
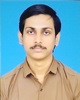
- Open Access
- Authors : Gaurav Prakash , Gautam Gahlot , Vishnu Jajoo
- Paper ID : IJERTV11IS050273
- Volume & Issue : Volume 11, Issue 05 (May 2022)
- Published (First Online): 01-06-2022
- ISSN (Online) : 2278-0181
- Publisher Name : IJERT
- License:
This work is licensed under a Creative Commons Attribution 4.0 International License
Coconut Shell Powder and Xantham Gum Analysis as A Lost Circulation Material in Drilling Fluid
Gaurav Prakash (Author) Department of Petroleum Engineering Engineering College Barmer
Barmer, Rajasthan, India
Gautam Gahlot2, Vishnu Jajoo3 (Co-Author) Department of Petroleum Engineering Engineering College Barmer
Barmer, Rajasthan, India
Abstract A drilling fluid must be circulated through the well and back to the surface. Occasionally, highly permeable, or cavernous formations and fractured zones, both natural and induced by the mud pressure, are encountered and circulation is partially or completely lost.
Loss of drilling fluid, owing to openings in the formation, can result in the loss of hydrostatic pressure at the bottom of the hole and allow influx of formation fluids and possibly loss of well control. It is essential that circulation be regained for drilling to continue. Most common thief zones are highly permeable formations. Because of higher permeability (because of large pore size), loss of drilling fluid into formation initiates.(Onuh
-
- et al., 2017).A wide variety of materials can be added to the drilling fluid to reduce the loss of drilling fluids in the high permeable zones. A fibrous material: coconut shell, bagasse and sawdust, to be acceptable as a lost circulation control additive, must possess the properties of high tensile strength, great flexibility, being chemically neutral and it is extremely desirable that the material shall be economical with regard to cost. The particle sizes of these materials are much larger than the particle sizes of solids normally suspended in the mud. Particle Size Distribution (PSD) of LCM is the most important criterion on which treatments are designed Circulation losses have always been a serious and expensive problem to the drilling industry. Even with the best drilling practices circulation losses do occur. To reduce such losses to acceptable level fluid Loss Control Material (LCM) is used., Xantham gum, coconut shell powder was investigated as lost circulation control materials Xantham gum and coconut shell powder shows a better effect on the rheological property.KeywordsCavernous formations, hydrostatic pressure, thief zones, loss control material.
- INTRODUCTIONDrilling fluids are usually categorized based on their basic material. The drilling mud can be water-based with solid particles suspended in it, or it can be oil-based with water or brine emulsified in the oil to produce a discontinuous phase and solid particles suspended in the oil continuous phase. Water-based drilling fluid including an aqueous fluid, at least one of a weighing-agents and at least one gelling agent, and a lubricant containing at least one ester derivative. Water-based drilling fluids may be appropriate for some types of formations; however, for proper drilling in other formations, the drilling fluid is injected into the well via the drill pipe and recirculated to the surface via the annular region formed by the wellbore. The drill string and the wall Before beingpushed back into the well, the drilling fluid is physically and chemically treated and conditioned at the surface.
Xanthan gum (Microbial Polysaccharides) is a water-soluble biopolymer formed by the action of bacteria on carbohydrates that we employ as a filtration control agent. Following the fermentation process, the bacteria are destroyed and the gum is extracted through precipitation with isopropyl alcohol. The gum is dried and ground once the alcohol has been recovered. The molecular weight of the polymer is around 5,000,000. Without the use of other chemicals, xanthan gum may increase viscosity in fresh, sea, and salt water. In solution, the molecule develops a stiff rod-like shape. This results in extremely high viscosities or gels.
Xanthan gum (Microbial Polysaccharides) is a water-soluble biopolymer formed by the action of bacteria on carbohydrates that we employ as a filtration control agent. Following the fermentation process, the bacteria are destroyed and the gum is extracted through precipitation with isopropyl alcohol. The gum is dried and ground once the alcohol has been recovered. The molecular weight of the polymer is around 5,000,000. Without the use of other chemicals, xanthan gum may increase viscosity in fresh, sea, and salt water. In solution, the molecule develops a stiff rod-like shape. This results in extremely high viscosities or gels at low shear rates. As a result, xanthan polymer has remarkable dispersion characteristics that are unrivalled by other polymers at comparable concentrations. Polymer muds made from xanthan gum are resistant to contamination by anhydrite, gypsum and salt. This polymer1 has particular application in clay free, potassium-based fluids where it will increase the carrying capacity of mud without increasing its viscosity. The polymer also has application in completion fluids where suspension of weighting materials is required.
