Recently, these panels are being produced in India. In India FACT (The Fertilisers & Chemicals Travancore Ltd.) & RCF (Rashtriya Chemicals & Fertilizers Ltd.), two fertilizer giants under the public sector are together setting up Rapid wall product manufacturing plant at Ambalamugal, Kochi and launched gypsum-based wall panels in the market, capable of replacing brick walls. (Tayade, et al., 2014)
Buildings using Glass Fiber Reinforced Gypsum (GFRG) panels hold promise as a rapid, affordable and sustainable mass housing solution. GFRG Panels are made of calcined
Fig 1. Typical cross-section of GFRG panel (all dimensions are in mm) Source: Building Materials & Technology Promotion Council (BMTPC)
-
AIM & OBJECTIVES
This paper aims to review and analyze the potential of using GFRG wall panels in the Indian construction industry through performance parameters. To achieve this aim, the following are the objectives:
-
To compare the GFRG panel system of construction with the RCC frame construction system based on identified parameters.
-
To assess the advantages and disadvantages (limitations) of the GFRG panel system.
-
To analyze the use of the GFRG Panel system through a case study.
-
-
METHODOLOGY
Following steps were undertaken as an approach towards this study:
Step 1:
Desk research of the existing literature on GFRG panel system including manufacturing and the installation process (published and unpublished)
Step 2:
Listing of specifications and the performance parameters and of the GFRG panels along with the comparisons of same with the conventional system
Step 3:
Identification of case study for comparison of GFRG Panel system and RCC / Masonry structure through detail estimation and BOQs
-
PERFORMANCE PARAMETERS OF GFRG PANEL BASED BUILDING
The parameters which have been identified for the comparison of GFRG Panels based construction and conventional (RCC frame) construction can be largely classified under following categories:
-
Load Bearing Strength
The Load Bearing Strength or Compressive Strength is the characteristic strength of a material below which not more than 5% of the test results are expected to fall. This concept assumes a normal distribution of the strengths of the samples. Load Bearing capacity tested in a Universal Compression Machine of GFRG panels against Brick masonry.
TABLE I. LOAD BEARING STRENGTH OF GFRG AND BRICK MASONARY
Material
Compressive Strength
GFRG Panel
4.77 mPa
Brick masonry (in 1:6 cement mortar)
4. 0 mPa
(BMTPC, 2014) (Rao, 2013)
-
Fire Resistance
As applied to elements of buildings, the fire- resistance rating classifies the ability of an assembly to confine and isolate fire within a zone comprised of fire- resistance rated walls, ceiling and floor assemblies.
TABLE II. FIRE RESISTANCE GFRG AND BRICK MASONRY
Building System
Fire rating
GFRG Panel
4 hrs (with infill)
Brick masonry (9)
4 hrs
-
Thermal Comfort
Thermal comfort and health criteria primarily involve the temperature and humidity conditions in the building. Too high temperature means that occupants are uncomfortably hot. Too low a temperature means that occupants are uncomfortably cold. The wrong humidity means that occupants feel damp or sweaty or too dry.
-
values (also referred to as heat transfer coefficients) is used to measure how effective elements of a buildings fabric are as insulators. That is, how effective they are at preventing heat from transmitting between the inside and the outside of a builing. The lower the U-value of an element of a building's fabric, the more slowly heat is able to transmit through it, and so the better it performs as an insulator.
TABLE III. U-VALUE COMPARISON BETWEEN GFRG BUILDING SYSTEM AND CONVENTIONAL SYSTEM
Building material
U-Value
GFRG Building System
Wall Panel
2.5 W/m2K
GFRG Slab
2.5 W/m2K
Conventional System (8 Brick masonry in 1:6 CM, RCC roof)
8 Brick Wall in 1:6 CM
2.1 W/m2K
4" Concrete Slab
2.3 W/m2K
-
-
Acoustic Performance
The number used to rate the effectiveness of a soundproofing system or material is Weighted Sound Reduction Index (Rw). Increasing the Rw by one translates to a reduction of approximately 1db in noise level. Therefore, the higher the Rw number, the better a sound insulator it will be.
