
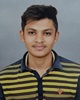
- Open Access
- Authors : Deep R Patel , Athul Shaju , Edward Bernard , Dr. A. M. Bisen
- Paper ID : IJERTV10IS050272
- Volume & Issue : Volume 10, Issue 05 (May 2021)
- Published (First Online): 27-05-2021
- ISSN (Online) : 2278-0181
- Publisher Name : IJERT
- License:
This work is licensed under a Creative Commons Attribution 4.0 International License
Conservation of Plastic Waste Into Article by Designing Mold for Injection Molding
Deep R Patel1
B. Tech Student Mechanical Engineering dept. ITM Vocational University,
Vadodara, India
Athul Shaju2
B. tech Student Mechanical Engineering dept. ITM Vocational University,
Vadodara, India
Edward Bernard3 Assistant Professor
Mechanical Engineering dept. ITM Vocational University, Vadodara, India
Dr. A. M. Bisen4 Vice Chancellor
ITM Vocational University, Vadodara, India
Abstract In this paper, we discuss the Design Development fabrication of a small injection molding machine for forming small plastic articles. The machine is designed and constructed to work as a prototype for producing very small plastic components as the material/granules are procured by the RECYCLING PLASTIC-BOTTLE CAPS. The motto of this project is to provide various useful articles with maximum cost efficiency and minimum wastage of plastic (such as duster, spoon, and trays). This can vastly help to Reuse and Recycle plastic waste (by bottle caps Polypropylene #5) and too educating principles of plastic waste management in coming years.
Keywords Machine, Mild Steel, Polypropylene #5, Prototype, Simulation.
(polypropylene #5 plastic). The scope of the work is to design and construct a cost-effective and environmentally friendly small injection molding machine- mold for the production of small and useful plastic articles.
-
OBJECTIVE
Plastic nowadays is the most worried polluted thing that harms the ecosystem. In addition, the global polypropylene market is expected to grow at a CAGR of 5.6 percent from 2016 to 2022, reaching 99.17 million tones, as shown in fig. 1(a).
I. INTRODUCTION
Injection Molding Machine offers diversified benefits as the process is well known for producing parts of different sizes and shapes by injecting molten material into mold and cooling it till it solidifies. Also, more efficient than alternatives manufacturing methods, including minimal losses from scrap. As it contains mainly two units: injection unit and clamping unit; the process has controllable cycle time, productivity rate, and effectiveness. In this injection molding machine, mild steel is used for the construction of supporting plates, hopper, mainframe, mold, and platens, handle and tie bars.
Discussing the material, plastic bottle "caps" are the main aspect on which the whole process is justified. These caps have been collected from scrap as a large amount of plastic is used by university or school students in canteens; tug shops, restaurants etc. Every single day. With such an act of reusing waste (cold drink bottle caps, mineral water bottles caps, tupperware container, ice cube molds & trays), it widely reduces initial production costs. The main aim of the research work is to design, construct, and testing of small injection molding- mold by recycling waste plastic material from college university campuses including bottle caps
Fig. 1. Data of PP market in recent years.
In this research, we have utilized pre-used bottle caps of (polypropylene #5) material. Our team collected plastic waste of the aforementioned kind from university campus as well as other sources with which we are associated (i.e., Restaurants and Hotels). The above-mentioned material, as shown in fig. 1(b)., was gathered, color-coded, recycled, and used in the development of a planned/determined product (whiteboard duster).
Can alternatively recycle following types of plastic: It has a capacity to mold the items from raw materials as following Maintaining the Integrity of the Specifications
-
Polystyrene / (C8H8)n
Nylon 66 / (C12H22N2O2)n
-
Nylon 66 / (C6H11NO)n
-
Polyethylene / (C2H4)n
-
Polycarbonate / C15H16O2
hopper in most injection moulding machines feeds the injection barrel by gravity. The plastic is melted and prepared for injection into the mould cavity by the injection barrel. One of two methods is used to move the molten plastic through the injection barrel. A reciprocating screw is used to propel the plastic forward. Since the reciprocating screw is more precise, it is more widely used. Allow the molten plastic to cool and solidify after injecting it into the empty mould cavity. Since the mould is made up of two parts, they must be separated in order for the part to fall out. Certain parts do not fall out of the mould by themselves; instead, an extra ejector pin is used to knock the element out of the mould after it has solidified. Furthermore, process mapping of whole cycle from collecting caps from scrap to final packaging of article is elaborated in fig. 2.
Fig. 1(b). Cap weight by brand wise (in Gram).
As a result, we chose polypropylene plastic for its ease of recycling and utility as an item.
-
-
PROCESS PLANNING
Fig. 2. Process flow chart of recycling of bottle caps into an
article.
Plastic resin is stored in the hopper and fed into the injection moulding machine. Plastic caps come in a variety of shapes and sizes, including beads, granules, and flakes. The
-
DESIGN
The first step to build a mold from the scrap is to design a layout of the designated article which was finalized to produce. Whiteboard duster was the one that was selected by the team as the article which could be recycled by PP #5 granules.
Finally, the duster's design was completed by creating a 2D drawing using AutoCAD software, as shown in fig. 3.
Fig. 3. 2D Drafting of Article designed through AUTOCAD Software.
-
Design Planning for mold
Fig. 4. Mold design (via Solidworks).
Prior to the machining processes (VMC, boring, drilling, turning, grinding), it was important to design the mould. The project team used Solidworks software to build it, as seen in
fig. 4. As a result, the project's costs were significantly reduced.