Cellulose fibers have demonstrated the unique characteristic of quickly forming a seal at the face preventing entrance of damaging fluids or solids into producing formations. Compared to the more rigid and brittle inorganic solids such as sized calcium carbonate, sized salts or fibrous calcium silicates, certain types of micronized cellulose fibers are flexible, highly compressible, 10 slightly swellable and partially extrudable. As a result, properly selected cellulose fibers have the ability to form quick, surface seals and minimize the penetration of solids or liquids into the formation.
- LOSS CONTROL MATERIALlost circulation material (LCM) is defined as a substanceMaterials
- METHODLOGYadded to cement slurries or drilling mud to prevent the loss of cement or mud to the formation. The substance may contain a blend of granular, fibrous and flake material with particle size distribution believed to be large enough to form bridge of material in the fracture or cavern. It is important that the bridge be within the formation and not on the surface of the wellbore where it can be dislodged by the drill pipe. Industry has developed the following three basic types of agents depending on the operational phase of the well to combat lost circulation.
- Bridging agents
- Gelling agents
- Cementing agents
Bridging agents are found effective to handle lost circulation problems and are classified in respect to their morphology as fibrous, flake, granular and blended.(Latifa Latif Kanba and Sami Fatih Mustafa, 2020).
Table 2.1: Types of additives base on its function in drilling fluid
Weighting Agents Deflocculation Agent Filtration Control Agent Viscosifying Agent Barite Hematite Calcium Carbonate Salt Lignosulfonate Polymers Phosphates Bentonite Starch Modified Cellulosic Synthetic Polymer Bentonite Polymer - Xantham GumXantham gum soluble in both cold and hot water, not affected by changes in pH value and high temperature xantham gum increases the viscosity of any liquid.as a result, characteristics include: colour, pH value, solubility.
Property Xantham gum Color White Or Cream Colored pH 6-7 Table 2.2: Physical properties of xantham gum.
- Coconut Shell Powder
Coconu shell powder is very fine-grained powder to generated by crushed coconut shell.
Coconut shell contains proper amount of cellulose and lignin.
Cellulose (wt%) 32-43 Hemicellulose(wt%) 0.15-0.25 Lignin(wt%) 40-45 Pectin(wt%) 3-4 Moisture content(wt%) 8 Table 2.3: Chemical composition of coconut shell
Table 2.4 : physical properties of coconut shell powder
The equipment used in this work includes the mud balance, rotary viscometer, agitator, spatula, weighing balance, wash bottle, measuring cylinder, beaker, stop watch, mixer, grinding machine, pH meter and low-pressure low temperature (LPLT) filter press. The raw materials used are bentonite, barite, water, xantham gum and coconut shell.
Mud samples MWTCSXG MWXG MWCS MWCSXG Bentonite(gm) 20 20 20 20 Barite (gm) 60 60 60 60 Water(ml) 350 350 350 350 Xantham gum (gm) NIL 2,4,6,8,10 NIL NIL Coconut shell powder(gm) NIL NIL 2,4,6,8,10 NIL Coconut shell powder and xantham gum(gm) NIL NIL NIL 2,4,6,8,10 - Preparation of Coconut Shell PowderVery large amount of coconut shell waste produced in every day. This waste be used in agriculture purpose and fuel or charcoal generation .so that we use coconut shell from local market or temple etc. it is fibrous type material, that contain proper amount of cellulose and lignin.Material: coconut shell from locally obtained, heat oven, grinding machine, measuring cylinder.
- To remove all moisture content, the sample was held in a high vacuum oven at 100. after that, it was ground into fine particle with a grinding machine for 20 minutes.
- The crushed material was sieved to 125 microns.
- Experiment ProcedureMud preparation involves the following steps:
- To prepare 20g bentonite clay and 60g barite mixed with 350ml of distilled water mixed with Hamilton beach. the density measured using mud balance. The mixer is been powered to rotate while mixing the mud samples for 30 minutes until homogeneous mixture is achieved. The first experiment was performed without the xantham gum and coconut shell in order to properly compare and analyze the effect of the coconut shell and/or xantham gum.
- Further experiment was conducted in the presence of the coconut shell and/or the xantham gum in different concentrations of 2 g, 4 g, 6 g, 8 g, and 10 g. The mud balance was used to measure the density of the mud, and the LPLT Filter Press after being pressurized, fitted with a filter medium was used to measure the fluid loss i.e the filtrate volume from the drilling fluid.
- Formulation of mud sample.
Property Coconut shell Colour Dark brown Specific gravity 1.33 Bulk density (kg/ ) 800 - Mud samples without coconut shell and xantham gum (MWTCSXG)
- Mud samples with Xantham gum (MWXG)
- Mud sample with coconut shell (MWCS)
- Mud samples with combination of coconut shell and Xantham gum (MWCSXG)
- EXPERIMENTAL RESULT
- INTRODUCTIONDrilling fluids are usually categorized based on their basic material. The drilling mud can be water-based with solid particles suspended in it, or it can be oil-based with water or brine emulsified in the oil to produce a discontinuous phase and solid particles suspended in the oil continuous phase. Water-based drilling fluid including an aqueous fluid, at least one of a weighing-agents and at least one gelling agent, and a lubricant containing at least one ester derivative. Water-based drilling fluids may be appropriate for some types of formations; however, for proper drilling in other formations, the drilling fluid is injected into the well via the drill pipe and recirculated to the surface via the annular region formed by the wellbore. The drill string and the wall Before beingpushed back into the well, the drilling fluid is physically and chemically treated and conditioned at the surface.