TABLE IV. ACOUSTIC PERFORMANCE COMPARISON BETWEEN GFRG AND CONVENTIONAL SYSTEM
Building material
Rw value
GFRG panel-based Building System
Wall Panel (Unfilled)
28
GFRG Slab
49
Conventional System (8 Brick masonry in 1:6 CM, RCC roof)
8 Brick Wall in 1:6 CM
52
4" Concrete Slab
29
(ECBC, B.E.E, 2011), (Approved Document E, 2010)
-
Cost (Economic Parameter)
Amount of Money spent on construction of a specific project. The cost of construction is often expressed in cost per unit area. The general construction cost of GFRG building ranges from INR 1200/ sqft to 1400/ sqft and for conventional
Building of the same scale is INR 500/sq.ft to 1800/ sqft approximately.
Economies of Scale: In microeconomics, economies of scale are the cost advantages that enterprises obtain due to size, output, or scale of operation, with cost per unit of output generally decreasing with increasing scale as fixed costs are spread out over more units of output.
Small scale rates
Large scale rates
Slab
Cost of panels
INR 1300/SQ.M
INR 1100/SQ.M
Above 20 panels
Small scale rates
Large scale rates
Slab
Cost of panels
INR 1300/SQ.M
INR 1100/SQ.M
Above 20 panels
TABLE V. PRICING DATA FOR GFRG PANELS
Note: The economy of scale is a project-specific parameter.
Source: BMTPC
-
-
ADVANTAGES OF GFRG OVER CONVENTIONAL BUILDING SYSTEMS:
GFRG panels satisfy the important requirements which are essential needs of the construction industry presently leading to many advantages of this product over conventional construction systems (Mujeeb & Udhayasakthi, 2017). The advantages are:
-
Cost-effective and innovative/ alternative construction material.
-
Sustainable / Environmentally friendly.
-
Easy, fast & economical construction.
-
The structure is safe against natural disasters like earthquakes, cyclones and fire.
-
The structure offers good sound insulation quality.
-
GFRG based building system is energy efficient, strong & durable.
-
Less embodied energy and CO2 emissions.
-
Offers less built-up area for the same carpet area.
-
Significant reduction in use of cement, sand, steel and water.
-
The structure is Lightweight and accurate (weight of panels – 43 kg/sqm), contributing to savings in foundation and reduction in design for earthquake forces, particularly in multi-storied construction.
-
Construction of 8-10 storeys building can be done when the GFRG panel system is designed as a load-bearing system, without the need for columns and beams.
-
Excellent finishes and there is no need for additional plastering. This feature also adds to the savings.
-
The structure is fireproof, earthquake resistant and has good sound attenuation quality
-
The durability of the GFRG building construction is the same as the conventional construction.
-
-
DISADVANTAGES / LIMITATION OF GFRG BUILDING SYSTEMS
Even though there are no drawbacks of using this technology, some of the practical issues which ascend are as under:
-
Expertise required to make a house using this technology. The handing, fixing and equipment required for these panels are fairly different from conventional style.
-
The Panels are customized according to the design (including the openings also), hence it is not possible to make changes during the fixing stage.
-
For building to be built on the GFRG panel system, equipment like the crane is required. In addition to this, a good amount of space around the plot is required for crane movement
-
Special care is necessary while storing the panels. Also, more space is required as compared to cement/blocks. This makes it difficult for a full-scale implementation in India (mass housing or affordable housing).
-
The panels are not suitable for curved walls or domes. In case it is essential, use masonry/concrete for that particular area.
-
The electrical/plumbing system should be such that most of the pipes go through the cavities (in order to facilitate minimum cutting of panel)
-
The span of a slab (floor/roof) should be restricted to a maximum of 5 m.
-
GFRG panel-based construction is only ideal if the same floor/roof is replicated for all floors in a multi-storeyed structure. For any variations, a structural designer needs to be consulted.