-
Selection of Mold from scrap
Since the mould was made from scrap metal, earlier it was weighed about 79 kg, as shown in Fig. 5. After machining it weighted about 68 kg, Scrap consisting Mild-steel was selected by considering various factors like shape, dimensions and usage.
Fig. 5. Scrap part.
-
-
ANALYSIS
-
Structural Simulation
The SOLIDWORKS simulation is used to simulate the recovered molds product (Whiteboard Duster) structural behavior. Static analysis was used to calculate the real-time loads.
The component was first simulated to the customized plastic material which matches its chemical and mechanical properties with PP. As, Polypropylene is used as raw material. All material properties required by the associated study form and material model were determined. As a result, the mechanical property of the material is given above in fig. 6.
Fig. 6. Material Properties.
Finite Element Analysis (FEA) can predict a product's real- world physical behavior by testing CAD models in practice.
This article's static test examines key features of the assigned variable, such as stresses and displacements is illustrated in
Fig. 6(a). Static Nodal Stress by applying 0.5 N force.
Fig. 6(b). Static- Displacement by applying 0.5 N force.
Fig. 6(a). and Fig. 6(b).
-
Draft Analysis
Mold draft make it easier to remove parts from the mould. The draft must be parallel to the mould opening and closing at an offset angle. The optimal draft angle for a given part is determined by the part's depth in the mould and the end-use purpose requied.
Fig. 7. Draft Analysis to ensure that the component ejects from the tooling adequately.
Conclusion
In this study, the finite element method was used to analyze the effect of recycled plastic as well as a reused mold for the better strength of the final product. As the improvements within the plastic injection machinery continue and tones of plastics are produced and wasted each passing year. Mold can be reused by replacing the cavity plates within the mold as rest of the mold can be used as it and can be used with various materials can be utilized. Polystyrene, Nylon 66, Polyethylene, etc. And with a minimum time limit with maximum productivity rate can also be made. Moreover, varieties of household products consisting of mentioned plastics raw material could be recycled while separating by the order of range in colors. Thus, Fig. 8. and Fig. 9. shows the outlook of mold and product respectively.
Fig 9. Finishing sample article from Mold.
-
-
FUTURE SCOPE
There are several possibilities for further study. One can study to determine the importance of reusing metal scrap and transform it into a mold by performing various machining processes. Plastic injection molding is a highly advanced method that has resulted in a range of useful items that we use every day in our everyday lives such as duster, spoon, trays, and many more. Several different materials other than PP can also be used as raw materials. This study's findings would provide a technological basis for future recyclable products, as the results clearly illustrate that demand for more eco-friendly products, such as recycled, reused, and sustainable plastics, will continue to rise as people become more conscious of climate change and other environmental factors.
ACKNOWLEDGMENT
With a sense of gratitude and respect, we would like to extend our heartiest thanks to all those who provided help & guidance during our research period. It was a pleasant and highly educative experience to work on a project on, Conservation of plastic waste into article by designing mold for injection molding.
We are grateful to Prof. Edward Bernard for giving us such a chance to undertake a project and were always ready to provide the best instruction and guidance to do work better.
We are very grateful to Dr. Anil Bisen, Vice-chancellor of ITM Vocational University, Vadodara for his continuous help and support.
REFERENCES
Fig. 8. Mold after machining and polishing.
-
Mulge, P. K., & Kalashetty, S. S. A Brief Literature Review on Optimization of Plastic Injection Moulding Process Parameters for Various Plastic Materials by using Taguchis.
-
Rathi, M. M., & Salunke, M. M. D. (2012). Analysis of injection moulding process parameters. International Journal of Engineering Research and Technology, 1(8), 1-5.
-
Kharche, M. N. A., Deshmukh, S. D., JNEC, A., & Patil, R. B. The Concept of Solid Modelling in The Plastic Injection Moulding Process.
-
Al-Hadad, M. A. A. M., & Wang, Q. CAE Analysis and Structure Optimization Design of Injection Mold for Charge Upper Cover.
-
Jauregui-Becker, J. M., Tosello, G., Van Houten, F. J., & Hansen, H.
N. (2013). Performance evaluation of a software engineering tool for automated design of cooling systems in injection moulding. Procedia CIRP, 7, 270-275.
-
Selvaraj, S., & Venkataramaiah, P. (2013). Design and fabrication of an injection moulding tool for cam bush with baffle cooling channel and submarine gate. Procedia Engineering, 64, 1310-1319.
-
Selvaraj, S., Venkataramaiah, P., & Vinmathi, M. S. (2015). Optimization of Process Parameters in Injection Moulding of FR Lever
Using GRA and DFA and Validated by Ann. Research Journal of Applied Sciences, Engineering and Technology, 11(8), 817-826.
-
Rafi, S. S., & Sami, A. (2011). Finite Element Analysis of a Beam with Piezoelectrics using Third Order TheoryPart II Dynamic Analysis- Active Vibration Control. International Journal on Emerging Technologies, 135-139.
-
Shakkarwal, P., & Yadav, L. (2013). Design and mould flow analysis of injection mould for connecting link. International Journal on Emerging Technologies, 4(1), 182-185.
-
Akhtar, S., & Abbas, M. (2013). Applying Finite Element Method for stress Analysis and Optimization of Lift arm of Tractor. International Journal on Emerging Technologies, 4(1), 108-111.