- et al., 2017).A wide variety of materials can be added to the drilling fluid to reduce the loss of drilling fluids in the high permeable zones. A fibrous material: coconut shell, bagasse and sawdust, to be acceptable as a lost circulation control additive, must possess the properties of high tensile strength, great flexibility, being chemically neutral and it is extremely desirable that the material shall be economical with regard to cost. The particle sizes of these materials are much larger than the particle sizes of solids normally suspended in the mud. Particle Size Distribution (PSD) of LCM is the most important criterion on which treatments are designed Circulation losses have always been a serious and expensive problem to the drilling industry. Even with the best drilling practices circulation losses do occur. To reduce such losses to acceptable level fluid Loss Control Material (LCM) is used., Xantham gum, coconut shell powder was investigated as lost circulation control materials Xantham gum and coconut shell powder shows a better effect on the rheological property.KeywordsCavernous formations, hydrostatic pressure, thief zones, loss control material.
- Mud sample without coconut shell powder and xantham gum;Table 4.1 Properties of Mud Samples
Physical properties Value pH 11 Mud density(ppg) 8.2 Fluid loss(ml) 29 - Mud sample with coconut shellTable 4.2 Properties of Mud SampleFluid loss in different concentration of
material
Fluid loss (ml)
35
30
25
20
15
10
5
2g 4g 6g 8g 10g MWTCSXG 29 29 29 29 29 MWCS 20 19 18 16 14 MWXG 8 6 5 5 4 MWCSXG 5 4 3 3 2 0
Physical properties Concentrations of xantham gum 2g 4g 6g 8g 10g pH 10 10 9 9 10 Fluid loss(ml) 8 6 5 5 4 Mud density(ppg) 15 16 16 18 20 Weight of material
- Mud sample with Xantham gum
Physical properties Concentrations of combined coconut shell and xantham gum 2g 4g 6g 8g 10g pH 10 11 12 12 12 Fluid loss(ml) 5 4 3 3 2 Mud density(ppg) 17 19 20 22 23 Table 4.3 Properties of Mud Sample
- Mud sample with combination of coconut shell and xantham gum.
Table 4.4 Properties of mud sample
Figure 2: Fluid loss in different material
CONCLUSION
In this study, the effect of different raw materials on the rheological properties of water-based mud xantham gum and coconut shell powder were used at an amount of (2,4,6,8,10) gm. From the results, the following was concluded:
- The coconut shell powder is a potential pH modifier.
- Xantham gum a better fluid loss control agent than coconut shell but the combination of coconut shell and xantham gum yield a better result.
- Mud with combination of xantham gum provide better viscosity and gel strength.
- Raw material of this study easily available and economical for us.
td>20
Physical properties | Concentrations of combined coconut shell and xantham gum | ||||
2g | 4g | 6g | 8g | 10g | |
pH | 10 | 11 | 12 | 12 | 12 |
Fluid loss(ml) | 5 | 4 | 3 | 3 | 2 |
Mud density(ppg) | 17 | 19 | 22 | 23 |
Figure 1: Mud density with different material
REFERENCES
[1] Onuh C.Y Et Al. (2017) Environmentally Friendly Fluid Loss Control Agent in Water-Based Mud for Oil and Gas Drilling Operations, International Journal Of Applied Engineering Research ISSN 0973- 4562, 12, P. 4 [2] Latifa Latif Kanba And Sami Fatih Mustafa (2020) Effect Of Different Raw Materials On Rheological Properties Special Lost Circulation Of Water-Based Mud. Republic Of Iraq Ministry of Higher Education and Scientific Research University of Kirkuk College of Engineering. [3] Ahmed Mohamed Alsabagh Et Al. (2015) Evaluation Of Some Natural Water-Insoluble Cellulosic Material As Lost Circulation Control Additives In Water-Based Drilling Fluid, Egyptian Journal Of Petroleum, 24(4). [4] Rabia H. (2002) Well Engineering And Construction [5] Emmanuel U. Akpan,Godpower C.Enyl, Ghasem G. Nasr Enhancing The Performance Of Xantham Gum In Water-Based Mud System Using An Environmentally Friendly Biopolymer, Journal Of Petroleum Exploration And Production Technology [Preprint],Https://Doi.Org/10.1007/S13202-020-00837-0