-
-
CONCLUSION / INFERENCES:
A detailed study, appraisal and analysis of the GFRG Panel based building System was carried out during this study which leads to the following are the conclusions:
-
GFRG Panel based construction is a new approach to building construction.
-
This construction method takes a giant leap towards sustainable living reducing the adverse impact on the environment which is generally attributed to the conventional construction technologies that have been followed.
-
Although theoretically there are advantages of using this technology, a few practical issues do arise as to its disadvantages (Ex. Crane movement, expertise, and storage of panels)
-
Even though GFRG panel technology is widely accepted and used in the southern part of India (mostly in Tamil Nadu, Andhra Pradesh and Kerala), it is not used in the northern part of the country. The main reason is the transportation cost of these panels which makes the use of these panels non-viable.
-
There is a lack of awareness pertaining to this technology among the people including developers, contractors and end-users.
-
This technology can be suitable to the affordable housing or EWS or where Rapid construction is required. It can be a good choice for Rehabilitation Housing, temporary housing (in case of natural calamity or disaster, etc.) or when there is a huge demand of housing in a short time. (subjected to the availability of the panels)
-
GFRG technology is comparable to conventional construction systems with few limitations. Example: Poor performance of un-fill panels in case of fire resistance and acoustics. Whereas both these parameters are up to the mark when panels ar infilled. (Filling of panels leads to extra cost and reduction in savings)
-
While looking at the completion of overall project including the infrastructure and external development which are required for a project to become operational it is observed that- even if the dwelling units are ready (in short time) in isolation, the whole project cannot be operational in the absence of external ancillary and supporting services( drainage, electrical supply, water supply, storm water, roads, etc.). Hence, extensive planning is required if this technology is to be used in mass housing projects where external development is of considerable importance.
-
Lastly, it is too early to endorse the use of this technology in all parts of India.
-
-
ACKNOWLEDGMENTS
I am thankful to Professor (Dr.) Virendra Kumar Paul and Professor (Dr.) Chaitali Basu for their valuable inputs and guiding me in framing the outline of this research paper.
I would also like to extend gratefulness to Mr. DP Singh from BMTPC for extending his help in providing all the relevant information pertaining to the GFRG Construction.
I am deeply grateful to Mr. NK Sharma from Hindustan Prefab Limited, New Delhi for these inputs and guidance and allowing us to visit the GFRG demonstration house on the campus.
I am thankful to Mr. Shalu V from FRBL for sharing the details of the projects constructed through GFRG building system
-
BIBLIOGRAPHY
-
Approved Document E, 2010. Resistance to Passage of Sound, Approved Document E. London: HM Government, UK.
-
Bhushan, Tatar & Pati, S. R., 2010. Time and Cost Optimization Techniques in Construction Project Management. International Journal of Latest Trends in Engineering and Technology, p. Vol.(7)Issue(3).
-
BMTPC, 2014. Prospective Construction Systems for Mass Housing. Building Materials & Technology Promotion Council.
-
ECBC, B.E.E, 2011. Energy Conservation Building Code User Guide. New Delhi: Bureau of Energy Efficiency.
-
Gopikrishnan, S., 2016. Glass Fiber Reinforced Gypsum Panel Based Building System in Affordable Housing in India, New Delhi: Thesis Report.
-
IS 1642 : 1989, 2010. Indian Standard fire safety of buildings (general): details of constructioncode of practice. New Delhi: Bureau of Indian Standards.
-
Mujeeb & Udhayasakthi, 2017. Case Study on Glass Fiber Reinforced Gypsum Panel in Mass House Economics. The Asian Review of Civil Engineering.
-
Rao, K. S., 2013. Structural Masonry: Properties and Behaviour.
Civil Engineering, IISc Bangalore.
-
Shinto, P., Cherian, P., Menon, D. & Prasad, A. M., 2016. Use of glass fibre reinforced gypsum panels with reinforced concrete infills for construction of walls and slab. Indian Concrete Journal.
-
Tayade, S., Shinde, N. & Patil, S., 2014. Study of an efficient building Material:Rapid wall. International Journal of Modern Trends in Engineering and Research,.